
- RCA 101 – 5-Why Analysis (Free Training)
- RCA 201 – Basic Failure Analysis
- RCA 301 – PROACT® RCA Certification
- RCA 401 – RCA Train The Trainer
- Other Trainings
- 5 Whys Root Cause Analysis Template
- RCA Template
- Chronic Failure Calculator
7 Powerful Root Cause Analysis Tools and Techniques
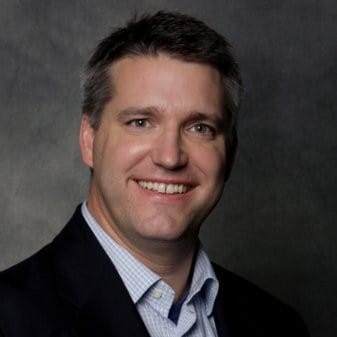
By Sebastian Traeger
Updated: February 22, 2024
Reading Time: 5 minutes

1. The Ishikawa Fishbone Diagram (IFD)
2. pareto chart, 4. failure mode and effects analysis (fmea), 5. proact® rca method, 6. affinity diagram, 7. fault tree analysis (fta).
With over two decades in business – spanning strategy consulting, tech startups and executive leadership – I am committed to helping your organization thrive. At Reliability, we’re on a mission to help enhance strategic decision-making and operational excellence through the power of Root Cause Analysis, and I hope this article will be helpful! Our goal is to help you better understand these root cause analysis techniques by offering insights and practical tips based on years of experience. Whether you’re new to doing RCAs or a seasoned pro, we trust this will be useful in your journey towards working hard and working smart.
Root Cause Analysis (RCA) shines as a pivotal process that helps organizations identify the underlying reasons for problems, failures, and inefficiencies. The goal is simple: find the cause, fix it, and prevent it from happening again. But the process can be complex, and that’s where various RCA techniques come into play.
Let’s dive into seven widely utilized RCA techniques and explore how they can empower your team’s problem-solving efforts.
Named after Japanese quality control statistician Kaoru Ishikawa, the Fishbone Diagram is a visual tool designed for group discussions. It helps teams track back to the potential root causes of a problem by sorting and relating them in a structured way. The diagram resembles a fishbone, with the problem at the head and the causes branching off the spine like bones. This visualization aids in categorizing potential causes and studying their complex interrelationships.
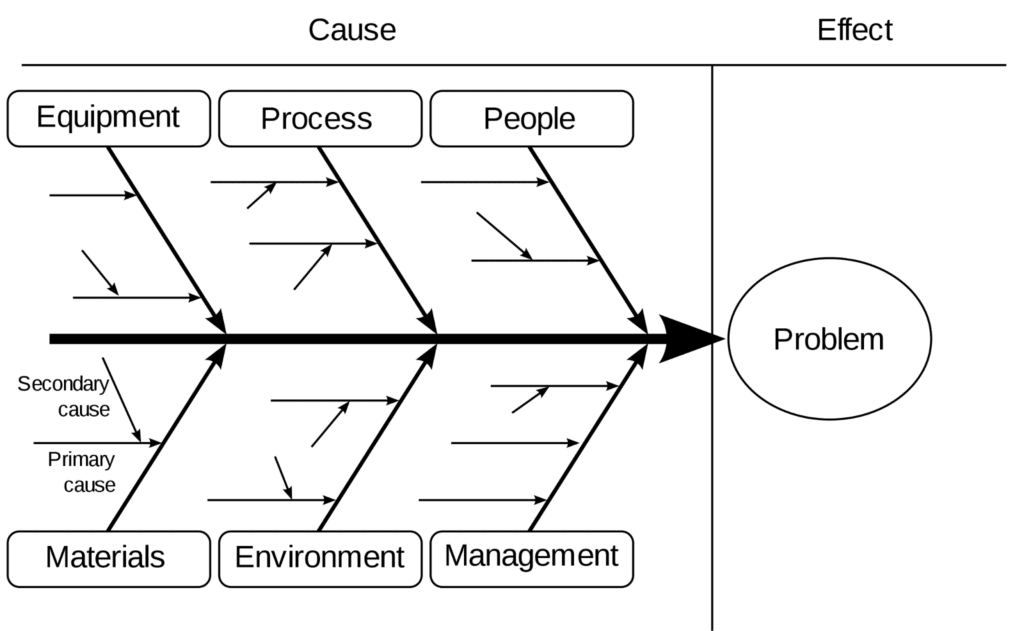
The Pareto Chart, rooted in the Pareto Principle, is a visual tool that helps teams identify the most significant factors in a set of data. In most situations, 80% of problems can be traced back to about 20% of causes. By arranging bar heights from tallest to shortest, teams can prioritize the most significant factors and focus their improvement efforts where they can have the most impact.
The 5 Whys method is the epitome of simplicity in getting to the bottom of a problem. By repeatedly asking ‘why’ (typically five times), you can delve beneath the surface-level symptoms of a problem to unearth the root cause. This iterative interrogation is most effective when answers are grounded in factual evidence.

When prevention is better than cure, Failure Mode and Effects Analysis (FMEA) steps in. This systematic, proactive method helps teams identify where and how a process might fail. By predicting and examining potential process breakdowns and their impacts, teams can rectify issues before they turn into failures. FMEA is a three-step process that involves identifying potential failures, analyzing their effects, and prioritizing them based on severity, occurrence, and detection ratings.
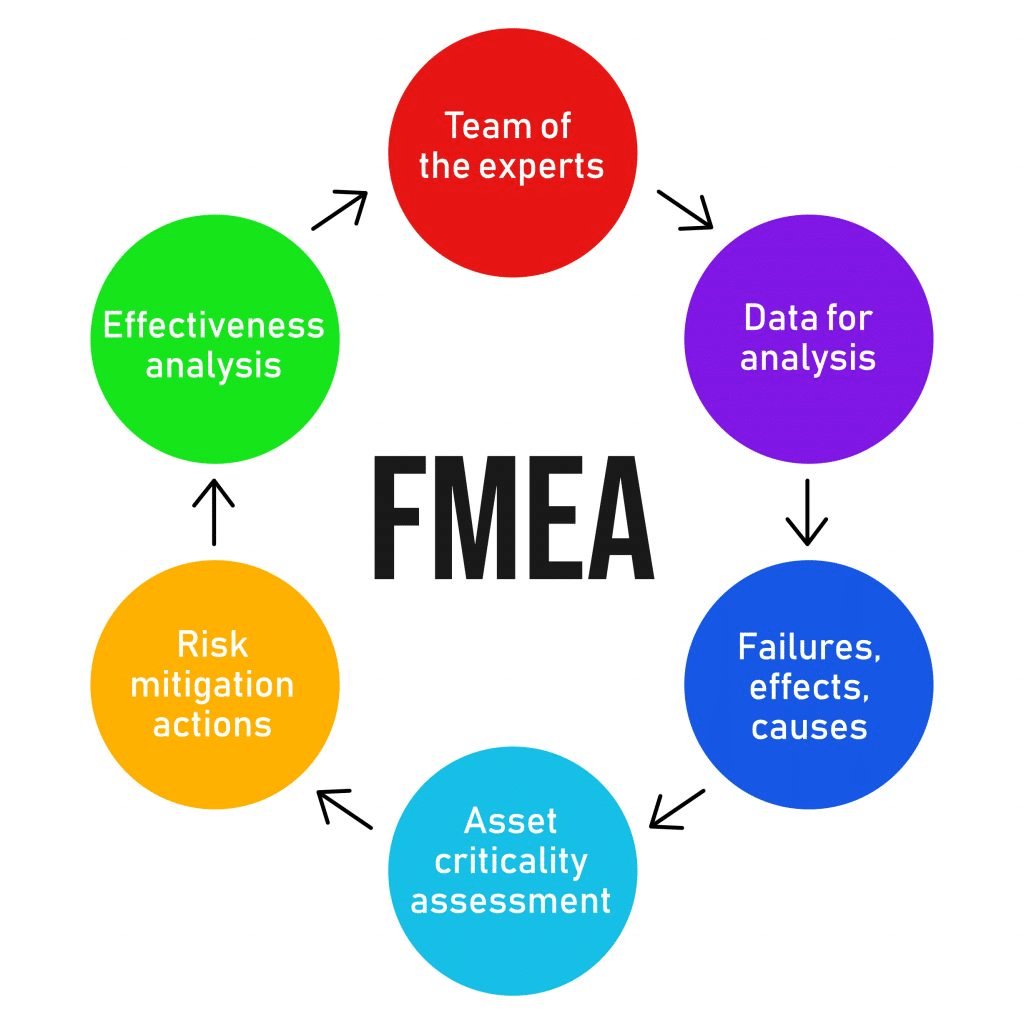
The PROACT ® RCA technique is a robust process designed to drive significant business results. Notably used to identify and analyze ‘chronic failures,’ which can otherwise be overlooked, this method is defined by its name:
PReserving Evidence and Acquiring Data: Initial evidence collection step based on the 5-P’s – Parts, Position, People, Paper, and Paradigms.
Order Your Analysis Team and Assign Resources: Assembling an unbiased team to analyze a specific failure.
Analyze the Event: Reconstructing the event using a logic tree to identify Physical, Human, and Latent Root Causes.
Communicate Findings and Recommendations: Developing and implementing solutions to prevent root cause recurrence.
Track and Measure Impact for Bottom Line Results: Tracking the success of implemented recommendations and correlating the RCA’s effectiveness with ROI.
PROACT® RCA excels in mitigating risk, optimizing cost, and boosting performance, making it a valuable addition to any RCA toolkit.
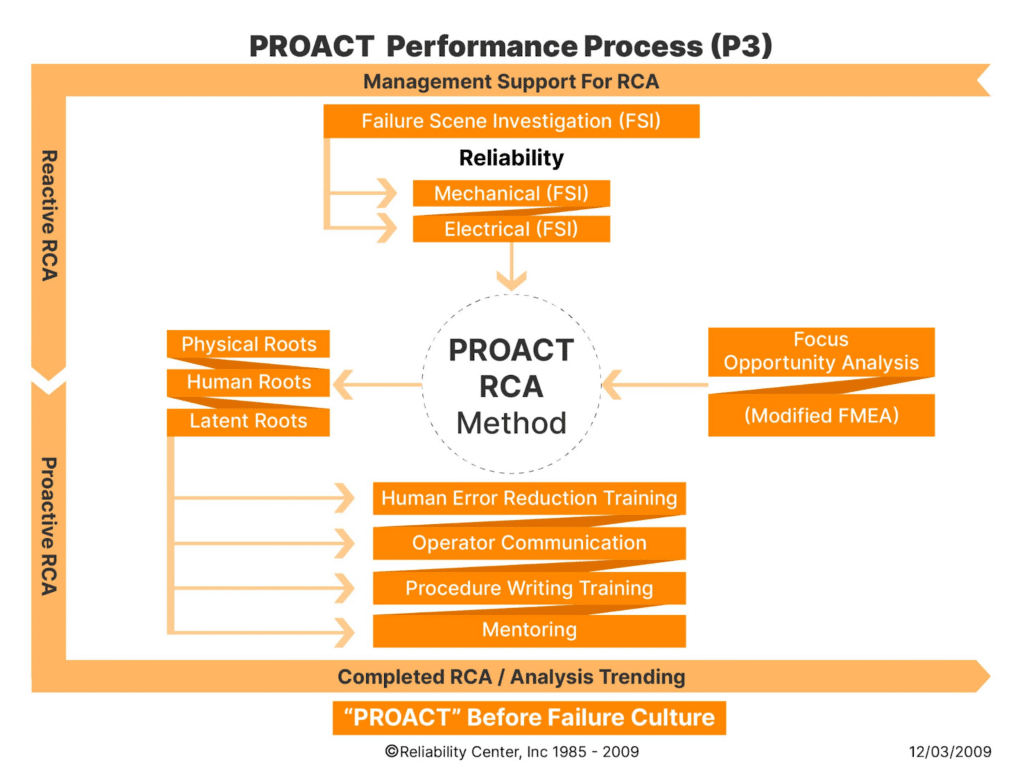
The Affinity Diagram is a powerful tool for dealing with large amounts of data. It organizes a broad range of information into groups based on their natural relationships, creating a clear, visual representation of complex situations. It’s particularly beneficial for condensing feedback from brainstorming sessions into manageable categories, fostering a better understanding of the broader picture.
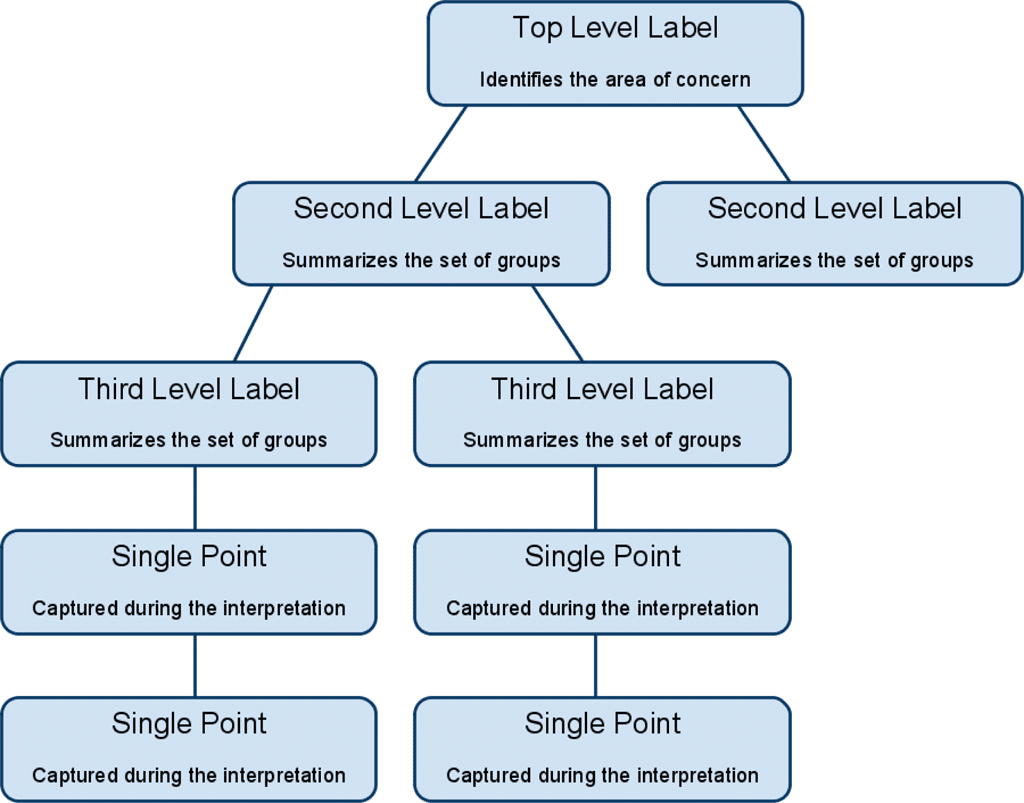
Fault Tree Analysis (FTA) is a top-down, deductive failure analysis that explores the causes of faults or problems. It involves graphically mapping multiple causal chains to track back to possible root causes, using a tree-like diagram. FTA is particularly useful in high-risk industries, such as aerospace and nuclear power, where preventing failure is crucial.
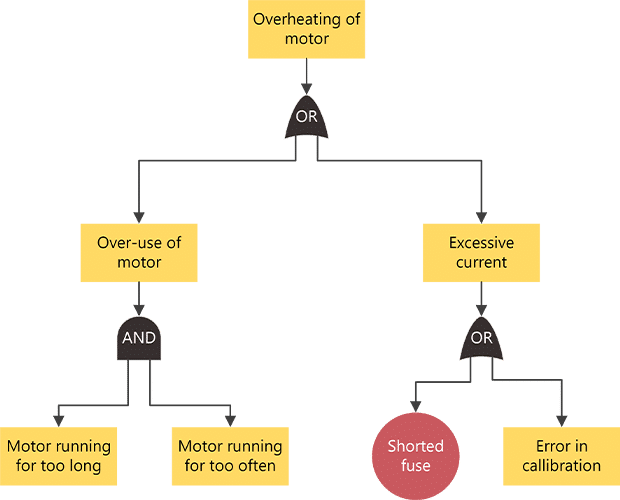
Each RCA technique provides a unique approach for viewing and understanding problems, helping you pinpoint the root cause more effectively. The key is to understand when and how to use each tool, which can significantly enhance your team’s problem-solving capabilities.
Power up your RCA analysis with our EasyRCA and revolutionize your problem-solving process. Start Your Free Trial.
In conclusion, the techniques presented offer a diverse set of tools to help organizations address problems and inefficiencies effectively. From visual representations like the Ishikawa Fishbone Diagram and Pareto Chart to more proactive approaches such as the 5 Whys and Failure Mode and Effects Analysis (FMEA), each technique provides a unique perspective on identifying and mitigating root causes.
The PROACT® RCA Method stands out for its comprehensive process, particularly suited for chronic failures. Additionally, the Affinity Diagram and Fault Tree Analysis (FTA) contribute valuable insights by organizing data and exploring causal chains, respectively. Leveraging these techniques strategically enhances a team’s problem-solving capabilities, enabling them to make informed decisions and drive continuous improvement.
I hope you found these 7 techniques insightful and actionable! Stay tuned for more thought-provoking articles as we continue to share our knowledge. Success is rooted in a thorough understanding and consistent application, and we hope this article was a step in unlocking the full potential of Root Cause Analysis for your organization. Reliability runs initiatives such as an online learning center focused on the proprietary PROACT® RCA methodology and EasyRCA.com software. For additional resources, visit our Reliability Resources .
- Root Cause Analysis /
Recent Posts
Root Cause Analysis with 5 Whys Technique (With Examples)
What Is Fault Tree Analysis (FTA)? Definition & Examples
Guide to Failure Mode and Effects Analysis (FMEA)
Root Cause Analysis Software
Our RCA software mobilizes your team to complete standardized RCA’s while giving you the enterprise-wide data you need to increase asset performance and keep your team safe.
Root Cause Analysis Training
[email protected]
Tel: 1 (800) 457-0645
Share article with friends:
Have a language expert improve your writing
Run a free plagiarism check in 10 minutes, generate accurate citations for free.
- Knowledge Base
- Starting the research process
- What Is a Fishbone Diagram? | Templates & Examples
What Is a Fishbone Diagram? | Templates & Examples
Published on January 2, 2023 by Tegan George . Revised on January 29, 2024.
A fishbone diagram is a problem-solving approach that uses a fish-shaped diagram to model possible root causes of problems and troubleshoot possible solutions. It is also called an Ishikawa diagram, after its creator, Kaoru Ishikawa, as well as a herringbone diagram or cause-and-effect diagram.
Fishbone diagrams are often used in root cause analysis , to troubleshoot issues in quality management or product development. They are also used in the fields of nursing and healthcare, or as a brainstorming and mind-mapping technique many students find helpful.
Table of contents
How to make a fishbone diagram, fishbone diagram templates, fishbone diagram examples, advantages and disadvantages of fishbone diagrams, other interesting articles, frequently asked questions about fishbone diagrams.
A fishbone diagram is easy to draw, or you can use a template for an online version.
- Your fishbone diagram starts out with an issue or problem. This is the “head” of the fish, summarized in a few words or a small phrase.
- Next, draw a long arrow, which serves as the fish’s backbone.
- From here, you’ll draw the first “bones” directly from the backbone, in the shape of small diagonal lines going right-to-left. These represent the most likely or overarching causes of your problem.
- Branching off from each of these first bones, create smaller bones containing contributing information and necessary detail.
- When finished, your fishbone diagram should give you a wide-view idea of what the root causes of the issue you’re facing could be, allowing you to rank them or choose which could be most plausible.
Receive feedback on language, structure, and formatting
Professional editors proofread and edit your paper by focusing on:
- Academic style
- Vague sentences
- Style consistency
See an example
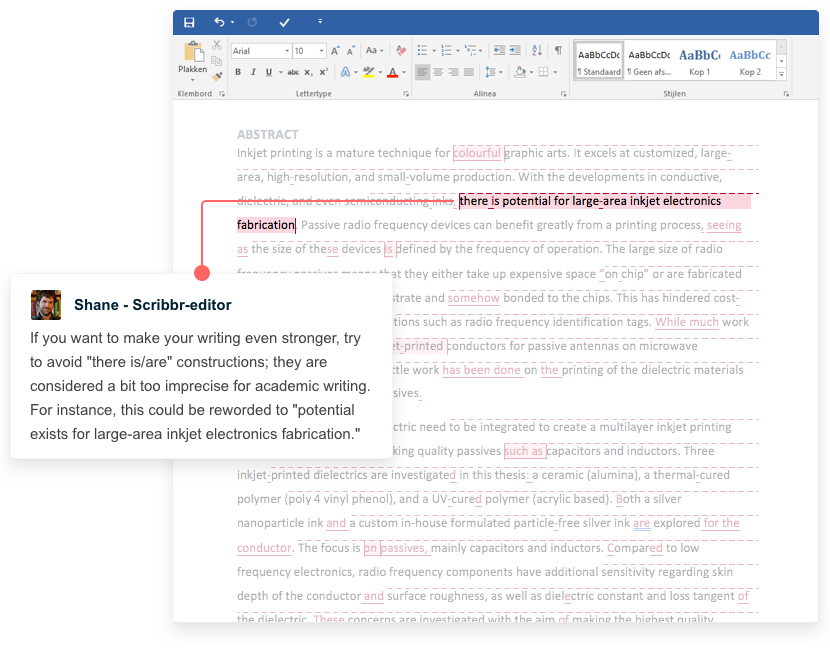
There are no built-in fishbone diagram templates in Microsoft programs, but we’ve made a few free ones for you to use that you can download below. Alternatively, you can make one yourself using the following steps:
- In a fresh document, go to Insert > Shapes
- Draw a long arrow from left to right, and add a text box on the right-hand side. These serve as the backbone and the head of the fish.
- Next, add lines jutting diagonally from the backbone. These serve as the ribs, or the contributing factors to the main problem.
- Next, add horizontal lines jutting from each central line. These serve as the potential causes of the problem.
Lastly, add text boxes to label each function.
You can try your hand at filling one in yourself using the various blank fishbone diagram templates below, in the following formats:
Fishbone diagram template Excel
Download our free Excel template below!
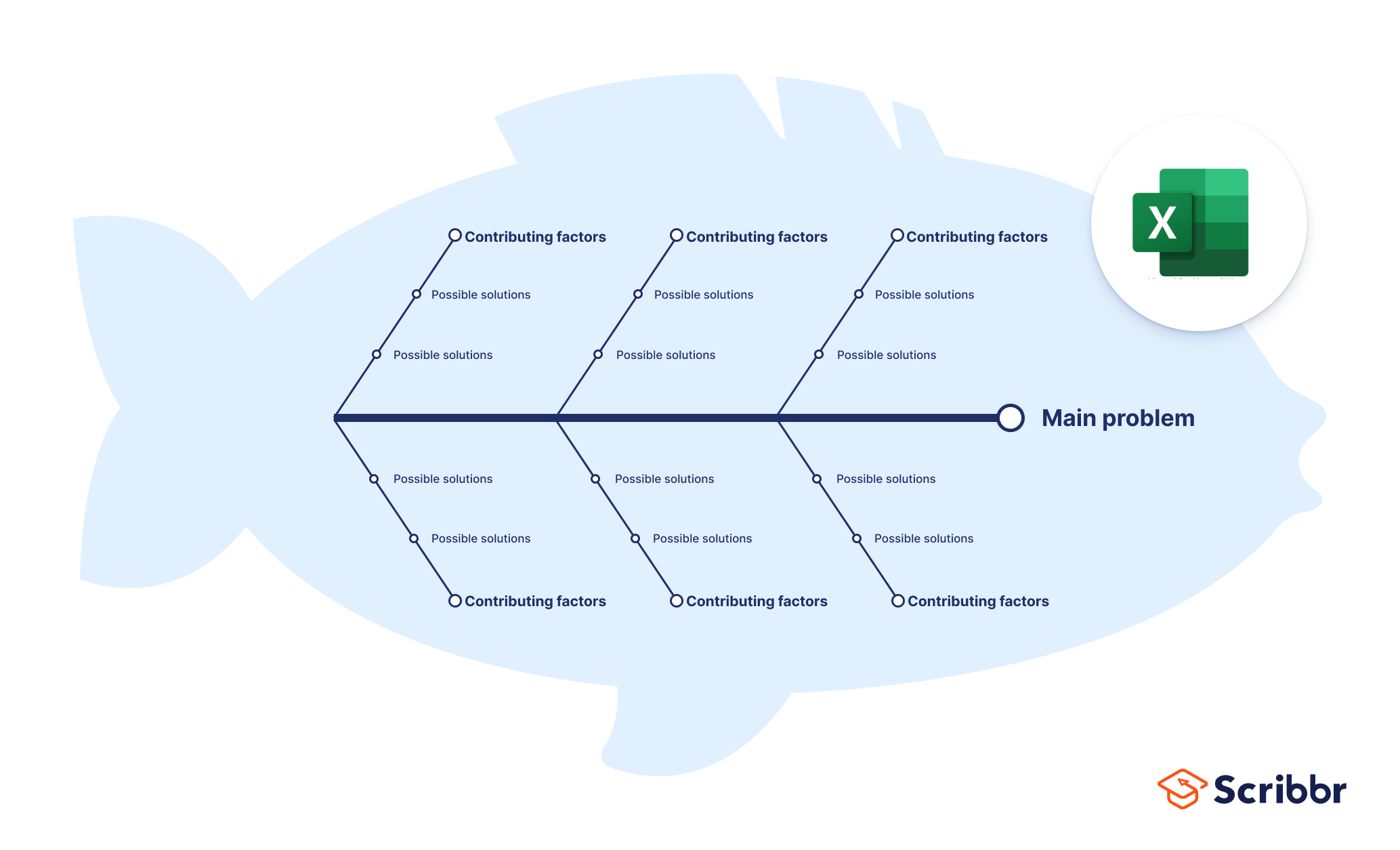
Fishbone diagram template Word
Download our free Word template below!
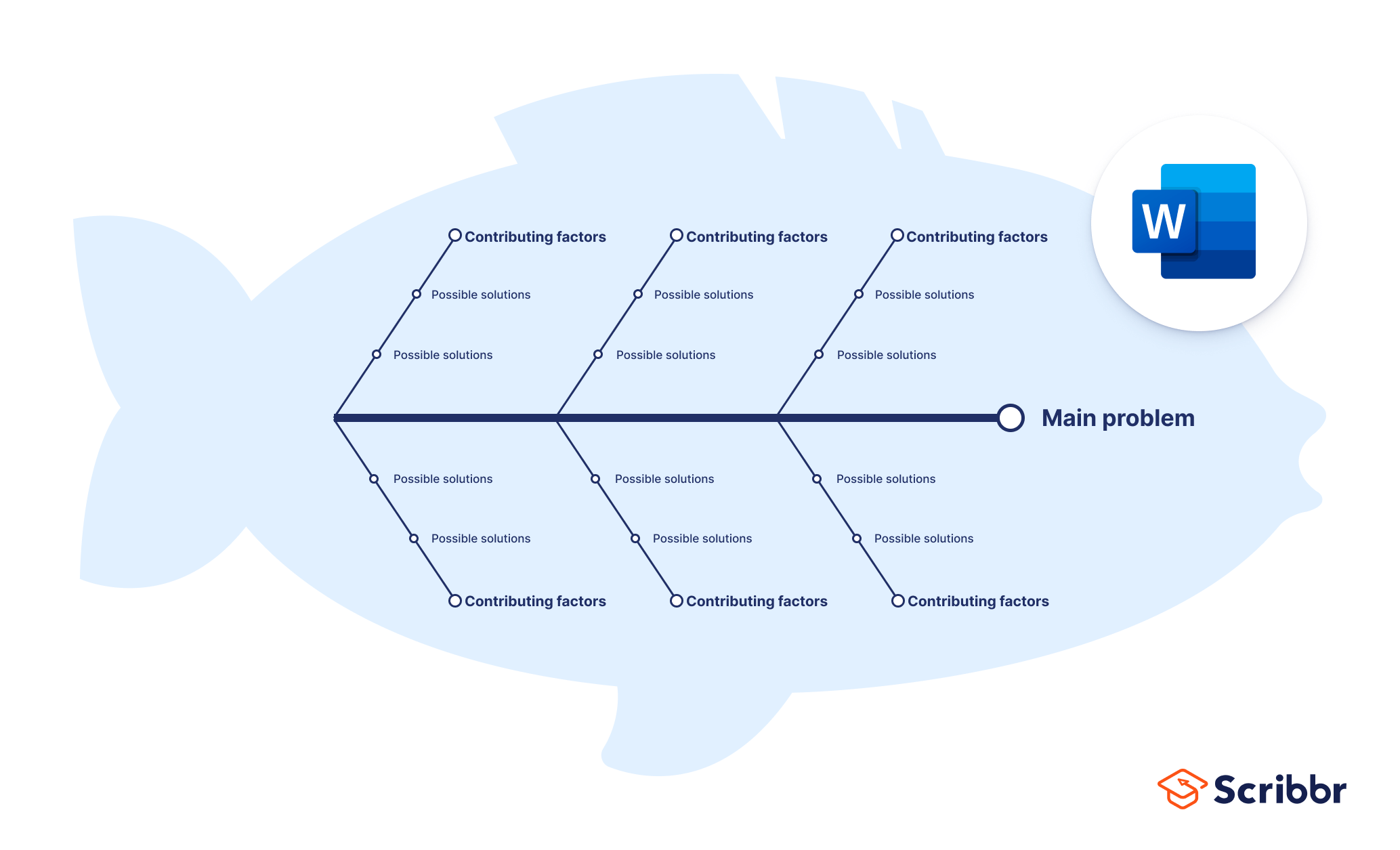
Fishbone diagram template PowerPoint
Download our free PowerPoint template below!
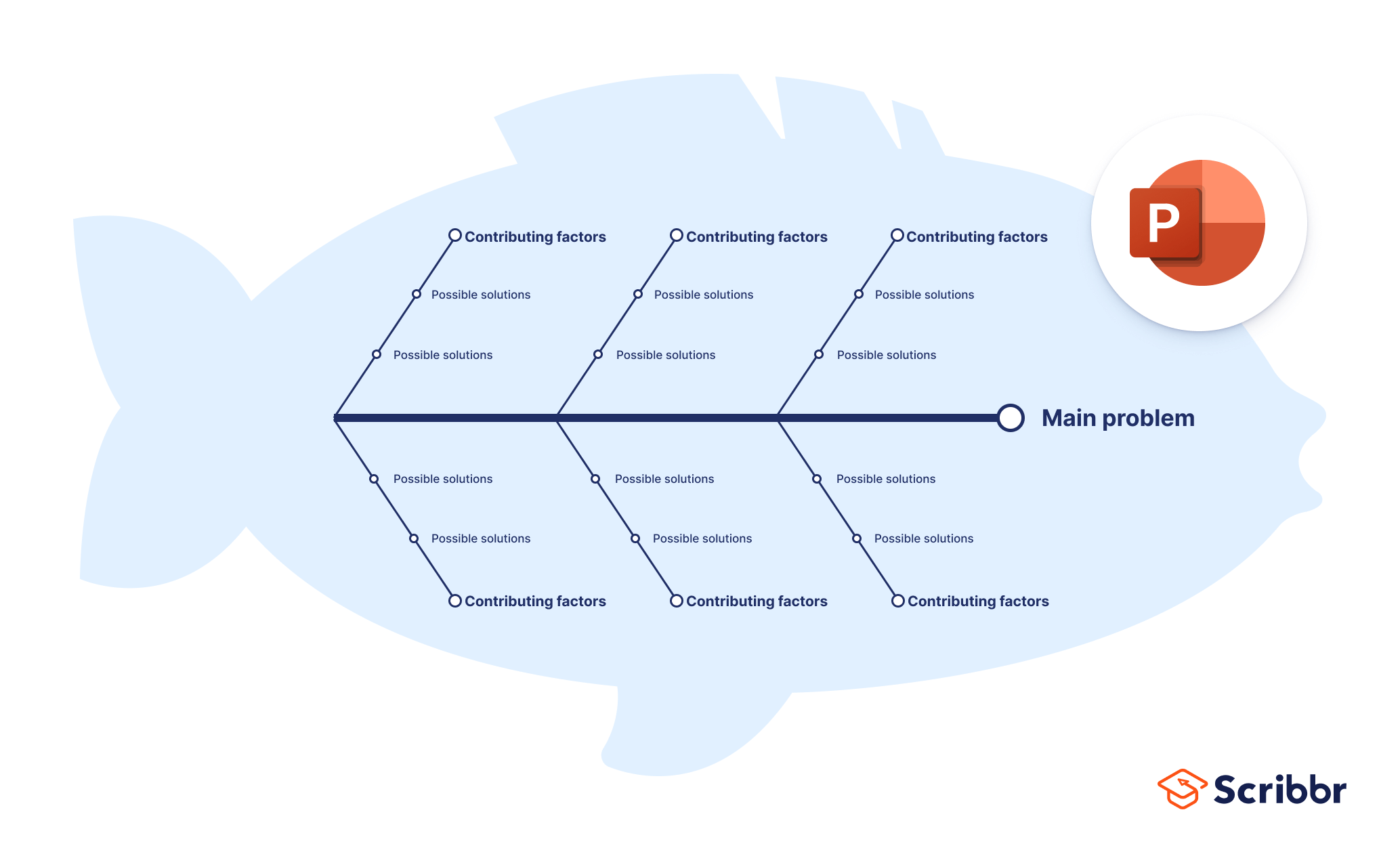
Fishbone diagrams are used in a variety of settings, both academic and professional. They are particularly popular in healthcare settings, particularly nursing, or in group brainstorm study sessions. In the business world, they are an often-used tool for quality assurance or human resources professionals.
Fishbone diagram example #1: Climate change
Let’s start with an everyday example: what are the main causes of climate change?
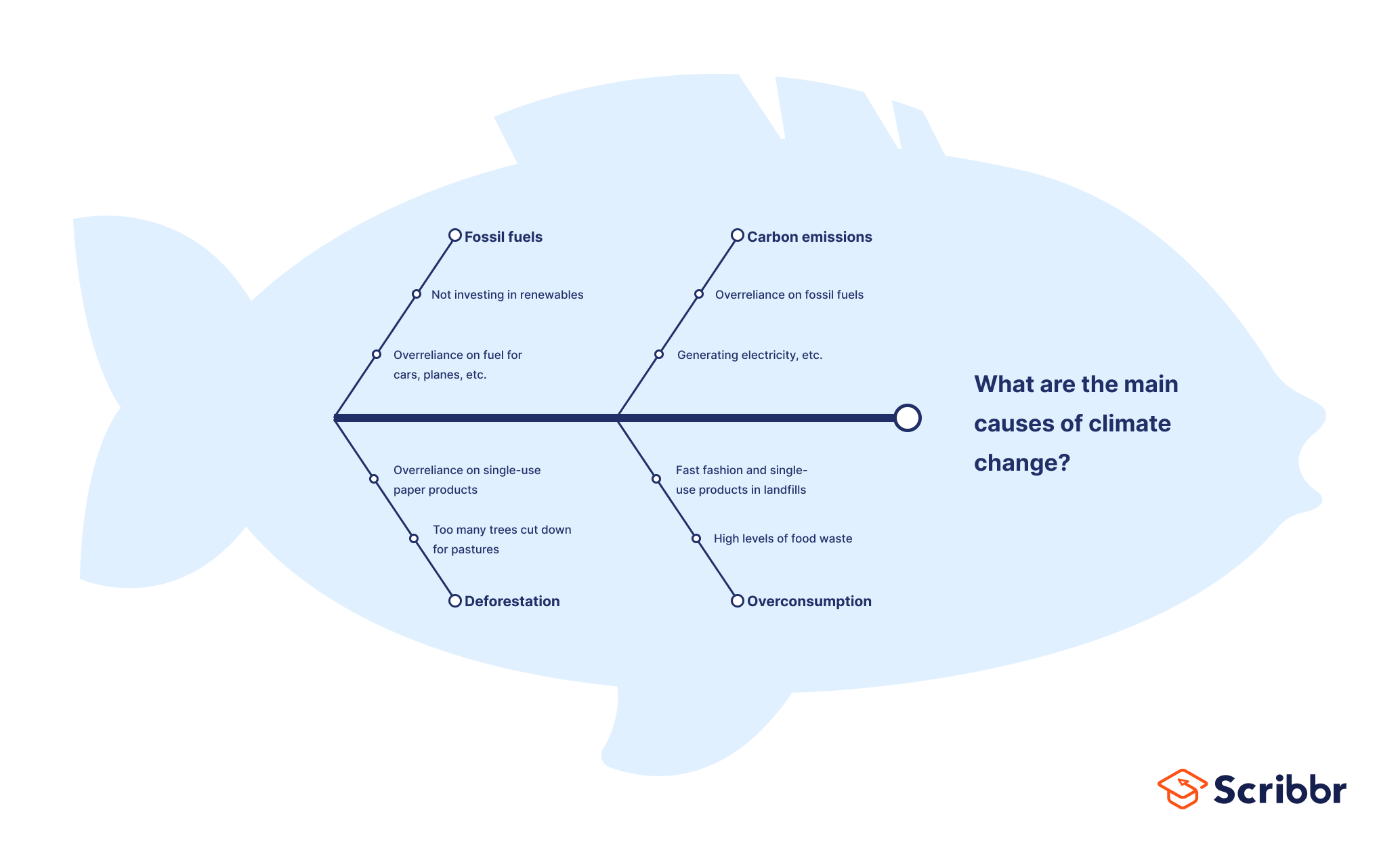
Fishbone diagram example #2: Healthcare and nursing
Fishbone diagrams are often used in nursing and healthcare to diagnose patients with unclear symptoms, or to streamline processes or fix ongoing problems. For example: why have surveys shown a decrease in patient satisfaction?

Fishbone diagram example #3: Quality assurance
QA professionals also use fishbone diagrams to troubleshoot usability issues, such as: why is the website down?
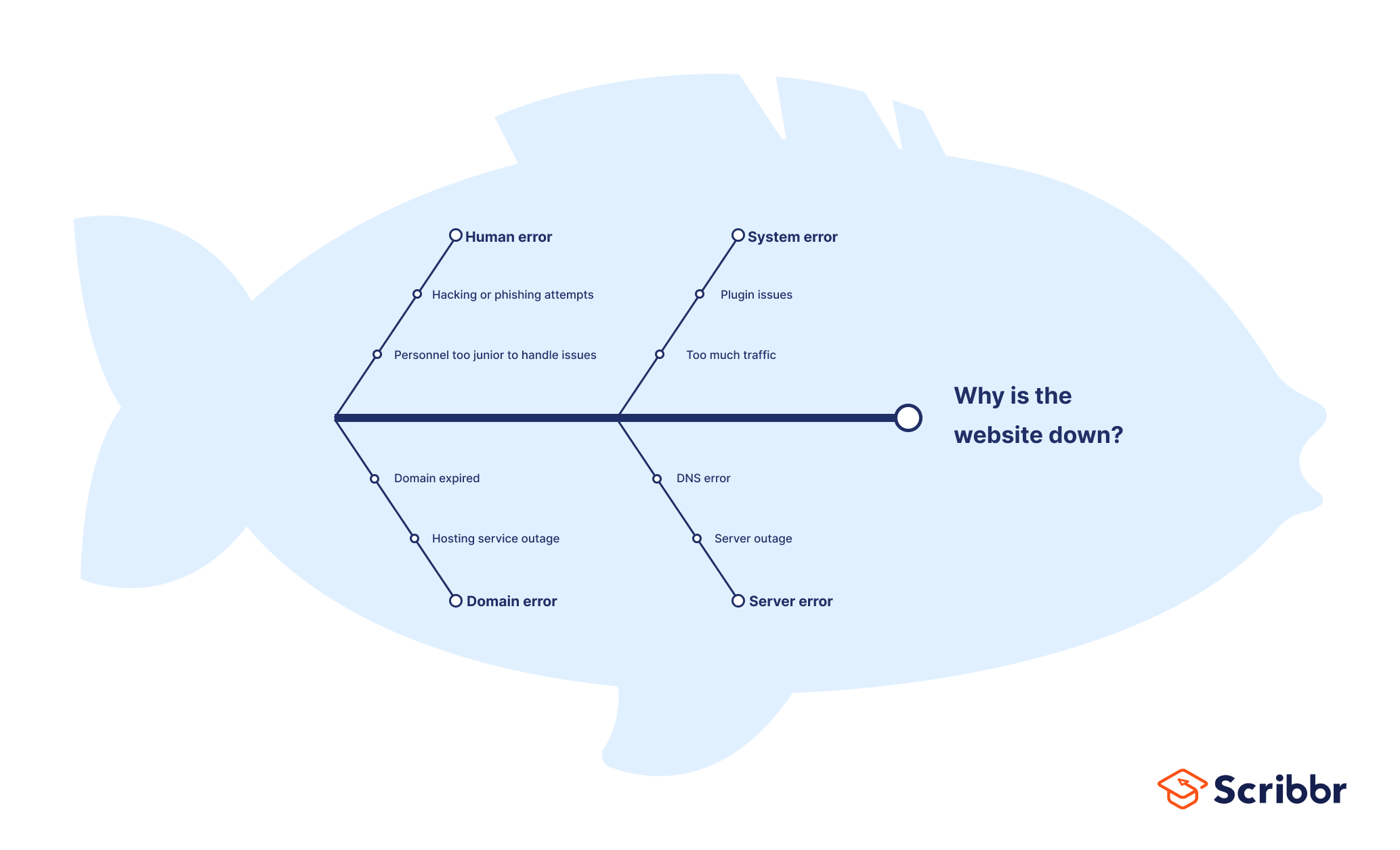
Fishbone diagram example #4: HR
Lastly, an HR example: why are employees leaving the company?
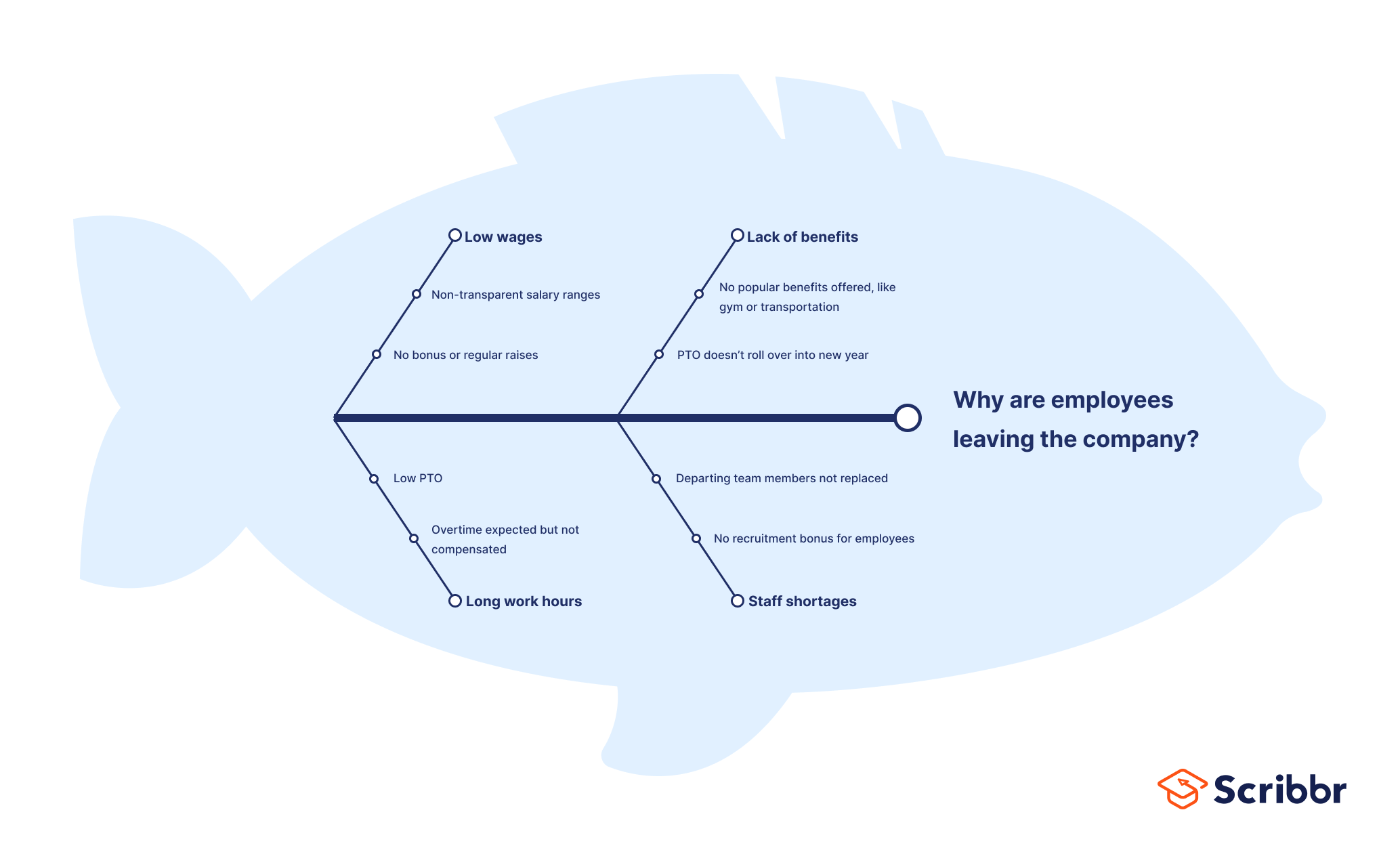
Fishbone diagrams come with advantages and disadvantages.
- Great tool for brainstorming and mind-mapping, either individually or in a group project.
- Can help identify causal relationships and clarify relationships between variables .
- Constant iteration of “why” questions really drills down to root problems and elegantly simplifies even complex issues.
Disadvantages
- Can lead to incorrect or inconsistent conclusions if the wrong assumptions are made about root causes or the wrong variables are prioritized.
- Fishbone diagrams are best suited to short phrases or simple ideas—they can get cluttered and confusing easily.
- Best used in the exploratory research phase, since they cannot provide true answers, only suggestions.
Here's why students love Scribbr's proofreading services
Discover proofreading & editing
If you want to know more about the research process , methodology , research bias , or statistics , make sure to check out some of our other articles with explanations and examples.
Methodology
- Sampling methods
- Simple random sampling
- Stratified sampling
- Cluster sampling
- Likert scales
- Reproducibility
Statistics
- Null hypothesis
- Statistical power
- Probability distribution
- Effect size
- Poisson distribution
Research bias
- Optimism bias
- Cognitive bias
- Implicit bias
- Hawthorne effect
- Anchoring bias
- Explicit bias
Fishbone diagrams have a few different names that are used interchangeably, including herringbone diagram, cause-and-effect diagram, and Ishikawa diagram.
These are all ways to refer to the same thing– a problem-solving approach that uses a fish-shaped diagram to model possible root causes of problems and troubleshoot solutions.
Fishbone diagrams (also called herringbone diagrams, cause-and-effect diagrams, and Ishikawa diagrams) are most popular in fields of quality management. They are also commonly used in nursing and healthcare, or as a brainstorming technique for students.
Cite this Scribbr article
If you want to cite this source, you can copy and paste the citation or click the “Cite this Scribbr article” button to automatically add the citation to our free Citation Generator.
George, T. (2024, January 29). What Is a Fishbone Diagram? | Templates & Examples. Scribbr. Retrieved April 2, 2024, from https://www.scribbr.com/research-process/fishbone-diagram/
Is this article helpful?
Tegan George
Other students also liked, how to define a research problem | ideas & examples, data collection | definition, methods & examples, exploratory research | definition, guide, & examples, what is your plagiarism score.
By using this site you agree to our use of cookies. Please refer to our privacy policy for more information. Close

7 Powerful Problem-Solving Root Cause Analysis Tools
The first step to solving a problem is to define the problem precisely. It is the heart of problem-solving.
Root cause analysis is the second important element of problem-solving in quality management. The reason is if you don't know what the problem is, you can never solve the exact problem that is hurting the quality.
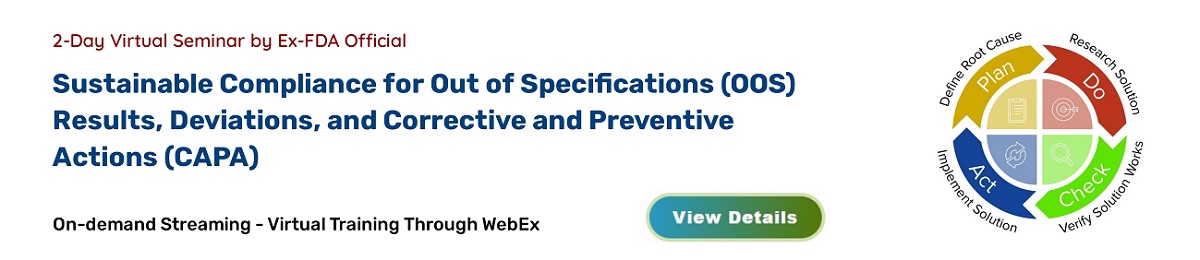
Manufacturers have a variety of problem-solving tools at hand. However, they need to know when to use which tool in a manner that is appropriate for the situation. In this article, we discuss 7 tools including:
- The Ishikawa Fishbone Diagram (IFD)
- Pareto Chart
- Failure Mode and Effects Analysis (FMEA)
- Scatter Diagram
- Affinity Diagram
- Fault Tree Analysis (FTA)
1. The Ishikawa Fishbone Diagram IFD
The model introduced by Ishikawa (also known as the fishbone diagram) is considered one of the most robust methods for conducting root cause analysis. This model uses the assessment of the 6Ms as a methodology for identifying the true or most probable root cause to determine corrective and preventive actions. The 6Ms include:
- Measurement,
- Mother Nature- i.e., Environment
Related Training: Fishbone Diagramming
2. Pareto Chart
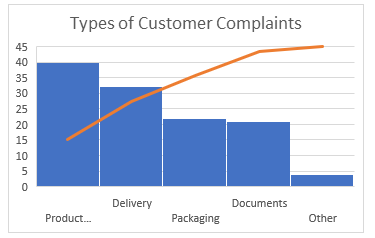
The Pareto Chart is a series of bars whose heights reflect the frequency or impact of problems. On the Chart, bars are arranged in descending order of height from left to right, which means the categories represented by the tall bars on the left are relatively more frequent than those on the right.
Related Training: EFFECTIVE INVESTIGATIONS AND CORRECTIVE ACTIONS (CAPA) Establishing and resolving the root causes of deviations, problems and failures
This model uses the 5 Why by asking why 5 times to find the root cause of the problem. It generally takes five iterations of the questioning process to arrive at the root cause of the problem and that's why this model got its name as 5 Whys. But it is perfectly fine for a facilitator to ask less or more questions depending on the needs.
Related training: Accident/Incident Investigation and Root Cause Analysis
4. Failure Mode and Effects Analysis (FMEA)
FMEA is a technique used to identify process and product problems before they occur. It focuses on how and when a system will fail, not if it will fail. In this model, each failure mode is assessed for:
- Severity (S)
- Occurrence (O)
- Detection (D)
A combination of the three scores produces a risk priority number (RPN). The RPN is then provided a ranking system to prioritize which problem must gain more attention first.
Related Training: Failure Mode Effects Analysis
5. Scatter Diagram
A scatter diagram also known as a scatter plot is a graph in which the values of two variables are plotted along two axes, the pattern of the resulting points revealing any correlation present.
To use scatter plots in root cause analysis, an independent variable or suspected cause is plotted on the x-axis and the dependent variable (the effect) is plotted on the y-axis. If the pattern reflects a clear curve or line, it means they are correlated. If required, more sophisticated correlation analyses can be continued.
Related Training: Excel Charting Basics - Produce Professional-Looking Excel Charts
6. Affinity Diagram
Also known as KJ Diagram, this model is used to represent the structure of big and complex factors that impact a problem or a situation. It divides these factors into small classifications according to their similarity to assist in identifying the major causes of the problem.
7. Fault Tree Analysis (FTA)
The Fault Tree Analysis uses Boolean logic to arrive at the cause of a problem. It begins with a defined problem and works backward to identify what factors contributed to the problem using a graphical representation called the Fault Tree. It takes a top-down approach starting with the problem and evaluating the factors that caused the problem.
Finding the root cause isn't an easy because there is not always one root cause. You may have to repeat your experiment several times to arrive at it to eliminate the encountered problem. Using a scientific approach to solving problem works. So, its important to learn the several problem-solving tools and techniques at your fingertips so you can use the ones appropriate for different situations.
ComplianceOnline Trainings on Root Cause Analysis
P&PC, SPC/6Sigma, Failure Investigation, Root Cause Analysis, PDCA, DMAIC, A3 This webinar will define what are the US FDA's expectation for Production and Process Control / Product Realization, the use of statistical tehniques, 6 sigma, SPC, for establishing, controlling , and verifying the acceptability of process capability and product characteristics, product acceptance or validation and other studies. Non-conformance, OOS, deviations Failure Investigations, and Root Cause Analysis, PDCA, DMAIC, and similar project drivers to improvement, A# and similar dash boards.
Accident/Incident Investigation and Root Cause Analysis If a major workplace injury or illness occurred, what would you do? How would you properly investigate it? What could be done to prevent it from happening again? A properly executed accident/incident investigation drives to the root causes of the workplace accident to prevent a repeat occurrence. A good accident/incident investigation process includes identifying the investigation team, establishing/reviewing written procedures, identifying root causes and tracking of all safety hazards found to completion.
Root Cause Analysis - The Heart of Corrective Action This presentation will explain the importance of root cause analysis and how it fits into an effective corrective and preventive action system. It will cover where else in your quality management system root cause analysis can be used and will give examples of some of the techniques for doing an effective root cause analysis. Attendees will learn how root cause analysis can be used in process control.
Addressing Non-Conformances using Root Cause Analysis (RCA) RCA assumes that systems and events are interrelated. An action in one area triggers an action in another, and another, and so on. By tracing back these actions, you can discover where the issue started and how it grew into the problem you're now facing.
Introduction to Root Cause Investigation for CAPA If you have reoccurring problems showing up in your quality systems, your CAPA system is not effective and you have not performed an in-depth root cause analysis to be able to detect through proper problem solving tools and quality data sources, the true root cause of your problem. Unless you can get to the true root cause of a failure, nonconformity, defect or other undesirable situation, your CAPA system will not be successful.
Root Cause Analysis and CAPA Controls for a Compliant Quality System In this CAPA webinar, learn various regulations governing Corrective and Preventive Actions (CAPA) and how organization should collect information, analyze information, identify, investigate product and quality problems, and take appropriate and effective corrective and/or preventive action to prevent their recurrence.
Root Cause Analysis for CAPA Management (Shutting Down the Alligator Farm) Emphasis will be placed on realizing system interactions and cultural environment that often lies at the root of the problem and prevents true root cause analysis. This webinar will benefit any organization that wants to improve the effectiveness of their CAPA and failure investigation processes.
Root Cause Analysis for Corrective and Preventive Action (CAPA) The Quality Systems Regulation (21 CFR 820) and the Quality Management Standard for Medical Devices (ISO 13485:2003), require medical device companies to establish and maintain procedures for implementing corrective and preventive action (CAPA) as an integral part of the quality system.
Strategies for an Effective Root Cause Analysis and CAPA Program This webinar will provide valuable assistance to all regulated companies, a CAPA program is a requirement across the Medical Device, Diagnostic, Pharmaceutical, and Biologics fields. This session will discuss the importance, requirements, and elements of a root cause-based CAPA program, as well as detailing the most effective ways to determine root cause and describing the uses of CAPA data.
Legal Disclaimer
This piece of content and any of its enclosures, attachments or appendices, references are created to provide solely for information purpose. ComplianceOnline has made all effort to provide accurate information concerning the subject matter covered. This content is created from interpretation, and understanding of relevant and applicable information and it is not all inclusive. It can be best used in conjunction with your professional judgment and discretion.
However, this piece of content and any other ancillary items disseminated in connection with same are not necessarily prepared by a person licensed to practice law in a particular jurisdiction. This piece of content is not a substitute for the advice of an attorney. If you require legal or other expert advice, you should seek the services of a competent attorney or other professional.
ComplianceOnline necessarily is not, cannot and will not be liable for any claims, damages, or regulatory legal proceedings initiated as a consequence of you using whole or any part of the content present in this document. If any action, claim for damages, or regulatory proceedings is commenced against ComplianceOnline as a consequence of your use of this document, then and in that event, you agree to indemnify ComplianceOnline for such claims, and for any attorney's fees expended by ComplianceOnline in connection with defense of same.

- Guide: Fishbone Diagram
Daniel Croft
Daniel Croft is an experienced continuous improvement manager with a Lean Six Sigma Black Belt and a Bachelor's degree in Business Management. With more than ten years of experience applying his skills across various industries, Daniel specializes in optimizing processes and improving efficiency. His approach combines practical experience with a deep understanding of business fundamentals to drive meaningful change.
- Last Updated: October 19, 2023
- Learn Lean Sigma
The Fishbone Diagram, also known by various other names such as Ishikawa Diagram, Cause and Effect Diagram or 6Ms, is a visual tool used in problem-solving and root cause analysis . Originating from the quality management sector, it is used as a systematic approach to identify, explore, and display possible causes of a specific problem.
Table of Contents
What is a fishbone diagram.
The Fishbone Diagram is a graphical tool used for identifying and organizing possible causes of a specific problem or outcome. The diagram resembles the skeletal structure of a fish, hence its name. At the “head” of the fish is the problem you’re trying to solve, and the “bones” branching off the spine are the multiple potential causes contributing to that problem.
The benefit of a Fishbone Diagram lies in its simplicity. It gives you a structured way to brainstorm and categorize the various factors affecting a specific issue. The diagram can get as detailed as you need it to be, allowing for sub-causes to branch off the main causes, offering even deeper insights.
The Components of a Fishbone Diagram
Head : The fish’s head represents the problem or effect you’re analyzing.
Spine : The long, horizontal line connecting to the head serves as the timeline or sequence of the problem.
Bones : These are the categories of potential causes. They branch off the spine, leading towards the head.
Sub-Bones : These are the more specific factors or sub-causes that stem from the main categories.
Why Use a Fishbone Diagram?
The Fishbone Diagram is a flexible tool that can be used for a range of applications. Here’s why it’s so useful:
1. Easy Visualization:
One of the primary advantages of using a Fishbone Diagram is its ability to simplify complex problems. With all potential causes visually represented in one place, it becomes easier to analyze and discuss the issues.
2. Team Collaboration:
The Fishbone Diagram is excellent for brainstorming sessions. It encourages team members to think critically and contributes to a shared understanding of the problem. It’s collaborative by design, allowing for the collective intelligence of the group to shine.
3. Root Cause Analysis:
Identifying symptoms of a problem is one thing; uncovering the root cause is another. The Fishbone Diagram excels at this by forcing you to dig deep into various contributing factors. By isolating these causes, you’re better positioned to find a lasting solution.
By using a Fishbone Diagram, you’re not just addressing a problem with a short-term fix; you’re conducting a thorough investigation to eliminate issues from the root up.
How to Create a Fishbone Diagram: A Detailed Guide
Creating a Fishbone Diagram might seem like a daunting task, but it’s actually a straightforward process. Here, we’ll break down each step in detail to ensure you can construct a Fishbone Diagram that serves its purpose effectively.
Materials You’ll Need:
- A whiteboard or large sheet of paper
- Markers or pens
- Sticky notes (optional)
- A team of people for brainstorming
Step 1: Identify the Problem
The first and most crucial step is to clearly identify the problem you’re trying to solve. This statement should be specific and concise. Write this problem statement at the far right side of your whiteboard or paper, as it will serve as the “head” of your fishbone diagram.
- Use data to define the problem whenever possible.
- Make sure the problem is mutually understood and agreed upon by all team members.
Step 2: Determine the Main Categories
Now, draw a horizontal line from the problem statement towards the left side of the board. This is the “spine” of your fish. Next, you’ll identify the major categories of causes that could be contributing to the problem. These categories will serve as the main “bones” branching off from the spine.
Common categories often include:
- Measurement
- Environment
- The categories can be industry-specific or general, depending on the problem you’re analyzing.
- Aim for 4-6 main categories for better manageability.
Step 3: Brainstorm Causes
Once you’ve determined the main categories, it’s time to brainstorm potential causes for each category. These causes will be the smaller “bones” that branch off from the main bones. If you’re working with a team, this is an excellent time for a brainstorming session.
- Use sticky notes to write down ideas so you can easily move them around.
- Encourage every team member to contribute; sometimes the most unexpected insights come from diverse perspectives.
The output of the root cause analysis at this point may look something like the below example. With the lack of preventative maintenance being explored with the 5Whys analysis.
Step 4: Dig Deeper with Sub-Causes
Sometimes, the primary causes can be broken down into smaller, more specific sub-causes. This is where the “ 5 Whys ” technique can be beneficial. For each primary cause, ask “Why?” up to five times to dig deeper into the root of the issue.
- Not all primary causes will need sub-causes; use your discretion.
- Keep the diagram organized to ensure readability.
Step 5: Analyze and Take Action
After all the causes and sub-causes have been identified, it’s time to analyze the Fishbone Diagram as a team. Highlight or circle the causes that seem most likely to be contributing to the problem. These are the areas that will need immediate attention and action.
- Use data or evidence to support your conclusions.
- Create an action plan assigning responsibility for each highlighted cause.
And there you have it! You’ve successfully created a Fishbone Diagram that will help you get to the root of your problem.
Examples and Case Studies: Understanding Fishbone Diagrams in Action
Case study: manufacturing unit with quality issues.
Imagine you run a manufacturing unit, and you’ve been receiving complaints about the quality of your products. You decide to use a Fishbone Diagram to get to the root of the issue.
Step 1: Identify the Problem Problem Statement: “High number of defective products in the last quarter.”
Step 2: main categories.
- People : Untrained staff, high employee turnover
- Process : Inconsistent quality checks, outdated SOPs (Standard Operating Procedures)
- Equipment : Aged machinery, lack of maintenance
- Environment : Poor lighting, extreme temperature fluctuations
Step 4: Dig Deeper (5 Whys)
- Untrained Staff : Why? No formal training program.
- Aged Machinery : Why? No budget allocated for equipment upgrades.
After analyzing the Fishbone Diagram, you realize that untrained staff and aged machinery are your primary culprits. Your next steps could involve investing in staff training programs and allocating budget for machinery upgrades.
By following these steps, you can develop targeted strategies to improve product quality significantly.
Common Mistakes and Tips: How to Make the Most of Your Fishbone Diagram
1. overlooking minor causes.
While it’s easy to focus on the most glaring issues, minor causes can accumulate and have a significant impact.
Tip : Don’t disregard a cause just because it seems minor. Sometimes, fixing smaller issues can lead to big improvements.
2. Ignoring Data
It’s tempting to rely solely on brainstorming and intuition, but data should be your guiding star.
Tip : Use metrics and KPIs to support or refute the causes you’ve identified. This adds credibility to your findings and helps you prioritize effectively.
3. Stopping at Symptoms
Identifying symptoms is just the first step; your ultimate goal should be to uncover the root causes.
Tip : Use techniques like the “5 Whys” to dig deeper into each cause and ensure you’re addressing the root of the issue, not just its manifestations.
Fishbone Diagrams are a fantastic asset in the toolbox of anyone interested in continuous improvement. Whether you’re a seasoned professional or just getting started, this simple yet powerful tool can help you dissect complex problems and develop targeted solutions.
They encourage you to look beyond the obvious and delve into the intricacies that contribute to each problem. So go ahead, grab that pen and paper (or a whiteboard, if you’re feeling fancy), and start your journey towards effective problem-solving.
- Ilie, G. and Ciocoiu, C.N., 2010. Application of fishbone diagram to determine the risk of an event with multiple causes. Management research and practice , 2 (1), pp.1-20.
- Coccia, M., 2018. The Fishbone diagram to identify, systematize and analyze the sources of general purpose Technologies. Journal of Social and Administrative Sciences , 4 (4), pp.291-303.
Q: What is the origin of the Fishbone Diagram?
A: The Fishbone Diagram was originally developed by Dr. Kaoru Ishikawa, a Japanese quality control statistician, in the 1960s. It’s also sometimes referred to as the Ishikawa Diagram in his honor.
Q: Can Fishbone Diagrams be used for non-manufacturing problems?
A: Absolutely! While Fishbone Diagrams are popular in manufacturing and quality management, their application is not limited to these areas. They can be used in healthcare, software development, event planning, and even for personal problem-solving.
Q: How many main categories should my Fishbone Diagram have?
A: The number of main categories can vary depending on the complexity of the problem. However, it’s generally advisable to have between 4-6 main categories for easier analysis and readability.
Q: Can I use software to create a Fishbone Diagram?
A: Yes, there are several software tools available for creating Fishbone Diagrams, such as Microsoft Visio, Lucidchart, and various other project management software options. However, a simple pen and paper or a whiteboard can be just as effective for smaller teams or simpler problems.
Q: How do I know which causes to prioritize after creating a Fishbone Diagram?
A: After creating your Fishbone Diagram, you should analyze it with your team to identify the most likely root causes of the problem. Using data to support your conclusions can be very helpful. You may also employ techniques like the Pareto Analysis to prioritize causes based on their impact.
Daniel Croft is a seasoned continuous improvement manager with a Black Belt in Lean Six Sigma. With over 10 years of real-world application experience across diverse sectors, Daniel has a passion for optimizing processes and fostering a culture of efficiency. He's not just a practitioner but also an avid learner, constantly seeking to expand his knowledge. Outside of his professional life, Daniel has a keen Investing, statistics and knowledge-sharing, which led him to create the website learnleansigma.com, a platform dedicated to Lean Six Sigma and process improvement insights.
Free Lean Six Sigma Templates
Improve your Lean Six Sigma projects with our free templates. They're designed to make implementation and management easier, helping you achieve better results.
Other Guides
5 Root Cause Analysis Tools for More Effective Problem-Solving
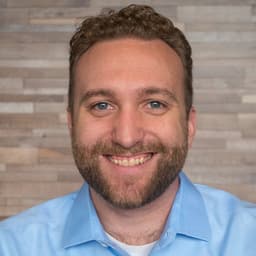
Next to defining a problem accurately, root cause analysis is one of the most important elements of problem-solving in quality management. That’s because if you’re not aiming at the right target, you’ll never be able to eliminate the real problem that’s hurting quality.
So which type of root cause analysis tool is the best one to use? Manufacturers have a range of methods at their fingertips, each of which is appropriate for different situations. Below we discuss five common root cause analysis tools, including:
- Pareto Chart
- Fishbone Diagram
- Scatter Diagram
- Failure Mode and Effects Analysis (FMEA)
Download our free Root Cause Analysis 101 Guidebook
1. pareto chart.
A Pareto chart is a histogram or bar chart combined with a line graph that groups the frequency or cost of different problems to show their relative significance. The bars show frequency in descending order, while the line shows cumulative percentage or total as you move from left to right.

The Pareto chart example above is a report from layered process audit software that groups together the top seven categories of failed audit questions for a given facility. Layered process audits (LPAs) allow you to check high-risk processes daily to verify conformance to standards. LPAs identify process variations that cause defects, making Pareto charts a powerful reporting tool for analyzing LPA findings.
Pareto charts are one of the seven basic tools of quality described by quality pioneer Joseph Juran. Pareto charts are based on Pareto’s law, also called the 80/20 rule, which says that 20% of inputs drive 80% of results.
Learn how to create Pareto charts in this post or download the Pareto Chart Tip Sheet and Sample Excel File
The 5 Whys is a method that uses a series of questions to drill down into successive layers of a problem. The basic idea is that each time you ask why, the answer becomes the basis of the next why. It’s a simple tool useful for problems where you don’t need advanced statistics, so you don’t necessarily want to use it for complex problems.
One application of this technique is to more deeply analyze the results of a Pareto analysis. Here’s an example of how to use the 5 Whys:
Problem: Final assembly time exceeds target
- Why is downtime in final assembly higher than our goal? According to the Pareto chart, the biggest factor is operators needing to constantly adjust Machine A
- Why do operators need to constantly adjust Machine A? Because it keeps having alignment problems
- Why does Machine A keep having alignment problems? Because the seals are worn
- Why are Machine A’s seals worn? Because they aren’t being replaced as part of our preventive maintenance program
- Why aren’t they being replaced as part of our preventive maintenance program? Because seal replacement wasn’t captured in the needs assessment
Of course, it may take asking why more than five times to solve the problem—the point is to peel away surface-level issues to get to the root cause.
Learn more about the 5 Whys method in this blog post or download our free 5 Whys worksheet
3. Fishbone Diagram
A fishbone diagram sorts possible causes into various categories that branch off from the original problem. Also called a cause-and-effect or Ishakawa diagram, a fishbone diagram may have multiple sub-causes branching off of each identified category.

Learn more about how to use a fishbone diagram in this blog post and download our free set of fishbone diagram templates
4. Scatter Plot Diagram
A scatter plot or scatter diagram uses pairs of data points to help uncover relationships between variables. A scatter plot is a quantitative method for determining whether two variables are correlated, such as testing potential causes identified in your fishbone diagram.
Making a scatter diagram is as simple as plotting your independent variable (or suspected cause) on the x-axis, and your dependent variable (the effect) on the y-axis. If the pattern shows a clear line or curve, you know the variables are correlated and you can proceed to regression or correlation analysis.
Download a free tip sheet to start creating your own scatter diagrams today!
5. Failure Mode and Effects Analysis (FMEA)
Failure mode and effects analysis (FMEA) is a method used during product or process design to explore potential defects or failures. An FMEA chart outlines:
- Potential failures, consequences and causes
- Current controls to prevent each type of failure
- Severity (S), occurrence (O) and detection (D) ratings that allow you to calculate a risk priority number (RPN) for determining further action
When applied to process analysis, this method is called process failure mode and effects analysis (PFMEA). Many manufacturers use PFMEA findings to inform questions for process audits , using this problem-solving tool to reduce risk at the source.
No matter which tool you use, root cause analysis is just the beginning of the problem-solving process. Once you know the cause, the next step is implementing a solution and conducting regular checks to ensure you’re holding the gain and achieving sustainable continuous improvement.
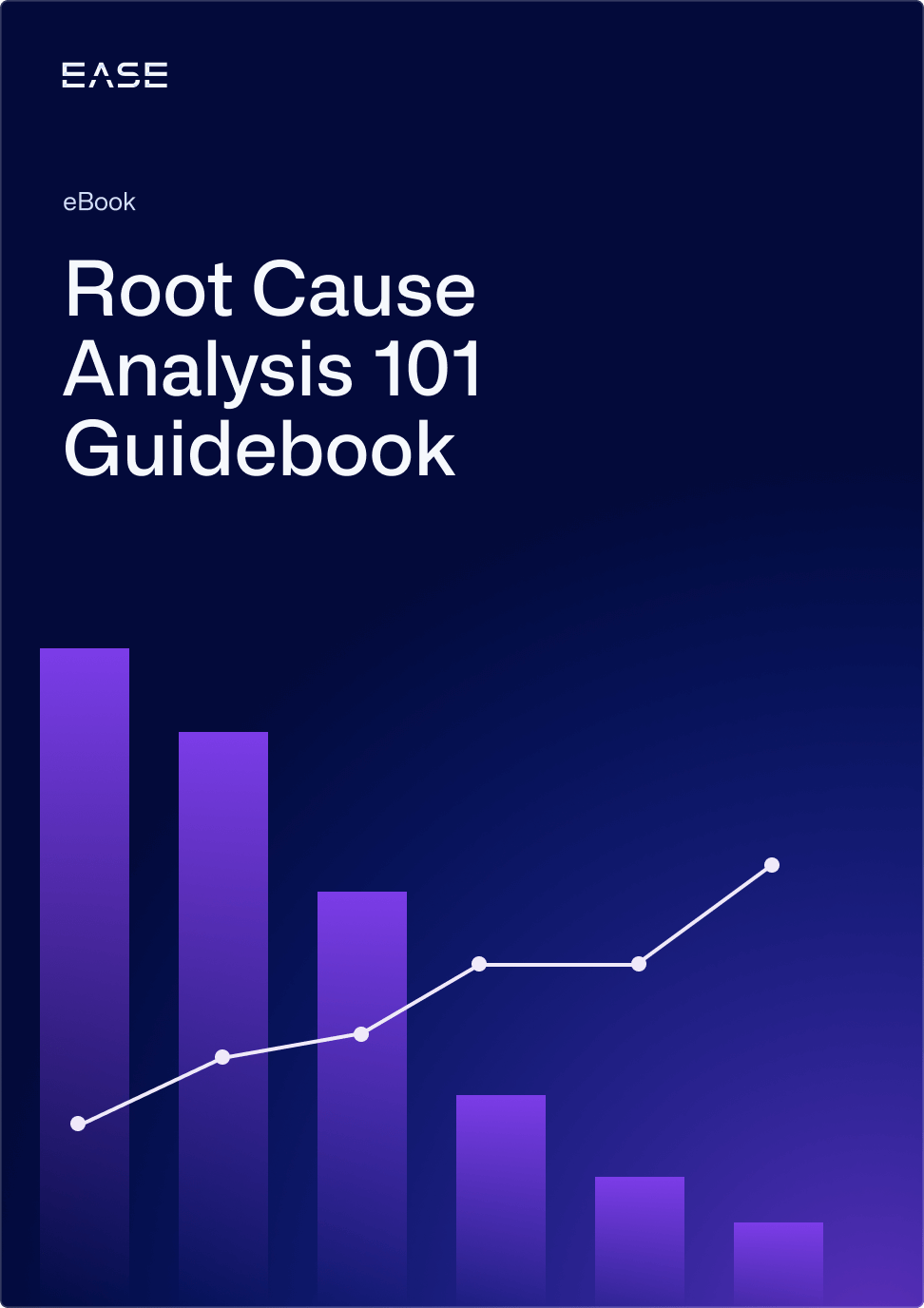
Related articles

The Fishbone Analysis Tool (Ishikawa Diagram): A Simple Intro
The fishbone analysis tool is a visual method used to help capture and understand various things including the root causes to a problem. Completed diagrams look like a fish skeleton. Summary by The World of Work Project
Fishbone Analysis
Fishbone analysis diagrams are also known as Ishikawa diagrams. They are a visual tool that helps individuals and teams captured and understand the root causes to a specific problem.

The problem statement that is being considered is captured in the fish’s head. The specific root-causes that contribute to the problem are captured along the fish’s fins (or rib bones). The major causes of the problem are captured at the ends of the fins.
This approach produces comprehensive visualizations of problems which help with the solution process. When designing solutions, it’s important to ensure that any proposed solution addresses the major root causes that have been identified.
Using it in Practice
Fishbone analysis is often part of a more comprehensive approach to team problem solving and is often combined with silent brainstorming .

The standard approach that we would use around a fishbone analysis forms part of a facilitated team problem solving approach, using the A3 Thinking method . This is normally completed using post-it notes initially, and is only captured in fishbone diagram at a later stage. The process is as follows:
- Firstly, have a team silently brainstorm the root causes of a chosen problem statement using the 5 whys approach to ensure depth.
- Secondly, have the team group their individual root causes into themes.
- Thirdly, have the team review the grouped thematic areas and, if happy with them, name them. These names then become the major-causes to the identified problem.
- Fourthly, review the root-causes and major causes, checking them for completeness against an appropriate list of potential major-causes.
- Finally, progress to the solution design phase.
Major-causes: 3 Common Groups
It’s important to understand the common major-causes which can affect a specific type of problem. With these in mind it’s possible to check the completeness of the root-causes you’ve identified.

For example, if you know that a common major-cause is “people capability” and you’ve identified no root-causes of this nature, you can go back and spend further time identifying appropriate root-causes to your problem.
By doing this you can ensure that you’ve identified all of the appropriate root causes, and are thus in a position to identify a better solution to your problem.
Below, we consider three groups of major-causes that you may wish to use to check your root-causes for completeness. Each group is useful in different circumstances. More groups are available, and you can always create your own group which is appropriate for your specific circumstances.
The PPPS Major-causes
PPPC stands for people, process, platform and culture. These are an excellent set of common major-causes to consider for any problem in an office or a professional-services working environment. Most problems in this environment have root causes within all four of these major-causes.
The 5 Ms Major-causes
The 5 Ms are: machine, method, material, man and measurement. These major causes are useful for consideration in the manufacturing sector where you would expect to potentially find root-causes in relation to all of them.

The 5 Ps Major-causes
The 5 Ps are: product, price, promotion, place, people. These are simply the 5 Ps of marketing (which we’ve yet to write about), converted into potential major-causes. These are appropriate major-causes to consider in relation to a product marketing problem.
Want to be a better manager?
Every year we run an open cohort of our Connected Management programme for those working in small organisations or organisations that are not able to fund personal and professional development. The 10 session programme is £1100 per person with discounts of up to 40% for self-funders and non-profits.
In 2024, we have a cohort on Wednesday 3.30pm UK time and Thursdays 9am UK time from April 17/18. It comprises 10 online live workshops with two great facilitators and access to a bank of support materials. Learn more about the programme by clicking below.
Learning More
Thinking about what we do from different perspectives and with others is very helpful for decision making. Tools like the reframing matrix process or hackathons can help us do this.
Part of the reason we’re not great at problem solving is that we all have thinking habits and cognitive biases that restrict our creativity. In particular, these decision making biases often lead us towards bad (or irrational) decisions. And sometimes we make decisions just because ISLAGIATT …
Similarly, Drilling into issues with the 5 Whys helps us understand root causes more and creating an ease/benefit matrix helps us decide what to focus on in the first place. When we are actually working on things like this in groups it’s useful to use techniques like silent brainstorming to get the best results.
To learn more about creativity, innovation and problem solving, you might enjoy the third of our three podcasts specifically on these topics. It focuses mainly on cognitive processes:
The World of Work Project View
Fishbone analysis is a helpful tool. It’s a useful way to visualize, share, track and analyze root causes to a specific problem. The approach of comparing root causes to a list of common major-causes for that kind of problem is also very helpful.
In our view though, the real magic comes from getting the right people in the room and leading an effective root-cause ideation / brainstorming activity. In many ways this is more important than how you visualize the root-causes that you capture.
Our Podcast .
Our Podcast is a great way to learn more about hundreds of fascinating topics from around the world of work.
In this instance, most of our content has come from our working experience. The original source of this model though is by Kaoru Ishikawa and you can read more in his book: “Introduction to Quality Control” .
The World of Work Project: The Fishbone Analysis Tool (Ishikawa Diagram): A Simple Intro
We’re a small organization who know we make mistakes and want to improve them. Please contact us with any feedback you have on this post. We’ll usually reply within 72 hours.
Share This Story, Choose Your Platform!
Related posts.

Predictive Analytics In The World Of Work

The Foursquare Ethical Decision Model: A Simple Summary

The ISLAGIATT Decision Making Process

The Reframing Matrix Process: A Simple Way To Improve Creativity

Bounded Rationality: A Simple Summary

Dual Process Theory: A Simple Summary
Privacy overview.

In this online seminar, we explore two key factors that shape our performance and experience at work: Trust and Social Threats. We'll explain what they are, discuss how to build trust, share the domains of social threat and share hints and tips for managing both in the workplace.
In this online seminar, we explore the thorny issue of managing the demands on our time. In many workplaces it feels like there's a potentially infinite amount of work. To succeed, we need to learn to prioritize, say no when appropriate and manage our own boundaries. This seminar will explore these challenges and share insights on how we can all improve.
In 2012 Google decided to analyse their teams to discover what makes an effective team, why some teams are so successful, and some less so. What did they discover? Amongst other things, that Psychological Safety is a key differentiator for high performing teams. In this seminar we explain what Psychological Safety is, why it matters and how to increase it in your teams.
Subscribe For Latest Updates
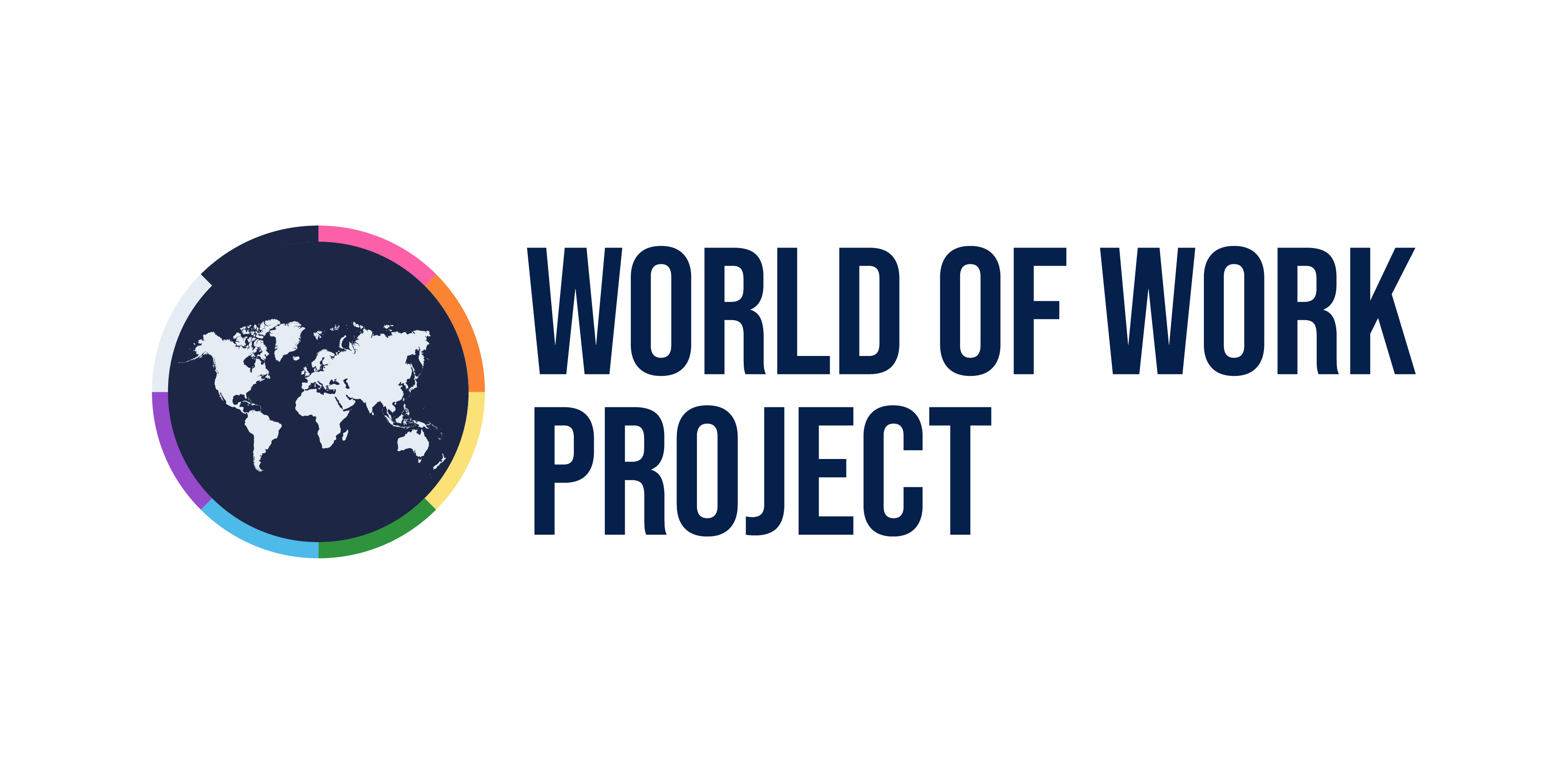
Nice to see you again :)
If you'd like to learn more about us and what we do, you can join thousands of members of the World of Work community around the globe in receiving our occasional newsletter, the WOW Mail. In it, we'll let you know what we're up to and share hints and tips.
After submitting this form, you'll receive an email asking you to confirm your registration. Click the button in that email to finalize your subscription. Your email provider might filter it into your junk folder, so please check there if you don't see it your main folder!
I agree to receive your newsletters and accept the data privacy statement.
We use Sendinblue as our marketing platform. By Clicking below to submit this form, you acknowledge that the information you provided will be transferred to Sendinblue for processing in accordance with their terms of use
The 6 Top Root Cause Analysis Tools to Identify Problems
Root cause analysis is one of the most crucial problem-solving elements in quality management. Learn everything about the analysis method and its importance to the Six Sigma methodology.
- What Is Lean Management?
- The 5 Principles of Lean
- What Is Shared Leadership?
- What Is Lean Manufacturing?
- What Is Value in Lean?
- 7 Wastes of Lean
- What Is Mura?
- What Is Muri?
- What Is 5S?
- What Is the Cost of Delay?
- What Is Value Stream Mapping?
- What Is a Pull System?
- What Is a Bottleneck?
- Just-in-Time Manufacturing
- Implementing a Kanban Pull System
- Pull System on the Portfolio Level
- What Is Kaizen?
- What Is Continuous Improvement?
- Built-In Quality Management
- What Is the Poka-Yoke Technique?
- What Is Plan-Do-Check-Act Cycle?
- 5 Whys: The Ultimate Root Cause Analysis Tool
- Gemba Walk: Where the Real Work Happens
- A3 Problem-Solving: Fight the Root Cause
- How To Perform Root Cause Analysis?
- Root Cause Analysis Tools
What Is a Pareto Chart?
What Is a Scatter Diagram?
- What Is a Fishbone Diagram?
- What Is Hoshin Kanri?
- What Is Hoshin Kanri Catchball?
- Demystifying the Hoshin Kanri X Matrix
- The Lean Transformation Model Explained
- Lean Transformation Roadmap - 8 Comprehensive Steps
- What Is Cycle Time?
- What Is Little's Law?
- What Is Takt Time?
- What Is Heijunka?
- What Is Jidoka?
- What Is Andon?
- Lean Six Sigma Principles
- Lean Six Sigma Tools
- Lean Six Sigma Implementation
- What Is Six Sigma?
- What Is DMADV?
- What Is DMAIC?
- Lean Project Management
Root cause analysis (RCA) is a process for identifying the root causes of problems and a systematic approach to responding to them. Root cause analysis is based on the idea that effective management should find a way to prevent problems before they occur and affect the work of an entire organization.
Root cause analysis is one of the most crucial problem-solving elements in quality management. Root cause analysis is an important part of Six Sigma methodology, as it is a key component of the analysis phase of DMAIC – define, measure, analyze, improve, and control.
There are six major tools of root cause analysis, which are used through the process of identifying the root causes of a problem.
- Pareto Chart
- Scatter Plot Diagram
- Fishbone Diagram
- Failure Mode and Effects Analysis (FMEA)
- Fault Tree Analysis
1. Pareto Chart
A Pareto chart is a bar chart sorted in descending order from the highest frequency to the lowest frequency from left to right. The height of the bars reflects the frequency or the impact of the problems. The Pareto chart assists the quality improvement team in focusing on areas of improvement with the greatest impact. The Pareto chart is used in Six Sigma to find out the problems, and their solutions, and root cause analysis is an important part of that process. To create a Pareto Chart , you can follow X, Y, and Z steps.
2. The 5 Whys
The 5 Whys method uses a series of questions to understand the layers of a problem. The idea is that each time you ask why, the answer you give becomes the fundamental of the next why until you find the sources of the problem. The 5 Whys is a simple tool used for problems where you don’t need any advanced data. This method is used to deeply analyze the results of a Pareto chart used in Six Sigma.
3. Scatter Plot Diagram
A scatter diagram is a two-dimensional graphical representation of a set of data. The scatter diagram graphs pair numerical data with one variable on each axis to look for their relationship. Its ability to show nonlinear relationships between variables is widely used in Six Sigma. Scatter plots are widely used as a tool for analyzing problems in Six Sigma. Scatter plots show how the variables relate to each other. This relationship is called correlation, and there are three types of correlation: positive, negative, and no correlation. In Six Sigma, a scatter plot will visually display the correlation between a problem and a cause, whether there is a positive, negative, or no correlation. This helps quality teams to evaluate which hypothetical cause has the greatest impact on a problem and which should be solved first.
4. Fishbone Diagram
A fishbone diagram , also called a cause-and-effect or Ishikawa diagram, sorts possible causes into various categories that originate from the initial problem. Moreover, a fishbone diagram may have additional multiple sub-causes derived from each identified category. The fishbone diagram is the most used cause-and-effect analysis tool in Six Sigma. The cause-and-effect analysis is one of the key tasks in any Six Sigma project.
5. Failure Mode and Effects Analysis (FMEA)
Failure mode and effects analysis (FMEA) is a method used to explore potential defects or failures during the process and product design. In Six Sigma, FMEA gives project teams a tool to predict the most likely failures that may impact the customers. The Failure Mode and Effects Analysis is implemented during the analysis phase of the Six Sigma DMAIC cycle, and it helps to estimate the significance of the impact of possible process failures.
6. Fault Tree Analysis (FTA)
Fault tree analysis (FTA) is a graphical tool and one of the more useful tools in Lean Six Sigma problem investigations. FTA explores the causes of system-level failures. Fault tree analysis prioritizes the risks in a way that allows the highest risks to be resolved first. It uses boolean logic to combine a series of lower-level events, and it is basically a top-down approach to identify the component level failures (basic events) that cause the system level failure (top events) to occur. When combined with other Lean Six Sigma tools , fault tree analysis helps the team focus on the most important input variables to the key output variables in a given process. FTA is a top-down approach to identifying the component-level failures that cause the system-level failure to occur.
How to Use the Tools in Root Cause Analysis?
Here you can see the ways to use the tools in Root Cause Analysis .
- The Fishbone diagram’s purpose is to identify the many possible causes for a problem and to sort ideas into useful categories. The fishbone diagram should be implemented when the root cause is entirely unknown.
- The Pareto chart’s purpose is to show which factors are more significant for a problem.
- The Scatter diagram’s purpose is to help you look for a relationship between two variables. It is a method of testing the correlation between the two variables. To implement this root cause analysis tool, you must plot the suspected cause on the x-axis while the effect is plotted on the y-axis.
- The 5 Whys purpose is to drill down on a particular problem by asking “Why?” until you identify the core problem. The 5 Whys is best used when implemented with a Pareto Analysis.
- Failure Mode and Effect Analysis (FMEA) aims to identify different modes in which systems can fail and analyze the consequences and effects of each failure mode. The Failure Mode and Effects Analysis can be implemented during any phase of a particular system - the planning, designing, implementation, or inspection phase, and it helps to estimate the significance of the impact of possible process failures.
- Fault tree analysis (FTA) purpose is to explore the causes of system-level failures in a top-down approach. You can implement a Fault Tree Analysis in five steps - identify the hazard, obtain an understanding of the system, create the fault tree, identify the cut sets, and lastly, mitigate the risk.
In What Steps Can Tools Be Used During a Root Cause Analysis?
Root cause analysis can be performed in six steps - define the event, find causes, find the root cause, find solutions, take action, and verify solution effectiveness. Some of the RCA tools can be implemented during the root cause analysis steps . To define the event and go to the source of the problem, you can use the 5 Whys. To find the potential causes of the event in question, you may implement Fishbone diagrams. To uncover the root cause that lies at the heart of the problem, you can use a Scatter Chart and Pareto Analysis.
Do Root Cause Analysis Tools Have Templates?
Yes, there are root cause analysis tools templates. RCA templates are used to analyze a recurring problem and help eliminate the root causes. Root cause analysis teams drill down to the root of the problem in order to implement solutions so the problem won’t appear again.
- The 5 Whys template can help ensure that business teams resolve the root cause of problems to avoid them from recurring. This 5 whys template has been designed to make it easier for you to ask and answer the question, “Why?”.
- The Fishbone Diagram template can be used to explore the potential causes of a particular issue, enabling your team to find a solution more effectively. A Fishbone Diagram template is particularly useful when relying on experience and ideas rather than quantitative data.
- The Pareto chart template is used to identify and list the problems and their causes. Then, you can score each problem individually and group them together by their cause. This is a clear, visual way to compare various factors contributing to any given problem.
- A Scatter diagram template can be used to help you find the relationship between respective factors and influences. A scatter diagram charts numerical data pairs with a variable on each axis.
What Is the Importance of the Tools of Root Cause Analysis?
Root cause analysis tools are important in determining and identifying defects and the main causes of defects. By identifying the root cause, the organization can find a permanent solution to it so that the possibility of its future re-occurrence can be reduced or eliminated. RCA plays an important role in developing a logical approach to solving problems.

How Do Tools of Root Cause Analysis Improve Work Efficiency?
The tools of root cause analysis improve work efficiency by detecting and eliminating possible or existing problems at the beginning of a process, system, or production.
Which Sectors Can Benefit from the Use of Root Cause Analysis Tools?
Root cause analysis tools have countless applications in many industries. Here you can see the list of Root Cause Analysis Sectors.
- Engineering, automotive manufacturing, and industrial process control prevent environmental releases and be utilized for failure analysis in engineering and maintenance.
- IT and data security, where root cause analysis helps individuals investigate security breaches.
- Healthcare, where root cause analysis tools are used in environmental science, the medical device industry, occupational safety, and health.
- Environmental industries, where RCA tools are used to make accident analyses in the aviation and rail industry and prevent their reoccurrence.
- The food and beverage industry should prevent food safety problems and regulatory action by identifying the causes.
We offer the most flexible software platform
for outcome-driven enterprise agility.
The main six approaches to root causes analysis are:
- Pareto Charts
- 5 Whys Analysis
- Scatter Plot Diagrams
- Fishbone Diagrams
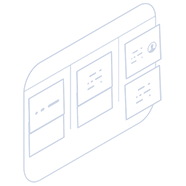
Start your free trial now and get access to all features.
During the 14-day trial period you can invite your team and test the application in a production-like enviroment.
What is a Fishbone diagram?
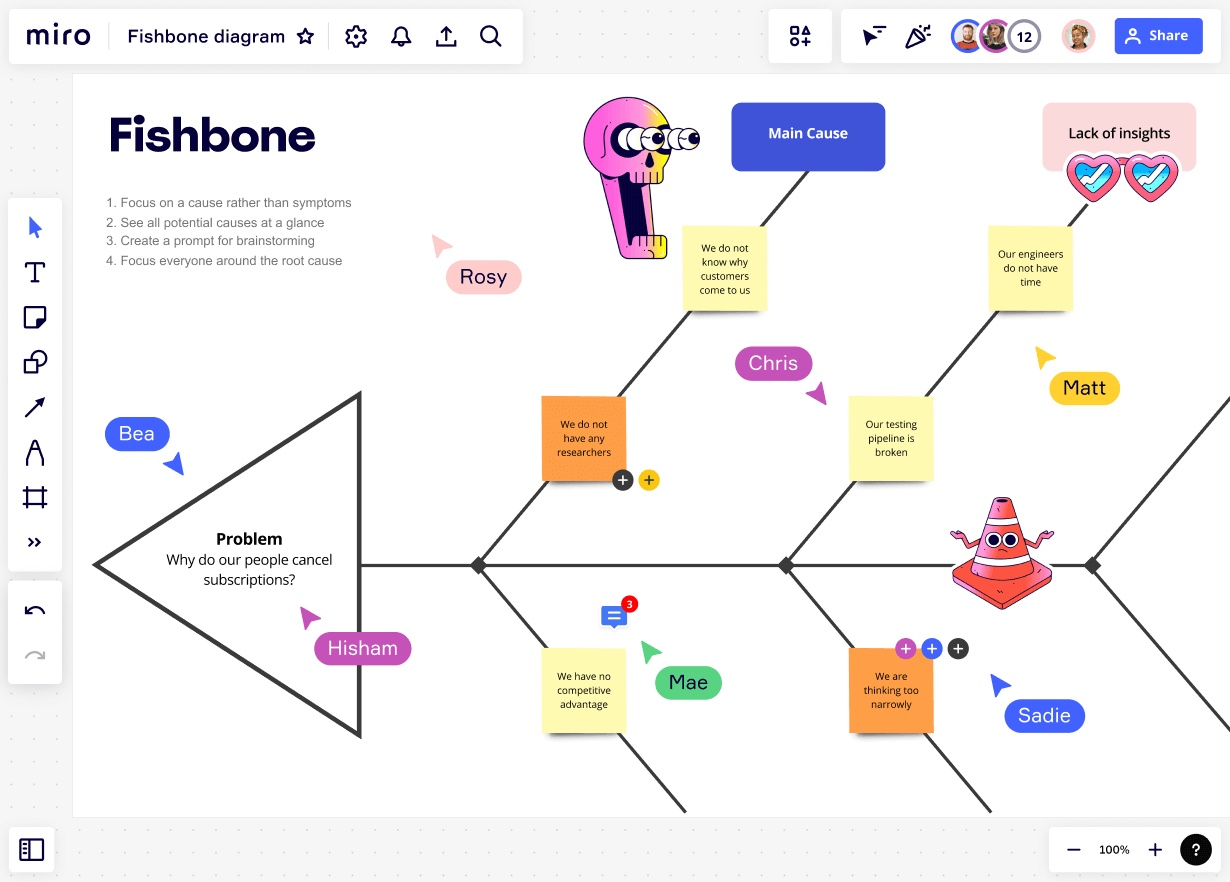
Table of Contents
Fishbone diagrams explained.
A fishbone diagram (also known as an Ishikawa fishbone diagram) is an effective problem-solving tool. Instead of focusing on a quick fix, creating a fishbone diagram helps to identify the root cause of a problem and find a long-term solution.
As a type of cause and effect diagram , the “fishbone” name comes from the diagram’s resemblance to a fish skeleton. A fishbone diagram consists of three main categories:
There’s a fish head at the head of the diagram, where you’ll outline the problem you’re trying to solve. The rest of the diagram branches out from here.
The spine stems from the head of the diagram (the problem statement), providing the outline of the fish. At the end of each spinal bone is a category that needs to be considered as part of the problem-solving process.
Branching out from each spinal bone, you’ll see a smaller rib bone. This is where the possible causes will sit to help you pinpoint the potential cause of the problem.
Benefits of fishbone diagrams
Fishbone diagrams are useful tools for improving existing processes and pinpointing causes of issues. Take a look at some benefits of performing a fishbone diagram root cause analysis:
Easily find the root cause of a problem
A fishbone diagram is a visual tool that adds structure and clarity to problem-solving. It indicates the problem and its possible causes in a single location, making it easier for teams to conduct a root cause analysis .
Prevent further problems
By finding the root cause of the problem, you fix the problem at its source and mitigate future issues. As a result, you’re far more likely to prevent the same (or similar) problems from cropping up in the future.
Collaborate with your team
A fishbone diagram is a great way to work with your team to brainstorm solutions . It’s a collaborative diagram, encouraging teams to review all the available information and discuss the best course of action.
If you’re part of a remote or hybrid team, an online platform like Miro allows you to collaborate with your team, no matter where they work. Simply share the diagram and hop on a video chat, and you can perform your root cause analysis virtually.
Example of a fishbone diagram
To see a fishbone diagram in action, look at this CEDAC Template from NEXT LEVEL Partners.
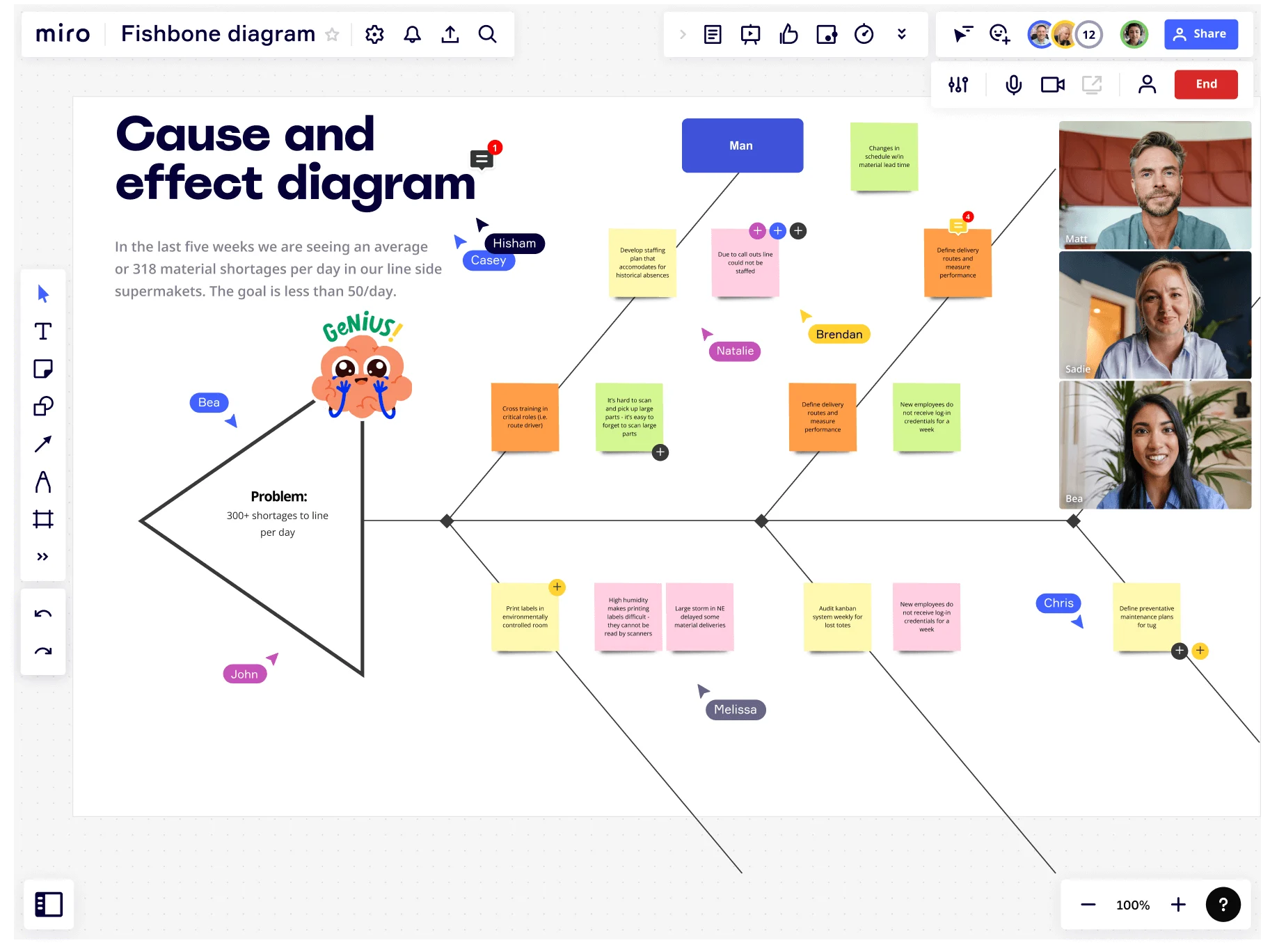
CEDAC is an acronym for Cause and Effect Diagram with the Addition of Cards. The diagram contains issues on the left-hand side of the ribs and solutions on the right-hand side.
Its inventor, Ryuji Fukuda, created CEDAC so that teams can delve deeper into their problem-solving analyses. By adding cards to the diagram, teams have a way of questioning existing information and suggesting new ideas. As a result, they’ll gain a deeper understanding of their problems and how to solve them.
Here are some of the common areas where the CEDAC model can be helpful:
Product development
Visualize issues with product development using the CEDAC diagram. Collaborate with the product team to identify the cause of the problem and use cards to identify the best possible solution.
Software features
Effectively allocate resources based on team structures and capabilities. Understand the most critical problems to solve and how they map together.
Product design
Define failures or problems with your product design, and identify effective solutions. Using the diagram’s cards, product designers can generate new and creative solutions to improve the design.
Internal processes
Pinpoint bottlenecks and figure out how to streamline and improve your business processes. Encourage team members to join in the discussion and make suggestions for improving the process going forward.
When to use a fishbone diagram
Take a look at some of the different instances when using a fishbone diagram can be useful for you and your team.
1. To analyze a problem statement
If you have a clear problem statement for your business, a fishbone diagram is a great way to analyze it in detail. You can see the problem’s culprit and decide how to fix the issue.
2. To brainstorm the causes of the problem
Also known as root cause analysis, a fishbone diagram allows you to discuss the potential causes of a problem. It’s the perfect opportunity to host a brainstorming session to identify pressing concerns and work through possible solutions.
3. To analyze a new product design
Use a fishbone diagram to map your new product design and visualize any potential hurdles before they come your way. As a result, you can put preventative measures in place before going live.
4. To improve your processes
If you’re struggling to streamline your processes and inefficiencies, a fishbone diagram can help. Use a fishbone diagram to pinpoint the troublesome areas of your process and find the cause of a problem. From there, you can determine exactly how to fix it.
5. For quality improvement
Use a fishbone diagram to visualize how and where you can improve to offer your customers a higher-quality experience. For example, you might want to improve the quality of your customer service. In this case, you can use the diagram to find areas for improvement in your existing processes.
How to make a fishbone diagram
Follow these simple steps to create an effective fishbone diagram:
1. Select the Fishbone Diagram Template
While you can always build your own diagram from scratch, you can also get a headstart by selecting this Fishbone Diagram Template . It’s free and easy to use, so you can start mapping your diagram immediately.
2. Outline your problem statement
When your diagram is ready to use, start by defining the problem. Otherwise known as a problem statement, this will sit at the head of the diagram. This must be as clear and concise as possible to find the right solution.
For example, in the diagram below, the main problem is that “40% of users cancel the subscription in the first month.” This statement clearly describes the problem and offers a solid starting point for finding a solution. Now, let’s consider how this would work if the statement were written differently — for example, “to increase customer retention.”
This statement is pretty vague, and there’s a lot of room for interpretation. Instead of focusing specifically on how to keep existing customers after the first month, teams might explore other avenues that won’t necessarily solve the actual problem.
The problem statement doesn’t have to be long and detailed. In fact, you should keep it short — ideally, no longer than a sentence. That way, it’ll be easy for your team to see the problem and won’t overcrowd the diagram. But the problem statement should always be clear and concise, leaving no room for interpretation.
If you’re new to problem statements or want a framework to guide you, look at Prime Motive’s Problem Framing Workshop Template .
3. Pinpoint your root causes
With your problem statement in place, you can now branch out and start to pinpoint the possible causes of the problem.
The specific causes will depend on what your problem statement is. For example, if your problem statement is related to product design, your root causes could include the following:
These are just a few examples. In your diagram, you might find that you have more or fewer root causes. With an intuitive platform like Miro, it’s easy to add or remove boxes based on how many you need.
When adding causes to your diagram, those with the biggest impact should be closest to the problem. The farther away a cause is from the head of the diagram, the less influence it has on the problem.
4. Identify individual causes
You can now identify the individual elements that contribute to the overall cause. These are the bones of the fish.
Let’s use an example to demonstrate how this works. Imagine that one of your root causes is “Equipment.” Here are some of the individual causes that might sit under this area:
You are using outdated and inefficient equipment
It’s expensive to replace existing equipment
There aren’t enough employees who know how to use the equipment
All of these elements could contribute to the problem you’re facing, but it’s up to you and your team to pinpoint the key elements at the root of the problem. Review all this information with your team, and you’ll be able to see which problem is most likely to have a long-term solution.
If you’re unsure how to identify the individual causes, look at the 5 Whys framework . It’s a simple brainstorming tool that helps teams explore the reasons behind a potential problem.
5. Create a plan of action
After working with your team to find the root cause of the problem, you can create an action plan for improvements. This involves mapping out the steps you need to take to solve your problem and how you’ll measure success (we suggest using the SMART Goals framework for this).
During this stage, be sure to focus on how to make lasting improvements. Don’t lose sight of the bigger picture in favor of a quick fix. The purpose of the fishbone diagram is to implement a long-lasting solution to your problem, so keep this in mind when creating your plan of action for the future.
Fishbone diagram categories: the 6Ms of production
The fishbone diagram is used across various industries, but the original diagram was created to improve the manufacturing process. The six methods (6Ms) of production come from this original diagram, and engineers and designers would use this structure to cover all their bases.
The 6Ms of production are as follows:
1. Manpower
The functional activity involved in designing and delivering a product.
The production process and any other processes that contribute to the delivery of the final product.
Any systems, tools, or equipment used in manufacturing.
4. Material
The raw materials and components needed to create the end product.
5. Milieu (or Mother Nature)
Any environmental factors, such as weather, floods, or fire. Although most milieu factors can’t be controlled, there are some instances where businesses can put preventative measures in place to mitigate problems.
6. Measurement
The physical measurements (volume, distance, temperature, and so on) of a product, machine, or workspace.
The 6Ms are only relevant if you’re using the fishbone diagram to improve a manufacturing or production process. If you’re using the diagram for any other purpose, there’s no need to follow this structure.
Discover more
How to build a fishbone diagram
What is a cause and effect diagram
What is root cause analysis?
What is the 5 Whys Framework?
5 Whys: Examples, explanations, and how to find the causes of problems
Get on board in seconds
Join thousands of teams using Miro to do their best work yet.
- Skip to main content
- Skip to primary sidebar
- Skip to footer
Additional menu

Fishbone diagrams: How to use them for problem-solving
October 5, 2023 by MindManager Blog
When something goes wrong, it’s essential to understand the root cause in order to prevent it from occurring again.
However, life and business are both complex, making it difficult to identify at times the underlying causes which created the situation you’re facing now. That’s where and when a fishbone diagram can help!
In this article, we’ll dive into everything you need to know about fishbone diagrams and how to use them for problem-solving.
What is a fishbone diagram?
Fishbone diagrams (also called Ishikawa diagrams and cause-and-effect diagrams) are visualizations used to identify and illustrate the causes for a specific event. Potential causes are often brainstormed and then categorized in order to identify a problem’s root cause.
The diagram gets its name due to the branches radiating out from the main issue in a way that resembles a side view of a fish skeleton. However, the process can be applied to most mind map layouts.
Here’s a fishbone diagram example:
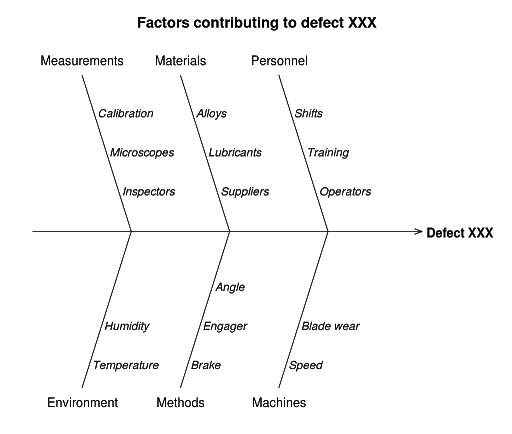
When to use fishbone diagrams
Fishbone diagrams help focus you and your team’s energy on the root cause of a problem instead of merely addressing and wasting time on the symptoms.
Here are a few common applications of Fishbone diagrams:
Manufacturing: Discover the root cause of a manufacturing issue by brainstorming and ranking the likelihood and impact of all the areas that influence the production process.
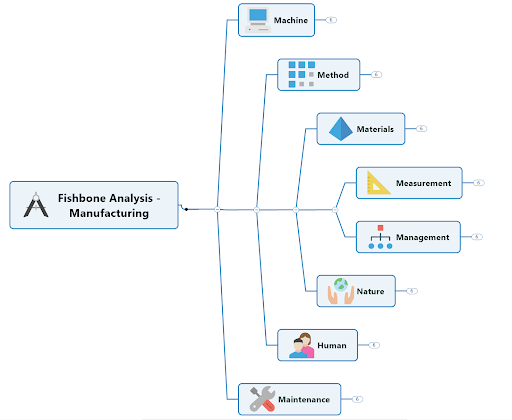
How to create a fishbone diagram in MindManager in 5 steps
Fishbone diagrams are quick to make in MindManager and the examples above are included as templates to make it even easier.
MindManager’s ease of capturing ideas during brainstorming makes it the ideal tool to capture and organize potential causes. The visual format allows you to see all the causes simultaneously, draw relationships between causes, and identify if the root cause is found multiple times within the diagram.
Here’s how to create a fishbone diagram:
- In MindManager, go to the File menu, select New and then click into the Problem-Solving folder. There you’ll find three templates for Fishbones, the manufacturing, service, and product analyses. Select a template.
- Enter the issue in the central topic.
- Next, either brainstorm potential causes and add them as floating topics initially and categorize them after the brainstorming session. Or, use each category as a guide for a mini-brainstorm session and enter the potential causes directly in the appropriate branch.
- Add more details to your causes as new subtopics or notes with the cause itself.
- Once all the potential causes have been identified, you can take the diagram a step further and rank each cause. One way to do this would be to use the Priority marker to rank the cause between 1 and 9. You can later filter the diagram and view specific priorities and hide the less important ones that will distract the focus of the team.
Key MindManager features for fishbone diagrams
There is no one single ‘right’ way to create, categorize, or rank items within a fishbone diagram.
With that said, here’s a list of ways to apply some of MindManager’s features to transform an ordinary diagram into a powerful application to visualize and empower your work.
- Use color (fonts, topic fill color) to categorize different causes.
- Change the font characteristics to emphasize different causes (e.g. bold, larger fonts, different font types, etc.).
- Use topic images to add greater context and enhance the visualizations.
- Write topic notes for more in-depth details related to each cause.
- Apply icons and tags to categorize causes.
- Hyperlink or add attachments to provide more details.
- Draw relationship lines between different connected causes throughout the diagram.
- Assign resources to any causes that you have identified. This may clarify who is responsible or accountable for that cause.
- Collapse branches for a quick overview or drill down into all the details.
- View the diagram through multiple lenses. For instance, you are not confined to the layout of the Fishbone diagram. Switch views to see the diagram as an outline, or dive in the Schedule, Icon or Tag views to see your content in groupings based on your assigned categories or due dates.
- Filter content to either show or hide topics that you have annotated with tags or icon markers. For instance, filter on all the top priority potential causes that need additional investigation.
- Share your diagram by either publishing it onto the web (and sharing a link) where anyone can open and view the Fishbone diagram interactively in their browser or export the diagram into a variety of different formats (e.g. Microsoft Word, HTML5, Microsoft Project, etc.).
Download MindManager today to get started on your fishbone diagram!
Ready to take the next step?
MindManager helps boost collaboration and productivity among remote and hybrid teams to achieve better results, faster.

Why choose MindManager?
MindManager® helps individuals, teams, and enterprises bring greater clarity and structure to plans, projects, and processes. It provides visual productivity tools and mind mapping software to help take you and your organization to where you want to be.
Explore MindManager
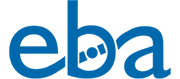
7 Steps to a Fishbone Diagram and to Identifying Those Causes
Often referred to as a cause and effect diagram, or Ishikawa, it is a simple root cause analysis tool that is used for brainstorming issues and causes of particular problems and can and often is used in conjunction with the 5 Whys tool.
In a fishbone diagram, the various causes are grouped into categories and the causes cascade from the main categories, flowing towards the effect, forming what resembles a fishbone appearance.
The prime remit is to brainstorm all the possibilities that could cause the problem and then drill down to the factor(s) that are causing this issue. Once found, eliminate them. It enables the team to focus on why the problem occurs, and not on the history or symptoms of the problem, or other topics that digress from the intent of the session. It also displays a real-time ‘snap-shot’ of the collective inputs of the team as it is updated.
How to Conduct a Fishbone Diagram
Draw the box on the right of a flip chart or large dry wipe board, and write the problem statement in the box. Be as clear and specific as you can about the problem.
Now draw the line going from left to right as the ‘Spine’, connecting to the problem statement.
Draw the ‘fishbones’ emanating from the spine. These represent the main cause categories.
Now label each Fishbone category. There are two options here. You can use the generic cause categories of People, Method, Machine, Material, Environment, which is easier to use for a group that is relatively new to this exercise, or you can brainstorm the major categories related to the specific problem.
Now brainstorm all the causes to the problem. You could use the approach of writing each cause on post it notes, going around the group asking each person for one cause. Continue going through the rounds, getting more causes, until all ideas are exhausted.
For each cause, agree in the group which category the issue should fall in. (An issue can fall in a number of categories) and continue this process until the group have run out of ideas.
- Next, get each individual in the team in turn, to put a tally mark against the top three causes they think affect the problem. You can use supporting data to help you decide, if it is available.
- Once completed, the facilitator adds up all the tallies for each cause and selects the top three with the highest scores. These three issues will now form the basis of additional investigation in order to find the root cause. The team may then investigate these causes further and use problem-solving techniques like 5 Whys to eliminate their occurrences.
An example Fishbone Diagram
The group in the example below, had a problem with excessive scrap. They then got a cross functional team together to understand possible reasons, listing each possible cause into categories.
The next step would be to pick the top three causes and delve deeper to find the true root causes.
A Few Tips Along the Way
1. Remember, as with any task-based activity, always close the session off with actions and owners – “Who is doing what by when?” This is important, as it keeps the teams focused on the project.
2. Hold people accountable and summarise the event, including the actions and deliverables to take away.
3. Have regular reviews with the team in between events, checking for status against the action plan, and work ways of getting tasks back on track if they are falling behind schedule. Keep on top of everything!
4. Leave every task and bit of information clear and concise, so the team understands what is expected of them.
5. As a part of Visual Management, why not create and place a number of large Problem solving boards around the shop floor or in the office. Get the teams to start identifying day to day issues, using QCPC charts and then running quick problem solving sessions, using fishbone diagrams and 5 whys together, 3 times a month for the highest turnbacks on these QCPC charts. You will systematically be embedding a problem solving and continuous improvement culture without even knowing it!
Other Related Articles
- Kepner Tregoe Problem solving
- Six Sigma Tools
- Consensus Decision making
- Lean Manufacturing Principles
- 5 Step Approach
- Failure Mode effects Analysis (FMEA)
- 8D Problem Solving

Fishbone Diagrams for Consequential Problem-Solving

Visualize Processes and Improve
The most successful businesses are not perfect. They are resilient. Every business encounters problems; most encounter them frequently. The ones that thrive are developing a problem-solving culture and arm employees with the tools to find and resolve the root causes of issues effectively. When employees are effective, empowered problem-solvers, obstacles turn into opportunities. One powerful problem-solving tool is the Fishbone Diagram.
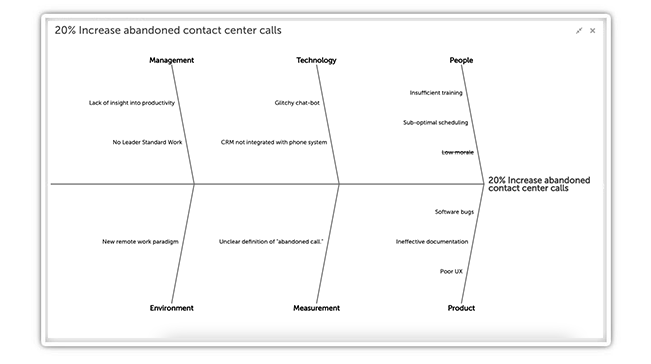
What is a Fishbone Diagram?
A Fishbone Diagram also called an Ishikawa diagram or cause and effect diagram is a visual management tool used to document all the potential causes of a problem to uncover the root causes. The Fishbone Diagram helps users group these causes into categories and provides a structure to display them. When used effectively, it ensures that teams address the actual cause of the problem and don’t just implement a Band-aid solution.
The Fishbone Diagram is called such due to its resemblance to a fish’s skeleton. It was developed by Kaoru Ishikawa and became popular in the 1960s. It is used within many modern quality management methodologies, including Six Sigma and Lean Manufacturing.
When to Use a Fishbone Diagram
Although we refer to the Fishbone Diagram as a structured problem-solving tool, it has other uses. It is helpful in breaking down the contributors to any process or system. Some ways to use it to test a problem statement, conduct root cause analysis, predict the results of a new process, streamline an existing process, improve quality outcomes, and uncover bottlenecks.
How to Use a Fishbone Diagram
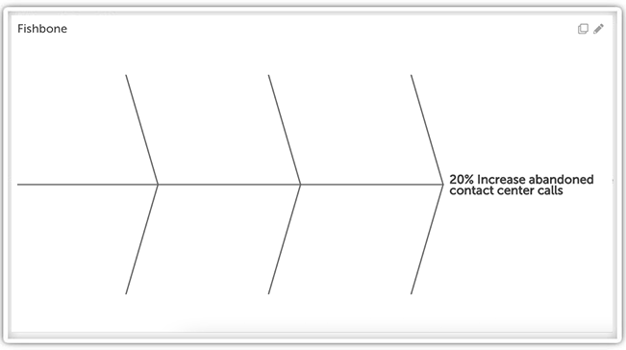
Step 1: Define the Problem
The first step in problem-solving, whether you use the Fishbone or not, is defining the problem correctly. Ideally, the problem statement will include an objective metric that can be used to determine success. For example, a problem statement such as, “The contact center abandon rate is too high,” will not be as helpful as a statement like, “The contact center abandon rate increased by 20% last month.”
In terms of the Diagram, the problem statement represents the “head” of the fish.
Keep in mind:
- If you are using a fishbone diagram to improve a process, instead of the problem, you will define your desired outcome in an objective and achievable way.
- Each of the “bones” in the diagram will represent a category of potential causes, but causes with the most significant impact should be closest to the “head.”
Step 2: Decide on Categories of Causes
The Fishbone tool forces you to think about the potential causes for the problem in several categories represented by the bones. The number will depend on the type and complexity of the problem. You can choose categories that make sense for your project, but in manufacturing, the 6 Ms are often used. They include:
- Man - the people involved in the process
- Methods - the Standard Work by which the process is performed
- Machines - the equipment and tools needed for the process
- Materials - the raw inputs, parts, consumables, and so forth
- Measurements - the data that is used to evaluate process results
- Mother Nature (Environment) - the conditions under which the process is performed.
Another commonly used structure is the McKinsey 7S Framework, which includes Strategy, Structure, Systems, Shared Values, Skills, Style, and Staff. Marketers may go with the 4Ps of Marketing; Product, Place, Price, and Promotion. Non-manufacturing process may include additional categories such as:
In our software call center abandon rate example, we’ll choose the categories of :
- Measurement
- Environment
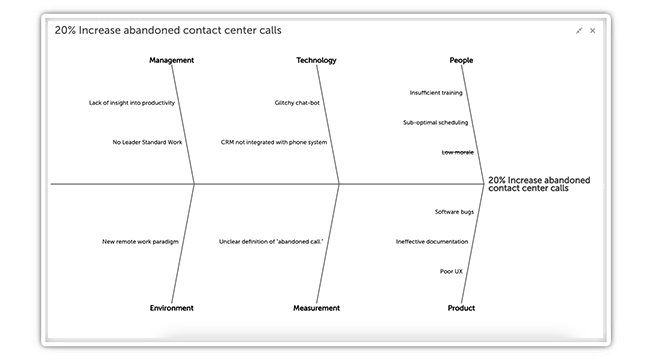
Step 3: Brainstorm Potential Causes and Identify Roots
Now that the categories are defined, the team can go through each one and try to determine all the individual influences that can affect our results. Look at each type and list everything that falls within it. If a potential cause sounds more like a symptom than the root of the matter, the 5 Whys technique can be used to ensure that bottom-line reasons are included. If a source cause supersedes a potential cause, it can be removed from the diagram, or you can use strikethrough to preserve it while moving on to the fundamental problem. In this example, I’ve struck through “Low morale” as a potential cause because it is most likely a symptom of the lack of training and scheduling problems.
Step 4: Analyze the Diagram and Determine Next Steps
The Fishbone Diagram does not direct you to the solution, but it gives you an idea about where to look. By identifying potential causes in this manner, the team can assess the impact of each and brainstorm possible solutions. As in the case of our example, you’ll probably find more opportunities for improvement than you can tackle at once, but the exercise will put the team in a better position to decide what to do next. The Fishbone Diagram also becomes a good starting point for the next improvement cycle once your most critical root causes are addressed.
See How it Works: Schedule a Demo
The benefits of digital fishbone diagrams.
Back in the 1960s when the Fishbone Diagram was introduced, teams used paper to visualize their problem statement and possible causes. While that approach is acceptable for small groups working in the same space for a short period, it is not ideal for the way people work today.
That’s why KaiNexus has incorporated Fishbone Diagrams into our continuous improvement software platform.
- The Fishbone Diagram is created and managed in the same platform you will use for implementing the changes once the analysis is complete.
- Information about your problem, the potential causes, and possible solutions are all collected for future review.
- Remote teams can be as effective as in-person ones.
- Roles and permissions can be applied to determine who can add access and edit Fishbones.
- Fishbone Diagrams can be used for Items, Projects, Improvements, Incidents, Tasks, and Charts.
- Set up to 6 custom categories per diagram or reuse existing categories
- Highlight or strikethrough items
Using digital Fishbone Diagrams that are integrated with your improvement management software will help your team solve problems faster and accelerate the pace of positive change.
Fishbone Diagram Tips
The Fishbone diagram approach is not complicated, but you can do a few things to get the most out of it. We recommend:
- Use category names that are meaningful for your business. If “Methods” isn’t quite right, maybe “Procedures” is a better fit, for example.
- Don’t overload the categories. Create a new one if necessary. Likewise, don’t overcomplicate it; there’s no need to use six categories if four will do.
- Be careful not to add causes that are actually solutions.
- Prioritize your causes by keeping the most impactful ones closest to the “head”
- Use Fishbone Diagrams along with, not instead of, other problem-solving techniques such as The 5 Whys, A3s, process maps, and control charts.
KaiNexus is delighted to put one more digital improvement tool in the hands of our customers. If you’d like to know more about the impact of KaiNexus, one of our experts is available to help.
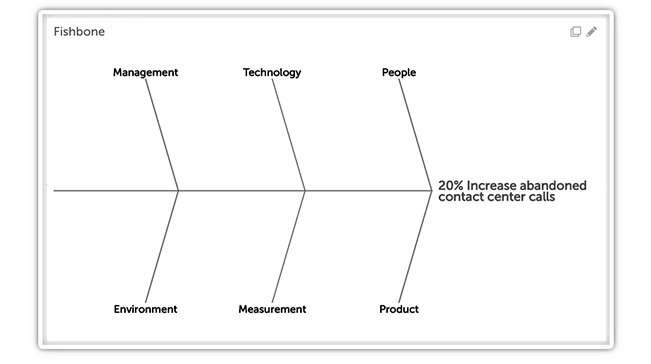
Want to learn more about KaiNexus Fishbone Diagrams?
Check out our fishbone video or support.kainexus.com for more information..
Improvement Software Features
virtual visual management
IMPROVEMENTS & PROJECTS
whatever you do
CHARTS & DATA
track key metrics

KAINEXUS MOBILE
improve from anywhere
engagement, activity & impact
increase collaboration
SMART NOTIFICATIONS
knowledge sharing
see how it works
- Our Customers
Why KaiNexus
- Collaboration
- Standardization
- Customer Success Manager
- Lean Strategy
- Solutions Engineering
- Customer Marketing
- Configuration
- Continuous Enhancements
- Employee Driven
- Leader Driven
- Strategy Development
- Process Driven
- Daily Huddles
- Idea Generation
- Standard Work
- Visual Management
- Advanced ROI
- Notifications
- Universal Badges
- Case Studies
- Education Videos
Copyright © 2024 Privacy Policy
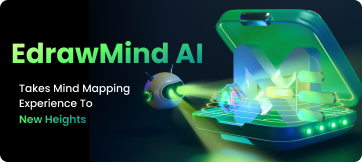
- Mind Map Maker
- Concept Map Maker
- Bubble Map Maker
- Brace Map Maker
- Sunburst Chart Maker
- Online AI Note Taker
- Timeline Maker
- Tree Diagram Maker
- Fishbone Diagram Maker
- Organizational Chart Maker
- Gantt Chart Maker
- Spider Diagram Maker
- EdrawMind AI
- AI Summarize
- AI Mind map
- AI Article generation
- AI Copywriting
- AI Translation
- --> --> >--> -->