- Noatum Group
- Get to know us
- Our Leadership
- Recognition and awards
- Our history
- Certifications
- Maritime Containers
- Air Containers
- Conversion Tables
- Dangerous goods labels
- Goods tariff code

Freight Management
- Contract Logistics / Warehouse & Distribution
- Customs services
- International Supply Chain Management
- Project cargo logistics
- Reefer Logistics
Automotive & Aerospace
Chemical industry, construction.
- Consumer Electronics
- Industrial Manufacturing
Oil and Gas
- Pharma & Healthcare
Renewable Energy
Case studies.
- Location & Contact
- Maritime containers
- Air containers
- Get a quote
Home / Case Studies
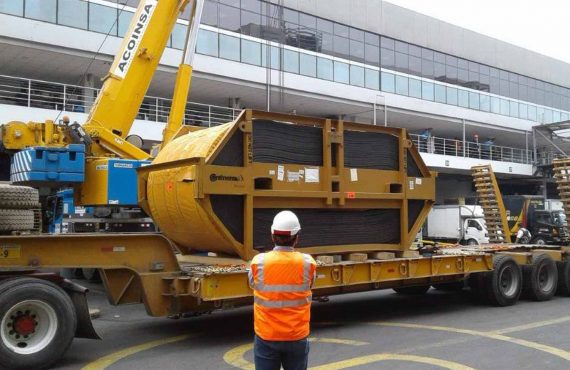
Case Study – Air transport services for mining industry
Our client needed to transport a total of 8 cable reels of 23 tons each from Shanghai. The challenge was to make the shipment in the shortest possible time with reasonable costs.
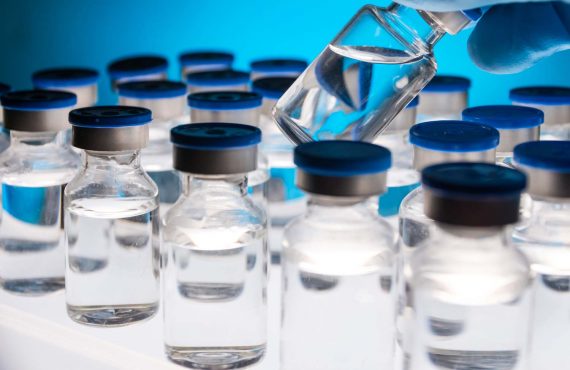
Case Study – Air Charter for Healthcare
The start of the Covid-19 vaccination campaign was imminent and our client needed regular shipments of syringes from China, where the factory was located, to Peru so they could ensure the vaccination campaign ran smoothly.
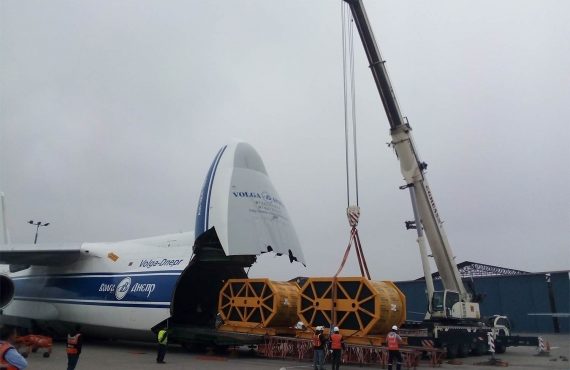
Case study – Air charter for the mining sector
Our client needed to urgently ship two conveyor belts from Santiago de Chile to Lima. These conveyor belts are used to move the mineral extracted from the mine into the storage area. Due to their size and weight, more than 60 tonnes, it was necessary to study in detail what would be the best transport solution to deliver in the shortest possible time.
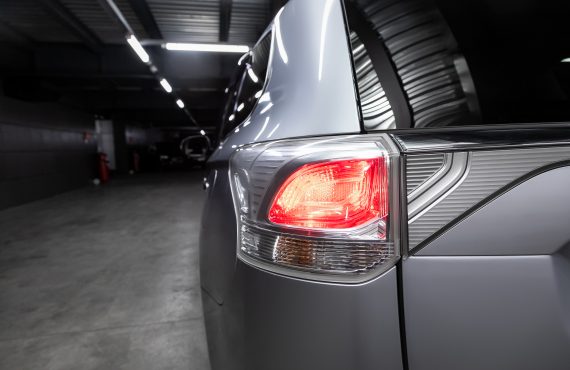
Case Study – Automotive logistics
To create a cost saving solutions with enhanced service levels, whilst maintaining existing structures and warehouse facilities.
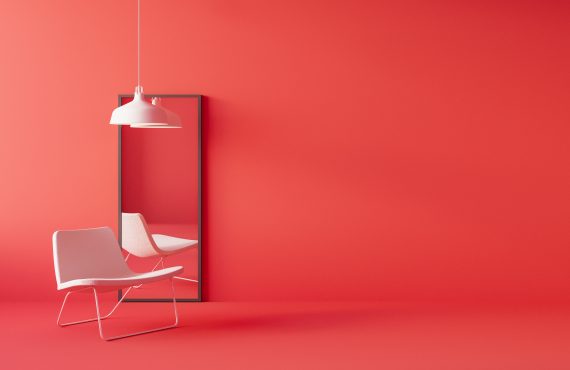
Case Study – Retail logistics: LG Harris
When understanding the LG Harris supply chain requirements, Noatum Logistics quickly identified that their buying terms were CIF (cost, insurance, freight) across the majority of their supply base. This prevented shipment visibility for LG Harris until the goods arrived into port. Accounting for over 1,000 TEU per annum was a major headache. The supply chain model was completely reactive with little or no reporting or key-performance-indicator (KPI) management. This created high demurrage charges, inbound-inventory and stock-control challenges at the LG Harris distribution centre (DC) located in the Midlands (UK).
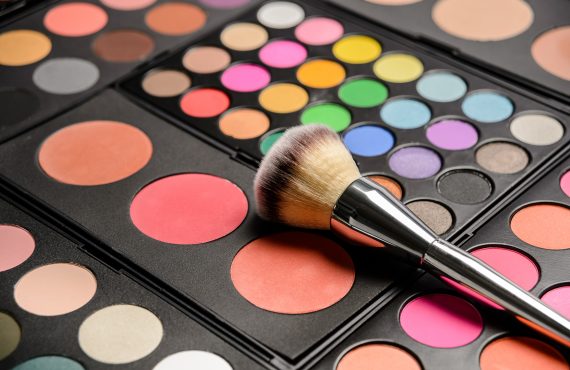
Case Study – Personal care logistics
The customer felt its supply chain was working fine. No pain, no need to change! However, having worked with Noatum Logistics in the past, and experienced improved operations, the new leader was willing to let us review the company’s pricing and route information on outbound shipments to the United States, Japan, Taiwan, Malaysia and Australia.
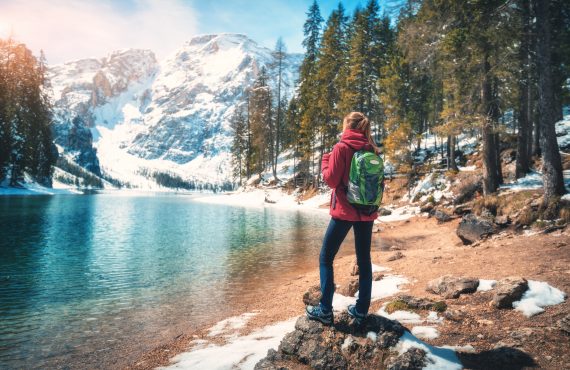
Case Study – Outdoor retailer logistics
The retailer faced major challenges with days-in-inventory and capacity at its distribution center (DC). Days-in-inventory time continued to increase over the prior five years The single distribution center experienced overly high storage levels, delays with unloading railcars and shipping containers, and an overall worsening in port-to-DC transit times (hovering around 40 days).
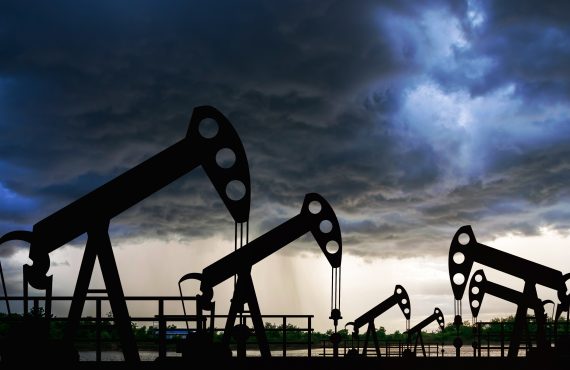
Case Study – Oil & Gas industry
With each unit weighing approximately 32,000 pounds, the company faced high shipping costs for the pumping units sourced from China.
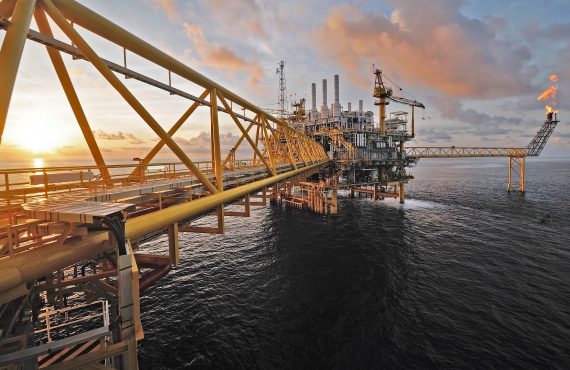
Case Study – Oil and Gas logistics
The customer suspected they were being overcharged for shipping. They were not using freight forwarders, instead allowing manufacturers to arrange for the ocean-freight shipping of the oilfield equipment from China to Canada. Cargo was shipped using fixed load plans with no optimization for larger batches.
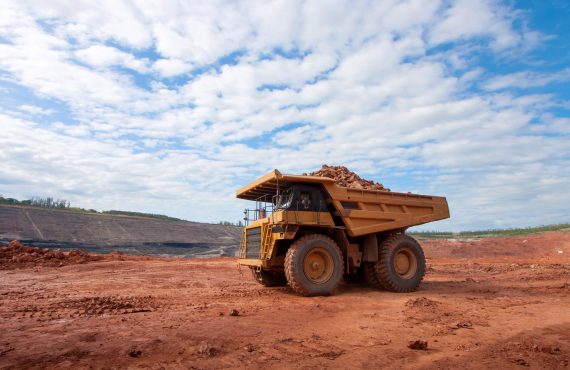
Case Study – Mining logistics
An initial assignment was for the movement of Autoclave and Flash Vessel pieces from their manufacturing plant, located 30 miles inland from the Shanghai port, to the mining project 90 miles east of Lima, Peru. The equipment pieces were over size and over weight, requiring special loading/unloading procedures; ocean, rail and ground transportation; and infrastructure modifications.
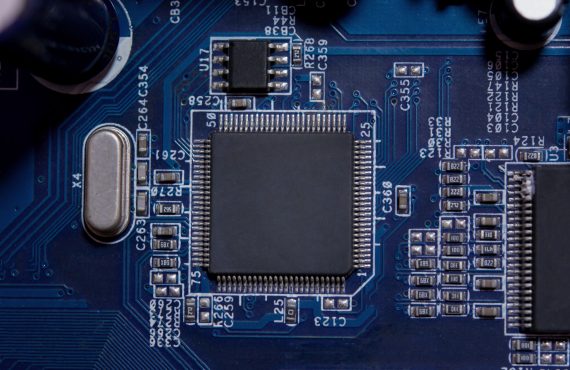
Case Study – High Tech logistics
With a significant segment of the semiconductor wafer foundry base moving to Asia, our customer decided to relocate operations closer to their end user. Our customer opened an equipment integration facility in Singapore near their customer who provides wafer fabrication equipment. Unfortunately, this move created an increase in real estate and labor costs, thus denying our customer the warehouse space to stage components for assembly and integration.

Case Study – Pharma&Healthcare logistics
Sourcing product from Korea, the customer initially used Noatum Logistics to assist with international freight forwarding and the custom clearance process for shipments to the U.S. As the customer grew their customer base and product offering, it was apparent their outsourced warehouse solution in the U.S. could not keep up with their needs. The end customers’ orders frequently required special packing, rush deliveries, and special project handling, straining the customer’s inventory management practices.
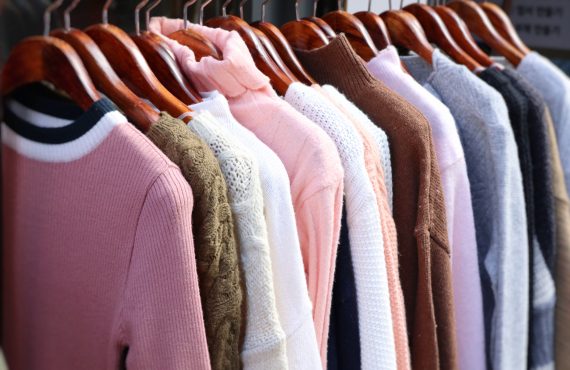
Case Study – Fashion industry logistics: Gant
Capitalise on the retail expertise and capabilities of Noatum Logistics, including our robust warehouse management technologies and local capacity. The benefits of greater inventory visibility and control would cascade into other supply chain functions including transportation, warehousing, distribution and customer service.
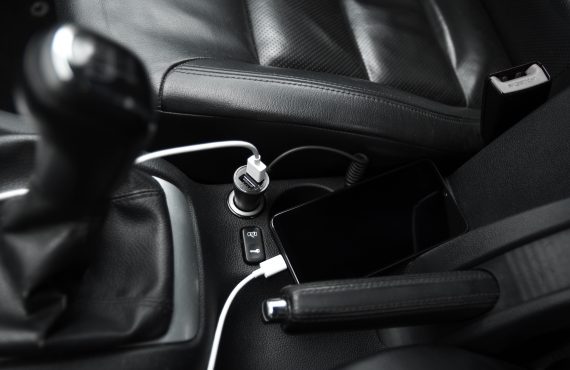
Case Study – Consumer Electronics logistics
A leading manufacturer of cell phone accessories was in a crisis. Issues with an overseas partner completely shut down their supply chain. They needed a new logistics services provider to quickly step in and get shipments moving. The manufacturer also recognized the need to rethink its supply chain to gain better control over vendors, reduce costs and achieve more efficient handling of orders.
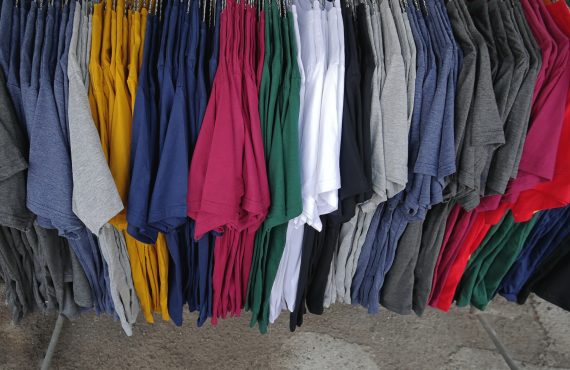
Case Study – Apparel retailer logistics
A retail client of Noatum Logistics for international freight forwarding services sought additional assistance for improving control over its global supply chain. The client recognized that greater visibility to purchase orders and shipments would lead to better purchasing, transportation and distribution decisions.
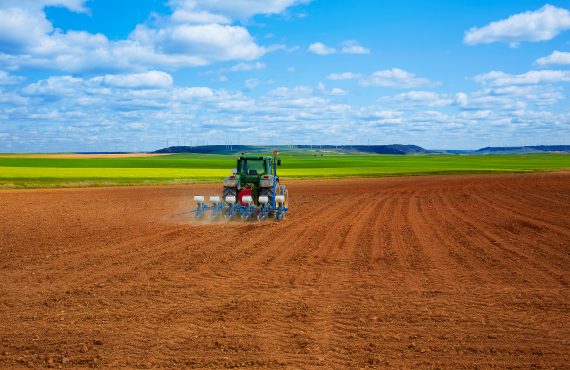
Case Study – Industrial Manufacturing logistics
Our customer is a leading multinational manufacturer of automobiles and agricultural machinery. The company entered the U.S. market in 2000; since 2002, Noatum Logistics has handled the company’s customs brokerage at Noatum Logistics’ Houston branch.
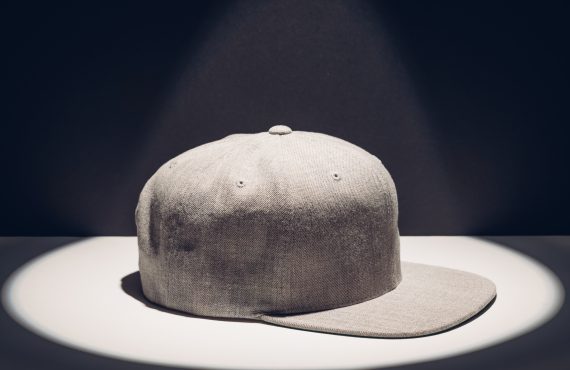
Case Study – Fashion industry logistics
Founded in 1920, New Era Cap Company is an American headwear company headquartered in Buffalo, New York. Best known for being the official on-field cap for Major League Baseball, the official sideline cap for the National Football League, and the official on-court cap for the National Basketball Association.
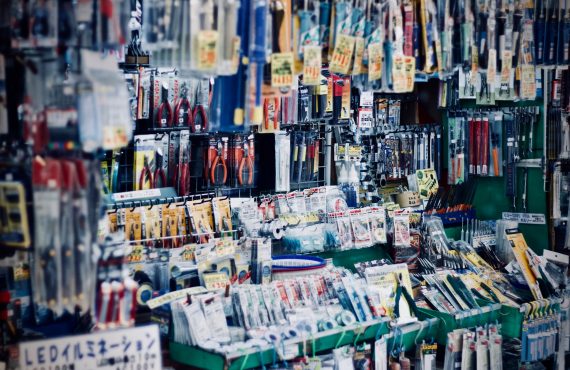
Case Study – High tech firm
The customer, a global provider of secure IP/Ethernet switching solutions, sources products from South China and Taiwan for sales in the United States. They identified cost containment objectives and wanted to improve the overall performance of their supply chain.
Logistics Services
- Freight management
Logistics Solutions
Key industries.
- Automotive Logistics
- Chemicals Logistics
- Construction Logistics
- Fashion Logistics
- Food Logistics
- Furniture Logistics
- Mining Logistics
- Oil and Gas Logistics
- Retail Logistics
- Renewable Energy Logistics
- Case studies

Noatum Logistics is a company of Noatum group
Reach out: [email protected] Whistleblowing: Online portal
© Copyright 2024. All Rights Reserved.
- Livro de reclamaçoes
- Privacy Policy
- Legal warning
- Cookies Policy
- All our business are subject to Noatum Logistics USA LLC Terms & Conditions
Select your country
- Browse All Articles
- Newsletter Sign-Up
Logistics →
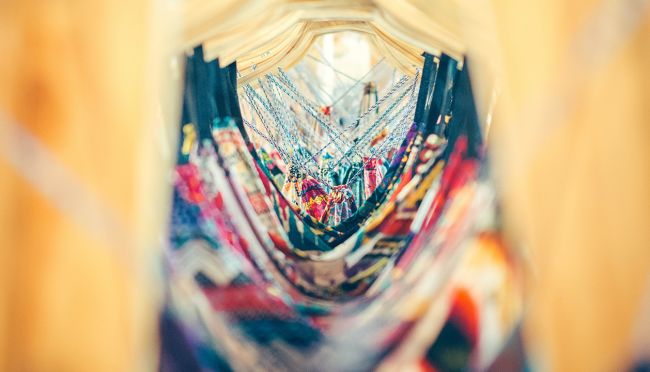
- 25 Apr 2023
How SHEIN and Temu Conquered Fast Fashion—and Forged a New Business Model
The platforms SHEIN and Temu match consumer demand and factory output, bringing Chinese production to the rest of the world. The companies have remade fast fashion, but their pioneering approach has the potential to go far beyond retail, says John Deighton.

- 18 Oct 2022
- Cold Call Podcast
Chewy.com’s Make-or-Break Logistics Dilemma
In late 2013, Ryan Cohen, cofounder and then-CEO of online pet products retailer Chewy.com, was facing a decision that could determine his company’s future. Should he stay with a third-party logistics provider (3PL) for all of Chewy.com’s e-commerce fulfillment or take that function in house? Cohen was convinced that achieving scale would be essential to making the business work and he worried that the company’s current 3PL may not be able to scale with Chewy.com’s projected growth or maintain the company’s performance standards for service quality and fulfillment. But neither he nor his cofounders had any experience managing logistics, and the company’s board members were pressuring him to leave order fulfillment to the 3PL. They worried that any changes could destabilize the existing 3PL relationship and endanger the viability of the fast-growing business. What should Cohen do? Senior Lecturer Jeffrey Rayport discusses the options in his case, “Chewy.com (A).”
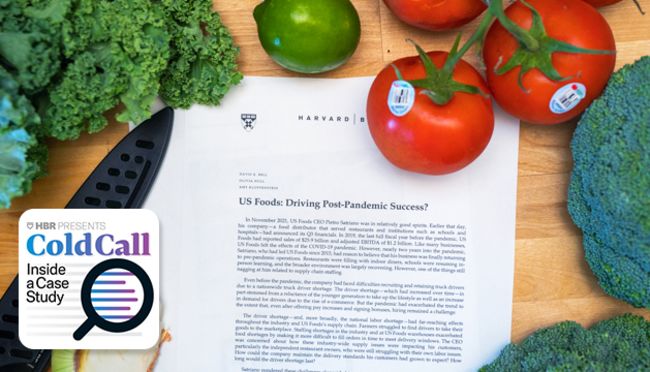
- 12 Jul 2022
Can the Foodservice Distribution Industry Recover from the Pandemic?
At the height of the pandemic in 2020, US Foods struggled, as restaurant and school closures reduced demand for foodservice distribution. The situation improved after the return of indoor dining and in-person learning, but an industry-wide shortage of truck drivers and warehouse staff hampered the foodservice distributor’s post-pandemic recovery. That left CEO Pietro Satriano to determine the best strategy to attract and retain essential workers, even as he was tasked with expanding the wholesale grocery store chain (CHEF’STORE) that US Foods launched during the pandemic lockdown. Harvard Business School Professor David E. Bell explores how post-pandemic supply chain challenges continue to affect the foodservice distribution industry in his case, “US Foods: Driving Post-Pandemic Success?”
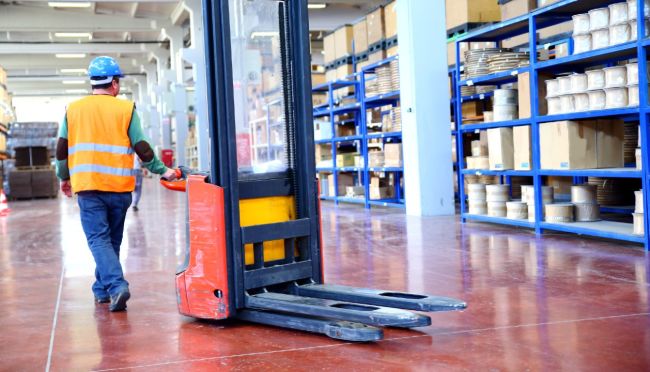
- 05 Jul 2022
- What Do You Think?
Have We Seen the Peak of Just-in-Time Inventory Management?
Toyota and other companies have harnessed just-in-time inventory management to cut logistics costs and boost service. That is, until COVID-19 roiled global supply chains. Will we ever get back to the days of tighter inventory control? asks James Heskett. Open for comment; 0 Comments.
- 19 Oct 2021
- Research & Ideas
Fed Up Workers and Supply Woes: What's Next for Dollar Stores?
Willy Shih discusses how higher costs, shipping delays, and worker shortages are putting the dollar store business model to the test ahead of the critical holiday shopping season. Open for comment; 0 Comments.
- 26 Mar 2014
How Electronic Patient Records Can Slow Doctor Productivity
Electronic health records are sweeping through the medical field, but some doctors report a disturbing side effect. Instead of becoming more efficient, some practices are becoming less so. Robert Huckman's research explains why. Open for comment; 0 Comments.
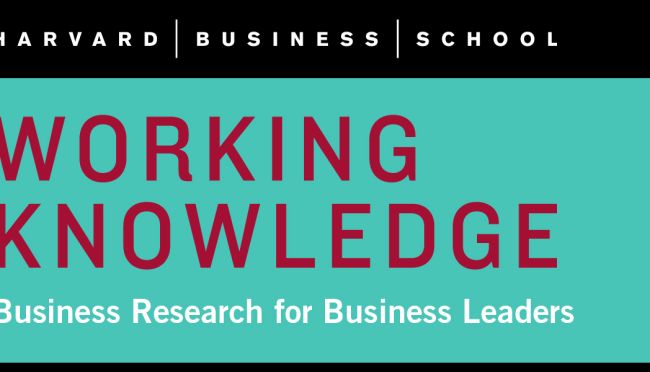
- 11 Nov 2013
- Working Paper Summaries
Increased Speed Equals Increased Wait: The Impact of a Reduction in Emergency Department Ultrasound Order Processing Time
This study of ultrasound test orders in hospital emergency departments (EDs) shows that, paradoxically, increasing capacity in a service setting may not alleviate congestion, and can actually increase it due to increased resource use. Specifically, the study finds that reducing the time it takes to order an ultrasound counter intuitively increases patient throughput time as a result of increased ultrasound use without a corresponding increase in quality of care. Furthermore, the authors show that in the complex, interconnected system or hospitals, changes in resource capacity affects not only the patients who receive the additional resources, but also other patients who share the resource, in this case, radiology. These results highlight how demand can be influenced by capacity due to behavioral responses to changes in resource availability, and that this change in demand has far reaching effects on multiple types of patients. Interestingly, the increased ultrasound ordering capacity was achieved by removing what appeared to be a "wasteful" step in the process. However, the results suggest that the step may not have been wasteful as it reduced inefficient ultrasound orders. In healthcare, these results are very important as they provide an explanation for some of the ever-increasing costs: reducing congestion through increased capacity results in even more congestion due to higher resource use. Overall, the study suggests an operations-based solution of increasing the cost/difficulty of ordering discretionary but sometimes low-efficacy treatments to address the rise in healthcare spending. Therefore, to improve hospital performance it could be optimal to put into place "inefficiencies" to become more efficient. Key concepts include: A process improvement can inadvertently cause an increase in demand for a service as well as associated shared resources, which results in congestion, counter intuitively decreasing overall system performance. While individual patients and physicians may benefit from the reduced processing time, there can be unintended consequences for overall system performance. Closed for comment; 0 Comments.
- 25 Jan 2013
Why a Harvard Finance Instructor Went to the Kumbh Mela
Every 12 years, millions of Hindu pilgrims travel to the Indian city of Allahabad for the Kumbh Mela, the largest public gathering in the world. In this first-person account, Senior Lecturer John Macomber shares his first impressions and explains what he's doing there. Closed for comment; 0 Comments.
- 07 Aug 2012
Off and Running: Professors Comment on Olympics
The most difficult challenge at The Olympics is the behind-the-scenes efforts to actually get them up and running. Is it worth it? HBS professors Stephen A. Greyser, John D. Macomber, and John T. Gourville offer insights into the business behind the games. Open for comment; 0 Comments.
- 19 Oct 2010
The Impact of Supply Learning on Customer Demand: Model and Estimation Methodology
"Supply learning" is the process by which customers predict a company's ability to fulfill product orders in the future using information about how well the company fulfilled orders in the past. A new paper investigates how and whether a customer's assumptions about future supplier performance will affect the likelihood that the customer will order from that supplier in the future. Research, based on data from apparel manufacturer Hugo Boss, was conducted by Nathan Craig and Ananth Raman of Harvard Business School, and Nicole DeHoratius of the University of Portland. Key concepts include: Two key measures of supplier performance include "consistency", which is the likelihood that a company will continue to keep items in stock and meet demand, and "recovery", which is the likelihood that a company will deliver on time in spite of past stock-outs. Improvements in consistency and recovery are associated with increases in orders from retail customers. Increasing the level of service may lead to an increase in orders, even when the service level is already nearly perfect. Closed for comment; 0 Comments.
- 19 Jul 2010
How Mercadona Fixes Retail’s ’Last 10 Yards’ Problem
Spanish supermarket chain Mercadona offers aggressive pricing, yet high-touch customer service and above-average employee wages. What's its secret? The operations between loading dock and the customer's hands, says HBS professor Zeynep Ton. Key concepts include: The last 10 yards of the supply chain lies between the store's loading dock and the customer's hands. Poor operational decisions create unnecessary complications that lead to quality problems and lower labor productivity and, in general, make life hard for retail employees. Adopting Mercadona's approach requires a long-term view and a leader with a strong backbone. Closed for comment; 0 Comments.
- 12 Jul 2010
Rocket Science Retailing: A Practical Guide
How can retailers make the most of cutting-edge developments and emerging technologies? Book excerpt plus Q&A with HBS professor Ananth Raman, coauthor with Wharton professor Marshall Fisher of The New Science of Retailing: How Analytics Are Transforming the Supply Chain and Improving Performance. Key concepts include: Retailers can better identify and exploit hidden opportunities in the data they generate. Integrating new analytics within retail organizations is not easy. Raman outlines the typical barriers and a path to overcome them. Incentives must be aligned within organizations and in the supply chain. The first step is to identify the behavior you want to induce. To attract and retain the best employees, successful retailers empower them in specific ways. Closed for comment; 0 Comments.
- 05 Jul 2006
The Motion Picture Industry: Critical Issues in Practice, Current Research & New Research Directions
This paper reviews research and trends in three key areas of movie making: production, distribution, and exhibition. In the production process, the authors recommend risk management and portfolio management for studios, and explore talent compensation issues. Distribution trends show that box-office performance will increasingly depend on a small number of blockbusters, advertising spending will rise (but will cross different types of media), and the timing of releases (and DVDs) will become a bigger issue. As for exhibiting movies, trends show that more sophisticated exhibitors will emerge, contractual changes between distributor and exhibitors will change, and strategies for tickets prices may be reevaluated. Key concepts include: Business tools such as quantitative and qualitative research and market research should be applied to the decision-making process at earlier stages of development. Technological developments will continue to have unknown effects on every stage of the movie-making value chain (production, distribution, exhibition, consumption). Closed for comment; 0 Comments.
- 20 Dec 2004
How an Order Views Your Company
HBS Professors Benson Shapiro and Kash Rangan bring us up to date on their pioneering research that helped ignite today’s intense focus on the customer. The key? Know your order cycle management. Closed for comment; 0 Comments.
- 15 Apr 2002
In the Virtual Dressing Room Returns Are A Real Problem
That little red number looked smashing onscreen, but the puce caftan the delivery guy brought is just one more casualty of the online shopping battle. HBS professor Jan Hammond researches what the textile and apparel industries can do to curtail returns. Closed for comment; 0 Comments.
- 26 Nov 2001
How Toyota Turns Workers Into Problem Solvers
Toyota's reputation for sustaining high product quality is legendary. But the company's methods are not secret. So why can't other carmakers match Toyota's track record? HBS professor Steven Spear says it's all about problem solving. Closed for comment; 0 Comments.
- 19 Nov 2001
Wrapping Your Alliances In a World Wide Web
HBS professor Andrew McAfee researches how the Internet affects manufacturing and productivity and how business can team up to get the most out of technology. Closed for comment; 0 Comments.
- 22 Jan 2001
Control Your Inventory in a World of Lean Retailing
"Manufacturers of consumer goods are in the hot seat these days," the authors of this Harvard Business Review article remind readers. But there is no need to surrender to escalating costs of inventories. In this excerpt, they describe one new way to help lower inventory costs. Closed for comment; 0 Comments.
- 12 Oct 1999
Decoding the DNA of the Toyota Production System
How can one production operation be both rigidly scripted and enormously flexible? In this summary of an article from the Harvard Business Review, HBS Professors H. Kent Bowen and Steven Spear disclose the secret to Toyota's production success. The company's operations can be seen as a continuous series of controlled experiments: whenever Toyota defines a specification, it is establishing a hypothesis that is then tested through action. The workers, who have internalized this scientific-method approach, are stimulated to respond to problems as they appear; using data from the strictly defined experiment, they are able to adapt fluidly to changing circumstances. Closed for comment; 0 Comments.
Rapid Response: Inside the Retailing Revolution
A simple bar code scan at your local department store today launches a whirlwind of action: data is transmitted about the color, the size, and the style of the item to forecasters and production planners; distributors and suppliers are informed of the demand and the possible need to restock. All in the blink of an electronic eye. It wasn’t always this way, though. HBS Professor Janice Hammond has focused her recent research on the transformation of the apparel and textile industries from the classic, limited model to the new lean inventories and flexible manufacturing capabilities. Closed for comment; 0 Comments.

- SUGGESTED TOPICS
- The Magazine
- Newsletters
- Managing Yourself
- Managing Teams
- Work-life Balance
- The Big Idea
- Data & Visuals
- Reading Lists
- Case Selections
- HBR Learning
- Topic Feeds
- Account Settings
- Email Preferences
It’s Time to Rethink Your Global Logistics
- Willy C. Shih
- Adrien Foucault

The pandemic has overloaded companies’ usual shipping networks.
The initial supply and demand shocks caused by the pandemic were followed by an import surge as suppliers tried to replenish inventories, which threw normal transportation operations into turmoil. In the United States, this has included a lack of freight-handling capacity at Los Angeles and Long Beach ports, overloaded U.S. intermodal rail networks, and a lack of containers. But alternatives to established logistics networks exist. It’s time for companies to take advantage of them.
Over the last three decades, companies have established wide-ranging global supply chains that have taken advantage of steadily improving scale economies in global logistics. Efficient and reliable ocean and air cargo have linked low-cost manufacturing hubs across Asia with major markets in the United States and Europe. Much of this global sourcing was driven by the cost savings reaped through labor arbitrage, cost savings that were so dramatic that it more than covered the expense associated with moving products across vast distances to markets, or the extra cost of carrying inventory in long pipelines.
- Willy C. Shih is a Baker Foundation Professor of Management Practice at Harvard Business School.
- Adrien Foucault is an MBA student at Harvard Business School and has worked at maritime transport company CMA CGM.
Partner Center
Case Studies in Carbon-Efficient Logistics
Logistics is a leading source of carbon. Nearly 6 percent of the greenhouse gases generated by humans come from the flow of products to consumers. Reducing these emissions takes more than setting goals; it requires clear, measurable initiatives that hit sustainability targets while delivering lower costs and higher service levels.
Sponsored by Environmental Defense Fund (EDF), Dr. Edgar E Blanco Research Director of the Carbon-Efficient Supply Chains Research Project at the MIT Center for Transportation & Logistics, worked alongside three US companies to help them quantify the carbon footprint of some of their logistics initiatives. The goal was to document the projects, and illustrate to other companies that it is possible to reduce cost and become more environmentally friendly.
In this case study we present two Ocean Spray initiatives – distribution network redesign and intermodal shift from road to rail – that in combination led to a 20% reduction in transportation CO2 emissions, while achieving comparable cost savings across the transportation network.
Shifting to Rail – A Collaborative Approach
Ocean Spray, CSX (the rail operator), and fruit shipping companies partnered in order to enable Ocean Spray to ship more products intermodally from its New Jersey distribution center to the company's Florida facility. Prior to the collaboration, these boxcars were returning empty to the Florida region. Shipments that shifted to intermodal generated 65% less emissions while saving over 40% of transportation costs.
Distribution Network Redesign
Ocean Spray added new manufacturing and distribution capabilities in Florida to support the company’s growing customer base. To fully and effectively utilize these additions, Ocean Spray conducted a national network re-design project to determine which customers will receive product from the new location. Ocean Spray projected that over 17% of the total shipments will be served from the new facility.
Read the full Ocean Spray case study here .
In this case study, we analyzed the inbound shipping operations of Caterpillar’s North American large mining truck facility to determine – based on weight, packaging, routing, and scheduling – opportunities to streamline shipping protocols, and thus reduce carbon emissions associated with the supply chain. When combined, the streamlined shipping and packaging efforts could reduce Caterpillar’s overall carbon emissions by 340-730 tonnes of CO2 per year.
Switching Shipment Packaging from Steel to Light-Weight Plastic
At present, Caterpillar uses steel containers to transport parts. Caterpillar has been working for the past four years to phase out these steel containers and replace them with plastic containers, which weigh considerably less.
Analyzing Inbound Shipments to Identify Potential Consolidation
To construct the very large vehicles used in the mining industry, parts are shipped from all over the globe for assembly at Caterpillar’s manufacturing facility in Decatur, Illinois. We analyzed historical shipment data to identify areas where shipments could be consolidated to save fuel and reduce vehicle CO2 emissions. More specifically, we analyzed:
Read the full Caterpillar case study here .
Boise Inc. has launched two initiatives to improve its logistics operations and environmental performance. The Carload Direct Initiative is shifting product transport to rail, and the Three-Tier Pallet Initiative is increasing railcar utilization. Both initiatives have resulted in a combined 62-72% reduction in the company’s CO2 emissions, as well as cost savings on those shipments.
Reducing CO2 Emissions Through Carload Direct
Traditionally, manufacturers use trucks, or a mix of trucks and rail, to transport their products to customers. As trucks produce greater emissions than trains, a logical way to reduce emissions is to minimize the use of trucks and maximize the use of rail. Boise coordinated with its customers to promote rail transport so that product could be sent directly from the manufacturing plant to the customer’s warehouse. The transition from using a mix of truck and rail to exclusively rail eliminated more than 2,600 tons of C02; the equivalent of saving over 264,000 gallons of fuel consumed by road vehicles.
Optimizing Railcar Utilization with Three-Tier Pallets
Prior to this project, railcars were loaded two pallets high, leaving a space from the top of the second pallet to the roof of the railcar, thus under-utilizing the full capacity of the railcar. Boise redesigned its pallets and loading structure by creating a half-pallet, which allowed the company to rethink pallet stacking and maximize shipping capacities for its loads. These redesigns maximized carloads by reducing the number of shipments required to deliver product. Using just 930 railcars in 2011 reduced the company’s C02 emissions by 190 tons, which is equal to the C02 emissions from 21,637 gallons of fuel consumed by road vehicles.
Read the full Boise case study here .
Hear directly from Dr. Edgar Blanco, from MIT CTL, joined by EDF’s Jason Mathers, Ross Corthell from Boise, Kristine Young from Ocean Spray, and Zena Onstott from Caterpillar as they share their insights from these case studies on this webinar .
To find out more about the case studies, contact Dr. Edgar E. Blanco , Research Director, Carbon Efficient Supply Chains Research Project, MIT CTL, and co-founder of the LEAP consortium.
The Carbon Efficient Supply Chains Research Project is addressing three challenges: how to measure the carbon footprint of a supply chain, developing strategies for reducing supply chain carbon emissions, and communicating carbon footprints to consumers and stakeholders. Further information is available here .
The Leaders in Environmental Assessment and Performance (LEAP) consortium is a vehicle for organizations to leverage MIT’s knowledge and resources as well as the lessons learned from corporate environmental efforts. LEAP is a joint initiative between MIT CTL and the MIT Material Systems Laboratory. Further information is available here .
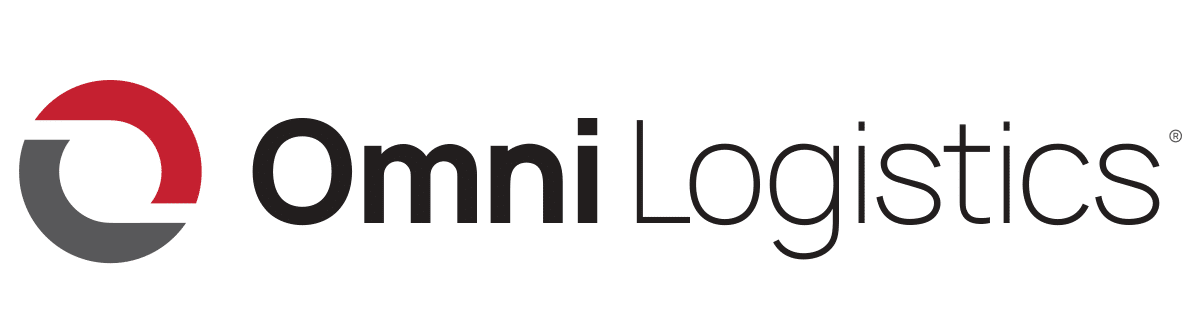
Case Studies
Learn more about how omni logistics can help you..
Read some of our global case studies that give you a first hand look at how Omni Logistics has helped other companies succeed. Expect the best in comprehensive supply chain solutions. We’re ALL IN for our clients.
CASE STUDIES
Critical on-time delivery for international retail stores., increasing performance and reducing fines., regaining visibility to sustain in-stock performance., meeting the needs of a growing security technology company., a unique logistics solution for a unique electronics challenge., supply chain problem solving with life-giving results., are you ready to part of an all in team.
Please enter the following information:
Mach1 is now Omni Logistics
Mach 1 is now Omni Logistics! We look forward to offering a wide range of solutions and capabilities as part of the Omni team. You will now be redirected to the Omni Logistics website.
Schedule a 15 Minute Call
Privacy overview.
Necessary cookies are absolutely essential for the website to function properly. This category only includes cookies that ensures basic functionalities and security features of the website. These cookies do not store any personal information.
Any cookies that may not be particularly necessary for the website to function and is used specifically to collect user personal data via analytics, ads, other embedded contents are termed as non-necessary cookies. It is mandatory to procure user consent prior to running these cookies on your website.
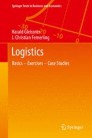
- © 2013
Basics — Exercises — Case Studies
- Harald Gleissner 0 ,
- J. Christian Femerling 1
Berlin School of Economics and Law, Berlin, Germany
You can also search for this author in PubMed Google Scholar
Investa Holding GmbH, Eschborn, Germany
- Offers a broad range of exercises and case studies
- Written by authors with outstanding logistics industry practice and teaching experience
- Suitable complementary case study book is available
- Includes supplementary material: sn.pub/extras
Part of the book series: Springer Texts in Business and Economics (STBE)
1.74m Accesses
24 Citations
12 Altmetric
- Table of contents
About this book
Authors and affiliations, about the authors, bibliographic information.
- Publish with us
Buying options
- Available as EPUB and PDF
- Read on any device
- Instant download
- Own it forever
- Compact, lightweight edition
- Dispatched in 3 to 5 business days
- Free shipping worldwide - see info
- Durable hardcover edition
Tax calculation will be finalised at checkout
Other ways to access
This is a preview of subscription content, log in via an institution to check for access.
Table of contents (14 chapters)
Front matter, introduction.
- Harald Gleissner, J. Christian Femerling
The Principles of Logistics
Logistics systems, logistical infrastructure, transport systems and logistics services, warehousing, handling, and picking systems, inventory, stock and provisioning management, logistics network planning, it in logistics, investment and financing in logistics.
- Logistics Controlling
Business Models and Industry Solutions
Outline solutions to case studies, back matter.
Logistics is the ideal book for Bachelor students of logistics, providing a solid foundation as well as a practical guide. In modular and clear form, it explains key concepts, principles, and practices of logistics. Learning objectives as well as several case studies are integrated into each chapter.
It features chapters on Principles of Logistics; Logistics Systems; Transport Systems and Logistics Services; Warehousing, Handling and Picking Systems; Inventory, Stock and Provisioning Management; Logistics Network Planning; IT in Logistics; and Logistics Controlling.
In addition, the second fully updated German edition has been extended by the chapters Logistics Infrastructure and Investment and Financing in Logistics.
“This book offers, in a very clear and concise manner, access to fundamental management topics of modern logistics. Well-chosen case studies serve to illustrate best practice solutions.”
Professor Peter Klaus, member of Logistics Hall of Fame
”This new textbook facilitates a comprehensive and easy-to-grasp insight into the complex subject area of logistics. The authors have succeeded in presenting a good mix of theoretical foundation and practical application. Due to its clear structure and extensive range of topics, this book is highly suitable not only for students, but also for practitioners.”
Bernhard Simon, Managing Director, DACHSER GmbH & Co. KG
- Supply Chain Management
- Transport Systems
- Warehousing
- Engineering Economics
Harald Gleissner
J. Christian Femerling
Book Title : Logistics
Book Subtitle : Basics — Exercises — Case Studies
Authors : Harald Gleissner, J. Christian Femerling
Series Title : Springer Texts in Business and Economics
DOI : https://doi.org/10.1007/978-3-319-01769-3
Publisher : Springer Cham
eBook Packages : Business and Economics , Business and Management (R0)
Copyright Information : Springer Nature Switzerland AG 2013
Hardcover ISBN : 978-3-319-01768-6 Published: 19 February 2014
Softcover ISBN : 978-3-319-34743-1 Published: 03 September 2016
eBook ISBN : 978-3-319-01769-3 Published: 11 February 2014
Series ISSN : 2192-4333
Series E-ISSN : 2192-4341
Edition Number : 1
Number of Pages : XXI, 311
Number of Illustrations : 156 b/w illustrations
Topics : Operations Management , Engineering Economics, Organization, Logistics, Marketing , Organization
Policies and ethics
- Find a journal
- Track your research
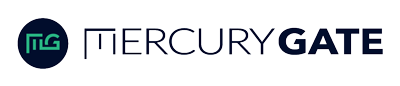
Heart of Efficiency: 3 Logistics Case Studies that Show the Love
- February 13, 2024
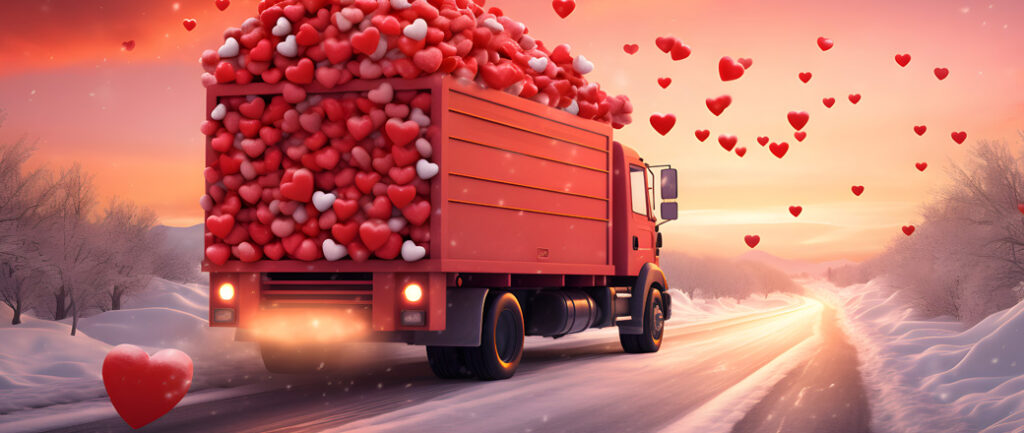
This article dives into three compelling logistics case studies showcasing how MercuryGate enhances transportation management for three of our clients.
As we unwrap these stories, you’ll discover success stories conveying how logistics technology creates harmony in your complex supply chain.
Logistics Case Study #1: Using Analytics to Drive Operational Efficiency
- Significant Improvement in Timestamp Accuracy : Transitioning to MercuryGate’s platform increased timestamp accuracy from 60% to 89%.
- Increased On-Time Delivery Metrics : MercuryGate’s data-driven insights allowed more precise analysis of driver performance and operational procedures, leading to more efficient and accurate service delivery.
- Elevated Customer Service Ratings : MercuryGate’s solutions significantly increased customer service ratings — especially for on-time delivery.
Our SaaS video case study, available here , exemplifies how data-driven insights can lead to significant operational improvements and heightened customer experiences.
Logistics Case Study #2: Super Users Achieve TMS Eminence & Partner for Success
- Embracing Future-Ready Technology : By aligning with MercuryGate, this customer effectively evaluates and integrates various vendors, such as third-party payers or transportation tracking software, fostering a more comprehensive logistics solution.
- Combating Fraud with Advanced Logistics Technology : MercuryGate worked with this logistics provider to develop dynamic logic and validation workflows, ensuring carriers meet stringent criteria and safeguarding customer interests.
- Innovative Collaboration and Forward Thinking : The partnership’s focus on innovation and anticipating future needs led to significant advancements. By looking forward and not just relying on past builds, we push the boundaries of logistics technology.
This logistics case study is one of continuous improvement and adaptation. It illustrates how a deep understanding of each partner’s capabilities and needs can lead to remarkable success. Our customer’s transformation underlines the importance of embracing logistics technology to stay ahead in the dynamic world of transportation management. Watch the complete case study here .
Logistics Case Study #3: Navigating Intermodal Transportation
- Integration with Third-Party Providers : MercuryGate’s platform facilitated integration, including rates and schedules, bid creation to execution, and tracking and tracing equipment on the rails, enhancing overall operational efficiency.
- Streamlined Billing Capabilities : MercuryGate’s SaaS logistics technology platform solves billing complexities associated with boxcar movements, demonstrating its versatility and adaptability to stringent intermodal billing requirements.
This collaboration is comparable to finding the perfect Valentine, where the “matchmaking” of technology with logistics needs dramatically increased efficiency. Watch the video case study here .
Calculate your potential Saving While Using an enterprise TMS
Mercurygate’s impact: a story of innovation and partnership.
In conclusion, to commemorate Valentine’s Day, let’s celebrate the partnerships, innovations, and technological advancements that transform logistics. If these stories of transformation inspire you, imagine what MercuryGate can do for your business. Schedule a demo and take the first step toward becoming our next success story in logistics innovation.
And add one more delighted customer to our list of logistics case studies to find out how we help Facil improve transportation visibility. Download it today and find out how much this MercuryGate user loves our solutions.
Subscribe To The MercuryGate Blog
Related resources, baltimore bridge disaster: supply chain impacts & solutions.
Achieving Supply Chain Sustainability Success
Maximizing Efficiency in Carrier Claims Management
Import Compliance Deep Dive: Tackling Tough Questions in Global Trade
More Resources
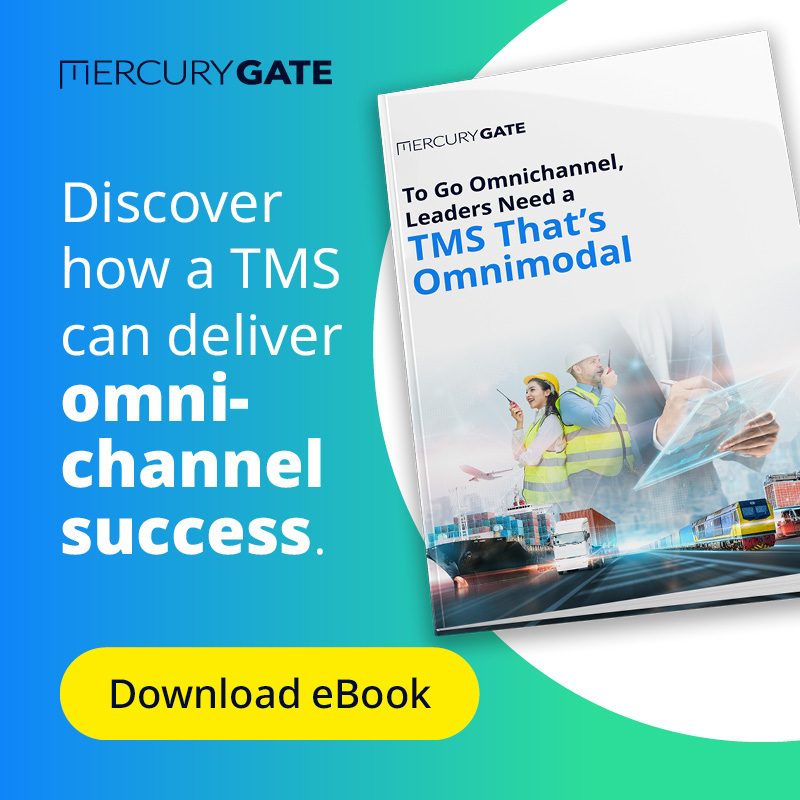
Find out why our logistics technology users feel the love
Case Studies: How AI Consulting Has Helped Logistics Companies Succeed
According to McKinsey , the successful implementation of AI has helped businesses improve logistics costs by 15%, inventory levels by 35%, and service levels by 65%. AI consulting for logistics businesses brings a number of benefits, but RTS Labs has taken it a step further by delivering tangible results through its tailored AI consulting services.
In this blog, we’ll explore real case studies showcasing how RTS Labs has empowered logistics companies to succeed through the strategic application of AI. From optimizing supply chain operations to enhancing last-mile delivery efficiency, these case studies offer valuable insights into the transformative power of AI consulting in the logistics industry.
Case Study 1: Streamlining Supply Chain Operations
Client: swift logistics.
Problem Swift Logistics, a leading transportation and logistics company, faced challenges in optimizing its supply chain operations. The company struggled with inefficient route planning, resulting in increased fuel costs, longer delivery times, and reduced overall productivity. Additionally, manual inventory management processes led to inaccuracies and stockouts, impacting customer satisfaction.
Solution RTS Labs conducted a comprehensive analysis of Swift Logistics’ supply chain processes and implemented AI-driven solutions to address the identified challenges. Leveraging predictive analytics and machine learning algorithms, RTS Labs developed a dynamic route optimization system that factored in real-time traffic data, delivery constraints, and customer preferences. Additionally, AI-powered inventory management systems were deployed to forecast demand accurately and optimize stock levels in warehouses and distribution centers.
- Reduced Fuel Consumption by 20%: Streamlining delivery routes led to a significant 20% decrease in fuel usage, cutting operational costs and promoting environmental sustainability.
- Shortened Delivery Times by 30%: Optimal route planning resulted in a notable 30% improvement in delivery efficiency, enhancing customer satisfaction and maintaining a competitive edge.
- Minimize Stock Outs by 40%: Accurate demand forecasting reduced stockouts by 40%, ensuring shelves were consistently stocked, fulfilling orders promptly, and preventing lost sales opportunities.
- Achieved Cost Savings and Improved Profitability: These optimizations led to substantial cost savings and improved profitability, validating the transformative impact of AI on Swift Logistics’ operations.
Testimonial “ Teaming up with RTS Labs has completely transformed how we run our supply chain. Thanks to their AI-powered solutions, our route planning is more efficient than ever, and we’re nailing inventory management with pinpoint accuracy. Now, our deliveries are quicker, our shelves are stocked just right, and our customers couldn’t be happier. RTS Labs gets us – they know the ins and outs of logistics, and their customized solutions are game-changers. ” – John Kavinsky, CEO of Swift Logistics
Case Study 2: Enhancing Last-Mile Delivery Efficiency
Client: express fulfillment.
Problem Express Fulfillment, a fast-growing e-commerce fulfillment provider, struggled to meet the increasing demand for same-day and next-day deliveries. The company faced challenges in optimizing last-mile delivery routes, resulting in missed delivery windows, higher transportation costs, and customer dissatisfaction. Additionally, manual order processing and scheduling processes led to inefficiencies and delays in order fulfillment.
Solution RTS Labs collaborated with Express Fulfillment to implement AI-driven solutions to enhance last-mile delivery efficiency. Using advanced predictive analytics and route optimization algorithms, RTS Labs developed a real-time delivery scheduling system that optimized delivery routes based on factors such as order volume, delivery windows, and traffic conditions. Furthermore, AI-powered chatbots were deployed to automate order processing and customer communication, improving operational efficiency and reducing turnaround times.
- 25% Reduction in Transportation Costs: The real-time delivery scheduling system optimized routes, leading to a 25% decrease in transportation costs.
- 40% Improvement in On-Time Delivery Rates: With optimized routes and better scheduling, on-time delivery rates improved by 40%, enhancing customer satisfaction.
- 50% Reduction in Order Processing Times: AI-powered chatbots streamlined order processing, reducing processing times by 50% and improving operational efficiency.
Testimonial “ Our partnership with RTS Labs has been transformative. Their AI solutions have optimized our delivery operations, resulting in significant cost savings and improved customer satisfaction. With streamlined processes and better scheduling, we’ve been able to meet growing demand and scale our business effectively. ” – Emily Johnson, COO of Express Fulfillment
Case Study 3: Optimizing Warehouse Operations
Client: global logistics solutions.
Problem Global Logistics Solutions, a multinational logistics provider, faced challenges in optimizing warehouse operations to accommodate seasonal peaks and fluctuating demand patterns. Manual picking and packing processes resulted in bottlenecks, leading to longer order fulfillment times and increased labor costs. Inefficient space utilization within warehouses compounded the issue, limiting storage capacity and hindering throughput. Moreover, manual inventory tracking methods led to inaccuracies, stockouts, and delays in replenishment.
Solution To address these challenges, RTS Labs proposed tailored AI-driven solutions. They developed a customized automated picking and packing system, integrating machine learning algorithms and robotics technology to optimize order fulfillment processes. This system dynamically adjusted resource allocation based on real-time demand forecasts and historical data analysis, ensuring efficient utilization of labor and warehouse space. Additionally, AI-powered inventory management systems were implemented for precise inventory tracking and proactive replenishment, enabling seamless operations and reducing stockout occurrences.
- 50% Reduction in Order Fulfillment Time: The automated picking and packing system halved order fulfillment times, enhancing operational efficiency.
- 30% Decrease in Labor Costs: By automating processes and optimizing resource allocation, labor costs decreased by 30%, leading to substantial savings.
- 60% Increase in Storage Capacity Utilization: AI-driven space optimization strategies increased storage capacity utilization by 60%, maximizing warehouse throughput and efficiency.
Testimonial “ Our journey with RTS Labs has been nothing short of transformative for our warehouse operations. Their tailored AI solutions have completely revolutionized how we work, bringing remarkable improvements in efficiency and accuracy. Thanks to their expertise and commitment, we’ve not only met but exceeded our goals, delighting our customers while driving down costs. RTS Labs has truly been a game-changer for us. ” – Sarah Parker, Director of Operations at Global Logistics Solutions.
Case Study 4: Compliance Monitoring and Risk Management
Client: secure logistics inc..
Problem Secure Logistics Inc., specializing in secure transportation services, faced a pressing challenge in ensuring compliance with stringent regulatory standards while effectively managing operational risks. The company struggled with manual compliance monitoring processes, leading to inconsistencies in adherence to security protocols and an increased likelihood of security breaches. With the transportation sector’s ever-evolving regulatory landscape, Secure Logistics Inc. needed a robust solution to automate compliance monitoring and mitigate potential risks to maintain the integrity of its operations.
Solution Recognizing the critical need for a tailored solution, RTS Labs developed an advanced AI-driven compliance monitoring and risk management system for Secure Logistics Inc. Leveraging sophisticated machine learning algorithms, the system ingested data from security checkpoints, vehicle inspections, and incident reports in real time. This data was then analyzed to identify patterns, anomalies, and potential compliance issues swiftly and accurately.
- Improved Compliance by 30%: The AI-driven system enabled Secure Logistics Inc. to achieve a 30% improvement in compliance with regulatory standards by automating the monitoring of security protocols and ensuring consistent adherence across all operations.
- Reduced Security Incidents by 25%: By proactively identifying and mitigating potential risks in real-time, Secure Logistics Inc. experienced a significant reduction in the frequency of security incidents, enhancing the safety and security of its transportation services.
- Enhanced Operational Security: The implementation of RTS Labs’ AI solution not only bolstered compliance and mitigated risks but also contributed to overall operational security.
Testimonial “ RTS Labs’ AI solution transformed our security operations. With automated compliance checks and risk management, we’ve improved regulatory adherence and minimized security incidents. Their expertise has strengthened our operations, ensuring we deliver secure transportation services effectively. ” – Mark Johnson, Security Director at Secure Logistics Inc.
Case Study 5: Optimizing Cold Chain Logistics for Pharmaceutical Shipments
Client: frostcargo pharmaceuticals.
Problem FrostCargo Pharmaceuticals, a specialized logistics provider for temperature-sensitive pharmaceutical products, faced a unique challenge in maintaining the integrity of its cold chain during transportation. With stringent temperature requirements and regulatory compliance standards, they struggled to ensure consistent temperature control across their supply chain, leading to occasional product spoilage and compliance issues.
Solution RTS Labs collaborated closely with FrostCargo Pharmaceuticals to develop a tailored AI-driven solution to optimize cold chain logistics. Leveraging advanced temperature monitoring sensors and predictive analytics, RTS Labs designed a real-time temperature control system that continuously monitored temperature variations during transit. The system utilized machine learning algorithms to analyze historical temperature data, predict potential deviations, and trigger proactive interventions to maintain optimal storage conditions.
- 99% Temperature Compliance: The AI-driven temperature control system achieved a remarkable 99% compliance rate, ensuring pharmaceutical products remained within the specified temperature range throughout transit.
- Elimination of Product Spoilage: By addressing temperature fluctuations, FrostCargo Pharmaceuticals eliminated product spoilage incidents, preserving the quality and efficacy of pharmaceutical shipments.
- Enhanced Regulatory Compliance: The implementation of the AI solution enabled FrostCargo Pharmaceuticals to meet and exceed regulatory compliance standards, enhancing trust and credibility among clients and regulatory authorities.
Testimonials “ Their AI solution completely transformed how we manage our cold chain logistics. Now, with real-time temperature monitoring and predictive analytics, we’ve waved goodbye to worrying about spoiled products. Thanks to their deep understanding of pharmaceutical logistics, our service quality has skyrocketed, putting us ahead of the pack in the market. ” – Emily Chen, Logistics Manager at FrostCargo Pharmaceuticals
Case Study 6: Improving Cross-Border Freight Management
Client: globaltrans freight solutions.
Problem GlobalTrans Freight Solutions, a company specializing in cross-border freight transportation, faced significant challenges in managing customs clearance processes efficiently. The complexity of international regulations and the manual nature of paperwork led to delays at border crossings, increased transit times, and heightened operational costs. Additionally, inconsistent communication with customs authorities and lack of real-time visibility into shipment status further compounded the problem.
Solution RTS Labs collaborated with GlobalTrans Freight Solutions to develop an AI-driven customs clearance and border management system. Leveraging machine learning algorithms and natural language processing (NLP), the system automated the classification of goods, streamlined documentation processes, and facilitated communication with customs authorities. Furthermore, real-time tracking and monitoring capabilities were integrated to provide end-to-end visibility into the status of shipments, enabling proactive management of border crossings.
- 50% Reduction in Custom Clearance Duration: Cut customs clearance times in half, leading to faster transit of goods across borders.
- 30% Reduction in Transit Time: Reduced transit times by 30%, enabling quicker deliveries and improved customer satisfaction.
- 40% Reduction in Operational Costs: Achieved a substantial 40% reduction in operational costs associated with border delays and penalties, resulting in significant cost savings.
Testimonial “ Thanks to the AI consulting team at RTS Labs, we’ve been able to tackle our toughest logistics challenges with confidence. Their expertise and dedication have truly made a difference in our operations. We couldn’t have achieved our goals without their invaluable support and guidance. ” – Sarah Rodriguez, CEO of GlobalTrans Freight Solutions
Wrapping Up
These case studies offer a clear picture of the transformative power of AI consulting in the logistics sector. They underline the vital role played by RTS Labs in helping companies navigate complex challenges and achieve remarkable improvements in their operations.
The message is crystal clear: AI consulting is no longer a luxury but a necessity for logistics businesses striving to stay competitive in today’s fast-paced world. With RTS Labs at the helm, companies can harness the full potential of AI to streamline processes, enhance efficiency, and drive success.
Ready to revolutionize your logistics operations with AI consulting? Let RTS Labs be your trusted partner in driving efficiency, optimizing processes, and unlocking new possibilities.
Reach out to us if you'd like to be featured on our podcast.
Transform your last mile with personalized, actionable insights in just seven minutes. Take our Assessment >
Meet us in-person or virtually at these events, locus exclusive webinar series, upcoming roundtable discussions, locus in the news, watch our videos, infographics.
- Case Studies
- Whitepapers
Partner With Us to Solve Your Logistics Problems
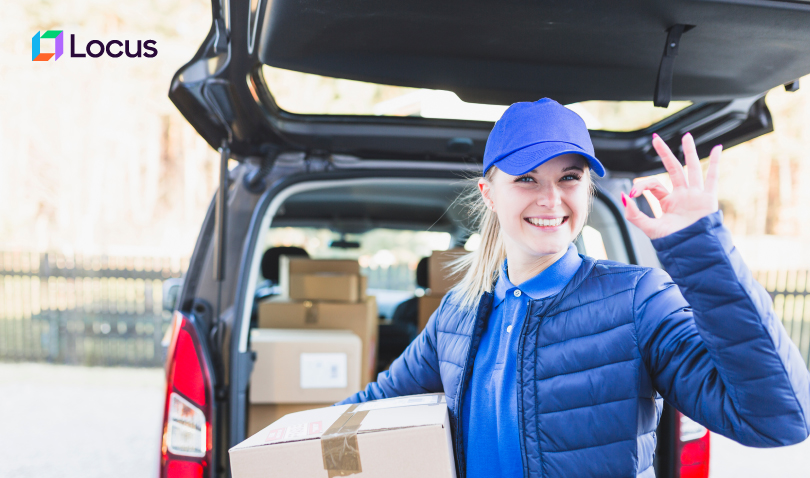
How to eliminate human dependency in Retail/FMCG Sales Beat Planning
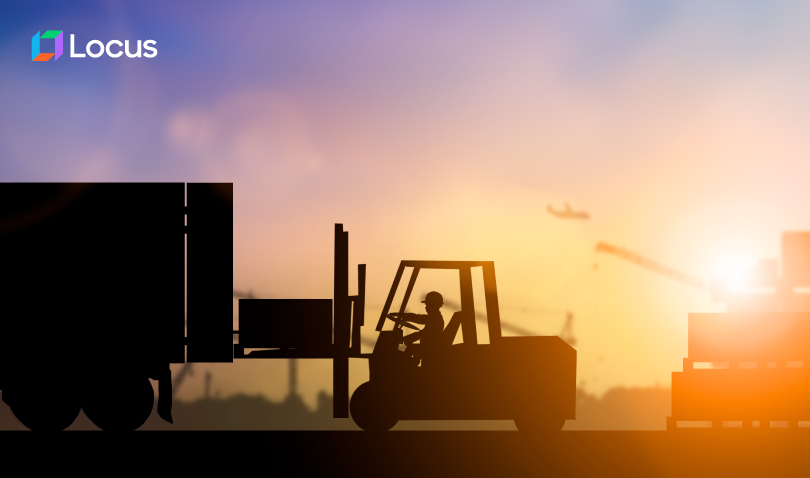
Streamlining the FMCG Distribution Supply Chain with a Comprehensive TMS Solution
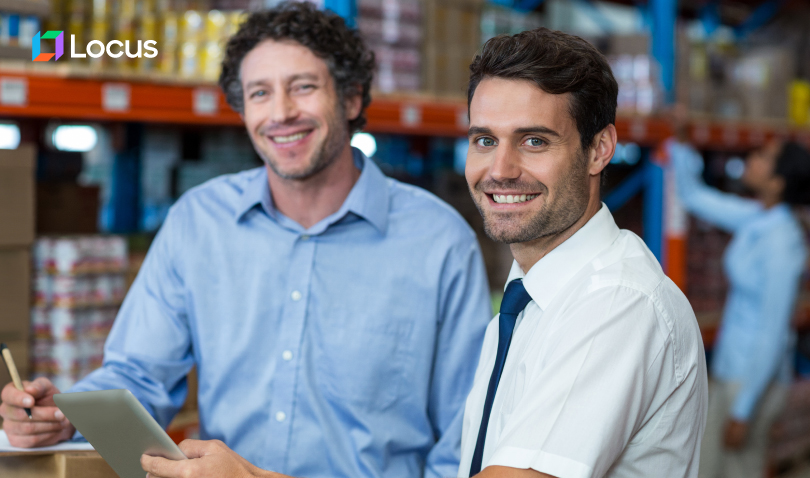
How can FMCG players utilize sales reps more effectively
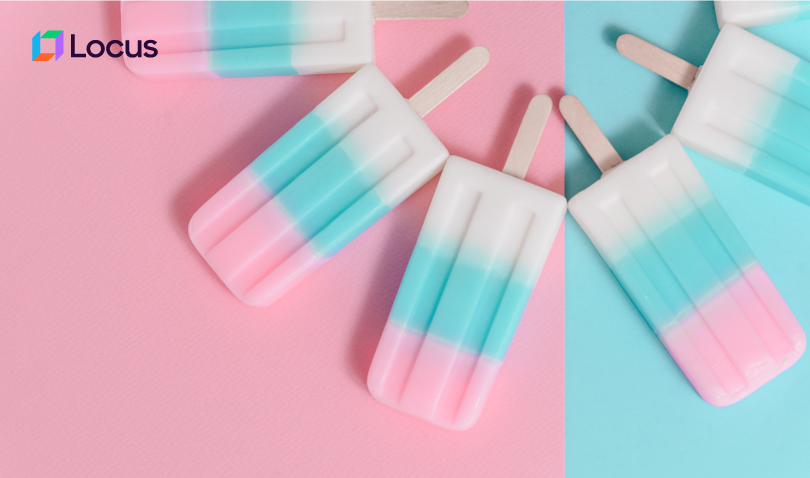
How to optimize various legs of the FMCG supply chain?
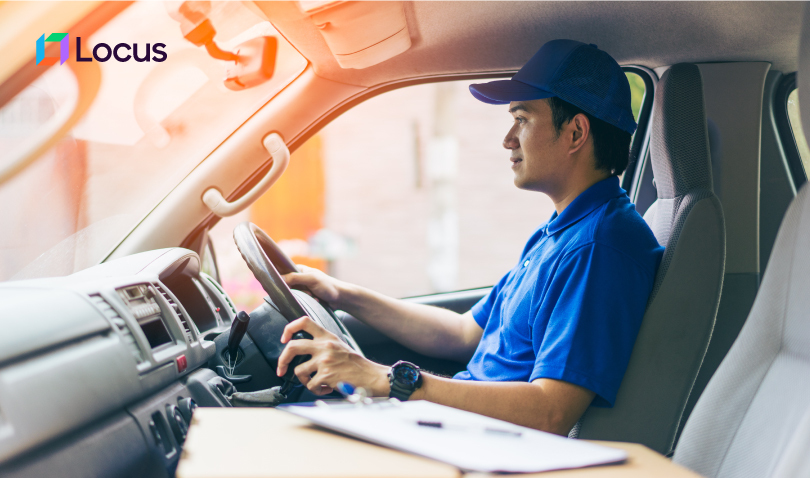
How Locus Enhanced End-to-End Operational Efficiency for this Indonesian Manufacturing Giant
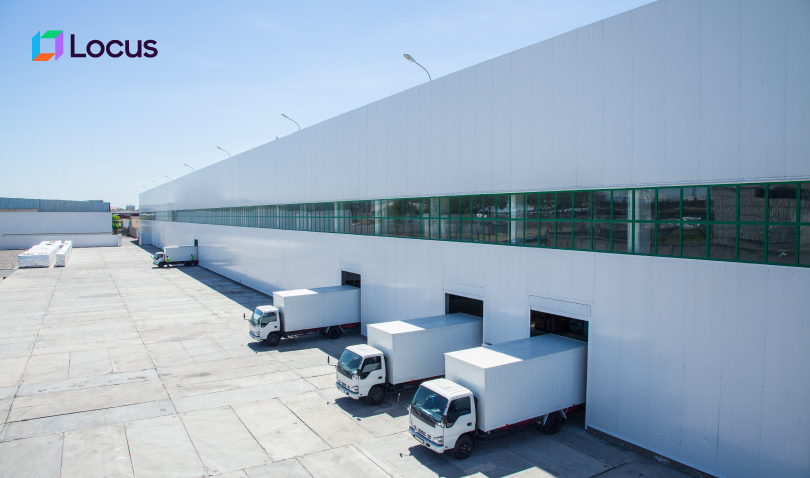
Optimizing Indonesia’s Growing Cold Chain Businesses
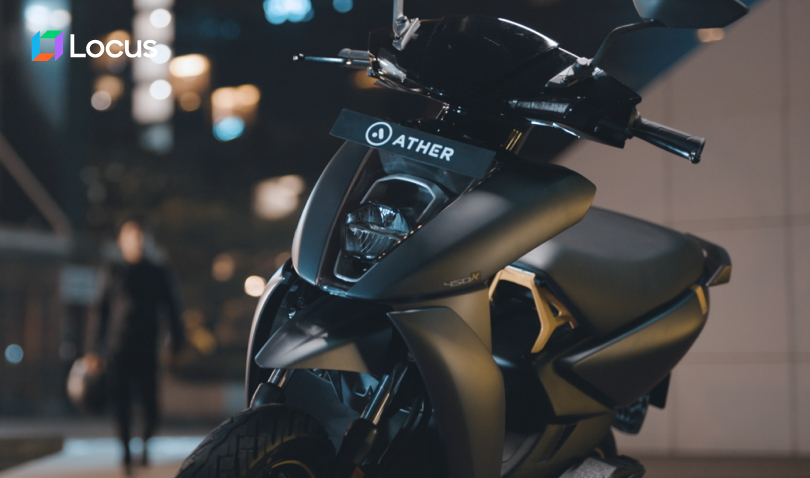
Enabling unparalleled on-site customer service at scale
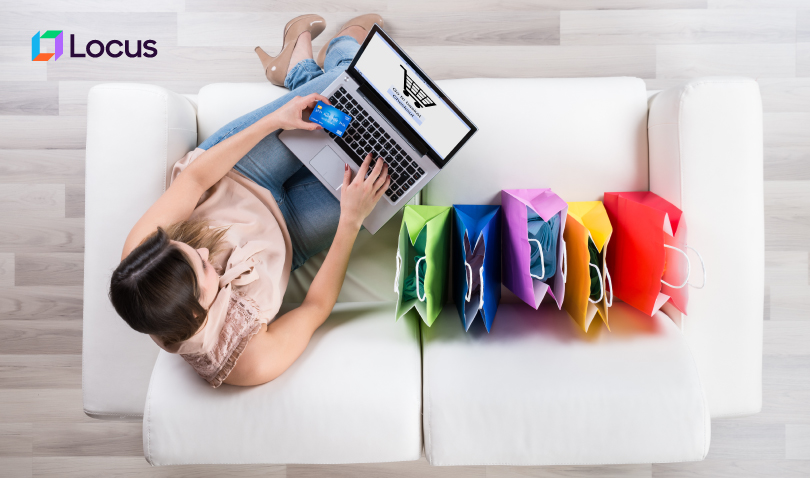
How to increase operational efficiencies in E-commerce
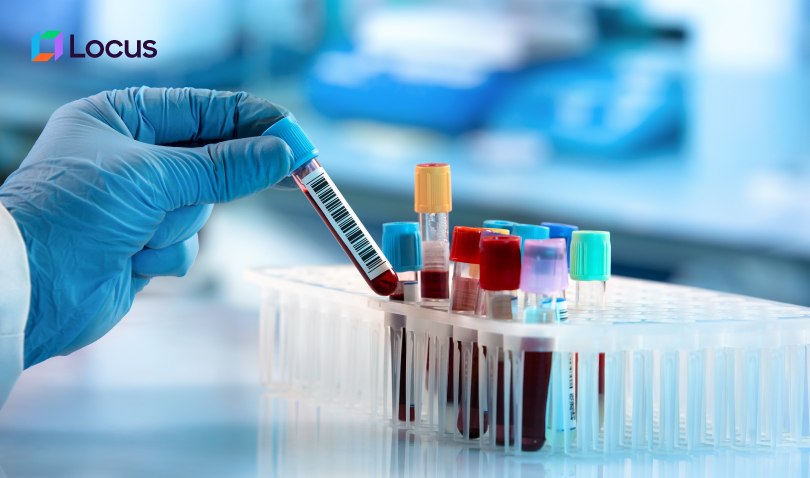
How to increase visibility for on-demand pharma companies?
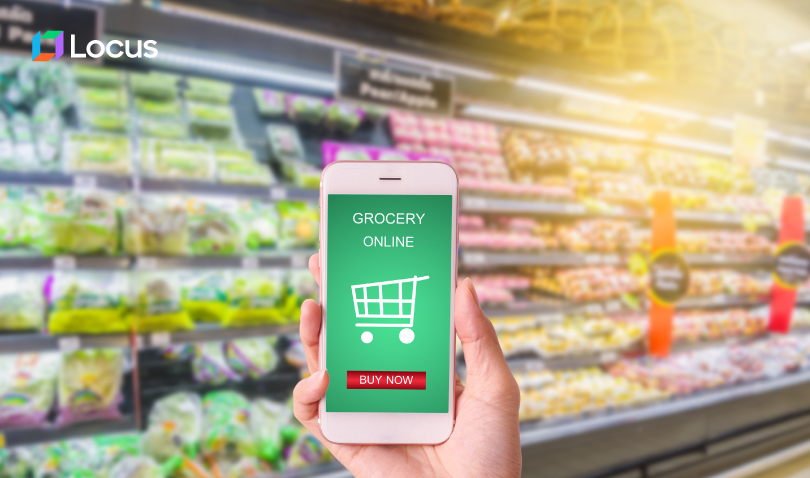
Enabling customer satisfaction through smart logistics in E-grocery
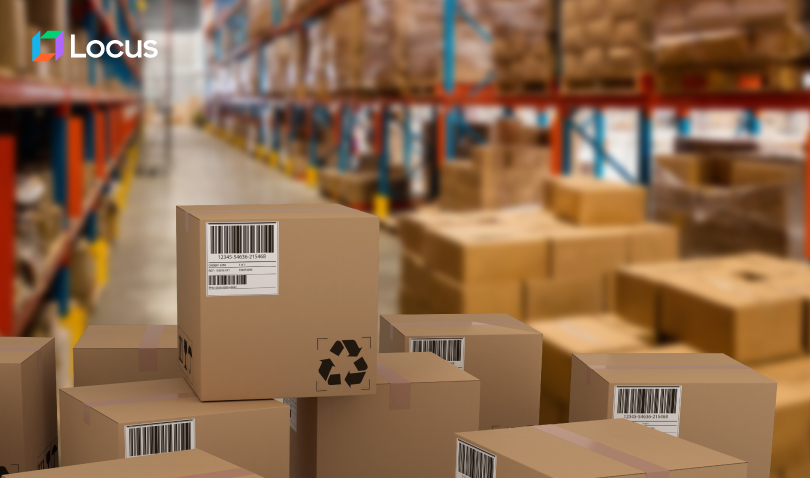
How to reduce manual shipment processes for courier services?
Delve into the world of logistics here.
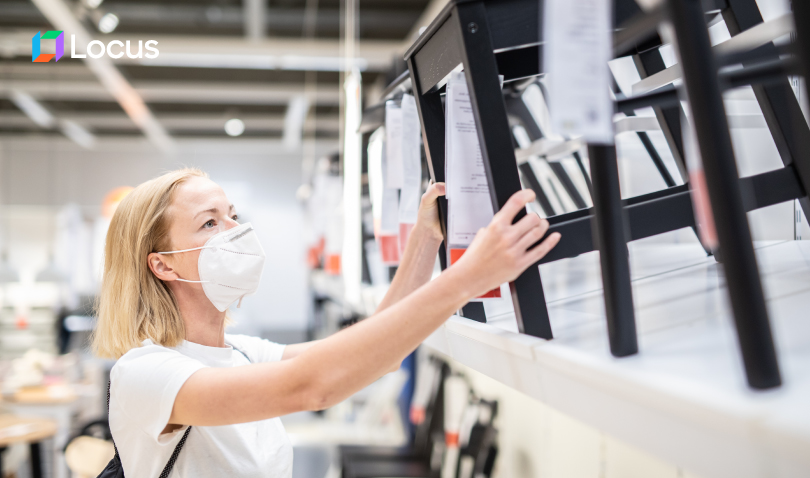
The Logistics of Furniture Retail
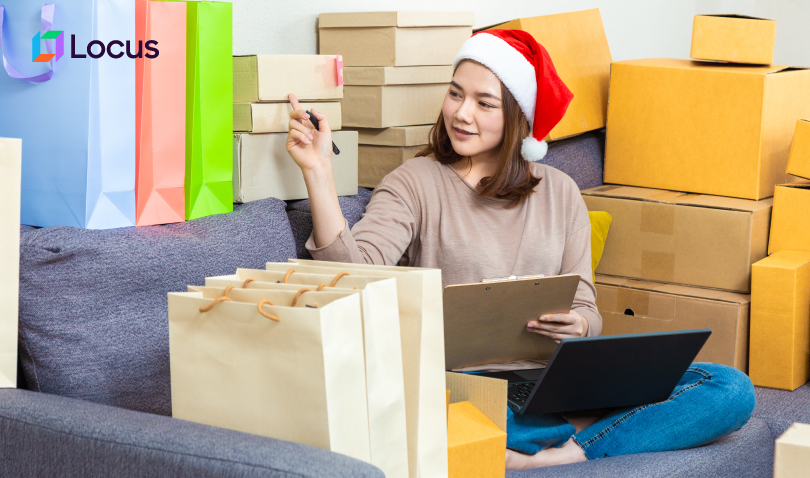
Holiday Season Trends That Will Shape the Retail Supply Chain Industry
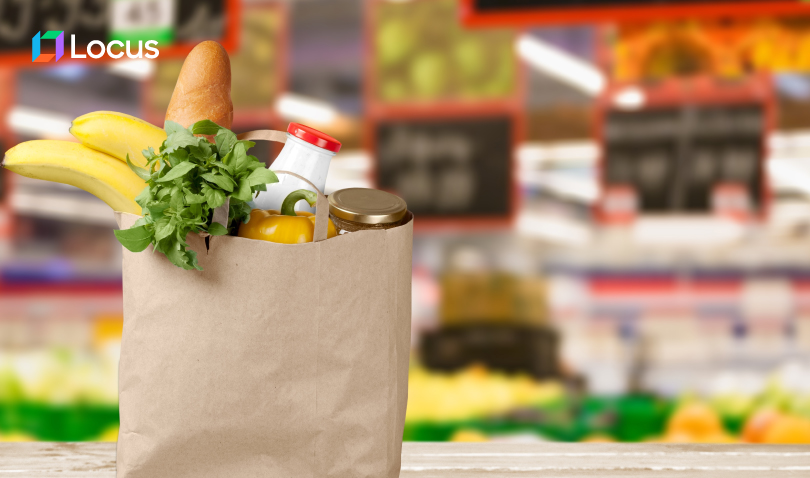
A Look at the Future of Grocery Retail in North America
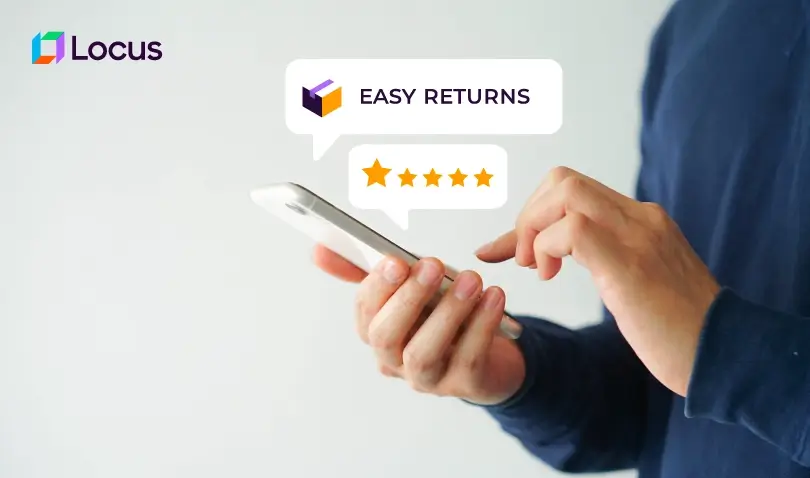
A Comprehensive Guide to Effective Returns Management
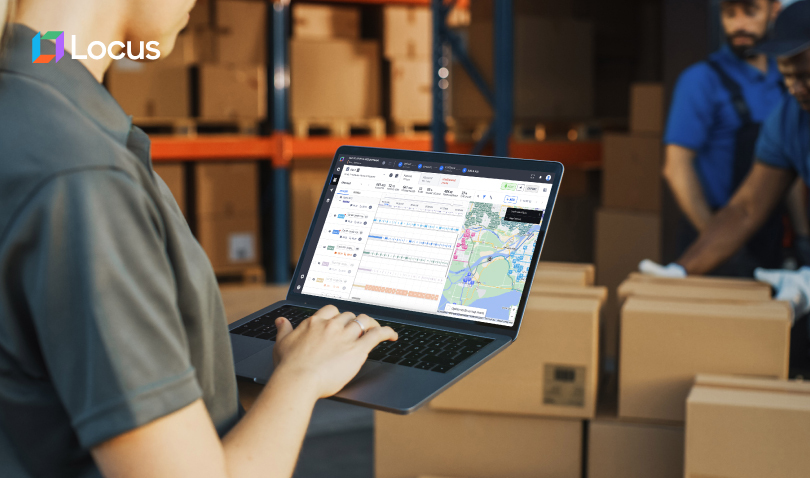
Buying vs. Building Logistics Software: How to Choose?
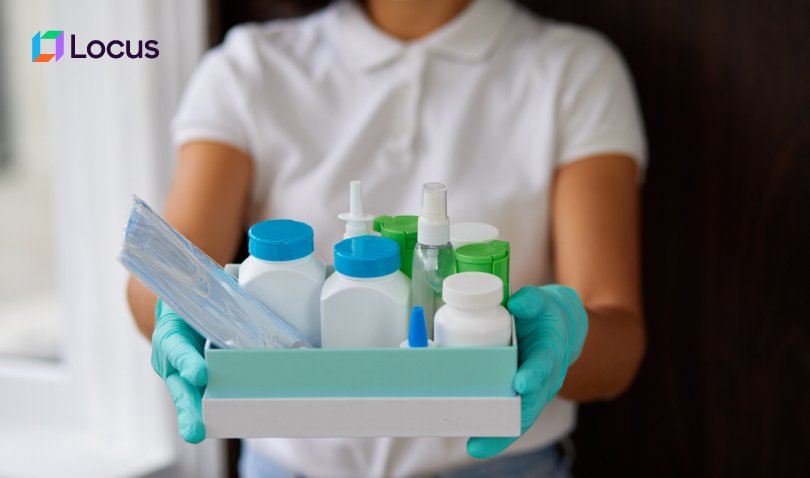
Evolution of Healthcare Supply Chain and the Importance of Logistics Tech
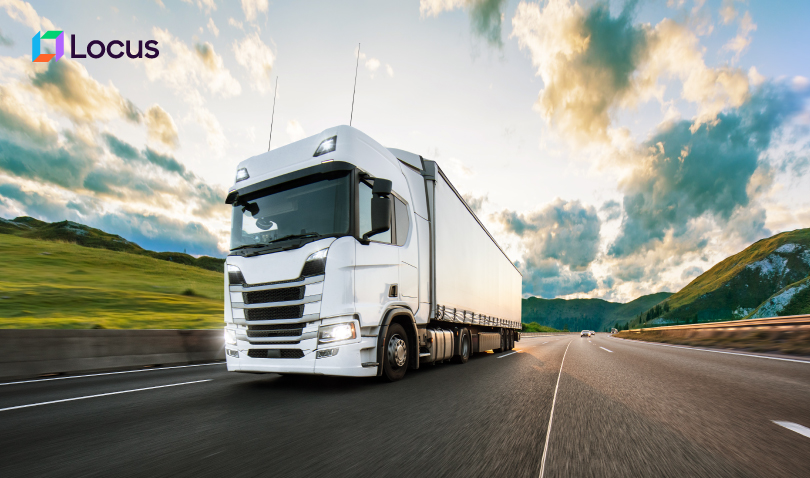
The Future is Now: Why Transportation Management Systems are Indispensable to Growth in Logistics
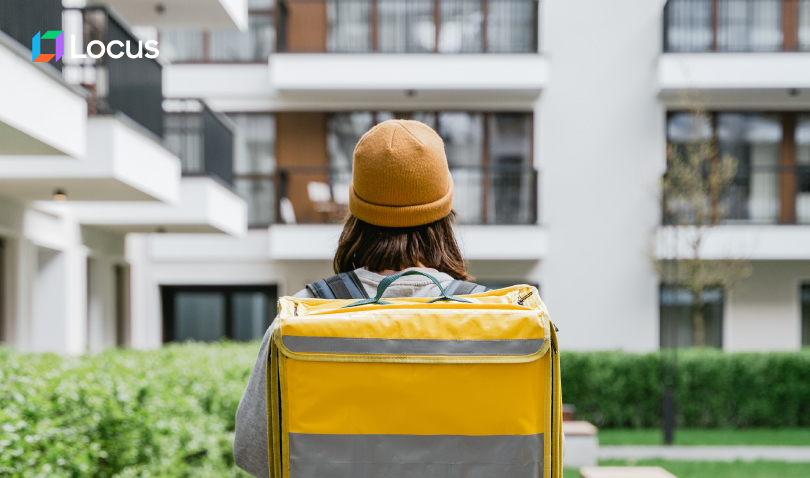
Last-mile Delivery: Finding the Right Balance
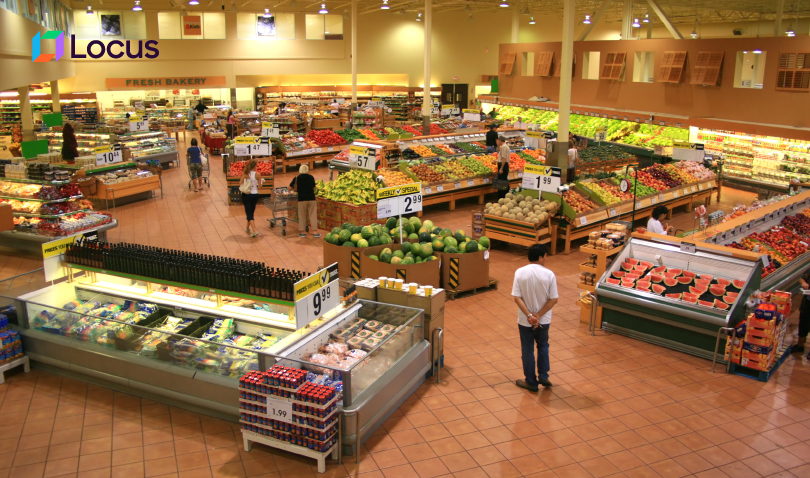
Hope Comes In the Form of AI for Big-Box Stores
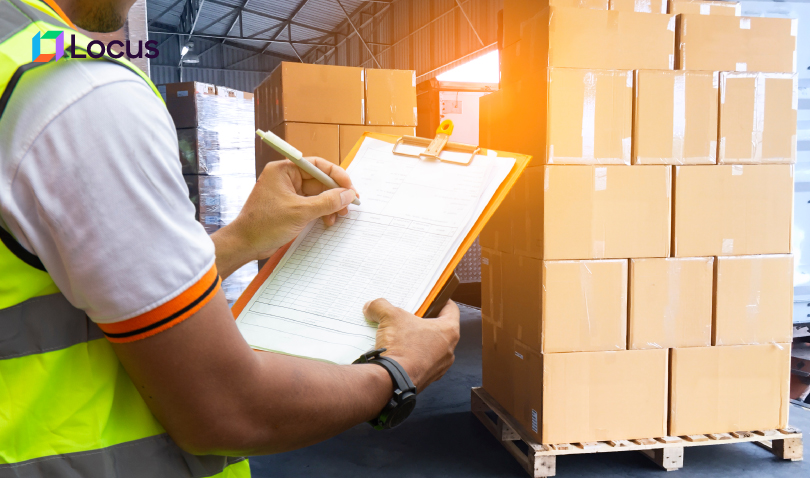
Transform your wholesale distribution supply chain with logistics tech
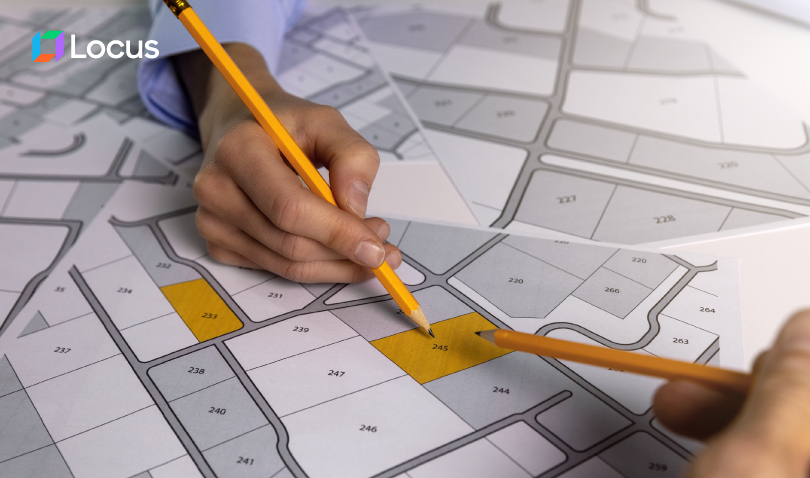
How to Optimize Your Business Using Territory Planning
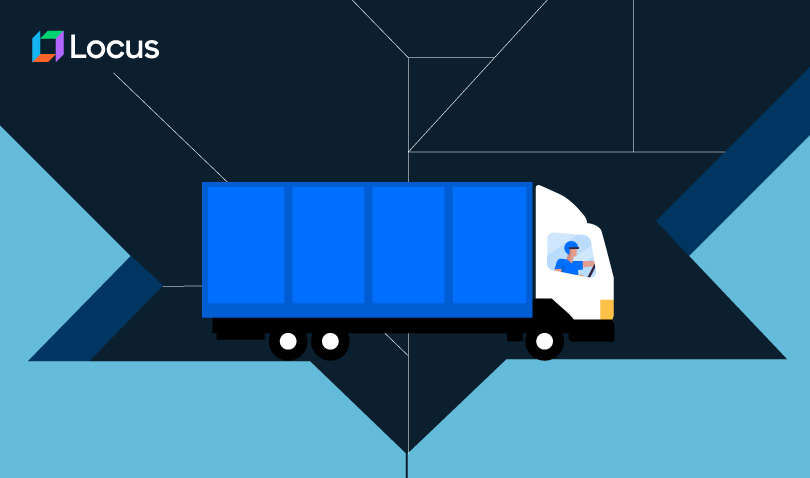
Optimize Cannabis Delivery Operations
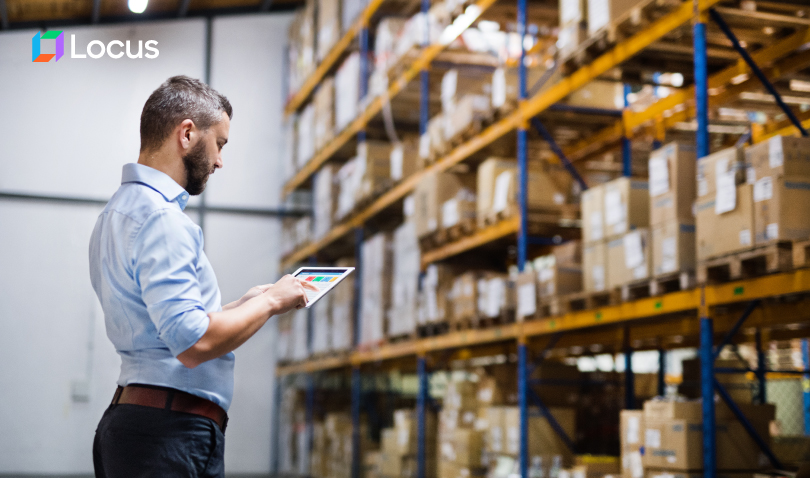
Digital Twins — Transforming the Supply Chain
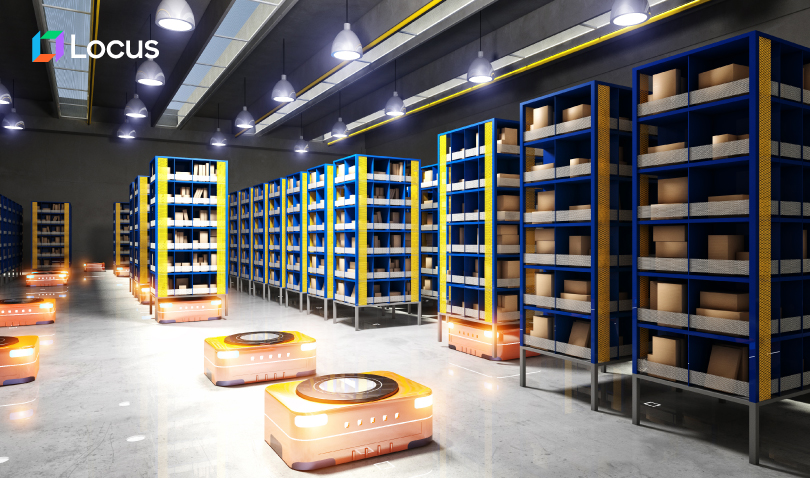
Micro-Fulfillment Centers are Shaping Up the Future of E-Grocery Deliveries
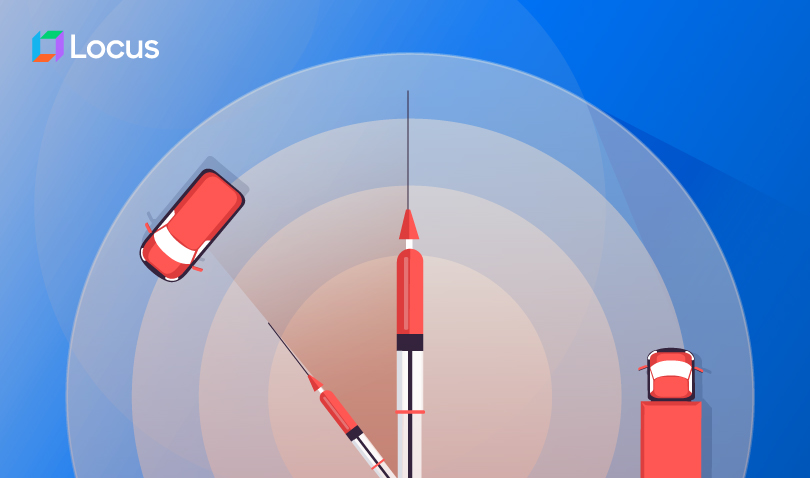
The Final Frontier: Designing an optimal cold chain network to distribute the COVID-19 Vaccine
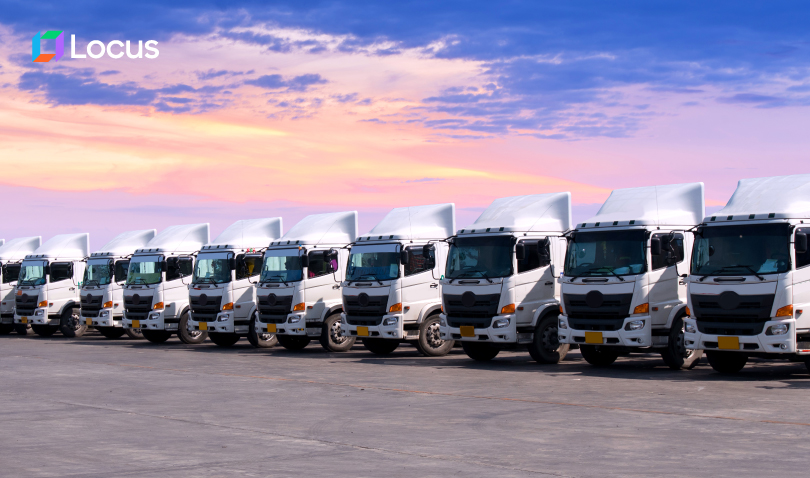
Captive vs Outsourced Fleet: Math behind Transportation and Distribution
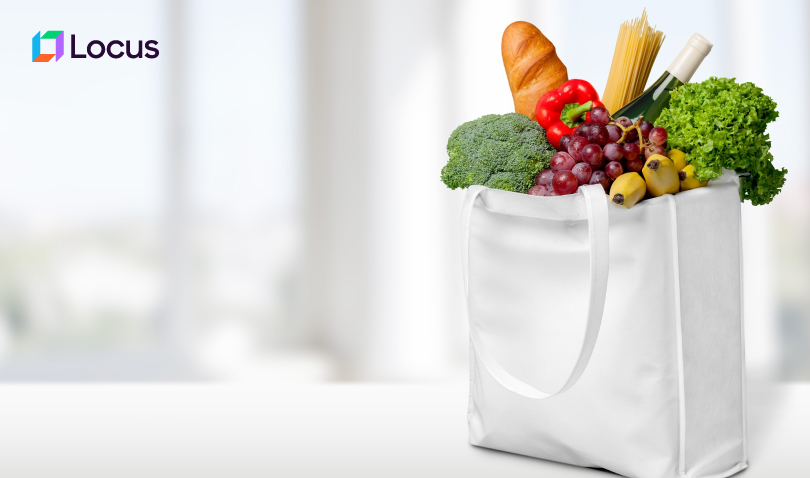
How to Keep the Promise of Same-Day Grocery Delivery Amidst COVID-19
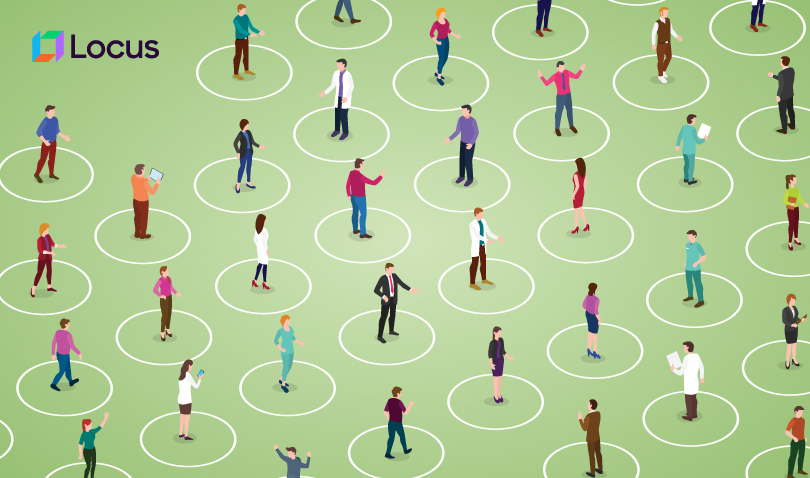
Post-Pandemic Sustainability: What lies ahead of the Supply Chain Industry
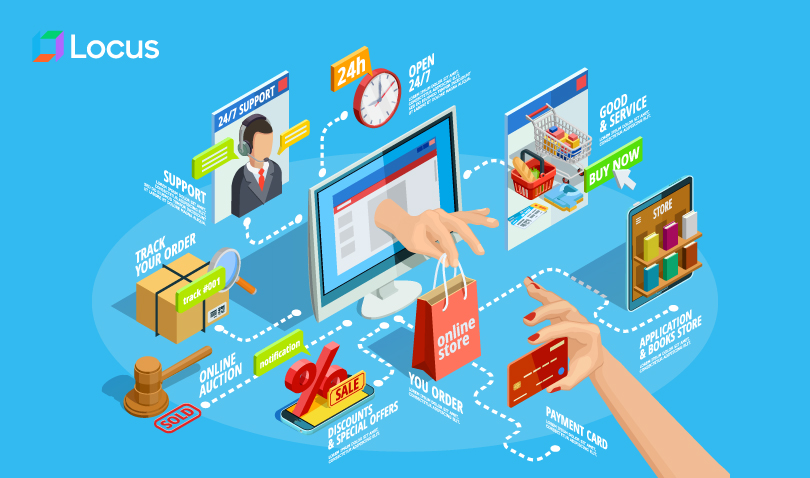
The Role of AI-powered Logistics in E-commerce 4.0
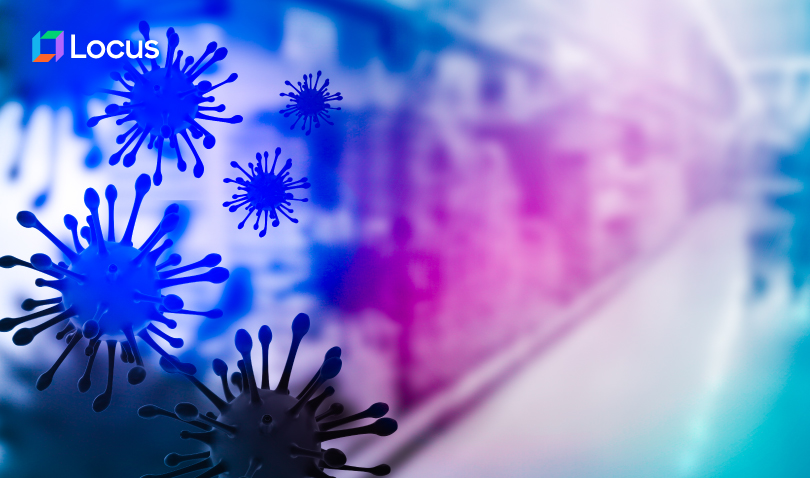
COVID-19 and Supply Chain: Disruptions and Actions
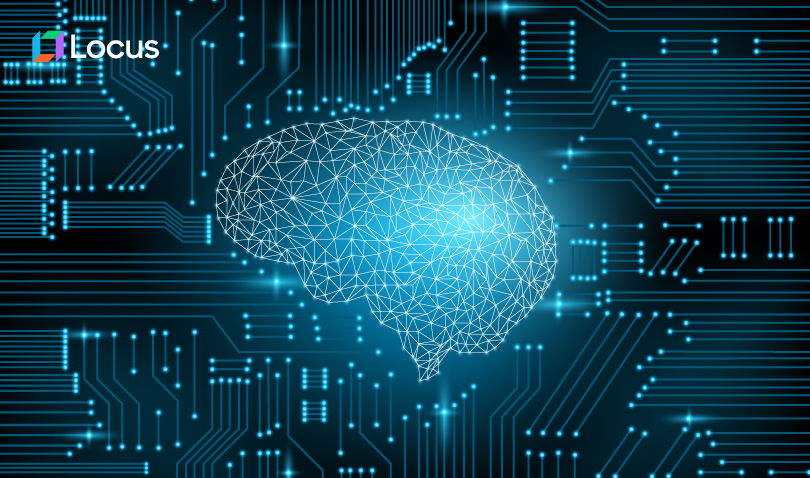
Artificial Intelligence: The solution for supply chain problems in the Engineering Industry
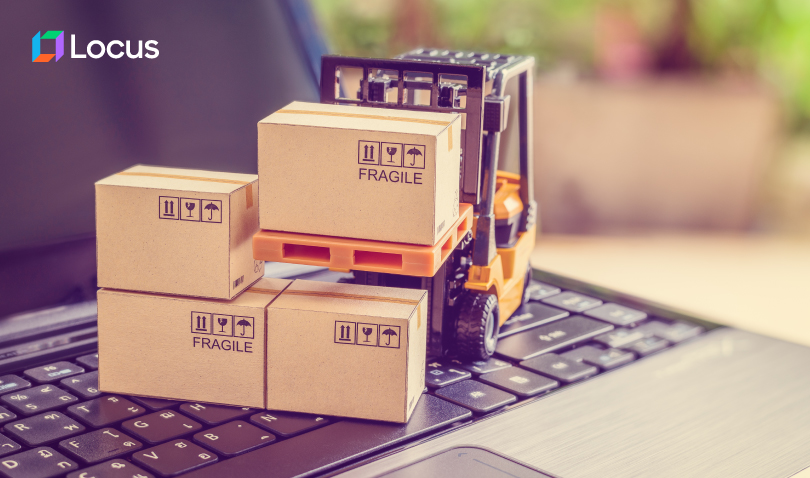
How Locus automated logistics operations for Indonesia’s leading E-commerce player
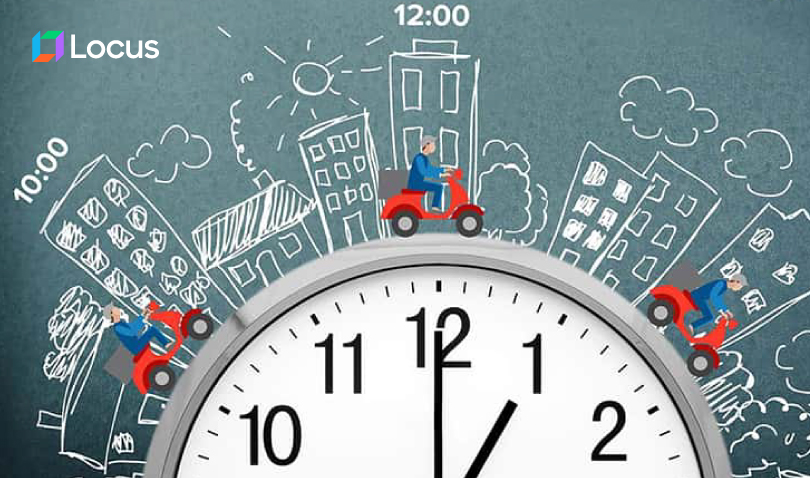
How Locus is managing customer-preferred time windows for its clients
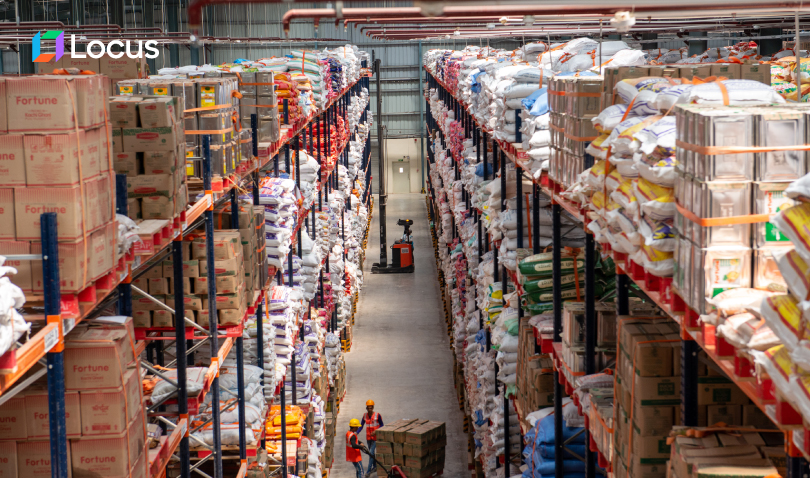
Multi-Echelon SupplyChain Inventory Optimization – A mathematical perspective
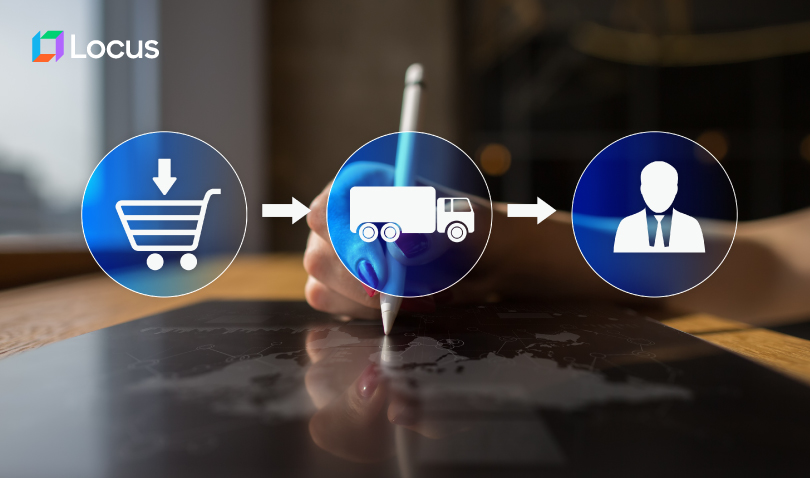
How Locus filled the gaps in the supply chain of Southeast Asia’s largest e-commerce player
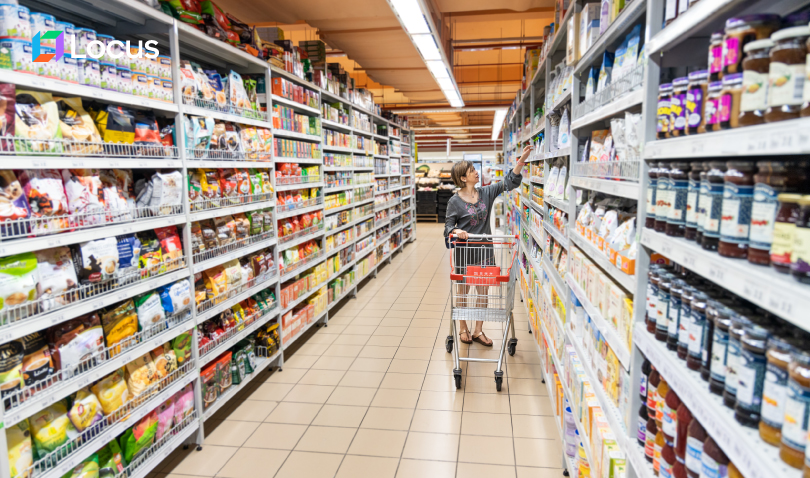
FMCG Insight Report II
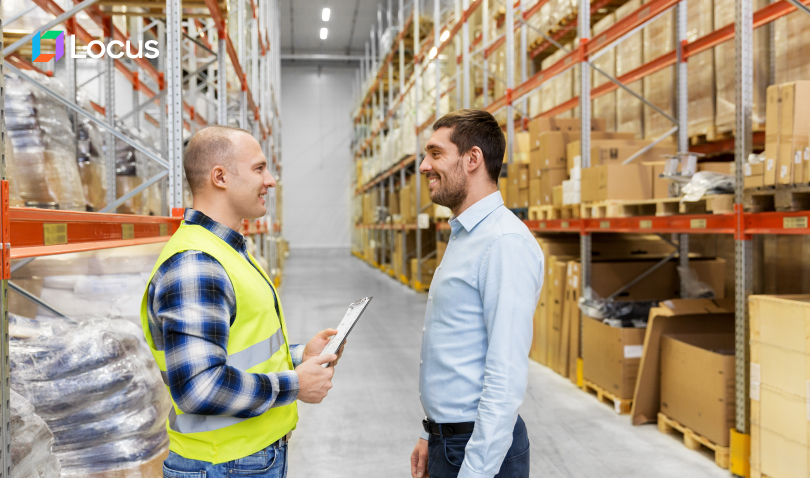
The Future Of Sales Transformation : Dynamic PJP
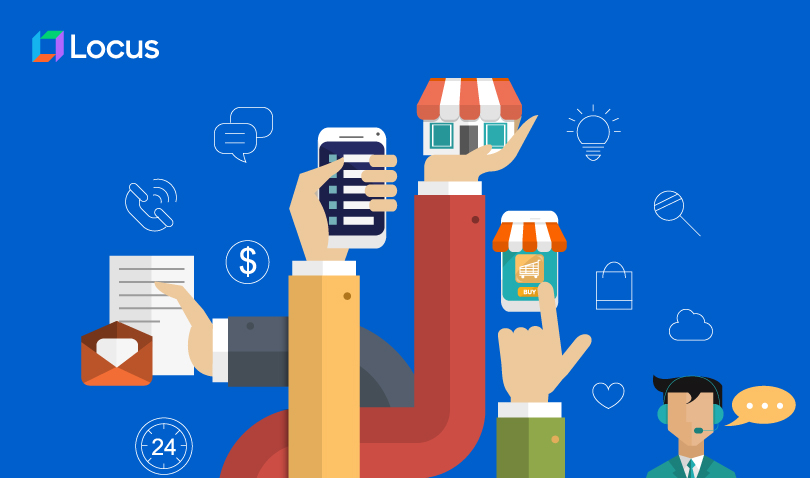
Locus’ Guide To Omnichannel Fulfilment
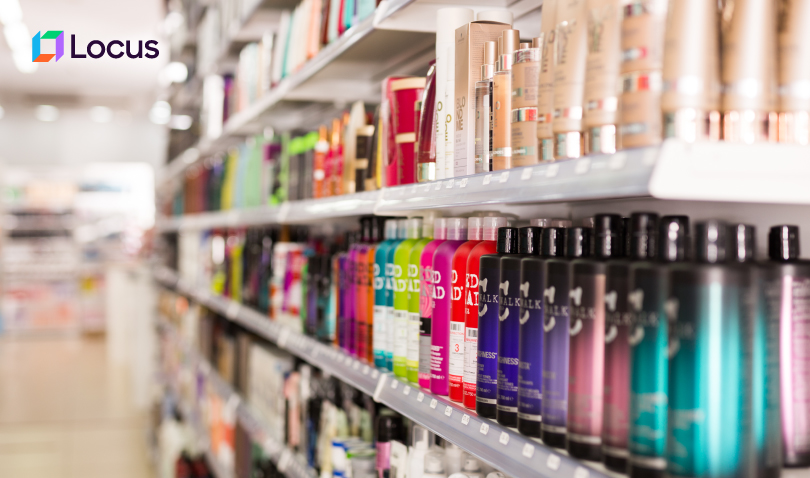
FMCG Sales Beat - Insight Report
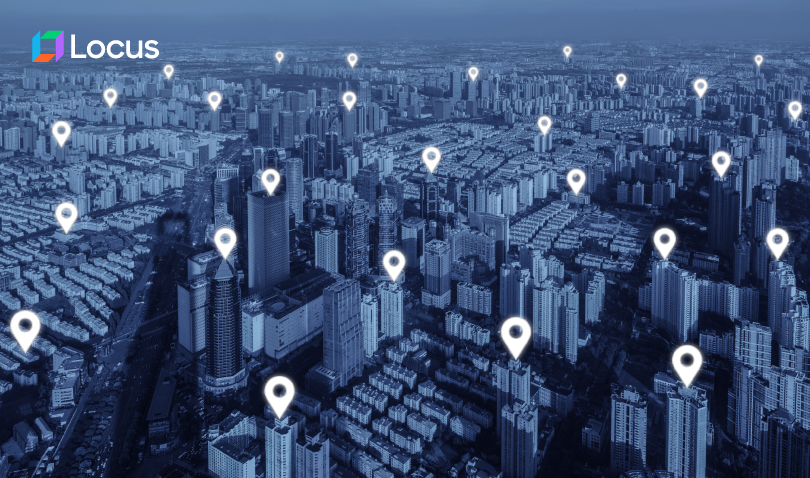
Why Businesses need Route Optimization?
Long reads on logistics and technology.
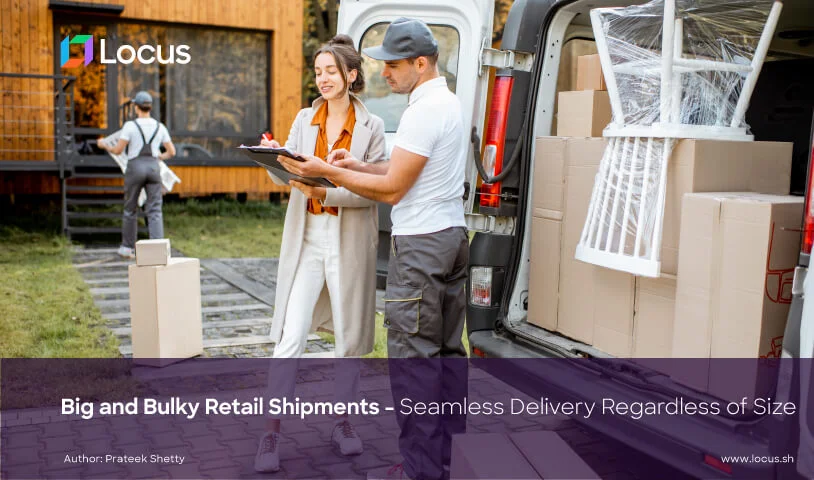
Big and Bulky Retail Shipments - Seamless Delivery Regardless of Size
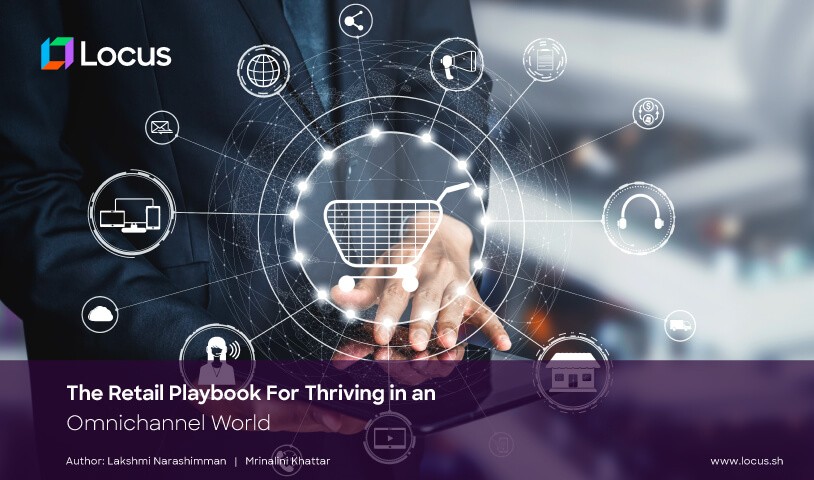
The Retail Playbook For Thriving in an Omnichannel World
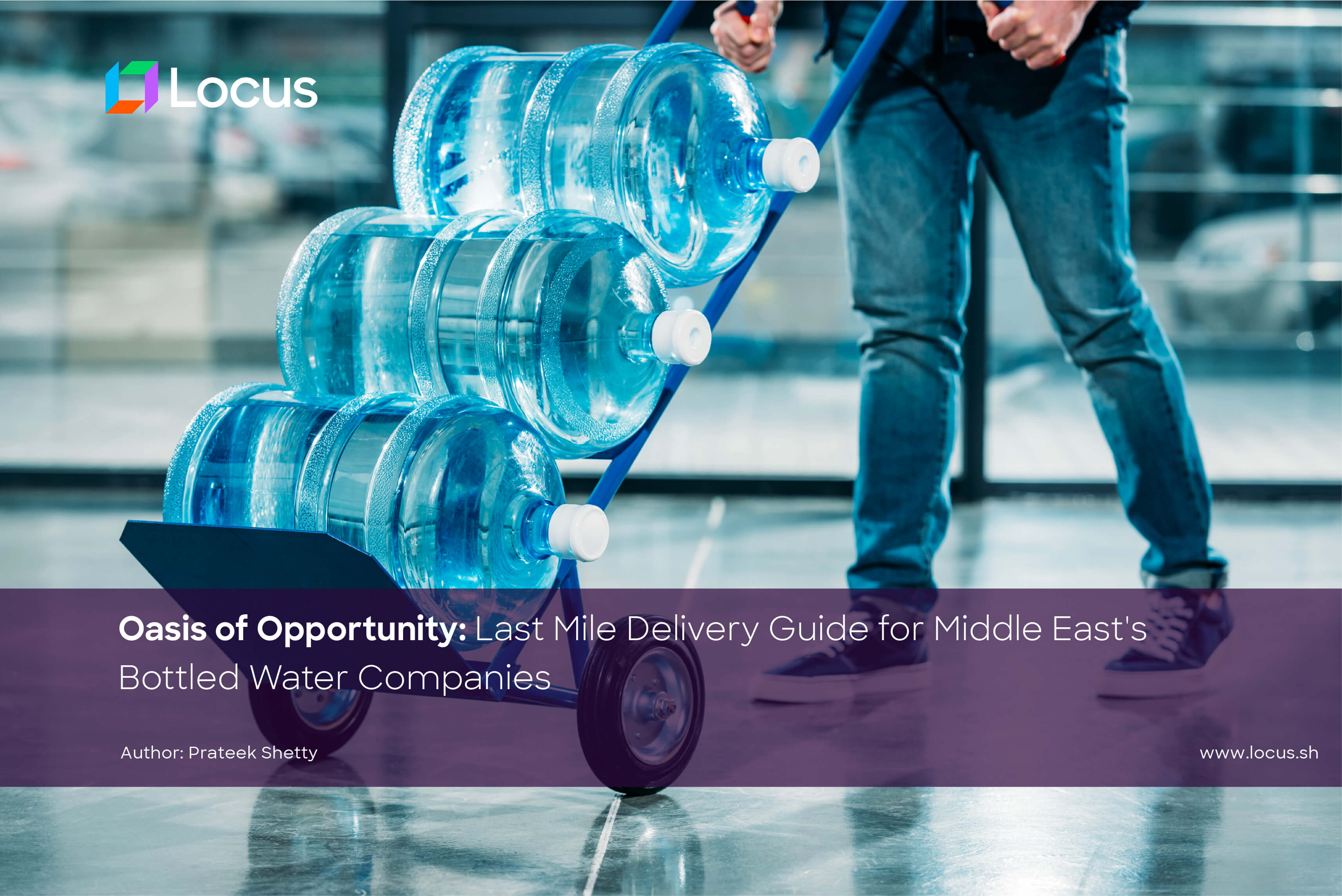
Middle East Bottled Water Manufacturers: Last-mile Delivery Strategies
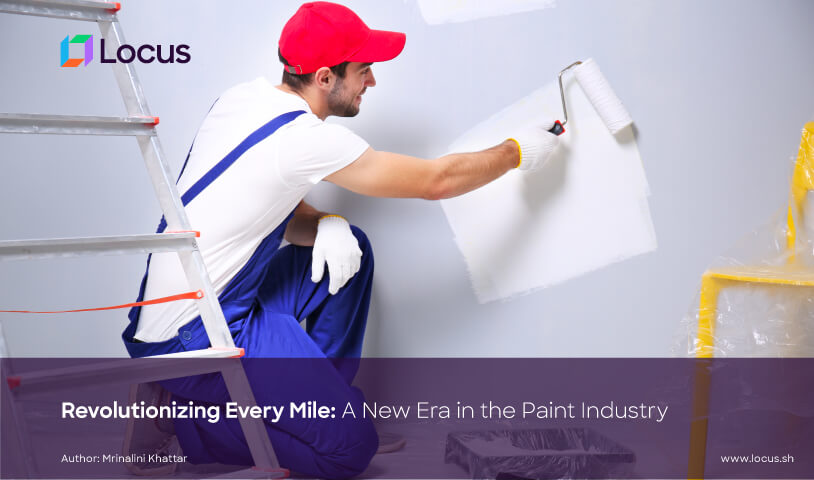
Revolutionizing Every Mile: A New Era in the Paint Industry
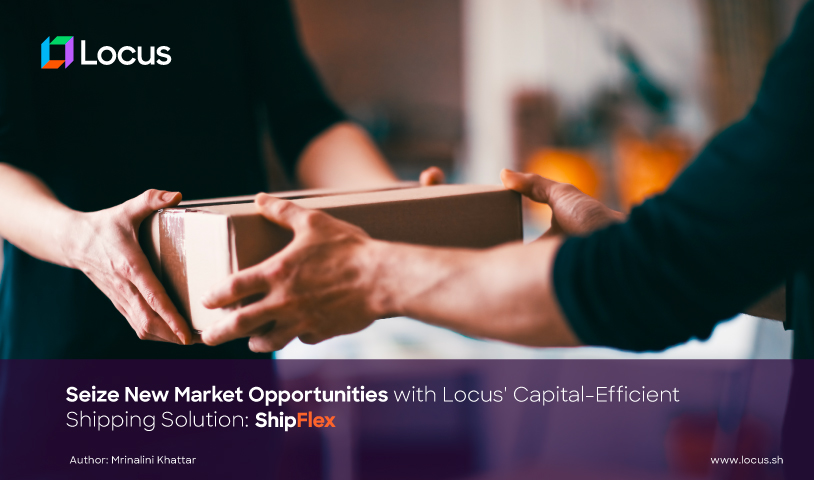
Efficient Shipping Solution to Automate Your Carrier Selection
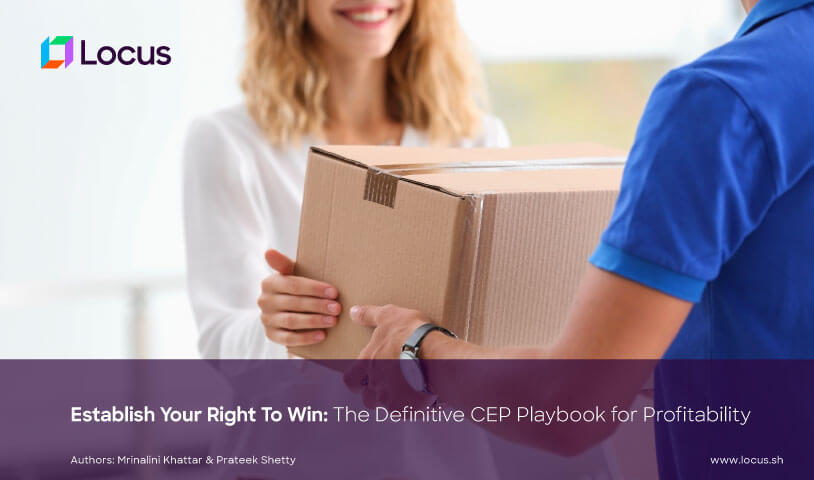
Establish Your Right To Win: The Definitive CEP Playbook for Profitability
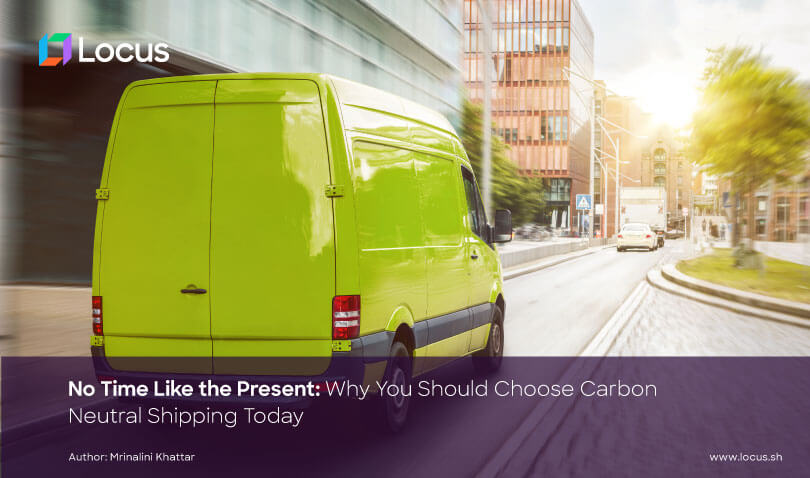
Why You Should Choose Carbon Neutral Shipping Today
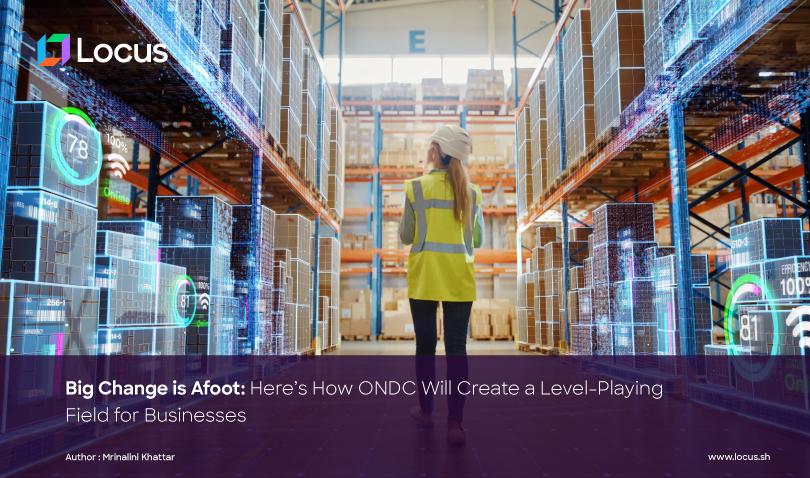
Here's How ONDC Will Create a Level-Playing Field for Businesses
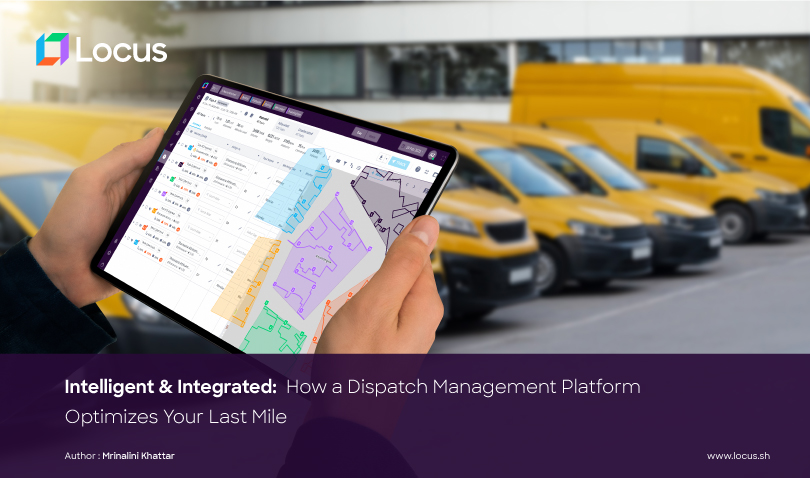
How a Dispatch Management Platform Optimizes Your Last-mile
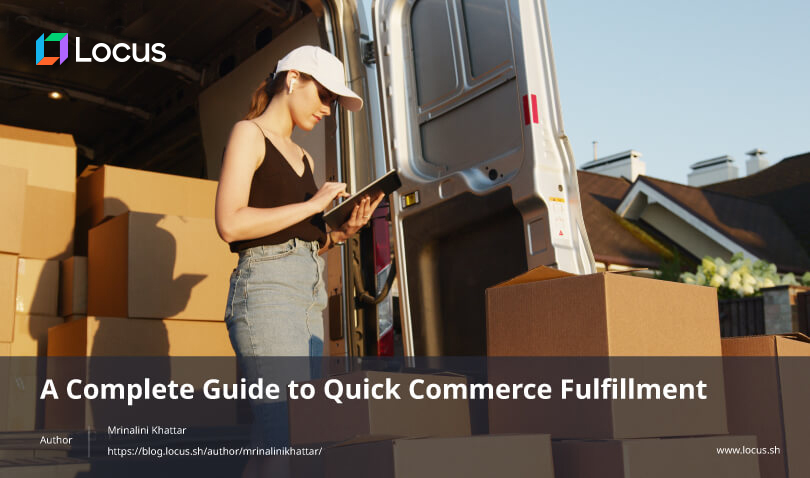
Locus' Guide to Quick Commerce Fulfillment
![case study for logistics industry [E-book] The Complete Guide to Same-Day Delivery](https://locus.sh/assets/img/resources/ebook/same-day-delivery.jpg)
[E-book] The Complete Guide to Same-Day Delivery
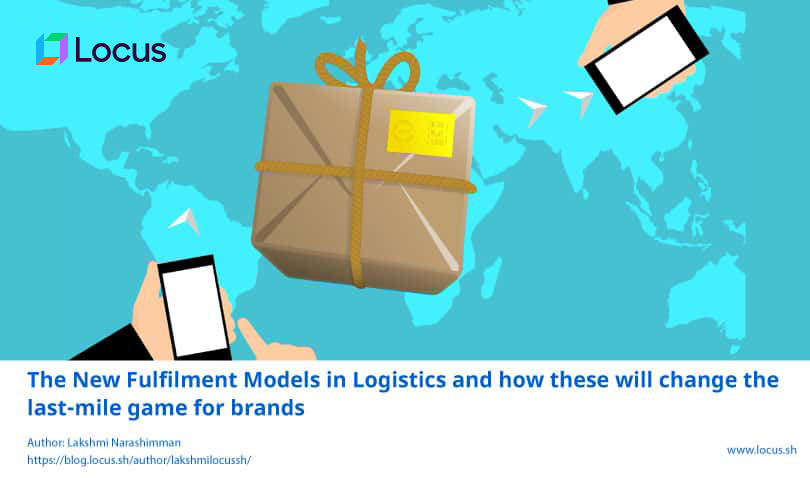
The New Fulfillment Models in Logistics
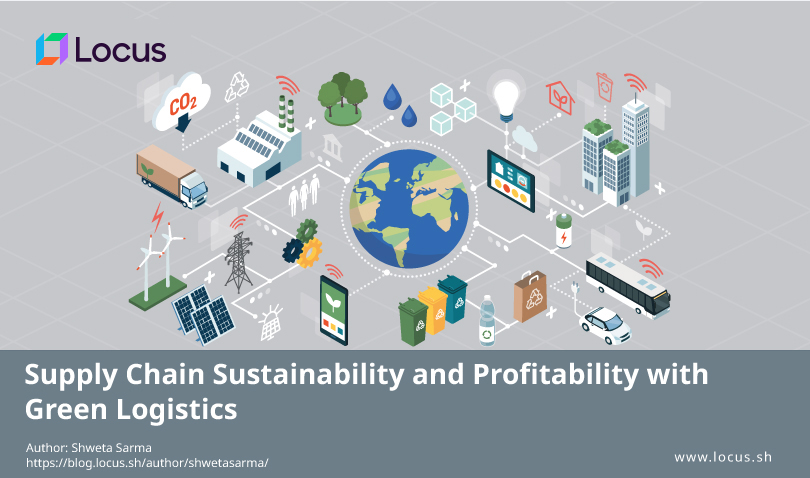
Supply Chain Sustainability and Profitability with Green Logistics
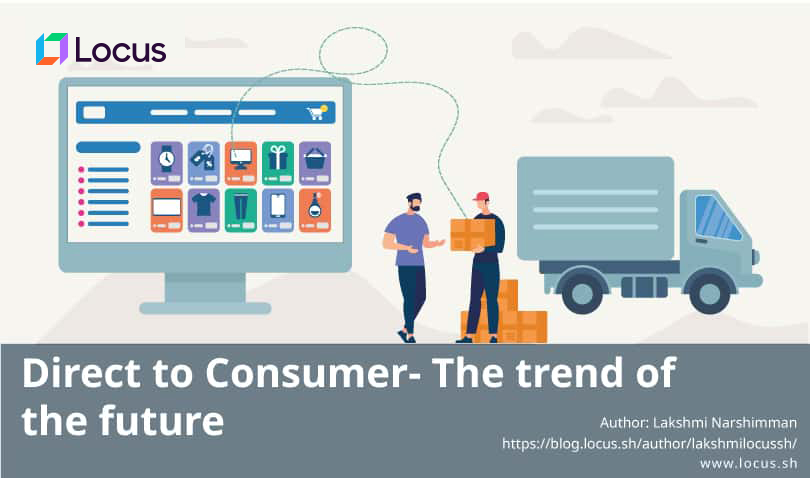
Direct to Consumer- The trend of the future
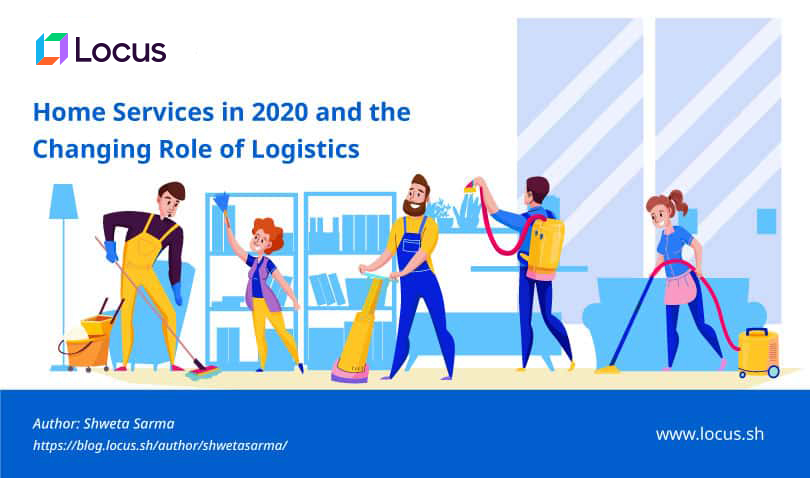
Home Services in 2020 and the Changing Role of Logistics
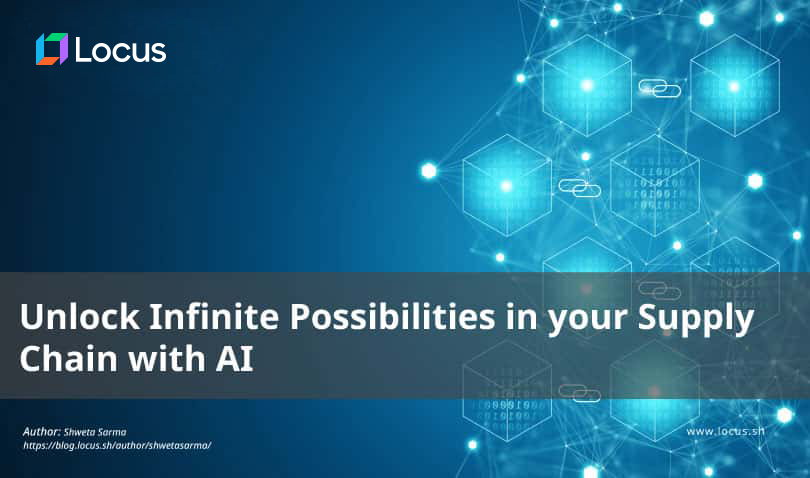
Unlock Infinite Possibilities in your Supply Chain with AI
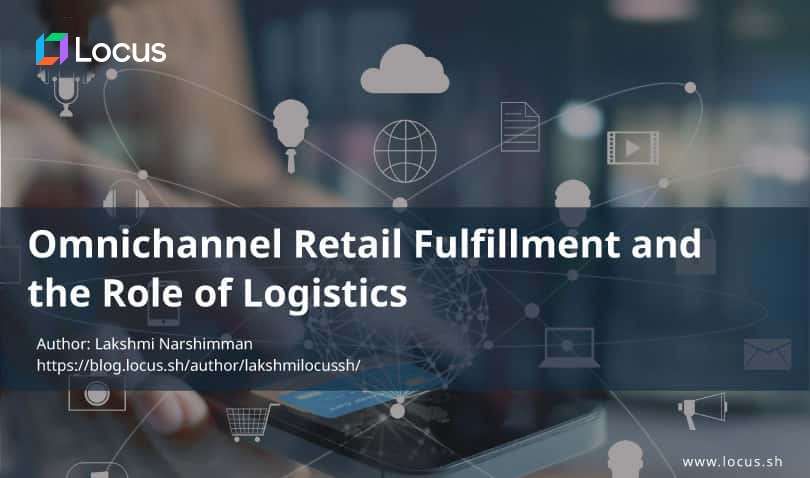
Omnichannel Retail Fulfillment and the Role of Logistics
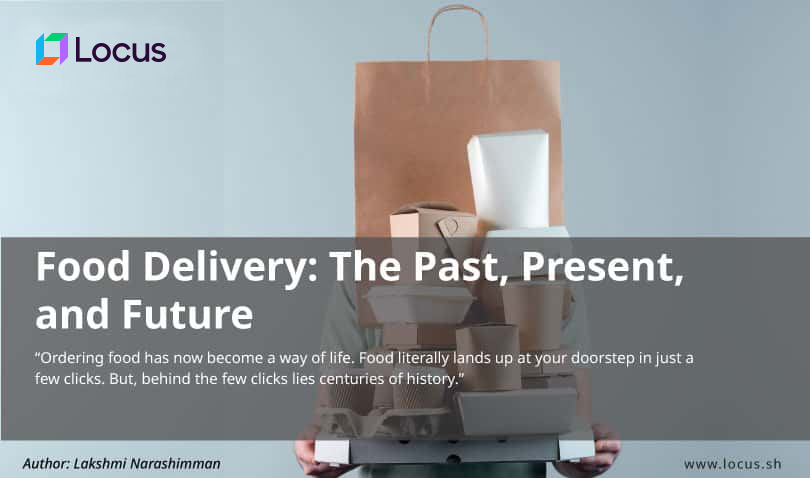
Food Delivery: The Past, Present, and Future
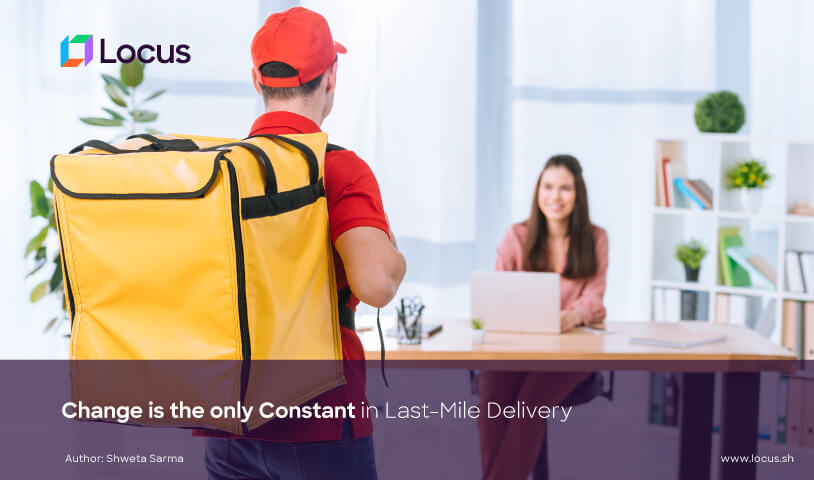
Change is the Only Constant in Last-mile Delivery
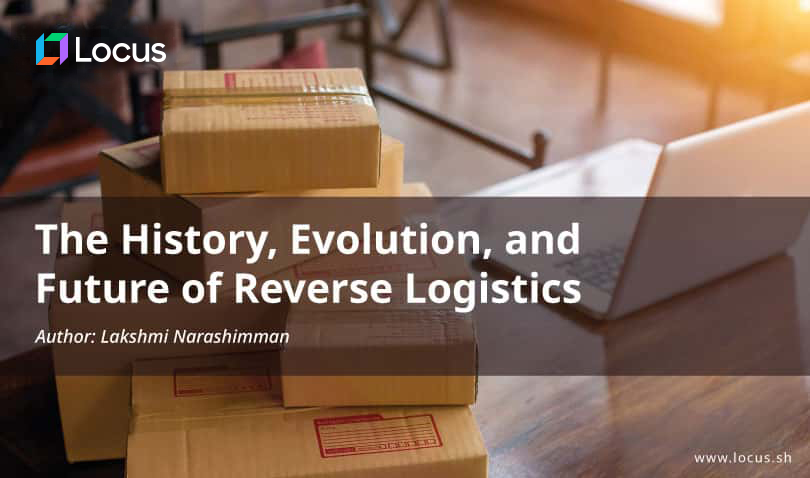
The History, Evolution and Future of Reverse Logistics
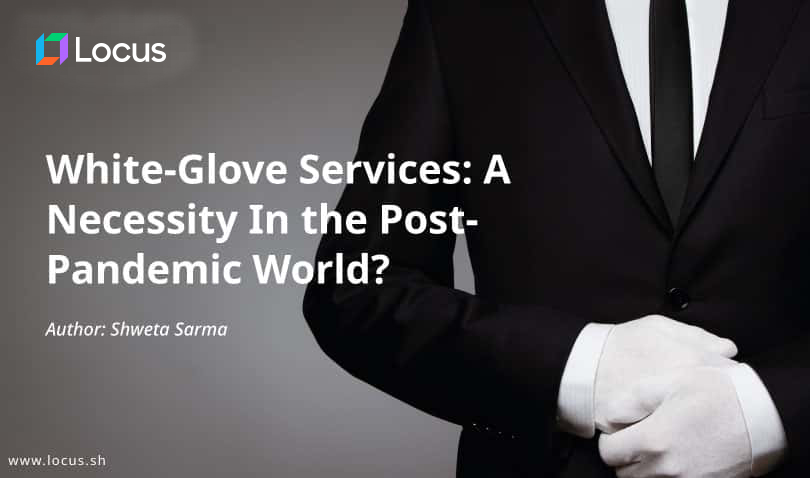
White Glove Services: A Necessity in the Post-Pandemic World?
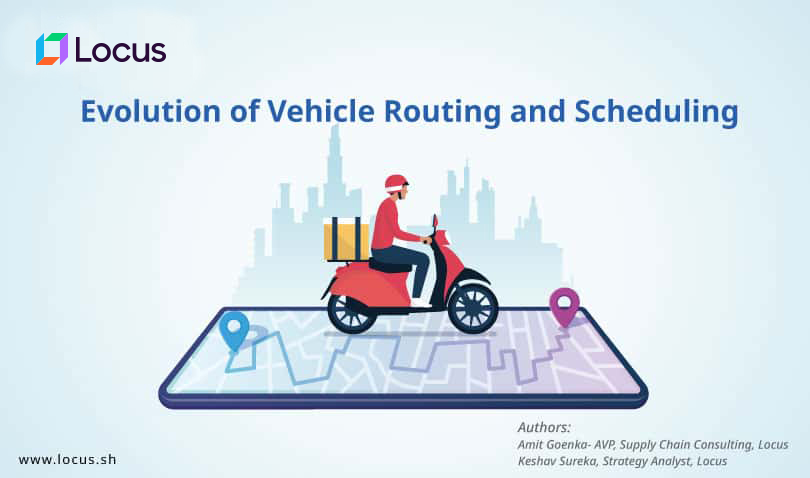
Evolution of Vehicle Routing and Scheduling
Convert your logistics operations to a revenue generator.
By clicking submit, you are providing us with your consent to communicate via email or phone
I would also like to subscribe to the Exclusive Newsletters, Content & Event invitations and notifications by Locus in related areas. You can refer to our Privacy Policy .
Market (Europe - English)
- United States
Top Searches
- Real Time Visibility
Case Studies
Freight sourcing.
Sonepar plugs into a new era of freight matching with Transporeon Freight Procurement
How Transporeon is helping Limagrain Europe achieve its field of dreams
Transporeon improving Amica’s logistics processes
Pirelli: Managing Complexity in Freight Procurement
Benetton Group: Comparability of offers and transparency
AB InBev brews up double-digit spot freight savings with Transporeon Autonomous Procurement
RPM Logistics Deploys Autonomous Truckload Procurement
ZF Friedrichshafen: Easy handling of complex logistics tenders
Transport Execution
Ritex Logistics' journey to operational excellence with Transport Assignment solutions
Transporeon solutions help Essity reach 1bn people every day
Barilla Group achieves 99% carrier allocation success
Duracell: Managing Parcel, FTL and LTL shipments on one Transportation Management Platform
Acerinox: Globalization with a single tool
How we helped DHL to innovate at a crucial time
Facil chooses Transport Operations to streamline transportation flows
How Pfeifer is putting logistics efficiency at the root of their business
Flowing with success: Acqua Vera
Girteka Logistics: Developing relationships between business partners
H.Essers: Finding price-competitive capacity and speeding up the average time to carrier acceptance with Freight Matching
Barilla: Digitalization is the secret ingredient that keeps your pasta fresh
Perfect transport partners with the Transporeon Transportation Management Platform
How Burgo Group digitises its logistics
How K+S achieves efficient end-to-end processes and carrier connectivity with Transporeon and Visibility Hub
Dock & Yard Management
ArcelorMittal Hamburg: Improving time management and streamlining processes in logistics
Metro Logistics: Digitisation ensures transparency in the incoming goods department
How GEBA Trans is improving its customer service offering with Transporeon’s Visibility Hub
How Nestlé is using Transporeon Visibility Hub to manage supply chain disruptions
Saint Gobain Isover: Rapidly scalable visibility solution with high levels of automation
Sustainability
IKEA Supply Chain Operations & Girteka Logistics: You can’t manage what you can’t measure
Schneider Electric: Unlocking greater visibility into the market
Freight Audit & Payment
Top 50 Fortune 500 FMCG company saves big with Freight Audit solution
Interested in our solutions?
Get in touch with us to learn more!
Our solutions for your transport and logistic needs
Visibility Hub
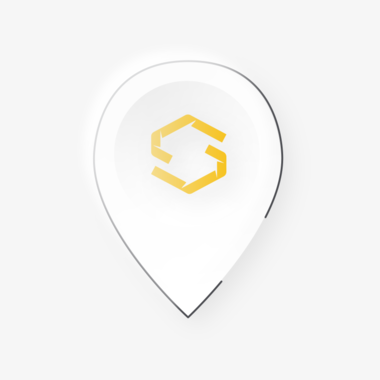
- Reduce check calls and automate processes.
- Increase performance and customer satisfaction.
- Reduce wait and dwell times with more accurate ETAs.
- Increase your on-time performance and avoid penalties
- Reduce CO2 emissions and empty mileage.
Freight Audit and Payment Hub
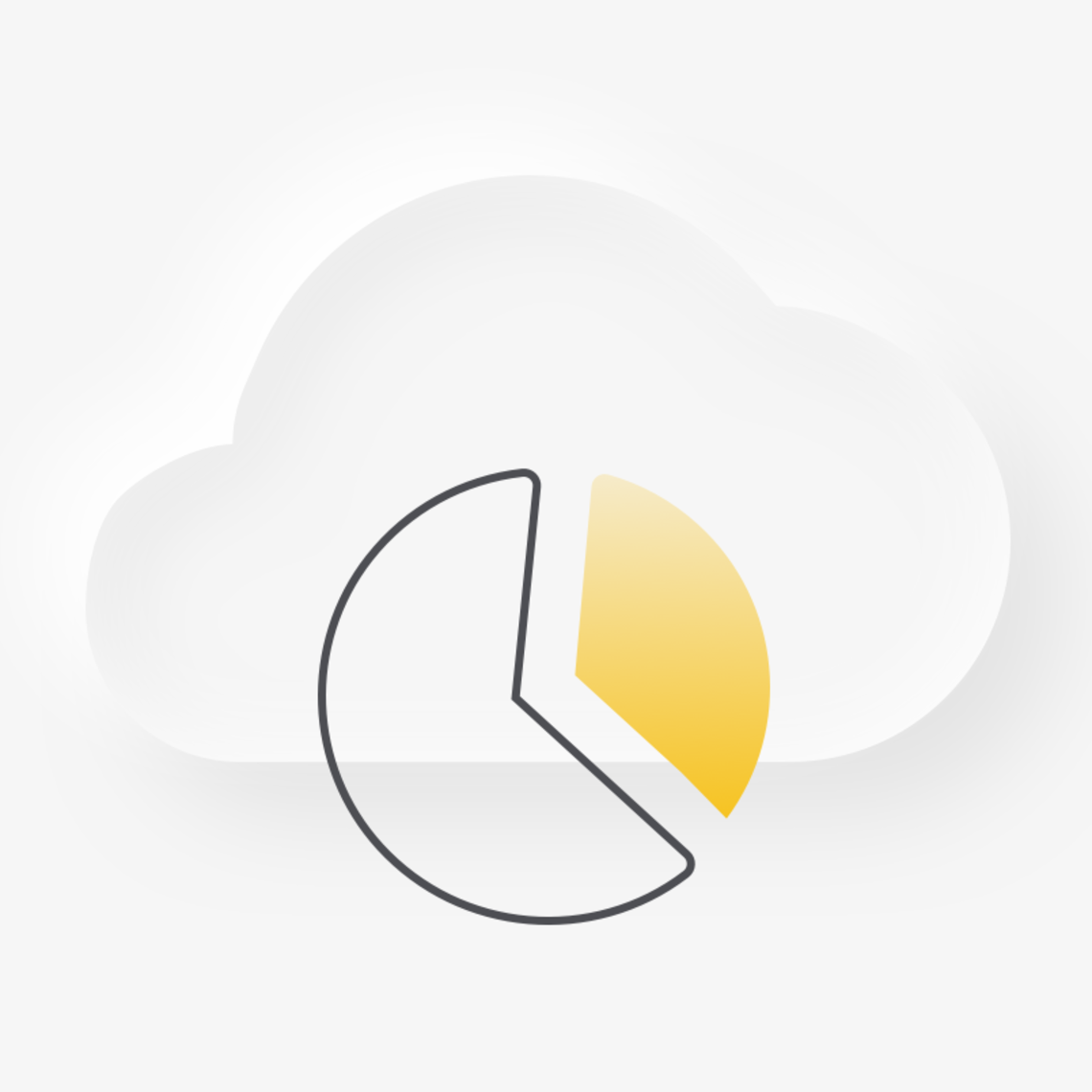
- Pre-fill and validate fields from the Transporeon platform.
- Easily transfer documents to ERP systems via the interface.
- All relevant parties maintain access to the latest versions of all documents.
- Get automatic reminders and notifications for requirements documents.
- Instantaneous and traceable digital transmission of all documents.
Transport Execution Hub
Attachment Services
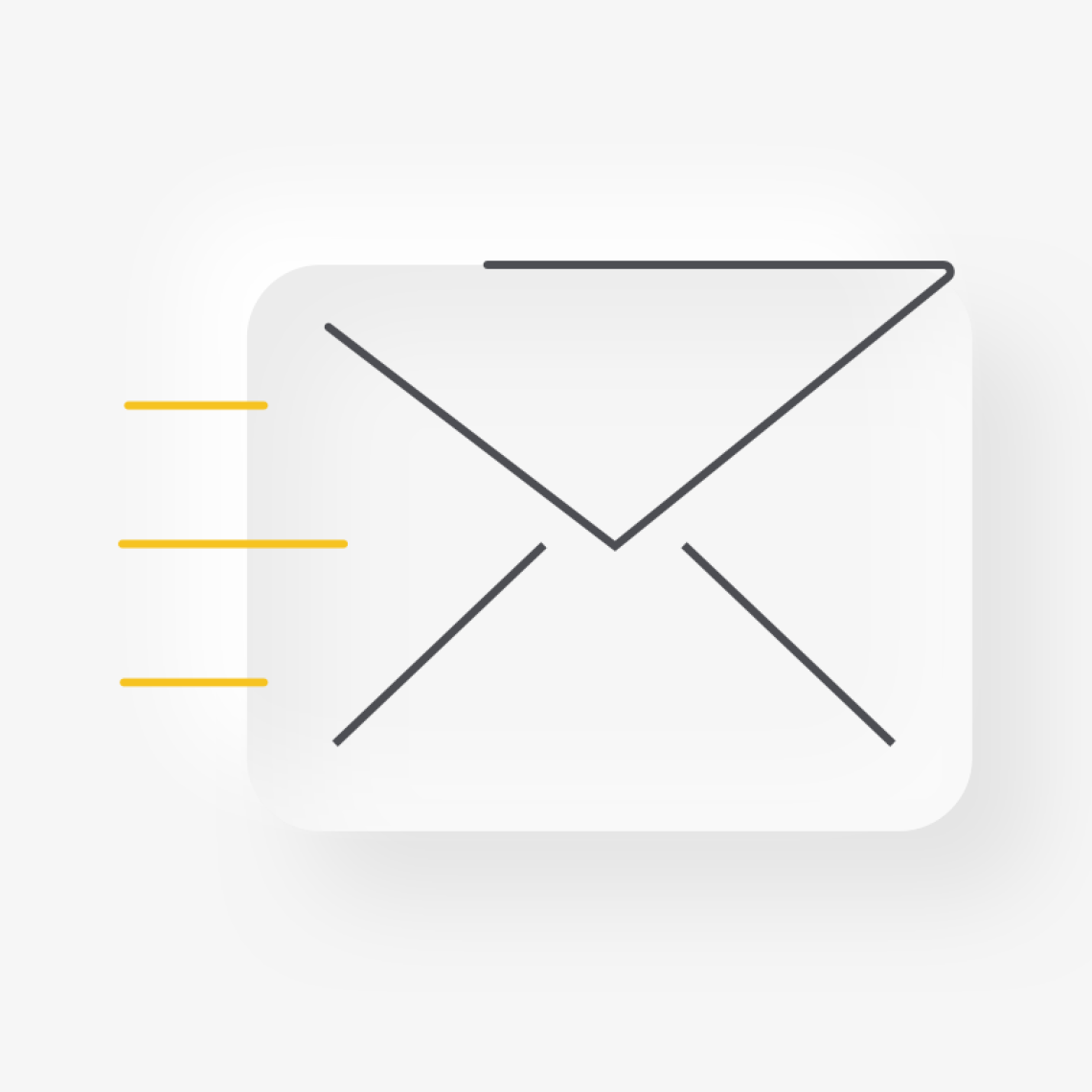
- Pre-fill and validate fields from the Transporeon platform
- Easily transfer documents to ERP systems via the interface
- All relevant parties maintain access to the latest versions of all documents
- Get automatic reminders and notifications for requirements documents
- Instantaneous and traceable digital transmission of all documents
Freight Sourcing Hub
Autonomous Procurement
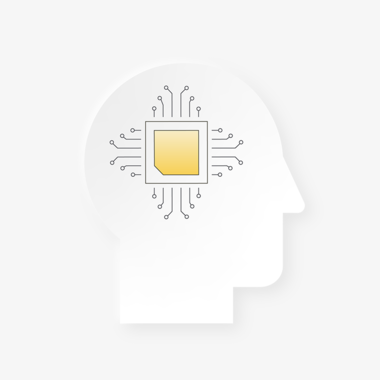
- Automates procurement using data and behavioural science.
- Analyses how carriers make pricing decisions.
- Achieves requested capacity at lower freight rates for road transports.
- Fully automated process of predicting, framing offers, and concluding assignments.
- Entirely carrier specific and automated process.
Best Carrier
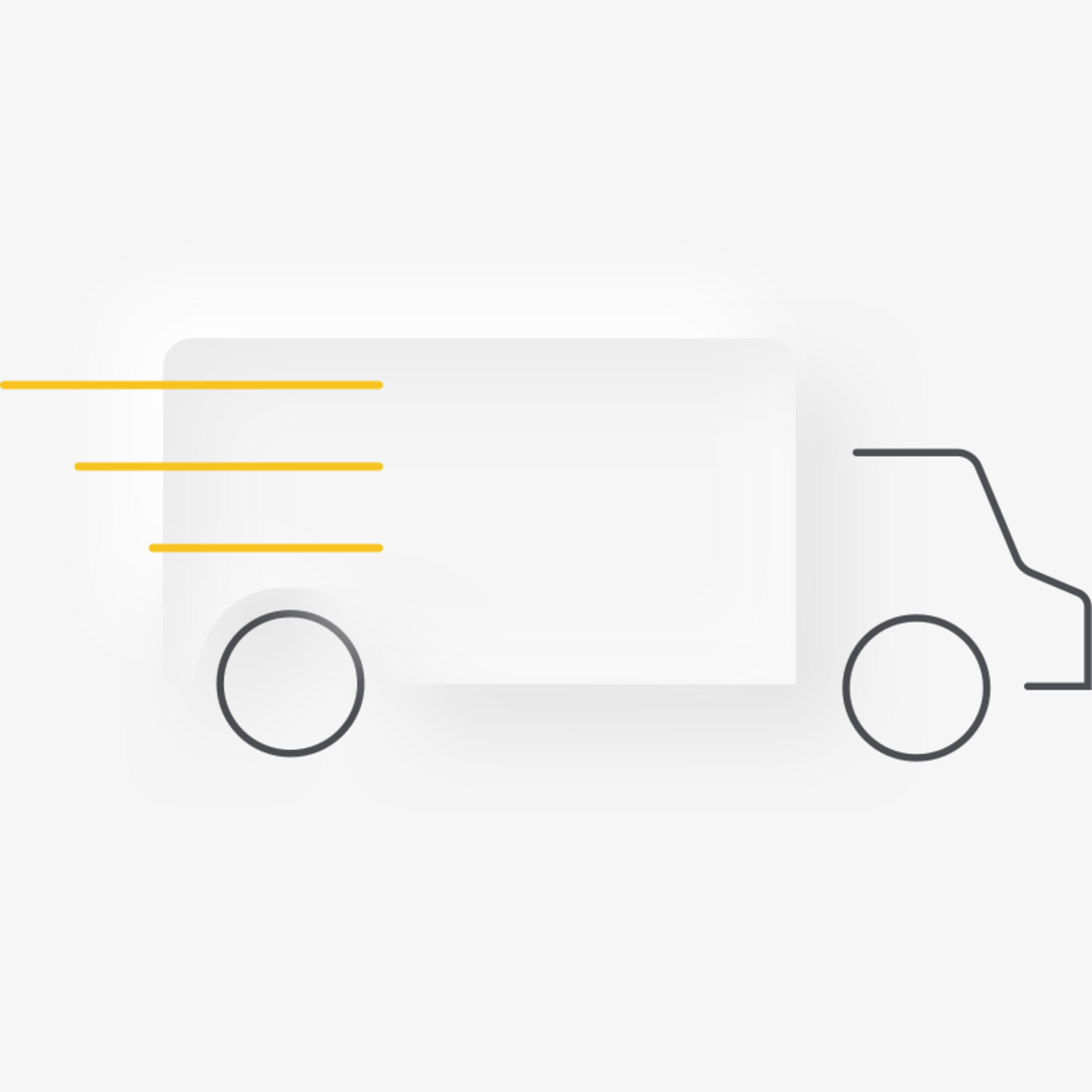
- Access the spot market more easily.
- Cut transaction costs by up to 19%.
- React quickly to market fluctuations.
- Improve process efficiency with better integrations.
- Cloud-based system provides real-time transparency.
Sustainability Hub
Carbon Visibility
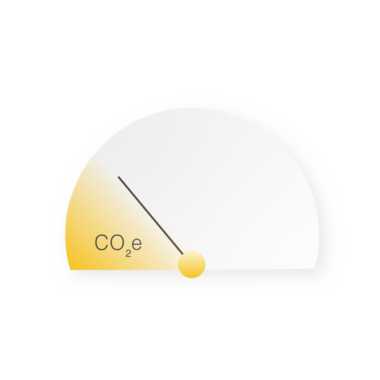
- Precise measuring & reporting on logistics emission.
- Across entire supply chain and all transport modes.
- Based on the highest market standards covering the total emissions (Well-to-Wheel).
- Enables operations to move to Net Zero logistics.
Carrier Premium Account
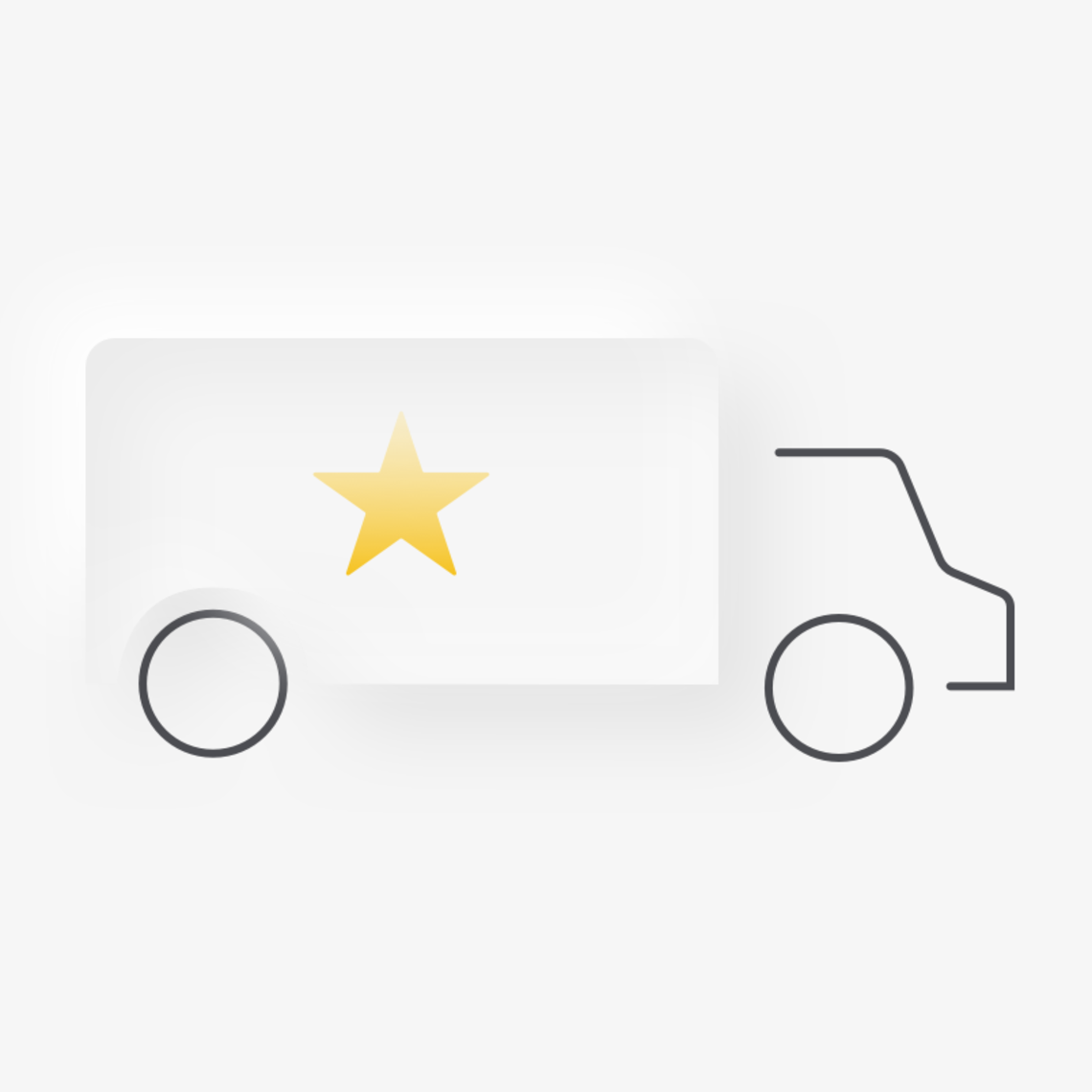
- Apply for suitable calls for bids with one click and win new customers.
- Make your business known on the platform and in the service provider database.
- Clear distribution of competencies and tasks between Head Office and Branch Office.
- Optimize internal processes through additional functions and reports.
Dock & Yard Management Hub

Digital Transport Documents
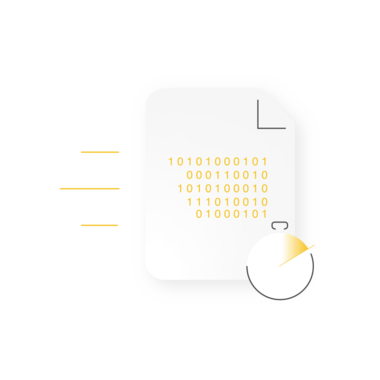
- Paperless management of the consignment note through all involved parties
- Easy usage due to conveniently comment and signing of the eCMR on a mobile device
- Provide the eCMR in real time via Transporeon platform plus additional communication channels
Platform Capabilities
ERP Interfaces
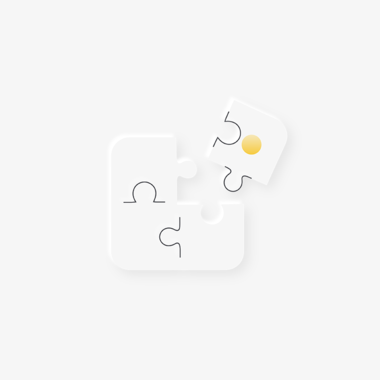
- Integrate the Transporeon platform into your ERP system using the ERP interfaces.
- Stay within your ERP system while using the full-service power of the integrated Transporeon platform.
Event Management
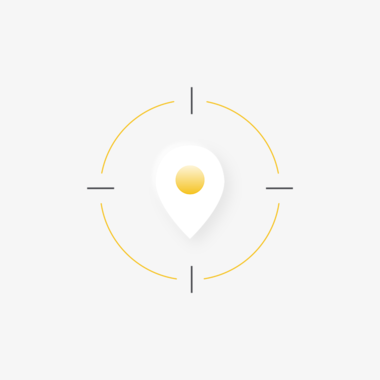
- Track transports from collection to end-point delivery with digital event management.
- Events can be defined and provided to customer needs.
- View actual delivery status and trigger subsequent processes.
- Reliable information about time of arrival for all parties.
- Enable proactive reactions or automated platform based mitigation tasks.
Extended Yard Management powered by Peripass
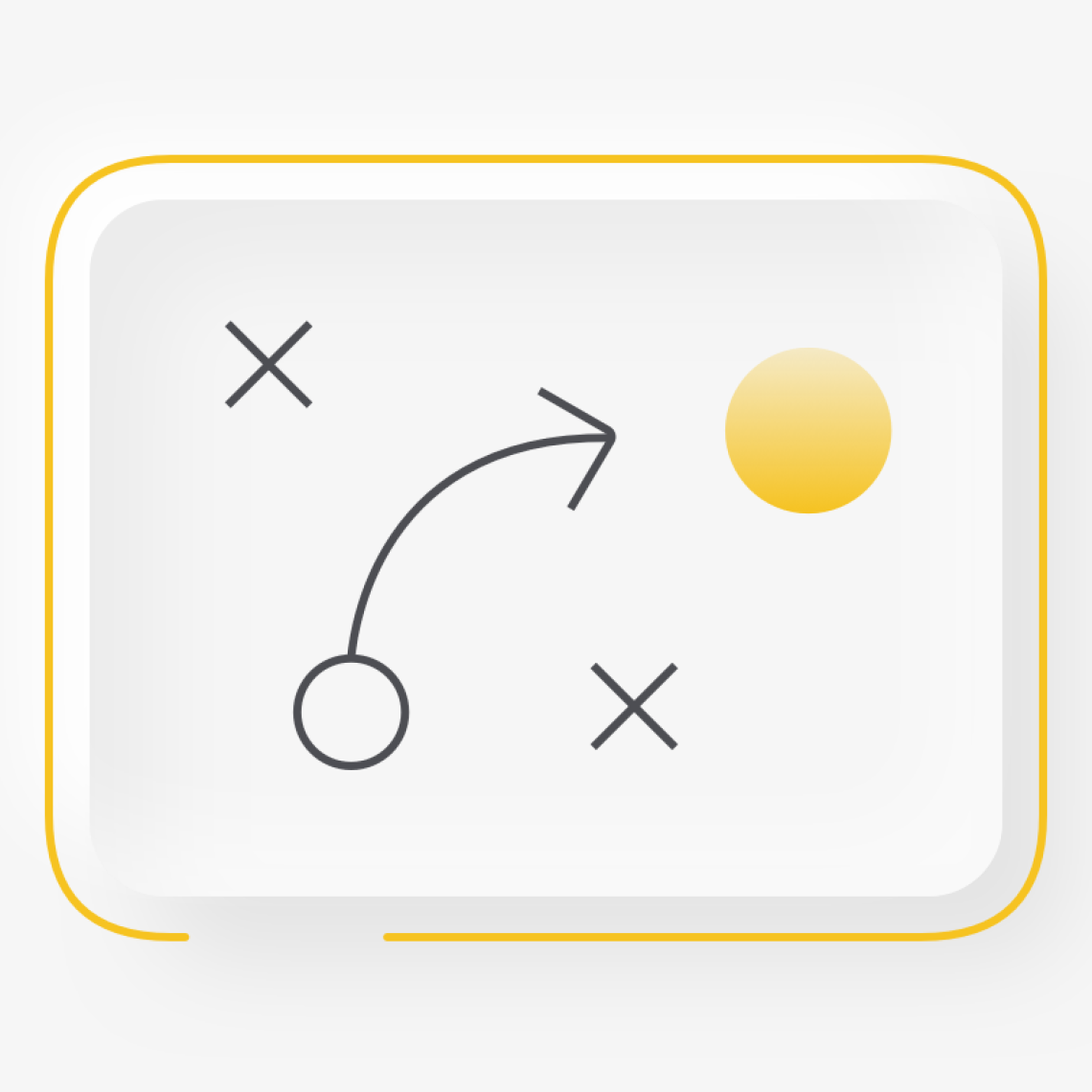
- Reduce manual efforts by digitising the registration process.
- Save on reception costs and reduce waiting times.
- Keep an overview of your site and how capacity is used.
- Shorten lead times, increase volumes and reduce waiting costs by 85%.
- Get a real-time overview of all trucks, containers, trailers etc on site.
- Centralise and digitise the operations of shunters, forklift and truck drivers and security personnel on site.
Freight Audit & Payment Hub
Freight Audit
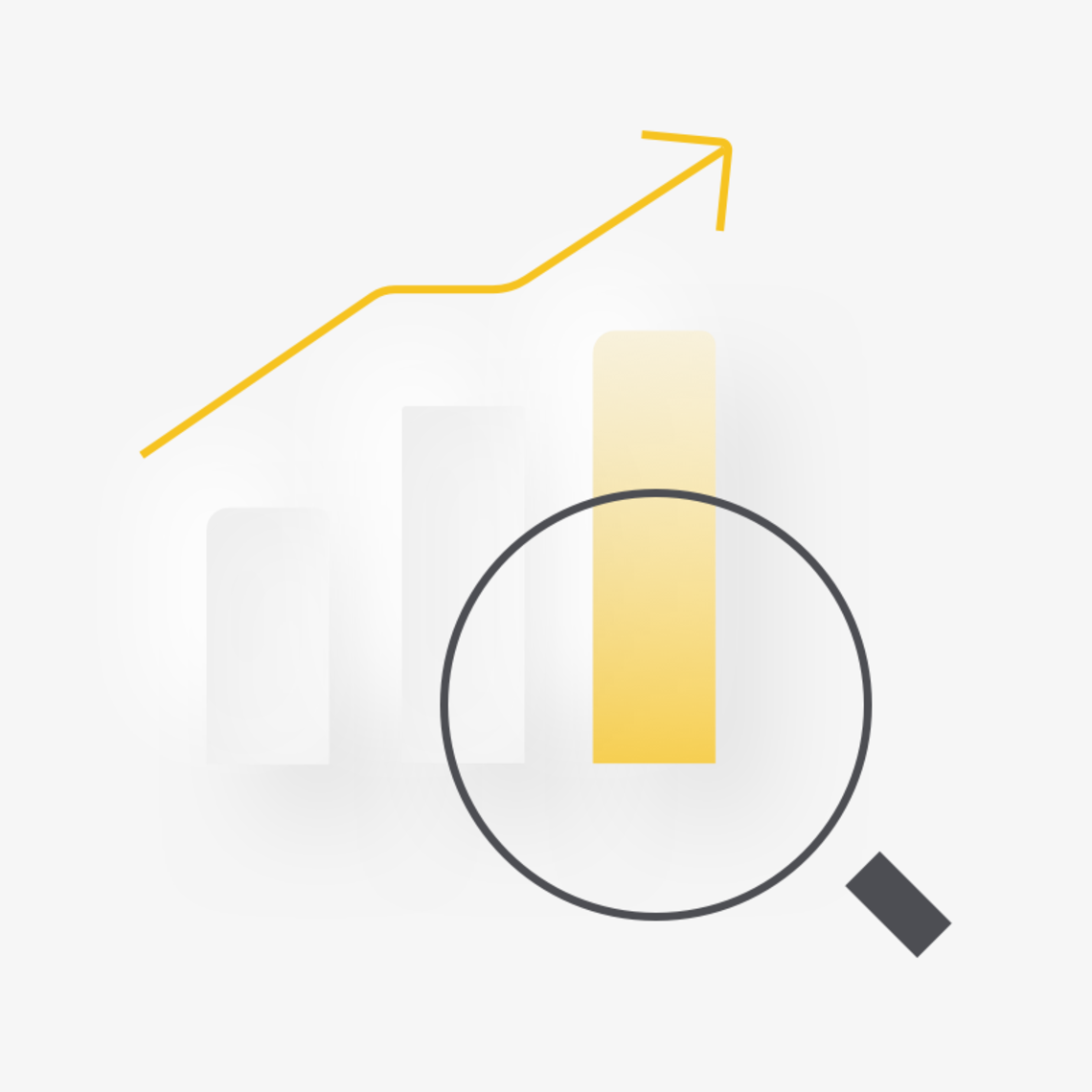
- Full visibility of process, data and carrier performance.
- Logistics should no longer deal with invoicing.
- Underbilling is reported.
- Receives alerts about rejection/approval.
- Cost allocation of freight audit costs are automated.
Freight Matching
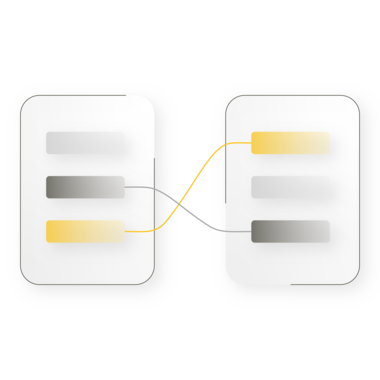
- Maximize profitability and productivity by equipping your teams to utilize available capacity opportunities within your trusted network, faster.
- Enable your carriers to realize their full potential by matching with the loads that are right for them.
- Manage your carrier relationships with more transparency from increased number of data points.
- Stay in control of your shipments and provide end-to-end visibility to your customers, and eradicate check calls.
- Reduce manual effort, and increase accuracy with full digitalization.
Freight Procurement
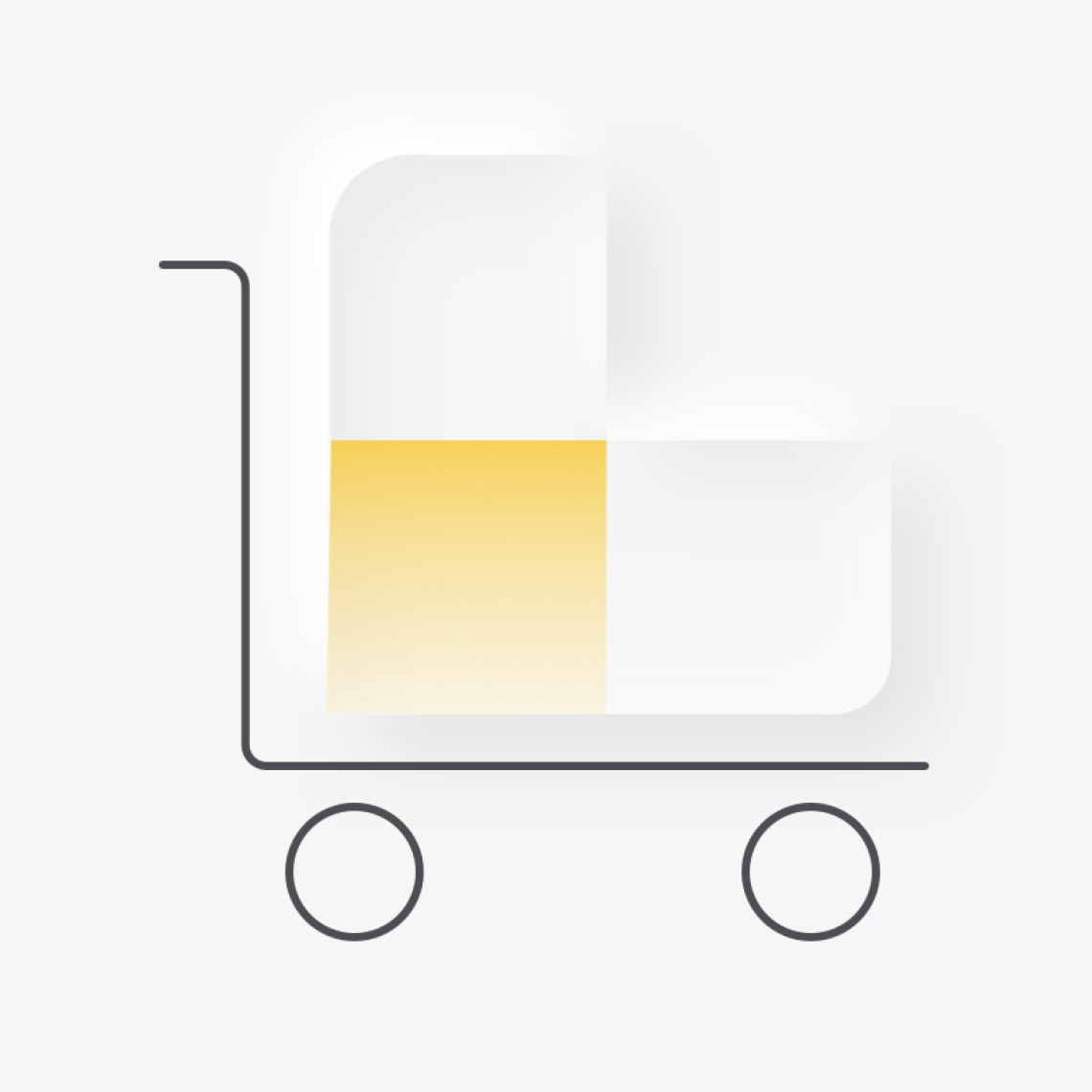
- Smart purchasing strategy.
- Achieve optimum freight rates.
- Reduce administrative effort and costs.
- Find suitable partners worldwide.
- Audit-proof the tendering process.
Procurement Advisory
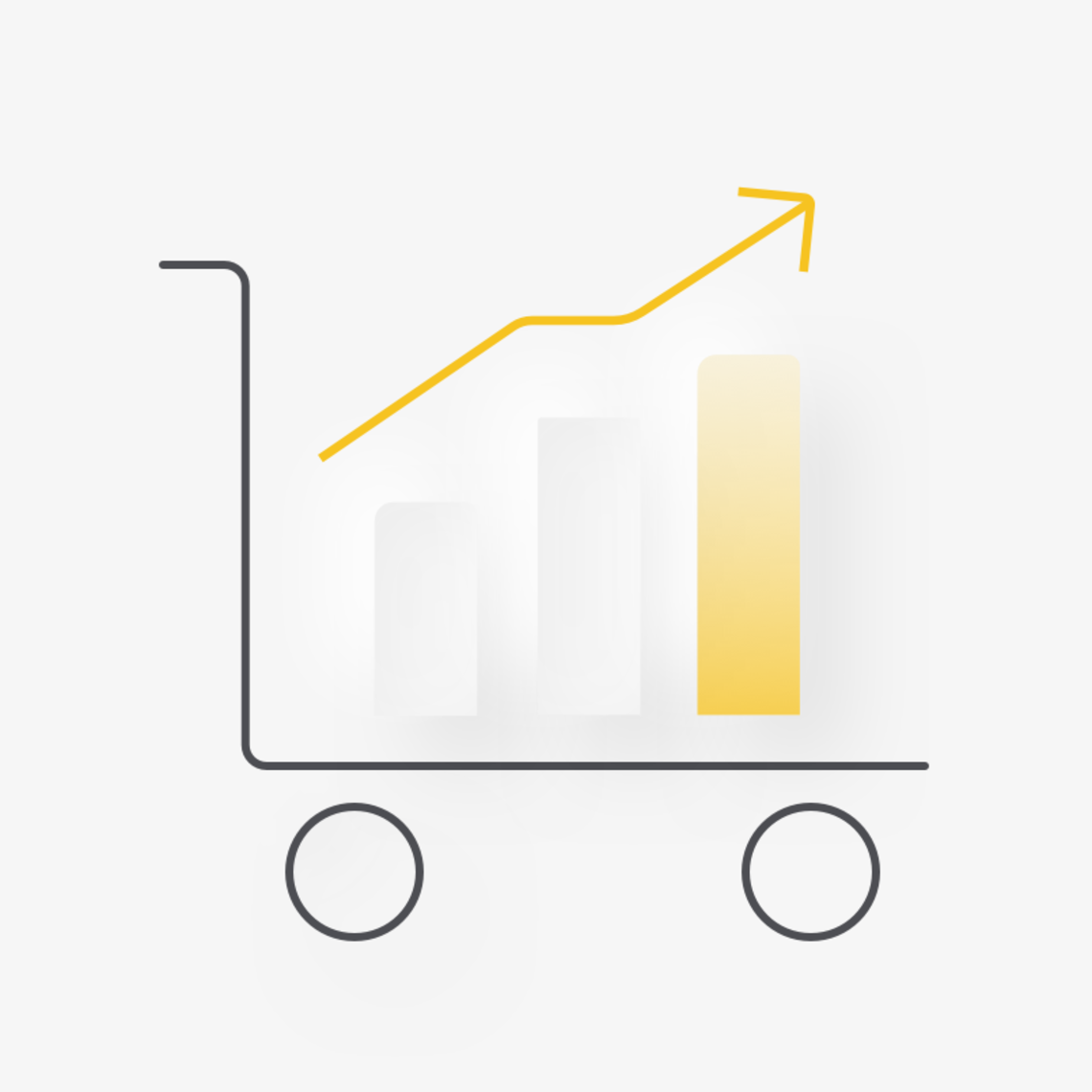
- Save up to 19% on freight costs.
- Save 30% on administrative effort with e-sourcing.
- Use only quality-approved data for tender processes and RFQ events.
- Ensure 100% compliance with tendering processes.
Freight Settlement
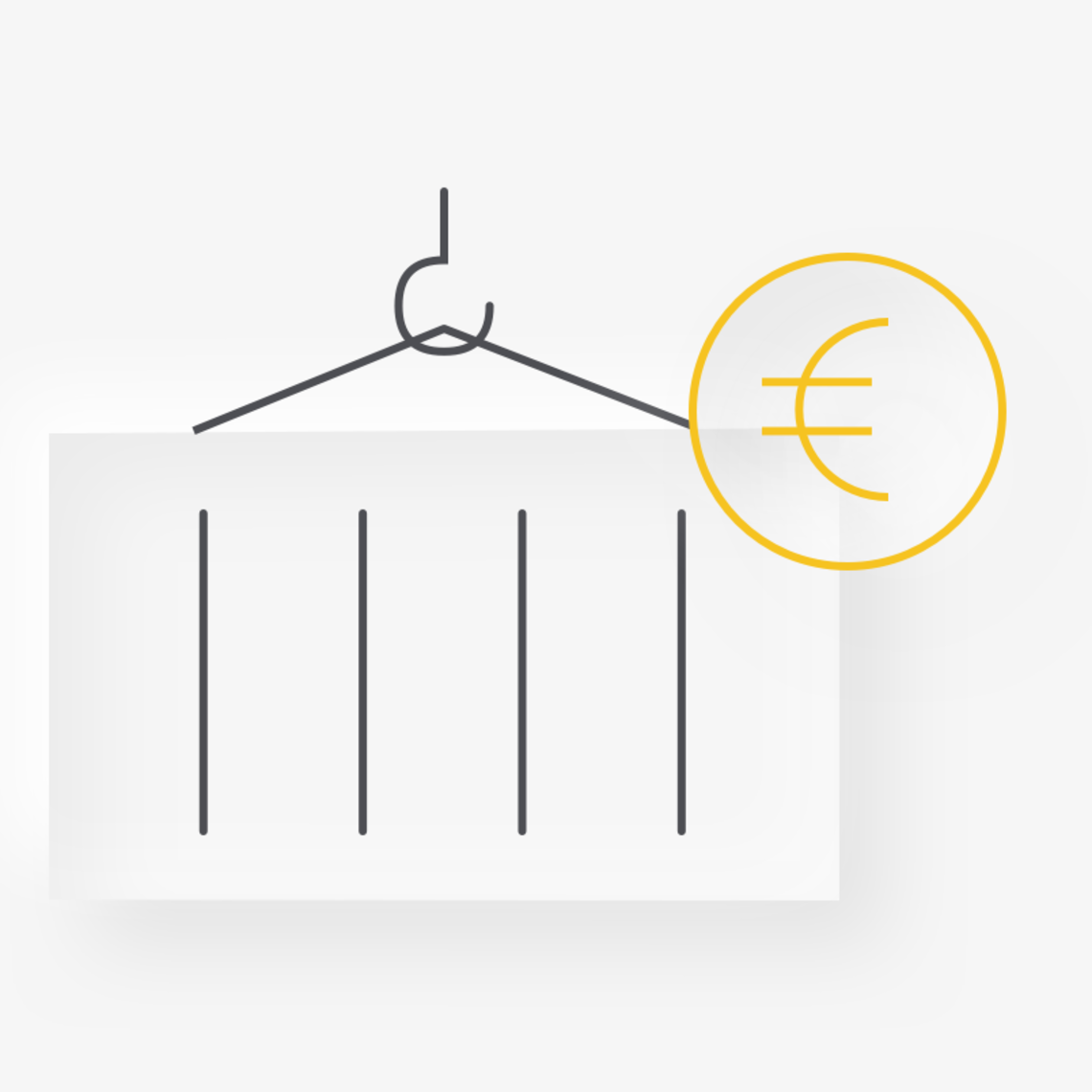
- Save time by resolving billing issues before the invoice is sent.
- Simplified control of individual invoice items.
- All settlement transactions are displayed in their entirety to provide complete transparency.
- Company-wide and standardized coordination process.
- Can be also used as stand-alone-solution also compatible with other products.
Insights Hub
Market Insights
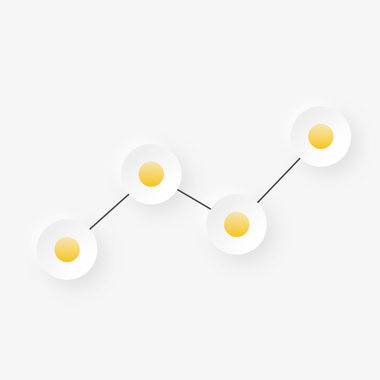
- Monitor the contractually agreed rates between shippers, logistic service providers, and the spot market.
- Use important "indirect" indicators to illustrate the capacity situation on any given lane or market.
- Define the lanes and metrics that you want to monitor.
- Get a clear overview of the biggest market changes and top movers.
Strategic Benchmarking
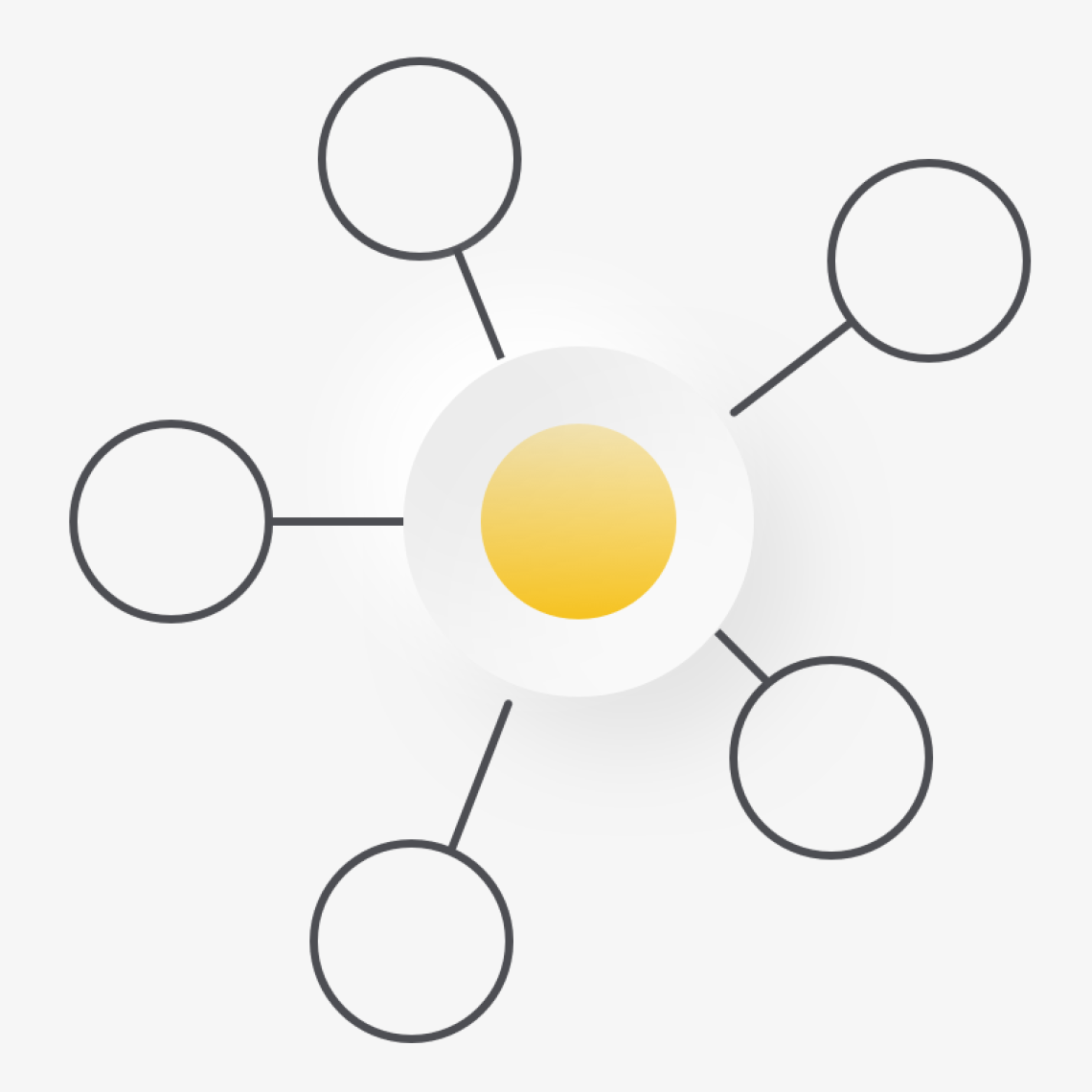
- Persistent freight cost savings with up to 8% with our state of art benchmarking approach.
- Get the most comprehensive overview of all markets and for all modes.
- Profit from insights into latest market developments & forecasts.
- Get a deeper understanding of rate developments & costs drivers.
- Receive regular information with market overviews, developments, cost drivers.
No-Touch Order
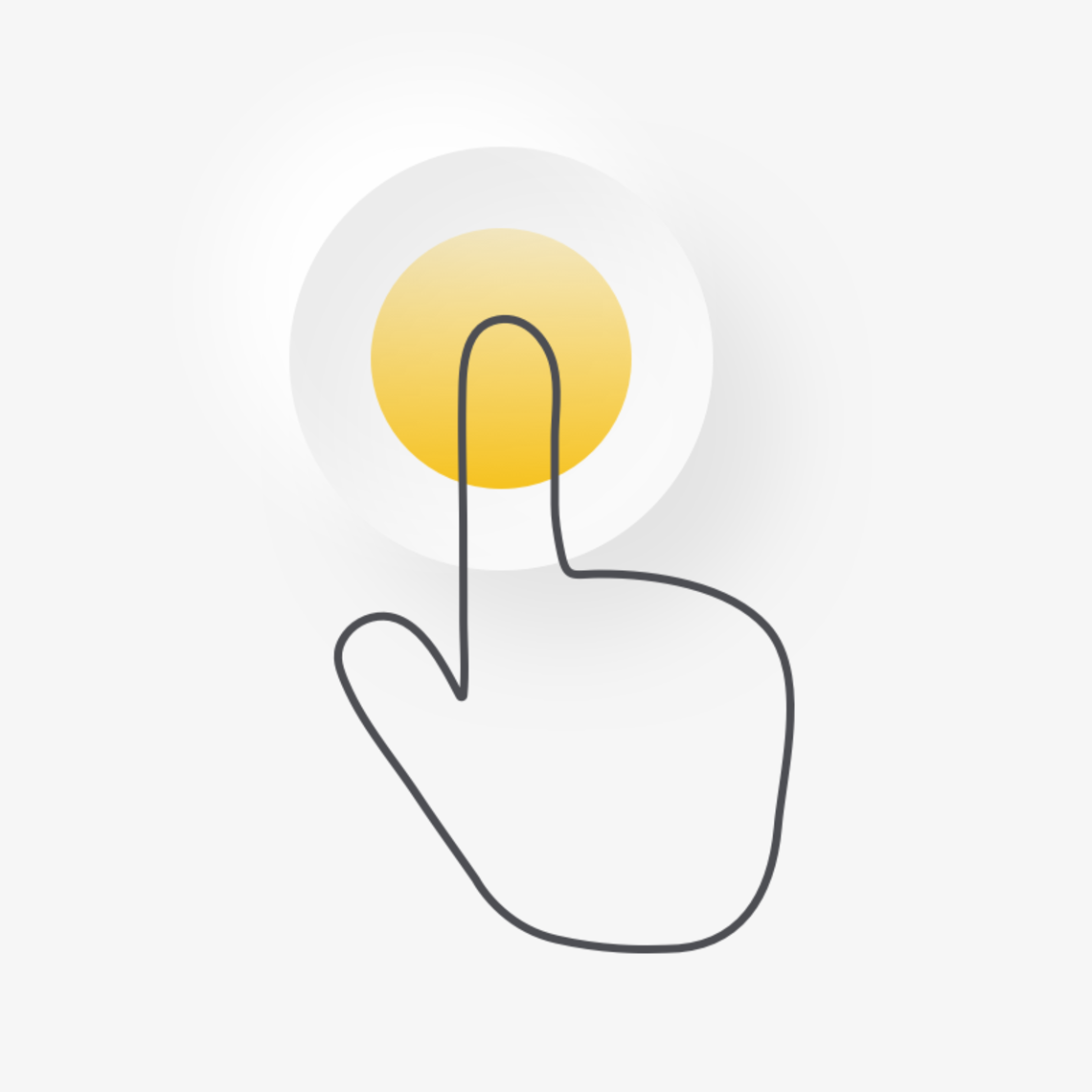
- Automated shipment execution processes.
- Fewer empty runs.
- Cut process costs by up to 30%.
Rate Management
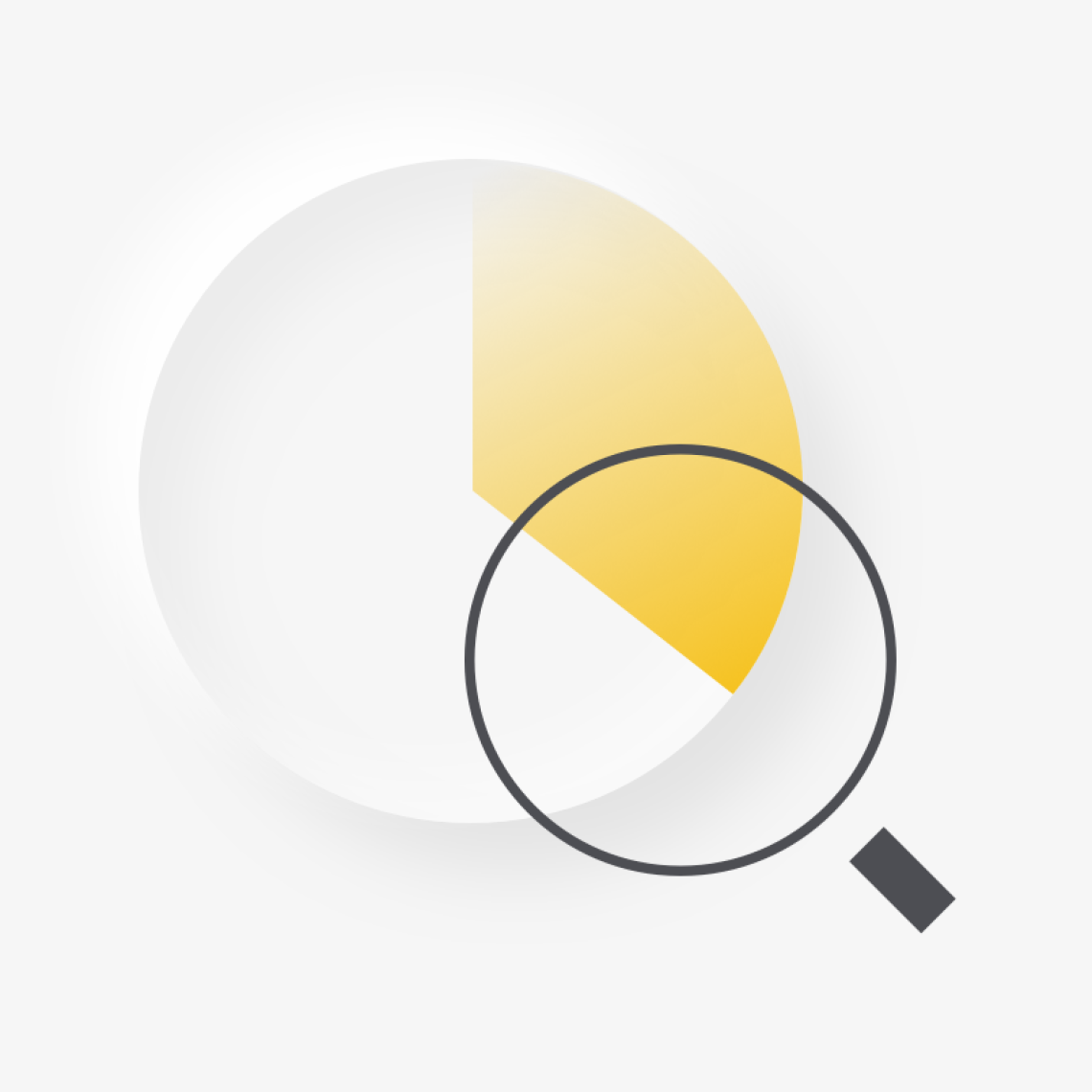
- All freight rates and freight contracts in one centralized database.
- Rate query engine factors in multiple currencies, surcharges and total chargeable cost per available carrier.
- Optimization of inquiry processes and better usage of internal resources.
- Fully integrated process of assigning transports and management of rates in an organization.
- Centralized interfaces and import/export functions.
Real Time Workflow
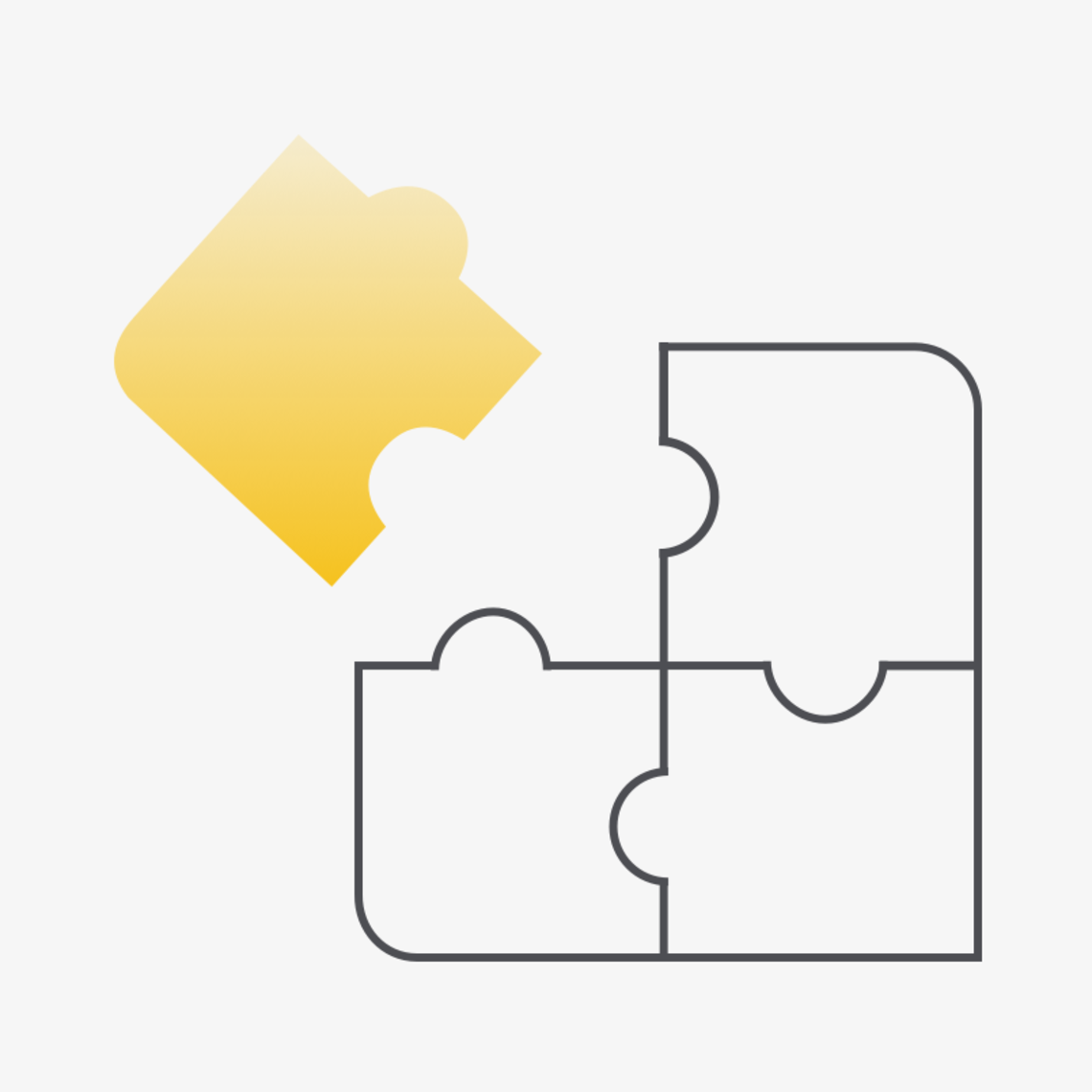
- Less labor-intensive solution due to electronic workflows and paperless management of transport documents.
- Integration of drivers into the digital workflow.
- Immediate updates about status changes and shipping stages of the goods to be delivered.
- Photographic documentation of transport damage and proof of cargo safety.
Real-Time Yard Management
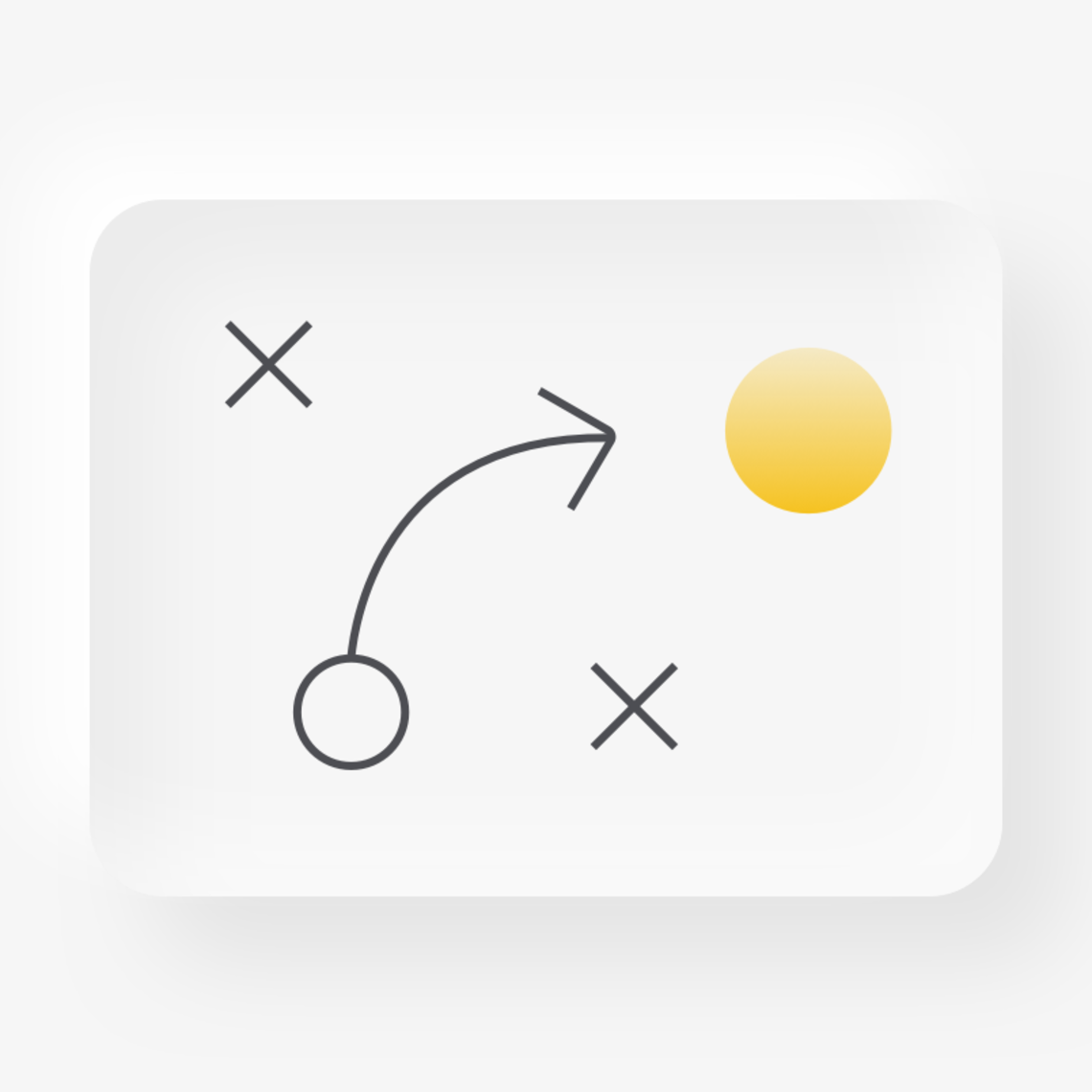
- Improve overall visibility and ability to predict changes.
- Combine yard, transport, and warehouse management.
- Automate arrivals, check-ins, and call-offs.
- Avoid costs and fees caused by idle and inefficient processes.
- Monitor, measure, and improve KPIs.
Time Slot Management for Retail
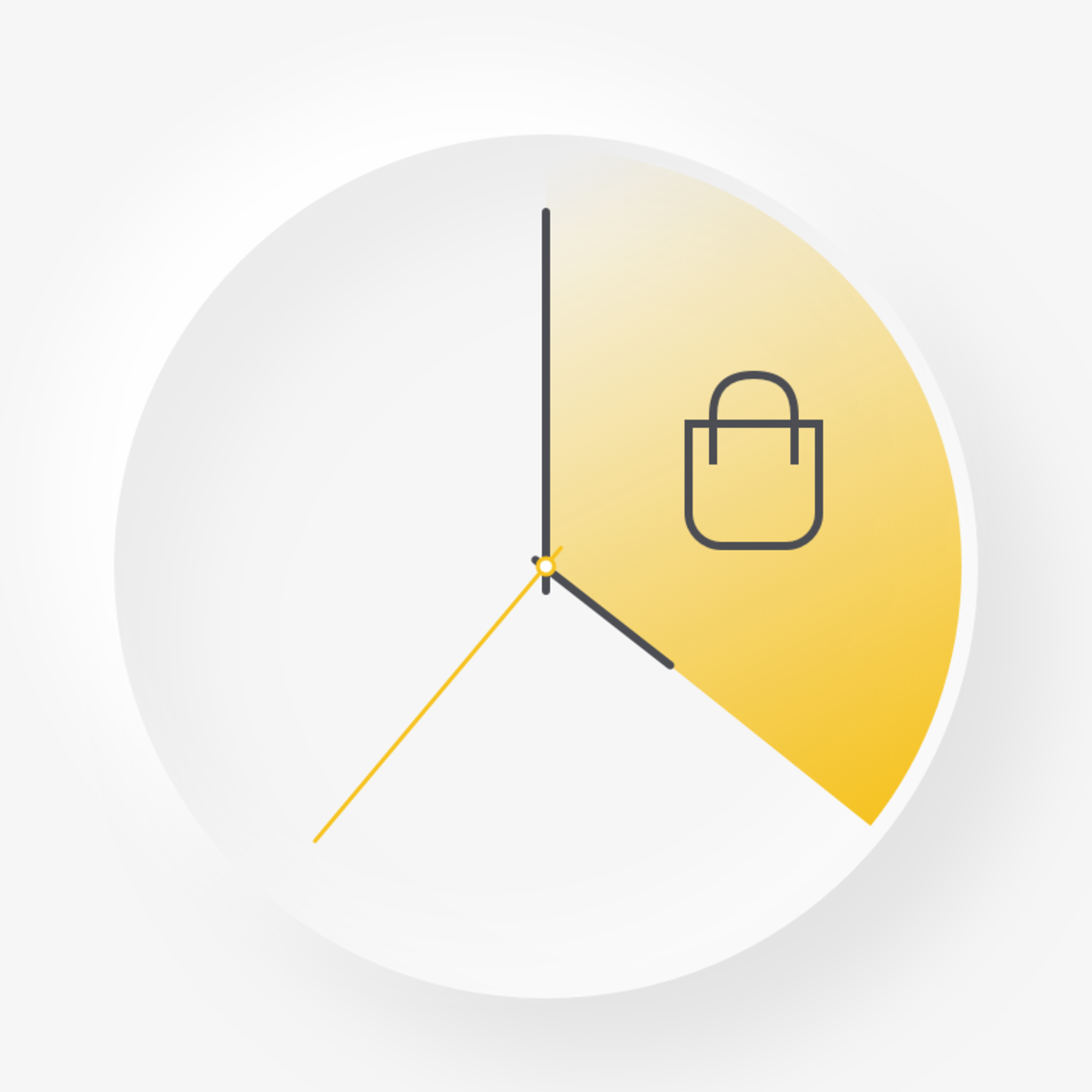
- Increase handling capacity by up to 20%
- Reduce driver wait times by up to 40%
- Shorten loading times by up to 60 minutes
- Audit and legal security
- Completely documented processes
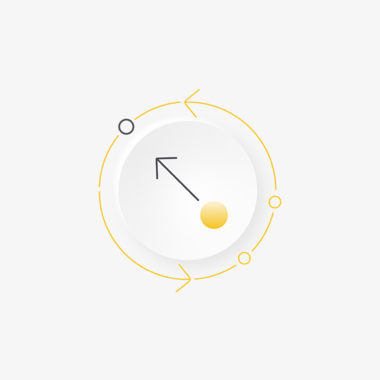
- The SAP Add Ons integrates all Transporeon functionalities without a need for interfaces or middleware into the SAP ERP system.
- Benefit from the Transporeon UX within your standard SAP system.
Market Intelligence & Benchmarking
Supply Chain Advisory
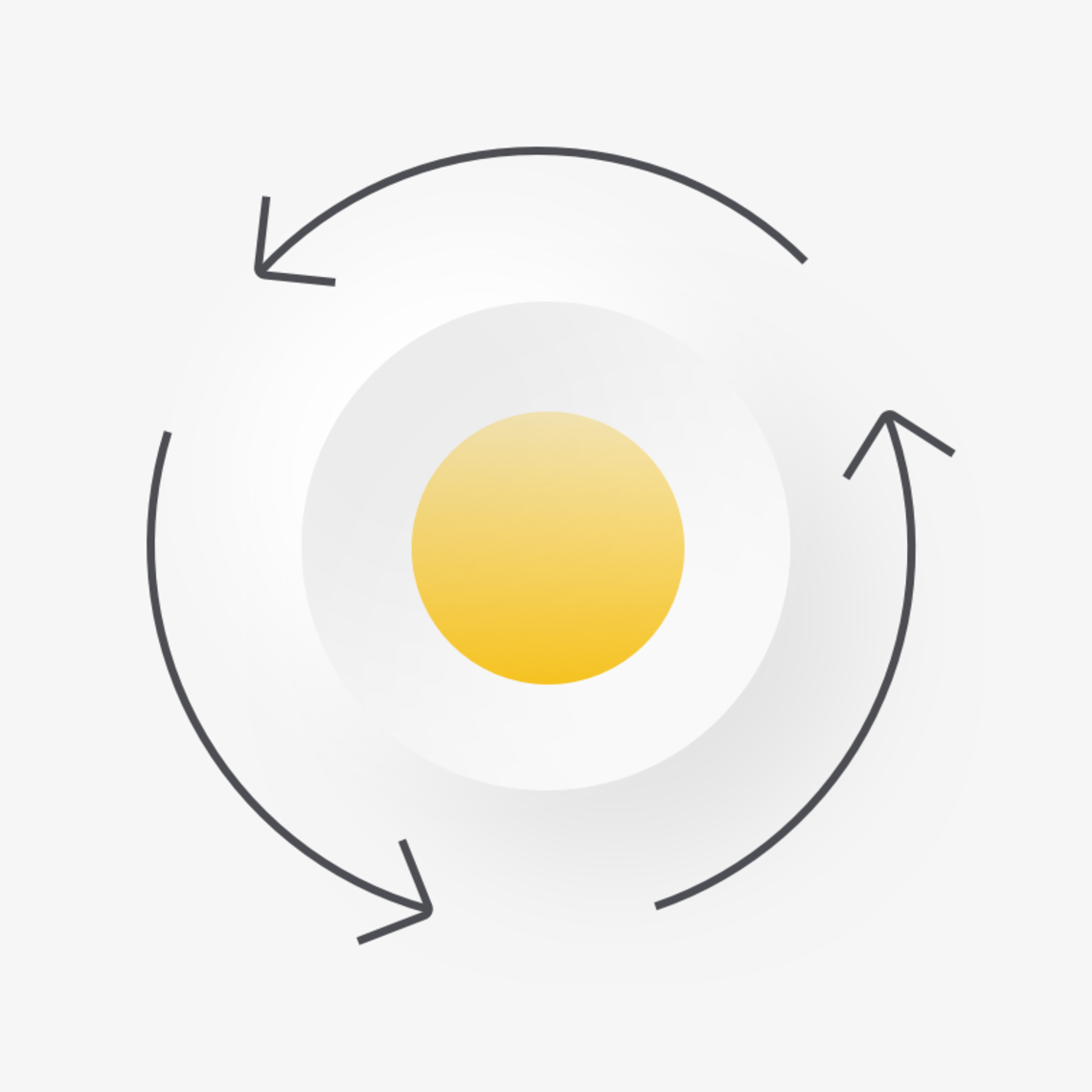
- Know-How from more than 1,700 supply chain projects and 25+ years of experience
- Gain full global network transparency
- Achieve cost savings through supply chain optimization
- Support for all phases, from conception to implementation into your supply chain
- Deep knowledge of all modes of transport
- Specialized Benchmarks with proven Market Intelligence methodology
- be_ixf; php_sdk; php_sdk_1.4.26
- https://ziplinelogistics.com/why-zipline/case-studies/
Zipline Logistics acquires Summit Eleven [read more]
Why Zipline
Logistics case studies.
Zipline Logistics prioritizes YOUR bottom line. We are experts in retail logistics and exclusively service CPG brands shipping into retail. This means we’re a logistics solutions provider — not just a rate and a truck — and we genuinely care about and invest in CPG brands’ success.
Check out the Zipline love stories below for examples of challenges our customers have faced and the results we’ve driven alongside them.
“Zipline has eliminated all of these issues for Isik”
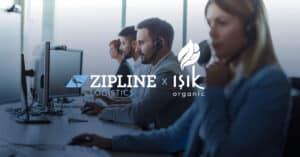
Shipper: Isik Organic, a leading grower, manufacturer, and exporter of organic dried fruits & nuts and frozen fruits and headquartered in Turkey.
Challenge: During the height of the COVID-19 pandemic, I sik was dealing with carriers arriving late to delivery appointments, products being damaged while in transit, and keeping t ransportation costs within budget .
Results: Over the course of the first two years working together, Zipline has eliminated virtually all of these issues for Isik. Their OTIF has improved and their transportation costs have gone down considerably.
See Full Logistics Case Study
T. Marzetti Dramatically Increases OTIF
Shipper : T. Marzetti, a leading specialty foods company headquartered in Columbus, Ohio.
Challenge: T. Marzetti was struggling to meet delivery deadlines and as a result, experiencing heavy retail compliance fines and damaged relationships with their retail partners.
Results : T. Marzetti’s OTIF score was in the mid-80’s when they started working with Zipline. One year later, their OTIF score was up to 94%. Before Zipline, Marzetti felt alone in putting out fires and educating their partners on the impacts of not meeting retail expectations. Whereas with Zipline, these issues were immediately met with proactive communication that led to quick solutions.
“What Make Zipline Different is the People”
Shipper: Be Well Nutrition, Inc., known for its ICONIC PROTEIN line of beverages, powders, and coffee.
Challenge: The relationship between Zipline Logistics and Mariah Nguyen, COO of Be Well Nutrition, Inc. , began about ten years ago when Nguyen was working for Vita Coco. Nguyen enjoyed Zipline’s people and service so much that she carried the relationship to the next four companies she worked with.
Results: ICONIC PROTEIN, Be Well’s line of protein beverages, powders, and coffee , has relied on Zipline as its exclusive transportation broker since 2018. Zipline manages both procurement of ingredients and LTL & FTL customer order fulfillment. Zipline has offered this client a competitive advantage through in depth freight analyses, resulting in both time and cost savings.
True Logistics Partnership
Shippers: Premium drink mixer company, Fever Tree; and importer, distributor and brand representative for premium biscuit/snack manufacturers, Brand Passport.
Challenge: Both Fever Tree and Brand Passport needed a logistics service provider that could meet a wide range of transportation needs while identifying new supply chain efficiencies and showcasing true partnership.
Results: Zipline Logistics went above and beyond to provide knowledge, data, and recommendations that helped streamline operations for Fever Tree and Brand Passport. Invested in customer success, Zipline fully managed orders, optimizing along the way and involving the customer on an exception-management basis. Zipline built trust, provided peace of mind, and helped both brands solve for their logistics challenges.
3PL Partnership and Service
Shipper: Global producer of coconut products, Vita Coco
Challenge: Vita Coco required a logistics partner that instilled total confidence and enabled it to focus on its brand, not transportation. Navigating a fast-growth market segment, they needed a 3PL that could scale alongside them and provide ongoing supply chain consultation.
Results: Zipline Logistics has successfully grown together with Vita Coco, expanding to meet domestic transportation and drayage needs. Vita Coco now cuts down on overhead costs by funneling logistics through its customer service department, relying on Zipline Logistics to properly handle transportation and identify new optimization and savings opportunities.
Zipline Love Stories: Specialized 3PL Adds Value to Multibillion-Dollar Retailers
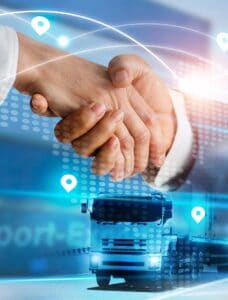
Challenge: The shoe company was challenged by it’s tiny storefronts in bustling metropolitan areas, which required multiple perfectly timed deliveries per week. The specialty retailer needed consistent manpower transporting expensive, valuable, time sensitive, and extremely high volume shipments from ports to distribution centers.
Results: Zipline played a major role in helping the shoe brand skyrocket. Since entrusting us with nearly 100% of their domestic freight over the last three years, their revenue nearly doubled as they explosively expanded from four stores to 30+. After six years of business with the specialty retailer, Zipline has moved 17,000+ loads at 96% on-time delivery rate. Since partnering with us, we have seen their revenue grow by close to $3.5 Billion.
WTRMLN WTR Streamlines Refrigerated LTL Operations
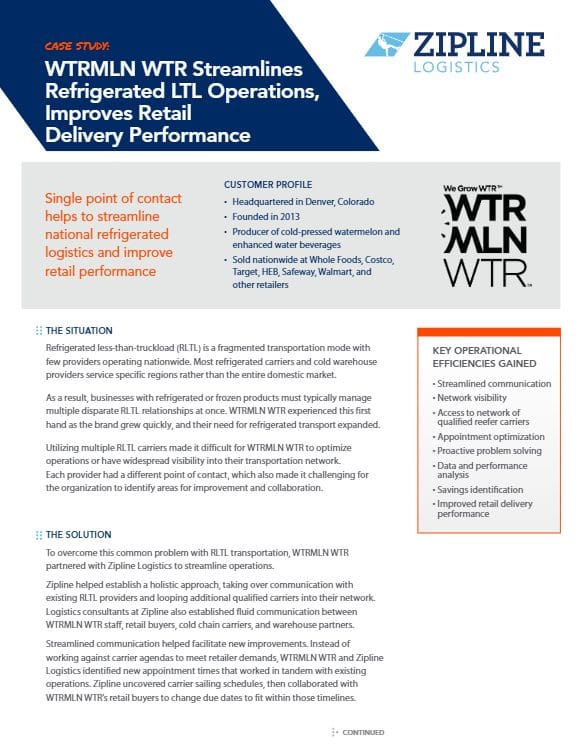
Challenge : WTRMLN WTR grew quickly and expanded its sales across the United States. Because the brand’s product is temperature-sensitive, it required refrigerated shipping to fulfill its growing orders. Temp-controlled shipping is fragmented with few providers operating nationwide. WTRMLN WTR needed to manage relationships with several disparate regional providers at once.
Results: By working with Zipline, WTRMLN WTR gained new visibility into their operations adding transparency into their supply chain and uncovering beneficial consolidation opportunities, scheduling improvements, and network reconfiguration.
Download Logistics Case Study
Consolidation and Managed Transportation Solution
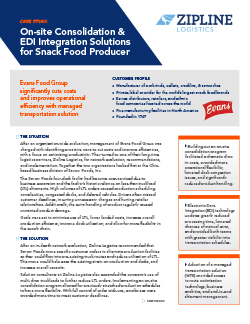
Shipper: Global producer of pork snack products, Evans Food Group
Challenge : Evans Food Group was charged with identifying proactive ways to cut costs and improve efficiencies throughout its supply chain. Goals were set to minimize use of LTL, lower landed costs, increase overall production efficiency, improve dock utilization, and allow for more flexibility.
Results: Solution consultants at Zipline Logistics developed an on-site order consolidation program that successfully reduced LTL utilization and lowered landed costs per pallet by 20%. Adoption of a managed transportation solution and EDI order tendering technology also enabled Evans Food Group to greatly improve internal efficiencies and gain more visibility into its supply chain.
Beverage Transportation Specialists
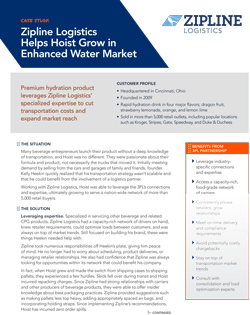
Shipper: Emerging enhanced-water brand, Hoist
Challenge: As a growing beverage brand, Hoist needed to scale its transportation strategy and engage a logistics partner that could provide guidance on how to meet retailer demands.
Results: Hoist leveraged Zipline Logistics’ beverage transportation expertise to meet retailer requirements, cut transportation costs, and grow its network. By engaging an experienced 3PL partner, Hoist no longer had to worry about scheduling product pick-ups or deliveries and could instead focus on growing its brand.
Improving On-Time Delivery by 17%
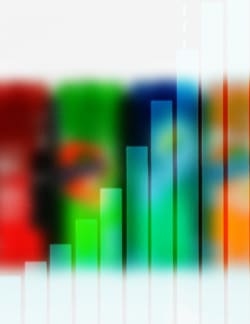
Challenge: The company grew extremely fast and struggled to consistently meet retail compliance standards due to a complex national footprint.
Results: Zipline brought smart technologies and seasoned retail logistics professionals to the table. Through the facilitation of appointment flexibility, order visibility, and cross-departmental communication, the soda manufacturer was able to better serve customers and improved its on-time delivery by 17 percent.
Beverage Transportation and Minimum Orders
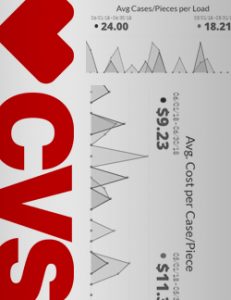
Challenge: The growing beverage brand was entering new retail markets and facing common issues associated with securing new shelf space. When their new customer began purchasing small quantities of product to test sell, the brand was breaking even on their orders due to the cost of transport.
Results: Zipline Logistics leveraged its proprietary shipper intelligence tool, KanoPI, to show the beverage brand that once began to order even slightly more product their costs would come down. By isolating critical metrics in KanoPI and renegotiating order minimums, they were able to remain with and ultimately achieve long-term profitability with the retailer.
Solving for Retail Vendor Compliance Issues
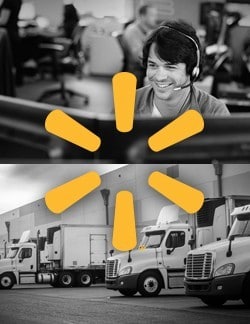
Challenge: The brand was experiencing reoccurring delivery problems and rejected orders at Walmart. This caused freight to be late, extra paperwork, and the potential for costly fees related to retail vendor compliance failures.
Results: Zipline took over management of Walmart deliveries. Solution consultants identified proactive ways to rework delivery appointments, optimize dues dates, and book more reliable transportation, ultimately improving the brand’s vendor performance.
Transportation Network Analysis
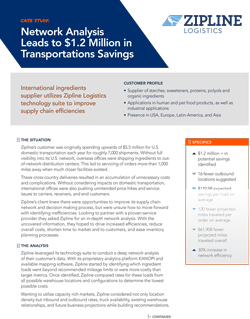
Shipper: International food ingredients supplier
Challenge: Overseas offices were shipping product out-of-network, which led to an accumulation of unnecessary costs and complications. The organization required more visibility into its U.S. supply chain to proactively identify opportunities to cut transportation spend and avoid service issues.
Results: Zipline Logistics leveraged its shipper intelligence tool KANOPI to identify $1.2 million in transportation savings for its customer. Consultants identified trends within data and found specific shipments that were driving up transportation costs. With inefficiencies isolated, they optimized modes and altered warehouse locations to achieve a 30% increase in network efficiency.
Want to See Logistics Case Studies in Action?
Reach Out to Zipline Logistics
Request a Quote
We appreciate the opportunity to provide you with a quote. Please click Get Started in the box below and complete the Request a Quote form on that page. The appropriate Zipline Logistics Solution Consultant will contact you within 24 hours. If you have more general inquiries, please complete the contact us form or call us at 888.469.4754.
For general inquiries, please click Get Started in the box below and complete the Contact Us form on that page. The appropriate Zipline Logistics Solution Consultant will contact you within 24 hours. For additional questions, feel free to call us at 888.469.4754.
Carrier Qualification
If you would like to join our Carrier Network, please complete our Carrier Qualification Form by clicking on Get Started below. If you have more general inquiries, please complete the contact us form or call us at 888.469.4754
3PL Case Studies: Analyzing Successful Examples of Third-Party Logistics
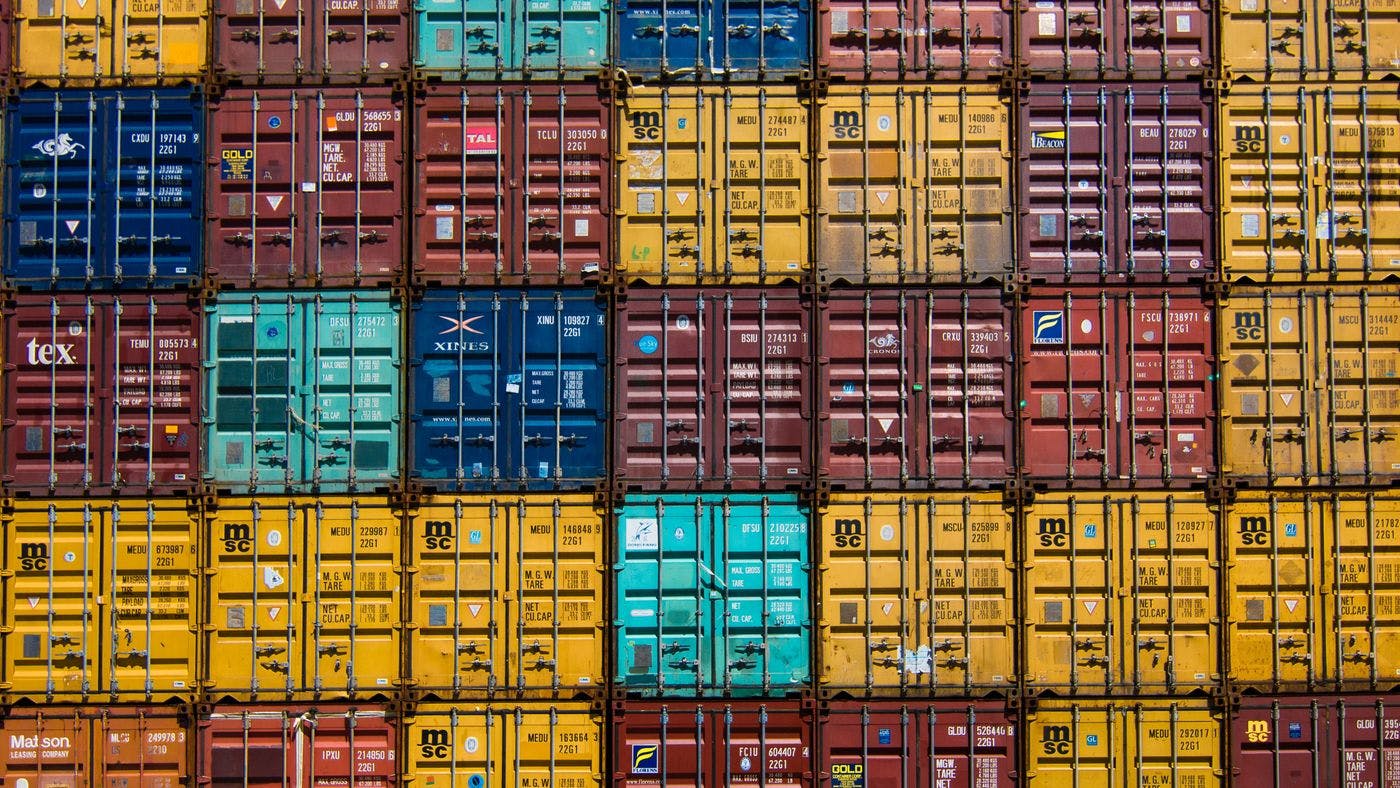
Introduction to 3PL: Understanding the Basics
In the ever-evolving world of logistics, businesses are constantly seeking ways to optimize their supply chain operations. This is where Third-Party Logistics (3PL) comes into play. 3PL refers to the outsourcing of logistics activities to a specialized service provider, allowing companies to focus on their core competencies while leveraging the expertise of a logistics partner.
What is 3PL and Why is it Important?
At its core, 3PL involves the integration of transportation, warehousing, and distribution services into a cohesive and efficient supply chain solution. By outsourcing these functions to a 3PL provider, businesses can benefit from their expertise, infrastructure, and technology, resulting in improved operational efficiency, reduced costs, and enhanced customer satisfaction.
One of the key advantages of 3PL is the scalability it offers. As businesses grow and expand, their logistics requirements become more complex. By partnering with a 3PL provider, companies can tap into a network of resources and capabilities, allowing them to adapt quickly to changing market demands and scale their operations seamlessly.
Benefits of Using 3PL Services
The decision to engage a 3PL provider comes with a wide range of benefits. Let's explore some of the advantages that businesses can gain by partnering with a 3PL:
Expertise and Specialization : 3PL providers are industry experts with extensive knowledge and experience in managing logistics operations. They possess the necessary skills and resources to streamline processes and optimize supply chain efficiency.
Cost Savings : By outsourcing logistics functions to a 3PL provider, businesses can reduce their capital expenditure on infrastructure, technology, and personnel. 3PL providers leverage economies of scale to offer cost-effective solutions, allowing companies to focus on their core business activities.
Flexibility and Scalability : As companies experience fluctuations in demand, a 3PL partner can adjust resources accordingly, ensuring optimal capacity utilization. This flexibility allows businesses to respond to market changes quickly and effectively.
Access to Technology and Innovation : 3PL providers invest in advanced technologies, such as warehouse management systems (WMS), transportation management systems (TMS), and real-time tracking tools. By leveraging these technologies, companies can gain visibility, traceability, and control over their supply chain operations.
Global Reach and Network : 3PL providers often have extensive networks and global reach, enabling businesses to expand their market reach and penetrate new regions. This global presence ensures seamless cross-border logistics and compliance with international regulations.
Key Players in the 3PL Industry
The 3PL industry comprises a diverse range of service providers, each offering unique capabilities and areas of specialization. Let's take a closer look at the key players in the 3PL industry:
Transportation Providers : These 3PL providers focus primarily on transportation services, including freight forwarding, trucking, air cargo, and ocean freight. They have expertise in managing the movement of goods across different modes of transportation and optimizing routes for cost and time efficiency.
Warehousing and Distribution Centers : Warehousing and distribution-focused 3PL providers offer storage, inventory management, order fulfillment, and distribution services. They operate warehouses strategically located to facilitate efficient product flow and ensure timely delivery.
Integrated Logistics Providers : Integrated logistics providers offer end-to-end supply chain solutions, combining transportation, warehousing, and value-added services. They provide comprehensive logistics solutions, from procurement to distribution, and often specialize in specific industries or verticals.
Freight Forwarders : Freight forwarders act as intermediaries between shippers and carriers, coordinating the movement of goods across international borders. They handle documentation, customs clearance, and logistics coordination, ensuring smooth international shipments.
Factors to Consider When Choosing a 3PL Provider
Selecting the right 3PL provider is crucial for achieving successful logistics outsourcing. To make an informed choice, businesses should consider the following factors:
Industry Expertise : Assess the 3PL provider's experience and track record in your specific industry. Look for providers with a deep understanding of your industry's unique requirements and challenges.
Infrastructure and Technology : Evaluate the provider's infrastructure, including warehouses, transportation fleet, and technology capabilities. Ensure they have the necessary resources and technology to meet your logistics needs effectively.
Network and Global Reach : Consider the provider's network and coverage. If you operate internationally or have plans for global expansion, choose a 3PL partner with a strong global presence and established international partnerships.
Service Level Agreements (SLAs) : Review the SLAs offered by the 3PL provider. Pay attention to key performance indicators (KPIs) such as on-time delivery, order accuracy, and inventory accuracy. Ensure their performance standards align with your business requirements.
Scalability and Flexibility : Assess the provider's ability to scale operations and adapt to your changing business needs. Ensure they can handle fluctuations in demand and offer flexible solutions to accommodate your growth.
By considering these factors, businesses can make an informed decision when selecting a 3PL provider, setting the stage for a successful logistics outsourcing partnership.
In the next section, we will delve into real-world case studies to explore how companies have leveraged 3PL services to optimize their supply chain operations and achieve tangible benefits.
Case Study 1: Company A - Streamlining Supply Chain Operations
Overview of company a.
Company A is a leading manufacturer of electronic goods with a global presence. With a diverse product portfolio and a wide customer base, the company faced numerous challenges in managing its supply chain operations efficiently. In an effort to streamline their logistics processes and improve overall supply chain performance, Company A decided to partner with a 3PL provider.
Challenges Faced by Company A
Before engaging the 3PL provider, Company A faced several key challenges in their supply chain operations:
Lack of Visibility : The company struggled with limited visibility across their supply chain, making it difficult to track inventory levels, anticipate demand fluctuations, and identify potential bottlenecks.
Inefficient Inventory Management : Company A had issues with inventory accuracy and control. Stockouts and overstocking problems were common, leading to increased carrying costs and missed sales opportunities.
Complex Transportation Network : With a global customer base, Company A had to manage complex transportation routes and multiple carriers, resulting in higher transportation costs and longer lead times.
Inadequate Warehouse Space : The company's existing warehouses were reaching capacity, hampering their ability to accommodate inventory growth and handle peak demand periods effectively.
Solution Provided by the 3PL Provider
To address these challenges, Company A partnered with a 3PL provider that specialized in supply chain optimization. The 3PL provider conducted a thorough analysis of Company A's supply chain operations and devised a comprehensive solution tailored to their specific needs.
The solution encompassed the following key elements:
Advanced Technology Integration : The 3PL provider implemented a robust Warehouse Management System (WMS) that provided real-time visibility into inventory levels, order status, and warehouse operations. This technology integration enhanced inventory accuracy, reduced stockouts, and improved order fulfillment efficiency.
Optimized Transportation Management : The 3PL provider leveraged their network of carriers and transportation expertise to optimize transportation routes, consolidate shipments, and negotiate favorable freight rates. This resulted in cost savings, reduced lead times, and enhanced overall transportation efficiency.
Warehouse Space Expansion : Recognizing the need for additional warehouse space, the 3PL provider recommended the strategic expansion of Company A's warehouse footprint. They identified suitable locations, designed efficient layouts, and managed the construction and setup of new warehouses, ensuring seamless integration with existing operations.
Demand Planning and Forecasting : The 3PL provider implemented advanced demand planning and forecasting tools, enabling Company A to anticipate demand patterns, optimize inventory levels, and improve supply chain responsiveness. Accurate demand forecasting helped the company reduce stockouts and minimize excess inventory.
Implementation of the 3PL Solution
The implementation phase involved close collaboration between Company A and the 3PL provider. The 3PL provider assigned a dedicated team of logistics experts who worked closely with Company A's supply chain and operations teams to ensure a smooth transition.
The implementation process included the following steps:
Data Collection and Analysis : The 3PL provider collected data on Company A's existing supply chain operations, including inventory levels, transportation routes, warehouse capacities, and historical sales data. They conducted a detailed analysis to identify areas for improvement and develop tailored solutions.
Solution Design : Based on the analysis, the 3PL provider designed a comprehensive solution that addressed Company A's specific challenges and goals. This included the selection and integration of appropriate technologies, optimization of transportation routes, and expansion of warehouse facilities.
Pilot Testing : Before full-scale implementation, the 3PL provider conducted pilot testing to validate the effectiveness of the proposed solution. This involved testing the WMS, transportation optimization algorithms, and demand forecasting models in a controlled environment to ensure accuracy and reliability.
Training and Change Management : The 3PL provider conducted training sessions for Company A's employees to familiarize them with the new systems, processes, and technologies. Change management strategies were implemented to ensure smooth adoption of the 3PL solution across the organization.
Results and Benefits Achieved
As a result of partnering with the 3PL provider and implementing their tailored solution, Company A experienced significant improvements in their supply chain operations. The key benefits achieved were:
Enhanced Visibility : The implementation of the WMS provided Company A with real-time visibility into their inventory levels, order status, and warehouse operations. This visibility allowed for proactive decision-making, improved inventory accuracy, and better demand planning.
Improved Inventory Management : With the demand planning and forecasting tools, Company A was able to optimize their inventory levels, reducing stockouts and overstocking. This led to lower carrying costs, improved order fulfillment rates, and increased customer satisfaction.
Cost Savings : The optimized transportation management solution resulted in cost savings for Company A. By consolidating shipments, negotiating better freight rates, and optimizing transportation routes, the company achieved significant reductions in transportation costs.
Increased Warehouse Capacity : The strategic warehouse space expansion recommended by the 3PL provider allowed Company A to accommodate their growing inventory needs and handle peak demand periods more efficiently. This expansion improved overall warehouse utilization and reduced the risk of capacity constraints.
The successful partnership with the 3PL provider not only streamlined Company A's supply chain operations but also positioned them for future growth and improved customer service. By leveraging the expertise and capabilities of the 3PL provider, Company A achieved substantial operational improvements and gained a competitive edge in the market.
Case Study 2: Company B - Optimizing Inventory Management
Overview of company b.
Company B is a global retail giant with an extensive product portfolio, serving customers across various channels. With a vast network of suppliers and distribution centers, the company faced significant challenges in managing their inventory effectively. In order to improve inventory management, reduce costs, and enhance customer satisfaction, Company B decided to leverage the expertise of a 3PL provider.
Experience the Cybership Advantage!
Unlock your businesses true potential with Cybership, your trusted 3PL partner. Streamline logistics, focus on growth, and ensure efficient order fulfillment. Partner with us today and elevate your business to new heights.
Inventory Management Issues Faced by Company B
Before partnering with the 3PL provider, Company B encountered several key inventory management challenges:
Excessive Inventory Levels : Company B struggled with maintaining optimal inventory levels, resulting in high carrying costs and the risk of obsolescence. Inaccurate demand forecasting and inefficient replenishment processes contributed to this issue.
Stockouts and Lost Sales : Inadequate inventory management practices led to frequent stockouts, causing lost sales opportunities and customer dissatisfaction. Inaccurate inventory data and lack of real-time visibility contributed to this challenge.
Inefficient Replenishment Processes : Company B's replenishment processes were time-consuming and lacked automation. Manual order processing, delayed supplier communication, and inconsistent lead times impacted the efficiency of inventory replenishment.
Lack of Inventory Accuracy : The company faced challenges in maintaining accurate inventory records across their distribution centers, resulting in discrepancies between system inventory and physical stock. This led to inefficiencies in order fulfillment and increased costs.
3PL Solution for Inventory Optimization
To address these inventory management challenges, Company B partnered with a 3PL provider specializing in inventory optimization. The 3PL provider conducted a thorough analysis of Company B's inventory management processes and designed a comprehensive solution to improve efficiency and accuracy.
The solution included the following key elements:
Demand Forecasting and Analysis : The 3PL provider implemented advanced demand forecasting models, leveraging historical sales data, market trends, and seasonality patterns. This enabled Company B to generate more accurate demand forecasts, leading to improved inventory planning and optimization.
Inventory Visibility and Real-time Tracking : The 3PL provider implemented a robust inventory management system that provided real-time visibility into inventory levels across all distribution centers. This allowed Company B to track inventory movements, monitor stock levels, and identify potential issues proactively.
Automated Replenishment Processes : The 3PL provider automated the replenishment processes, integrating Company B's systems with suppliers and streamlining order processing. This automation reduced manual errors, improved communication with suppliers, and accelerated the replenishment cycle.
ABC Analysis and SKU Rationalization : The 3PL provider conducted an ABC analysis to classify Company B's products based on their sales contribution. This analysis helped identify slow-moving and obsolete items, enabling the company to rationalize their SKU portfolio and optimize inventory levels accordingly.
Integration and Collaboration with the 3PL Provider
Successful implementation of the 3PL solution required close integration and collaboration between Company B and the 3PL provider. The integration process involved the following steps:
Data Integration : The 3PL provider worked closely with Company B's IT team to integrate their inventory management systems, demand forecasting tools, and supplier databases. This facilitated seamless data exchange and information sharing between the two entities.
Process Alignment : The 3PL provider conducted workshops and training sessions to align Company B's employees with the new inventory management processes and systems. This ensured smooth adoption and collaboration between the internal teams and the 3PL provider.
Performance Monitoring and KPIs : Key performance indicators (KPIs) were defined to monitor the effectiveness of the solution. These KPIs included metrics such as inventory turnover, stockout rates, order fulfillment accuracy, and carrying costs. Regular performance reviews were conducted to identify areas for improvement and optimize inventory management further.
Continuous Improvement Initiatives : The 3PL provider worked closely with Company B's teams to identify opportunities for continuous improvement. This involved analyzing data, identifying bottlenecks, and implementing process enhancements to further optimize inventory management.
Improved Inventory Management and Cost Savings
Through the partnership with the 3PL provider and the implementation of their tailored solution, Company B achieved significant improvements in inventory management and cost savings. The key outcomes and benefits included:
Optimized Inventory Levels : By leveraging advanced demand forecasting models and implementing inventory visibility tools, Company B achieved optimal inventory levels. This resulted in reduced carrying costs, minimized stockouts, and improved order fulfillment rates.
Enhanced Customer Satisfaction : With accurate inventory data and real-time visibility, Company B was able to meet customer demands promptly, reducing the occurrence of backorders and improving overall customer satisfaction.
Streamlined Replenishment Processes : The automated replenishment processes reduced manual errors, improved communication with suppliers, and accelerated the order processing cycle. This led to faster replenishment times, reduced lead times, and increased operational efficiency.
SKU Rationalization and Cost Reduction : Through the ABC analysis and SKU rationalization, Company B identified slow-moving and obsolete items, enabling them to reduce excess inventory and optimize their SKU portfolio. This resulted in cost savings and improved inventory turnover.
The collaboration with the 3PL provider not only transformed Company B's inventory management practices but also positioned them for future growth and improved profitability. By leveraging the expertise and technology of the 3PL provider, Company B achieved significant improvements in inventory efficiency, cost savings, and customer satisfaction.
Case Study 3: Company C - Enhancing Last-Mile Delivery
Overview of company c.
Company C is a leading e-commerce company with a vast customer base and a strong presence in the online retail industry. As the demand for online shopping continues to surge, Company C faced challenges in meeting customer expectations for fast and efficient last-mile delivery. In order to enhance their last-mile delivery operations and improve customer satisfaction, Company C decided to partner with a 3PL provider specializing in innovative last-mile solutions.
Last-Mile Delivery Challenges Faced by Company C
Before engaging the 3PL provider, Company C encountered several key challenges in their last-mile delivery operations:
Delivery Time and Speed : The rapid growth of e-commerce led to increased customer expectations for fast and timely deliveries. Company C struggled to meet these expectations, resulting in delayed deliveries and customer dissatisfaction.
Route Optimization : Company C's delivery routes were suboptimal, resulting in longer transit times, inefficient fuel consumption, and increased delivery costs. The lack of advanced routing and tracking tools hindered their ability to optimize routes effectively.
Customer Communication : Limited communication and transparency in the delivery process led to customer frustration. Company C needed a solution to provide real-time updates and notifications to customers, improving their overall delivery experience.
Last-Mile Logistics Capacity : As the order volume increased, Company C faced challenges in expanding their last-mile logistics capacity. They needed a scalable solution to handle peak demand periods and ensure timely deliveries.
Innovative Last-Mile Solution by the 3PL Provider
To address these last-mile delivery challenges, Company C partnered with a 3PL provider known for its innovative last-mile solutions. The 3PL provider conducted a thorough analysis of Company C's delivery processes and designed a comprehensive solution to enhance last-mile operations.
Route Optimization and Tracking Tools : The 3PL provider implemented advanced routing and tracking software, enabling Company C to optimize delivery routes based on real-time traffic conditions, delivery constraints, and customer preferences. This technology allowed for efficient routing, reduced transit times, and improved fuel efficiency.
Real-Time Customer Communication : The 3PL provider implemented a customer communication platform that provided real-time delivery updates and notifications to customers. This allowed customers to track their deliveries, receive estimated arrival times, and make necessary arrangements if needed.
Crowdsourced Delivery Network : Recognizing the need for scalability and flexibility, the 3PL provider introduced a crowdsourced delivery network. This network comprised of independent contractors who could fulfill delivery orders during peak periods, ensuring timely deliveries and increased capacity.
Innovative Delivery Options : The 3PL provider introduced innovative delivery options such as same-day delivery, time-slot delivery, and alternative pickup locations. These options provided customers with flexibility and convenience, improving their overall delivery experience.
Implementation and Integration of the Last-Mile Solution
The successful implementation of the last-mile solution required close collaboration between Company C and the 3PL provider. The implementation process involved the following steps:
Data Integration and System Configuration : The 3PL provider worked closely with Company C's IT team to integrate their systems, including order management, inventory, and tracking systems. This integration ensured seamless data exchange and real-time visibility into delivery operations.
Driver Onboarding and Training : The 3PL provider onboarded and trained the independent contractors who would be part of the crowdsourced delivery network. This included training on delivery protocols, customer service, and the use of the tracking and communication tools.
Continuous Monitoring and Performance Management : The 3PL provider implemented a robust performance management system to monitor the performance of the delivery network. Key performance indicators (KPIs) such as on-time delivery, customer satisfaction, and delivery cost were tracked and reviewed regularly for continuous improvement.
Customer Feedback and Iterative Enhancements : Company C and the 3PL provider actively sought customer feedback to identify areas for improvement. Based on this feedback and data analysis, iterative enhancements were made to the last-mile solution to further optimize delivery operations and customer satisfaction.
Enhanced Last-Mile Delivery Efficiency and Customer Satisfaction
Through the partnership with the 3PL provider and the implementation of their innovative last-mile solution, Company C achieved significant improvements in last-mile delivery efficiency and customer satisfaction. The key outcomes and benefits included:
Faster and More Reliable Deliveries : The implementation of route optimization and tracking tools enabled Company C to improve delivery time and speed. Reduced transit times and optimized routes ensured faster and more reliable deliveries, meeting customer expectations for timely service.
Improved Customer Communication : The real-time customer communication platform allowed Company C to provide accurate and timely delivery updates to customers. This enhanced transparency and improved customer satisfaction by keeping them informed throughout the delivery process.
Scalability and Flexibility : The introduction of the crowdsourced delivery network provided Company C with the scalability and flexibility needed to handle peak demand periods. This ensured increased capacity during busy seasons, allowing the company to meet customer demands effectively.
Enhanced Delivery Options : The innovative delivery options, such as same-day delivery and time-slot delivery, provided customers with greater flexibility and convenience. The availability of alternative pickup locations further improved the overall delivery experience for customers.
The partnership with the 3PL provider not only transformed Company C's last-mile delivery operations but also positioned them as a leader in customer-centric logistics. By leveraging the expertise and technology of the 3PL provider, Company C achieved significant improvements in last-mile delivery efficiency, customer satisfaction, and competitive advantage in the e-commerce industry.
Conclusion: Key Takeaways and Lessons Learned
The case studies presented in this blog post highlight the transformative impact of 3PL services on supply chain operations. By partnering with specialized third-party logistics providers, companies like Company A, Company B, and Company C were able to overcome their specific challenges and achieve significant improvements in their respective areas of focus.
Summary of the 3PL Case Studies
Let's recap the key takeaways and lessons learned from the case studies:
Company A - Streamlining Supply Chain Operations : Company A's partnership with a 3PL provider enabled them to streamline their supply chain operations by implementing advanced technology, optimizing transportation management, and expanding warehouse space. The result was enhanced visibility, improved inventory management, and cost savings.
Company B - Optimizing Inventory Management : Company B's collaboration with a 3PL provider led to optimized inventory levels, improved customer satisfaction, and cost reduction. By leveraging advanced demand forecasting, enhanced inventory visibility, and automated replenishment processes, Company B achieved efficiency and accuracy in inventory management.
Company C - Enhancing Last-Mile Delivery : Company C's partnership with a 3PL provider resulted in faster and more reliable last-mile deliveries, improved customer communication, scalability through a crowdsourced delivery network, and enhanced delivery options. The innovative last-mile solution led to increased customer satisfaction and operational efficiency.
Common Success Factors in 3PL Implementation
While each case study presented unique challenges and solutions, there were common success factors that contributed to the positive outcomes:
Collaborative Partnership : A strong collaboration between the company and the 3PL provider is essential for successful implementation. Close integration, effective communication, and shared goals drive alignment and ensure a smooth transition.
Tailored Solutions : Each company's supply chain is unique, requiring tailored solutions to address specific challenges. A thorough analysis of existing processes and a customized approach are crucial in designing effective 3PL solutions.
Advanced Technology Adoption : Leveraging advanced technology, such as warehouse management systems, demand forecasting tools, and real-time tracking, enables companies to gain visibility, optimize processes, and enhance overall supply chain performance.
Continuous Improvement Mindset : Implementing 3PL solutions is not a one-time fix but an ongoing process. Regular monitoring, performance management, and feedback collection allow for continuous improvement and optimization.
Considerations for Implementing 3PL Solutions
When considering the implementation of 3PL solutions, companies should keep the following considerations in mind:
Alignment with Business Objectives : Clearly define the objectives and expected outcomes of engaging a 3PL provider. Ensure that the chosen provider aligns with your strategic goals and has the expertise and capabilities to meet your specific needs.
Evaluation of Provider Expertise : Conduct a thorough evaluation of the 3PL provider's industry experience, track record, and specialization. Look for providers with a proven record of success in addressing challenges similar to yours.
Integration and Communication : Seamless integration of systems, processes, and teams is crucial for successful implementation. Effective communication and information sharing between the company and the 3PL provider facilitate collaboration and ensure smooth operations.
Performance Metrics and KPIs : Establish clear performance metrics and key performance indicators (KPIs) to monitor the effectiveness of the 3PL solution. Regularly review and analyze these metrics to identify areas for improvement and drive continuous optimization.
Future Trends in the 3PL Industry
The 3PL industry continues to evolve, driven by technological advancements, changing customer expectations, and emerging market trends. Some of the future trends that companies should be aware of include:
E-commerce Expansion : As e-commerce continues to grow, 3PL providers will play a crucial role in enabling fast and efficient order fulfillment, last-mile delivery, and returns management.
Automation and Robotics : The adoption of automation and robotics in warehouses and fulfillment centers will increase, leading to improved efficiency, accuracy, and productivity in logistics operations.
Data Analytics and Artificial Intelligence : The use of data analytics and artificial intelligence (AI) will become more prevalent in supply chain optimization, demand forecasting, route optimization, and inventory management.
Sustainable Logistics : Environmental sustainability will be a key focus in the 3PL industry. Companies will increasingly seek 3PL providers that offer eco-friendly solutions, such as electric vehicles, alternative fuels, and sustainable packaging.
Final Thoughts
The case studies presented in this blog post demonstrate the significant impact that 3PL services can have on supply chain operations. From streamlining supply chain processes to optimizing inventory management and enhancing last-mile delivery, partnering with a specialized 3PL provider can drive operational efficiency, cost savings, and improved customer satisfaction.
As businesses continue to face new challenges and market dynamics, the role of 3PL providers will become increasingly vital in navigating complex supply chains. By carefully selecting the right 3PL partner, aligning objectives, and embracing technological advancements, companies can position themselves for success in an ever-evolving logistics landscape.
Toggle theme Compare Providers
This site uses cookies to improve your experience. By viewing our content, you are accepting the use of cookies. To help us insure we adhere to various privacy regulations, please select your country/region of residence. If you do not select a country we will assume you are from the United States. View our privacy policy and terms of use.
- Materials Handling
- Tracking and Tracing

“A3” is an Obligation for the Coach
The Lean Thinker
FEBRUARY 9, 2021
We had case studies , exercises , all in an effort to teach people to be better problem solvers. .” They teach “problem solving” courses so people can learn to do this properly. I have developed, and delivered, a couple of those back when I was working in internal continuous improvement offices.

3 Ways to Benchmark to Boost Supply Chain Performance
Logistics Bureau
APRIL 19, 2021
If you’ve never done a benchmarking exercise before, read on. Case Study : An Automotive Parts Business. This exercise would involve you measuring particular functions or aspects of your business and comparing that against other parts of your business. The Benefits of Benchmarking. Informal Benchmarking.
This site is protected by reCAPTCHA and the Google Privacy Policy and Terms of Service apply.
Trending Sources
- The Logistics of Logistics
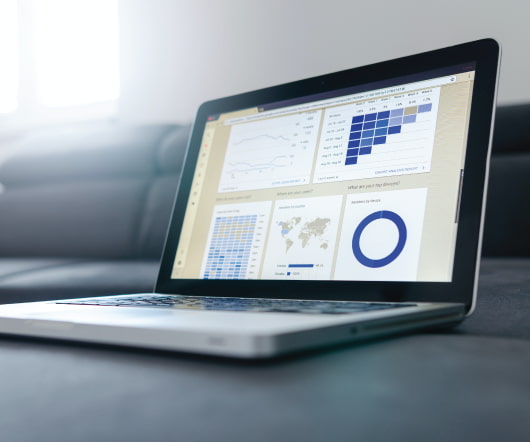
Condition Monitoring- A Case Study-Part II
Infosys Supply Chain Management
JULY 31, 2014
None of the fleet engineers understood the actual intent of the data collection, neither did they appreciate the whole exercise , actually none of the stake holders did! Anything over and above this and which did not contribute directly to the improvement of such PM programs were deemed as wasteful exercise .
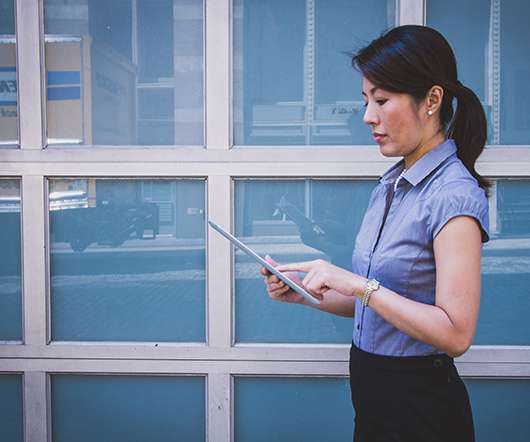
JANUARY 15, 2015
The purpose is sometimes not known well, as in this case the maintenance teams were completely cutoff from the mainstream use of the Asset data. None of the fleet engineers understood the actual intent of the data collection, neither did they appreciate the whole exercise .
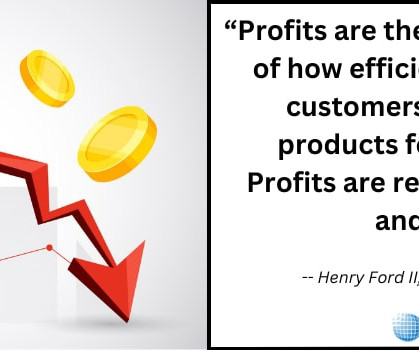
Cost to Serve Analysis—And the Costs of Neglecting It
SEPTEMBER 4, 2023
View case study Learn more about cost-to-serve benefits. If you haven’t done a segmentation exercise , that would be a positive first step towards understanding customer profitability. So, for now, I will leave you with a final reminder of the case study I mentioned earlier in this article.
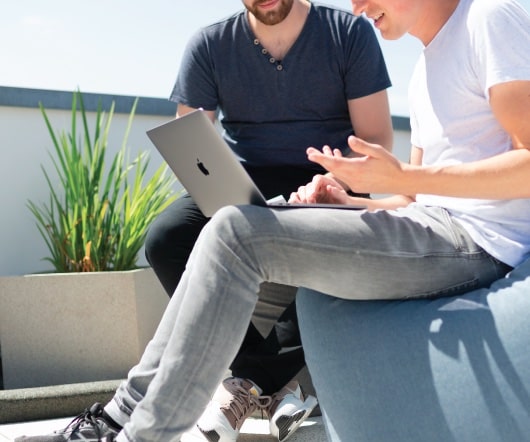
5 Mini Case Studies: Successful Supply Chain Cost Reduction and Management
SEPTEMBER 26, 2018
The following five mini case studies explore a few high-profile companies that have managed to sustain their supply chain cost reduction efforts and keep expenses under control. Of course, the above case studies are merely summaries of the changes these high-profile brands made to their supply chains.
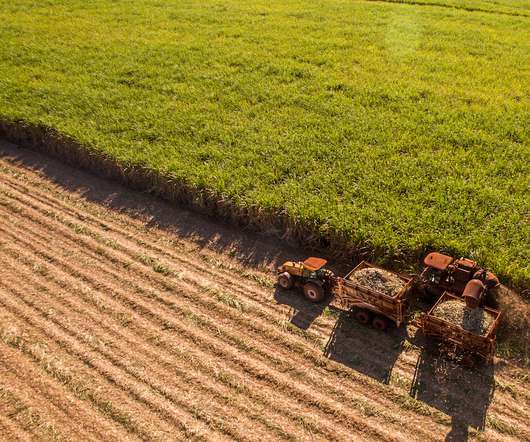
S&OP in Agribusiness: How to Harvest the Benefits with Advanced Analytics
JULY 23, 2019
Decision-making goes from a highly tedious and error-prone exercise to a process that combines computational intelligence with the business knowledge needed to analyze the optimizer’s results. Read our case study to find out how Tereos Sugar & Energy Brazil has improved its S&OP Process with optimization technology.
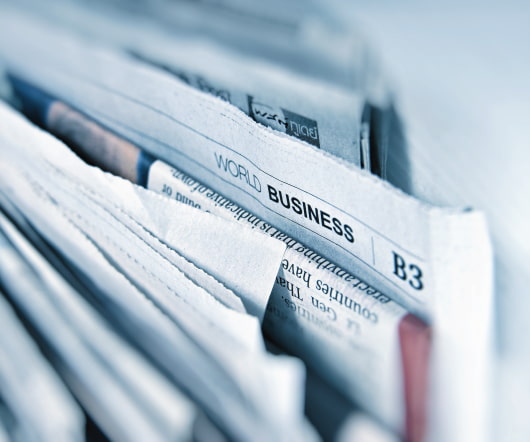
Decision-making goes from a highly tedious and error-prone exercise to a process that combines computational intelligence with the business knowledge needed to analyze the optimizer’s results. Download our case study to find out how Tereos Sugar & Energy Brazil has improved its S&OP Process with optimization technology.
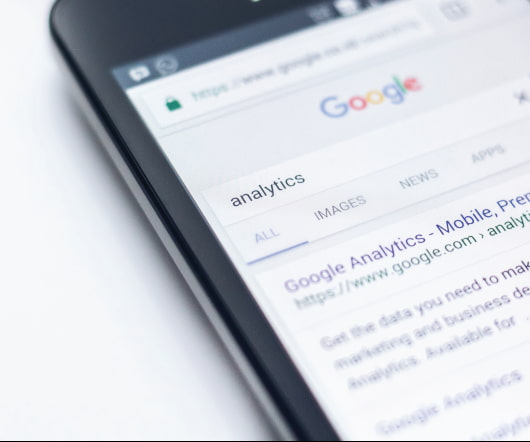
7 Mini Case Studies: Successful Supply Chain Cost Reduction and Management
MAY 24, 2019
The following five mini case studies explore a few high-profile companies that have managed to sustain their supply chain cost-reduction efforts and keep expenses under control. Of course, the above case studies are merely summaries of the changes these high-profile brands made to their supply chains. Sunsweet Growers.
The ‘So What’ of my experiences in East Timor – Reflections on East Timor by a Logistics Unit Commander Part 4
Logistics in War
OCTOBER 4, 2019
At the operational and tactical level, East Timor may not be a great case study for combat arms officers however for the logistician, there are lessons to be learned at every level from the Commander Joint Logistics down to the private soldier. And this is more than the biennial Exercise Talisman Sabre. Cost-capture.
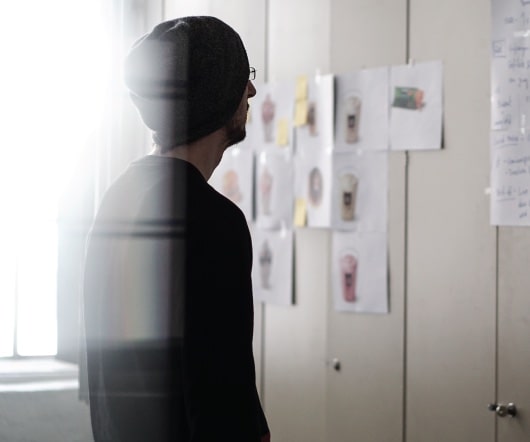
The five most popular ‘Logistics In War’ posts of 2017
DECEMBER 26, 2017
It describes the importance of logistics considerations in force design though two case studies – the US Army development of its SBCT capability, and the Australian Army’s recent history of change. USMC MV-22 Osprey during Exercise Talisman Sabre 2017 – Photo by Department of Defence.
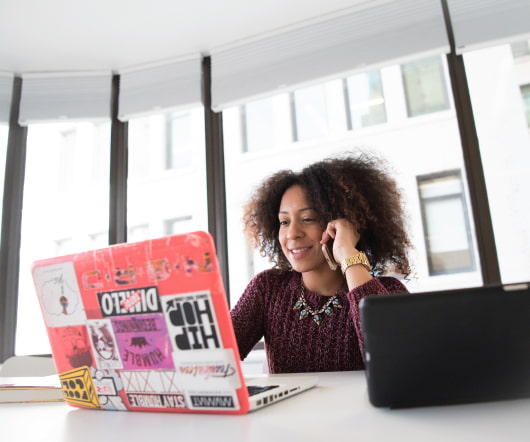
Where Does Supply Chain Design End and Planning Begin? (Takeaways from LLamasoft’s SummerCon 2017 Conference)
Talking Logistics
JUNE 29, 2017
The first one arrived a few years ago when a growing number of companies started treating supply chain design as a continuous business process instead of a standalone project or a once-a-year exercise . Overall, the sessions were all very insightful and informative.
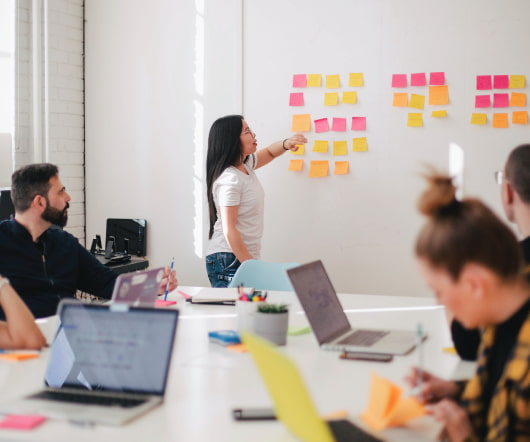
Logistics KPIs Case Study: Whirlpool’s Supply Chain and Logistics Success Driven by Effective KPI Implementation
GlobalTranz
OCTOBER 29, 2015
We conclude our ongoing series in talking about effective KPI management by giving you a real live Logistics KPIs management case study from Whirlpool's engagement with a logistics service level provider. We hope the following case study shows you the proverbial proof in the pudding of effective Logistics KPIs management. .
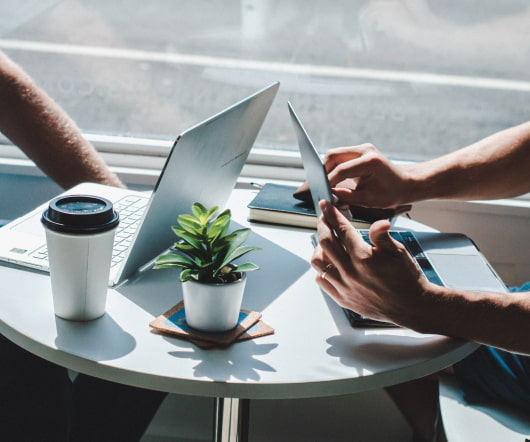
‘The furthest, the weakest’ – how logistics creates national power
AUGUST 28, 2018
It is unsurprising that a recent USPACOM exercise highlights the vital importance of strategic and operational lift in this environment. One need only refer to Kenneth Privratsky’s Logistics in the Falklands War: A case study in expeditionary warfare to get a sense of the logistics factors at play.
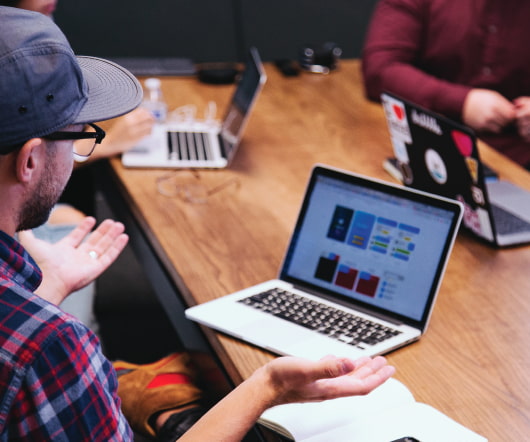
‘The furthest, the weakest’ – how logistics and distance influence national power
MAY 16, 2018
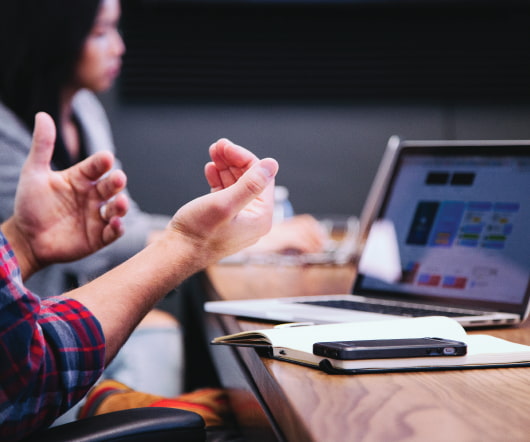
Case Study: Cloud-based WMS Works for Media Provider
Logistics Business Magazine
FEBRUARY 19, 2018
But newly released functionality in ProSKU now means that multiple items can be bulk-picked in one exercise and then sorted into individual orders. The post Case Study : Cloud-based WMS Works for Media Provider appeared first on Logistics Business® Magazine. The new process saves time and increases accuracy and efficiency.
7 Reasons Why the Supply Chain Matters to Business Success
JANUARY 9, 2019
Mini Case Study : Walmart. If your supply chain network design has not been under the microscope, and you care about business success, it’s probably time to consider the benefits of a design review and optimisation exercise . Mini Case Study : Whirlpool.
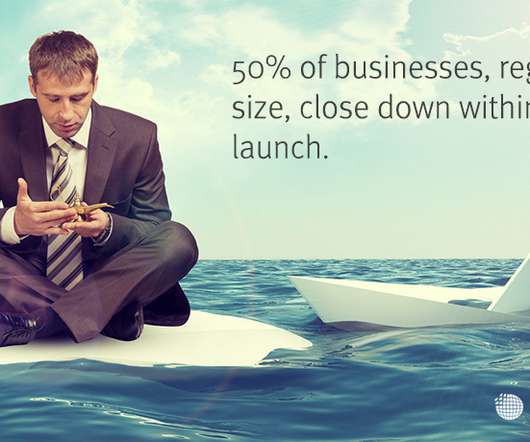
8 Reasons Why Your Business’ Success Depends Upon Your Supply Chain
JANUARY 7, 2020
Condition Monitoring- A Case Study-Part I
Here''s presenting the case study of how a seemingly workable condition monitoring exercise can possibly go wrong. The case company had procured a fleet of excavators and pipe layer equipment for their interstate gas pipeline project.
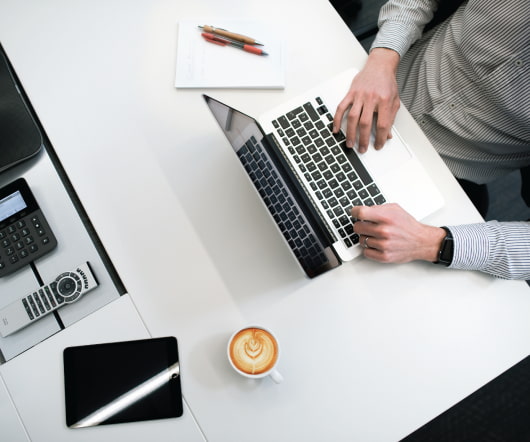
Supply Chain Management:Importance of Proactive Master Data.
JULY 26, 2013
Case Studies . |. This exercise was done before the monthly planning cycle start. This exercise yield positive results, in terms of planning community getting their confidence back in APO system & overall solution, over a period of time. Mobile Banking. Payments Treasury. Wealth Management. View all Infosys blogs.
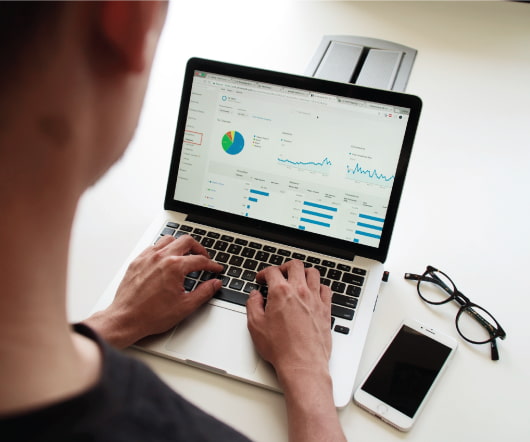
Business Process Optimization in Asset Management - Infosys Blogs
JUNE 20, 2013
Case Studies . |. Following are some of the key considerations which I think an organization should make to reap benefits from an optimization exercise in Asset management. Companys managements view of Asset management as a mere liability creating exercise needs to change. Mobile Banking. Payments Treasury. Offerings. |.
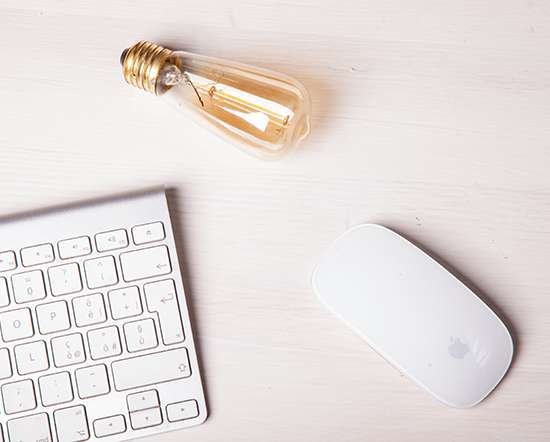
Supply Chain Management:Confluence of IT and Business Strategy.
MAY 21, 2012
Case Studies . |. These forms key contributors to an effective transformation exercise . They are an integral unit for success of any transformation exercise and should go hand in hand. Mobile Banking. Payments Treasury. Wealth Management. View all Infosys blogs. Supply Chain Management. Features & Opinions. |.
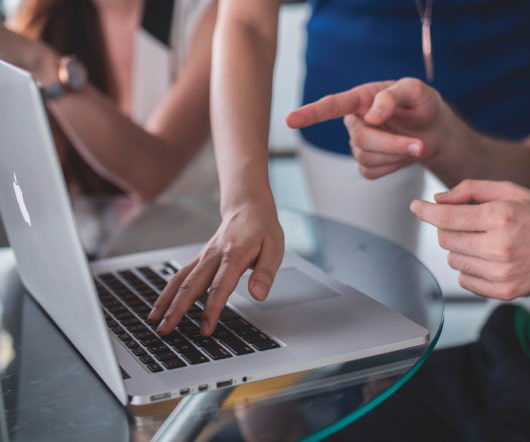
Supply Chain Management:The Upcoming 2011 Holiday Buying.
NOVEMBER 1, 2011
Case Studies . |. Mobile Banking. Payments Treasury. Wealth Management. View all Infosys blogs. Supply Chain Management. Features & Opinions. |. Offerings. |. White Papers. |. News & Events. |. The Infosys global supply chain management blog enables leaner supply chains through process and IT related interventions.
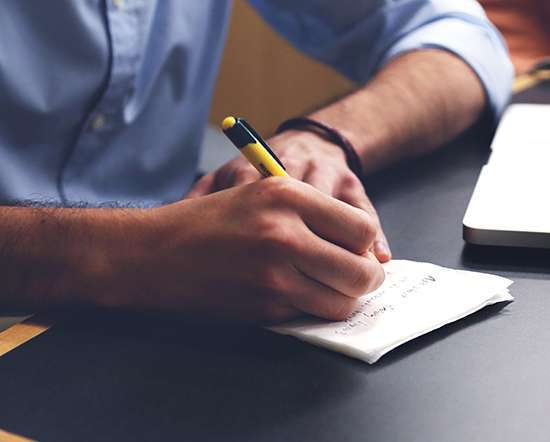
Supply Chain Management:'Asset' in Enterprise Asset Management
JULY 3, 2012
Case Studies . |. You do regular exercise to ensure frequency of your breakdown can be reduced or you take your kid for scheduled vaccinations - Preventive Maintenance. Mobile Banking. Payments Treasury. Wealth Management. View all Infosys blogs. Supply Chain Management. Features & Opinions. |. Offerings. |. White Papers. |.
Supply Chain Management:A New Lens for Supply Chain Roadmaps
FEBRUARY 8, 2012
Case Studies . |. Enterprise transformations are a multi-year exercise in the making. Mobile Banking. Payments Treasury. Wealth Management. View all Infosys blogs. Supply Chain Management. Features & Opinions. |. Offerings. |. White Papers. |. News & Events. |.
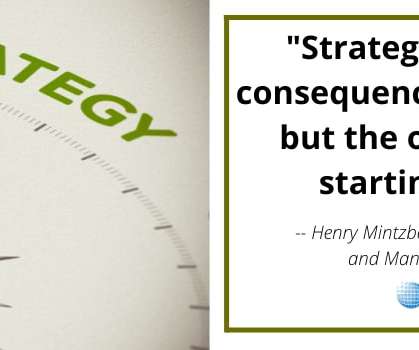
No Supply Chain Strategy? Here’s How to Develop One
JULY 18, 2022
The added benefit of working with such a partner is that because they collect performance data from hundreds of companies, they can help you choose the most appropriate key performance indicators to use in your benchmarking exercise . They can also aid you in identifying and implementing best practices to further your performance objectives.
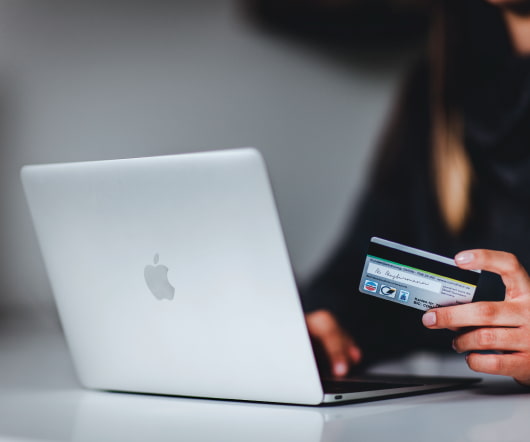
Supply Chain Management:Face book, Twitter and Asset Management
JUNE 20, 2012
Case Studies . |. EAM can often become a tedious exercise for a public organization due to its inherent nature of spread and unavailability of dedicated workforce for continuous monitoring of Assets. Mobile Banking. Payments Treasury. Wealth Management. View all Infosys blogs. Supply Chain Management. Features & Opinions. |.
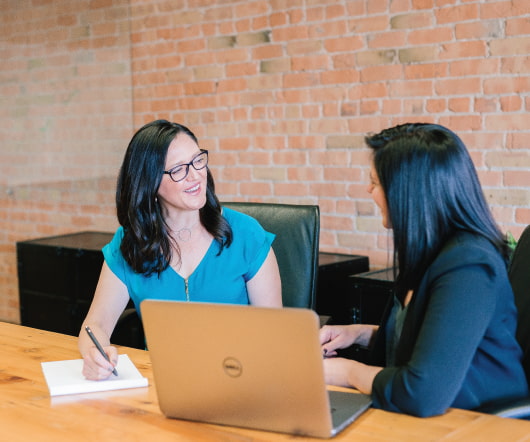
Planning to sustain the force – Reflections on East Timor by a Logistics Unit Commander Part Two
SEPTEMBER 21, 2019
At the operational and tactical level, East Timor may not be a great case study for combat arms officers however for the logistician, there are lessons to be learned at every level from the Commander Joint Logistics down to the private soldier. This would not be like a month-long exercise in the local training area.
Swinging into action – reflections on East Timor by a logistics Unit Commander Part Three
SEPTEMBER 25, 2019
At the operational and tactical level, East Timor may not be a great case study for combat arms officers however for the logistician, there are lessons to be learned at every level from the Commander Joint Logistics down to the private soldier. The proposal was denied.
Supply Chain Management:Headline for the 2012 Holiday Buying.
NOVEMBER 16, 2012
Case Studies . |. As was the case last year, the 2012 holiday buying season will be very much about the continued leveraging power of consumers in exercising multi-channel buying preferences and technology-enabled online tools. Mobile Banking. Payments Treasury. Wealth Management. View all Infosys blogs. Offerings. |.
Stay Connected
Join 84,000+ Insiders by signing up for our newsletter
- Participate in Logistics Brief
- Add a Source
- Add a Resource
- 2019 Logistics Brief MVP Awards
- 2020 Logistics Brief MVP Awards
- 2021 Logistics Brief MVP Awards
- 2022 Logistics Brief MVP Awards
- Mon. Apr 22
- Sun. Apr 21
- Fri. Apr 19
- Thu. Apr 18
- Apr 13 - Apr 19
- Supply Chains
- Distribution
- Transportation
- More Topics

Input your email to sign up, or if you already have an account, log in here!
Enter your email address to reset your password. a temporary password will be e‑mailed to you., be in the know on, logistics brief.
Expert insights. Personalized for you.
We organize all of the trending information in your field so you don't have to. Join 84,000+ users and stay up to date on the latest articles your peers are reading.

Get the good stuff
Subscribe to the following Logistics Brief newsletters:
You must accept the Privacy Policy and Terms & Conditions to proceed.

You know about us, now we want to get to know you!
Check your mail, we've sent an email to . please verify that you have received the email..
We have resent the email to
Let's personalize your content
Use social media to find articles.
We can use your profile and the content you share to understand your interests and provide content that is just for you.
Turn this off at any time. Your social media activity always remains private.
Let's get even more personalized
Choose topics that interest you., so, what do you do.
Are you sure you want to cancel your subscriptions?
Cancel my subscriptions
Don't cancel my subscriptions
Changing Country?
Accept terms & conditions.
It looks like you are changing your country/region of residence. In order to receive our emails, you must expressly agree. You can unsubscribe at any time by clicking the unsubscribe link at the bottom of our emails.
You appear to have previously removed your acceptance of the Terms & Conditions.

We noticed that you changed your country/region of residence; congratulations! In order to make this change, you must accept the Aggregage Terms and Conditions and Privacy Policy. Once you've accepted, then you will be able to choose which emails to receive from each site .
You must choose one option
Please choose which emails to receive from each site .
- Update All Sites
- Update Each Site
Please verify your previous choices for all sites
Sites have been updated - click Submit All Changes below to save your changes.
We recognize your account from another site in our network , please click 'Send Email' below to continue with verifying your account and setting a password.
You must accept the Privacy Policy and Terms & Conditions to proceed.
This is not me
Success Stories
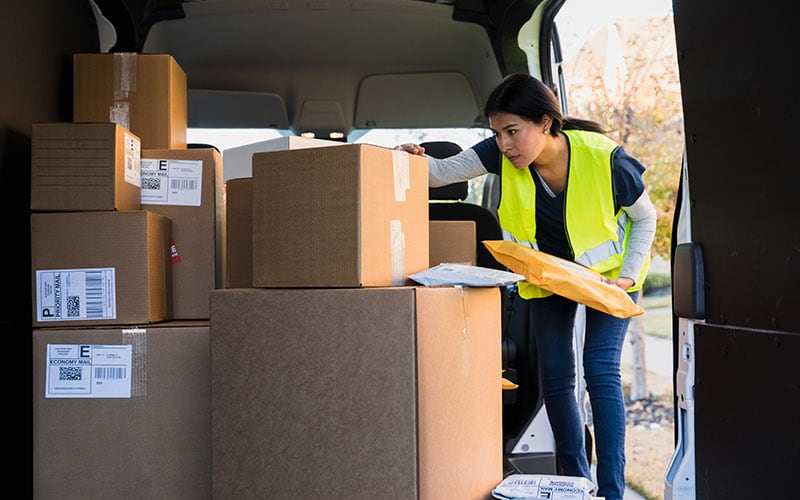
Posten Norge Service Integration and Management
- a.prlst-para')[this.getAttribute('data-index')].href, encodeURIComponent(this.getAttribute('data-title')));" class="share">
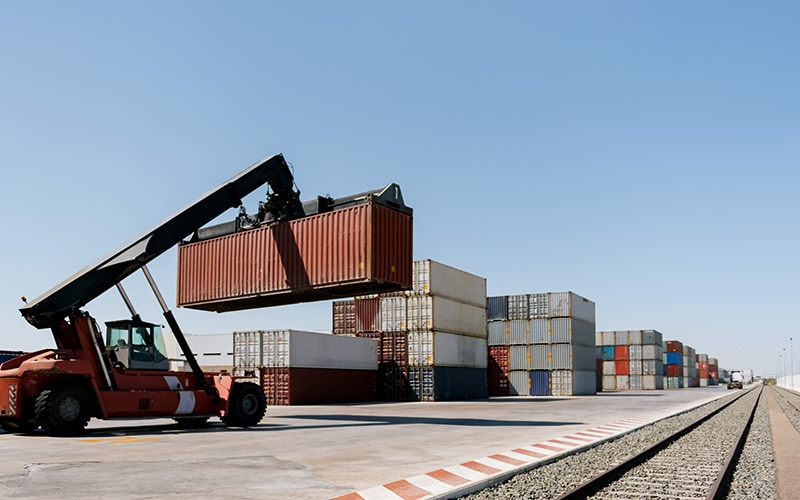
Infosys Consulting leading CSX’s financial transformation program to help propel them into a new digital future
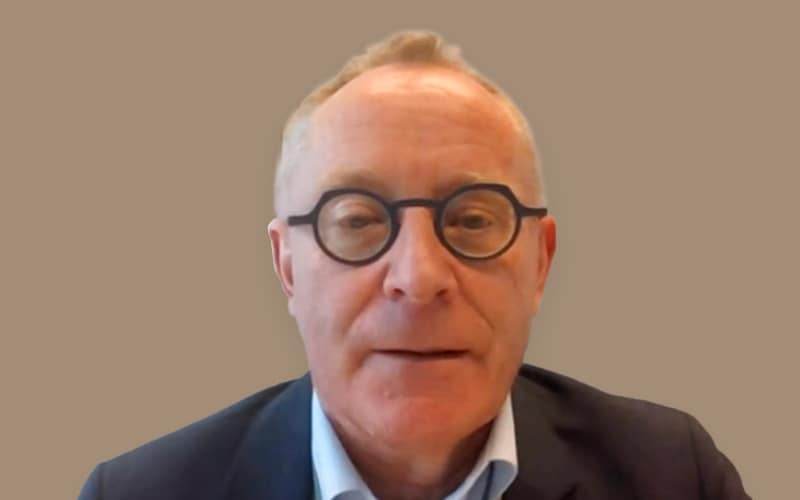
Client Testimonial
Infosys provides Managed Protection, Detection and Response to bpost (Belgian Post Group)
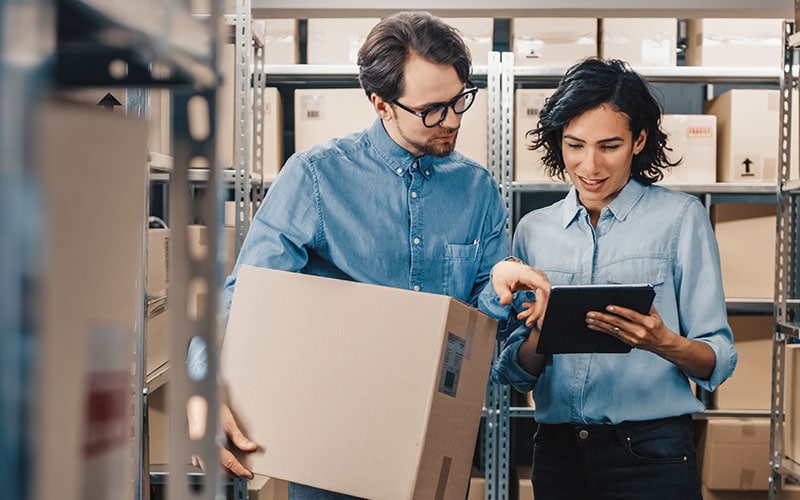
Route Optimization For Canadian Postal Service Company: Planning, Scheduling & Routing Optimization
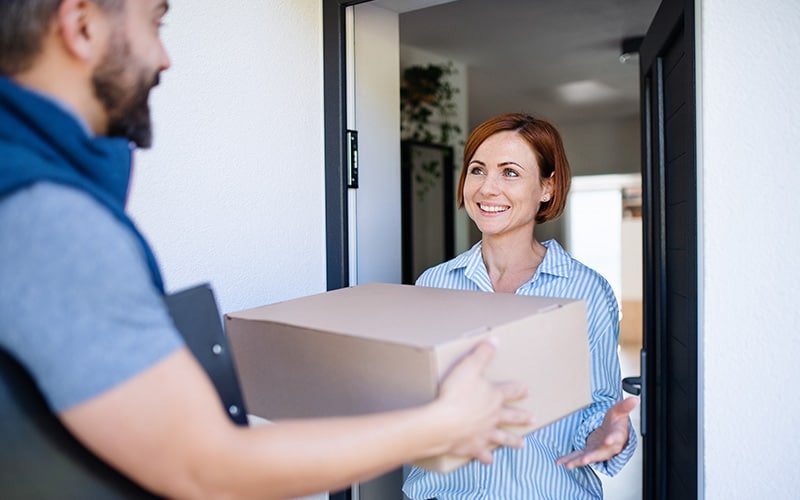
Testimonial
Finnish Postal Service reinvents itself with digital technologies
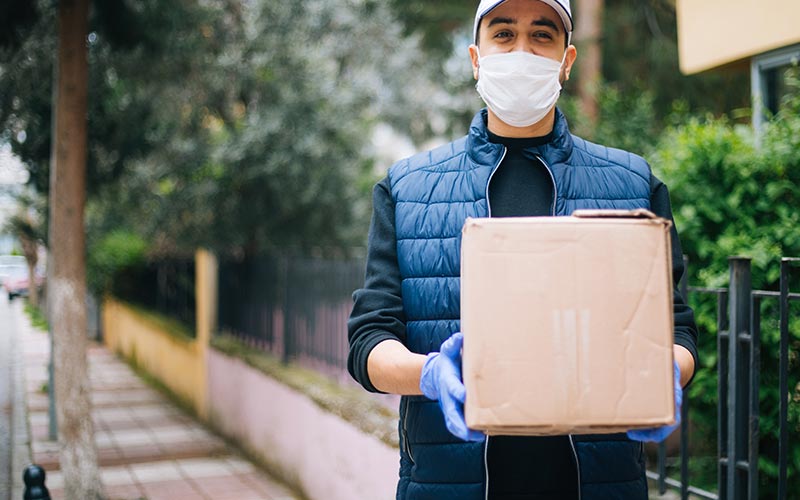
Making the Security Incidents More Visible with Infosys Security Solution
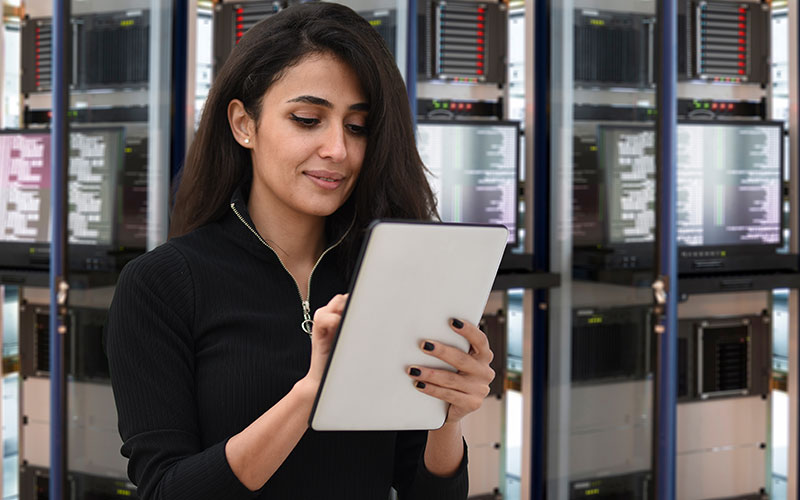
Partnership
’Our partnership transforms the customer experience’: LivePerson
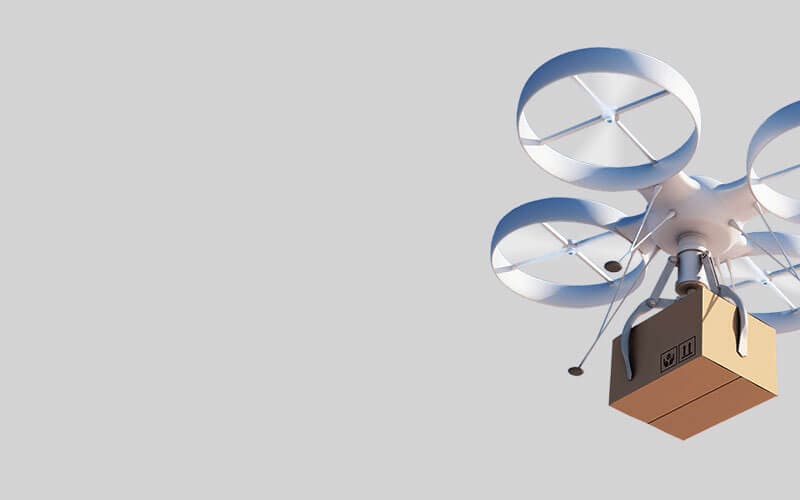
Cloud-based testing service ensures smooth post-M&A data integration
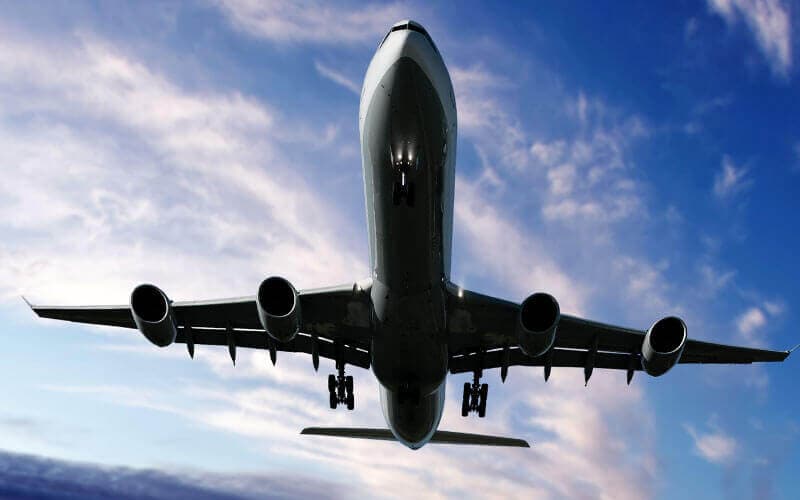
4PL logistics ecosystem enables JIT procurement
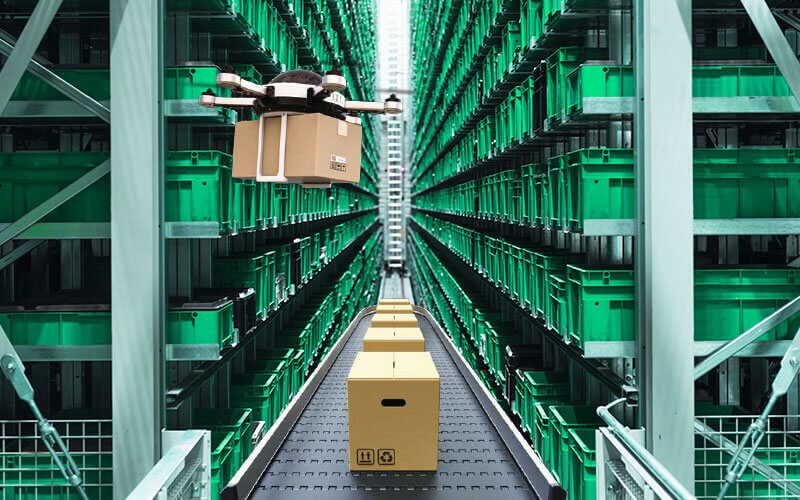
Hackathons shape next-gen digital freight marketplace
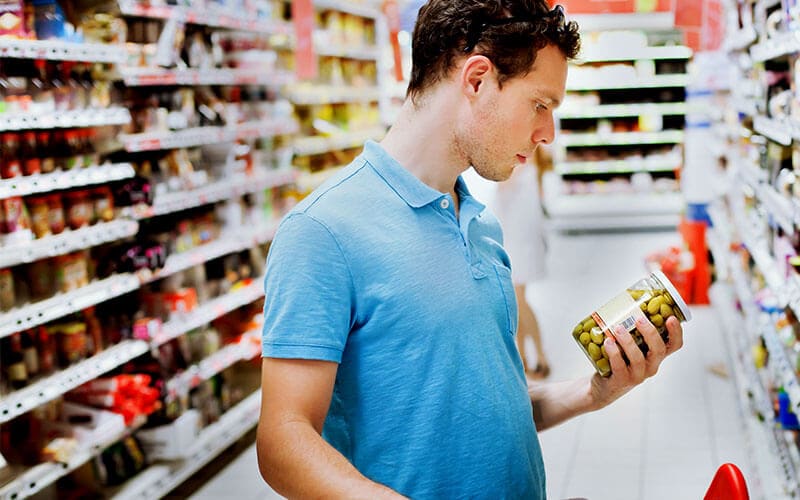
Food services enterprise modernizes business intelligence ecosystem
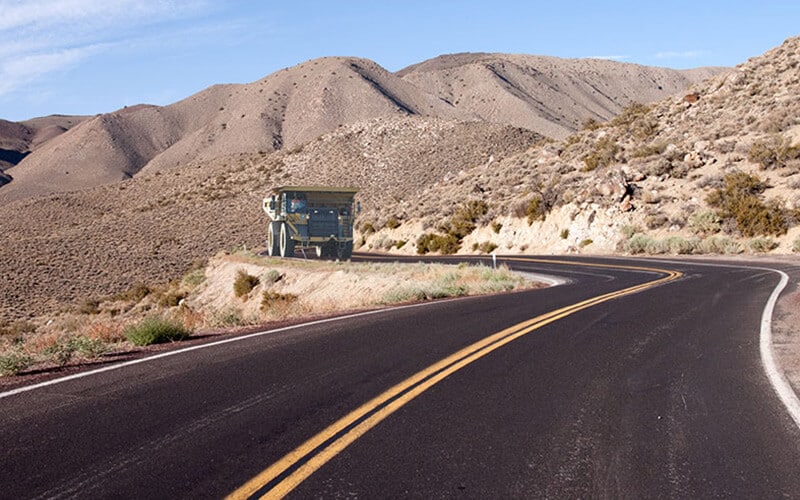
Predictive freight analytics streamlines mining logistics
India’s postpandemic logistics sector: The need for technological change
Since the COVID-19 crisis began, it has affected almost all business operations in every sector and every part of India. Logistics has been particularly hard-hit, without which only certain cottage industries may function. Even before the second wave of the disease began, in the spring of 2021, the pace of recovery was unclear. In 2019, the McKinsey Global Institute (MGI) predicted that India’s logistics sector would expand at a compound annual growth rate of more than 10 percent, from $200 billion in early 2020 to at least $320 billion in 2025. Unfortunately, the sector’s future is much more uncertain now than it was when MGI made that forecast.
Although the picture is constantly evolving, there are things that we already know and things that we know we don’t know. The known unknowns, such as the pace of the recovery, will become less opaque over time. No doubt the sector also faces unknown unknowns, but that is always true, so they shouldn’t prevent Indian companies from assessing the problems and acting to correct them. In this paper, we consider solutions for warehousing and transport.
About the authors
In the warehousing function, as we explain, companies could consider shrinking their product mix, allocating more inventory to essential items, reducing nonessential inventory, and introducing innovative packaging and materials-handling processes to reduce levels of human contact. In the transport function, the key steps for consideration are making tactical choices among less than truck loads (LTL), full truck loads (FTL), and milk runs for delivering goods and using efficient multimodal transportation more extensively.
Looking ahead, logistics players in every function can adopt digital technologies to stay relevant.
The impact of COVID-19 and the near-term prognosis
One thing we do more or less know is the pandemic’s impact so far on two key functions of the logistics sector: warehousing and transportation. In the near term, estimating demand, allocating capacity, and distributing products across sectors and regions remain difficult challenges.
Warehousing
Even in good times, very difficult and sophisticated inventory-management decisions are needed to manage inventory stored in warehouses. Ordering and maintaining appropriate quantities is now harder than ever because traditional forecasting techniques have become ineffective: experienced buyers make decisions to purchase raw materials, but that experience may count for less in a radically changed country and world.
Given these strong headwinds, most companies could shrink their product mix to allocate warehousing to the most essential items in their portfolio. Producers of nonessentials in particular could continue to minimize their inventories, which significantly increase their holding costs and take up valuable warehouse space. But for essential items, the ongoing uncertainty around supply means that it might make more sense for producers to keep inventories high than to risk stockouts. In any case, just-in-time approaches to scheduling may not work, at least in the near future.
Not surprisingly, the pandemic has made many companies question if large regional warehouses are really the best way to keep supply chains agile; smaller warehouses at more locations could be a better response to uncertainty. 1 “Emerging trends in warehousing segment post Covid-19 lockdown,” Financial Express , May 29, 2020, financialexpress.com. Lockdown restrictions have also forced companies to ask themselves whether distribution centers could maintain service levels more effectively than a warehouse system can. Such centers may certainly make it more fruitful to deploy the latest technology.
In the future, India’s warehousing industry may enjoy higher demand as producers shift their focus away from China and toward other Asian countries, including India itself. But one thing is certain: warehouses must reduce the amount of human contact involved in handling materials. As a result, demand for innovative packaging and materials-handling processes is rising throughout the supply chain. Companies that lease space in warehouses, for example, are demanding more streamlined and automated processes. Those that have their own facilities must implement such processes as well.
Transportation
COVID-19 has forced India to restrict the movement of goods across government-defined zones and across states, so the use of suboptimal routes has increased. Meanwhile, a shortage of drivers raised truck-rental costs by a staggering 56 to 74 percent. 2 Pallavi Nahata, “Coronavirus lockdown: Truck rentals jump as drivers ply back empty trucks,” Bloomberg, April 10, 2020, bloombergquint.com. For these and other reasons, logistics functions may remain open to all options during and after the pandemic, so they will have to act nimbly.
The way companies use FTLs, LTLs, and milk runs, for example, is changing. In the supply chains of fast-moving consumer goods and some other products, milk runs are more efficient because they can effectively aggregate demand across several different SKUs and companies. To become more responsive to changing demand, companies are also increasing their use of LTLs. 3 “COVID-19 & domestic shipping: How to be proactive vs. reactive,” Mohawk Global, April 15, 2020, mohawkglobal.com. Strategically choosing when to use LTLs, FTLs, and milk runs to meet demand is one of the key decisions that must be made, and the principles that guided them before the pandemic have been overtaken by events.
A related trend—the rising importance of last-mile deliveries for e-commerce—has been underway for years, but COVID-19 has intensified it. Since the pandemic started, consumers around the world, and certainly in India, have been shopping online in much larger numbers, particularly for groceries. In fact, demand on India’s online grocery-shopping portals surged last year by up to 80 percent, just as their operational capacity fell by half. 4 Sangeeta Tanwar, “How India’s food and grocery startups staged a comeback after initial Covid-19 blues,” Quartz India, April 27, 2020, qz.com. That, however, is a short-term problem. The long-term one is that logistics for last-mile deliveries must continue to rely on small, informal truck companies that lack the resources or sophistication to use modern methods. To stay relevant in the postpandemic next normal, all logistics partners will have to keep up with the shift to digital.
Of course, trucks dominate transportation in India’s logistics sector. But during the lockdown’s most stringent phases, railways have been the only mode of transport that operated without restrictions and could thus convey goods and commodities across the country at almost prepandemic levels. 5 Nishant Sharma, “Railways expects to earn more from freight this fiscal despite Covid-19 outbreak,” Bloomberg, June 20, 2020, Bloombergquint.com. The railways have chiefly moved essential products: the need for a constant supply of them is pressing, and the output of nonessential goods has fallen because the businesses that manufactured and sold such products shut down as a result of continuing restrictions in place. In February 2021, for the first time since the pandemic’s onset, Indian Railways saw year-on-year revenue growth, signaling, at least for a time, the return of pre-COVID-19 levels of operation. 6 “1st time post Covid-19 pandemic, Indian Railways freight revenue surges to Rs 98,000 crore,” Zee Business, February 14, 2021, zeebiz.com
Air shipping had taken a huge hit because air travel was in effect frozen or limited until only recently. In the past, a significant percentage of all air-freight shipments flew in the underbellies of passenger planes. Since most of them had been grounded, airline companies couldn’t afford frequent air-freight flights even for essential items. However, airline cargo operations are expected to recover to pre-COVID-19 levels by the beginning of 2022. 7 “Air cargo volume revives despite capacity worries,” Mint, Oct 8, 2021, livemint.com
One saving grace of the current crisis is that it has given India its best opportunity to shift toward multimodal transport—typically rail, supplemented by trucks for moving shipments to their final destinations. The government could encourage the transport of aggregated assortments of goods by rail not only to promote cheaper, faster multimodal freight transport but also to ease the pressure on road networks.
Pain points
In December 2019, several months before the crisis hit, McKinsey and the Indian Institute of Logistics 8 A center of excellence of the Confederation of Indian Industries. conducted a comprehensive survey of the country’s manufacturing companies. 9 The survey included 190 executives from 60 manufacturing companies representing a wide cross-section of industries, including automotive, fast-moving consumer goods, life sciences, steel, and telecommunications. Of these 60 companies, 40 percent had revenues of more than $200 million, and half had more than 800 employees. One of the goals was to identify and understand the key external and internal pain points for logistics functions.
Warehousing and transportation: How to remove the pain points
Best practices and greater collaboration could not only improve the way the logistics sector’s warehousing and transportation functions serve their customers but also increase the bottom line.
In the COVID-19 era and beyond, as we have seen, it is more important than ever to determine the appropriate mix of regional and central warehouses. To get it right, companies must take into account factors such as delivery lead times, the importance and frequency of demand, the material value of products, and the impact of warehouse configurations on capital and operating expenditures and on the customer experience. (Fewer regional warehouses could increase the frequency of milk runs and therefore costs, for example, but more warehouses could increase delivery lead times.) The other crucial best practice for the warehouse function is to estimate warehousing and packaging costs by tracking suitable KPIs, such as warehousing overhead per ton, daily handling costs per full-time employee, and packaging costs per product price.
Warehousing can benefit from closer collaboration with materials management by taking advantage of its access to service-level agreements with customer-service units. These agreements can help warehousing determine the relative importance of demand in specific regions or zones—which is now, of course, more problematic than ever. Transport functions can help warehousing to map central and regional warehouses by providing access to agreements with logistics service providers.
Best-practice transport functions use rail for inbound shipments of high-volume products with low variable consumption and for outbound shipments of high-volume products with low variable demand. A simple product segmentation based on volumes and volatility can help to identify appropriate products. Another best practice—that has been particularly helpful during the pandemic and will likely continue to be—is to optimize logistics flows by simulating network configurations with varying ports of call, last-mile-connectivity options, and the like. Controlling costs by identifying and tracking suitable KPIs (such as road, rail, and sea freight per ton per kilometer, as well as the percentage of volume and weight that each transport mode uses) has significant value as well.
Greater collaboration among logistics functions will be required to enable the sophisticated strategies that will be essential to optimize logistics flows. Such strategies, for example, require estimates of inventory levels and warehouse-space constraints. Materials management can give the transport function that kind of data. Still more important in the long run, transport teams must design the digital logistics networks of the future in close collaboration with warehousing.
The survey found that the top three external pain points were the small number of formal transport companies that can use efficient technologies, India’s overstrained highways, and a severe shortage of drivers. The pandemic has exacerbated all of these problems, and individual companies can do relatively little to solve them.
Companies can do much more, however, about the top internal pain points: the failure of most logistics functions to use best practices, as well as the insufficient degree of coordination and collaboration between the warehousing and transport functions. Overcoming these two problems could help India’s economy, and the companies within it, to recover from the pandemic and prosper in the next normal. The solutions involve not only technology but also organizational structure and practices (see sidebar “Warehousing and transportation: How to remove the pain points”).
Technological challenges, opportunities, and structural reforms
In a McKinsey survey conducted last year on the readiness of Indian organizations for Industry 4.0, 66 percent of the respondents said that before the onset of COVID-19, their employers had implemented either no or very few Industry 4.0 use cases (Exhibit 1). 10 The survey, conducted in the second half of 2020, had 45 responses. Yet in the very same survey, 60 percent of the respondents reported that the pandemic had increased the value of Industry 4.0 initiatives (Exhibit 2). Organizations are therefore now more likely to implement technology projects across the value chain. The logistics sector in particular must do so.
The need for digitization in logistics
As we have seen, COVID-19 has revealed the weaknesses and inefficiencies of India’s current logistics system. Only a shift to more formal, technologically capable organizations may allow the sector to meet the challenges yet to come: the things that we know we don’t know—for example, whether, when, and how the COVID-19 crisis will finally end—not to mention the unknown unknowns. The pandemic has made this kind of agility, and the technological sophistication it demands, a necessity for survival, not just a competitive advantage. But almost all of the small, informal logistics players in the country’s supply chains (for instance, the firms that operate 75 percent of India’s trucks) cannot adapt to rapid technological change. Even many of the larger logistics companies may find it a challenge. All of these organizations, large and small, face serious threats.
Digital logistics
Many technologies are transforming logistics, and most of them are already in use around the world and fairly mature. The following technologies represent the most potential opportunity for the logistics sector:
Integrated logistics platforms are online marketplaces where companies buy and sell logistics services.
Telematics helps companies monitor vehicles and cargo digitally, in real time.
Digital logistics control towers serve as nerve centers for supply-chain operations by capturing data at all levels, providing end-to-end visibility, and facilitating strategic decision making.
Blockchain helps companies develop systems to verify and rate the transactions that truckers and shippers complete, so manufacturers can generate smart contracts that automatically pay vendors when shipments reach their destinations.
Cognitive logistics process automation uses artificial intelligence to automate responses to changes in logistics networks by processing a range of data on the status, health, and performance of supply chains and by giving stakeholders real-time recommendations.
Real-time replanning makes supply chains visible from end to end and fully integrates them into IT systems.
Augmented-reality devices superimpose computerized data on the user’s field of vision, helping to improve pickup rates and reduce picking errors.
Exoskeletons —robotic clothes—increase the physical capacity of their users and can reduce the number of injuries and raise productivity.
Autonomous mobile robots (AMRs) navigate through warehouses and move racks to pickers, pick and move items from baskets, deliver shipments to packers, and the like. AMRs can reroute themselves dynamically when they meet obstacles; the more common automated guided vehicles (AGVs) cannot.
The more successful larger companies throughout the logistics sector may gravitate toward artificial intelligence, blockchain, and other technological solutions to help solve for the present cash crunch and other problems (Exhibit 3). Technologies that promote the free flow of data—for instance, the sharing of information with logistics providers—will be more important than ever. To carry out the necessary transformation, companies may seek tighter control over their supply chains, so contracts with logistics and other suppliers will likely evolve (for example, through the adoption of the smart contracts mentioned in the sidebar “Digital logistics”).
These changes will reward companies with the resources and know-how to adopt them. McKinsey’s Travel, Logistics & Infrastructure Practice estimates that advanced technology could not only reduce logistics costs by as much as 25 percent but also help companies offer better service and free internal capacity for other purposes.
A slow but steady start toward digitization
Already, the logistics sector is beginning to change, but mostly at big companies, many of them based abroad. Organizations are scrambling to bolster the supply chains. A regulatory relaxation by India’s national government, for example, has enabled experimentation with beyond-visual-line-of-sight (BVLOS) drones in designated areas. 11 Alnoor Peermohamed, “DGCA nod clears runway for the dawn of drone age,” Economic Times, June 4, 2020, economictimes.indiatimes.com. About 13 companies, including food- and grocery-delivery businesses, budget airlines, and drone start-ups, have received approval to test BVLOS drones, which could be a game changer in last-mile deliveries. Similarly, multiple logistics players are innovating the way they operate through adoption of new technologies, such as blockchain, or through partnerships to help improve operational efficiency. Organizations have also started helping employees prepare for the digital future by improving their skills.
The current disruptive impact of the COVID-19 crisis shows clearly that long-awaited structural reforms to make logistics a formal, streamlined sector are more necessary than ever. The pandemic has exacerbated the sector’s long-term problems, but the solutions pose problems of their own for many large companies and almost all small ones. Yet these changes would have great benefits for the country as a whole.
Knut Alicke is a partner in McKinsey’s Stuttgart office; Sumit Dutta is a partner in the Chicago office; K. Ganesh is a senior knowledge expert and associate partner in the Chennai office, where Ramanath KB is a knowledge specialist; and Hanish Yadav is a partner in the Gurugram office.
Explore a career with us
Related articles.

COVID-19 and supply-chain recovery: Planning for the future
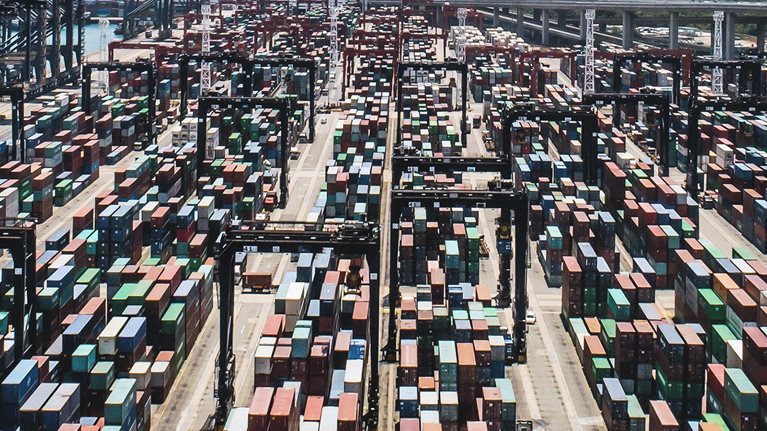
Asia: The highway of value for global logistics
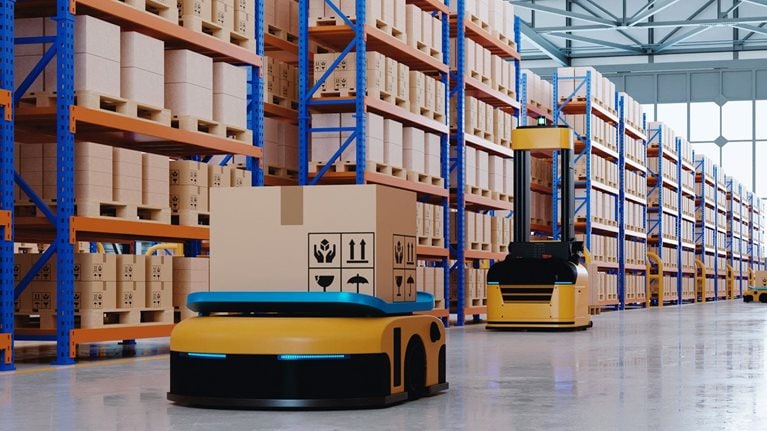
Unlocking the omnichannel opportunity in contract logistics
The emergence and adoption of digitalization in the logistics and supply chain industry: an institutional perspective
Journal of Enterprise Information Management
ISSN : 1741-0398
Article publication date: 23 March 2021
Issue publication date: 11 November 2021
Despite increasing interest in digital services and products, the emergence of digitalization in the logistics and supply chain (L&SC) industry has received little attention, in particular from organizational theorists. In response, taking an institutionalist view, the authors argue that the emergence and adoption of digitalization is a socially constructed phenomenon.
Design/methodology/approach
This paper shows how actor-level frameshifts contribute to an emergence of an overarching “digitalization logic” in the L&SC industry at the field level. Building on a longitudinal analysis of field actors' frames and logics, the authors track the development of digitalization over the last 60 years in the L&SC sector.
The authors classify specific time periods by key field-configuring events, describe the relevant frameshifts in each time period and present a process that explains how and why digitalization has emerged, been adopted and manifested itself in the L&SC industry.
Originality/value
The findings of the study provide insights about the evolution of a digitalization logic and thus advance the institutional view on digitalization in the L&SC industry.
- Supply chain
- Institutional theory
- Institutional logics
- Digitalization
Herold, D.M. , Ćwiklicki, M. , Pilch, K. and Mikl, J. (2021), "The emergence and adoption of digitalization in the logistics and supply chain industry: an institutional perspective", Journal of Enterprise Information Management , Vol. 34 No. 6, pp. 1917-1938. https://doi.org/10.1108/JEIM-09-2020-0382
Emerald Publishing Limited
Copyright © 2021, David M. Herold, Marek Ćwiklicki, Kamila Pilch and Jasmin Mikl
Published by Emerald Publishing Limited. This article is published under the Creative Commons Attribution (CC BY 4.0) licence. Anyone may reproduce, distribute, translate and create derivative works of this article (for both commercial and non-commercial purposes), subject to full attribution to the original publication and authors. The full terms of this licence may be seen at http://creativecommons.org/licences/by/4.0/legalcode
1. Introduction
Digitalization in the logistics and supply chain management (L&SC) industry is of increasing strategic importance for businesses as it impacts established paradigms, business models and industry boundaries ( Barrett et al. , 2015 ; Cichosz et al. , 2020 ). A mounting number of companies allocate resources to exploit digital opportunities that have the potential to transform societies, economies and organizations ( Cichosz et al. , 2020 ; Hribernik et al. , 2020 ; Mikl et al. , 2020b ). However, digitalization in L&SC seems to be a double-edged sword: on the one part, companies such as Amazon have fundamentally changed the L&SC landscape through digital products and services ( Cohen, 2018 ; Liebmann, 2013 ), thus having embraced and pushed digitalization as a force of change, not only between institutions, organizations and companies but also as an opportunity to create completely new products and services ( Loebbecke and Picot, 2015 ). On the other part, traditional L&SC companies such as sea or rail freight forwarder are still characterized by low levels of digitalization and manual processes ( Economist, 2018 ), thus risking to miss out on digital advances (see, e.g. Lyall et al. , 2018 ) that “[rewrite] the rules of business and supply chains” ( O'Marah, 2017 ).
Although research in digitalization in L&SC is an increasingly popular topic among academics (e.g. Busse and Wallenburg, 2011 ; Cichosz et al. , 2020 ), little understanding exists “how the digital revolution will impact key [L&SC] concepts” ( Stank et al. , 2019 , p. 957). In particular, the topic of how digitalization has emerged and manifested itself in L&SC has received only little attention, in particular from organizational theorists and business historians. So far, there is only limited research available investigating the change through digitalization and what events have led to an agreement in organizations and companies to put digitalization on the agenda in the L&SC industry.
In line with Orlikowski and Barley (2001) , we argue that institutional theory has relevant concepts and constructs that can help us understand the emergence and the adoption of digitalization and its impact on L&SC. An institutional perspective on digitalization allows us to understand digitalization as a socially constructed process in which key actors in L&SC eventually reach convergence around a so-called “digitalization logic” in L&SC. In particular, by examining digitalization from an institutional perspective, this paper attempts to answer how actors in the L&SC field reach a consensus to “institutionalize” digitalization in their organizations' practices and processes ( Thornton and Ocasio, 2008 ). To do so, this paper uses an inductive approach to reconcile the emergence of digitalization in L&SC based on examination how digitalization has been recognized and being addressed over time. As L&SC management is subject to conflicting and competing opinions, an examination of both symbolic and cognitive elements and the implementation of organizational practices provide not only insights about how digitalization has and can influence companies but more fundamentally about whether digitalization is a phenomena that L&SC organizations need to adopt in order to gain and maintain legitimacy ( Suchman, 1995 ) or to maintain or build a competitive advantage ( Koch and Windsperger, 2017 ; Porter, 1985 ).
Our paper makes three main contributions to further advance the understanding of institutional interactions by which digitalization emerges and manifests itself in the L&SC industry. First, we conceptualize the emergence and the adoption of digitalization as a social construct, where the digitalization logic is subject to change as field-level frames show discursive behavior over time. Second, abstracting from our findings on digitalization over a period of 60 years, we identify key frames and illustrate how these frames shift and drive digitalization in L&SC. Third, our study depicts the process of the emergence, adoption and manifestation of a digitalization logic in logistics industry, thereby highlighting the key determinants behind digital and technological advances in L&SC.
The remainder of the paper is structured as follows: we first theorize about the influence of institutions and describe the underlying concepts of logics and frameshifts in the context of the L&SC industry. This is followed by a description of the research design and the method used to investigate the emergence, adoption and manifestation of the digitalization logic. Next, we present and discuss the findings and conclude with implications to theory and practice, highlight the limitations of the study and provide future research avenues.
2. An institutional perspective on digitalization in the L&SC industry
2.1 the adoption of digitalization in the l&sc industry.
Digitalization plays an increasing role in the L&SC industry ( Cichosz et al. , 2020 ; Mikl et al. , 2020a ), and numerous scholars have addressed and discussed its transformation potential for societies, economies and organizations (e.g. Garay-Rondero et al. , 2019 ; Holmström et al. , 2019 ; Seyedghorban et al. , 2020 ; Stank et al. , 2019 ; Wieland, 2020 ). For the purpose of this study, we base our definition of digitalization on the work of Brennen and Kreiss (2016) and Ritter and Pedersen (2020) and define digitalization as “the exploitation of new technologies with processes to gain a competitive advantage and the potential to transform the L&SC sector.” One reoccurring theme within the literature discussing the opportunities through digitalization in the L&SC industry is the adoption of digital products and services and the implementation of new technologies ( Mathauer and Hofmann, 2019 ; North et al. , 2019 ; Verma and Bhattacharyya, 2017 ).
Institutionalist scholars argue that the adoption of organizational practices and measures is guided by institutions ( DiMaggio and Powell, 1983 ; Scott, 1991 ; Thornton et al. , 2012 ). According to Djelic and Quack (2008) , these institutions represent “collective frames and systems that provide stability and meaning to social behavior and social interaction and take on a rule-like status in social thought and action” (p. 300). These institutions exist in organizational fields: in the context of our study, the organizational field represents the L&SC industry. In this organizational field, richly contextualized spaces exist where various actors with different interests negotiate at multiple levels over issue interpretation and often find common ground ( Herold and Lee, 2019 ; Scott, 1991 ; Thornton et al. , 2012 ; Wooten and Hoffman, 2008 ). For example, referring again to the example from the introduction, the company Amazon seems to have found “common ground” with their suppliers and customers about the importance and the benefits of digitalization. In other words, the actors of and around Amazon have built a collective awareness that digitalization has serious implications on their organizations, while sea and rail freight forwarders seem to have not reached the same level of consensus, as their low level of digitalization indicates ( Economist, 2018 ).
We argue that the emergence and the adoption of digitalization is a socially constructed phenomenon, in which institutional norms and practices, rather than individualized choices, motivate actors to adopt digital processes and practices (see Berger and Luckmann, 1968 ). In particular, the adoption of digitalization is the outcome of a process of negotiations and social interaction where the various actors in the organizational field legitimize their actions ( Fischer et al. , 1998 ; Suddaby et al. , 2017 ). Legitimacy, which Suchman (1995) defines as a “generalized perception or assumption that the actions of an entity are desirable, proper or appropriate within some socially constructed system of norms, values, beliefs and definitions” (p. 574), is experienced intersubjectively – and distinctively – within actors in the organizational field ( Clark, 1985 ; Giddens, 1984 ), i.e. although institutions guide the processes and behaviors, in practice, companies adopt digitalization in different ways, time frames or not at all. From an institutional perspective, the emergence and adoption is thus related “to the ways in which legitimacy of particular ways of organizing become tied to issues of existing logics, power and interest” ( Hinings et al. , 2018 , p. 56, p. 56).
2.2 Understanding digitalization through institutional logics and frames
From social construction perspective, the adoption of digitalization in the L&SC industry (on the field level) can only occur when actors build a collective awareness that digitalization may represent serious opportunities or threats for their organizations ( Rachinger et al. , 2019 ). Critical moments in the social construction of digitalization may occur when actors in L&SC feel being left behind or not able to control the opportunities and changes in digital technology, which then may have implications for the actors' legitimacy or even worse their survival ( Suchman, 1995 ). However, through the process of understanding and narrowing the scope and the significance of digitalization in the field, actors automatically engage in socially constructing digital processes and practices and, based on their sense of consensus and their logics, may begin to take collective action to determine if and how digitalization will be adopted. As such, we assert that the adoption of digitalization in L&SC as social construct involves an overarching logic: the “digitalization logic.”
According to Scott (2012) , institutional logics reflect “values and norms, ideas, beliefs, and meaning systems that guide the behavior of actors” (p. 32). In other words, institutional logics represent the organizing principles within an organizational field shaping cognition and behavior in an industry ( Besharov and Smith, 2014 ). Against this background, it is necessary to emphasize how different and often competing logics cause actors to frame issues distinctively and to propose particular actions ( Herold et al. , 2019 ; Purdy and Gray, 2009 ). However, institutional logics can also coexist ( Reay and Hinings, 2009 ; Seo and Creed, 2002 ), recombine ( Djelic and Quack, 2008 ) or blend ( Lounsbury, 2008 ). This interaction between logics refers to deliberate attempts to convince other field actors to shift their frames rather than by accident as “frames function to organize experience and guide action” ( Snow et al. , 1986 , p. 464). As a consequence, field frames emerge when the various frames of actors converge around a shared frame ( Kaplan, 2008 ; Lounsbury and Ventresca, 2003 ).
As such, the identification of logics and frames within the organizational field provides a foundation for a dynamic and richer understanding of the influence of actors which action unfolds. Examining digitalization from an institutional view is thus about how digital-enabled institutional logics and frames emerge and diffuse both through fields and organizations ( Hinings et al. , 2018 ). In particular, frame analysis can be regarded as a useful tool to analyze how field-level actors participate in “discursive struggles” to advance their practices and logics ( Kaplan, 2008 ). In these evolving fields exist thus the potential for the emergence and diffusion of field-level frames, such as digitalization, given that actors with conflicting frames can solve their frame discrepancies. Hardy and Maguire (2010) found that shifts in frames that change key actors' perceptions are triggered by so-called key field-configuring events. According to Sewell (1996) , a key field-configuring event can be defined as “(1) a ramified sequence of occurrences that (2) is recognized as notable by contemporaries, and that (3) results in a durable transformation of structures” (p. 844).
However, despite attempts to identifying the mechanisms that facilitate field change to advance theory from an institutional perspective, little attention has been given to examine how a digitalization logic emerges, is adopted and can manifest itself, in particular in the context of the L&SC industry. An examination of these dynamics in the field, i.e. the adoption and implementation of digitalization, provides an opportunity to better understand how a digitalization logic can emerge and manifest itself in the field. As such, this paper aims to examine to identify how actors with various logics shift frames to allow a consensus and advance the emergence, adoption and manifestation of the digitalization logic in the organizational field of L&SC.
3. Methodology
3.1 research approach.
How has digitalization emerged, been adopted and manifested itself in the L&SC industry?
To answer the research question, we use the construct of “institutional logics” ( Scott, 1991 ; Thornton et al. , 2012 ) to examine the emergence and the adoption of digitalization in L&SC, i.e. how a “digitalization logic” has emerged and has been adopted. In line with institutional logics, the emergence and the adoption of a digitalization logic is based on both symbolic and cognitive elements (to recognize the issue) and the implementation of organizational practices (to address the issue) ( Thornton and Ocasio, 2008 ). For the data collection as well as for the analysis, we adopt a so-called “historical process research” approach ( Langley, 1999 ). In contrast to other research approaches focusing on differences, process research aims to provide an understanding why and how “discrete events and states” ( Elsbach and Sutton, 1992 , p. 708) develop over time; thus, process research collects data of activities, events and decisions over time ( Langley, 1999 ). To illustrate how digitalization emerged and manifested itself in L&SC, we applied a diachronic approach to understand the developments in the field over time and associated consensus around the digitalization logic (for a similar approach, see Ansari et al. , 2013 ).
A crucial element of the data collection was the determination of relevant actors and the classification of key field-configuring events and milestones ( Hardy and Maguire, 2010 ) that change key actors' perceptions about digitalization. In particular, the identification of the key field-configuring events and milestones had three specific goals: (1) to identify key historical events of digitalization in L&SC, (2) to assess the time periods when frameshifts in digitalization occurred, i.e. we looked for “discursive shifts” ( Maguire and Hardy, 2009 ) and “breaches that reveal the usually undiscussed boundaries of taken-for-granted understandings” ( Schneiberg and Clemens, 2006 , p. 214) and (3) determine the key actors that affect and are affected by the emergence of digitalization.
In order to determine these key events and actors, we conducted three group discussions “to stimulate discussion and thereby understand (through subsequent analysis) the meanings and norms which underlie those group answers” ( Bloor et al. , 2001 , pp. 42–43). The first group consisted of five academic L&SC experts from Central and Eastern Europe; the second group comprised five L&SC practitioners from Central and Eastern Europe, each with more than 10 years' experience in the industry. In particular, academic participants were chosen on the basis of their experience and standing in academic community, i.e. senior academic researchers or university professors with an associated publication track record with a focus on technologies, digitalization or entrepreneurship in the field of logistics or supply chains. Practitioners were chosen based on their experience in medium-to-large multinational corporations and their area of responsibility, i.e. being part of senior management with an international track record in L&SC and having strategic and operational management experience as well as an involvement in technology or digitalization projects.
In the first and second group discussion, the respective participants were asked to name and describe significant events and milestones in the emerging field of digitalization, the rationale behind these events and how it affected the actors' perceptions about digitalization in the last 60 years, i.e. from the years 1960 to 2020. 1960 was chosen as starting point as it represents the start of so-called “Logistics 2.0” era, i.e. the start of the digitalization in L&SC ( Frazzon et al. , 2019 ). The group discussions lasted between 60 and 90 min until all participants agreed with identified events and milestones. The feedback of each group was then consolidated to compare the results. The results were discussed internally between the researchers to identify overlaps and differences, which allowed us to create a preliminary list of digitalization events and milestones. In the third group discussion, we presented the preliminary list and invited both groups to further consolidate the events and milestones that were seen as the key field-configuring events in digitalization in the L&SC industry, which led to the final list of events and milestones in the field of L&SC digitalization.
At the same time, secondary data were collected to track old and new developments in digitalization and in the L&SC industry. According to Rabinovich and Cheon (2011) , the use of secondary data has some unique advantages, for example, it is less subject to biases, has higher internal validity and is available in great quantity. Following a rigorous methodological approach (see, e.g. Denyer and Tranfield, 2009 ; Durach et al. , 2017 ), an inclusion criteria list was developed and agreed on by all authors. We decided to not restrict the search to academic papers but also include nonacademic articles as scholars encourage researchers to include wide range of studies ( McKinnon, 2013 ; Pawson, 2006 ; Tranfield et al. , 2003 ).
For academic papers, we focused on peer-reviewed articles as they are considered to be higher quality than nonpeer-reviewed articles ( Denyer and Tranfield, 2009 ). To reduce bias, two databases were selected for the literature search: Scopus and Web of Science. These databases were selected as they represent large repositories of business research, providing a broad range of publishing outlets of highest impact for the research community ( Sandberg and Aarikka-Stenroos, 2014 ). Furthermore, Google Scholar was also used to confirm/double-check the relevant list of peer-reviewed articles. We used the main keywords “digitalization” in combination with “supply chain” and “logistics” but in order to expand our scope and include as many relevant articles as possible, we repeated the search and replaced “digitalization” with related terms such as ”technology,” “ICT,” “big data” or “computer” and added keywords including “adoption,” “implementation” or “diffusion.”
We used academic papers for two purposes. First, we further sighted studies that may help us to further deconstruct the emergence of digitalization and their associated concepts to better understand their implications on frameshifts and field-level changes. Second, we used recent papers to reflect on the key actors behind the emergence to better understand how organizations companies adopt a digitalization logic. For nonacademic papers, we used the keywords to identify any relevant information in consultancy or industry reports, press releases, websites, newspapers and magazines not only to support our arguments but also to substantiate and validate the identified key field-configuring events and milestones. These articles dealt with the impacts of digitalization and described events and milestones that had an influence on companies, consumers and state actors. With the help of these data sets, we were able to triangulate and determine specific key field-configuring events and the key actors' frames.
3.2 Data analysis and presentation of results
The analysis of the data occurred in four steps: (1) the determination of the actors that affect or are affected by digitalization in L&SC, (2) the chronological identification of historical events, (3) the identification of key-configuring events and (4) the discussion of the interrelations to display the process behind the emergence, the adoption and the manifestation of the digitalization logic. All four steps were predominantly based on the findings from the group discussion but were complemented, validated and interpreted with the help of the collected secondary data.
First, we identified key actors that had a direct influence on digitalization but also actors who indirectly influenced the digitalization in L&SC. In this step, we did not restrict the term “key actors” to any definition, allowing to incorporate a wide range of relevant influences. Second, we derived key historical digitalization events in L&SC from the group discussions and the complementary secondary data: the historical events started with the introduction of electronic data interchange (EDI), which was one of crucial applications within the era of containerization and ended with the IBM–Maersk blockchain application in 2018. Overall, 13 events in the history of digitalization in L&SC were classified. After identifying the historical events, we investigated as a third step the field-configuring events that led to changes within the organizational field. In particular, we examined the frames within these event periods and assessed the extent of a shift in frames. Taking into account the group discussions and the secondary data, we identified 12 actor-level frameshifts.
As the fourth and last step, we examined the field framesshifts' interrelations to identify conditions under which a consensus was built to within the field that led to the emergence, adoption and manifestation of the digitalization logic in L&SC. To differentiate and classify the frames, we followed two steps: (1) we compared the emergence, adoption and the manifestation of digitalization logic between the industries related to L&SC and other industries, thereby not only highlighting the interrelations and the indirect influences on L&SC but also showing the similarities and differences between the industries and (2) used the terms “Industry 2.0” until “Industry 4.0” and “L&SC 2.0” until L&SC 4.0 to showcase the development of the digitalization logic, thereby displaying a clear classification of the field frames and the process of the emergence, adoption and the manifestation of digitalization logic in L&SC.
As described above, the results are presented in four steps: (1) the determination of the actors that affect or are affected by digitalization in L&SC, (2) the chronological identification of historical events, (3) the identification of key configuring events and (4) the discussion of the interrelations to display the process behind the emergence, the adoption and the manifestation of the digitalization logic. Each step will be discussed in detail below.
4.1 Key actors in logistics and supply chain's digitalization
As a first step, we identified the relevant actors that affect or are affected by the digitalization in the L&SC industry (see Table 1 ) through the group discussions and the additional data from secondary sources. In the process, we also included the current frames of the respective actors and allocated an underlying logic to the actors. We restricted the underlying logics to what Thornton et al. (2012) define as so-called “core” logics that influence the behavior of actors, which includes the market, corporations, state, family, religion, community and profession. However, not all core logics can be applied in the context of the emergence and adoption of digitalization in L&SC, such as religion and family, and we restricted the underlying logics to state, corporation and market. Some of these core logics influence (or have influenced) the digitalization directly, while other have influenced indirectly. For example, states mostly influence the emergence and the adoption of digitalization indirectly through providing broadband capacity or the investment in faster Internet connections; thus, the state provides an underlying prerequisite without which digitalization cannot occur, but the state does not proactively encourage L&SC companies to implement more digital products and services. In the context of our research, which focuses on how digitalization emerged and manifested itself in L&SC companies (firm level) and the L&SC industry (field level), the core logics of corporation and market are also heavily influencing the L&SC sector. In particular, a corporation logic would indicate an L&SC company embraces and pushes digitalization internally through new practices, products or services (e.g. Amazon), while a market logic would rather indicate that an L&SC company reacts to external market developments that increase digitalization levels (e.g. the adoption of radio-frequency identification [RFID]).
4.2 Key historical digitalization events in L&SC
As a second step, the group discussions identified the main historical events that have shaped and had an influence on the emergence and the adoption of digitalization in L&SC over the last 60 years. We used these examples to further explain and validate the frameshifts (see Figure 1 ).
4.3 Field-configuring events
With regard to key configuring events, the identification of the frameshifts from the group discussion and complementary secondary data allowed us to categorize these shifts into five overarching field frames (see Table 2 ), namely: Field frame 1: the transformation from analog to digital services, Field frame 2: the dissemination of L&SC management software, Field frame 3: the globalization of supply chains through the World Wide Web and the Internet, Field frame 4: the rise of e-commerce and Field frame 5: the deployment of the Internet of Things and big data. Below, we describe the key field frames along with the shifts and examples.
4.3.1 Field frame 1: the transformation from analog to digital services
The first frame that was identified in the group discussions represents the transformation from the use of analog technology to digital technology, leading to a gradual emergence of digitalization in the industry as well as in the L&SC but also in other industries, mainly in the USA. Similar to the development of “Industry 2.0” ( Yin et al. , 2018 ), L&SC 2.0 emerged, which was characterized by computerized coordination processes between different participants in the same chain ( Frazzon et al. , 2019 ).
During L&SC 2.0, EDI (i.e. structured electronic transmission of data between organizations) emerged, and the first EDI message were sent in 1965 using telex messages for trans-Atlantic shipping manifests between The Netherlands and the USA ( McCarthy, 2013 ; Sheombar, 1992 ). Between 1965 and 1980, the development of EDI led to more paperless procedures, the introduction of electronic shipping documents and the use of terminal operating systems ( Heilig et al. , 2017 ), thus displaying early signs of digitalized services. Through the increased use of EDI for international freight forwarding ( Murphy and Daley, 1999 ), international agencies created several standards for exchanging data in trade documents like ISO 3535 and EDI Standard For Administration, Commerce and Trade covered by the norm ISO 9735 ( Janssens, 2011 ). In addition, the automation of sorting and cargo handling become also popular in the 1970s with, e.g. increased use of automated sorting conveyer belts ( Klumpp, 2018 ; Neradilová and Fedorko, 2016 ).
4.3.2 Field frame 2: the dissemination of L&SC management software
The business environment during the second frame was characterized by the emergence of the personal computer (PC). By 1981, IBM's PC became a standard platform and business and government sectors were dominated by PCs ( Ensmenger, 2012 ). Organizations, businesses and individuals increasingly used software solutions for daily operations, word-processing and accounting tasks, with Microsoft becoming the largest PC software company worldwide in the late 1980s ( Campbell-Kelly, 2001 ; Dornberger et al. , 2018 ). The rise of PCs cannot only be viewed as a milestone for better computer access to planners and a new graphical environment for planning but led to a dissemination of flexible spreadsheets and map-based interfaces which enabled huge improvements in L&SC planning and execution technology ( Smith, 2003 ; Tyworth, 1991 ). For L&SC companies, the increase of computerization can also be linked to the rise of L&SC 3.0, known as “systems of logistics management” ( Yavas and Ozkan-Ozen, 2020 ).
The participants highlighted in the group discussions that one of the first companies to recognize the value of supply chain planning and efficiency was Walmart in the USA. As one of the first retailers, Walmart leased not only an IBM computer system in 1975 to electronically control the inventory for its merchandise in their warehouses but also “Retail Link”, an early version of enterprise resource planning (ERP), to integrate its supply chain by providing vendors with relevant information such as sales or inventory levels ( Lummus and Vokurka, 1999 ). As a consequence, ERP systems emerged in the L&SC environment not only to integrate multiple databases for efficiency purposes but also to improve data availability and accuracy, leading to a recognition among managers and companies to better plan and integrate L&SC components ( Robinson, 2007 ; Rutner et al. , 2003 ).
Digital innovations also emerged in the delivery industry, for example, to track packages, with FedEx Express launching the first digitized management system offering package status in real time in 1979, using early prototypes of handheld computers that could scan barcodes ( Baldwin, 2013 ). The integration of databases also allowed an innovation that changed L&SC in manufacturing, the just-in-time (JIT) delivery, which was perfected by Toyota using technological advancements and gained increased attention in the 1980s, further stimulating digitalization efforts for L&SC ( Lai and Cheng, 2016 ; Spencer et al. , 1994 ).
4.3.3 Field frame 3: the globalization of supply chains via the World Wide Web
The business environment in frame 3 is built around the introduction of the World Wide Web, making companies realize the enormous business potential through the Internet. Internet usage took off in the late 1990s and was widely adopted. Overall, participants described the significant impact of the Internet on information flows, which switched from analog to digital from only 1% in 1993 to 51% in 2000 and more than 97% in 2007 ( Hilbert and López, 2011 ). The participants also agreed that the introduction of the World Wide Web and the Internet brought other field actors: the states, which was also confirmed by Drezner (2004) . By upgrading capacity and communication lines, the state pursued mutual interests with corporations and the market, indicating a blending of state, corporation and market logics.
Through the Internet, global communication and coordination of L&SC “made the world smaller” ( Levinson, 2016 ), and manufacturing companies were increasingly outsourcing parts of the supply chain to contract manufacturers, leading to rise of global trade routes ( Cox, 1999 ; Mason et al. , 2002 ). In 2003, global trade represented for the first time more than 50% of the world's gross domestic product (GDP) and was characterized by worldwide complex and multilayered supply chains ( Kroes and Ghosh, 2010 ; World Bank, 2019 ). However, on the one part, the rise of outsourcing was also accompanied by the rise of logistics service providers (LSPs), which were considered as differentiator for a manufacturer's competitive position ( Ansari and Modarress, 2010 ; Li, 2011 ). On the other part, LSPs increasingly recognized the value of offering information technology (IT) and digital solutions to their clients and was also seen as a “competitive differentiator” ( Lieb and Lieb, 2010 ; Razzaque and Sheng, 1998 ).
4.3.4 Field frame 4: the rise of e-commerce
The fourth frame comprises the impact and the rise of online shopping and technology companies, where in early stages, businesses saw e-commerce either as an opportunity or as a competition ( Xu et al. , 2015 ). L&SC companies need to adapt to changing consumer behavior needs with changing business models ( Cho et al. , 2008 ). At the beginning of e-commerce, actors in the field had competing views on how to deal with and react to e-commerce business models. However, the group discussions also highlighted that although the dot-com bubble and often unsustainable online shops collapsed in 2000, businesses recognized e-commerce as an opportunity and adapted their business models, which led to a rise in business-to-consumer (B2C) and business-to-business (B2B) shipments.
The rise of e-commerce can mainly be attributed to the company Amazon, which delivered its first book in 1994 but has since then shaped not only the online shopping experience but also the L&SC landscape ( Wessel and Christensen, 2012 ). Amazon's product – selling online and shipping – “changed the game” ( Liebmann, 2013 ) and challenged brick-and-mortar stores through a new business model that was built around a facilitated network connecting worldwide suppliers and consumers ( Christensen et al. , 2011 ; Wieland and Wallenburg, 2012 ). This network of suppliers and consumers using Amazon as a platform was also built around far-reaching L&SC that relied heavily on IT infrastructure to coordinate the digital information flows. As such, Amazon can be regarded as a “pioneer” that was among the first to use “big data” as an opportunity to gain a competitive advantage ( Wu and Lin, 2018 ), thus not only having adopted a digitalization logic but to further advance and manifest the technology for competitive reasons.
4.3.5 Field frame 5: the deployment of the Internet of Things and big data
The business environment in frame 5 relies heavily on digital products and services and the assumption that information and data of consumers and their transactions can be turned into a competitive advantage, further manifesting and expanding the digitalization logic in the field. More specifically, digitalization is characterized by interconnectivity, automation, machine learning and real-time data, which was also highlighted by the groups’ discussions. As such, the digitalization logic dominates combining physical production and operations with smart digital technology and big data to create a more holistic ecosystem for companies and state actors, the so-called Industry 4.0 which translates into L&SC 4.0, which led and is leading to a digital transformation within the L&SC industry ( Tang and Veelenturf, 2019 ; Yavas and Ozkan-Ozen, 2020 ).
Companies increasingly see digitalization as an opportunity to transform L&SC. For example, in 2017, IBM and Maersk introduced blockchain technology to streamline global customs and shipping processes ( Dobrovnik et al. , 2018 ; Groenfeldt, 2017 ; Kummer et al. , 2020 ). Studies and trials in the shipping industry predict enormous potential for growth and efficiencies through the use of artificial intelligence (AI) ( Rozados and Tjahjono, 2014 ; Schrauf and Berttram, 2018 ; The Economist, 2019 ). AI can be used for predictive analytics in the shipping supply chain ( Gunasekaran et al. , 2017 ) to, for example, the so-called anticipatory shipping which is used to “predict when a customer will make a purchase and begins shipping the product to the nearest hub before the customer places the orders online” ( Lee, 2017 , p. 593).
Given the ample opportunities for enhancements through digitalization in the L&SC industry, it is not a question whether L&SC companies should invest and adopt in process of digitalization, but rather who can use existing automated and digitalized products and services to further generate revenues or to build a competitive advantage. As a consequence, a digitalization logic in the L&SC industry has itself manifested as “digitalization is increasingly impacting the practice of SCM, to the point that SCM processes and activities in 2020 and beyond will no longer be recognizable vs the ingrained processes and activities that emerged from the 20th century/analogue age” ( Stank et al. , 2019 , p. 967).
4.4 The process of the emergence, adoption and manifestation of the digitalization logic
The construction of the field frames and its implications allows to draw conclusions how the digitalization logic in the L&SC industry has emerged on a firm level and manifested itself on the field level. In field frame 1, the emergence of digitalization in L&SC companies can be attributed to what Strang and Soule (1998) call “collective theorizing,” i.e. that several actors in the field were becoming aware that digitalization represents or may represent an opportunity for differentiation and thus is “emerging as a new tool to build and sustain […] absolute advantages” ( Bilbao-Osorio et al. , 2013 , p. 42). In response to the inventions and innovations that served as key factors for a potential change for businesses, L&SC managers engaged in collective theorizing and broadened the scope of digitalization, also creating awareness about the issue and thus leading other actors to embrace the emergence of digitalization in L&SC companies.
In field frame 2, actors started to change their thinking about digitalization, and thus, a shift from the emergence of digitalization to a broader adoption could be observed. Driven by successes of Walmart's supply chain innovations and the JIT delivery, managers increasingly invested in and adopted technologies to maintain or gain competitive advantages. As the FedEx founder Fred Smith were saying, "The information about the package is as important as the package itself" ( Baldwin, 2013 ), indicating that technology advancements can help to build a competitive advantage. As such, complementing the collective theorizing to embrace digitalization, actors in the field were also subject what Ansari et al. (2013) call “active learning,” which occurs when “new information and evidence or changes in material and discursive conditions prompt actors to rethink the assumptions about the calculus of perceived gains and losses underpinning their logics” (p. 1,029). Managers learned that the adoption of new technologies and the use of digital products and services lead to better transparency and operational efficiencies, leading to a widespread adoption of digital management software and systems in L&SC.
Field frame 3 was characterized by the introduction of the Internet which can be considered a milestone for the advancement of L&SC companies, in particular with regard to outsourcing and the associated rise of LSPs ( Sink and Langley, 1997 ). The increasing reliance of manufacturers and global operating companies on LSPs to handle complex and multilayered L&SC processes did not only lead to innovations to increase the efficiency within the L&SC sector but had far-reaching implications on power relations and power structures between nations and businesses. For L&SC companies, implementing and upgrading existing IT capabilities in order to participate in and gain from complex worldwide supply chain constructs “changed the game” and made digitalization a dominant and integral part of logistics. As such, it can be argued that with the introduction of the World Wide Web and the use of the Internet, L&SC companies permanently integrated digital products and services in organizational structures and business practices, thus adopted a digitalization logic.
We could observe in field frame 4, the key actors seek to benefit from digitalization, thus seeing a shift from adoption to manifestation of the digitalization. However, for L&SC companies, in particular for sea and rail, adapting their business model to incorporate the changes stemming from e-commerce was slow due to the reliance on old legacy information systems ( Busse and Wallenburg, 2011 ; Economist, 2018 ; Fruth and Teuteberg, 2017 ). Our data suggest that although incumbent global L&SC companies have adopted a digitalization logic, their fragmented IT management systems and the associated decentralized IT approach made it difficult to catch up with the “new” technology companies such as Amazon and Alibaba which are built on new infrastructure and technology and can use richer and more visible L&SC data ( Choudary et al. , 2019 ).
Field frame 5 represents “L&SC 4.0” ( Winkelhaus and Grosse, 2020 ) or what Stank et al. (2019) call the “digitally dominated paradigm” for the L&SC industry, indicating a catalytic amplification in which “actions at lower levels shifted the calculus for higher-level actors” ( Ansari et al. , 2013 , p. 1,030), thus promoting a wider acceptance and a manifestation of a digitalization logic. Characterized by enhanced visibility, improved analytics and heightened operational flexibility and reduced cycle times, Stank et al. (2019) claim that digitalization will change L&SC and supply chain processes fundamentally and argue that “the digital world is here to stay” (p. 967). Our observations also suggest that from an institutional perspective, digitalization logic not only be adopted in L&SC but has itself manifested in organizational practices and structures. In other words, the digitalization logic has been “institutionalized” in L&SC organizations with the potential to further transform L&SC processes.
Figure 2 presents a summary and a timeline overview that depicts the process of the emergence, adoption and the manifestation of digitalization logic in the L&SC industry and other industries. In particular, the figure shows not only the development of digitalization from L&SC 2.0 to L&SC 4.0 but compares the digitalization process with the evolution from Industry 2.0 to Industry 4.0. Moreover, it depicts the role of actors in the process, i.e. it presents the key actors that were identified in Table 1 , to demonstrate their impact between emergence and manifestation of the digitalization.
5. Conclusion
Digitalization plays an increasingly strategic role in the L&SC industry; the ability to collect and analyze big data, improved visibility and connectivity of information in combination with a physical network with fast and reliable delivery options will have a significant impact on logistics productivity and supply chain networks. Deconstructing the emergence, adoption and the manifestation of digitalization in L&SC industry provides a broader understanding about institutional and industry processes and developments. With this study, we made three contributions: first, we showed how the digitalization logic has emerged, adopted and manifested itself in the L&SC industry. Drawing on institutional theory, which showed the emergence of the digitalization logic on a firm-level starting in 1960s to the manifestation on the field level in 2020, thereby advancing the institutional view on digitalization. In particular, we demonstrated how the interaction between different actors and logics led to institutional change and the process from L&SC 2.0 to L&SC 4.0. Second, we classified historical milestones and key configuring events in L&SC industry that have shaped the emergence and the adoption of the digitalization logic, thereby providing an overview about the key developments in L&SC. More specifically, the categorization of frames allowed us to identify how companies and actors revised their frames, leading to overarching field frameshifts that changed the perception of digitalization and eventually to the manifestation of a digitalization logic in L&SC. Third, we responding to calls to better understand, deconstruct or further advance the implications of digitalization on organization and its processes and structures. Digital advances in today's industries are increasingly impacting the business, social and political environments within the L&SC industry. A better understanding how digitalization has emerged may offer insight into future developments and how companies and organization can react to these developments.
As such, our findings have relevant theoretical and managerial implications. From a theoretical perspective, our theorizing provides insight into the institutionalization of technological progress, which becomes more relevant in today's competitive L&SC environments. Although the adoption of digital products and services in different time frames and sometimes seem random, our study shows that the adoption and manifestation of digitalization in organizations is linked to large and complex sociotechnical system, the “institutional complexity” in which multiple logics are present at the firm and field level. Moreover, using institutional theory to investigate the emergence, adoption and manifestation of digitalization, this study offers an alternate to explain the mechanisms behind changes in actors' perceptions and frames' shifts as well as the diffusion of an institutional logic through a field. In other words, our study shows how field actors dealing with multiple logics not only create various frames but also how these actors revise their frames to reach consensus in the field.
From a managerial perspective, our findings can help managers in the L&SC industry to better understand the transformation of structures and practices that can change the “rules of the game.” Although digitalization can be considered as a competitive advantage in the near-, middle- and long term, certain branches within the L&SC industry have not caught up yet and sometimes show little interest or efforts to drive digitalization in their companies or in their industry branch. For managers, our study not only shows the importance to enforce digitalization in the L&SC industry but also provides insight into the different adoption mechanisms and the associated actors that enact field-level changes, which can help to gain a better understanding how to implement digital practices in their company.
However, these findings need to be viewed in the light of their limitations. Although we are confident that the institutional view is the right approach to better understand the emergence, adaption and manifestation of the digitalization in L&SC, other theories may provide a different view and a more nuanced understanding. We are aware that this topic, covering the developments of over 60 years, is quite complex, and the digitalization within the L&SC industry may have also other influences and is shaped by different actors. The group discussion and the subsequent identification and consolidation of the milestones and frames is inherently subjective; thus, scholars may identify other key events and milestones that had an impact on digitalization in the L&SC industry. And although we have identified the frameshifts and identified how digitalization has established itself on the field level, developing a deeper understanding of “first mover” companies with regard to digitalization and their impact on the field level may also pose an opportunity for future researchers to further explore the link between firm- and field-level changes. Future research may also draw on our findings concerning the role of actors and their influence on digitalization in L&SC industry and compare or contrast our findings with other industries.
Research into digitalization, in particular in the history of digitalization, is still in its infancy. By investigating the emergence, adoption and manifestation of digitalization in the L&SC industry, we have taken the first step toward a better understanding of digitalization and its impact on businesses. We hope that both the findings and the discussions presented in this research will spark discussions and projects in the L&SC and digitalization sphere.
Historical events of logistics and supply chain's digitalization
Digitalization logic: from the emergence to manifestation
Key actors in L&SC digitalization
Field frames of logistics and supply chain's digitalization
Ansari , A. and Modarress , B. ( 2010 ), “ Challenges of outsourcing logistics to third-party providers ”, International Journal of Logistics Systems and Management , Vol. 7 No. 2 , pp. 198 - 218 .
Ansari , S. , Wijen , F. and Gray , B. ( 2013 ), “ Constructing a climate change logic: an institutional perspective on the “tragedy of the commons ”, Organization Science , Vol. 24 No. 4 , pp. 1014 - 1040 .
Baldwin , R. ( 2013 ), “ Shipshape: tracking 40 Years of FedEx tech ”, Wired , available at: https://www.wired.com/2013/04/40-years-of-fedex/ .
Barrett , M. , Davidson , E. , Prabhu , J. and Vargo , S.L. ( 2015 ), “ Service innovation in the digital age: key contributions and future directions ”, MIS Quarterly , Vol. 39 No. 1 , pp. 135 - 154 .
Berger , P.L. and Luckmann , T. ( 1968 ), The Social Construction of Reality: A Treatise in the Socialogy of Knowledge , Anchor Books , Graden City, NY .
Besharov , M.L. and Smith , W.K. ( 2014 ), “ Multiple institutional logics in organizations: explaining their varied nature and implications ”, Academy of Management Review , Vol. 39 No. 3 , pp. 364 - 381 .
Bilbao-Osorio , B. , Dutta , S. and Lanvin , B. ( 2013 ), “ Digitization for economic growth and job creation: regional and industry perspective ”, available at: https://www.strategyand.pwc.com/m1/en/reports/digitization-for-economic-growth-and-job-creation.pdf .
Bloor , M. , Frankland , J. , Thomas , M. and Robson , K. ( 2001 ), Focus Groups in Social Research , Sage , London .
Brennen , J.S. and Kreiss , D. ( 2016 ), “ Digitalization ”, in Jensen , K.B. , Rothenbuhler , E.W. , Pooley , J.D. and Craig , R.T. (Eds), The International Encyclopedia of Communication Theory and Philosophy , Wiley-Blackwell , Chichester , pp. 556 - 566 .
Busse , C. and Wallenburg , C.M. ( 2011 ), “ Innovation management of logistics service providers ”, International Journal of Physical Distribution and Logistics Management , Vol. 41 No. 2 , pp. 187 - 218 .
Campbell-Kelly , M. ( 2001 ), “ Not only Microsoft: the maturing of the personal computer software industry, 1982-1995 ”, Business History Review , Vol. 75 No. 1 , pp. 103 - 145 .
Cho , J.J.K. , Ozment , J. and Sink , H. ( 2008 ), “ Logistics capability, logistics outsourcing and firm performance in an e‐commerce market ”, International Journal of Physical Distribution and Logistics Management , Vol. 38 No. 5 , pp. 336 - 359 .
Choudary , S.P. , Van Alstyne , M.W. and Parker , G.G. ( 2019 ), “ Platforms and blockchain will transform logistics ”, Harvard Business Review , available at: https://hbr.org/2019/06/platforms-and-blockchain-will-transform-logistics .
Christensen , C. , Raynor , M. and McDonald , R. ( 2011 ), Disruptive Innovation , Perseus Book LLC (Ingram) .
Cichosz , M. , Wallenburg , C.M. and Knemeyer , A.M. ( 2020 ), “ Digital transformation at logistics service providers: barriers, success factors and leading practices ”, International Journal of Logistics Management , Vol. 31 No. 2 , pp. 209 - 238 .
Clark , P.A. ( 1985 ), A Review of the Theories of Time and Structure for Organizational Sociology , University of Aston , Bimingham .
Cohen , R. ( 2018 ), “ How Amazon's delivery logistics redefined retail supply chains ”, Journal of Supply Chain Management, Logistics and Procurement , Vol. 1 No. 1 , pp. 75 - 86 .
Cox , A. ( 1999 ), “ Power, value and supply chain management ”, Supply Chain Management: International Journal , Vol. 4 No. 4 , pp. 167 - 175 .
Denyer , D. and Tranfield , D. ( 2009 ), “ Producing a systematic review ”, in Buchanan , D. and Bryman , A. (Eds), The Sage Handbook of Organizational Research Methods , Sage Publications , London , pp. 671 - 689 .
DiMaggio , P.J. and Powell , W.W. ( 1983 ), “ The Iron Cage Revisited: institutional isomorphism and collective rationality in organizational fields ”, American Sociological Review , Vol. 48 No. 2 , pp. 147 - 160 .
Djelic , M.-L. and Quack , S. ( 2008 ), “ Institutions and transnationalization ”, in Greenwood , R. , Oliver , C. , Suddaby , R. and Sahlin-Andersson , K. (Eds), The SAGE Handbook of Organizational Institutionalism , Sage , London , pp. 299 - 323 .
Dobrovnik , M. , Herold , D. , Fürst , E. and Kummer , S. ( 2018 ), “ Blockchain for and in logistics: what to adopt and where to start ”, Logistics , Vol. 2 No. 3 , p. 18 , doi: 10.3390/logistics2030018 .
Dornberger , R. , Inglese , T. , Korkut , S. and Zhong , V.J. ( 2018 ), “ Digitalization: yesterday, today and tomorrow ”, in Dornberger , R. (Ed.), Business Information Systems and Technology 4.0 , Springer , Cham , pp. 1 - 11 .
Drezner , D.W. ( 2004 ), “ The global governance of the Internet: bringing the state back in ”, Political Science Quarterly , Vol. 119 No. 3 , pp. 477 - 498 .
Durach , C.F. , Kembro , J. and Wieland , A. ( 2017 ), “ A new paradigm for systematic literature reviews in supply chain management ”, Journal of Supply Chain Management , Vol. 53 No. 4 , pp. 67 - 85 .
Economist , T. ( 2018 ), “ The global logistics business is going to be transformed by digitization ”, Economist , available at: https://www.economist.com/briefing/2018/04/26/the-global-logistics-business-is-going-to-be-transformed-by-digitisation .
Elsbach , K.D. and Sutton , R.I. ( 1992 ), “ Acquiring organizational legitimacy through illegitimate actions: a marriage of institutional and impression management theories ”, Academy of Management Journal , Vol. 35 No. 4 , pp. 699 - 738 .
Ensmenger , N. ( 2012 ), “ The digital construction of technology: rethinking the history of computers in society ”, Technology and Culture , Vol. 53 No. 4 , pp. 753 - 776 .
Fischer , E. , Reuber , A.R. , Hababou , M. , Johnson , W. and Lee , S. ( 1998 ), “ The role of socially constructed temporal perspectives in the emergence of rapid-growth firms ”, Entrepreneurship: Theory and Practice , Vol. 22 No. 2 , pp. 13 - 30 .
Frazzon , E.M. , Rodriguez , C.M.T. , Pereira , M.M. , Pires , M.C. and Uhlmann , I. ( 2019 ), “ Towards supply chain management 4.0 ”, Brazilian Journal of Operations and Production Management , Vol. 16 No. 2 , pp. 180 - 191 .
Fruth , M. and Teuteberg , F. ( 2017 ), “ Digitization in maritime logistics—what is there and what is missing? ”, Cogent Business and Management , Vol. 4 No. 1 , p. 1411066 .
Garay-Rondero , C.L. , Martinez-Flores , J.L. , Smith , N.R. , Morales , S.O.C. and Aldrette-Malacara , A. ( 2019 ), “ Digital supply chain model in Industry 4.0 ”, Journal of Manufacturing Technology Management , Vol. 31 No. 5 , pp. 887 - 933 .
Giddens , A. ( 1984 ), The Constitution of Society: Outline of the Theory of Structuration , University of California Press , Berkley, CA .
Groenfeldt , T. ( 2017 ), IBM and Maersk Apply Blockchain to Container Shipping , Forbes , available at: https://www.forbes.com/sites/tomgroenfeldt/2017/03/05/ibm-and-maersk-apply-blockchain-to-container-shipping .
Gunasekaran , A. , Papadopoulos , T. , Dubey , R. , Wamba , S.F. , Childe , S.J. , Hazen , B. and Akter , S. ( 2017 ), “ Big data and predictive analytics for supply chain and organizational performance ”, Journal of Business Research , Vol. 70 , pp. 308 - 317 .
Hardy , C. and Maguire , S. ( 2010 ), “ Discourse, field-configuring events, and change in organizations and institutional fields: narratives of DDT and the Stockholm Convention ”, Academy of Management Journal , Vol. 53 No. 6 , pp. 1365 - 1392 .
Heilig , L. , Lalla-Ruiz , E. and Voß , S. ( 2017 ), “ Digital transformation in maritime ports: analysis and a game theoretic framework ”, Netnomics: Economic Research and Electronic Networking , Vol. 18 Nos 2-3 , pp. 227 - 254 .
Herold , D.M. and Lee , K.-H. ( 2019 ), “ The influence of internal and external pressures on carbon management practices and disclosure strategies ”, Australasian Journal of Environmental Management , Vol. 26 No. 1 , pp. 63 - 81 .
Herold , D.M. , Farr‐Wharton , B. , Lee , K.H. and Groschopf , W. ( 2019 ), “ The interaction between institutional and stakeholder pressures: advancing a framework for categorising carbon disclosure strategies ”, Business Strategy and Development , Vol. 2 No. 2 , pp. 77 - 90 .
Hilbert , M. and López , P. ( 2011 ), “ The world's technological capacity to store, communicate, and compute information ”, Science , Vol. 332 No. 6025 , pp. 60 - 65 .
Hinings , B. , Gegenhuber , T. and Greenwood , R. ( 2018 ), “ Digital innovation and transformation: an institutional perspective ”, Information and Organization , Vol. 28 No. 1 , pp. 52 - 61 .
Holmström , J. , Holweg , M. , Lawson , B. , Pil , F.K. and Wagner , S.M. ( 2019 ), “ The digitalization of operations and supply chain management: theoretical and methodological implications ”, Journal of Operations Management , Vol. 65 No. 8 , pp. 728 - 734 .
Hribernik , M. , Zero , K. , Kummer , S. and Herold , D.M. ( 2020 ), “ City logistics: towards a blockchain decision framework for collaborative parcel deliveries in micro-hubs ”, Transportation Research Interdisciplinary Perspectives , Vol. 8 , p. 100274 .
Janssens , G. ( 2011 ), “ Electronic data interchange: from its birth to its new role in logistics information systems ”, International Journal of Information Technology and Systems , Vol. 3 , pp. 45 - 56 .
Kaplan , S. ( 2008 ), “ Framing contests: strategy making under uncertainty ”, Organization Science , Vol. 19 No. 5 , pp. 729 - 752 .
Klumpp , M. ( 2018 ), “ Automation and artificial intelligence in business logistics systems: human reactions and collaboration requirements ”, International Journal of Logistics Research and Applications , Vol. 21 No. 3 , pp. 224 - 242 .
Koch , T. and Windsperger , J. ( 2017 ), “ Seeing through the network: competitive advantage in the digital economy ”, Journal of Organ Dysfunction , Vol. 6 No. 1 , p. 6 .
Kroes , J.R. and Ghosh , S. ( 2010 ), “ Outsourcing congruence with competitive priorities: impact on supply chain and firm performance ”, Journal of Operations Management , Vol. 28 No. 2 , pp. 124 - 143 .
Kummer , S. , Herold , D.M. , Dobrovnik , M. , Mikl , J. and Schäfer , N. ( 2020 ), “ A systematic review of blockchain literature in logistics and supply chain management: identifying research questions and future directions ”, Future Internet , Vol. 12 No. 3 , p. 60 .
Lai , K.-h. and Cheng , T.E. ( 2016 ), Just-in-time Logistics , Routledge , New York .
Langley , A. ( 1999 ), “ Strategies for theorizing from process data ”, Academy of Management Review , Vol. 24 No. 4 , pp. 691 - 710 .
Lee , C. ( 2017 ), “ A GA-based optimisation model for big data analytics supporting anticipatory shipping in Retail 4.0 ”, International Journal of Production Research , Vol. 55 No. 2 , pp. 593 - 605 .
Levinson , M. ( 2016 ), The Box: How the Shipping Container Made the World Smaller and the World Economy Bigger-With a New Chapter by the Author , Princeton University Press , Princeton, NJ .
Li , L. ( 2011 ), “ Assessing the relational benefits of logistics services perceived by manufacturers in supply chain ”, International Journal of Production Economics , Vol. 132 No. 1 , pp. 58 - 67 .
Lieb , K.J. and Lieb , R.C. ( 2010 ), “ Environmental sustainability in the third-party logistics (3PL) industry ”, International Journal of Physical Distribution and Logistics Management , Vol. 40 No. 7 , pp. 524 - 533 .
Liebmann , W. ( 2013 ), Amazon Changes the Game…Again , Forbes , available at: https://www.forbes.com/sites/wendyliebmann/2013/06/25/amazon-changes-the-game-again/#155b0ec72dfb .
Loebbecke , C. and Picot , A. ( 2015 ), “ Reflections on societal and business model transformation arising from digitization and big data analytics: a research agenda ”, The Journal of Strategic Information Systems , Vol. 24 No. 3 , pp. 149 - 157 .
Lounsbury , M. and Ventresca , M. ( 2003 ), “ The new structuralism in organizational theory ”, Organization , Vol. 10 No. 3 , pp. 457 - 480 .
Lounsbury , M. ( 2008 ), “ Institutional rationality and practice variation: new directions in the institutional analysis of practice ”, Accounting, Organizations and Society , Vol. 33 No. 4 , pp. 349 - 361 .
Lummus , R.R. and Vokurka , R.J. ( 1999 ), “ Defining supply chain management: a historical perspective and practical guidelines ”, Industrial Management and Data Systems , Vol. 99 No. 1 , pp. 11 - 17 .
Lyall , A. , Mercier , P. and Gstettner , S. ( 2018 ), “ The death of supply chain management ”, Harvard Business Review , Vol. 15 , pp. 2 - 4 .
Maguire , S. and Hardy , C. ( 2009 ), “ Discourse and deinstitutionalization: the decline of DDT ”, Academy of Management Journal , Vol. 52 No. 1 , pp. 148 - 178 .
Mason , S.J. , Cole , M.H. , Ulrey , B.T. and Yan , L. ( 2002 ), “ Improving electronics manufacturing supply chain agility through outsourcing ”, International Journal of Physical Distribution and Logistics Management , Vol. 32 No. 7 , pp. 610 - 620 .
Mathauer , M. and Hofmann , E. ( 2019 ), “ Technology adoption by logistics service providers ”, International Journal of Physical Distribution and Logistics Management , Vol. 49 No. 4 , pp. 416 - 434 .
McCarthy , B. ( 2013 ), “ EDI history ”, The Logicbroker Blog , available at: https://blog.logicbroker.com/blog/2013/08/19/edi-history .
McKinnon , A.C. ( 2013 ), “ Starry-eyed: journal rankings and the future of logistics research ”, International Journal of Physical Distribution and Logistics Management , Vol. 43 No. 1 , pp. 6 - 17 .
Mikl , J. , Herold , D.M. , Ćwiklicki , M. and Kummer , S. ( 2020a ), “ The impact of digital logistics start-ups on incumbent firms: a business model perspective ”, International Journal of Logistics Management . doi: 10.1108/IJLM-04-2020-0155 .
Mikl , J. , Herold , D.M. , Pilch , K. , Ćwiklicki , M. and Kummer , S. ( 2020b ), “ Understanding disruptive technology transitions in the global logistics industry: the role of ecosystems ”, Review of International Business and Strategy . doi: 10.1108/RIBS-07-2020-0078 .
Murphy , P.R. and Daley , J.M. ( 1999 ), “ EDI benefits and barriers ”, International Journal of Physical Distribution and Logistics Management , Vol. 29 No. 3 , pp. 207 - 217 .
Neradilová , H. and Fedorko , G. ( 2016 ), “ The use of computer simulation methods to reach data for economic analysis of automated logistic systems ”, Open Engineering , Vol. 6 No. 1 , pp. 700 - 710 .
North , K. , Aramburu , N. and Lorenzo , O.J. ( 2019 ), “ Promoting digitally enabled growth in SMEs: a framework proposal ”, Journal of Enterprise Information Management , Vol. 33 No. 1 , pp. 238 - 262 .
O'Marah , K. ( 2017 ), Blockchain for Supply Chain: Enormous Potential Down the Road , Forbes , March 9th .
Orlikowski , W.J. and Barley , S.R. ( 2001 ), “ Technology and institutions: what can research on information technology and research on organizations learn from each other? ”, MIS Quarterly , Vol. 25 No. 2 , pp. 145 - 165 .
Pawson , R. ( 2006 ), Evidence-based Policy: A Realist Perspective , Sage , London .
Porter , M.E. ( 1985 ), Competitive Strategy: Creating and Sustaining Superior Performance , Free Press , New York .
Purdy , J.M. and Gray , B. ( 2009 ), “ Conflicting logics, mechanisms of diffusion, and multilevel dynamics in emerging institutional fields ”, Academy of Management Journal , Vol. 52 No. 2 , pp. 355 - 380 .
Rabinovich , E. and Cheon , S. ( 2011 ), “ Expanding horizons and deepening understanding via the use of secondary data sources ”, Journal of Business Logistics , Vol. 32 No. 4 , pp. 303 - 316 .
Rachinger , M. , Rauter , R. , Müller , C. , Vorraber , W. and Schirgi , E. ( 2019 ), “ Digitalization and its influence on business model innovation ”, Journal of Manufacturing Technology Management , Vol. 30 No. 8 , pp. 1143 - 1160 .
Razzaque , M.A. and Sheng , C.C. ( 1998 ), “ Outsourcing of logistics functions: a literature survey ”, International Journal of Physical Distribution and Logistics Management , Vol. 28 No. 2 , pp. 89 - 107 .
Reay , T. and Hinings , C.R. ( 2009 ), “ Managing the rivalry of competing institutional logics ”, Organization Studies , Vol. 30 No. 6 , pp. 629 - 652 .
Ritter , T. and Pedersen , C.L. ( 2020 ), “ Digitization capability and the digitalization of business models in business-to-business firms: past, present, and future ”, Industrial Marketing Management , Vol. 86 , pp. 180 - 190 .
Robinson , A. ( 2007 ), The Evolution and History of Supply Chain Management , Cerasis , available at: https://cerasis.com/history-of-supply-chain-management/ .
Rozados , I.V. and Tjahjono , B. ( 2014 ), “ Big data analytics in supply chain management: trends and related research ”, paper presented at the 6th International Conference on Operations and Supply Chain Management , Bali .
Rutner , S.M. , Gibson , B.J. and Williams , S.R. ( 2003 ), “ The impacts of the integrated logistics systems on electronic commerce and enterprise resource planning systems ”, Transportation Research Part E: Logistics and Transportation Review , Vol. 39 No. 2 , pp. 83 - 93 .
Sandberg , B. and Aarikka-Stenroos , L. ( 2014 ), “ What makes it so difficult? A systematic review on barriers to radical innovation ”, Industrial Marketing Management , Vol. 43 No. 8 , pp. 1293 - 1305 .
Schneiberg , M. and Clemens , E.S. ( 2006 ), “ The typical tools for the job: research strategies in institutional analysis ”, Sociological Theory , Vol. 24 No. 3 , pp. 195 - 227 .
Schrauf , S. and Berttram , P. ( 2018 ), “ How digitization makes the supply chain more efficient, agile, and customer-focused ”, available at: https://www.strategyand.pwc.com/gx/en/insights/2016/digitization-more-efficient.html .
Scott , W.R. ( 1991 ), “ Unpacking institutional arguments ”, in Powell , W.W. and DiMaggio , P.J. (Eds), The New Institutionalism in Organizational Analysis , University of Chicago Press , Chicago , pp. 164 - 182 .
Scott , W.R. ( 2012 ), “ Embedding the examination of multilevel factors in an organization field context ”, JNCI Monographs , Vol. 2012 No. 44 , pp. 32 - 33 .
Seo , M.-G. and Creed , W.D. ( 2002 ), “ Institutional contradictions, praxis, and institutional change: a dialectical perspective ”, Academy of Management Review , Vol. 27 No. 2 , pp. 222 - 247 .
Sewell , W.H. ( 1996 ), “ Historical events as transformations of structures: inventing revolution at the Bastille ”, Theory and Society , Vol. 25 No. 6 , pp. 841 - 881 .
Seyedghorban , Z. , Tahernejad , H. , Meriton , R. and Graham , G. ( 2020 ), “ Supply chain digitalization: past, present and future ”, Production Planning and Control , Vol. 31 Nos 2-3 , pp. 96 - 114 .
Sheombar , H.S. ( 1992 ), “ EDI‐induced redesign of co‐ordination in logistics ”, International Journal of Physical Distribution and Logistics Management , Vol. 22 No. 8 , pp. 4 - 14 .
Sink , H.L. and Langley , C.J. Jr ( 1997 ), “ A managerial framework for the acquisition of third-party logistics services ”, Journal of Business Logistics , Vol. 18 No. 2 , pp. 163 - 189 .
Smith , G.A. ( 2003 ), “ Using integrated spreadsheet modeling for supply chain analysis ”, Supply Chain Management: International Journal , Vol. 8 No. 4 , pp. 285 - 290 .
Snow , D.A. , Rochford , E.B. Jr , Worden , S.K. and Benford , R.D. ( 1986 ), “ Frame alignment processes, micromobilization, and movement participation ”, American Sociological Review , Vol. 51 No. 4 , pp. 464 - 481 .
Spencer , M.S. , Rogers , D.S. and Daugherty , P.J. ( 1994 ), “ JIT systems and external logistics suppliers ”, International Journal of Operations and Production Management , Vol. 14 No. 6 , pp. 60 - 74 .
Stank , T. , Esper , T. , Goldsby , T.J. , Zinn , W. and Autry , C. ( 2019 ), “ Toward a digitally dominant paradigm for twenty-first century supply chain scholarship ”, International Journal of Physical Distribution and Logistics Management , Vol. 49 No. 10 , pp. 956 - 971 .
Strang , D. and Soule , S.A. ( 1998 ), “ Diffusion in organizations and social movements: from hybrid corn to poison pills ”, Annual Review of Sociology , Vol. 24 No. 1 , pp. 265 - 290 .
Suchman , M.C. ( 1995 ), “ Managing legitimacy: strategic and institutional approaches ”, Academy of Management Review , Vol. 20 No. 3 , pp. 571 - 610 .
Suddaby , R. , Bitektine , A. and Haack , P. ( 2017 ), “ Legitimacy ”, The Academy of Management Annals , Vol. 11 No. 1 , pp. 451 - 478 .
Tang , C.S. and Veelenturf , L.P. ( 2019 ), “ The strategic role of logistics in the industry 4.0 era ”, Transportation Research Part E: Logistics and Transportation Review , Vol. 129 , pp. 1 - 11 .
The Economist ( 2019 ), “ Digitisation is helping to deliver goods faster ”, Economist , available at: https://www.economist.com/special-report/2019/07/11/digitisation-is-helping-to-deliver-goods-faster .
Thornton , P.H. and Ocasio , W. ( 2008 ), “ Institutional logics ”, in Greenwood , R. , Oliver , C. , Suddaby , R. and Sahlin , A. (Eds), The Sage Handbook of Organizational Institutionalism , Sage , London , pp. 100 - 129 .
Thornton , P.H. , Ocasio , W. and Lounsbury , M. ( 2012 ), The Institutional Logics Perspective: A New Approach to Culture, Structure, and Process , Oxford University Press .
Tranfield , D. , Denyer , D. and Smart , P. ( 2003 ), “ Towards a methodology for developing evidence‐informed management knowledge by means of systematic review ”, British Journal of Management , Vol. 14 No. 3 , pp. 207 - 222 .
Tyworth , J.E. ( 1991 ), “ Transport selection: computer modelling in a spreadsheet environment ”, International Journal of Physical Distribution and Logistics Management , Vol. 21 No. 7 , pp. 28 - 36 .
Verma , S. and Bhattacharyya , S.S. ( 2017 ), “ Perceived strategic value-based adoption of Big Data Analytics in emerging economy ”, Journal of Enterprise Information Management , Vol. 30 No. 3 , pp. 354 - 382 .
Wessel , M. and Christensen , C.M. ( 2012 ), “ Surviving disruption ”, Harvard Business Review , Vol. 90 No. 12 , pp. 56 - 64 .
Wieland , A. ( 2020 ), “ Dancing the supply chain: toward transformative supply chain management ”, Journal of Supply Chain Management , Vol. 57 No. 1 , pp. 58 - 73 .
Wieland , A. and Wallenburg , C.M. ( 2012 ), “ Dealing with supply chain risks ”, International Journal of Physical Distribution and Logistics Management , Vol. 42 No. 10 , pp. 887 - 905 .
Winkelhaus , S. and Grosse , E.H. ( 2020 ), “ Logistics 4.0: a systematic review towards a new logistics system ”, International Journal of Production Research , Vol. 58 No. 1 , pp. 18 - 43 .
Wooten , M. and Hoffman , A.J. ( 2008 ), “ Organizational fields: past, present and future ”, in Greenwood , R. , Oliver , C. , Shalin-Andersson , K. and Suddaby , R. (Eds), The Sage Handbook of Organizational Institutionalism , Sage , London , pp. 130 - 147 .
World Bank ( 2019 ), “ Data bank - world development indicators ”, available at: https://data.worldbank.org/indicator/NE.TRD.GNFS.ZS .
Wu , P.-J. and Lin , K.-C. ( 2018 ), “ Unstructured big data analytics for retrieving e-commerce logistics knowledge ”, Telematics and Informatics , Vol. 35 No. 1 , pp. 237 - 244 .
Xu , S.X. , Cheng , M. and Huang , G.Q. ( 2015 ), “ Efficient intermodal transportation auctions for B2B e-commerce logistics with transaction costs ”, Transportation Research Part B: Methodological , Vol. 80 , pp. 322 - 337 .
Yavas , V. and Ozkan-Ozen , Y.D. ( 2020 ), “ Logistics centers in the new industrial era: a proposed framework for logistics center 4.0 ”, Transportation Research Part E: Logistics and Transportation Review , Vol. 135 , p. 101864 .
Yin , Y. , Stecke , K.E. and Li , D. ( 2018 ), “ The evolution of production systems from Industry 2.0 through Industry 4.0 ”, International Journal of Production Research , Vol. 56 Nos 1-2 , pp. 848 - 861 .
Corresponding author
Related articles, we’re listening — tell us what you think, something didn’t work….
Report bugs here
All feedback is valuable
Please share your general feedback
Join us on our journey
Platform update page.
Visit emeraldpublishing.com/platformupdate to discover the latest news and updates
Questions & More Information
Answers to the most commonly asked questions here
MBA Knowledge Base
Business • Management • Technology
Home » Management Case Studies » Case Study: Wal-Mart’s Distribution and Logistics System
Case Study: Wal-Mart’s Distribution and Logistics System
As the world’s largest retailer with net sales of almost $419 billion for the fiscal year 2011, Wal-Mart is considered a “best-in-class” company for its supply chain management practices . These practices are a key competitive advantage that have enabled Wal-Mart to achieve leadership in the retail industry through a focus on increasing operational efficiency and on customer needs. Wal-Mart’s corporate website calls “logistics” and “distribution” the heart of its operation, one that keeps millions of products moving to customers every day of the year.
Wal-Mart’s highly-automated distribution centers, which operate 24 hours a day and are served by Wal-Mart’s truck fleet, are the foundation of its growth strategy and supply network. In the United States alone, the company has more than 40 regional distribution centers for import flow and more than 140 distribution centers for domestic flow. When entering a new geographic arena, the company first determines if the area will be able to contain enough stores to support a distribution center. Each distribution center supports between 75 to 100 retail stores within a 250-mile area. Once a center is built, stores are gradually built around it to saturate the area and the distribution network is realigned to maximize efficiencies through a process termed “reoptimization”. The result is a “trickle-down” effect: trucks do not have to travel as far to retail stores to make deliveries, shorter distances reduce transportation costs and lead time, and shorter lead time means holding less safety inventory. If shortages do occur, replenishment can be made more quickly because stores receive daily deliveries from distribution centers.

An important feature of Wal-Mart’s logistics infrastructure was its fast and responsive transportation system. The distribution centers were serviced by more than 3,500 company owned trucks. These dedicated truck fleets allowed the company to ship goods from the distribution centers to the stores within two days and replenish the store shelves twice a week. The truck fleet was the visible link between the stores and distribution centers. Wal-Mart believed that it needed drivers who were committed and dedicated to customer service. The company hired only experienced drivers who had driven more than 300,000 accident-free miles, with no major traffic violation.
Wal-Mart truck drivers generally moved the merchandise-loaded trailers from Wal-Mart distribution centers to the retail stores serviced by each distribution center. These retail stores were considered as customers by the distribution centers. The drivers had to report their hours of service to a coordinator daily. The coordinator scheduled all dispatches depending on the available driving time and the estimated time for travel between the distribution centers and the retail stores. The coordinator informed the driver of his dispatches, either on the driver’s arrival at the distribution center or on his return to the distribution center from the retail store. The driver was usually expected to take a loaded truck trailer from the distribution center to the retail store and return back with an empty trailer. He had to dispatch a loaded truck trailer at the retail store and spend the night there. A driver had to bring the trailer at the dock of a store only at its scheduled unloading time, no matter when he arrived at the store. The drivers delivered the trailers in the afternoon and evening hours and they would be unloaded at the store at nights. There was a gap of two hours between unloading of each trailer. For instance, if a store received three trailers, the first one would be unloaded at midnight (12 AM), the second one would be unloaded at 2 AM and the third one at 4 AM. Although, the trailers were left unattended, they were secured by the drivers, until the store personnel took charge of them at night. Wal-Mart received more trailers than they had docks, due to their large volume of business.
Because Wal-Mart’s fast, responsive transportation operations are such a major part of the company’s successful logistics system, great care is taken in the hiring, training, supervising, and assigning of drivers’ schedules and job responsibilities. From the onset of his retailing career, Wal-Mart founder Sam Walton recognized the importance of hiring experienced people and of building loyalty not only in his customers but also in his employees. The company hires only experienced drivers who have driven more than 300,000 accident-free miles and whom it believes will be committed to customer service. Its retail stores are considered important “customers” of the distribution centers. As stated in the “Private Fleet Driver Handbook” that each driver is given a copy of, drivers are expected to be “polite” and “kind” when dealing with store personnel and others. In addition to containing a driver’s code of conduct, the Private Fleet Driver Handbook gives instructions and rules for following pre-planned travel routes and schedules, the responsible unloading of a truck trailer at a retail store, and the safe-guarding of Wal-Mart’s property. For example, although drivers deliver loaded trailers in the afternoon and evening hours, a trailer can be brought to the store’s docks only at its scheduled unloading time. Because unloading is done at two-hour intervals during the night, a driver is expected to spend the night, returning to the distribution center at a pre-scheduled time with an empty trailer. Coordinators closely monitor the detailed records of each driver’s activities for adherence to rules. Violations are dealt with according to handbook procedures, which include employee education to prevent future occurrences of incorrect actions. By effectively managing every aspect of its transportation operations and treating its drivers fairly, Wal-Mart gets results that are unrivaled in the logistics arena. This philosophy parallels the successful coaching style of New York Giant’s football coach Tom Coughlin who believes that rules are more than just discipline. Rules are a key to consistency, which leads to preparedness, which then leads to proper execution.
To make its distribution process more efficient, Wal-Mart also made use of a logistics technique known as ‘cross-docking.’ In this system, the finished goods were directly picked up from the manufacturing plant of a supplier, sorted out and then directly supplied to the customers. The system reduced the handling and storage of finished goods, virtually eliminating the role of the distribution centers and stores. There were five types of cross-docking.
- Opportunistic Cross docking – In this method of cross docking, the exact information about where the necessary good should be shipped and from where it should be procured and exact quantity which will be sent was necessary. This method of cross docking has allowed the company to ship directly the goods, necessary retail clients, not storing them in warehouse bins or shelves. Opportunistic cross docking could also be used when the warehouse software of management installed by the retailer, has set ready it, that the specific product was ready to moving and could be moved immediately.
- Flow-through Cross docking – In this type of cross docking, there was a constant inflow and outflow of the goods from the distribution center. This type of cross docking was mostly suitable for the perishable goods which had very short interval of time, or the goods which were difficult to be kept in warehouses. This cross docking system was mainly accompanied by supermarkets and other retail discount stores, especially for perishable items.
- Distributor Cross docking – In this type of cross docking, the manufacturer has delivered the goods to directly to retailer. No intermediaries have been involved in this process. It has allowed the retailer to save a major portion of the expenses in the form of storage. As the retailer should not support the distribution center for storage various kinds of the goods, he has helped it to save warehouse costs. The lead time for the delivery of goods from the manufacturer to the consumer was also drastically reduced. However, this method had some disadvantages too. Expenses of transportation both for the manufacturer and for the retailer tended to increase during time when the goods have been required to be transported to different locations several times. Besides, the transportation system should be very fast. Otherwise, the purpose of cross docking has been lost. The transportation system should be also highly responsive and to take the responsibility for delays in delivery of the goods. The retailer was at a greater risk. He has lost that advantage to sharing risks with the manufacturer. This type of cross docking was suitable only for those retailers who had the big distributive network and could be used in situations when goods had to be delivered in a short span of time.
- Manufacturing Cross docking – In Manufacturing cross docking, these cross docking facilities served the factories and acted as temporary and “mini warehouses.” Whenever a manufacturing company required some parts or materials for manufacturing a particular product, it was delivered by the supplier in small lots within a very short span of time, just when it was needed. This helped reduce the transportation and warehouse costs substantially.
- Pre-Allocated Cross Docking – Pre-allocated cross docking is very much like the usual cross-docking, except that in this type of cross docking, the goods are already packed and labeled by the manufacturer and it is ready for shipment to the distribution center from where it is sent to the store. The goods can be delivered by the distribution center directly to the store without opening the pack of the manufacturer and re-packing the goods. The store can then deliver the goods directly to the consumer without any further repacking. Goods received by the distribution center or the store are directly sent into the outbound shipping truck, to be delivered to the consumer, without altering the package of the good. Cross docking requires very close co-ordination and co-operation of the manufacturers, warehouse personnel and the stores personnel. Goods can be easily and quickly delivered only when accurate information is available readily. The information can be managed with the help of Electronic Data Interchange (EDI) and other general sales information.
In cross docking, requisitions received for different goods from a store were converted into purchase or procurement orders. These purchase orders were then forwarded to the manufacturers who conveyed their ability or inability to supply the goods within a particular period of time. In cases where the manufacturer agreed to supply the required goods within the specified time, the goods were directly forwarded to a place called the staging area. The goods were packed here according to the orders received from different stores and then directly sent to the respective customers. To gain maximum out of cross-docking, Wal-Mart had to make fundamental changes in its approach to managerial control . Traditionally, decisions about merchandising, pricing and promotions had been highly centralized and were generally taken at the corporate level. The crossdocking system, however, changed this practice. The system shifted the focus from “supply chain” to the “demand chain,” which meant that instead of the retailer ‘pushing’ products into the system; customers could ‘pull’ products, when and where they needed. This approach placed a premium on frequent, informal cooperation among stores, distribution centers and suppliers with far less centralized control than earlier.
Besides, if the supplier knows also, that for the company it will be incredibly difficult to make proper adjustments to guarantee smooth transition to the different supplier, then they will be less inclined to lower their price as much. It is not, how existing suppliers deal with Wal-Mart; when they see that Wal-Mart has found the supplier who will give them lower price, current suppliers lower their prices accordingly. They know that logistical system of the Wal-Mart can address with transition easily, and consequently they do not receive additional leverage, as it will not be difficult or expensive for Wal-Mart to choose other supplier.
Another reason that Wal-Mart’s prices are so competitive is because they buy in such large quantities that transportation from one end of the supply chain to another is not as expensive for additional units. This aspect of the logistical system does not come from skill or expertise it simply comes from the sheer size of the company, but this is still a factor. On the other hand, the Wal-Mart buys so many supplies from different places throughout the world, that they have the luxury of using bigger trucks and using less fuel to go back and forth. Also if by chance they have to use shipping services to transport material from one location to another, Wal-Mart will give them so much business that they will get huge discounts.
On the whole, the logistical system that Wal-Mart uses is so effective because it is so flexible. This is why Wal-Mart is able to offer things much cheaper than other companies can.
About Wal-mart Stores
Wal-Mart Stores, Inc. is the largest retailer in the world, the world’s second-largest company and the nation’s largest nongovernmental employer. Wal-Mart Stores, Inc. operates retail stores in various retailing formats in all 50 states in the United States. The Company’s mass merchandising operations serve its customers primarily through the operation of three segments. The Wal-Mart Stores segment includes its discount stores, Supercenters, and Neighborhood Markets in the United States. The Sam’s club segment includes the warehouse membership clubs in the United States. The Company’s subsidiary, McLane Company, Inc. provides products and distribution services to retail industry and institutional foodservice customers. Wal-Mart serves customers and members more than 200 million times per week at more than 8,416 retail units under 53 different banners in 15 countries. With fiscal year 2010 sales of $405 billion, Wal-Mart employs more than 2.1 million associates worldwide. Nearly 75% of its stores are in the United States (“Wal-Mart International Operations”, 2004), but Wal-Mart is expanding internationally. The Group is engaged in the operations of retail stores located in all 50 states of the United States, Argentina, Brazil, Canada, Japan, Puerto Rico and the United Kingdom, Central America, Chile, Mexico,India and China.
Related Posts:
- Case Study: Why Woolworths Failed as a Business?
- Case Study of Cisco: Transformation of Entire Supply Chain into an Extended Enterprise System
- Case Study of Zara: Sustainability in Fast Fashion Industry
- Case Study: Tesco's US Grocery Market Entry
- Case Study: Supply Chain Management of Walmart
- Zara's Lean Operation: Source of Competitive Advantage
- Case Study: Wal-Marts Competitive Advantage
- Case Study: McDonalds Marketing Strategies
- Case Study: Why Walmart Failed in Germany?
- Case Study: Business Strategy Analysis of Wal-Mart
One thought on “ Case Study: Wal-Mart’s Distribution and Logistics System ”
Leave a reply cancel reply.
Your email address will not be published. Required fields are marked *
Green logistics in a South African retailer : a case study
- UnisaIR Home
- Electronic Theses and Dissertations
Show simple item record
Files in this item
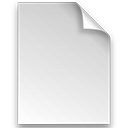
This item appears in the following Collection(s)
- SDG09 Industry, innovation and infrastructure [19]
- Theses and Dissertations (Applied Management) [31]
- Unisa ETD [12175] Electronic versions of theses and dissertations submitted to Unisa since 2003
Search UnisaIR
All of unisair.
- Communities & Collections
- By Issue Date
This Collection
- View Usage Statistics
Supply Chain Management
Creating resilient supply chains. Sustainable, flexible and autonomous.
Computer Vision Spearheading AI Productivity In 2024, Says Latest Research
Average productivity gains of 42% over three years predicted but potential barriers are a lack of skills and in-house knowledge.
Share this link via:
Or copy link:
Link has been copied
Munich, Germany. 18 th April 2024 – Adoption of Computer Vision technology, powered by AI, is at a tipping point and set to power productivity across a range of industry sectors, according to the latest research commissioned by Panasonic Connect Europe. On average, decision-makers predict a productivity increase of 42% in the three years following deployment. The manufacturing industry anticipates the biggest boost with increases in productivity as high as 52%.
Computer Vision is the field of artificial intelligence that enables computers and systems to derive meaningful information from digital images. It is the “eyes of AI”, observing, identifying, classifying, tracking, and ultimately interpreting images into usable “knowledge” that can be further interrogated by humans or by complementary AI.
Wide variety of applications
Respondents report that Computer Vision technology is being used across a wide variety of business departments and applications . Practical activities such as repairs and maintenance, production line monitoring, and quality control slightly outweigh use in security and health and safety. Applications in logistics and supply chain are popular, along with real-time projection mapping and people tracking, demonstrating the broad scope of use cases relevant to Computer Vision tech.
Available skills a barrier to deployment
The biggest barriers to deploying the technology were a lack of external specialist support (37%) and maintaining computer vision knowledge in the business (33%). Businesses are also highly sensitive to the potential ethical concerns of deploying AI-powered Computer Vision applications. The largest concern being data security (35%), closely followed by personal privacy and surveillance concerns, lack of corporate guidance and fears for job replacement – all level at 32%.
Wider AI deployment surging ahead
Looking at the wider adoption of Generative AI, the momentum is clear. Overall, more than two-thirds (67%) say that using generative AI is important to their business. More than one-third of respondents (37%) have already implemented a solution and are seeing benefits. A further third (34%) are in the planning stage or the process of implementing the technology. 17% are still thinking about it, but only 13% say they will not deploy Generative AI at all.
"The research shows clearly that Computer Vision technology is not just a concept but a present reality that is already steering businesses towards significant productivity and operational gains. Organisations across all sectors that are not yet in the planning stages of deployment are in danger of falling behind. There is also a clear need for specialists, such as Panasonic, to assist businesses in understanding how to deploy this technology effectively and responsibly."
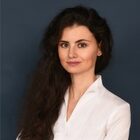
The independent research, carried out by Opinion Matters and commissioned by Panasonic Connect Europe, surveyed 300 senior decision makers responsible for digital transformation and AI/computer vision implementation, working in companies with an annual turnover of 50 million+ Euros across Germany and the UK.
Select your language
- Asia-Pacific


IMAGES
VIDEO
COMMENTS
Managing the Inbound Supply Chain. Penske helped this supplier minimize supply chain disruptions by designing a network that optimized mode selection, routing and analysis. Read supply chain case studies about our work with customers to create supply chain management solutions that support long-term growth and profitability.
Case Study - Industrial Manufacturing logistics. Our customer is a leading multinational manufacturer of automobiles and agricultural machinery. The company entered the U.S. market in 2000; since 2002, Noatum Logistics has handled the company's customs brokerage at Noatum Logistics' Houston branch. Read More.
At the height of the pandemic in 2020, US Foods struggled, as restaurant and school closures reduced demand for foodservice distribution. The situation improved after the return of indoor dining and in-person learning, but an industry-wide shortage of truck drivers and warehouse staff hampered the foodservice distributor's post-pandemic recovery.
It's Time to Rethink Your Global Logistics. by. Willy C. Shih. and. Adrien Foucault. March 12, 2021. HBR Staff. Summary. The initial supply and demand shocks caused by the pandemic were followed ...
Enhance profitability. Optimization typically leads to 5%- 10% net annual savings in total logistics operating costs, impacting: Transport costs. Fixed facility costs. Variable handling costs. Terminal productivity increases resulting from 'right-sizing'. Network analysis secures future performance of the supply chain given volatility in ...
BUILDING THE NO.1 LOGISTICS INFRASTRUCTURE IN THE 'SELECT-SHOP' INDUSTRY. Founded in 1977 in Yoyogi, Shibuya-ku in Tokyo, Baycrew's is a leading 'select-shop' company which provides products purchased domestically and abroad alongside its original items. Since their launch they've grown to an organization with over 5,500 employees ...
Case Studies in Carbon-Efficient Logistics. Logistics is a leading source of carbon. Nearly 6 percent of the greenhouse gases generated by humans come from the flow of products to consumers. Reducing these emissions takes more than setting goals; it requires clear, measurable initiatives that hit sustainability targets while delivering lower ...
Read Case Study. Unlock the power of optimized supply chain solutions with Omni Logistics. Explore our Case Studies to discover how we've transformed businesses across industries. From critical on-time delivery for international retail stores to innovative solutions for global technology manufacturers, we're ALL IN for our clients.
The global collaboration and integration of online and offline channels have brought new challenges to the logistics industry. Thus, smart logistics has become a promising solution for handling the increasing complexity and volume of logistics operations. ... Hawking P (2018). Big data analytics and IoT in logistics: A case study. International ...
About this book. Logistics is the ideal book for Bachelor students of logistics, providing a solid foundation as well as a practical guide. In modular and clear form, it explains key concepts, principles, and practices of logistics. Learning objectives as well as several case studies are integrated into each chapter.
This logistics case study is one of continuous improvement and adaptation. It illustrates how a deep understanding of each partner's capabilities and needs can lead to remarkable success. Our customer's transformation underlines the importance of embracing logistics technology to stay ahead in the dynamic world of transportation management.
Case Studies: How AI Consulting Has Helped Logistics Companies Succeed. According to McKinsey, the successful implementation of AI has helped businesses improve logistics costs by 15%, inventory levels by 35%, and service levels by 65%. AI consulting for logistics businesses brings a number of benefits, but RTS Labs has taken it a step further ...
Convert Your Logistics Operations to a Revenue Generator. Schedule a Demo. Locus has an enormous library of successful case studies, their use cases, success stories, approaches, and end results. Read & know about our solutions!
Know-How from more than 1,700 supply chain projects and 25+ years of experience. Gain full global network transparency. Achieve cost savings through supply chain optimization. Support for all phases, from conception to implementation into your supply chain. Deep knowledge of all modes of transport.
Logistics Case Studies. Zipline Logistics prioritizes YOUR bottom line. We are experts in retail logistics and exclusively service CPG brands shipping into retail. This means we're a logistics solutions provider — not just a rate and a truck — and we genuinely care about and invest in CPG brands' success. Check out the Zipline love ...
Cost Savings: By outsourcing logistics functions to a 3PL provider, businesses can reduce their capital expenditure on infrastructure, technology, and personnel. 3PL providers leverage economies of scale to offer cost-effective solutions, allowing companies to focus on their core business activities.
getty. With the Internet of Things (IoT), the world is undergoing a technological revolution. One of the industries that IoT has influenced immensely is logistics, with the global IoT in logistics ...
Logistics Bureau. SEPTEMBER 26, 2018. The following five mini case studies explore a few high-profile companies that have managed to sustain their supply chain cost reduction efforts and keep expenses under control. Of course, the above case studies are merely summaries of the changes these high-profile brands made to their supply chains.
The paper presents research carried out at a medium-size manufacturing organization in east Asia. The study tries to highlight the importance of supply chain management; specifically, our aim for this study is to understand logistics and performance measurement in the logistics and supply chain, and we include a theoretical discussion of online data collected and a case study of the logistic ...
Cloud-based testing service ensures smooth post-M&A data integration. Case Study. 4PL logistics ecosystem enables JIT procurement. Case Study. Hackathons shape next-gen digital freight marketplace. Case Study. Food services enterprise modernizes business intelligence ecosystem. Case Study. Predictive freight analytics streamlines mining logistics.
Even before the second wave of the disease began, in the spring of 2021, the pace of recovery was unclear. In 2019, the McKinsey Global Institute (MGI) predicted that India's logistics sector would expand at a compound annual growth rate of more than 10 percent, from $200 billion in early 2020 to at least $320 billion in 2025.
1. Introduction. Digitalization in the logistics and supply chain management (L&SC) industry is of increasing strategic importance for businesses as it impacts established paradigms, business models and industry boundaries (Barrett et al., 2015; Cichosz et al., 2020).A mounting number of companies allocate resources to exploit digital opportunities that have the potential to transform ...
Case Study: Wal-Mart's Distribution and Logistics System. As the world's largest retailer with net sales of almost $419 billion for the fiscal year 2011, Wal-Mart is considered a "best-in-class" company for its supply chain management practices. These practices are a key competitive advantage that have enabled Wal-Mart to achieve ...
A thematic analysis was used to analyse the data. The evidence from the study showed that there has been ongoing emphasis and implementation of GL in the retail industry of South Africa. The study concluded that retailers need to invest more in the adoption of technology to enhance the implementation of GL. en. dc.language.iso.
This study aims to explore the significance of trust among companies within the supply chain and investigate its effect on collaborative supply chain risk management. In the current uncertain business environment, it is crucial for companies to establish trust relationships with their trading partners and collaboratively manage risks. This research seeks to understand how such trust ...
Munich, Germany. 18 th April 2024 - Adoption of Computer Vision technology, powered by AI, is at a tipping point and set to power productivity across a range of industry sectors, according to the latest research commissioned by Panasonic Connect Europe. On average, decision-makers predict a productivity increase of 42% in the three years following deployment.