Staying on the Journey to Success: How CAPA Can Sustain Your Organization
By Andy Marker | January 30, 2018 (updated July 21, 2021)
- Share on Facebook
- Share on LinkedIn
Link copied
Experience, training, and sound procedures in your facility may mean that problems rarely arise. But, what about when they do? CAPA , or corrective action and preventive action , can provide a structure for finding the root cause of problems, solving those problems, documenting the conditions and solutions for the future, and looking for potential problems and their solutions. Corrective actions are often used in HR and other manufacturing contexts, but other industries may also be required by the Food and Drug Administration (FDA) to document CAPA processes and then follow the processes if a problem occurs — especially food processing or pharmaceutical and medical device manufacturing.
This article covers the important differences between corrective action and preventive action. It discusses CAPA within ISO 9001 and within the regulation FDA 21 CFR 820 and outlines how and what data sources serve users well in preventive action analysis. In addition, a CAPA consultant discusses how the essential tool, CAPA, can provide lasting support to your company.

What Is Corrective and Preventive Action?
Corrective and preventive actions are processes for identifying, documenting, and addressing defects, deficiencies, and nonconformities.
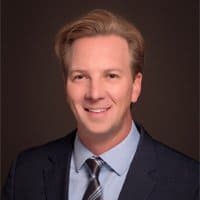
“CAPA is the immune system of your organization,” explains Nathan Conover, President of the consulting and training firm Pathwise . “It’s a system by which you can identify deviations or quality events, investigate them, and implement corrective and/or preventive actions to improve your organization,” he adds.
What Is CAPA?
CAPA is the abbreviation for corrective action and preventive action. These two aspects of CAPA have traditionally been connected, but are ideally are only distantly related. Here is the main difference between the two:
- Corrective Action: Elimination of the cause or causes of an existing nonconformity or undesirable situation in order to prevent recurrence.
- Preventive Action: Identification and elimination of the cause(s) of potential nonconformities in order to prevent occurrence.
In standards such as ISO 9000 and FDA 21 CFR 820, the description of preventive action follows directly after the description of corrective action, which has led to the misconception that the two processes must work together in series. In fact, they are separate, and preventive action ideally precedes corrective action to prevent or avoid the need for corrective action.
CAPA processes are used particularly in food processing, medical device development and manufacturing, and pharmaceuticals. FDA 21 CFR 820 is the quality system regulation that requires corrective and preventive procedures to be documented in medical device manufacturing facilities.
Corrective and preventive actions also have a place in the quality management process as defined in the Project Management Book of Knowledge (PMBOK). Corrective and preventive action is also considered a tool within Six Sigma for understanding regular business operations. CAPA has strong parallels with Design for Six Sigma (DFSS) , used to design new products or redesign existing products. The analytical aspects of both corrective and preventive actions also harken back to PDCA . The component of preventive action that encourages documentation and company education on innovations and lessons learned is similar to Yokaten in lean manufacturing.
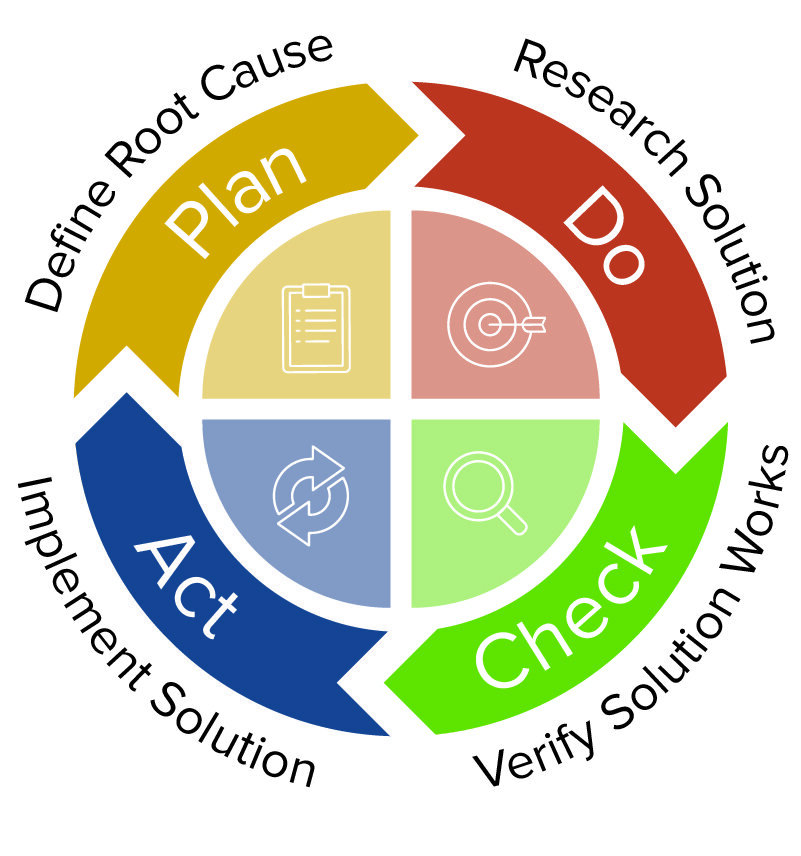
What Is the Difference between Corrective Action and Preventive Action?
Corrective is reactive. Preventive is proactive. Although these two actions use similar processes and some of the same analytical tools, they are not necessarily used together.
What Is the Meaning of Corrective Action?
Corrective action involves the identification, documentation, and elimination of the root cause of a nonconformity or problem to prevent the problem from recurring. Corrective actions are taken under more intense consideration than corrections (which address immediate issues), and you typically enact corrective actions over a slightly longer time period to prevent recurrence. For example, if you put a bucket under a leaking garburator, that’s a correction. If you inspect the entire sink and drain, learn that the unit repeatedly leaks and blocks because of a damaged seal and joint, and then remove and replace the garburator with an effective garburator that will not leak or clog, that’s a corrective action.
Most corrective action procedures use a variation of 8D problem solving. The following are some of the types of steps in a corrective or problem solving process:
- Promptly identify and document the problem. Use 5 Why questioning to acquire details and determine if this is an isolated event or if it is significant and has the potential to recur. Reporters may indicate that the problem is pervasive, but it may be limited. When documented, quality events should be reported to management. The 5 Why template below will help you identify the root cause of a problem.
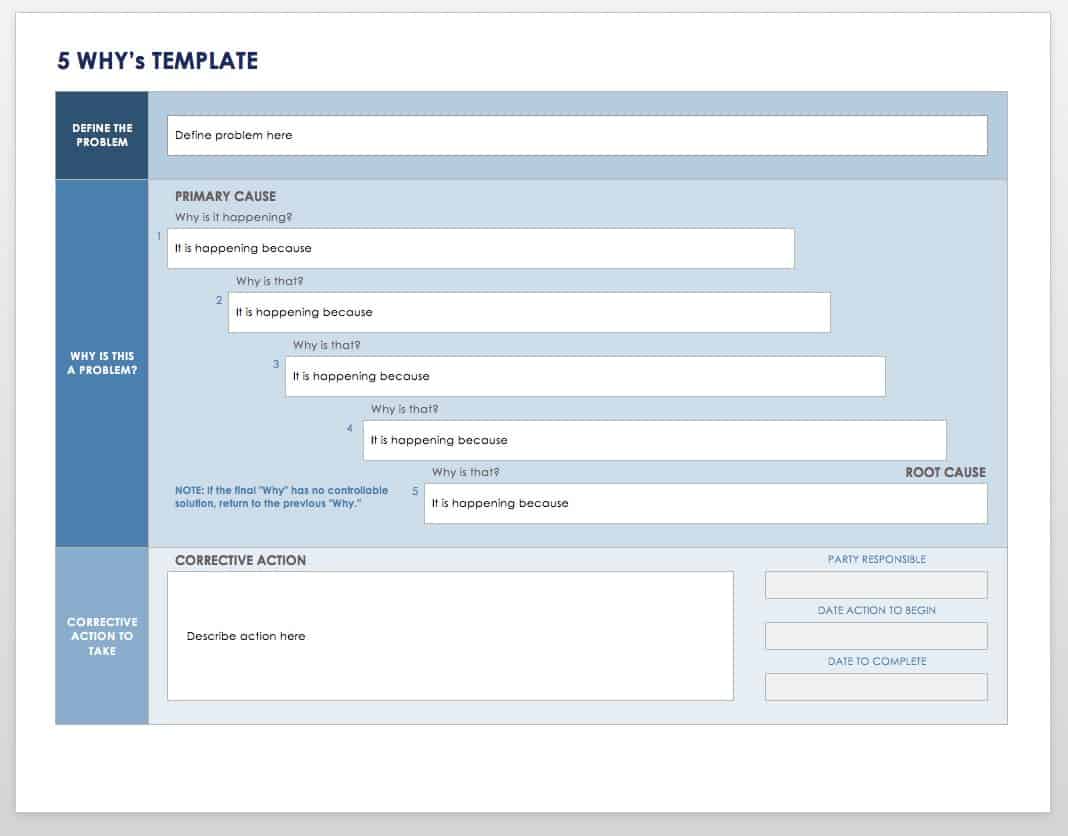
Download 5 Whys Template
Excel | Word | Smartsheet
- Implement a correction or containment or temporary repair. This may include removing a defective item from production.
- Find the cause of the issue. Use 5 Whys to help pinpoint a problem statement. Use an Affinity or Ishikawa (fishbone) diagram to help determine the root cause. You can use the free Ishikawa diagram template below to get started.
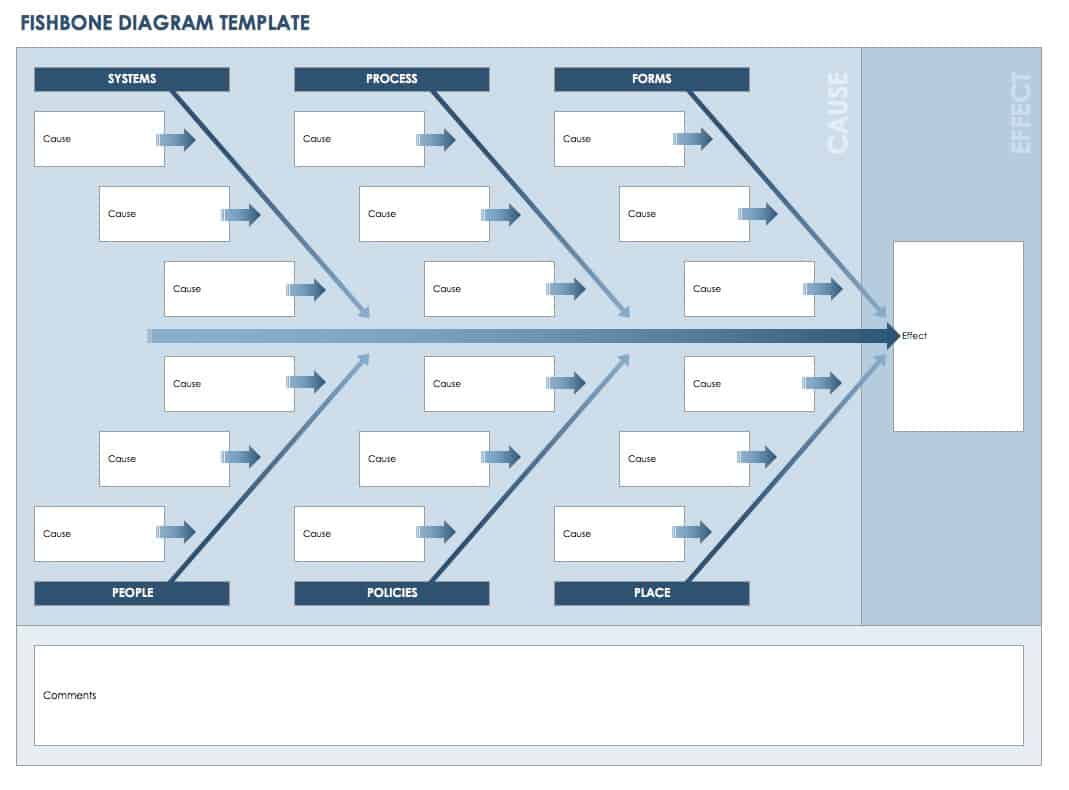
Download Fishbone Diagram Template - Excel
- Determine the solution that will prevent a recurrence. Solutions can include new parts, process changes, and even system changes.
- Implement the corrective action and ensure that everything is documented.
- Verify that the action continues to be effective and that the problem does not recur. Document the evidence of continued success.
Risk-Based Prioritization
Along with the defined corrective action procedures, a predefined risk-based prioritization eliminates small nonconformities that teams can solve when they discover problems without initiating corrective procedures. Weight matrices help with these questions — the criteria often include frequency (frequently, occasionally, or rarely) and impact (negligible, critical, or even resulted in injury or death). Safety usually trumps frequency in action response.
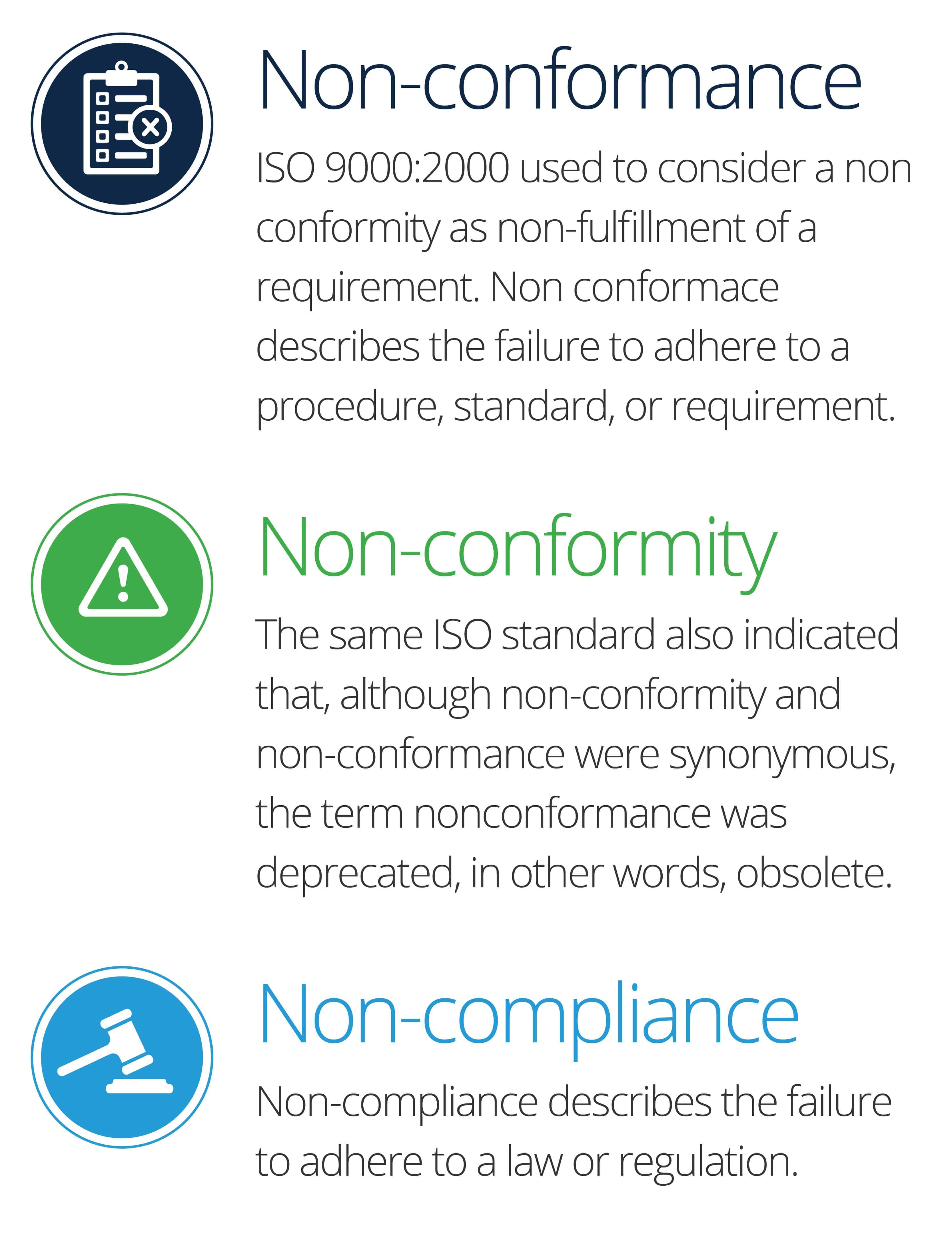
What Is Preventive Action in ISO?
Until the release of ISO 9000:2015, preventive action was one of the few mandatory procedures required by ISO 9001. Companies were also required to keep records on nonconformities and preventive actions taken. However, some practitioners considered the standard to be unclear regarding where to look for potential problems. Pundits explained that preventive actions concerned risk and directed practitioners to ISO 9004, “managing for the sustained success of an organization — a quality management approach,” which was considered a pointer to what preventive actions should address.
ISO 9000:2015 eliminates the requirement for predefined procedures for both corrective action and preventive action. In fact, preventive action is now considered a part of good planning and risk management. It fully incorporates the notion that prevention comes first and eliminates problems and, thereby, the need for corrective action. As of 9001:2015, you simply document what happened and how you fixed it. Following are the essential CAPA-related definitions:
- Correction or Immediate Action: This eliminates the immediate problem. It doesn’t eliminate the issue permanently, but it allows a process or work to continue. In PMBOK, correction is also known as defect repair . An example of this process is mopping up water and adding a bucket under the leak.
- Corrective Action: This eliminates the cause of the nonconformity and prevents repetition. Corrective actions move products, procedures, processes, and projects back to baselines. On a large scale, corrective action is necessary if a project moves away from the project management golden triangle of budget, schedule, and quality. An example of corrective action would be investigating the sink, drain, and supply system, learning that the garburator backed up twice before, replacing the garburator, and confirming that nothing leaks.
- Preventive Action: This prevents potential occurrences. Preventive action determines what in a project might veer away from the project management golden triangle of budget, schedule, or quality. An example of this process would be checking the other garburator in another sink as well as U traps in two other sinks for existing problems and asking if any parts should be replaced now before they fail.
The following are tools that you can use to analyze risk or potential problems:
- Hazard and Operability Study (HAZOP): A HAZOP is a sequenced and methodical study of a process that is in development or in operation. The HAZOP seeks to identify problems that may represent risks to personnel or equipment.
- Failure Modes and Effects Analysis (FMEA): FMEA is a step-by-step approach for identifying all possible failures in a design, a manufacturing or assembly process, or a product or service. Failure modes means the ways (or modes) in which something might fail.
- Fault Tree Analysis (FTA): FTA is commonly used in safety and reliability engineering to break a system into subsystems to understand where problems may occur. FTA is often used in pharmaceutical development and manufacturing.
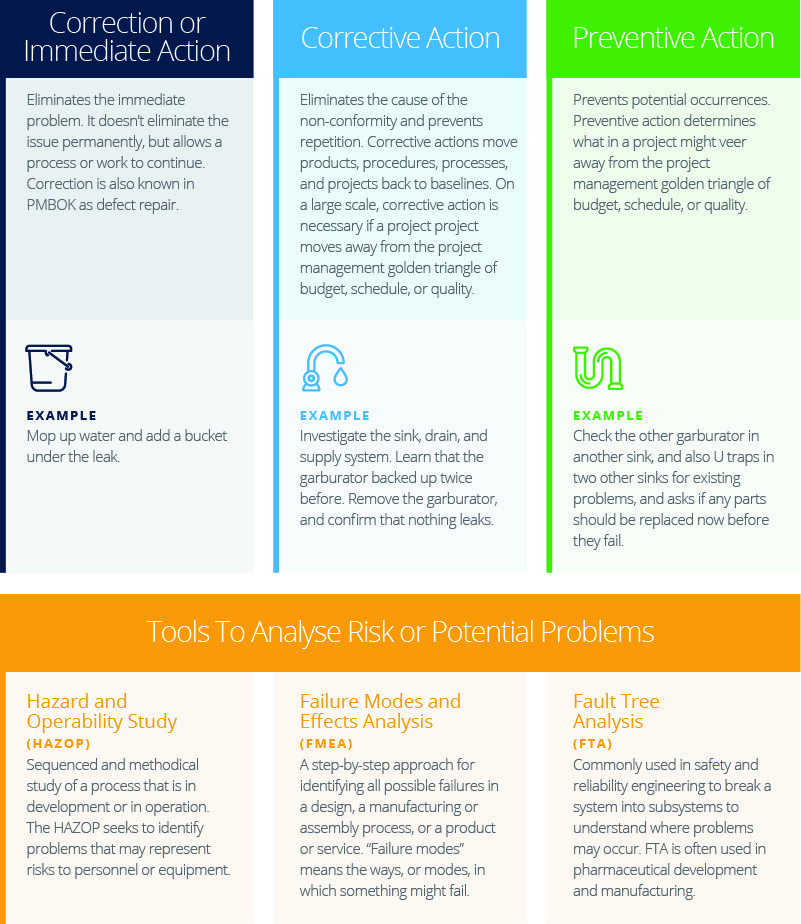
What Is a Preventive Action Process?
A preventive action process , in addition to including a specific preventive action plan to mitigate potential problems, also comprises the implementation of controls to ensure that any preventive measures continue to work. Preventive action means identifying not only potential problems, but also opportunities for improvement. With changes that are enacted through a preventive action process, controls should be included to prevent and check for possible nonconformities.
What Is an Example of Preventive Control?
A preventive control , also known as an internal control , serves to reduce the chances of problems and nonconformities that occur. Although many fields employ them, preventive controls form a particularly important part of food preparation quality control. Under the FDA’s Food Safety Modernization Act (FSMA), for example, certain food preparation facilities must write a food safety plan, which begins with a hazard analysis and addresses specific types of controls. For instance, among other preventive controls, food preparation must include allergen tracking, and packaging must be labelled appropriately. However, preventive controls can be as simple as employees washing their hands and segregating utensils used for raw foods. The FSMA lists corrections and corrective actions as a management aspect of preventive controls to be implemented in quality events, such as when a deviation from a preventive control occurs. The practice of preventive controls for food safety even has its own professional support group, the Food Safety Preventive Controls Alliance ( FSPCA ).
Approaches to Preventive Analysis and Actions
One complaint with regard to CAPA in ISO 9000 was that it was vague about how possible problems might be found. So, where do you look for for possible problems? Think about what could go wrong.
According to Conover, “It’s when you’re in production. That’s when all the unanticipated risks typically occur. It’s where you think, ‘Oh my gosh, we didn’t anticipate that this would happen.’” He says that’s why the analogy to a human immune system is strong: “Your immune system reacts to antigens that are unknown or toxic to the body. Once the antigens are discovered, [your immune system] applies antibodies. In the future, in some cases, T-cells will selectively recognize previously known antigens and minimize any effect. Just like with CAPA, those things that happen in pre-production, production, or post-production should have corrective and/or preventive actions that ensure that they do not occur or recur,” he emphasizes.
Teams may find potential problems in internal or external data sources. Internal data sources may include process control data, trend analysis, the results of proficiency testing, or internal audits. External data includes customer complaints, service reports, and even data for similar products produced by other companies.
Risk analysis should be done when you adopt new tools or software. Preventive actions may also be sparked through the results of regularly assessing employees and then deciding if more or revised training is required. Risk analysis can help target costs, so the exercise doesn’t appear to be a waste of money when problems don’t occur. FMEA is one tool to view potential problems.
Here are some examples of preventive actions:
- Creating disaster recovery plans for hazards and unexpected situations throughout your facility
- Implementing or updating safety and security policies
- Creating checklists
- Implementing lean practices to reduce waste that can contribute to problems and nonconformities
- Implementing and following preventive maintenance plans to ensure that equipment performs efficiently, effectively, and safely
Some experts still think that preventive actions follow the experience of corrective actions. This sensible approach focuses on capturing the experience for the future, including tagging keywords from the action report in databases and updating documents, such as FMEA, requirements documents, and procedures.
What Is 21 CFR 820?
21 CFR 820 stands for Title 21 Code of Federal Regulations 820. Title 21 governs food and drugs for the FDA. CFR 820 is the quality system regulation that applies to manufacturers of medical devices. 21 CFR 820 borrows heavily from ISO 9000: It requires facilities to create and maintain procedures for implementing corrective and preventive actions so that employees can address problems with devices currently or imminently on the market.
A well-defined CAPA process, or subprocess , as the FDA calls it, provides structure for accomplishing three things:
- Gathering and analyzing information to find existing and potential problems and nonconformities
- Observing quality issues and applying effective corrective or preventive actions as needed
- Ensuring that corrective and preventive actions have been effective
In the FDA’s view, a CAPA process also provides a structure for communicating CAPA activities to employees, reporting to management, and documenting activities for review and future improvement purposes.
The CAPA concept is also integral to the Current Good Manufacturing Process (cGMP), an approach advocated by the FDA. CAPA may be applied to a variety of aspects of product development, such as design, production, product testing, and post-market use. CAPA may also be applied in product packaging, distribution, and shipping.
Questions in a CAPA Inspection
When the FDA inspects your facility, it may seek to ensure that you have documented CAPA procedures and make sure that they contain certain elements. For example, your records should show that you could find the root cause of problems and that you are tracking trends to ensure you avoid future problems or recurrences of problems. Investigators also look for evidence that you tested CAPA actions to ensure effectiveness before you implemented them. Moreover, the FDA wants to verify that the data source and statistical process methods you employed were sufficient for the task.
What Is a CAPA Report?
A CAPA report provides a consistent vehicle for recording defects and issues as well as the method of their correction. Usual details include where the problem occurred, the customer’s name and address, the details of the problem, whether there was a product breakdown, whether there was an injury, and so on. The report also states what immediate action or correction was taken. The report may walk you through the process, suggest tools for the root cause analysis (such as 5 Whys and cause and effect analysis), and provide room to record analysis results. It may also provide guidance on how to route the report depending on the outcome of the analysis.
You can use the free template below to create a CAPA report.
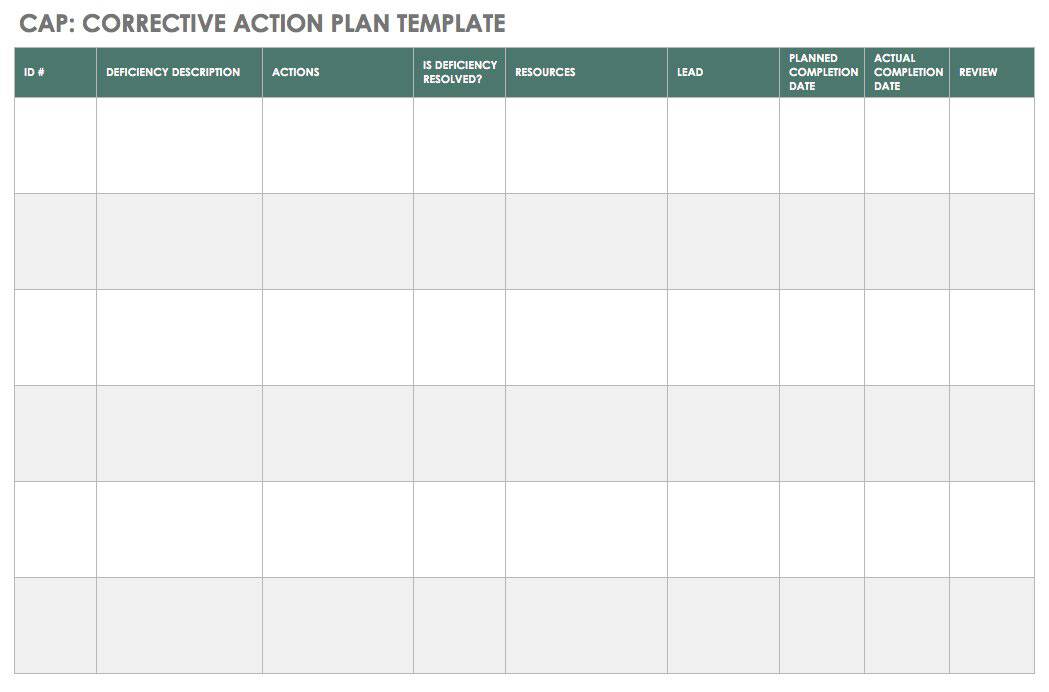
Download CAPA Report Template
Misconceptions About CAPA
Although regulations may require organizations to document CAPA processes and follow them during quality events, and tons of web content exists concerning how to implement CAPA, employees and managers often harbor the following doubts and misconceptions about CAPA:
- It’s a Punishment because Something Has Gone Wrong: For the health of a company, someone has to implement the CAPA process. Training a dedicated CAPA team can help to depersonalize CAPA assignments.
- It’s Extra Work: “When everybody has a part-time job of being an investigator, typically nothing changes,” says Conover. He gives the example, “‘You’re a QE and, by the way, in your spare time, which you don’t have, you’re an investigator.’” In that scenario, he says, the extra work remains undone. The solution is to establish a review board with people trained in appropriate roles so that CAPA becomes a regular responsibility.
- Training Is Too Expensive: Management often complains that neither budgets nor schedules offer resources for training employees in the efficient execution of CAPA. You can save money by having the process in place. You should also ask yourself how much it costs to have a product recalled. “Here are our biggest comments: We don’t have time to train. We don’t have the money to train. There's no budget. I can’t pull people off the floor for a day and a half,” says Conover. The bottom line? “Organizations that train are the ones that sustain, and those that don’t won’t survive beyond five, 10, or 15 years,” he concludes.
Software Solutions for CAPA
The many details and documents necessary for a good quality management system are represented in CAPA. Although software can’t make up for a poor CAPA procedure or lack of follow through, a strong platform can help track the many updates that should be added to assorted documents. Software can also support documentation and audit trail requirements for the FDA’s GMP, GLP (good laboratory practice), and GCP (good clinical practice). With a web-based system, authorized users can access a central repository to get all the documents and information they require. Online templates and automated workflows provide routing, notification, and electronic approval. Finally, software can help with analytics and reporting.
Improve CAPA Procedures with Work Management in Smartsheet
Empower your people to go above and beyond with a flexible platform designed to match the needs of your team — and adapt as those needs change.
The Smartsheet platform makes it easy to plan, capture, manage, and report on work from anywhere, helping your team be more effective and get more done. Report on key metrics and get real-time visibility into work as it happens with roll-up reports, dashboards, and automated workflows built to keep your team connected and informed.
When teams have clarity into the work getting done, there’s no telling how much more they can accomplish in the same amount of time. Try Smartsheet for free, today.
Discover why over 90% of Fortune 100 companies trust Smartsheet to get work done.
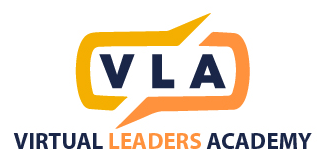
Virtual Leaders Academy
Your cart is currently empty!
CAPA Tools in Problem Solving: Mastering Continuous Improvement
Corrective and Preventive Actions (CAPA) tools serve as invaluable instruments, allowing organizations to identify, analyze, and eliminate the root causes of problems. This comprehensive exploration delves into the world of CAPA tools, understanding their significance, exploring various types, and elucidating their role in fostering a culture of continuous improvement.
Understanding CAPA Tools
What is CAPA?
Corrective and Preventive Actions, commonly abbreviated as CAPA, is a systematic approach to solving problems, identifying the root causes of issues, and implementing measures to prevent their recurrence. It’s a vital component of quality management systems, ensuring that organizations not only address existing problems but also proactively work to prevent similar problems in the future.
The Significance of CAPA Tools
CAPA tools are designed to provide a structured framework for problem-solving. They enable organizations to:
- Identify Problems : CAPA tools facilitate the identification of problems or discrepancies in processes, products, or services.
- Investigate Root Causes : These tools help in conducting in-depth investigations to identify the underlying causes of the problems.
- Implement Corrective Actions : CAPA tools guide the implementation of immediate corrective actions to address the existing issues promptly.
- Develop Preventive Actions : By understanding the root causes, organizations can develop preventive actions to stop similar issues from occurring in the future.
- Monitor and Review : CAPA tools assist in monitoring the effectiveness of the implemented actions and reviewing their impact on the overall process or system.
Types of CAPA Tools
- Fishbone Diagram (Ishikawa Diagram) : This graphical tool is instrumental in identifying and categorizing potential causes of a problem. It helps in visualizing the various factors contributing to an issue, making it easier to identify root causes.
- 5 Whys Technique : Rooted in simplicity, the 5 Whys technique involves asking “why” repeatedly until the root cause of a problem is identified. It’s a powerful tool to uncover deeper issues beyond surface-level symptoms.
- Failure Mode and Effects Analysis (FMEA) : FMEA is a systematic method for evaluating a process to identify where and how it might fail and to assess the relative impact of different failures. It prioritizes failure modes and guides corrective and preventive actions.
- Pareto Analysis : As previously discussed, Pareto Analysis helps in identifying the vital few causes that contribute the most to a problem. It assists in prioritizing efforts and resources to address the most significant issues.
- Control Charts : Control charts are graphical representations of processes over time. They help in identifying patterns, trends, and abnormalities in processes, enabling organizations to take corrective actions when necessary.
Implementing CAPA Tools Effectively
- Clear Documentation : Proper documentation of the problem, investigation process, identified root causes, and implemented actions is crucial. Clear documentation ensures that everyone involved understands the issue and the steps taken to address it.
- Cross-Functional Teams : In complex issues, involving cross-functional teams with diverse expertise can provide a well-rounded perspective. Different viewpoints can aid in comprehensive problem analysis.
- Data-Driven Decisions : CAPA tools rely heavily on data. Ensuring that the data collected is accurate, relevant, and comprehensive is vital for making informed decisions and implementing effective solutions.
- Continuous Monitoring : Implementing CAPA is not a one-time task. Continuous monitoring and regular reviews are essential to ensure that the implemented actions are effective and that new issues are promptly addressed.
- Employee Training and Engagement : Training employees in the proper use of CAPA tools and fostering a culture of engagement where employees feel comfortable reporting issues is essential. Employees are often the first to notice problems and can provide valuable input during the CAPA process.
Real-World Applications of CAPA Tools
- Healthcare Industry : In healthcare, CAPA tools are utilized to address patient safety incidents, medical errors, and regulatory compliance issues. They help healthcare providers in identifying the causes of adverse events and implementing measures to prevent their recurrence.
- Manufacturing and Quality Control : Manufacturing industries employ CAPA tools to identify defects in products and processes. By addressing these defects, manufacturers enhance product quality and reduce waste, ultimately saving costs.
- Information Technology : IT companies use CAPA tools to investigate software bugs, system failures, and security breaches. Rapid identification and resolution of these issues are critical in maintaining the reliability and security of IT systems.
- Pharmaceutical Sector : Pharmaceutical companies rely on CAPA tools to ensure product quality, compliance with regulations, and patient safety. CAPA processes are essential in addressing deviations in manufacturing processes and preventing the distribution of faulty products.
- Food and Beverage Industry : Ensuring food safety is paramount in this industry. CAPA tools help in identifying and rectifying issues related to food contamination, processing errors, and quality control, safeguarding consumers’ health.
Challenges and Considerations in Implementing CAPA Tools
- Resistance to Change : Implementing CAPA tools often requires a cultural shift within an organization. Resistance to change can hinder the adoption and effectiveness of these tools.
- Resource Allocation : CAPA processes can be resource-intensive, requiring time, expertise, and technology. Allocating sufficient resources while balancing other organizational needs is a challenge.
- Compliance and Regulations : Industries such as healthcare and pharmaceuticals need to adhere to stringent regulations. Ensuring that CAPA processes comply with these regulations adds complexity to the implementation.
- Complex Systems : In intricate systems, identifying the root cause of a problem can be challenging due to numerous interconnected components and variables. Simplifying the problem without oversimplifying it is a delicate balance.
- Data Integrity : Ensuring the integrity and accuracy of the data used in CAPA processes is crucial. Inaccurate data can lead to misguided analyses and ineffective solutions.
Corrective and Preventive Actions (CAPA) tools represent a cornerstone in the realm of quality management and continuous improvement. In a world where problems are inevitable, the ability to identify their root causes and implement effective solutions is a hallmark of successful organizations. By employing diverse CAPA tools, understanding their nuances, and fostering a culture of problem-solving, industries can not only address existing issues but also proactively prevent future challenges. In essence, the effective implementation of CAPA tools transforms problems from obstacles into opportunities, propelling organizations toward excellence and sustained growth.
- Guide: Corrective and Preventive Actions (CAPA)
Daniel Croft
Daniel Croft is an experienced continuous improvement manager with a Lean Six Sigma Black Belt and a Bachelor's degree in Business Management. With more than ten years of experience applying his skills across various industries, Daniel specializes in optimizing processes and improving efficiency. His approach combines practical experience with a deep understanding of business fundamentals to drive meaningful change.
- Last Updated: August 9, 2023
- Learn Lean Sigma
The importance of a systematic approach to addressing discrepancies cannot be overstated in an era where quality assurance is paramount. The Corrective and Preventive Actions (CAPA) methodology is a beacon in this realm, providing a structured path to not only identifying and resolving nonconformities, but also preventing their recurrence. CAPA, which is widely recognized in a variety of industries ranging from healthcare to manufacturing, not only improves the quality and dependability of products and services but also fosters a culture of continuous improvement. This guide walks businesses through the CAPA process step by step, ensuring they are prepared to face challenges and raise their standards.
Table of Contents
What is capa.
Corrective and Preventive Actions (CAPA) form a key approach in quality management systems. They provide a structured approach to managing and resolving issues as they arise. Both corrective and preventive actions are often used within other methodologies, such as 8D.
CAPA is divided into two focuses:
- Correct Actions: Corrective actions focus on identifying and resolving existing issues, which are often triggered by customer complaints, the results of internal or external audits, and process monitoring.
- Preventive Actions: Preventive actions are a proactive approach to identifying potential failures before they result in actually being an issue and allowing businesses to take action to prevent them.
Corrective Actions
Corrective actions target existing problems and usually follow the following steps:
Step 1: Identification
The first step of taking corrective action is to identify existing issues or non-conformity. These can come in various forms such as customer feedback or complaints, internal audits, external audits from customers who review your processes, government regulator audits, or internal performance metrics.
Most medium to large businesses will have various forms of audits such as finance, health and safety or environmental, the audits review processes and usually result in corrective actions needing to be taken.
Step 2: Investigation
Once an issue has been identified the next step is to understand the cause of the issue. Structured methods are usually used to understand the root cause of the issue that occurred in the first place.
Root cause analysis tools such as Fishbone Analysis or 5 Whys are usually used. These tools are used as they provide a clear demonstration of root cause analysis of the issue which can be demonstrated to the stakeholder who raised the issue, such as the auditor or customer.
Step 3: Action Plan
Step 4: review.
Finally, after the actions are implemented, there should be a review of the effectiveness of the actions. To understand if the actions sufficiently resolved the problem, if they did not the cycle should be repeated again until the issue is fully resolved.
Preventive Actions
Preventive actions are proactive measures that aim to reduce the likelihood of problems occurring in the first place. Where Corrective Actions deal with existing issues, Preventive Actions seek to avoid potential future issues.
Here’s a breakdown of the steps involved:
Step 1: Forecasting
The first step in taking preventive action is to foresee ways in which potential issues might occur. This can involve looking at KPIs for trends, control charts behaviour, FMEA , SWOT analysis , customer feedback, and market trends.
Step 2: Risk Assessment
Once the potential risks of failure are identified, the next step is to assess the risk. A risk assessment looks into what the impact, detectability and likelihood of the risk occuring and can be scored a risk priority number (RPN) which is calculated when using an FMEA analysis
Example of FMEA:
Based on the risk assessment, a preventive action plan should then be developed. This could involve process changes, employee training, or resource allocation.
Preventive actions are not a set-it-and-forget-it process; they are a continuous process of reviewing and improving. Businesses need to continuously monitor processes and feedback, adjust, and improve as necessary.
Through its systematic approach, CAPA is two-fold: It addresses current non-conformities via Corrective Actions and aims to reduce future risks through Preventive Actions. This guide provided you a structured walk-through of each stage in the CAPA process, ensuring your business is fully equipped to both tackle challenges and elevate its standards. So, it’s not just about compliance or ticking boxes; it’s about ingraining a culture of continuous improvement.
- Motschman, T.L. and Moore, S.B., 1999. Corrective and preventive action . Transfusion science , 21 (2), pp.163-178.
- Raj, A., 2016. A review on corrective action and preventive action (CAPA). African Journal of Pharmacy and Pharmacology , 10 (1), pp.1-6.
- Westcott, R., 2005. Corrective vs. preventive action. Quality Progress , 38 (3), p.104.
Q: What is the primary purpose of the CAPA process?
A: The CAPA process aims to identify, address, and prevent nonconformities or issues within processes, products, or services, ensuring continuous improvement and adherence to quality standards.
Q: How is a Corrective Action different from a Preventive Action?
A: Corrective Actions address existing nonconformities or issues, ensuring they do not recur. In contrast, Preventive Actions focus on identifying potential issues or risks and implementing measures to prevent them from occurring in the first place.
Q: Why is Root Cause Analysis important in the CAPA process?
A: Root Cause Analysis (RCA) identifies the underlying reasons for an issue, rather than just addressing its symptoms. By understanding and addressing the root cause, organizations can implement more effective and long-lasting solutions.
Q: Is documentation crucial in CAPA? Why?
A: Absolutely! Documenting each step of the CAPA process ensures traceability, facilitates reviews, provides evidence for regulatory compliance, and offers a reference for future problem-solving activities.
Q: What tools can be used for Root Cause Analysis?
A: Several tools aid RCA, including the “5 Whys” technique, Fishbone Diagram (Ishikawa), and Fault Tree Analysis. The choice of tool depends on the nature of the problem and the preference of the investigating team.
Q: How often should the Effectiveness Review be conducted?
A: The frequency of the Effectiveness Review can vary based on the severity of the initial issue and the industry’s regulatory standards. However, it’s generally advised to set regular intervals (e.g., monthly, quarterly) to ensure continued effectiveness of implemented actions.
Q: Why is it important to foster a blame-free environment in CAPA?
A: A blame-free environment promotes openness and transparency. When team members feel safe reporting issues without fear of reprisal, it leads to quicker identification and resolution of problems and encourages a culture of continuous improvement.
Daniel Croft is a seasoned continuous improvement manager with a Black Belt in Lean Six Sigma. With over 10 years of real-world application experience across diverse sectors, Daniel has a passion for optimizing processes and fostering a culture of efficiency. He's not just a practitioner but also an avid learner, constantly seeking to expand his knowledge. Outside of his professional life, Daniel has a keen Investing, statistics and knowledge-sharing, which led him to create the website learnleansigma.com, a platform dedicated to Lean Six Sigma and process improvement insights.
Free Lean Six Sigma Templates
Improve your Lean Six Sigma projects with our free templates. They're designed to make implementation and management easier, helping you achieve better results.
Other Guides

Continuous Improvement Toolkit
Effective Tools for Business and Life!
A3 Thinking: A Structured Approach to Problem Solving
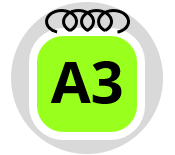
- 5 MINUTES READ
Also known as A3 Problem Solving.
Variants include 8D and CAPA.
A significant part of a leader’s role involves addressing problems as they arise. Various approaches and tools are available to facilitate problem-solving which is the driving force behind continuous improvement. These methods range from the advanced and more complex methodologies like Six Sigma to the simpler and more straightforward A3 thinking approach.
The power of the A3 approach lies in its systematic and structured approach to problem-solving. Although it appears to be a step-by-step process, A3 is built around the PDCA philosophy. It relies on the principle that it is much better to address the real root-cause rather than trying to find a solution. Hence, it’s important not to jump to the solution when solving a problem as it is likely to be less effective.
A3 thinking provides an effective way to bring together many of the problem-solving tools into one place. For example, techniques such as the 5 Whys and fishbone analysis can be used during the ‘Analysis’ stage to help identifying the root causes. Additionally, visual aids and graphs are highly recommended in the A3 report, as they are more effective than text in communicating ideas and providing concise project updates.
A3 thinking involves the practice of consolidating the problem, analysis, countermeasures, and action plan onto a single sheet of paper, commonly an A3-sized sheet. This brief document serves as a summary of the project at hand and is regarded as a valuable storytelling tool for project communication. Utilizing the A3 approach doesn’t require any specialized software or advanced computer skills. You may however use readily available A3 templates , or rely on basic tools such as paper, pencil and an eraser as you will need to erase and rewrite several times.

One of the characteristics of the A3 approach is that it does not get into specific details. Detailed documents are usually attached to the A3 report to prevent overwhelming the reader with an excess of information.
The A3 process is typically structured in multiple stages based on the PDCA model. The primary focus is on developing understanding of the current situation and defining the desired outcome before thinking about the solution. While the exact number of stages may vary depending on the preference of the company, what truly matters is adhering to a structured approach to problem-solving.
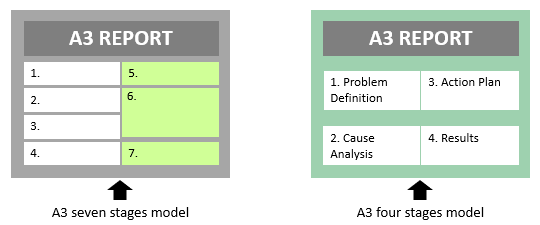
A3 Seven Stages Model
An A3 process is often managed by an individual who should own and maintain the A3 report. This individual takes the lead in steering the process, facilitating team involvement, and preparing the A3 report with team input. One of the most common models for A3 thinking is the seven stages model which is described in the following.
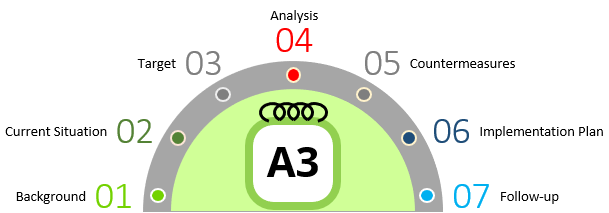
1. Background – The first step is to identify the business reason for choosing this problem or opportunity. In this stage, you need to identify the gap in performance and the extent of the problem.
2. Current situation – The purpose of this stage is to document the current state of the problem. You may need to refer to the process map or go to the Gemba to truly understand the current situation.
3. Target – The purpose of this stage is to define the desired future state. Clearly identify the expected benefits from solving the problem, the scope, and the key metrics that will help measure the success of the project.
4. Analysis – The objective of this stage is to conduct an in-depth analysis of the problem and understand why it’s happening. It might involve tools like the 5 Whys and cause-and-effect analysis, as well as advanced statistical methods.
5. Countermeasures – Countermeasures are the actions to be taken to eliminate root causes or reduce their effects. The team should brainstorm and evaluate possible countermeasures based on the analysis conducted earlier.
6. Implementation Plan – To achieve the target, develop a workable plan to implement the countermeasures. Gantt charts are great ways to manage implementation plans very simply and easily. Once the action plan is finalized, the team should begin working on the activities needed to implement the countermeasures.
7. Follow-up – The final stage involves evaluating the implementation of the plan and the results achieved. Follow-up actions are important to ensure the benefits extend beyond the project’s completion.

A3 thinking is considered to be the practical form of the PDCA model.
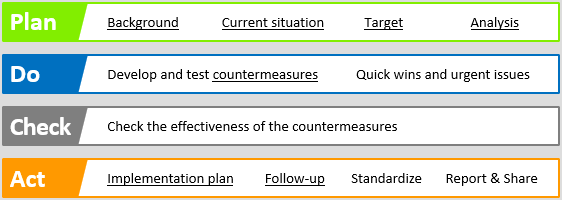
There are many online templates that can be used to manage your problem-solving efforts. One of the simplest and most straightforward ways is to use this A3 problem solving template .
Wrapping Up
A3 thinking represents a logical and structured approach for problem solving and continuous improvement. This approach can be used for most kinds of problems and in any part of the business. Originating from the Toyota Production System (TPS), it has been adopted by many Lean organizations around the world.
A3 thinking not only provides a systematic approach for problem-solving. The development of a continuous improvement culture is at the core of A3 thinking. It has become one of the most popular Lean tools today where people and teams work together to solve problems, share results and learn from each other.
Other Formats
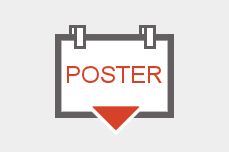
Do you want to use the slides in your training courses?

A3 Thinking Training Material – $18.85
Related Articles
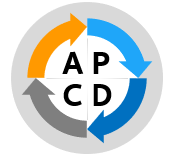
Project Charter
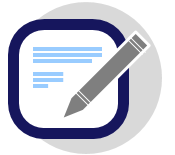
Gantt Chart

Related Templates
A3 Problem Solving
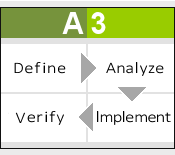
Written by:
CIToolkit Content Team
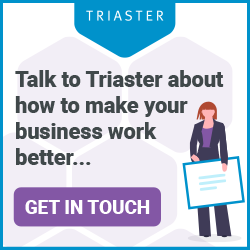
5 fundamentals of the CAPA quality process
The CAPA quality process, in a nutshell, consists of the specific improvements a regulated organization makes to its processes to eliminate defects and non-conformities.
Effective CAPAs are the backbone of your quality management system , acting as the mechanism for fixing problems and optimizing your processes.
Robust CAPA management requires 5 key fundamental areas. Let's dive in and take a look at everything you need to know about the CAPA process.
CAPA meaning
The world of quality management is full of acronyms. SOPs. NCRs. GxP. And CAPAs. So what does 'CAPA' mean?
What does CAPA stand for?
CAPA stands for 'corrective and preventive action'.
As the name suggests, CAPAs are about problem-solving. And it's a two-step process: when something goes wrong, a CAPA is executed to fix ('correct') the immediate issue, then to ' prevent ' it reoccurring with some tweak or improvement that addresses the cause.
CAPA definition
CAPA is defined as a systematic approach used in various regulated industries, including manufacturing, healthcare, and quality management, to identify, investigate, and address problems or non-conformities in products, processes and systems.
The purpose of CAPA is to rectify existing issues and prevent their recurrence in the future.
A CAPA system is therefore a crucial part of the modern quality management system, since quality in general is all about ensuring the integrity and quality of the products and services your company provides.
We can see how important this is when we consider that over half of the causes of a business failure can be attributed to internally generated problems that weren't properly addressed.
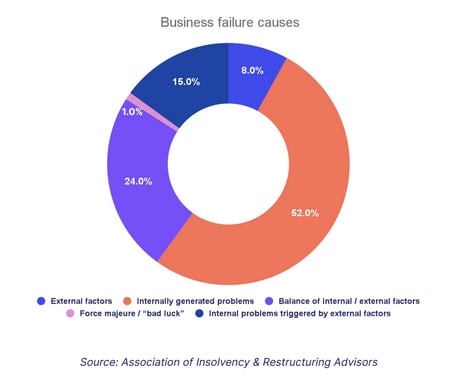
The Shewhart Cycle, more commonly known as Plan Do Check Act, is a classic quality management approach that enshrines CAPA procedures.
In this case, the 'check' and 'act' portions of the cycle are synonymous with CAPAs: systems and processes are checked , problems are found, then those problems are fixed with corrective and preventive actions .
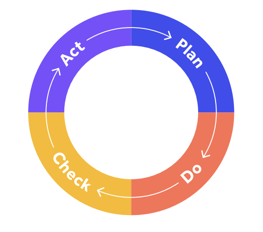
What is CAPA?
What does a CAPA system or CAPA procedure look like in real life, then?
Remember, establishing a CAPA system requires a commitment to quality and continuous improvement. It's an ongoing process that helps you identify and resolve issues proactively, ensuring that your business operates efficiently and delivers high-quality products or services.
And it's not always something businesses get right.
CAPA requirements for medical devices marketed in the United States are laid out in FDA 21 CFR 820.100(a) - and failure to instil proper CAPA procedures is a consistent leading cause for FDA audit failure and the sending of Form 483s as a slap on the wrist.
FURTHER READING: 5 major CAPA medical device requirements
Our recent analysis of Form 483s sent to drug companies in 2022 found a similar pattern, with investigations of discrepancies and failures - a key part of CAPA, as we'll see below - the second-highest cause of Form 483 submissions.
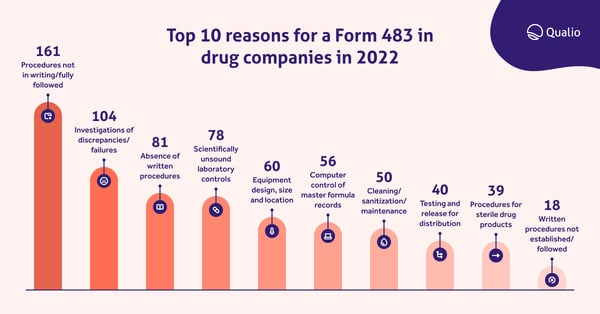
Establishing a CAPA system
A robust CAPA management system needs a coordinated web of activity in place.
Start by determining the key steps and procedures for your CAPA system.
How will issues be reported, investigated and resolved?
What are the roles, responsibilities and accountabilities of the individuals involved in the process?
And most significantly - what reporting mechanisms can you get in place?
You can only correct and prevent faults that you know about, so it's vital that your organization has a system in place for fast, easy reporting that kicks off a CAPA process quickly.
This could be having a designated person(s) on-site for people to report issues to, or better yet an electronic cloud-based form for instant submission from anywhere.
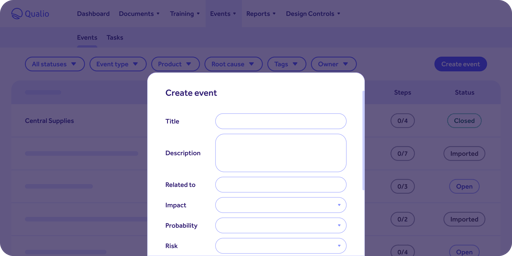
You should proactively look for things to fix, too, so a robust internal auditing program needs to be established. Build a repeatable audit cadence that lets you interrogate key areas of your business and spot weaknesses, bottlenecks, defects and faults to which CAPAs could be applied.
Consider, too, how to keep an ear open to customer complaints. Complaints and complaint investigations are integral to an effective CAPA system, since they provide a source of external data to inform your CAPA processes once your device or drug has hit the market.
RELATED READING: How to build a complaint management system
Any effective CAPA system needs robust reporting, too.
Demonstrating 'improvement' by implementing CAPAs is a key regulatory requirement, cropping up in Clause 10 of Annex SL and, by extension, all modern ISO standards. If an auditor notes some non-conformances in a session, too, they'll expect to see documented evidence of how you've fixed them when they next visit.
A CAPA report is therefore a crucial ingredient to include in your CAPA strategy, since it proves you've effectively treated a defect with clear application of CAPAs.
Lastly, you should have clear targets in mind for your CAPA steps to be applied to.
Where should your CAPAs be applied? There are 4 key areas you should prioritize for your CAPA activity:
1. Facilities & people : equipment, manufacturing environment, etc. 2. Organizational system : documents, SOPs, quality controls, etc. 3. Processes : steps, outputs, handoffs, etc. 4. Product : specifications, integrity, characteristics, etc.
These 4 areas will provide over 90% of your day-to-day operational risks, so it makes sense to apply the bulk of your corrective and preventive actions there.
Tips for CAPA procedures
- Make your CAPAs SMART - that is, specific, measurable, achievable, relevant and time-bound.
- Clearly define roles and responsibilities for each stage of the CAPA process. Assign specific individuals or teams responsible for initiating, coordinating and tracking CAPA activities to completion. This ensures accountability and ownership, encouraging timely resolution.
- Get a mechanism in place for classifying the issues you're addressing. CAPA application should be sensible and risk-based - there's no point throwing all your resources at a minor defect when there's a major fire to fight.
- Link your CAPAs to the severity, impact on quality, and potential risks of the issues they're addressing. This allows you to allocate resources tactically and address critical issues with the highest priority.
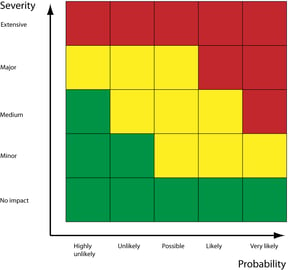
- Make CAPA awareness an evolving part of your company culture with training. Not only should all individuals with CAPA responsibilities be adequately trained, your entire organization should understand the importance of actively reporting issues so they can be fixed. Foster a culture of continuous improvement by encouraging employees to look for and report issues, and even to suggest improvement options themselves. Reward employees that take an active role here. Then ensure you regularly assess and enhance your CAPA strategy to adapt to your evolving organizational needs, such as when new products, processes and procedures are rolled out.
- A final tip is around optimizing your CAPA strategy. CAPA execution needs to be fast, accurate and controlled to have maximum impact and success. Manual or paper-based quality systems block visibility of quality issues and their root causes, making targeted CAPAs impossible.
One of our customers noted this very issue:
To accelerate and simplify your CAPA system and the execution of your CAPA procedures, more and more organizations are turning to CAPA management software .
To provide effective safeguards against regulatory risk, CAPA management is usually included as core functionality within a modern electronic quality management system (eQMS).
At a high level, any effective electronic CAPA system must:
- Let you build bespoke CAPA procedures which address your quality system requirements
- Facilitate data analysis to identify the sources of product quality issues
- Enable your organization to monitor trends for preventive action
- Integrate with other systems and QA processes to assure data quality
- Facilitate statistical analysis and formal failure investigations
- Allow your organization to validate the success of your preventive and corrective actions
LEARN MORE: 8 essential functions your CAPA software must have
With these tips in mind, let's take a look at the 5 fundamental steps of the CAPA quality process.
CAPA steps: the 5 fundamentals of the CAPA quality process
1. detection.
The problem identification and CAPA detection phase requires an appropriate documentation of the issue at hand. The description should be complete, including who, what, when, where, why, and how many.
Moreover, a risk analysis should be performed based on compliance risk. The results of the risk analysis should inform the CAPA timeline. In most cases, low-risk issues do not carry the same sense of urgency as high-risk issues.
2. Investigation & root cause determination
Next, your quality management team should commit to rapid investigation and root cause determination.
There are several methods for conducting root cause analysis, including:
- Brainstorming
- Flowcharting
- Fishbone diagrams
- Affinity diagrams
- Physics of failure
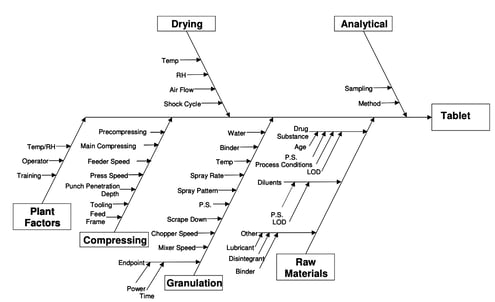
End-to-end traceability is crucial here. You should be able to track, and document, every root cause, change and applicable action step from the beginning to the end of your CAPA process.
RELATED READING: The 9 core elements of a quality management system
3. Proposed corrections
In this next phase, correction and containment should be completed as soon as possible to prevent further disruption.
Your organization should proactively review processes and procedures to identify broader issues. In the case of a product-related issue, field correction and/or recall may be required.
4. Implementation
At this point, long-term corrective and preventive actions work to resolve or eliminate the cause of nonconformity.
A corrective action is an action that eliminates the immediate cause of a nonconformity.
On the flipside, a preventive action eliminates the cause of potential future nonconformity.
RELATED READING: The 4 most common problems with CAPA processes
5. Verification of effectiveness
Finally, you need to validate and verify your corrective and preventative actions' effectiveness. Once a CAPA investigation is complete, determine if nonconformities have been resolved. Did it work?
You should also determine if your corrective and preventive actions haven't created new areas of inconsistencies.
For instance, any changes to your production process that were made to address an issue should also be seen as a new source of potential problems. Monitor your actions closely for a set period of time to ensure no adverse, unintended consequences occur.
Finding the best CAPA software for your company
Quality management issues have an immediate and significant impact on the success of your company. Failure to follow CAPA procedures and identify the root cause of compliance issues can cause repeatable problems at unavoidable costs.
What's more, ineffective complaint handling can jeopardize brand reputation and customer relationships. As a result, purchasing control breakdowns may be linked to unreliable input quality, and speeding through the validation will produce unfavorable results.
This is precisely why an electronic quality management system is a necessity. By adopting the right solution during the start-up or scale-up phase, you can build your organization a strong baseline for effective CAPA, supply chain management, and complaint handling.
Qualio is the first cloud-based electronic quality management system designed for growing life sciences organizations.
Schedule a demo today to learn more about how Qualio can help your organization embed world-class digital CAPA control.

Meg has amassed over a decade of experience as a QA/RA and compliance professional, with a range of cross-functional skills and knowledge spanning from non-profits to medical device start-ups. Meg is Senior Quality Specialist at Qualio, a member of the Qualio+ expert team, and a certified auditor for both ISO 9001 and ISO 13485.
Related Articles
What are the objectives [5 examples] of quality assurance in the pharmaceutical industry, the ultimate guide to pharmaceutical quality assurance, qualio now offers industry-leading high availability.
G2 EQMS VENDOR REPORT 2023
Learn how real eQMS customers rank Qualio vs. our competitors
- Core Values
- Differentiators
- Employee & Consultant Reviews
- Client Reviews
- Corporate Social Responsibility
- Quality Assurance
- Regulatory Affairs
- Clinical Operations
- Commissioning, Qualification, and Validation
- Chemistry, Manufacturing, and Controls
- Expert Witness
- Consulting Projects
- Staff Augmentation
- FTE Recruitment
- Functional Service Program
- Browse Consultant CVs
- Start a Consultant Search
- Join Our Consulting Team
- Insider Newsletter
- White Papers
- Case Studies
Corrective and Preventive Action (CAPA): The Definitive Guide [2024]
“Insufficient corrective and preventive action procedures” has consistently topped the list of most common FDA inspectional observations within the medical device industry since the fiscal year 2010.
Its prevalence as the top problem year after year makes it clear that many device companies have issues, both known and unknown, within their CAPA programs.
While the immediate compliance threats are obvious, less so are those that leave companies vulnerable to serious quality system issues that can grow and metastasize under the radar of their quality management system, putting both patients and their businesses at risk.
This guide tackles CAPA from a slightly different perspective than most are used to seeing in industry publications and seminars.
We’ve gathered insights from the quality and compliance experts who have seen it all and fixed it all firsthand. In addition to exploring the solutions that have proven to be effective in the field, we’ll also examine one, if not the , most pivotal component of CAPA: root cause analysis .
Table of Contents
Use the links below to jump around this guide.
CAPA 101: The Basics
What the fda expects from your capa process, root cause analysis: a practical perspective, an informed approach to addressing and preventing "human error", determining when capa is appropriate, how capa interfaces with your quality management system, the anatomy of an effective and compliant capa form, an adaptable capa model you can use, common capa problems to avoid, the value an expert third-party consultant can bring to your capa program.
- Get Expert Assistance
Since this guide is comprehensive, we suggest downloading our PDF version, which you can access, save, and use below.
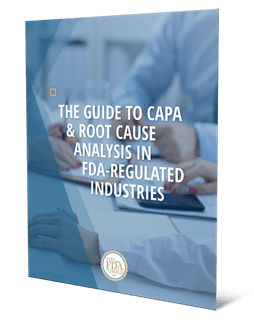
The Guide to CAPA & Root Cause Analysis in FDA-Regulated Industries
Download the full white paper version of this guide below. It offers everything we cover here and more in a handy PDF you can use to assess and enhance your CAPA program.
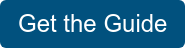
Meet the Contributors
Watch our free CAPA webinar
What is CAPA?
According to the U.S. Food and Drug Administration (FDA) , corrective and preventive action aims to collect information, analyze information, identify and investigate product and quality problems, and take appropriate and effective corrective and/or preventive action to prevent recurrence.
Verifying or validating corrective and preventive actions, communicating corrective and preventive action activities to responsible people, providing relevant information for management review, and documenting these activities are essential in dealing effectively with product and quality problems, preventing their recurrence, and preventing or minimizing device failures.
Corrective and Preventive Action (CAPA) was first formally introduced by the U.S. Food and Drug Administration (FDA) in 2006 as a component of the Quality Systems Guidance. This guidance would go on to form the basis of the ICH Guideline Q10. Since then, it’s found its way into the EU GMP Guide, laying out the CAPA process within the pharmaceutical space.
For medical device companies, CAPA is addressed in ISO 13485, which, unlike Q10, divides the concept into its two concepts: “Corrective measures” (addressed in Chapter 8.5.2) and “Preventive measures” (addressed in Chapter 8.5.3). Despite separating these processes, both must be documented and evaluated to demonstrate improvement and preventive action, making CAPA the practical process by which both are united. With this in mind, we’ll treat it as one concept here.
What is CAPA used for?
A CAPA procedure addresses deviations or problems that have already occurred and puts measures in place to avoid future deviations or problems. This entire process of analyzing errors, deviations, and their effects can— and should —be carried out as a component of broader risk assessment rooted in a well-defined and documented risk management program.
CAPA-triggering deviations can originate from a variety of sources within a quality management system, such as internal audits, customer feedback, or in the most serious cases, safety or security-related incidents that result in faulty products due to inadequate controls.
No matter why or where CAPA is initiated, it should always begin by identifying and taking immediate actions to stabilize the situation and limit its further effects. This is where an honest and accurate assessment of its severity is absolutely crucial. In the worst-case scenarios, this could mean an immediate halt to the production and distribution of all impacted products.
What does a typical CAPA process look like?
In most cases, a CAPA is executed much like a typical PDCA (Plan-Do-Check-Act) cycle:
- Begin with a detailed problem description by accurately evaluating and documenting it. Similar to the planning stage of the PDCA cycle, all CAPAs should start by describing the problem in detail, ensuring everything is documented accurately.
- Perform a root cause analysis. Once the problem is clearly defined, determine its root cause by performing a thorough root cause analysis.
- Implement, verify, validate, and document necessary corrective and preventive measures . This change should seek to remedy the root cause of the problem and ensure no further problems will occur. This could be a change in the production process, a training improvement, or another transformative measure.
- Check for effectiveness and evaluate success. Finally, the effectiveness and success of the measures implemented is checked and evaluated accordingly. Like with the “Act” phase of PDCA, this justifies whether and why the CAPA process was successful. If the CAPA process was not or only partially successful, another CAPA process must be initiated. A successful CAPA process may result in a re-evaluation or addition to the risk analysis.
The diagram below offers a simplified look at the general steps of CAPA. An adaptable model for CAPA is offered later in the paper.
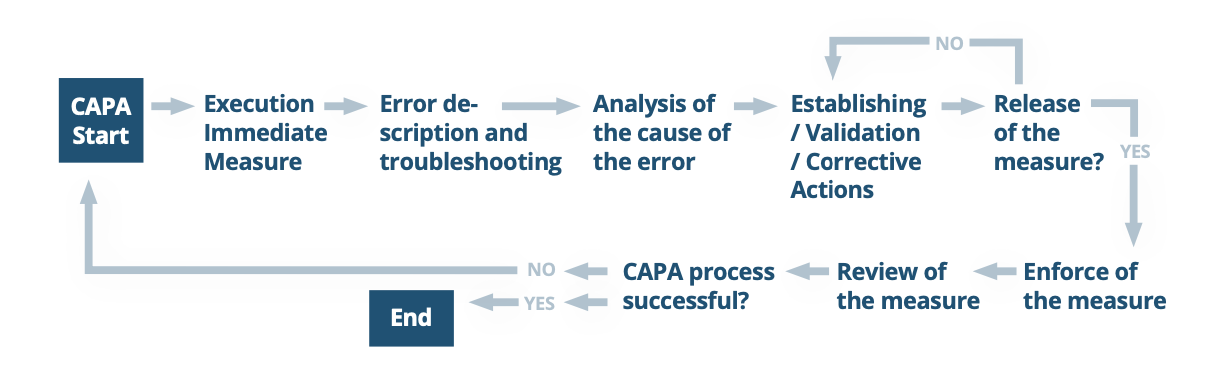
Given the numerous inspectional observations citing insufficient established CAPA procedures, it’s worth revisiting what regulators expect to see from your process.
In a 2014 presentation , FDA’s Joseph Tartal described the basics of effective corrective and preventive action—a resource every company should use to evaluate against their own processes. Among many important points, one stands out as particularly useful when ensuring your procedure meets regulators’ expectations:
“Manufacturers should consider that their corrective action and preventive action documentation can demonstrate to FDA that the manufacturer’s quality system is effective and enables the manufacturer to identify problems quickly and implement effective corrective and preventive actions (or not).” — Brian Dense
In addition to helping manufacturers meet the broad expectations for effective CAPA, FDA also makes public its own inspectional guide , which lays out the specific objectives for investigators when evaluating a device company’s CAPA system and related documentation.
We’ve summarized its main points below.
This should serve as your ultimate preparedness checklist when evaluating your CAPA processes for compliance with FDA regulations.
Verify that CAPA system procedure(s) that address the requirements of the quality system regulation have been defined and documented.
Determine if appropriate sources of product and quality problems have been identified. Confirm that data from these sources are analyzed to identify existing product and quality problems that may require corrective action.
Determine if sources of product and quality information that may show unfavorable trends have been identified. Confirm that data from these sources are analyzed to identify potential product and quality problems that may require preventive action.
Challenge the quality data information system. Verify that the data received by the CAPA system are complete, accurate, and timely.
Verify that appropriate statistical methods are employed (where necessary) to detect recurring quality problems. Determine if the results of analyses are compared across different data sources to identify and develop the extent of product and quality problems.
Determine if failure investigation procedures are followed. Determine if the degree to which a quality problem or nonconforming product is investigated is commensurate with the significance and risk of the nonconformity. Determine if failure investigations are conducted to determine the root cause (where possible). Verify that there is control for preventing the distribution of nonconforming product.
Determine if appropriate actions have been taken for significant product and quality problems identified from data sources.
Determine if corrective and preventive actions were effective and verified or validated prior to implementation. Confirm that corrective and preventive actions do not adversely affect the finished device.
Verify that corrective and preventive actions for product and quality problems were implemented and documented.
Determine if information regarding nonconforming product and quality problems and corrective and preventive actions has been properly disseminated, including dissemination for management review.
⚠️ A few action items to consider:
- Evaluate your current CAPA process on the criteria listed above.
- Highlight and remediate any gaps that exist between regulatory expectations and current processes.
- Follow up on all changes with the necessary documentation, training, or other actions needed to implement, support, and maintain those improvements.
- Note any gaps or improvements that require third-party assistance from a qualified CAPA professional and contact a firm to pair you with the appropriate resource.
Need expert assistance with any of these considerations? Get in touch with us to discuss the best way to close gaps, ensure compliance, and enhance your CAPA program.
While much attention is given to the tools, techniques, and methodologies for “extinguishing the problem at the source,” much less attention is given to the fact that none of them will be effective if they aren’t implemented properly.
The factors for proper use boil down to two fundamentals every organization should immediately evaluate against and enhance if room for improvement exists:
Having the right team(s) in place to collect data and conduct the investigation in order to determine what factors should and shouldn’t be included in the analysis
Crystal clear communication with the proper measures in place to minimize bias and the role of inter-organizational politics in obstructing the free and open exchange of facts and ideas
Without these two fundamentals, even the best root cause analysis process will likely fail to properly identify and address the true root causes of the problems affecting your products and quality system.
Once a foundation is established on these two important pillars, turn your attention to the major challenges companies face in conducting root cause effectively.
- Challenge #1: Devoting too little time to investigating and determining the root cause of an issue
- Challenge #2: Simply restating the problem statement as the root cause of the problem
- Challenge #3: Not having a reliable set of tools and methods for carrying out an effective investigation
- Challenge #4: Failing to reference the tools you do use in your CAPA procedure, thereby opening the door to regulatory scrutiny
Since each company faces its own set of challenges, prescribing a universal set of solutions is impossible. A solution for one organization can end up introducing more problems when applied the same way in another.
It’s important to reiterate that this guide is intended to reveal the realm of possible solutions and improvements available to you—not compel you to use one or another. Given this frame, let’s explore a topic that’s familiar to many, but provides the critical foundation from which action is taken: root cause analysis .
“In many organization, politics are allowed to influence the CAPAs simply because there are too many people involved in the approval process—approval to actually open a CAPA, or approval to finish one. Very often there are too many people, or the wrong people, in the approval process. I’ve seen real problems get swept under the rug because somebody won’t approve the effort to go forward with it. I’ve also seen good solutions get shot down on real problems, because somebody didn’t want to spend the money or the time. I would be cautious about adding too many levels and too many people to the process.” — Brian Dense
A Brief Overview of Root Cause Analysis Methodologies
There are a number of reliable methodologies for analyzing root cause, however, not all are equally effective in every scenario. Applying the same methodology to every investigation can fail to go far or wide enough into the problem, undermining the entire effort.
While each methodology deserves to be thoroughly understood by those putting them to use, we’ve summarized the key takeaways for three of the most common models to help you choose the right one for a given scenario.
Fault Tree Analysis (FTA)
This deductive procedure is used to determine the various combinations of hardware and software failures and human errors that could cause undesired events (referred to as top events) at the system level.
The generic example below was developed for sixsigmastudyguide.com's FTA explainer:
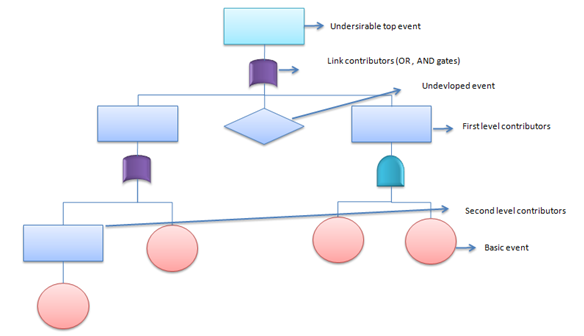
- Advantages: FTA values the judgment of experts from many disciplines and provides a common perspective on a given problem.
- Disadvantages: FTA relies on multiple expert opinions and judgments at various stages, making it prone to inaccuracy and bias. For larger systems, the quantitative analysis might be so complex, it requires computer algorithms to accomplish.
- Understanding the logic leading to a “top event” or undesired state
- Demonstrating compliance with system safety and reliability requirements
- Prioritizing multiple contributors which led to a top event or undesired state Recommended Applications
- Analyzing and forecasting system reliability, maintainability, and safety
Fishbone Diagram
Also called a “cause and effect” or “Ishikawa” diagram (among others), a fishbone diagram is a visual tool for looking at cause and effect. A problem or effect is displayed at the “head” or “mouth” of the fish, and possible contributing factors are listed on the “bones” under various cause categories. These models work best when the “head” of the fish contains a very detailed problem statement. This helps eliminate the scope creep of the team’s discussions. What happened? When? Where? These can help narrow the focus to solve the problem.
Here's an example pulled from tulip.co's explainer guide on the concept:
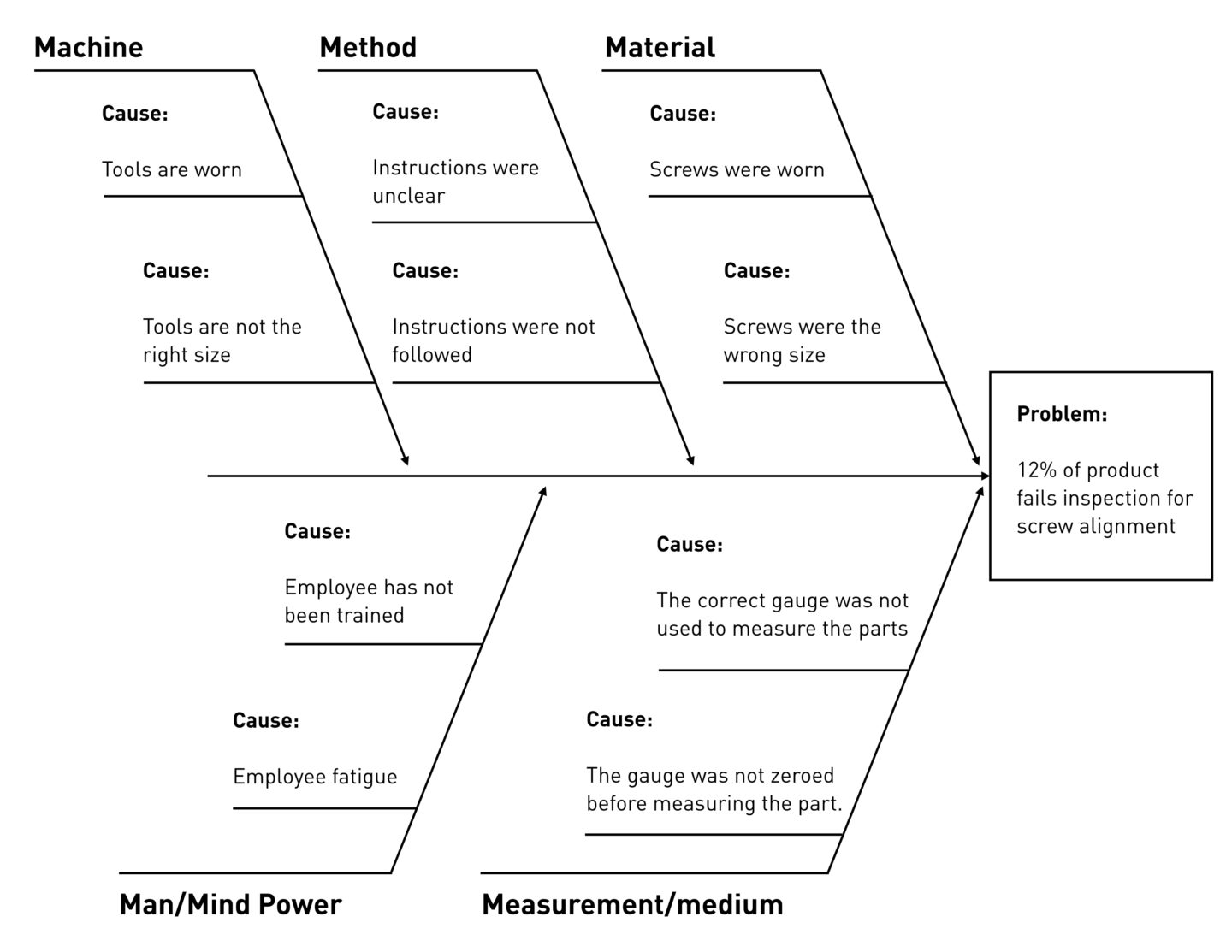
- Advantages: Fishbone diagrams are particularly useful for organizing potential causes, helping teams think through causes they might otherwise miss, and providing a living document that shows the status of all potential causes and whether they have been proved, disproved, or acted upon.
- Disadvantages: Fishbone diagrams are by nature a divergent approach to problem-solving, so they make it possible for teams to expend a lot of energy speculating about a potential cause that may have no effect on the problem.
- Directing a team to focus on identifying all possible categories and consider alternative causes
- Refocusing a team on the causes of a problem rather than the symptoms
- Improving product design
- Preventing quality defects
- Identifying potential factors causing an overall effect
The 5 Whys is arguably the simplest technique for root cause analysis. It can be very effective when answers come from people with hands-on experience in examining the process. It is remarkably simple: when a problem occurs, you drill down to its root cause by asking “why?” five (or more) times. Then, when a countermeasure becomes apparent, you follow it through to prevent the issue from recurring.
- Advantages: This is essentially a simpler form of a fault tree analysis, making it a straightforward process when investigating specific accidents instead of chronic problems.
- Disadvantages: Results can be non-reproducible and inconsistent. For instance, two teams analyzing the same issue may reach a different solution. It also leaves the door open to stopping short of reaching the true root cause.
- Resolving simple or moderately difficult problems
- Resolving issues involving human factors
- Resolving issues where statistical analysis is not needed or possible
The Importance of Cross-Functionality When Conducting Root Cause Analysis
Today, it’s common for organizations to place a high value on taking personal responsibility for quick problem resolution. While this value is rooted in good intention, placing the focus at least in part on speed must be done with extreme caution to ensure root causes are fully identified and resolved.
Speed, in this case, is a risky substitute for thoroughness. When this risk is ignored, the incentive to kick the can down the road to get it cleared and closed as fast as possible begins obstructing your ability to conduct a thorough investigation and analysis. Rather than resolving problems, they’re simply moved from one function to another in a dangerous game of hot potato.
Processes that give rise to problems are rarely localized to a single department or function. In many cases, the more complex a process is, the more functions it crosses. To truly resolve problems at their root—quickly and completely—a cross-functional group consisting of stakeholders from all inputs, work tasks, and outputs involved must be established to solve the problem from every angle.
To be reliably successful, root cause investigation and analysis must start by defining the process in which an issue (or issues) have arisen from one end to the other—evaluating all inputs, work done, and outputs being handed off to the next process. To do this effectively, knowledgeable representatives and owners from all functional areas must work together, including engineering, sales, quality, regulatory, etc. .
Cross-functionality is especially important given that the point at which a problem is detected is rarely where the root cause truly lies. The further upstream you need to travel to find it, the more you can expect to rely on the knowledge of other functions you’re led to when tracing the principal cause. This is where communication and cooperation between functions become critical. Without a cross-functional approach, assumptions made by one function conveniently replace the informed knowledge of another—leading to dangerous gaps in understanding how other steps in the process are impacted.
Creating a cross-functional team may slow down the process and ask more of those involved, but this added investment is often returned in the quality of the results it achieves.
- Evaluate the current methodologies and tools utilized when investigating the root cause.
- Determine whether current processes suffer from the challenges described and consider ways to overcome them.
- Determine how well current processes ensure the best methodologies and tools are selected from diverse options based on applicability to specific goals.
- Adjust processes as necessary to include currently unused methodologies and tools given staff are fully trained and confident in using them.
- Consider how prior problems could have been solved better if addressed with another methodology or tool and prepare to employ them if similar issues arise in the future.
- Evaluate your current root cause analysis process on its degree of cross-functionality.
- If needed, revise this process to incorporate more stakeholders from other functions.
- To accelerate problem resolution, establish the team’s assignment and timeline up-front.
Genuine human errors do happen, but they’re cited far more frequently than they should be. In truth, most problems that appear to be caused by human error— especially those that occur multiple times—are actually rooted in processes or systems that when left unchanged, will keep producing the problem despite the convenient band-aids often placed over them.
When human error is identified more frequently than it should be expected to happen, it signals to investigators that problems aren’t being investigated thoroughly enough, thereby shifting them into problem-hunting mode and opening your quality management system up to even greater scrutiny.
But what about the rare instances where one-time errors are made by otherwise well-trained personnel following well-defined processes? A moment of inattention due to a passing distraction can lead to serious problems. In these cases, the human error classification may be justified after a thorough investigation reveals nothing in every possible place there is to look. Again, this conclusion should never be jumped to as a convenient way to avoid the important work of problem-solving (as it often is). It should only be considered as a viable justification when every other possible cause has been exhaustively explored and eliminated.
Given this caveat, it’s helpful to arm yourself with a model for analyzing what might appear to be human errors in order to determine whether actions (or inactions) were deliberate or inadvertent. The outcome can help you determine whether or not human behavior really is to blame as well as where you might expect to find a problem elsewhere (such as inadequate training, poor SOPs, etc.) if the root cause appears to be less human than you initially thought upon further analysis.
Enter the Skills, Rules Knowledge/Generic Error Modeling System illustrated below. It’s relatively simple but offers a reliable way to tease out genuine human errors from other problems while pulling real human errors apart even further to reveal their motivating factors.
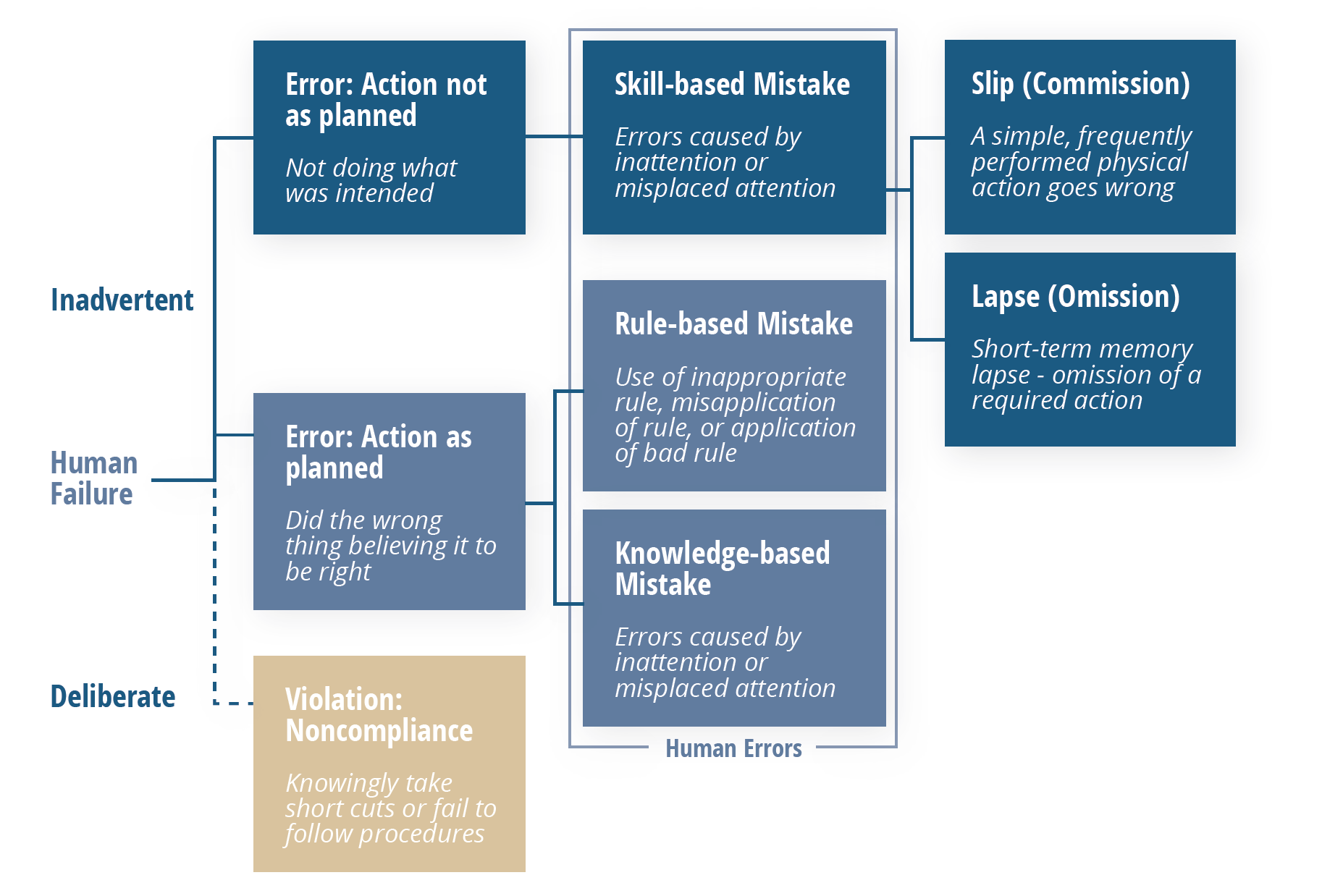
Following this model, errors that are shown to be “inadvertent” can be considered genuinely “human”, which then fall into one of three categories: skill-based, rule- based, or knowledge-based mistakes.
Those that are skill-based can be broken down one more time, into either a slip or a lapse. Both of these point to the same root cause: a lack of attention, which manifests itself in two different ways: momentary memory loss or a routine action that wasn’t performed.
Once more, it’s important to note that these types of errors should not be happening frequently. The vast majority of problems that appear to be a human error at first should lead you elsewhere upon further analysis.
Errors shown to fall into one of the two other categories should be viewed through a different lens. In these situations, processes—particularly related to training and oversight should be scrutinized as contributors as explained in the breakdown below.
Knowledge-based Errors
- Were they tasked with doing too many things at once?
- Is that department under-resourced?
- Was this individual’s supervisor aware that the person is multitasking beyond their limit?
Rule-based Errors
- Did they receive insufficient practice in training?
- Did practice actually reflect the operations they were performing on the floor?
- Does the procedure specify the details to the degree they need to be explained in order to be performed correctly?
- Conduct an objective assessment of your internal problem-solving processes (ideally with the help of an experienced third party) and remediate accordingly.
- Replace metrics that establish problematic incentives with goals focused on long-term trending.
- Explore ways to improve problem-solving within your QMS to reduce backlogs while thoroughly investigating issues.
Many companies suffer from either overusing or underusing their CAPA program— each presenting its own set of risks. Overusing CAPA typically results in a never-ending backlog of open projects, which prevents issues from being resolved in a timely manner, thereby allowing them to worsen while in queue. Underusing CAPA risks letting issues fly under the radar, which again enables them to grow and become harder and more expensive to fix when they’re finally detected. It would be reckless to prescribe hard-and-fast rules for when or when not to open a CAPA, but for those struggling with over or under-use, some general advice may be useful for taking immediate initial steps to correct yourself and set the stage for gradual improvement.
- Ramp up or scale back your CAPA program to deal with systemic or potentially systemic issues first. While not every problem deserving of a CAPA should be “systemic” in nature, these types of problems are typically a great fit when addressed with CAPA.
- Did the incident or event result in injury? If so, CAPA should obviously be mandatory.
- Has the issue, incident, or event occurred multiple times? If so, you likely have a system problem on your hands, which should definitely be handled through CAPA.
- Can the issue be managed effectively another way? “Effectively” is the keyword here. This question shouldn’t be used as an excuse to not open a CAPA if it’s necessary, but if other methods are worth considering, they should be explored.
- Does the issue appear to be critical following a risk assessment? High-risk issues like those deemed to be “critical” should be addressed through a formal CAPA.
Use creative trending techniques. Despite no hard-and-fast criteria for CAPA, quality system expert Brian Dense explains that trending data can be used to make informed decisions about the types of problems CAPA should be considered for while also reducing the amount of work involved.
“If companies did appropriate trending, they could actually combine and condense a lot of the work they’re doing in their CAPA program. You may have five different corrective action efforts going on at once, but you might have five problems that are each only slightly different. After investigating, you might discover they all have the same root cause. At that point, you should consider moving all of these CAPAs into one. Close the others, so that you’re not spending all this time worrying about a record. Have good procedures, with clear rationale. Give a good, solid justification for why you’re doing what you’re doing. Close the record, and put your focus on the best one to implement the corrective action. Trending helps companies reduce the amount of work they actually have to do within their CAPA programs.” — Brian Dense
- Consider establishing a system for recording internal CAPA trends in order to better use your program to address appropriate issues.
- Consider using general questions to better screen issues resulting in a CAPA.
Corrective and preventive actions should always be utilized when necessary throughout any area of your organization. Given this very important point, it’s also helpful to know which systems typically give rise to the problems CAPA is used to solve (and prevent). While again, these are by no means the only areas to expect issues to occur, it can help you prioritize regular monitoring and realize the true scope of problems by identifying their early indicators.
- Nonconforming Product: While one-time nonconformance issues aren’t necessarily worthy of a CAPA, systemic issues almost always are. Confident decisions here rely on your process for analyzing nonconformance data. This is one area where effective analysis can help you be proactive rather than reactive to addressing situations.
- Complaint Handling: Complaint handling processes are critical from FDA’s perspective. Investigating complaints requires a thorough process very similar in concept to a CAPA process. It should define the issue, determine root cause, and establish a plan to address and correct the situation. When this process is effective, CAPA should mainly be reserved for systemic issues. Again, this requires monitoring and analyzing to know when in fact complaints are being caused by an underlying systemic issue.
- Production & Process Controls: In most cases, product issues identified during the production process should be captured as nonconformances—the initial way issues with out-of-spec products are addressed. If the nonconformance is systemic, CAPA will likely be necessary. In other cases, you may identify issues with production-related processes. These require smart corrective and preventive action. While many of these can be addressed via your change-management process, again, CAPA should be considered when issues are revealed to be systemic.
- Supplier Management: Supplier issues that are beyond the scope of a nonconformance—again, mainly those shown to be systemic, should be dealt with either via internal CAPA or a supplier corrective action request (SCAR). Issues elevated and floated back to the supplier should be closely tracked and documented.
- Audits: While audits are typically seen as straining and time-consuming, they can be great opportunities for making improvements and discovering potential issues before they become problems. Once again, any systemic issues revealed during an audit should be prime candidates for a CAPA investigation.
In addition to being fully compliant with ISO 13485:2016 and 21 CFR 820.100, your CAPA procedure must also be effective. This means it has to be clear and functional for its users, the majority of whom likely aren’t CAPA experts.
We've outlined the high-level components of a CAPA form below. Download our accompanying white paper for more detail into each.
- Date of initiation
- Cross-reference number
- CAPA source
- Description of CAPA issue
- Investigator assigned and target due date
- Investigation of Root Cause
- Containment of nonconforming product
- Correction(s)
- Corrective action plan/target deadline for implementation
- Preventive action plan/target deadline for implementation
- Corrective and preventive actions implemented
- Plan for Verification of Effectiveness
- Verification of Effectiveness
- Signature and Closure Date
While CAPA doesn’t lend itself to a universal model or set of procedural steps, the high-level steps presented below offer a dependable baseline from which to compare your current process, build the foundation of a new one, or adjust to improve its effectiveness in correcting and preventing problems.
1. Create and Submit a Request
Begin with a request outlining the possible causes and probable sources.
“Do you have a document that describes how to request a CAPA? You need to have a way for personnel to approach the quality group and provide the critical information needed to request this.” — Larry Stevens, RAC
2. Review the Request Appropriately
CAPA request review should be handled by a Quality Manager or Quality Review Board to determine if it’s warranted. Ideally, a QRB should meet regularly to review CAPA requests and other open quality matters. If rejected, the rationale must be documented in case the issue resurfaces. If initiated, it should be assigned a unique sequential ID number and moved forward.
“Requests need to be documented and reviewed within a certain timeframe. If it’s rejected, that rationale needs to be documents and placed where requests are filed. Make sure you can justify these decisions on a risk basis. If you do open a CAPA, it needs to be uniquely identified and given a CAPA owner—typically the person who requested it who takes responsibility for moving it forward.” — Larry Stevens, RAC
3. Finalize Sources and Build Your Team
Identify all personnel, processes, procedures, and functions that could be involved with the CAPA and document in full. Create a team responsible for conducting the investigation and creating the action plan. Ensure your team is cross-functional and inform them of their roles in the investigation.
“Create a cross-functional team that will meet on these matters. Any individual CAPA may have a team of anywhere from three to five (or more) people. The CAPA owner, then, will ensure the members of the team understand what they’re doing and hold them accountable to the action plan that was created, documenting the progress as it evolves.” — Larry Stevens, RAC
4. Identify Immediate Corrective (and Other) Actions
Detain nonconforming products or materials. Take any other immediate steps to correct glaring problems and document in full.
“CAPAs dealing with nonconforming products often require quarantining those products and getting them out as an immediate step. Other types of glaring problems might be an employee incorrectly assembling a piece of equipment. That needs to be fixed right away while analyzing the reasons why that problem happened.” — Larry Stevens, RAC
5. Investigate and Record Findings
The cross-functional team should conduct a thorough investigation. Very importantly, the degree of effort, resource investment, and documentation should correspond to the level of risk for the given problem.
“A good record of your investigation should be generated. And please tell your engineers, or whoever is writing this that they should not be writing it for other employees to read. It should be written for FDA or outside auditors to read. Put enough detail into it so it doesn’t raise more questions. A “lack of training” resulting in “additional training” only raises more questions. What additional training was done? Who did it? How was it documented? These reports should be very detailed and written so that someone reading it gets the full story. If you give that document to FDA and the details aren’t there, you just told them you didn’t do anything.” — Larry Stevens, RAC
6. Determine Root Cause
Select an appropriate analytical approach and use it to arrive at the root cause of the CAPA. Remember that effective action plans require accurate analysis, so this step is absolutely critical.
“As part of that analytical procedure, you need to identify the tools you’ll use for root cause determination and create a formal document that identifies the root cause. This is a critical step in defining your action plan.” — Larry Stevens, RAC
7. Develop, Execute, and Implement Your Action Plan
Define and document the required action steps for correcting the issue now and preventing it in the future. Once documented, assign roles and responsibilities to your team and conduct the action steps. Common actions include updating procedures, reworking a process, adding inspections, training, supplier changes, manufacturing or storage changes, policy changes, etc.
“All of these actions should be well-documented and managed by the CAPA owner.” — Larry Stevens, RAC
8. Review, Approve, and Verify Effectiveness
Once finished, the Quality Manager, or ideally, the QRB conducts a review to ensure the process was completed exactly as described. Once reviewed, the Quality Manager or QRB certifies the CAPA was carried out correctly. Then, a set of requirements must be established to prove that the CAPA plan was effective at correcting and preventing the problem. Lastly, verification requirements must be validated to ensure they were met and the issue was resolved.
“This is something FDA looks at in determining the efficiency and effectiveness of your CAPA program. Are CAPAs reviewed on a regular basis and are they closed in a reasonable amount of time? Now, occasionally, a CAPA may extend to weeks or months for the effectiveness check. So, maybe there’s a provisional closure pending the completion of that check—showing everything you needed to do is essentially done.” — Larry Stevens, RAC
- Importing the 8D problem-solving model: You’ll notice that the process laid out above positions verification after implementing corrective and preventive actions. This is often found to be flipped in CAPA procedures, specifically when the process is derived from the Eight Disciplines (8D) methodology. While this system is commonly used among quality engineers in the automotive industry, its import into the device world puts it at odds with regulatory demands both under FDA and ISO regulations. In short, verification of effectiveness must be conducted after those actions are implemented.
- Unreasonable timeframes and deadlines: Another common problem is a tendency to use short, arbitrary timeframes for completing activities in an effort to convey a sense of tight control. While the logic here is simple—tight control looks compliant—timeframes set in a vacuum are a recipe for disaster when they can’t be met. In this case, a procedure that can’t be carried out as written can be even worse than not having a procedure in the first place. By design, it’s set up to fail.
- Feedback loops: Sources of information are incredibly important in just about any procedure. Misaligned inputs mean missing information. To ensure your inputs are aligned, identify the various processes that have worked for revealing root causes in the past. Discuss these matters with each of the stakeholders and write out a process in flow chart form. With this in hand, a procedure can be written or updated with verbiage, steps, and sections for responsibilities, purpose, scope, etc.
- Political influence: Problems caused by political dynamics can be particularly insidious and difficult to address within an organization. While endless white papers could be written on the effects of ego, power, and personalities, detecting their influence on your CAPA program is often relatively simple: Are too many people touching it? Overcommitting staff in the approval process, in particular, can be a clear signal that problems may be getting swept under the rug—or conversely—the program is being overused. Politics are also usually at play when viable solutions get turned down for a myriad of reasons. In general, the remedy is having the right people—and the right number of people—at each level. If one step feels bloated, it typically is.
We’d like to leave you with a well-stated perspective on the value of partnering with quality systems experts when establishing or improving processes, procedures, and more.
“I’ve spent thirty years working in the industry and there’s nothing in medical device manufacturing quality systems I haven’t touched one way or another—most of it many times over. When it comes to the value of an effective, knowledgeable consultant, there’s real fresh perspective, untainted by the, ‘we don’t do it that way here.’ Consultants come in from the outside and they’ve seen a million ways to do it. They’re adaptable to help you develop a process that best fits that organization, rather than just something that’s been 'bandaid-ed' over the years and never really was made efficient. I’m overusing the word politics, but and they come in with no politics. The consultant has no ax to grind with any department. You don’t have any fighting between, or power struggles, between functions because the consultants coming in, and he just wants to give them the best answer.” — Brian Dense
4 Ways Regulatory Compliance & Quality Assurance Consultants/Contractors Offer Unique Value and Cost Effectiveness
While some circumstances clearly underscore the need for outside expertise, the value of engaging a consultant, both financially and operationally, may not always be apparent. To avoid wasted time and budget—and potentially serious quality and compliance problems that could otherwise be avoided with the help of an experienced consultant, we’ve summarized a few of the major ways companies realize the benefits of bringing in an expert.
1. Answering complex regulatory questions and navigating new regulatory territory
While new regulatory challenges impact both drug and device companies, the device industry, in particular, is contending with sweeping new requirements on top of an increasing number of combination products that present complex regulatory issues of their own (regulatory authority jurisdictions, pre-market submission types, clinical trial design, multi-center review, etc.).
Third-party experts who specialize in specific domains are very often relied upon to step in and help internal teams navigate these complex areas.
The benefit, in this case, isn’t lost when the consultants leave. In addition to leading audits and conducting remediation and revision projects to bring a company into compliance with new requirements, these individuals offer unique and often indispensable training resources that give internal teams the insight needed to implement and maintain new processes, procedures, and systems well after the consultant’s work is done.
2. Preventing the costs of enforcement and its expensive aftermath
Increased regulatory compliance enforcement over the past few years has led to an explosion of new codes while underscoring the importance of putting effective compliance safeguards in place. The costs of these preventive measures are almost always far less than the expensive consequences of enforcement action.
In addition to the disruption and costs of an investigation itself, resulting settlements, subsequent multi-year reviews, effectiveness audits, and related litigation from shareholders and plaintiffs can all lead to massive combined expenses that pale in comparison to effective prevention measures.
Third-party consultants can provide objective assessments through robust quality system auditing to evaluate the key areas that come under regulatory scrutiny in areas such as GMP, GCP, GLP, Vendor/Supplier Management, Pharmacovigilance, and Data Integrity. These measures, when conducted routinely by unbiased outside experts, can be invaluable in preventing quality system issues from developing into system-wide problems that can have enormous implications, both financially and otherwise.
3. Avoiding the practical challenges of hiring from a small talent pool
For most small or medium-sized companies, hiring high-salary internal regulatory compliance staff is simply unfeasible from a business perspective. Even for large firms, finding the top talent to fill these positions can be incredibly challenging. The relatively small pool of QA/RA talent creates intense competition for skilled personnel.
With the regulatory environment becoming increasingly globalized, it can be difficult for in-house regulatory departments to keep up with various regulatory requirements and changes. Third-party experts can achieve harmony between disparate sets of requirements by conducting integrated regulatory assessments against national requirements from multiple jurisdictions.
4. Bringing industry best practices and standards to your processes, procedures, and systems
Third-party consultants encounter a variety of challenges working in the field, and thus, develop a variety of solutions to address them. This gives them a very unique perspective into what works best when addressing a certain problem or preparing for new development.
In general, most companies like to know what other companies are doing to handle similar issues. While consultants are obviously bound by contract not to reveal specifics, they’re expected to use their experience when developing best practices and standards to bring to each organization they work while also adding the scale and bandwidth needed to augment internal teams.
Consider the Costs
For many companies, seeking outside help from third-party experts can provide overall greater value compared to doing all regulatory work internally. While per- hour billing rates may initially appear high, the total financial picture can be one of cost savings when consultants are able to provide an ROI on overall efficiency versus the alternative.
- Effective consultants are valued for their ability to complete work quickly and without rework. This factor on its own is often enough to realize cost savings. Consultants who have conducted the same work many times and aren’t affected by the distractions of daily tasks that internal personnel are can often perform tasks far faster. Of course, consultants can only perform fast, effective work when the goals of the project are well-defined and organized ahead of time. This, in addition to ensuring a consultant is hired for their expertise rather than their billing rate are the two major factors that maximize efficiency while getting achieving the goals of a project.
- Companies can lower overall costs by carefully choosing the types of projects and processes that they outsource. While just about any situation can warrant the added assistance of a consultant, consider those that require a high degree of specialization and/or those that are conducted on a periodic or project-based frequency. As FDA-regulated manufacturers continue to compete for top talent in a globalized market while navigating a more complex regulatory environment, regulatory compliance and quality assurance consultants will continue to offer valuable pathways for planning and completing projects quickly, reliably, and cost-effectively.
Join the thousands of companies executing their projects with The FDA Group.
The FDA Groups helps life science organizations rapidly access the industry's best consultants, contractors, and candidates. Our resources assist in every stage of the product lifecycle, from clinical development to commercialization, with a focus in Quality Assurance , Regulatory Affairs , and Clinical Operations .
Our auditors can perform a detailed assessment of your existing quality systems and processes to highlight problem areas, and recommend and optionally implement improvements to build quality systems that are appropriate for your company’s stage of development. We can assist you with all aspects of compliance as they impact your product, including GLP, GMP, QSR, and GCP.
The FDA Group also specializes in planning and conducting comprehensive remediation projects, Our team of former FDA and industry professionals works hand-in-hand with regulated manufacturers to uncover the root cause of compliance issues, remediate them, and implement the necessary measures to safeguard your reputation for quality both now and in the future.
With over 2,500 resources worldwide, over 225 of whom are former FDA , we meet your precise resourcing needs through a fast, convenient talent selection process supported by a Total Quality Guarantee. Get direct access to the specialized life science talent you need to bring products to market and keep them there. Whether you’re looking for consulting or project support, full-time contract, contract-to-hire, or direct-hire talent, we rapidly identify the right resource the first time.
Learn more about our services by functional area:
- Chemistry, Manufacturing, and Controls (CMC)
Learn more about our services by engagement model:
Get in touch with us to learn more and get the support you need—when and where you need it.
FREE WHITE PAPER
Download the full white paper and take this guide with you. It offers everything we cover here, and more, in a handy PDF you can use to assess and enhance your CAPA program.
Topics: CAPA
Sign up for updates from our blog
Proprietary talent selection of former FDA and industry professionals amplified by a corporate culture of responsiveness and execution.
US Toll-Free: 1-833-FDA-GROUP
International: +001 508 926 8330
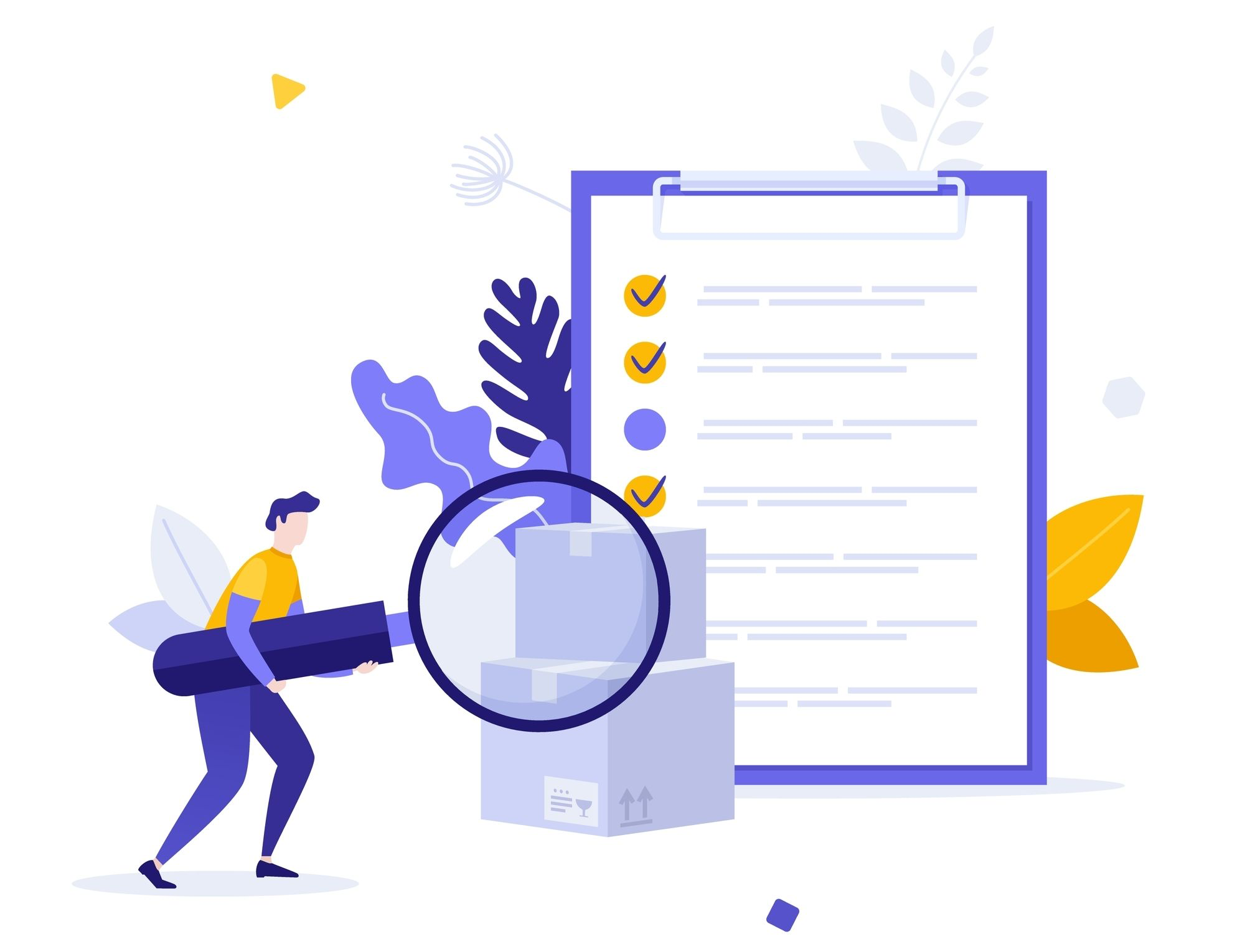

What is a CAPA? Understanding corrective and preventive actions
In today’s highly competitive landscape, organizations strive to maintain exceptional product quality , minimize risks, and meet regulatory requirements . Corrective and preventive actions , or “CAPAs,” are a powerful way to identify, investigate, and address deviations , nonconformances , and potential issues within processes, products, and services.
Below, we’ll define a CAPA and explain how it can be implemented into your day-to-day operations. We’ll share how CAPAs can improve your hardware products, benefit your teams, and address issues with newfound confidence.
What is corrective and preventive action (CAPA)?
A CAPA is a systematic process to identify, investigate, and resolve issues that arise during product development , manufacturing, or service delivery: Take corrective actions to address existing problems and implement preventive measures to avoid future occurrences. The primary goal of a CAPA is to improve processes, maintain product quality , and minimize defects.
Corrective action vs. preventive action
There are distinct differences between corrective and preventive actions.
Corrective action is more of a reactive approach. It aims to address existing problems by eliminating root causes or putting out fires that are currently affecting your organization.
As you may have guessed, preventive action is a proactive and anticipatory protocol. It helps you anticipate potential issues before they arise or become more severe. An internal audit , for example, can be used as a preventative tool during a management review to mitigate or eliminate developing topics.
Why is it important to have a CAPA process ?
Defining the issue is half the battle. You also need to collaborate with your team to determine a solution and move forward. Here’s why a defined CAPA process is a crucial business strategy:
Provides a uniform method for problem-solving
Consistency and efficiency across your organization is the most prominent advantage of the CAPA system . Without a defined, standardized procedure, your team may be unable to effectively identify, analyze, and resolve existing and potential issues.
Ensures compliance
Some industries have extremely stringent regulations that can limit your options when dealing with an issue. Securing compliance with all relevant regulatory bodies helps you avoid costly penalties.
For example, regulatory bodies such as the Food and Drug Administration ( FDA ) require you to have a robust CAPA process in place for things such as medical devices , biological products, and pharmaceuticals . A description of what the FDA requires is described below.These
Maintains product quality and minimizes defects
Organizations can address current issues, eliminate root causes, and prevent future problems. By systematically managing product-related issues, CAPAs enhances product quality , reduces defects, improves customer satisfaction, and ensures adherence to regulatory standards.
Increases customer satisfaction
An effective CAPA process will ensure the timely resolution of customer complaints and give your organization a mechanism for gathering and acting on customer feedback. You can then use this feedback to improve future iterations of your product.
When customers see their feedback is valued, it builds trust and brand loyalty. As a result of this customer-first approach, your brand perception will improve, and you’ll be better positioned to cultivate long-term customer relationships.
Who should set up a CAPA process ?
Organizations .
Various types of companies and industries would benefit from a CAPA system. However , there are a number of complex product-oriented industries where an effective process is required. Here are some industries where CAPAs are essential:
- Medical device : Medical devices have many restrictions. CAPA helps ensure that any issues or nonconformities in medical device design, manufacturing, or distribution are promptly addressed.
- Pharmaceutical: A CAPA process is required to address quality deviations , adverse events, product recalls, and other issues which improve both the safety and impact of your pharmaceuticals.
- Aerospace: A CAPA process enables you to identify, plan, and resolve any issues that may compromise airworthiness and quality.
- Automotive: Automotive companies use CAPA to address defects, quality issues , recalls, and noncompliance with regulatory standards.
- Electronics: The electronics industry, encompassing manufacturers of electronic components, devices, and equipment, relies on CAPA for quality, reliability, and compliance with regulations.
- Food and beverage: The food and beverage industry requires a robust CAPA process to address food safety hazards, product contamination, quality deviations , and regulatory noncompliance.
- Biotechnology: Biotechnology companies involved in developing biological products, diagnostics, and therapeutics, need a CAPA process to ensure the quality, safety, and efficacy of their products.
- Quality managers: Quality managers oversee the implementation and maintenance of the CAPA process within an organization. They’ll ensure compliance with quality standards, lead investigations, and monitor the effectiveness of corrective and preventive actions .
- Design engineers: Design engineers collaborate with their teams and play a crucial role in the CAPA process. They’re particularly valuable in addressing design-related issues that may impact product quality or performance with cross-functional teams to implement corrective actions and design changes .
- Regulatory affairs professionals: Regulatory affairs professionals monitor regulatory changes, provide guidance on compliance, and ensure that CAPA activities address any regulatory noncompliance effectively.
- Production managers: As a production manager, you will work closely with quality teams to identify process-related issues and implement improvements to enhance product quality and consistency.
Understanding CAPA in the context of ISO 13485 and 21 CFR 820
Two primary quality management standards require a corrective and preventive action plan : 21 CFR 820 and ISO 13485.
Understanding the CAPA processes and quality processes outlined in both standards is essential for organizations seeking to meet regulatory requirements and maintain high-quality standards.
21 CFR 820 , also known as the Quality System Regulation (QSR) for medical devices , sets forth the requirements for designing, manufacturing, packaging, labeling, storing, installing, and servicing medical devices intended for commercial distribution in the United States.
Under 21 CFR 820 , the CAPA process requires medical device manufacturers to establish procedures for investigating and addressing nonconformities and implementing corrective and preventive actions .
It includes steps such as identifying and documenting nonconformities , determining root causes, implementing corrective actions, verifying their effectiveness, and maintaining records of CAPA activities.
ISO 13485 is an international standard for quality management systems in the medical device industry. This standard is essential for companies looking to deliver products globally and remain compliant.
This provides a framework for organizations to establish and maintain a comprehensive quality management system that meets regulatory requirements and ensures the safety and effectiveness of medical devices .
The CAPA process in ISO 13485 requires organizations to have procedures for identifying, investigating, and correcting nonconformities and causes of nonconformities .
The ISO 13485 CAPA process involves problem identification, investigation, determining root causes, implementing corrective and preventive actions , and verifying their effectiveness.
The CAPA process
Now that we have explored the importance and significance of the CAPA process , let’s look at the process itself.
1. Problem identification
Problem identification is the recognition and documentation of quality issues , nonconformities , or deviations from established standards or requirements. It serves as the foundation for the subsequent steps of the CAPA process , as it sets the stage for investigation and resolution.
You can initiate this step through various means, such as customer complaints , internal audits , quality control checks, or regulatory inspections.
2. Investigation and root cause analysis
Root cause analysis helps identify the immediate causes of a problem and the underlying systemic or process-related issues. This step involves gathering relevant data, examining processes, procedures, and systems, conducting analyses, and identifying the primary factors contributing to the problem.
3. Corrective action implementation
Corrective actions should be carefully planned, documented, and executed to ensure their effectiveness and alignment with regulatory requirements and quality objectives.
Take decisive steps during this stage. Include process adjustments, system modifications, employee training, rework or repairs, or other necessary actions to resolve the matter and mitigate its impact.
4. Documentation and verification
Validation activities, such as testing and analysis, are part of this crucial step. Documentation and verification play a vital role in ensuring the effectiveness and traceability of the CAPA process .
Documentation records the entire process, demonstrating compliance with regulatory requirements and serving as a reference for future audits or inspections. Verification involves evaluating the results of corrective actions. Then, confirming their effectiveness in resolving the problem and preventing it from happening again.
5. Review and follow-up
The review and follow-up step involves assessing the overall effectiveness of the CAPA process and monitoring the implemented corrective actions over time.
Follow-up activities may involve occasional audits, performance monitoring, and ongoing surveillance to confirm sustained compliance and continuous improvement.
What the FDA looks for in your CAPA process
The FDA is one of the strictest regulating bodies in the United States. They’ll review your CAPA process to ensure it includes root cause analysis, verification and validation, in addition to the following:
Procedures and documentation
Your company must establish and maintain documented procedures for various quality processes , including CAPA management . These procedures outline the step-by-step approach for identifying, investigating, and resolving quality problems .
You are also required to define the roles and responsibilities of stakeholders involved in the CAPA process .
Documentation includes CAPA forms, templates , reports, and other relevant documents that capture the details of the quality issue , investigation findings, root cause analysis , and corrective/preventive actions implemented.
Risk-based approach
Companies are required to perform a risk analysis , which typically includes methods such as failure mode and effects analysis (FMEA) or fishbone diagrams. This analysis helps identify the root cause of the problem by examining potential failure modes and their potential impacts.
Implementing a risk-based approach lets you focus on critical issues impacting patient safety, product quality , and regulatory compliance.
Timeliness and efficiency
It’s crucial to promptly identify and address quality problems to mitigate their impact on patient safety and product quality ; timely CAPA actions help prevent potential harm and minimize the scope of issues.
It would be best to establish appropriate timeframes and escalation procedures to confirm that CAPA activities are conducted promptly. Timeliness and efficiency in CAPA execution demonstrate a commitment to effective quality management and regulatory compliance.
Training and competency
Personnel involved in the CAPA process should receive appropriate training to understand their roles and responsibilities and the procedures and requirements associated with CAPA management .
Training programs should cover problem identification, investigation techniques, root cause analysis methods, corrective action planning, and documentation requirements.
You can conduct competency assessments to evaluate the proficiency of personnel involved in CAPA activities. That way, you’ll identify any training needs or opportunities for improvement.
Continuous improvement
Emphasizing the ongoing enhancement of processes, products, and systems increases efficiency, effectiveness, and customer satisfaction.
Within the CAPA process , continuous improvement involves evaluating the effectiveness of implemented actions, monitoring outcomes, and seeking opportunities for further enhancements.
This may include analyzing data and trends, conducting periodic reviews and audits, and implementing additional preventive measures or process controls .
Optimize your CAPA process with Duro
A well-implemented CAPA process is critical for organizations operating in regulated industries such as medical devices , pharmaceuticals, aerospace, automotive, electronics, and food and beverage.
This process involves critical steps such as problem identification, investigation and root cause analysis , corrective action implementation, documentation and verification, and review and follow-up .
When it comes to establishing sound CAPA processes , your organization needs to lean on the right tools to maintain compliance. Duro, a leading PLM solution provider, gives businesses a centralized way for teams to collaborate and share information. Tie CAPA information back to your original designs with Duro. That way, you’ll ensure that everyone is on the same page and can easily manage revisions.
See how Carecubes leverages Duro for compliance, collaboration, and quality control. Alternatively , request a demo to see what we can do for your teams.
%20-%20Tint%20100.png?width=106&name=Logo%20-%20Standard%20-%20Blue%20(270%20x%20149)%20-%20Tint%20100.png)
Related Articles
- The Decline of American Manufacturing and Why Today’s Leaders Should Care
- How to Improve Manufacturing Workflow: 5S and Gemba Walks
- 5 Essential Activities of Current Good Manufacturing Practices
ARTICLES & RESOURCES
Explore materials, technologies, design, and manufacturing in the life sciences.
Manufacturing
Successfully Implementing a CAPA Process
The framework of corrective and preventive action (CAPA) can be intimidating to tackle; especially if you are in a new organization or one that does not already have an institutional understanding and belief in it. At its core, the CAPA framework provides common terminology to an organization and helps organize people and thoughts in order to facilitate problem solving and critical thinking. Problem solving can be fun and rewarding, but in the wrong environment, it can also be discouraging and counterproductive.
A CAPA system is a critical component of ISO business standards and many of us are familiar with it. However, ISO and ISO certifying bodies, only provide a framework for CAPA, they don't design and implement a functioning system for you. Creating and maintaining an effective CAPA system is up to each individual business and requires a few key components to be successful. Below is a simplified outline of CAPA to help you understand the framework and begin to institutionalize it constructively within your organization.
Defining the CAPA Process
An effective CAPA process is ultimately driven by critical thinking, strong problem solving, and organizational control. The first step is to create a defined process to manage corrective actions within your organization and to make sure that it is implemented each time a corrective action is initiated. With a defined process in place, an organization can begin to work on completing the process efficiently and putting preventive actions in place more readily. Assessing the long term sustainability of those corrective actions is a key part of the feedback loop.
In a strong Quality Management System most critical control points continuously pass through the CAPA system making it an easy way to identify existing problems in a company. Typically, quality auditors and regulatory organizations focus on the CAPA system to find deficiencies within a Company's Quality Management System. This is especially true in medical device manufacturing and biotech manufacturing. When this happens inspections are based on the documents that are controlled within the CAPA system; including but not limited to, customer complaints, quality audit reports, and nonconforming material reports. Monitoring the internal operations of your company and preparing risk assessments are a good way to ensure compliance with the quality and regulatory bodies.
Watch our video series about biomedical innovation.
Identifying the Event and the Root Cause
One of the key success factors to design and customize your own CAPA system is a management team's ability to determine the non-conformance event and root cause quickly and effectively. This has to be done without spreading risk to other areas of the business by misidentifying the root cause. It is also important to cultivate an atmosphere where teamwork and collaborative problem solving thrives, and blaming and disenfranchising individuals does not.
Quickly and comprehensively gathering as many details as possible about the event is critical. With the information gathered putting next steps into action to determine the root cause and following through on them can be executed efficiently. Digging deep to determine the root cause is important and strategies like the "5 Whys" can be a helpful tool in accomplishing this. Above all, strong teamwork and project management skills are essential.
Containing the Non-conformance Risk
When there is an occurrence and a corrective action response is in activation mode, aspects of the business become vulnerable. Awareness of the occurrence and efforts towards corrective actions are a key strategy to control the non-conformance risk from reoccurring or spreading into other areas of the business. identifying areas of the business where there are potential voids and putting robust corrective actions in place is critical. Highlighting these areas and maintaining awareness about them will help support their long-term sustainability.
The main focus is always to eliminate and control the risk of a non-conformance reoccurring - and this is accomplished with robust corrective actions. With that said, strong organizations build Quality Management Systems that put ample focus on preventative actions that shore up the risk surrounding a corrective action and help to mitigate both the direct and indirect risks associated to a non-conformance event. This is critical in advanced flexible materials markets.
Plan Do Check Act (PDCA)
Problem prevention and containment must always be documented to help prevent reoccurrence. This is the golden rule of a strong Quality Management System in any organization in the advanced flexible materials market. Sometimes it is tricky to keep steps in line with one another, but if you follow the simple Plan, Do, Check, Act cycle (PDCA), then your process will flow in a predictable pattern that eventually becomes an institutionalized way of working.
Plan, Do, Check, Act itself is a great tool to strengthen your organization's project management skills and continuous improvement goals. Learning from the output is an efficient way to reduce repeating quality problems that are costly and could greatly harm the business. Using this tool will help institutionalize pragmatic thinking and risk analysis into daily practices which is critical for medical device manufacturing and biotech manufacturing.
Reaping the Benefits of CAPA
Using CAPA to resolve non-conformance events and determine the root cause is an important problem solving tool for a business. It forces a team to review the correction, determine if corrective actions are considered effective, and then validate the successful impact of the corrective action. Implementing preventive actions and identifying risk in areas that affect product quality can prevent future nonconforming products. Analyzing your CAPA data and determining trends can then become an integral part of continually improving your business processes. This is where an organization can make a Quality Management System go beyond compliance to becoming an integral part of the strategic growth and improvement of a business over the long term.
Being prepared for any non-conformance should be the goal of your CAPA system, since the severity of a corrective action is usually at the utmost degree and requires immediate attention. It is important for the team to remain engaged throughout the process in order to drive the corrective action all the way to completion. A robust CAPA system for medical device manufacturing is critical because regulations require complete traceability within the organization. Investing in the process and your team's ability to efficiently and effectively execute it will benefit your company in the long run because after all CAPA is truly about strengthening and improving the core operations of your business.
Defining and institutionalizing CAPA is a critical part of a strong Quality Management System and it will benefit your organization in the long run. This is especially true in advanced flexible materials markets. To get started, define a CAPA process, learn how to identify an event, determine the root cause, and contain the risks associated to non-conformities. Utilizing tools like the "5 whys?" and "PDCA" can be helpful. Creating an environment that cultivates teamwork and problem solving is a key success factor to a strong CAPA system. Taking it all one step further by analyzing your CAPA data and identifying trends is a great strategic input for the long term growth and improvement of your organization.
.png)
Articles & Resources
Our articles and resources explore materials, technologies, design, and manufacturing in the life sciences. Together we're advancing biomedical innovation through curiosity and shared knowledge.
.png)
Video Series
Boyd Biomedical Design Stories explores what it takes to commercialize biomedical innovations in a modern susteainable way. A way that's the best way - for patients, practitioners, and all of us - as we seek to advance healthcare together.
.png)
Documentary Film
Project Frontline is a feature length documentary film which tells the inspiring story of collaboration during crisis and is a cautionary tale about our leadership in innovation, advanced manufacturing, and supply chain resilience.
By using this site you agree to our use of cookies. Please refer to our privacy policy for more information. Close

7 Powerful Problem-Solving Root Cause Analysis Tools
The first step to solving a problem is to define the problem precisely. It is the heart of problem-solving.
Root cause analysis is the second important element of problem-solving in quality management. The reason is if you don't know what the problem is, you can never solve the exact problem that is hurting the quality.
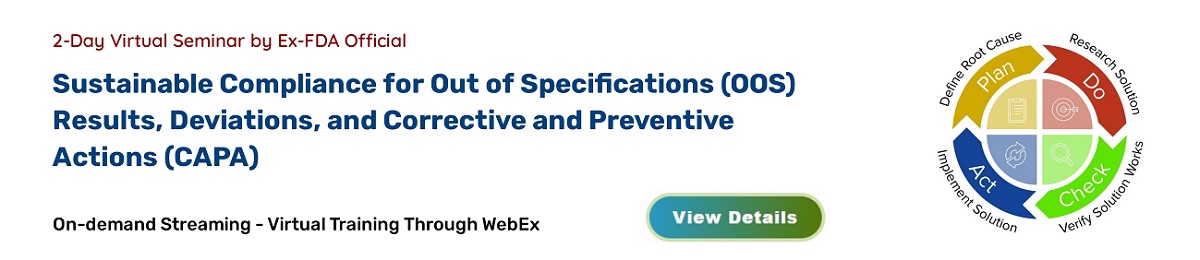
Manufacturers have a variety of problem-solving tools at hand. However, they need to know when to use which tool in a manner that is appropriate for the situation. In this article, we discuss 7 tools including:
- The Ishikawa Fishbone Diagram (IFD)
- Pareto Chart
- Failure Mode and Effects Analysis (FMEA)
- Scatter Diagram
- Affinity Diagram
- Fault Tree Analysis (FTA)
1. The Ishikawa Fishbone Diagram IFD
The model introduced by Ishikawa (also known as the fishbone diagram) is considered one of the most robust methods for conducting root cause analysis. This model uses the assessment of the 6Ms as a methodology for identifying the true or most probable root cause to determine corrective and preventive actions. The 6Ms include:
- Measurement,
- Mother Nature- i.e., Environment
Related Training: Fishbone Diagramming
2. Pareto Chart
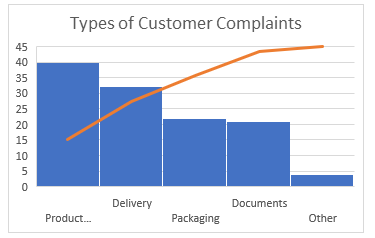
The Pareto Chart is a series of bars whose heights reflect the frequency or impact of problems. On the Chart, bars are arranged in descending order of height from left to right, which means the categories represented by the tall bars on the left are relatively more frequent than those on the right.
Related Training: EFFECTIVE INVESTIGATIONS AND CORRECTIVE ACTIONS (CAPA) Establishing and resolving the root causes of deviations, problems and failures
This model uses the 5 Why by asking why 5 times to find the root cause of the problem. It generally takes five iterations of the questioning process to arrive at the root cause of the problem and that's why this model got its name as 5 Whys. But it is perfectly fine for a facilitator to ask less or more questions depending on the needs.
Related training: Accident/Incident Investigation and Root Cause Analysis
4. Failure Mode and Effects Analysis (FMEA)
FMEA is a technique used to identify process and product problems before they occur. It focuses on how and when a system will fail, not if it will fail. In this model, each failure mode is assessed for:
- Severity (S)
- Occurrence (O)
- Detection (D)
A combination of the three scores produces a risk priority number (RPN). The RPN is then provided a ranking system to prioritize which problem must gain more attention first.
Related Training: Failure Mode Effects Analysis
5. Scatter Diagram
A scatter diagram also known as a scatter plot is a graph in which the values of two variables are plotted along two axes, the pattern of the resulting points revealing any correlation present.
To use scatter plots in root cause analysis, an independent variable or suspected cause is plotted on the x-axis and the dependent variable (the effect) is plotted on the y-axis. If the pattern reflects a clear curve or line, it means they are correlated. If required, more sophisticated correlation analyses can be continued.
Related Training: Excel Charting Basics - Produce Professional-Looking Excel Charts
6. Affinity Diagram
Also known as KJ Diagram, this model is used to represent the structure of big and complex factors that impact a problem or a situation. It divides these factors into small classifications according to their similarity to assist in identifying the major causes of the problem.
7. Fault Tree Analysis (FTA)
The Fault Tree Analysis uses Boolean logic to arrive at the cause of a problem. It begins with a defined problem and works backward to identify what factors contributed to the problem using a graphical representation called the Fault Tree. It takes a top-down approach starting with the problem and evaluating the factors that caused the problem.
Finding the root cause isn't an easy because there is not always one root cause. You may have to repeat your experiment several times to arrive at it to eliminate the encountered problem. Using a scientific approach to solving problem works. So, its important to learn the several problem-solving tools and techniques at your fingertips so you can use the ones appropriate for different situations.
ComplianceOnline Trainings on Root Cause Analysis
P&PC, SPC/6Sigma, Failure Investigation, Root Cause Analysis, PDCA, DMAIC, A3 This webinar will define what are the US FDA's expectation for Production and Process Control / Product Realization, the use of statistical tehniques, 6 sigma, SPC, for establishing, controlling , and verifying the acceptability of process capability and product characteristics, product acceptance or validation and other studies. Non-conformance, OOS, deviations Failure Investigations, and Root Cause Analysis, PDCA, DMAIC, and similar project drivers to improvement, A# and similar dash boards.
Accident/Incident Investigation and Root Cause Analysis If a major workplace injury or illness occurred, what would you do? How would you properly investigate it? What could be done to prevent it from happening again? A properly executed accident/incident investigation drives to the root causes of the workplace accident to prevent a repeat occurrence. A good accident/incident investigation process includes identifying the investigation team, establishing/reviewing written procedures, identifying root causes and tracking of all safety hazards found to completion.
Root Cause Analysis - The Heart of Corrective Action This presentation will explain the importance of root cause analysis and how it fits into an effective corrective and preventive action system. It will cover where else in your quality management system root cause analysis can be used and will give examples of some of the techniques for doing an effective root cause analysis. Attendees will learn how root cause analysis can be used in process control.
Addressing Non-Conformances using Root Cause Analysis (RCA) RCA assumes that systems and events are interrelated. An action in one area triggers an action in another, and another, and so on. By tracing back these actions, you can discover where the issue started and how it grew into the problem you're now facing.
Introduction to Root Cause Investigation for CAPA If you have reoccurring problems showing up in your quality systems, your CAPA system is not effective and you have not performed an in-depth root cause analysis to be able to detect through proper problem solving tools and quality data sources, the true root cause of your problem. Unless you can get to the true root cause of a failure, nonconformity, defect or other undesirable situation, your CAPA system will not be successful.
Root Cause Analysis and CAPA Controls for a Compliant Quality System In this CAPA webinar, learn various regulations governing Corrective and Preventive Actions (CAPA) and how organization should collect information, analyze information, identify, investigate product and quality problems, and take appropriate and effective corrective and/or preventive action to prevent their recurrence.
Root Cause Analysis for CAPA Management (Shutting Down the Alligator Farm) Emphasis will be placed on realizing system interactions and cultural environment that often lies at the root of the problem and prevents true root cause analysis. This webinar will benefit any organization that wants to improve the effectiveness of their CAPA and failure investigation processes.
Root Cause Analysis for Corrective and Preventive Action (CAPA) The Quality Systems Regulation (21 CFR 820) and the Quality Management Standard for Medical Devices (ISO 13485:2003), require medical device companies to establish and maintain procedures for implementing corrective and preventive action (CAPA) as an integral part of the quality system.
Strategies for an Effective Root Cause Analysis and CAPA Program This webinar will provide valuable assistance to all regulated companies, a CAPA program is a requirement across the Medical Device, Diagnostic, Pharmaceutical, and Biologics fields. This session will discuss the importance, requirements, and elements of a root cause-based CAPA program, as well as detailing the most effective ways to determine root cause and describing the uses of CAPA data.
Legal Disclaimer
This piece of content and any of its enclosures, attachments or appendices, references are created to provide solely for information purpose. ComplianceOnline has made all effort to provide accurate information concerning the subject matter covered. This content is created from interpretation, and understanding of relevant and applicable information and it is not all inclusive. It can be best used in conjunction with your professional judgment and discretion.
However, this piece of content and any other ancillary items disseminated in connection with same are not necessarily prepared by a person licensed to practice law in a particular jurisdiction. This piece of content is not a substitute for the advice of an attorney. If you require legal or other expert advice, you should seek the services of a competent attorney or other professional.
ComplianceOnline necessarily is not, cannot and will not be liable for any claims, damages, or regulatory legal proceedings initiated as a consequence of you using whole or any part of the content present in this document. If any action, claim for damages, or regulatory proceedings is commenced against ComplianceOnline as a consequence of your use of this document, then and in that event, you agree to indemnify ComplianceOnline for such claims, and for any attorney's fees expended by ComplianceOnline in connection with defense of same.

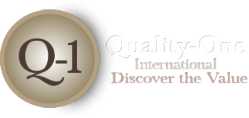
Eight Disciplines of Problem Solving (8D)
– Eight Disciplines of Problem Solving –
⇓ Introduction to 8D
⇓ What is 8D
⇓ Why Apply 8D
⇓ When to Apply 8D
⇓ How to Apply 8D
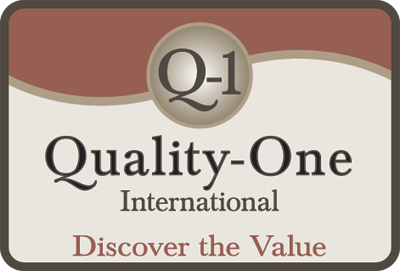
Introduction to Eight Disciplines of Problem Solving (8D)
The Eight Disciplines of Problem Solving (8D) is a problem solving methodology designed to find the root cause of a problem, devise a short-term fix and implement a long-term solution to prevent recurring problems. When it’s clear that your product is defective or isn’t satisfying your customers, an 8D is an excellent first step to improving Quality and Reliability.
Ford Motor Company developed this problem solving methodology, then known as Team Oriented Problem Solving (TOPS), in the 1980s. The early usage of 8D proved so effective that it was adopted by Ford as the primary method of documenting problem solving efforts, and the company continues to use 8D today.
8D has become very popular among manufacturers because it is effective and reasonably easy to teach. Below you’ll find the benefits of an 8D, when it is appropriate to perform and how it is performed.
What is Eight Disciplines of Problem Solving (8D)
The 8D problem solving process is a detailed, team oriented approach to solving critical problems in the production process. The goals of this method are to find the root cause of a problem, develop containment actions to protect customers and take corrective action to prevent similar problems in the future.
The strength of the 8D process lies in its structure, discipline and methodology. 8D uses a composite methodology, utilizing best practices from various existing approaches. It is a problem solving method that drives systemic change, improving an entire process in order to avoid not only the problem at hand but also other issues that may stem from a systemic failure.
8D has grown to be one of the most popular problem solving methodologies used for Manufacturing, Assembly and Services around the globe. Read on to learn about the reasons why the Eight Disciplines of Problem Solving may be a good fit for your company.
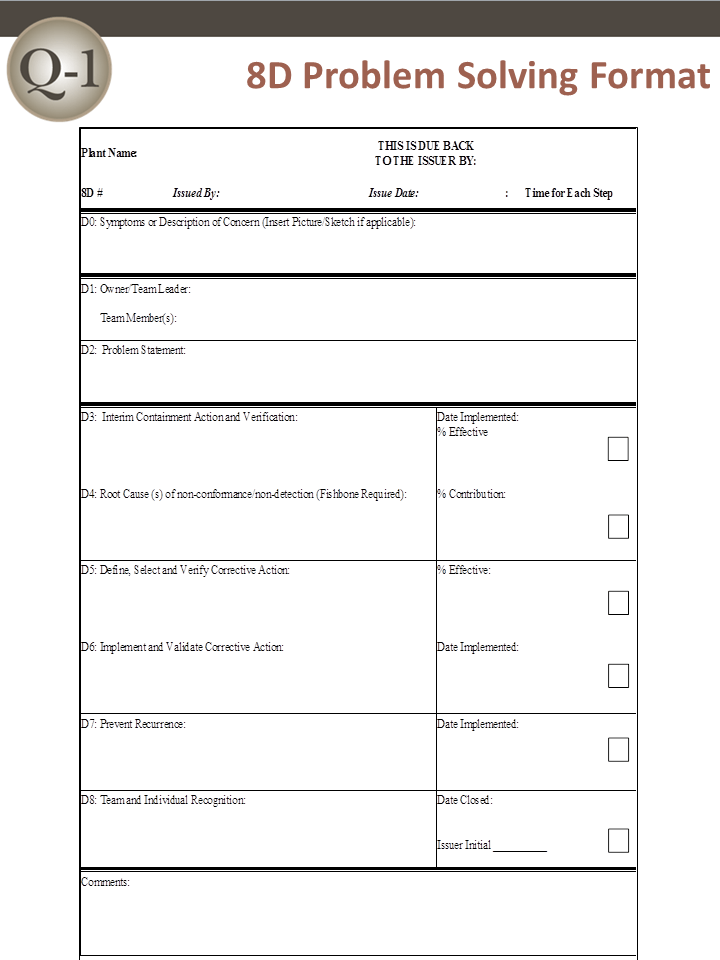
Why Apply Eight Disciplines of Problem Solving (8D)
The 8D methodology is so popular in part because it offers your engineering team a consistent, easy-to-learn and thorough approach to solving whatever problems might arise at various stages in your production process. When properly applied, you can expect the following benefits:
- Improved team oriented problem solving skills rather than reliance on the individual
- Increased familiarity with a structure for problem solving
- Creation and expansion of a database of past failures and lessons learned to prevent problems in the future
- Better understanding of how to use basic statistical tools required for problem solving
- Improved effectiveness and efficiency at problem solving
- A practical understanding of Root Cause Analysis (RCA)
- Problem solving effort may be adopted into the processes and methods of the organization
- Improved skills for implementing corrective action
- Better ability to identify necessary systemic changes and subsequent inputs for change
- More candid and open communication in problem solving discussion, increasing effectiveness
- An improvement in management’s understanding of problems and problem resolution
8D was created to represent the best practices in problem solving. When performed correctly, this methodology not only improves the Quality and Reliability of your products but also prepares your engineering team for future problems.
When to Apply Eight Disciplines of Problem Solving (8D)
The 8D problem solving process is typically required when:
- Safety or Regulatory issues has been discovered
- Customer complaints are received
- Warranty Concerns have indicated greater-than-expected failure rates
- Internal rejects, waste, scrap, poor performance or test failures are present at unacceptable levels
How to Apply Eight Disciplines of Problem Solving (8D)
The 8D process alternates inductive and deductive problem solving tools to relentlessly move forward toward a solution. The Quality-One approach uses a core team of three individuals for inductive activities with data driven tools and then a larger Subject Matter Expert (SME) group for the deductive activities through brainstorming, data-gathering and experimentation.
D0: Prepare and Plan for the 8D
Proper planning will always translate to a better start. Thus, before 8D analysis begins, it is always a good idea to ask an expert first for their impressions. After receiving feedback, the following criterion should be applied prior to forming a team:
Collect information on the symptoms
Use a Symptoms Checklist to ask the correct questions
Identify the need for an Emergency Response Action (ERA), which protects the customer from further exposure to the undesired symptoms
D1: Form a Team
A Cross Functional Team (CFT) is made up of members from many disciplines. Quality-One takes this principle one step further by having two levels of CFT:
- The Core Team Structure should involve three people on the respective subjects: product, process and data
- Additional Subject Matter Experts are brought in at various times to assist with brainstorming, data collection and analysis
Teams require proper preparation. Setting the ground rules is paramount. Implementation of disciplines like checklists, forms and techniques will ensure steady progress. 8D must always have two key members: a Leader and a Champion / Sponsor:
- The Leader is the person who knows the 8D process and can lead the team through it (although not always the most knowledgeable about the problem being studied)
- The Champion or Sponsor is the one person who can affect change by agreeing with the findings and can provide final approval on such changes
D2: Describe the Problem
The 8D method’s initial focus is to properly describe the problem utilizing the known data and placing it into specific categories for future comparisons. The “Is” data supports the facts whereas the “Is Not” data does not. As the “Is Not” data is collected, many possible reasons for failure are able to be eliminated. This approach utilizes the following tools:
- Problem Statement
- Affinity Diagram (Deductive tool)
- Fishbone/Ishikawa Diagram (Deductive tool)
- Problem Description
D3: Interim Containment Action
In the interim, before the permanent corrective action has been determined, an action to protect the customer can be taken. The Interim Containment Action (ICA) is temporary and is typically removed after the Permanent Correct Action (PCA) is taken.
- Verification of effectiveness of the ICA is always recommended to prevent any additional customer dissatisfaction calls
D4: Root Cause Analysis (RCA) and Escape Point
The root cause must be identified to take permanent action to eliminate it. The root cause definition requires that it can be turned on or off, at will. Activities in D4 include:
- Comparative Analysis listing differences and changes between “Is” and “Is Not”
- Development of Root Cause Theories based on remaining items
- Verification of the Root Cause through data collection
- Review Process Flow Diagram for location of the root cause
- Determine Escape Point, which is the closest point in the process where the root cause could have been found but was not
D5: Permanent Corrective Action (PCA)
The PCA is directed toward the root cause and removes / changes the conditions of the product or process that was responsible for the problem. Activities in D5 include:
- Establish the Acceptance Criteria which include Mandatory Requirements and Wants
- Perform a Risk Assessment / Failure Mode and Effects Analysis (FMEA) on the PCA choices
- Based on risk assessment, make a balanced choice for PCA
- Select control-point improvement for the Escape Point
- Verification of Effectiveness for both the PCA and the Escape Point are required
D6: Implement and Validate the Permanent Corrective Action
To successfully implement a permanent change, proper planning is essential. A project plan should encompass: communication, steps to complete, measurement of success and lessons learned. Activities in D6 include:
- Develop Project Plan for Implementation
- Communicate the plan to all stakeholders
- Validation of improvements using measurement
D7: Prevent Recurrence
D7 affords the opportunity to preserve and share the knowledge, preventing problems on similar products, processes, locations or families. Updating documents and procedures / work instructions are expected at this step to improve future use. Activities in D7 include:
- Review Similar Products and Processes for problem prevention
- Develop / Update Procedures and Work Instructions for Systems Prevention
- Capture Standard Work / Practice and reuse
- Assure FMEA updates have been completed
- Assure Control Plans have been updated
D8: Closure and Team Celebration
Teams require feedback to allow for satisfactory closure. Recognizing both team and individual efforts and allowing the team to see the previous and new state solidifies the value of the 8D process. Activities in D8 include:
- Archive the 8D Documents for future reference
- Document Lessons Learned on how to make problem solving better
- Before and After Comparison of issue
- Celebrate Successful Completion
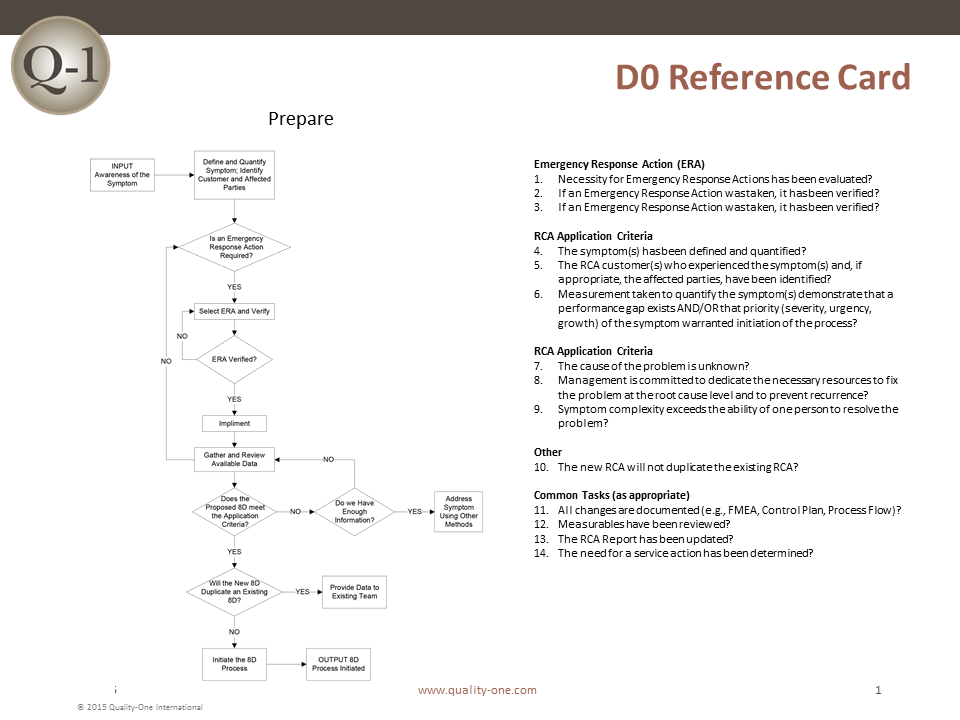
8D and Root Cause Analysis (RCA)
The 8D process has Root Cause Analysis (RCA) imbedded within it. All problem solving techniques include RCA within their structure. The steps and techniques within 8D which correspond to Root Cause Analysis are as follows:
- Problem Symptom is quantified and converted to “Object and Defect”
- Problem Symptom is converted to Problem Statement using Repeated Whys
- Possible and Potential Causes are collected using deductive tools (i.e. Fishbone or Affinity Diagram)
- Problem Statement is converted into Problem Description using Is / Is Not
- Problem Description reduces the number of items on the deductive tool (from step 3)
- Comparative Analysis between the Is and Is Not items (note changes and time)
- Root Cause theories are developed from remaining possible causes on deductive tool and coupled with changes from Is / Is Not
- Compare theories with current data and develop experiments for Root Cause Verification
- Test and confirm the Root Causes
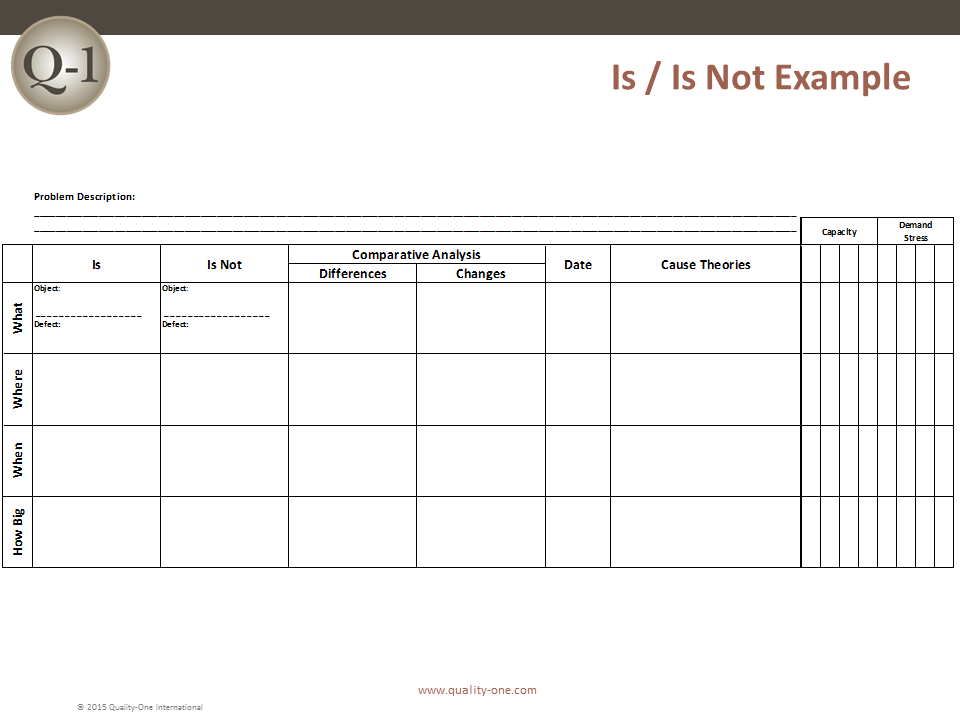
Example: Multiple Why Technique
The Multiple / Repeated Why (Similar to 5 Why) is an inductive tool, which means facts are required to proceed to a more detailed level. The steps required to determine problem statement are:
- Problem Symptom is defined as an Object and Defect i.e. “Passenger Injury”
- Why? In every case “SUV’s Roll Over”
- Why? In every case, it was preceded by a “Blown Tire”
- Why? Many explanations may be applied, therefore the team cannot continue with another repeated why past “Blown Tire”
- Therefore, the Problem Statement is “Blown Tire”
- Why? Low (Air) Pressure, Tire Defect (Degradation of an Interface) and High (Ambient) Temperature
- Counter measures assigned to low pressure and tire defect
This example uses only 4 of the 5 Whys to determine the root causes without going further into the systemic reasons that supported the failure. The Repeated Why is one way to depict this failure chain. Fault Tree Analysis (FTA) could also be used.
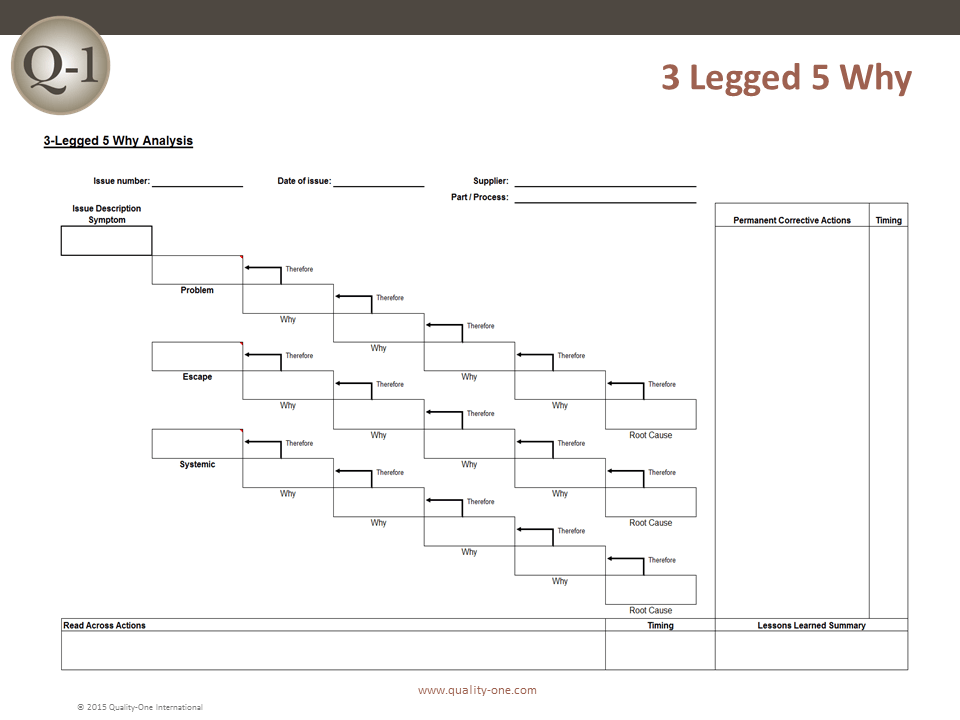
Learn More About Eight Disciplines of Problem Solving (8D)
Quality-One offers Quality and Reliability Support for Product and Process Development through Consulting, Training and Project Support. Quality-One provides Knowledge, Guidance and Direction in Quality and Reliability activities, tailored to your unique wants, needs and desires. Let us help you Discover the Value of 8D Consulting , 8D Training or 8D Project Support .
Contact Us | Discover the Value!
(248) 280-4800 | [email protected]
Remember Me
- Don't have an account? Register
- Lost your password? Click here
- Already have an account? Log in
- Capability Development
- Problem Solving & Decision Making for CAPA (Corrective And Preventive Actions)
Problem Solving & Decision Making for CAPA (Corrective And Preventive Actions)
Available as:
- In-house class
Problem Solving & Decision Making for Corrective and Preventive Actions (CAPAs) is an FDA-recognized, step-by-step approach to close out deviations with complete, well-documented investigations. Through this workshop, you’ll learn how to respond to deviations with a process that is focused, rapid, and fully documented. Ideal for pharmaceutical and medical device companies, Problem Solving & Decision Making for CAPAs provides the essential framework for satisfying agency investigation requirements and eliminating future deviations.
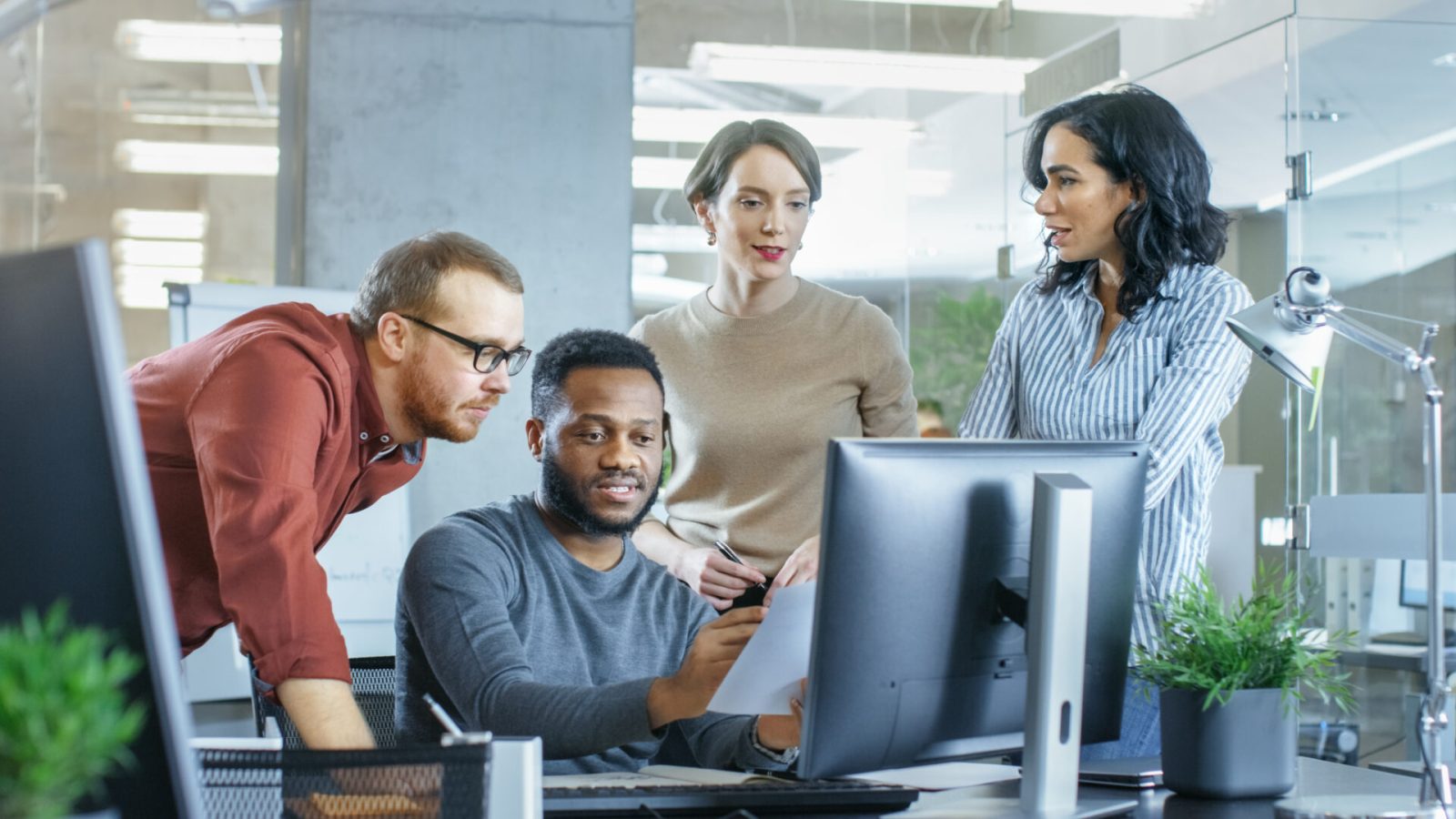
What You Get:
- 3 days led by an expert instructor
- Access to digital tools and resources
- Skills and approaches for satisfying agency investigation requirements and eliminating future deviations
- Certificate of completion
- Certification Credits : 2.1 CEUs
To see the total select country, date and number of participants
To see the total select language, date and number of participants
In this county services are provided by the official KT licensee.
* Before applicable taxes
Class seats guaranteed with payment. Seat reservations held for 72 hours.
Contact us to inquire for more details or have the workshop customized upon your corporate needs.
Anyone who has to investigate, find root cause, manage investigations or CAPAs. This includes operators who support investigations through to managers who approve investigations.
- Learn root cause analysis to cut through the complexity of pharmaceutical and bio-pharmaceutical manufacturing, confidently respond to warning letters, satisfy auditors, and avoid future issues
- Establish a systematic approach to classify and prioritize investigations, find cause, choose the most effective and efficient corrective and preventive actions to maintain compliance and improve throughput
- Reduce cycle time for investigation approval and the number of open investigations
- Incorporate risk analysis into decision making to avoid future problems and leverage opportunities for improvement
Skills Developed
- Take corrective and preventive actions by using a structured troubleshooting approach
- Use logic and data to systematically find and confirm true and root causes
- Reduce the cost of investigations by increasing the efficacy and speed of CAPAs
- Use incisive, easy-to-learn and apply questioning techniques
- Focus on accurate results even when tensions are high and costs are rising
- Improve transparency with structured thinking and clear communications
Return on Investment
- Reduce outstanding investigations
- Increase accuracy of investigations
- Avoid FDA 483s Warning Letters
- Improved ratings on internal audits
- Speed reviews/approvals. Reduce time to find root cause
- Reduce recurring problems. Decrease average time to closure
“Reinforcing the communication and follow-up on who-does-what has led to better communication and less falling through the cracks. In our matrix organization, this is rather critical.” — Group Project Manager, Life Sciences “KT PSDM CAPA provides a common approach and logical process to develop corrective action and preventive action.” – Assisant QC Manager
Problem Solving & Decision Making for CAPAs
Contact Form
Showcase your skills.
The KT Badge Program is a visible recognition of your rational process skills. Your Kepner-Tregoe Digital Badges can be shown on your social media profile page, your email signature, and your personal website. And finally the authenticity of your KT badge can be validated on our website portal.
The Foundation Badge is the starting point and highlights that you have attended a KT training program. Once you have begun applying the KT technologies you will progress through the levels of Practitioner, Advanced, and ultimately, achieve recognition as a KT Expert.
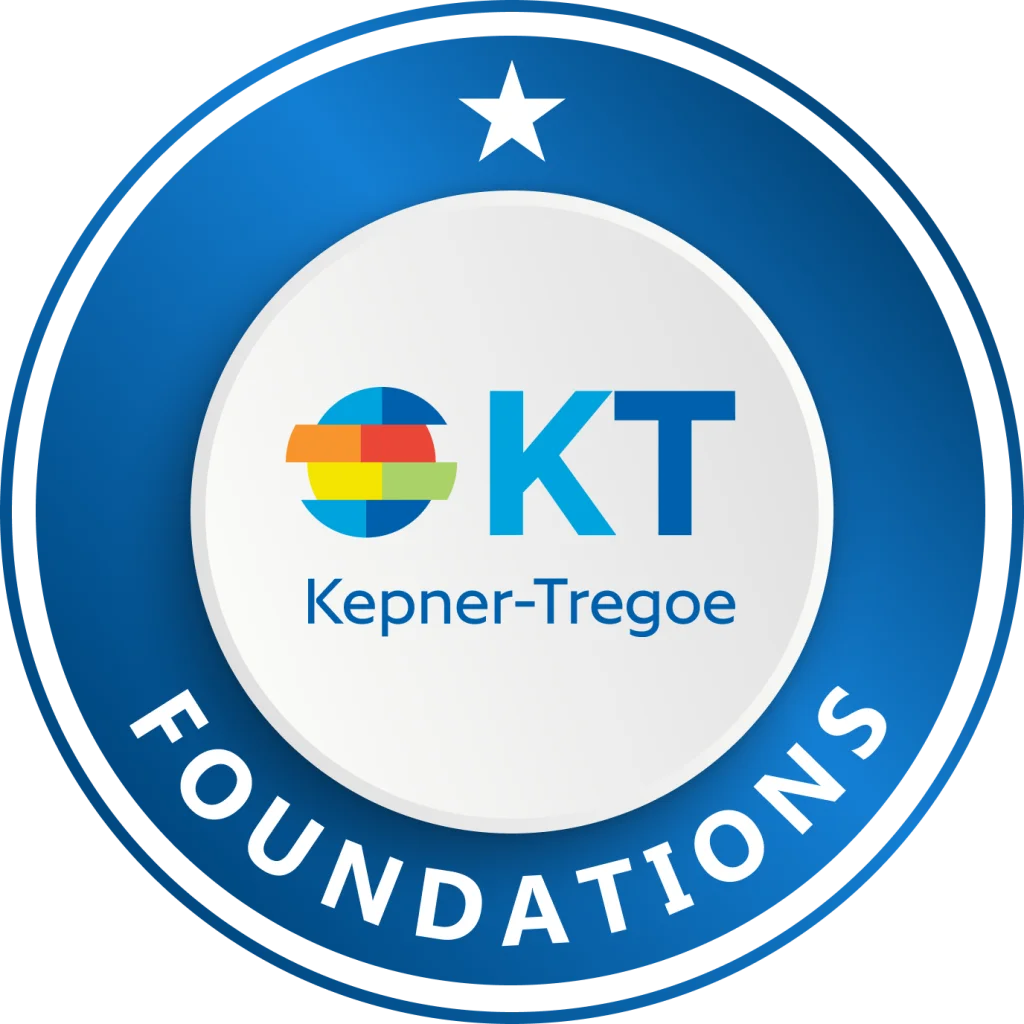
Kepner-Tregoe Foundations
If you have successfully participated in this workshop, you are eligible to receive the KT Foundations Badge. Click to find out more about our Badge Program:
Related Workshops
For inquiries, details, or a proposal!
Request in-house class offer
Subscribe to the kt newsletter.
How to do root cause analysis in the CAPA system? | Demo Registration

Streamline Your Root Cause Analysis and Corrective Action Plans for your eQMS
Root cause analysis and corrective action plans are not simply a template! They are an interconnected process that involves a series of critical steps of your Quality System.
Want to know more about this closed-loop process? Click the links below to learn root cause analysis tools or register to try QIT Corrective Action Software and QIT Quality Management System today to see how it works.
- Root Cause Analysis Tools – 5W1H
- Root Cause Analysis Tools - 5-Why Analysis
- Root Cause Analysis Tools - Fishbone Analysis
- Root Cause Analysis Tools - 8D Process
- Root Cause Analysis Tools - Summary
- An effective root cause analysis system
- QIT Root Cause Analysis System
Testimonial: "I don't believe a simple NCR can uncover so many hidden problems in our quality system, unless I’m mistaken. I’m very pleased with the root cause analysis and the Watch List features of the program.” – Gary QA Manager
Are you looking for a way to improve your problem-solving skills and prevent issues from recurring? Do you want to use professional root cause analysis tools like 8D, 5-why, fishbone diagram and more?
Then you need QIT Corrective Action Software, the best solution for managing and resolving problems in any industry. QIT’s approach is simple. Let's answer some of the basic questions first:
- How do you improve quality? We resolve problems from audit, design, manufacturing, delivery, and service... in fact, from the entire company.
- How do you identify the problem to be resolved? We collect defects, customer complaints, audit findings, nonconformance reports and then identify the high-risk and high-cost issues.
- Once you have identified the problems, how do you resolve them? We have a systematic root cause analysis system to identify the real root causes and monitor the corrective action and preventive actions.
- What is your systematic root cause analysis system to identify real root cause and monitor improvement actions? We use root cause analysis template e.g. 8D process, 4W1H, 5-why, fishbone diagram and etc. – That is QIT CAPA Management System!

QIT Corrective & Preventive Action (CAPA) Software is a web-based 8D CAPA system with a built-in Corrective Action Template, Corrective Action Forms, and Corrective Action Reports for all businesses. With QIT Corrective Action Software, you can:
- Collect data and form teams easily
- Identify the root cause of any problem with proven methods
- Implement effective actions and monitor their impact
- Generate reports and share them with stakeholders
- Comply with industry standards and regulations
Don’t let problems slow you down or cost you money. Try QIT Corrective Action Software today and see the difference for yourself. Click here to get a free demo and a special offer!
Corrective Action Plan and Root Cause Analysis Form

Copyright © 2024 QIT Consulting, Inc.. All rights reserved. Home | Privacy Policy | Site Map
- Enterprise QMS Solution
- Corrective Action Solution
- CRM & Complaint Management
- Audit Management
- Document Control Solution
- Training Management Solution
- Supplier Management
- Process Engineering
- Quality Assurance
- Other Services
- Our Mission
- QIT Guiding Principles
- Customer Testimonials
Quality Support Group

Basic Problem Solving Workshop
Course Description When failure occurs, we demand a rigorous process of investigation be initiated to identify why it occurred. Problem Solving is a process that investigates and solves problems, identifies causes, takes corrective action, and prevents recurrence of the root causes. The ultimate purpose of problem solving is to ensure the problem can never be experienced again. Problem solving can be applied in many disciplines, including:
- Manufacturing
- Product Design
- Testing Verification and Validation
- Distribution, Shipping, Transport and Packaging
- Use-Applications
As everyone probably knows, “perfect” is a rare state. Problems pop up from time to time and people need to solve them. As a result, it is important that people become effective problem solvers. Having a workforce with well-developed problem-solving skills is a significant competitive advantage for a company.
All people can benefit from strong problem-solving skills. However, those skills don’t come “built-in” to every person. And even those with a natural knack for it can always get better or learn to apply those skills more effectively in each work circumstance. As a result, it’s a good idea to provide resources to help people develop and use problem-solving skills at work.
Why “Problem Solving for Employees” Matters:
- Employees should recognize the importance of being good problem solvers.
- Understanding the positive impact of employee problem solving increases workplace productivity.
- Identifying the basic steps in the problem-solving process helps employees manage problems efficiently when they do arise.
- Using effective problem-solving techniques on the job keeps problems from reoccurring.
Who Should Attend This course is designed for production employees, managers, and supervisors.
Learning Objectives Through training, participants will learn to:
- Describe the problem
- Formulate an accurate problem statement
- Apply root cause analysis tools
- Implement potential solutions
Course Outline The problem-solving process has four major parts:
1. Grasp the Situation During the first part of the problem-solving process, Grasp the Situation, participants learn to:
- Identify the problem
- Clarify the problem
- Use the 5W2H tool
2. Cause Investigation During Cause Investigation, participants learn to use several Root Cause Analysis (RCA) tools, including:
- Conducting a “5-Why” investigation to identify the root cause
- Is/Is-Not Techniques
- Cause & Effect Diagrams
3. Problem Correction Problem Correction involves the use of specific actions to correct the problem. Participants learn to implement short-term temporary measures (required to protect their customers) and follow with longer-term corrective actions.
4. Prevention In the fourth and final part of the problem-solving process, participants learn to take specific actions to make sure a problem cannot recur, typically through error proofing and capturing the lessons learned.
Prerequisites None
Course Format 8 hours (8:30am-4:30pm EST or 2 x 4-hour virtual sessions) Combination lecture and classroom exercises Available virtually, at QSG’s training facilities or on-site at your organization Course Instructor: Dave Margil – Consultant, Lean Six Sigma , Jim Wasson – Consultant, Lean Six Sigma/Process Improvement
8:30am-4:30pm (EST)
Course Evaluations Set 1 Course Evaluations Set 2 Course Evaluations Set 3 – Montreal Course Evaluations Set 4
Follow QSG on LinkedIn ! Become a QSG Member today!
Always Keep Improving!
If you have any questions, would like more information, or would like to speak with a QSG representative, please contact us at any time!
More From Forbes
Leveraging systems models: a strategic advantage for it professionals.

- Share to Facebook
- Share to Twitter
- Share to Linkedin
Thomas Lim is the Vice-Dean of Centre for Systems Leadership at SIM Academy. He is an AI+Web3 practitioner & author of Think.Coach.Thrive!
IT professionals increasingly need to navigate projects arising from greater business complexity. The integration of systems models with established methodologies, like design thinking, agile and lean, presents a unique opportunity for IT experts to enhance their capacity and expertise. This systemic integration not only enriches their problem-solving tool kits but also ensures the delivery of innovative, sustainable solutions that align with the strategic objectives of their organizations.
The landscape of IT projects has expanded beyond straightforward software development to include complex ecosystems involving artificial intelligence (AI), cloud computing, big data and more. This complexity necessitates a holistic view of project management and solution development, where understanding interdependencies and emergent behaviors becomes crucial. Systems models, with their focus on the interrelations within and among systems, offer a comprehensive framework for analyzing and addressing these complexities.
Enhancing Design Thinking With Systems Thinking
Within the Design Thinking phases, there are opportunities to embed systems thinking models. For example, during the Ideate phase, using causal loops would help clarify the Theory of Success.
Agile methodologies emphasize flexibility, rapid iteration and stakeholder collaboration. Integrating systems dynamics into agile practices allows IT professionals to model and simulate the behaviors of complex systems over time. This predictive capability can inform sprint planning, risk management and the prioritization of features based on their potential impact on the system. By understanding the feedback loops and causal relationships that drive system behavior, IT teams can anticipate challenges and opportunities, leading to more informed decision-making and effective agile implementation.
Diagnosing With The Levels Of Perspective Model
The Levels of Perspective Systems Model categorizes viewpoints from which a system can be analyzed, ranging from concrete events to deep-rooted structures and mental models. This hierarchical framework includes the Events level, Patterns of Behavior level, Structural level and, sometimes, the Mental Models level. Each level offers a unique lens through which IT developers can understand and address complex challenges.
Enhancing Design Thinking
Design thinking emphasizes empathy, collaboration and iterative learning to solve problems creatively. By applying the Levels of Perspective Model, IT developers can deepen their empathetic understanding by recognizing not only the immediate needs (Events level) but also the underlying patterns and behaviors of users (Patterns of Behavior level). This approach allows developers to design solutions that are more closely aligned with users' evolving behaviors and preferences. Additionally, considering the Structural and Mental Models levels enable developers to identify and challenge assumptions about what users need or value, leading to more innovative and user-centric solutions.
Complementing Agile Methodologies
The Levels of Perspective Model can enhance agile practices by encouraging developers to look beyond the immediate backlog of tasks (Events level) and consider the broader patterns of team dynamics and project progress (Patterns of Behavior level). This wider perspective can help in anticipating challenges and opportunities for improvement.
Stacking Systemic Choices Using The Hierarchy Of Choices
The Hierarchy of Choices model offers a structured approach to decision-making that can greatly enhance the effectiveness of IT developers. By delineating decisions across five levels—fundamental, primary, secondary, tertiary and other choices—this model provides a comprehensive framework that aligns closely with design thinking and agile and lean methodologies, enhancing developers' capacity to deliver impactful, user-centered solutions efficiently.
Fundamental Choice: The Purpose Behind Existence
At the core of every IT project is the fundamental question: Why does this project exist? This aligns with the empathetic core of design thinking, which starts with understanding the user's needs and challenges.
Primary Choice: Defining Desired Outcomes
What results does the project aim to achieve? Identifying primary choices involves setting clear, measurable goals, a principle that resonates with the outcome-focused nature of agile methodologies. For developers, defining these outcomes provides a clear direction for the project, facilitating prioritization and helping to maintain focus on delivering value to the end-users.
Secondary Choice: Crafting The Strategy
Deciding on the strategy—how the project will achieve its goals—ties into lean thinking, which emphasizes value streams and waste elimination. For IT developers, understanding the chosen strategy informs the selection of technologies, architectural patterns and development practices that align with project goals. This strategic alignment ensures that resources are optimized and efforts are directed toward activities that directly contribute to the project's objectives.
Tertiary Choice: Selecting Tactics
Tactical choices concern the specific actions taken to implement the strategy. This is where agile practices shine, offering a flexible framework for iterative development, continuous integration and regular feedback loops. Developers, by making informed tactical decisions, can adapt to changes quickly, experiment with solutions and refine their approach based on real-time feedback, all while ensuring alignment with the overarching strategy.
Finally, the model includes a broad category for other choices, encompassing the operational decisions related to the what, where, how and when of project execution.
The Road Ahead
As IT professionals strive to navigate the complexities of modern projects, the integration of systems models with traditional methodologies like design thinking, agile and lean offers a powerful synergy. This systemic integration enables a holistic understanding of complex environments, fosters innovative problem-solving and supports the agile adaptation to change. By embracing these integrated approaches, IT professionals can elevate their expertise, deliver impactful solutions and achieve strategic alignment in their projects, ensuring their role as key drivers of digital transformation.
In conclusion, the relevance of systems models in the IT domain cannot be overstated. As we advance into a future where projects become increasingly complex and interconnected, the ability to integrate and apply these models alongside established IT methodologies will be a defining skill for IT professionals. This systemic integration not only enhances their capacity to address current challenges but also positions them to lead the way in shaping the digital landscapes of tomorrow.
Forbes Coaches Council is an invitation-only community for leading business and career coaches. Do I qualify?
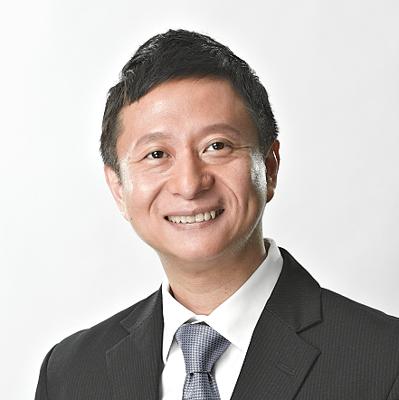
- Editorial Standards
- Reprints & Permissions
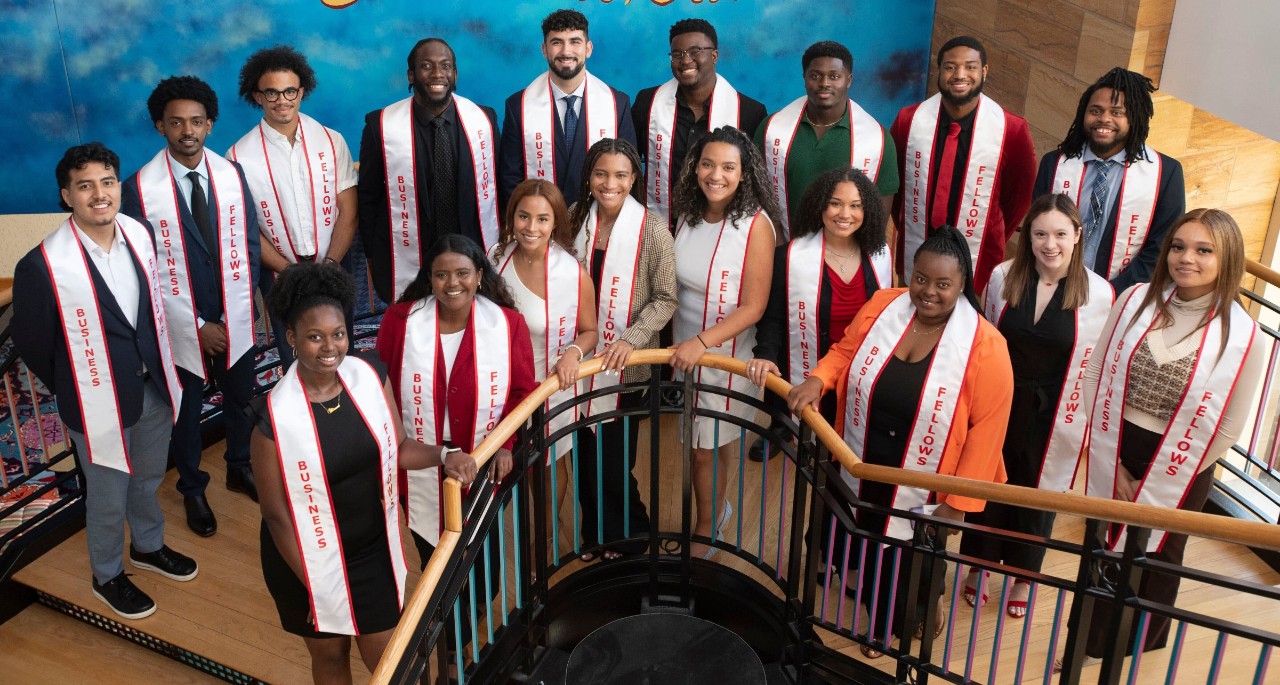
The 2024 Toast recognizes achievements of Lindner’s Business Fellows
Students saluted for accomplishments inside and outside of the classroom.
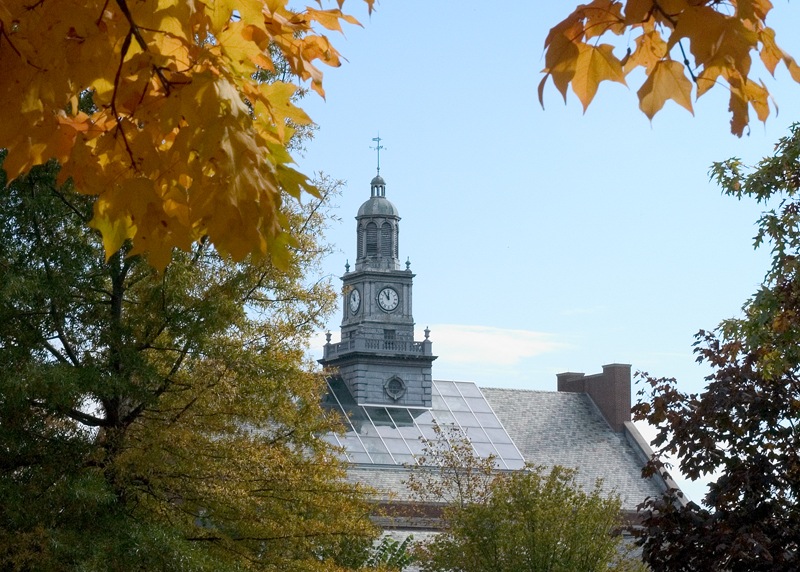
The Carl H. Lindner College of Business Office of Inclusive Excellence hosted its annual Toast event for the Business Fellows program April 18 at The Graduate Hotel Cincinnati.
Students, Lindner staff and faculty, alumni, corporate partners and community leaders attended the celebration of the Business Fellows graduates. Business Fellows supplies underrepresented students with wraparound support to attain professional and personal success, while facilitating a culture of inclusion and belonging at Lindner and UC.
Nick Castro , assistant dean, Office of Inclusive Excellence, expressed gratitude to attendees for being pieces of Business Fellows’ “big puzzle” in his opening remarks.
From left: Eugene Burse, BBA ’26; Kyle Caisaguano, BS ’24; Ejiro Agoba, BS ’24; Hailey Manuel, BBA ’26, Quincy Allfree, BBA ’24; Briana Jarrell, BBA ’24; and Julian Hill, BBA ’23.
“When you put that puzzle together, what we have is our Business Fellows being supported and successful. Whether you are part of an advisory group, the Dean's Cabinet, a donor or a scholarship supporter, a faculty or staff member, or a family member, everybody in this room has impacted each other in some way, shape or form. And I think those are positive ways, shapes and forms.”
Castro then introduced WCPO reporter Raven Richard, who emceed the Toast for the third successive year. After acknowledging past and current Business Fellows Executive Board members, Richard thanked the event’s leadership sponsors: PNC Bank, Truepoint Wealth Counsel and Western & Southern Financial Group. Also recognized were companies who have sponsored the Office of Inclusive Excellence throughout the current academic year.
- Sycamore Capital
- MassMutual Ascend
- Cardinal Health
- Protective Life
- Sherwin Williams
Dean Lewis spotlights career trajectories, problem solving
Lindner Dean Marianne Lewis, PhD, stands with representatives from Cintas, sponsors of Lindner’s Office of Inclusive Excellence.
Lindner Dean Marianne Lewis , PhD, delivered the keynote address, touching on Business Fellows' origins and its growth before coaching the students on career progression.
“It’s going to start slow, and you’re going to build your network. You’re going to start developing your skills. You’re really going to know your job, and it’ll get easier, faster — and it will be amazing what you can do. A big part of that climb is innovation. It’s about problem solving with creativity, collaboration and some push.”
Lewis also spoke about interacting with Business Fellows alumni, rising expectations and ambitions, and more.
“They talked about the challenges and opportunities of the rungs in your ladders. Some of us don’t have all the rungs, and it’s awfully hard to get from rung to rung when you’re missing six in between. And they made the point that Business Fellows was vital for their rungs. The corporate partners and alumni were vital for their rungs. (Last week) they were saying, ‘We want to be rungs.’ And I share it with you because I hope we can all remember that we can be someone’s rung.”
“If we are going to truly model a culture of inclusive excellence, we need to be reaching out to others who don't have all the rungs. Because, from what we've learned, we know we have a special sauce to help make it happen. We know how to do the wraparound support.”
“Our expectations are rising. Our ambitions are rising. And, together, we will keep rising. I’m grateful to have a community that we can continue to push the envelope with in so many special ways.”
Student honors
Richard returned to the stage to announce the evening’s awards, beginning with the PACE Honors. The PACE Honors recognize students who best exemplify Professionalism, Academics, Character and Engagement (PACE) , principles essential to student development at Lindner. The following students were acknowledged in this category:
- Professionalism: Eugene Burse, BBA ’26
- Academics: Kyla Ward, BBA ’27
- Character: Matt Santiago, BBA ’25
- Engagement: Nariah Edwards, BBA ’26
Business Fellows was, is and will always be one of the main reasons why I know I belong. Once you feel and begin to treasure this relatedness through belonging, the mindset becomes being the best person you can be, so that you may inspire your loved ones.
Joshua Moore, BBA ’23
Next, outstanding first-, second-, third- and fourth-year students were honored for their passion for the Business Fellows community and its resources. The following students were recognized in this category:
- First Year: Mirsayah Wasnuk, BBA ’27
- Second Year: Hailey Manuel, BBA ’26
- Third Year: Gabe Galiatsatos, BBA ’25
- Fourth Year: Quincy Allfree, BBA ’24
The Fellows Impacting Fellows honor was bestowed upon Prince Kalala, BBA ’24, for going above and beyond in impacting his peers with mentoring and relationship development.
Celebrating seniors, the Toast
After an invocation of gratitude from Quincy Allfree, BBA ’24, and dinner and lighthearted conversation, Richard returned to the stage to individually honor graduating Business Fellows, who received a commemorative plate and a stole to wear at graduation.
- Paola Alcantara
- Quincy Allfree
- Zachary Bahri
- Savana Berhane
- Kyle Caisaguano
- Samoya Cochrane
- Lance Entsuah
- Saron Eyouel
- Holly Giese
- Julian Hill
- Tierra Hudson
- Brianna Jarrell
- Prince Kalala
- Kendall Kelly
- Joshua Moore
- Dagim Negash
- Elizabeth Piper
- Kayla Stone
- Alexia Thomas
Joshua Moore, BBA ’23, raised his glass to his fellow Business Fellows after delivering the closing toast.
Joshua Moore, BBA ’23, delivered the closing toast with heartfelt remembrance and thoughtful perspective of his time with Business Fellows.
“Business Fellows was, is and will always be one of the main reasons why I know I belong. Once you feel and begin to treasure this relatedness through belonging, the mindset becomes being the best person you can be, so that you may inspire your loved ones.”
Moore ended with advice for younger students.
“Please don’t view Business Fellows as just another club, because trust me, if you put the time in, it will give you so much more beyond academia and professionalism. It will make you a better person, a better friend, a better teacher, and so much more.”
Featured image at top: 2024 Business Fellows graduating seniors. Photos/Joseph Fuqua II.
Interested in Business Fellows?
The Business Fellows program provides underrepresented students from a range of backgrounds with wraparound support to achieve professional and personal success. Through career connections, community and leadership development, Business Fellows empowers future business leaders to solve problems that matter and advances a culture of inclusion and belonging within Lindner and at the University of Cincinnati.
- Lindner Diversity & Inclusion
- Lindner College of Business
- Business Fellows
Related Stories
The toast celebrates business fellows graduates, award winners.
April 14, 2022
The University of Cincinnati Carl H. Lindner College of Business and its supporters recognized the impressive accomplishments of the Business Fellows during The Toast last week at the Graduate Cincinnati.
April 25, 2024
Lindner Business Fellows homecoming event puts growth on full display
October 24, 2023
The Carl H. Lindner College of Business’ Office of Inclusive Excellence hosted current students, alumni and supporters from across the university to celebrate the office’s signature Business Fellows program on Oct. 12. The event also recognized the program’s founders and early champions.
- Work & Careers
- Life & Arts
Become an FT subscriber
Try unlimited access Only $1 for 4 weeks
Then $75 per month. Complete digital access to quality FT journalism on any device. Cancel anytime during your trial.
- Global news & analysis
- Expert opinion
- Special features
- FirstFT newsletter
- Videos & Podcasts
- Android & iOS app
- FT Edit app
- 10 gift articles per month
Explore more offers.
Standard digital.
- FT Digital Edition
Premium Digital
Print + premium digital, weekend print + standard digital, weekend print + premium digital.
Today's FT newspaper for easy reading on any device. This does not include ft.com or FT App access.
- 10 additional gift articles per month
- Global news & analysis
- Exclusive FT analysis
- Videos & Podcasts
- FT App on Android & iOS
- Everything in Standard Digital
- Premium newsletters
- Weekday Print Edition
- FT Weekend Print delivery
- Everything in Premium Digital
Essential digital access to quality FT journalism on any device. Pay a year upfront and save 20%.
- Everything in Print
Complete digital access to quality FT journalism with expert analysis from industry leaders. Pay a year upfront and save 20%.
Terms & Conditions apply
Explore our full range of subscriptions.
Why the ft.
See why over a million readers pay to read the Financial Times.
International Edition

IMAGES
VIDEO
COMMENTS
Most corrective action procedures use a variation of 8D problem solving. The following are some of the types of steps in a corrective or problem solving process: Promptly identify and document the problem. Use 5 Why questioning to acquire details and determine if this is an isolated event or if it is significant and has the potential to recur.
Corrective and Preventive Actions (CAPA) tools serve as invaluable instruments, allowing organizations to identify, analyze, and eliminate the root causes of problems. This comprehensive exploration delves into the world of CAPA tools, understanding their significance, exploring various types, and elucidating their role in fostering a culture of continuous improvement.
Step 1: Identification. The first step of taking corrective action is to identify existing issues or non-conformity. These can come in various forms such as customer feedback or complaints, internal audits, external audits from customers who review your processes, government regulator audits, or internal performance metrics. Most medium to ...
A3 thinking involves the practice of consolidating the problem, analysis, countermeasures, and action plan onto a single sheet of paper, commonly an A3-sized sheet. This brief document serves as a summary of the project at hand and is regarded as a valuable storytelling tool for project communication. Utilizing the A3 approach doesn't require ...
CAPA stands for 'corrective and preventive action'. As the name suggests, CAPAs are about problem-solving. And it's a two-step process: when something goes wrong, a CAPA is executed to fix ('correct') the immediate issue, then to 'prevent' it reoccurring with some tweak or improvement that addresses the cause. CAPA definition
Learn how to define the problem, assess conditions for root causes, define proper actions to contain and prevent the problem, and then develop a plan to deploy those actions. Common methods, including the 8D approach, are covered and tools for performing incident and root cause analysis, and the use of various CAPA checklists, are provided.
Challenge #4: Failing to reference the tools you do use in your CAPA procedure, thereby opening the door to regulatory scrutiny; Since each company faces its own set of challenges, prescribing a universal set of solutions is impossible. A solution for one organization can end up introducing more problems when applied the same way in another ...
A CAPA is a systematic process to identify, investigate, and resolve issues that arise during product development, manufacturing, or service delivery: Take corrective actions to address existing problems and implement preventive measures to avoid future occurrences. The primary goal of a CAPA is to improve processes, maintain product quality ...
Learn how to define the problem, assess conditions for root causes, define proper actions to contain and prevent the problem, and then develop a plan to deploy those actions. Common methods, including the 8D approach, are covered and tools for performing incident and root cause analysis, and the use of various CAPA checklists, are provided.
Using CAPA to resolve non-conformance events and determine the root cause is an important problem solving tool for a business. It forces a team to review the correction, determine if corrective actions are considered effective, and then validate the successful impact of the corrective action.
Manufacturers have a variety of problem-solving tools at hand. However, they need to know when to use which tool in a manner that is appropriate for the situation. In this article, we discuss 7 tools including: ... In this CAPA webinar, learn various regulations governing Corrective and Preventive Actions (CAPA) and how organization should ...
improvements. The framework emphasizes the adoption of a risk-based approach to problem solving and the need of leadership engagement to allocate resources to solve those issues that are high risk, issues which are closest to and could impact the customer or patient. Similarly. streamlined CAPA requirements for internal issues is intended
This course aims to teach you everything there is to know about CAPA system & 8D problem solving and how to create CAPA file from Scratch! Apart from that you will also learn about various lean six sigma and continuous improvement tools such as DMAIC, PDCA cycle etc. which will help one to acquire a Lean six sigma white or yellow belt.
It's a systematic approach to solve the problem. CAPA tool is not a problem-solving tool it acts as an improvement tool also. CAPA is also known as 8D Problem solving method. Corrective Action & Preventive Action from Phase 1 to Phase 8. Is the CAPA (Corrective Action & Preventive Action) process mandatory as per ISO 9001, TS16949, and other ...
The corrective and preventive action is designed by a team that includes quality assurance personnel and personnel involved in the actual observation point of non-conformance. It must be systematically implemented and observed for its ability to eliminate further recurrence of such non-conformation. The Eight disciplines problem solving method ...
3. A3 Problem Solving Approach. 4. Eight Disciplines or 8D Problem Solving Approach. Depending upon the complexity of the problem you can choose one of these approaches. While taking these approaches, there are many tools and techniques which could be applied. I will cover many such tools, for example: 1.
Introduction to the CAPA and Problem Solving Process During this session, participants will learn how to integrate problem solving processes in their own initiatives and make their CAPA program a valuable and meaningful tool for realizing cost savings and process improvement. The problem-solving process has four major parts: 1. Grasp the Situation
The 8D problem solving process is a detailed, team oriented approach to solving critical problems in the production process. The goals of this method are to find the root cause of a problem, develop containment actions to protect customers and take corrective action to prevent similar problems in the future. The strength of the 8D process lies ...
Essentials. Problem Solving & Decision Making for Corrective and Preventive Actions (CAPAs) is an FDA-recognized, step-by-step approach to close out deviations with complete, well-documented investigations. Through this workshop, you'll learn how to respond to deviations with a process that is focused, rapid, and fully documented.
8D Approach | 8D Problem-Solving Steps. 8D Step - D1: Establish the Team. D2: Defining the problem. D3: Containment or Interim Actions. D4: Identifying & Verifying Root Cause. D5: Identify Permanent Corrective Actions-PCA. D6: Implementing the Permanent Corrective Action. D7: Preventive Actions.
Corrective and preventive action (CAPA), also called corrective action / preventive action or simply CAR, is a problem solving tool that will help you identify key issues, facilitate the root cause analysis process, and monitor the improvement actions.
The problem-solving process has four major parts: 1. Grasp the Situation. During the first part of the problem-solving process, Grasp the Situation, participants learn to: Identify the problem. Clarify the problem. Develop a problem statement. Use the 5W2H tool. 2.
The eight disciplines (8D) model is a problem solving approach typically employed by quality engineers or other professionals, and is most commonly used by the automotive industry but has also been successfully applied in healthcare, retail, finance, government, and manufacturing. The purpose of the 8D methodology is to identify, correct, and ...
The integration of systems models not only enriches IT experts' problem-solving tool kits but also ensures the delivery of innovative, sustainable solutions.
Celebrating seniors, the Toast. After an invocation of gratitude from Quincy Allfree, BBA '24, and dinner and lighthearted conversation, Richard returned to the stage to individually honor graduating Business Fellows, who received a commemorative plate and a stole to wear at graduation. 2024 Business Fellows graduates. Paola Alcantara.
That means someone buying an averagely priced house on a five-year fix at 4.84 per cent and currently paying around £1,300 per month might be stress tested to make sure they can afford a 9.5 per ...