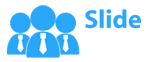
Researched by Consultants from Top-Tier Management Companies

Powerpoint Templates
Icon Bundle
Kpi Dashboard
Professional
Business Plans
Swot Analysis
Gantt Chart
Business Proposal
Marketing Plan
Project Management
Business Case
Business Model
Cyber Security
Business PPT
Digital Marketing
Digital Transformation
Human Resources
Product Management
Artificial Intelligence
Company Profile
Acknowledgement PPT
PPT Presentation
Reports Brochures
One Page Pitch
Interview PPT
All Categories

How to Implement Kaizen: 19 Kaizen PPT Templates to Guide You

Anuj Malhotra

Kaizen is a Japanese philosophy that believes “change is good”. “Kai” means change and “zen” means good. In business settings, Kaizen is also a strategic tool that brings about continuous improvement, in terms of increased productivity, superior quality, lower costs, efficient processes, increased safety, and better customer experience. The word “Continuous” is worth remembering here as Kaizen is a never-ending improvement process.
The Kaizen story began after World War II when Toyota started implementing quality circles in its production processes. A group of workers identified the problems, analyzed, and proposed solutions to improve productivity. “The Toyota Way” later became extremely popular in the western world thanks to the work of Masaaki Imai who published his book Kaizen: The Key to Japan's Competitive Success in 1986. The book was translated into 14 languages making Kaizen a must for any organization that wishes to bring significant improvements in their processes without making any big, radical changes.
5S of Kaizen
To support continuous improvement, Kaizen theorists recommend practicing 5S which will lead to standardized processes, better time management, improved work culture, and an increase in employee satisfaction. These 5S are - Sort, Set in Order, Shine, Standardize, and Sustain. This slide elaborates upon the 5S framework:

Download Kaizen 5S Framework
Kaizen principles: summary.
- Team effort - Implementing Kaizen is not just the job of one person or higher-ups in the management but involves each and every member of the organization.
- Good processes - Kaizen believes that good processes bring good results. If any department is performing poorly, it’s the process and not the people that are at fault.
- Focus on small, continuous changes - Kaizen practitioners believe that small, continuous changes bring much better results than a few drastic, big-level changes.
- See it to believe it - Kaizen practice tells you to visit the place of operation to see first hand the problems experienced and processes followed.
- Elimination of waste - The basic objective of Kaizen is to eliminate waste called “Muda”. It guides a business in identifying these 3 MUs - Muda (waste), Mura (inconsistency), and Muri (strain on people and machines). Here’s a slide that shows the difference between the three:

Grab this Presentation Slide
Are you following the Kaizen way in your organization? Whatever industry your business belongs to - finance, healthcare, IT, or any other - you stand to gain a lot with Kaizen. Here are 19 Kaizen PowerPoint Templates to help you get started and document all your efforts for everyone in the organization to see:
Download the Complete Kaizen PowerPoint Presentation
Implementing kaizen: step by step guide.
The system for implementing Kaizen is called the PDCA Cycle, an iterative model of change comprising four stages - Plan, Do, Check, and Act. It is a continuous activity that has to be repeated again and again. This model is also known as the Deming cycle, Shewhart cycle, and plan–do–study–act (PDSA) model.

Download PDCA Cycle PPT Slide
Stage 1 - plan.
1.1 - Write the Problem Statement
Identify which area or department requires improvement. Is customer care getting poor reviews? Also, identify the Key Performance Indicators that show there is an actual problem. For instance, the average handle time is too high in the last quarter compared to the average handle time and so on.

Use this Problem Statement Template
1.2 - Identify Root Cause
Try to identify the reasons leading to poor performance. Remember everyone is involved in Kaizen, so you need to visit the call center, meet the customer care representatives face to face and ask them to share the problems faced and reasons for unproductivity. Thereafter, you might come to know that with the expansion of services, more manpower was needed but was not provided resulting in work pressure. Or they were not given proper training about the products and services resulting in confusion.
Also, listen to the call recordings and experiences shared by customers to see where the team is failing and identify areas of improvement.

Download this Presentation Slide
1.3 - Set Goals
Based on the initial data you have collected, set goals for improvement. Thereafter, while setting goals, try adhering to the SMART model i.e. the goals should be Specific, Measurable, Achievable, Relevant, and Time-Bound. For example, your goals could be to hire 50 new customer reps in a month, hold exhaustive training sessions twice a week, and reduce the average handle time from 5 minutes to 3.5 minutes.

Use this Goals PPT Template
1.4 - Prepare Detailed Action Plan
Now is the time to prepare a detailed action plan by involving all the stakeholders. If the goals require efforts by the HR department, team leaders, staff, or any specific department, involve them in preparing a detailed action plan. Try to answer the below 5Ws and 1H while doing so. The point is that it is a fact and data-driven and encompasses all the relevant criteria like time and ownership.

Download the Action Plan Template
Stage 2 - Do
2.1 - Collect and Analyze Data
We need hard facts and reliable data to recognize the patterns. Is the lower conversion on your site a seasonal fluctuation or has it been downhill after the introduction of the new interface? Data collected for the past few years helps you arrive at reliable conclusions.
You can use multiple data collection tools like interviews, online surveys, telephonic chats, field studies, and so on to collect the data. Kaizen recommends visiting the shop floor (the place where actual operations take place) to see for yourself the operation in action and identify problem areas. In lean manufacturing, this concept is called Gemba meaning “the real place”. Gemba kaizen suggests that whenever a problem occurs, visit the site and gather data from all sources. Therefore, this is the place where the best improvement ideas will come.
Collect data for all the KPIs you have identified like lead time, cycle time, average handle time, and so on.

Access the Above Slide Here
You can use seven basic Quality Tools at this stage for data analysis and presentation:
1. Checklist- A checklist or a checksheet is a simple way to analyze data. Rather than relying on memory, use a checklist to remember the things that need to be done or items that need to be obtained.

Download this Checklist PowerPoint Template
2. Control Chart - Are your processes under control or out of control? Use Control Charts to show how processes are changing over time. A control chart has a centerline (average), an upper limit line, and a lower limit line. Plot your data on this chart and compare the same with these lines to draw conclusions.

Download the Control Chart Diagram
3. Flow Chart - Visually represent the steps in a business process as it moves through various departments using a flow chart. Additionally, this removes any confusion and the process is clear to all.

Download the Flow Chart Diagram
4. Histogram - Show the variation in sets of data using Histograms. A histogram is often confused with a bar graph but unlike a bar graph, in a histogram, there are no spaces between bars. Show the frequency of data using the histogram below:

Download Histogram Slide
5. Scatter Diagram - Scatter Diagrams are basically line graphs but with no line. It is used to see whether a relationship exists between two items. Plot the cause on X-axis and the effect on Y-axis and interpret the data accordingly.

Download the Scatter Diagram
6. Cause and Effect Analysis - While analyzing and visually presenting the data, one can use the Cause and Effect Analysis diagram also known as the “ Fishbone ” diagram. Place the problem at the mouth of the fish and list the possible causes on the branches or bones of the fish. Thereafter, have main categories like people, equipment, policies, and procedures as the branches and put sub-causes on the sub-branches. It is a great visual to clearly see all major and minor causes of a problem.

Download Fishbone Diagram Template
7. Pareto Analysis - You may also use Pareto Analysis, a statistical technique based on the 80/20 rule. According to this rule, 80% of the problems stem from just 20% causes. While doing Pareto Analysis, you score each problem, group related problems together, and focus all your efforts on the most important causes while ignoring the smaller ones. Here’s a Pareto Chart template that you can use while doing your analysis:

Download Pareto Analysis Chart
2.2 Develop Solutions
After collecting and analyzing the data, it’s time for all team members to have an open brainstorming session to develop solutions to the problem. Thereafter, you need to follow all rules of brainstorming like participation by all, no criticism of any idea, no judgmental looks, and no limitations on the number of ideas a person can share. You can follow the most popular brainstorming techniques to have a fruitful discussion round.

Download the Solutions Slide
Stage 3 - Check
The solutions developed in the previous stage need testing for effectiveness. Upon testing and measurement, you need to:
3.1 - Ensure Goals are Satisfied
Are the goals set in the first stage being met with the solutions suggested? If not, you need to develop more effective solutions or you need to reevaluate the goals set earlier. So you need to go back to reassess your goals and their accomplishment status.

Grab the Goals Assessment Slide Here
3.2 - Implement Solutions
The success in the trial phase now needs complete implementation to bring about Kaizen - change for good. The new way becomes the standard way and this becomes the baseline for further improvement. Maintain a standard operating sheet that will be followed by all. The standard operating sheet will lay out the work sequence, the finishing time of the task, the inventory for smooth operation, and safety guidelines. Here is a standard operating sheet template that you can use:

Download the Standard Operating Sheet
Stage 4 - Act
Kaizen is a continuous process - a mindset for continuous improvement. So in this stage, you need to keep monitoring the solutions, improvise them and as bottlenecks emerge, repeat the cycle once again - Plan, Do, Check, Act. However, this should become a culture, a habit so that you never stagnate and keep improving and improving.
At the end of the first cycle, show the Kaizen before and Kaizen after so that everybody in the organization knows the result of their efforts:

Download the Kaizen Report Form
Got your dose of motivation from this simple but powerful philosophy to bring your business on the path of improvement? Get started by using the Kaizen ppt templates and process we have compiled under one PowerPoint file for you.
Try out our latest designs for inspiration…
There is no dearth of creative designs at SlideTeam. So when it comes to raising business efficiency to the maximum, the answer is our well-crafted Kaizen templates and slides. An epitome of instructional design and informative content, these templates will help you set your eyes on the right targets and strategies easily. Also, a key feature of all these stunning sets is their ease of use and practicality. So whether you are giving your team any updates on faster processing or teaching them how to eliminate waste, pick these templates to add that extra bit of efficacy to your presentations. Check out these five designs and click to download.
Shine the spotlight on the 3MUs and other Kaizen strategies with the help of this complete deck. Replete with catchy icons and editable graphics, this template will come in handy when you want to express more than the ordinary. So get your teammates on the same page and hit the ground running when you are planning for Kaizen to improve your business. Download the template below and deploy however you like.

Download this design
You can describe a project action plan or important points of the Kaizen strategy verbally. But what will really make a difference is presenting facts and figures with a help of good visual aids like this full-fledged Kaizen template designed by our experts. Take the help of this impeccable set to outline all important aspects that your team needs to work on when bringing in the Kaizen perspective to the table. Download and start personalizing this template right away.

Grab this design
Illustrate the difference between traditional and Kaizen modes of running a business with the help of this well-defined template. Containing just 12 slides, this template will help you explain key aspects of your strategy like event planning, process management, and the 5S framework. You can also highlight the reforms in the manufacturing process and general work practices to jack up those numbers. Plan ahead and present to perfection.

Should you feel the need to dive deep into Kaizen PDCA quality improvement techniques, you can download and deploy this handy template. You can also elucidate factors like objectives, evaluation schemes, and productivity to give your team a competitive edge over traditional businesses. Additionally, you can freely edit the contents of this 55-slide PPT template. Feel free to chuck out the slides you do not need. Also, personalize it as much as you like.

Let this functional Kaizen planning PPT template be your guide in the time of uncertainty. Download this 80-slide template detailing product management and quality control practices for your conglomerate. The visually-appealing design is also fully editable, so you can easily include your brand themes in your presentation. You can also rearrange the slides or reproduce the layout in the form of printed handouts for better clarity on the subject. So download it now!

So there you have it. Deploy these modern designs of the Kaizen framework for business planning and execution to ensure a smooth ride to success. Let us know what you think of these templates in the comments below.
Related posts:
- Comment mettre en œuvre Kaizen: 19 modèles Kaizen PPT pour vous guider
- Cómo implementar Kaizen: 19 plantillas PPT de Kaizen para guiarlo
- Mejore continuamente sus operaciones con nuestras 20 mejores plantillas Kaizen en PowerPoint PPT
- How to Design the Perfect Service Launch Presentation [Custom Launch Deck Included]
Liked this blog? Please recommend us

8 thoughts on “How to Implement Kaizen: 19 Kaizen PPT Templates to Guide You”
This form is protected by reCAPTCHA - the Google Privacy Policy and Terms of Service apply.
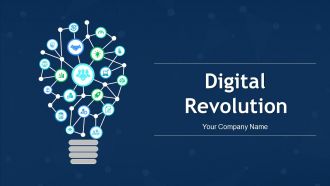
Digital revolution powerpoint presentation slides
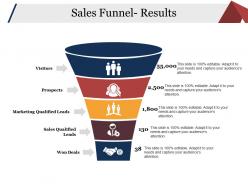
Sales funnel results presentation layouts
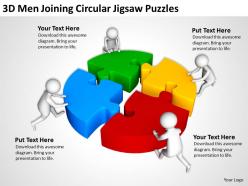
3d men joinning circular jigsaw puzzles ppt graphics icons
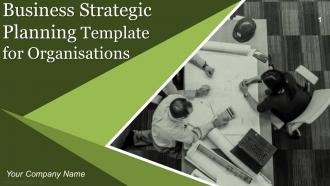
Business Strategic Planning Template For Organizations Powerpoint Presentation Slides
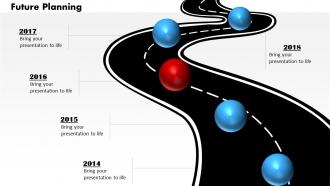
Future plan powerpoint template slide
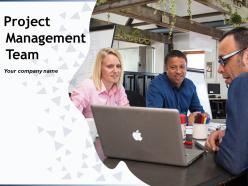
Project Management Team Powerpoint Presentation Slides
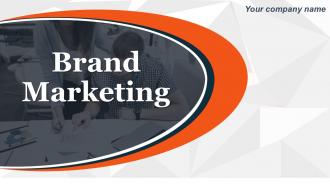
Brand marketing powerpoint presentation slides
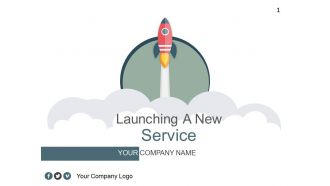
Launching a new service powerpoint presentation with slides go to market
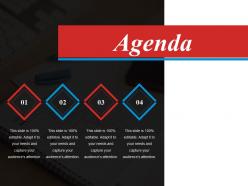
Agenda powerpoint slide show
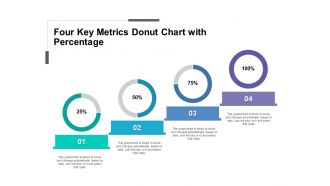
Four key metrics donut chart with percentage
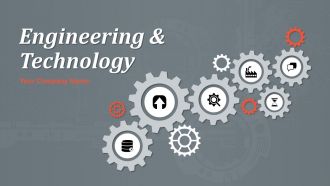
Engineering and technology ppt inspiration example introduction continuous process improvement
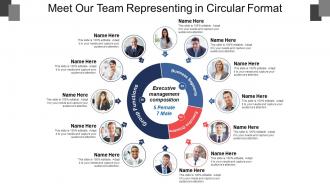
Meet our team representing in circular format

Got any suggestions?
We want to hear from you! Send us a message and help improve Slidesgo
Top searches
Trending searches
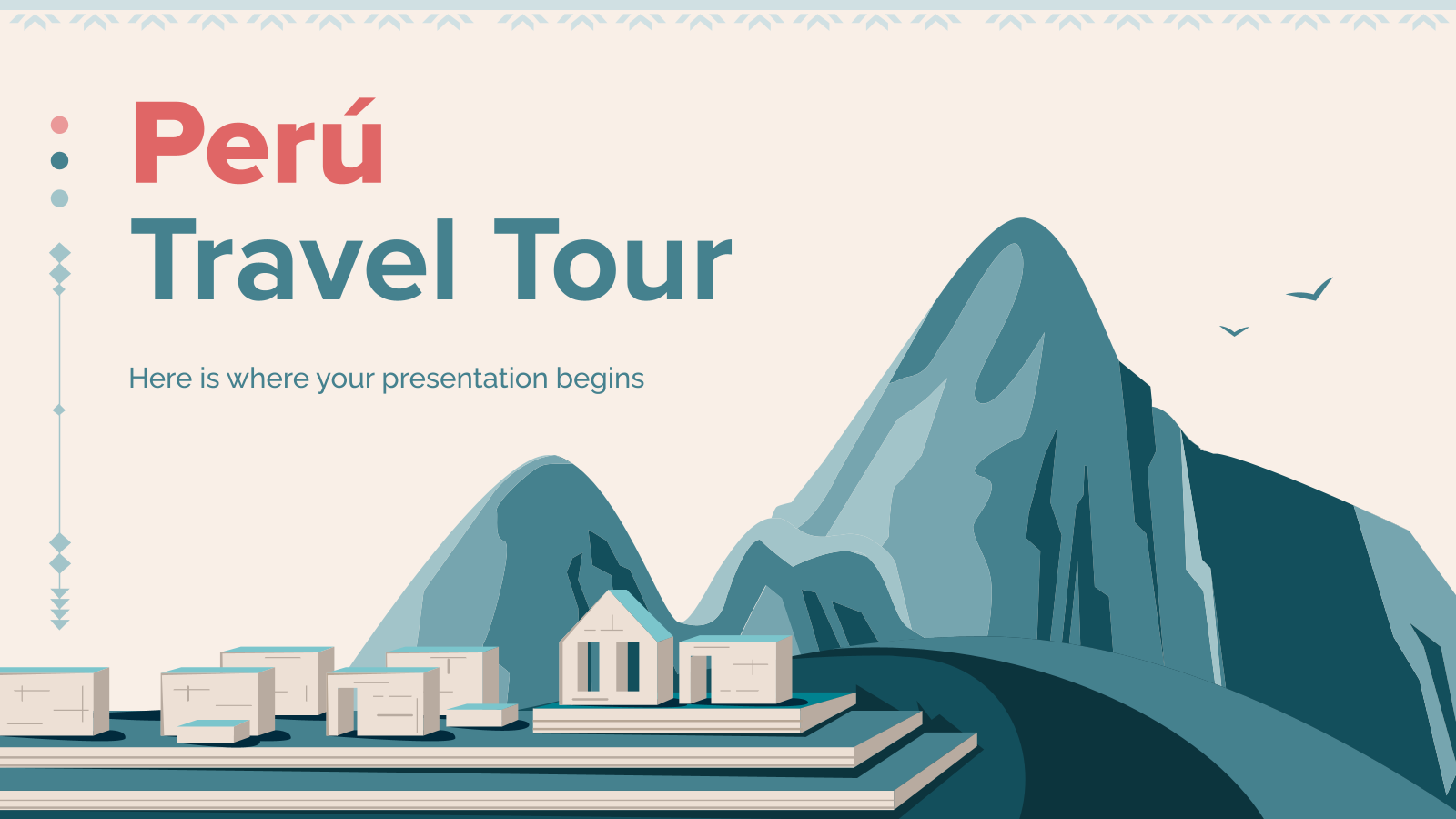
34 templates
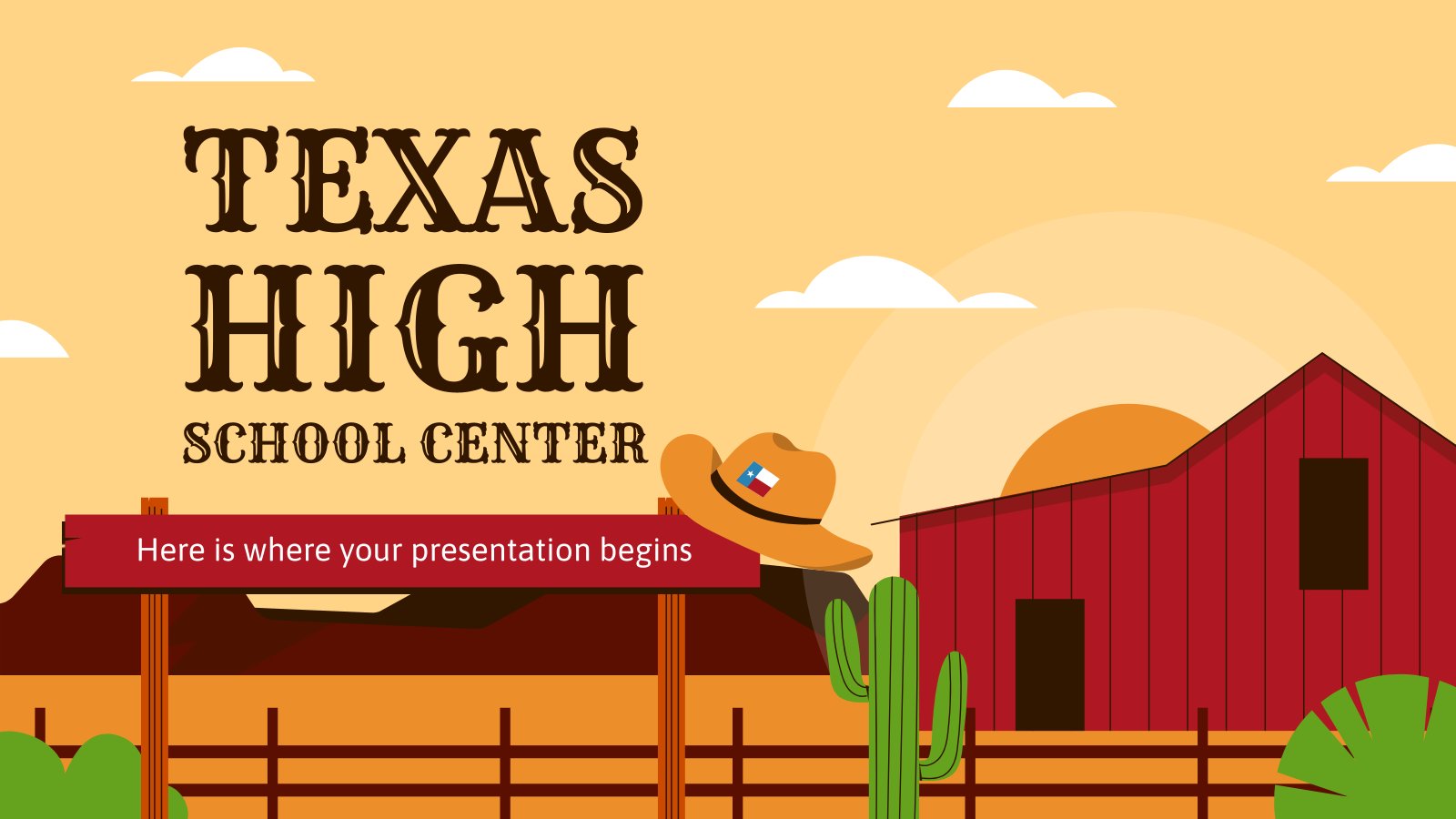
32 templates
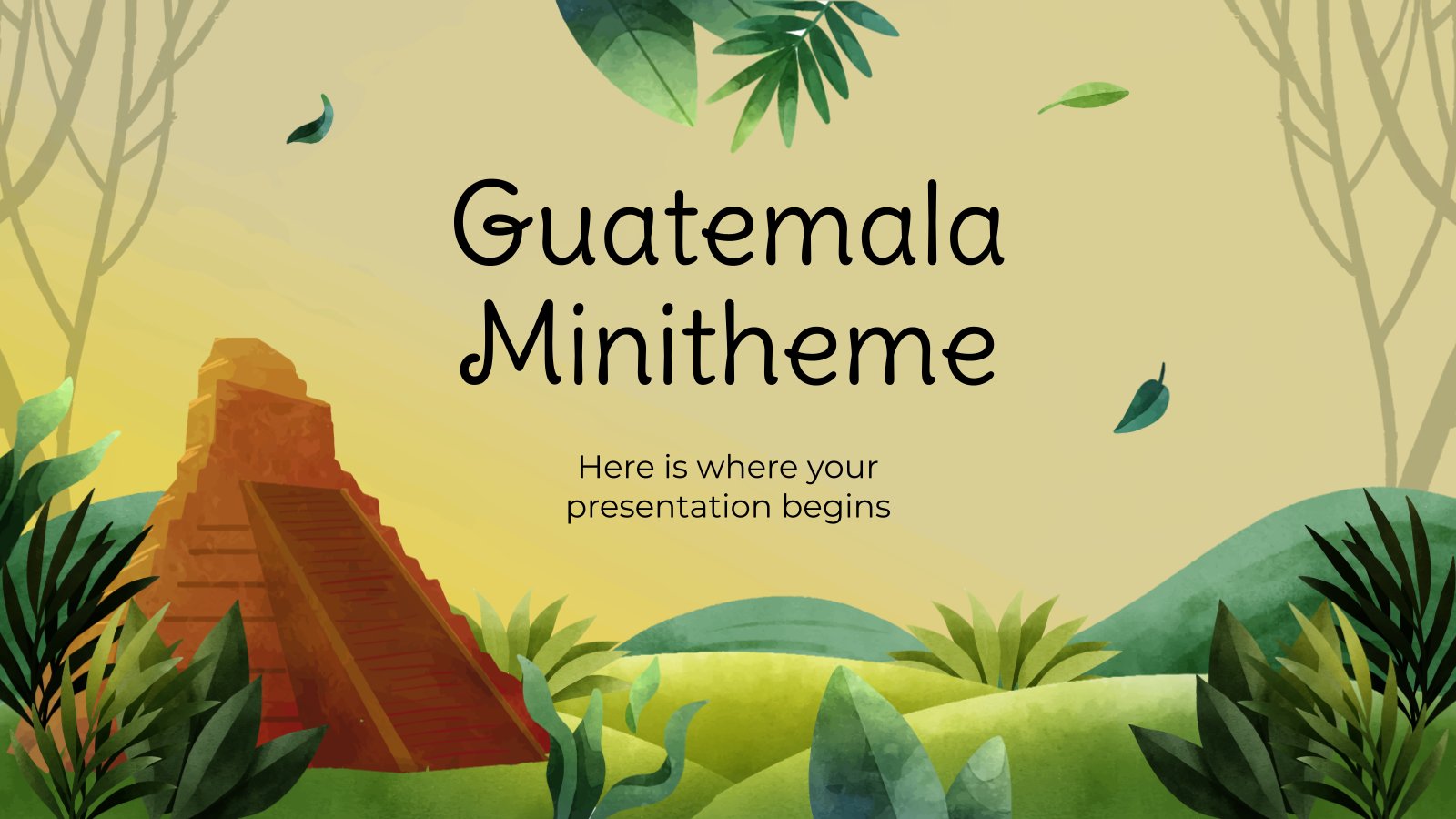
31 templates
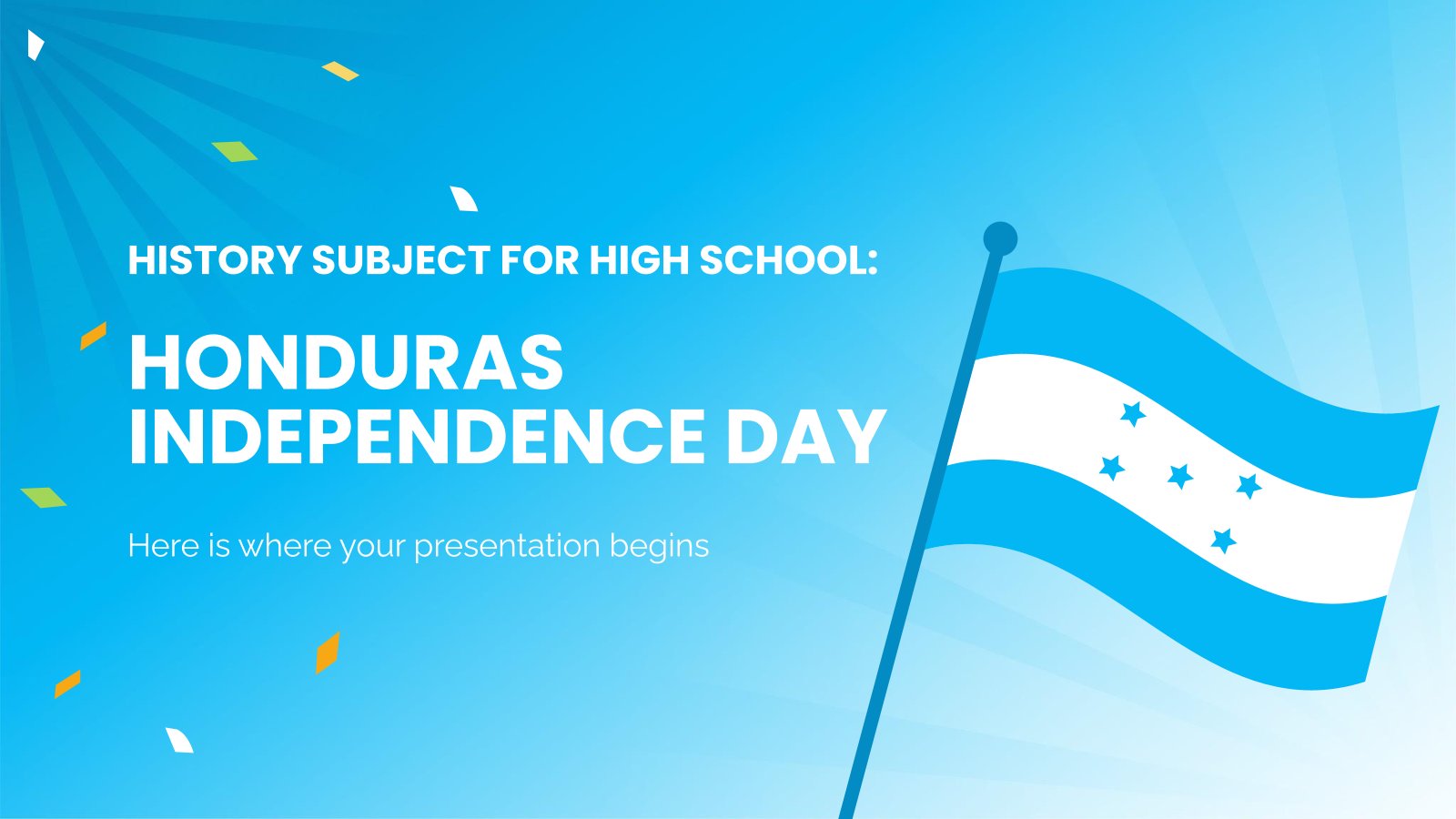
28 templates
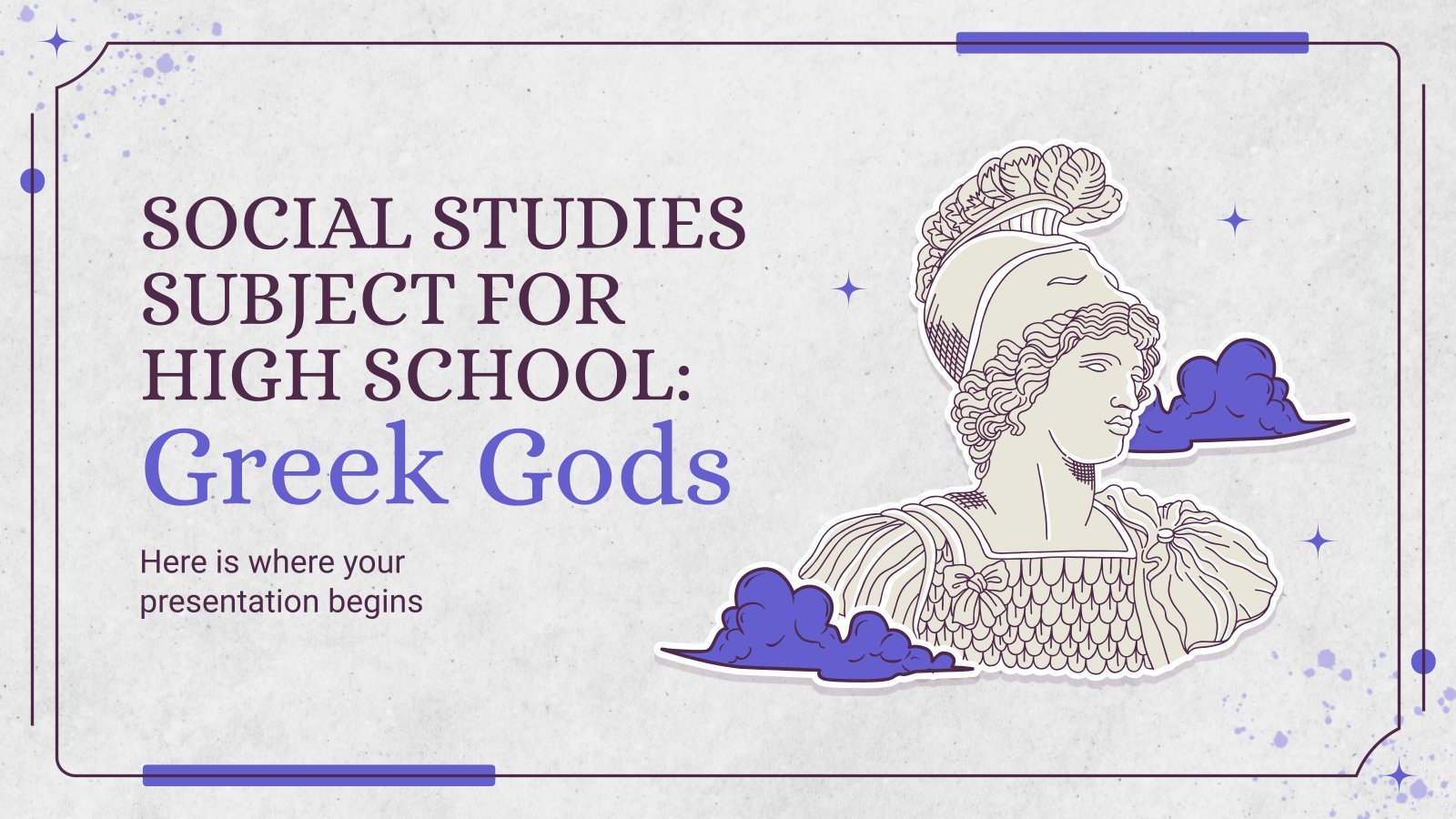
16 templates
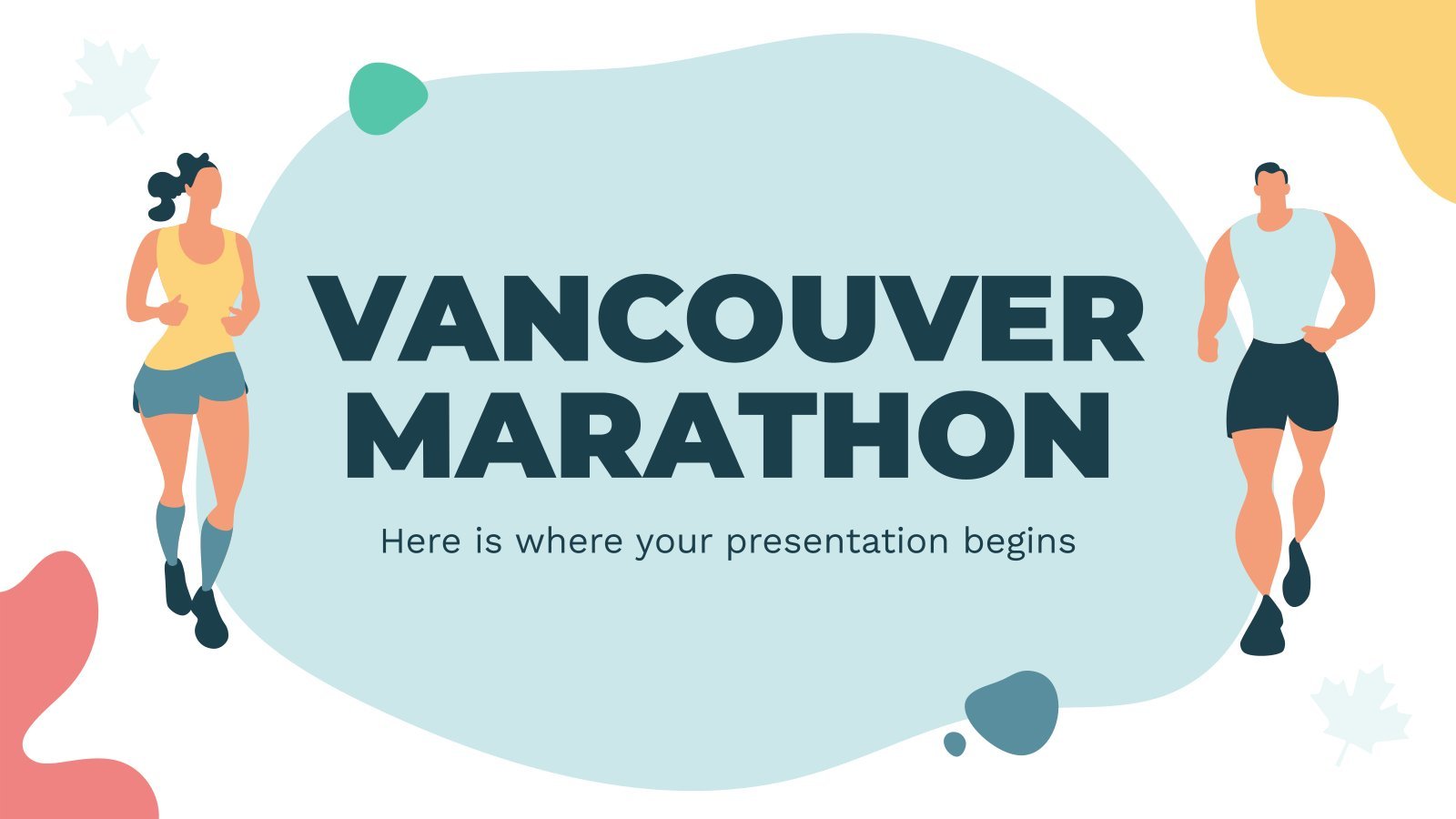
35 templates
Kaizen, Quality Management Method
Kaizen, quality management method presentation, free google slides theme and powerpoint template.
The Kaizen method is a philosophy of continuous improvement that has gained popularity in the business world. The concept is simple yet powerful: small, incremental changes lead to significant progress over time. Slidesgo wasn't built in one day—it's been a journey of small steps until we got to the top! We have prepared this template, with some Japanese inspiration, to make it easy for you to explain the Kaizen method and, possibly, propose it in your own business. It includes a calligraphic font for the titles and completely editable slides.
Features of this template
- 100% editable and easy to modify
- 35 different slides to impress your audience
- Contains easy-to-edit graphics such as graphs, maps, tables, timelines and mockups
- Includes 500+ icons and Flaticon’s extension for customizing your slides
- Designed to be used in Google Slides and Microsoft PowerPoint
- 16:9 widescreen format suitable for all types of screens
- Includes information about fonts, colors, and credits of the resources used
How can I use the template?
Am I free to use the templates?
How to attribute?
Attribution required If you are a free user, you must attribute Slidesgo by keeping the slide where the credits appear. How to attribute?
Related posts on our blog.
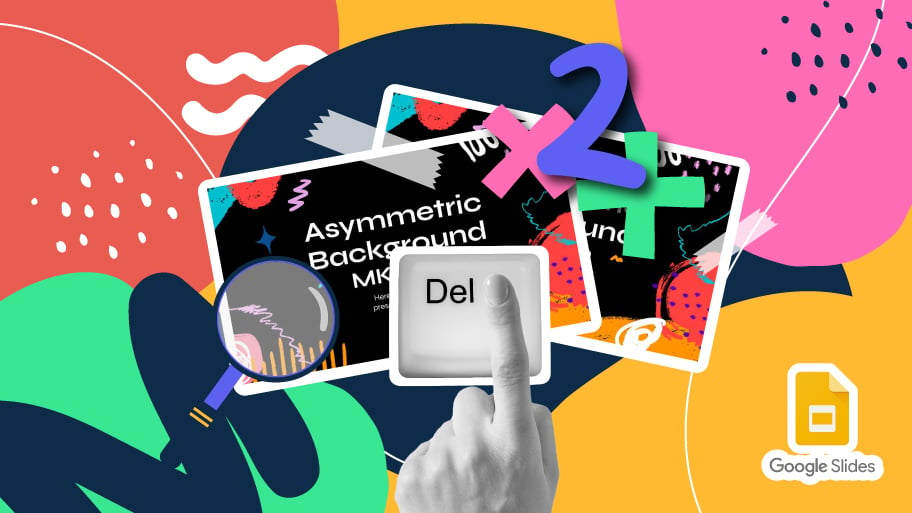
How to Add, Duplicate, Move, Delete or Hide Slides in Google Slides
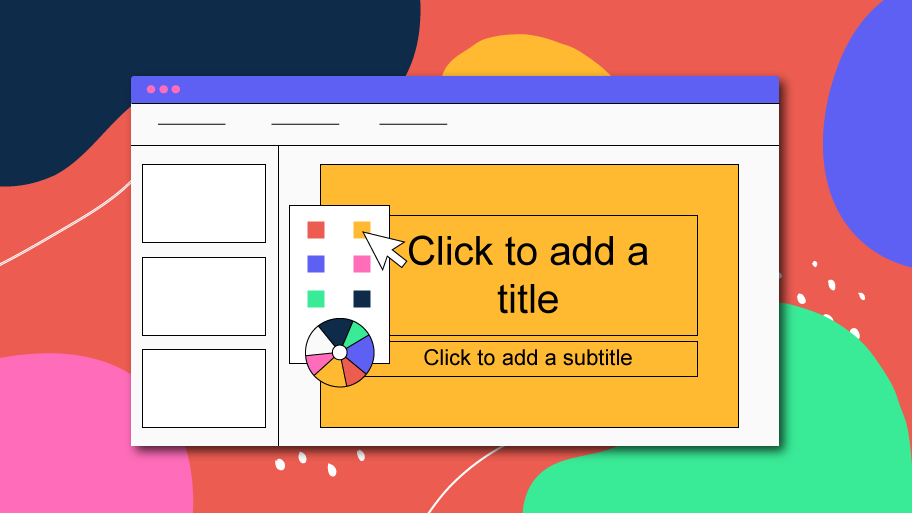
How to Change Layouts in PowerPoint
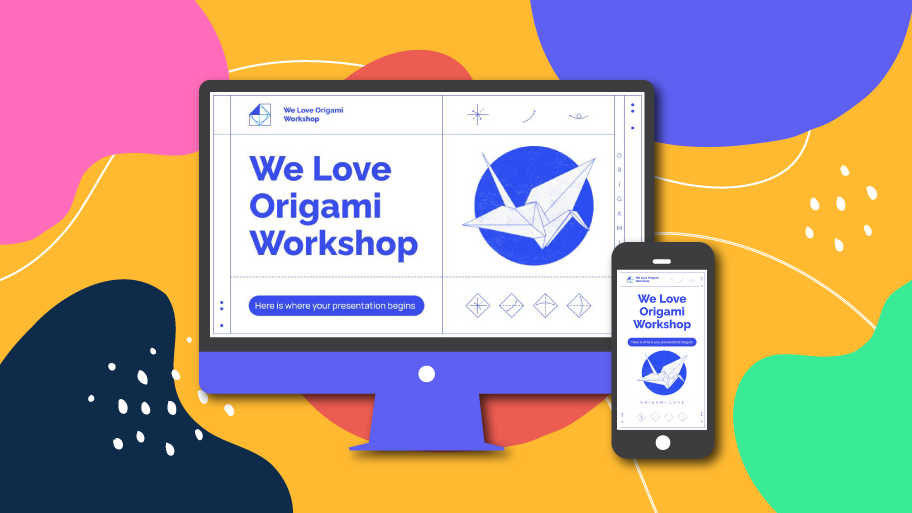
How to Change the Slide Size in Google Slides
Related presentations.

Premium template
Unlock this template and gain unlimited access
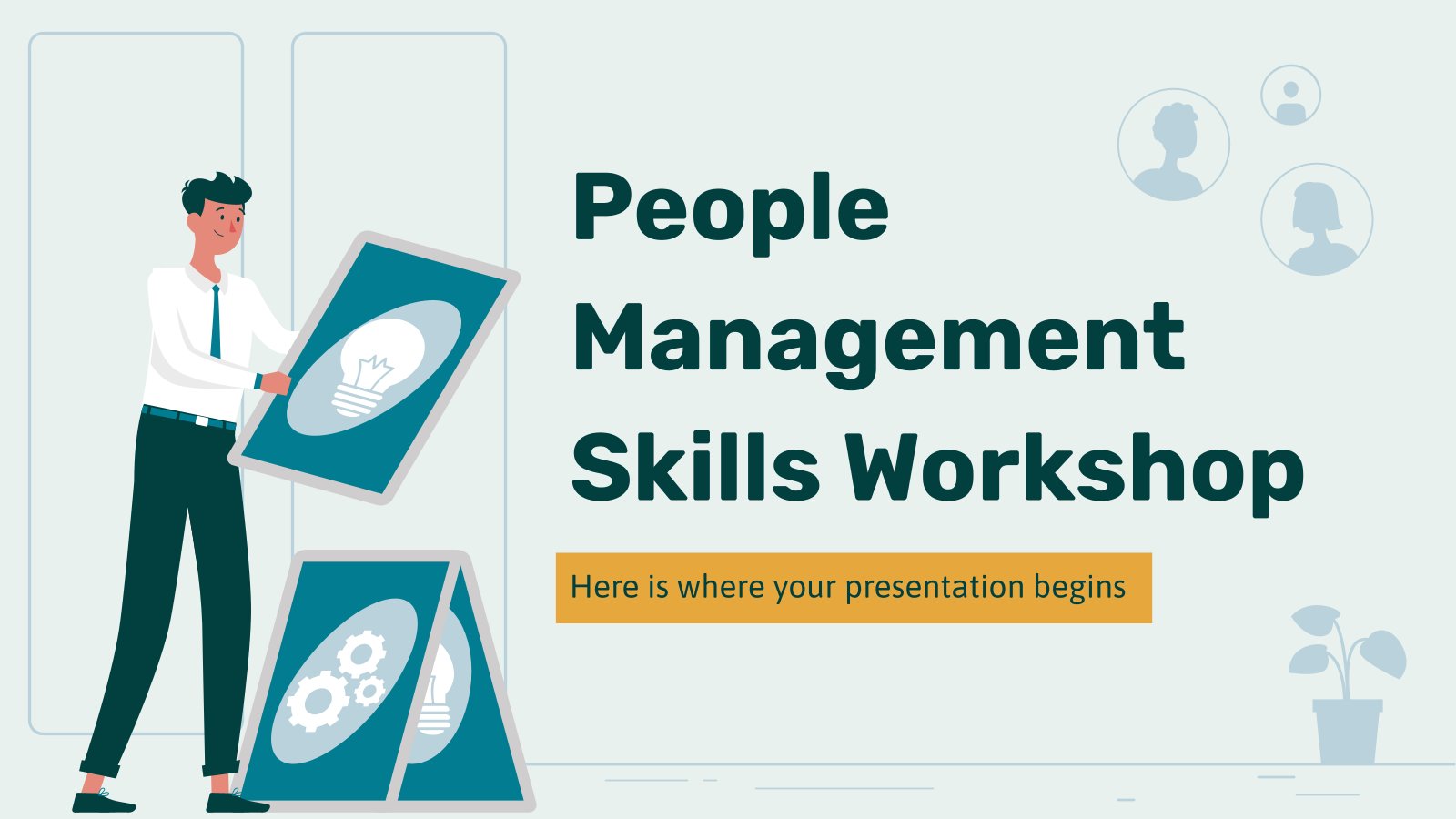
- Free Project Management Software
- Agile Project Management Software
- Project Management Software for Nonprofits
- Organization Apps to Boost Productivity
- Resource Management Software
- Monday Review
- ClickUp Review
- Monday Pricing
- ClickUp Pricing
- Wrike Pricing
- Asana Pricing
- Smartsheet Pricing
- Teamwork Pricing
- Airtable Pricing
- Scoro Pricing
- Asana vs Monday
- ClickUp vs Monday
- Wrike vs Asana
- Trello vs Asana
- ClickUp vs Asana
- What is Agile Project Management?
- Key Benefits of Agile Methodology
- Most Important Agile Metrics
- Agile Manifesto: Values and Principles
- Agile Project Management Certifications
What is Kaizen? Process, Examples, Principles
Most businesses experience failure at different levels and for different reasons. With the Kaizen program and methods, an organization can rise above these failures and become more productive in its activities.
Kaizen involves process changes that can be gradual but will eventually cause big organizational changes. The principles of Kaizen, if implemented properly, will inevitably result in notable improvement within the organization.
This article will expose you to what Kaizen means, Kaizen examples, Kaizen events, and principles you can implement to cause the required changes and potential improvements in your organization.
What is Kaizen?
Kaizen comes from the Japanese words for good and change, change for the better, or improvement. From the philosophical perspective, Kaizen promotes a mindset where small incremental changes ultimately create a notable impact over time.
As a methodology, Kaizen improves certain areas in an organization by engaging top management and front-line employees to make notable daily changes, conscious that small incremental improvements can yield big results.
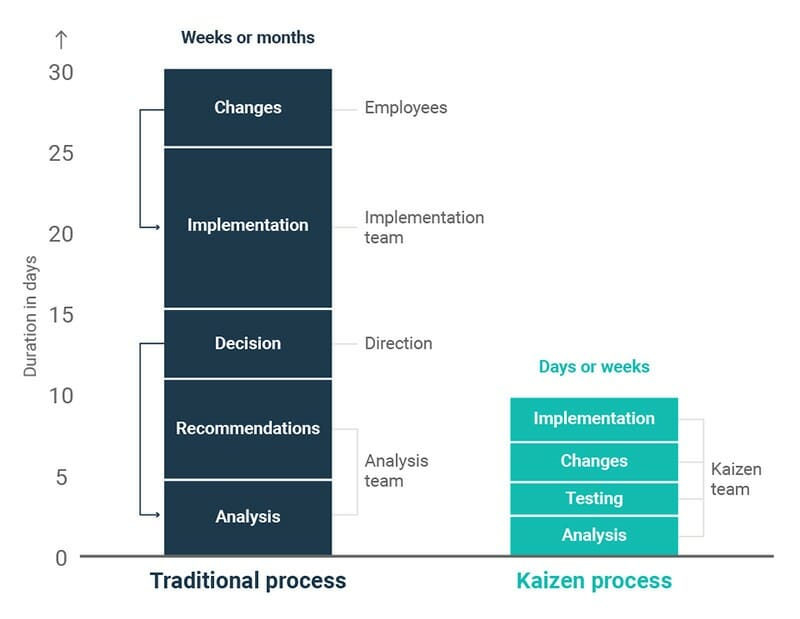
Japanese manufacturers first endorsed Kaizen as a vital and foundational business philosophy after World War II.
In the business world, Kaizen refers to a mindset where continuous improvement is experienced in the organization through notable gradual improvements.
The Kaizen theory has been proven relevant across various fields and can apply to real-life situations. This theory is considered the major building block of lean manufacturing and lean production in the manufacturing process.
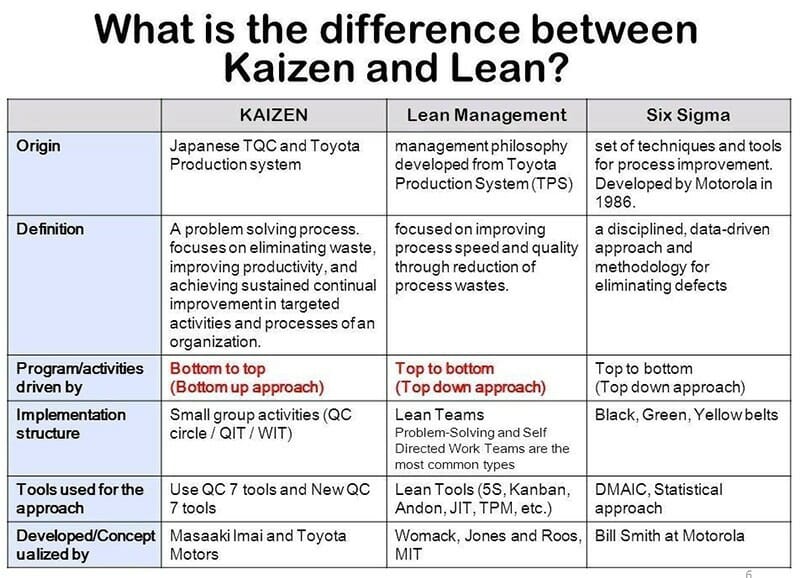
Positive elements such as teamwork, personal discipline, improved morale, quality circles, and suggestions for improvement are necessary for successful Kaizen implementation. They make up the Kaizen framework.
Companies use Kaizen blitz or events as a short-term approach to reducing waste and production costs.
Compared to other Kaizen activities, which focus on fundamental changes over a long period, a Kaizen event is a starting point for continuous improvement designed to deliver the desired results in a particular focus area through many small changes.
What are the Main Principles and Elements of Kaizen?
Since management usually expects immediate results from work done or regarding the execution of projects, implementing the Kaizen theory is almost impossible.
If you want to maximize the advantages of Kaizen, you must understand the principles and elements surrounding it and how to apply them.
1. Management Commitment
A major reason Kaizen's implementation fails is primarily the lack of support and other notable actions from leaders in the organization.
The top management of an organization is vested with the most important responsibility of ensuring that the Kaizen approach is implemented, followed by every manager and then the rank-and-file employees.
When the top management in an organization displays a long-term commitment to continuous improvement, the managers will inevitably follow through on the Kaizen initiative, and the employees will personally cultivate a Kaizen mindset.
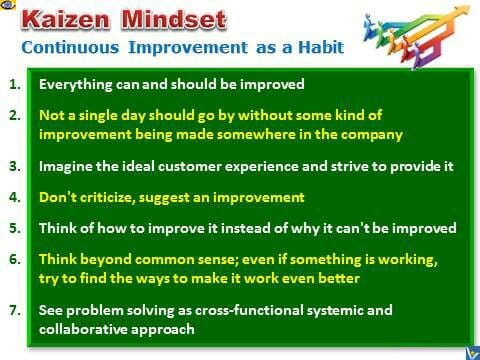
2. Employee Empowerment
Employees naturally get acquainted with the best possible ways to improve how the job is done. Organizational leaders should create a work-friendly environment where employees can feel empowered to contribute and bring up suggestions concerning the work.
Creating a work-friendly environment ensures that various suggestions for improvements can come from the different levels and ranks within the organization.
Leaders will boost their morale and confidence by encouraging workers to add value to the organization through their suggestions and contribution.
This strategy gives every individual in the organization a sense of responsibility and ownership of continuous improvement efforts, which will inevitably result in successfully implementing the Kaizen philosophy.
3. Gemba Walk
The achievement of operational efficiency started when the actual task was stated to be executed and not from the discussion in a conference room.

A Gemba Walk is derived from the term Gembutsu or Gemba, which means “the real place” normally performed by a manager to review or learn how a particular process works or functions and acquire in-depth information about workers and the work's continuous improvement.
Gemba Walk checklists serve as a useful guide for observing the relevant questions to be asked to determine the source of the problem and the next steps to take regarding finding solutions to these problems.
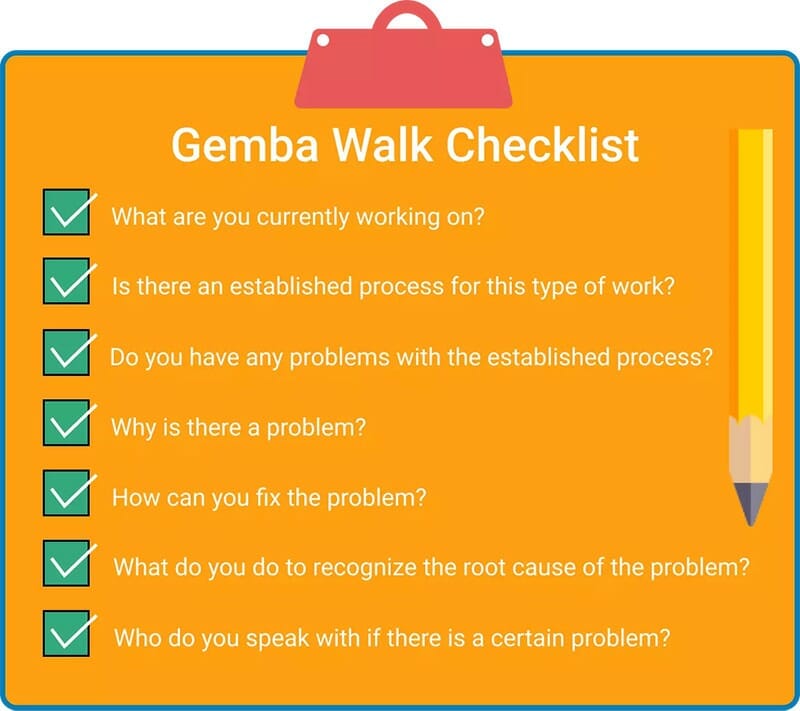
4. 5S Principles
One of the biggest challenges that have affected continuous improvement is assuming new ideas or ways of doing things will fail and holding on to old practices and methods of carrying out work.
The 5S Principles aim to improve workplace efficiency and effectiveness by successfully developing new ideas and methods to eliminate waste in the organization’s activities.
Organizations should not hold on to the mindset that a principle, method, or idea that worked previously means it will continue its work because that is not always the case.
Here are the 5S principles:
- Safety & Security
- Waste elimination
- Increased efficiency
- Low implementation cost for high-impact performance
- Development of a collaborative mindset among co-workers
Why Do Manufacturing Businesses Use Kaizen?
1. eliminates waste.
The Kaizen approach is very popular in the world of manufacturing businesses because of its notable principle of waste elimination and incremental improvements. These principles are useful to factory floors for a range of products.
Kaizen helps manufacturing businesses cut their production costs and increase their operating income .
2. Increase Competitive Advantage
Manufacturing businesses use Kaizen to boost their competitive advantage. The purpose of all Kaizen continuous improvement and changes is to produce high-quality products faster to gain a competitive advantage over their competitors.
What is the Kaizen Process?
The Kaizen method is a step-by-step process; the journey of Kaizen’s implementation can only move forward when the right questions are being asked.
The accurate knowledge and clear understanding of the main elements and core principles set the organization for success.
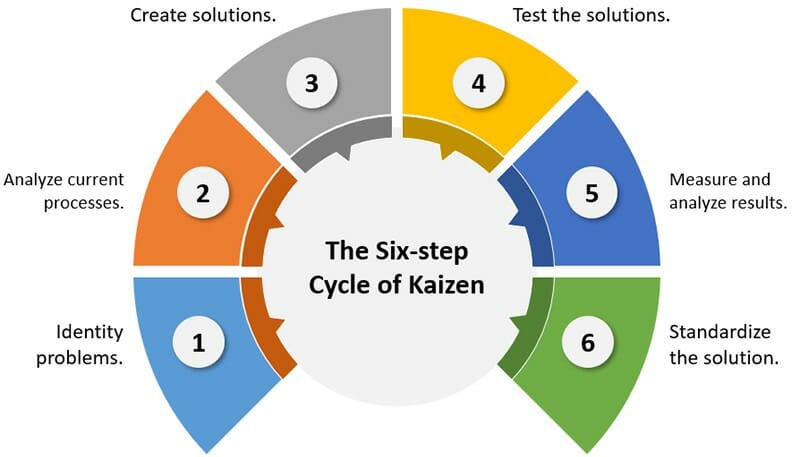
Here are key guide questions you can begin with that show clearly how the Kaizen activities are performed and the process works.
To implement Kaizen, you will have to follow this process.
1. Identify the Problem’s Root Cause
In a situation where an ongoing change-resistant procedure is inadequate or bad, it will be wrong to keep investing resources to solve the wrong problem.
The wise approach is for the leader to drop their assumptions and preconceived notion about who or what they think is wrong. They should ensure proper findings into the issue by implementing Gemba Walk and root cause analysis.
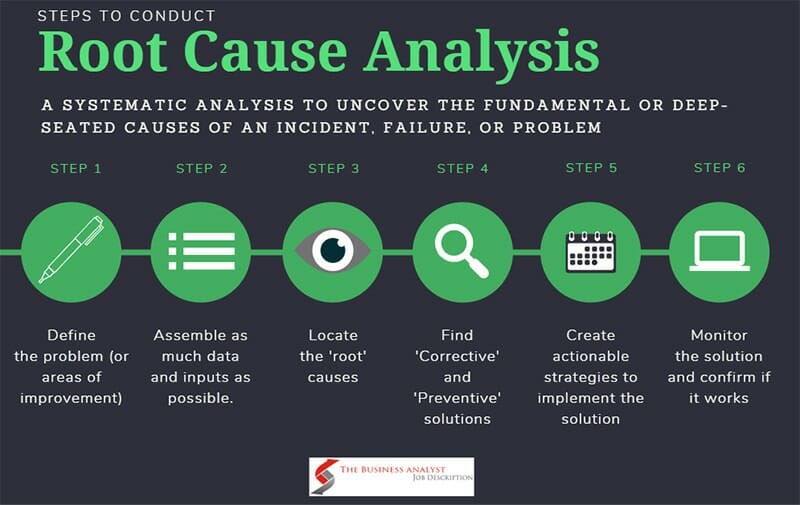
Avoid assuming that new methods will work. You can discover the solution by finding out the root cause of the problem.
As a leader, it is wise to place yourself in a position where you can easily identify quality gaps by communicating personally with workers and observing their work first-hand.
While observing your employee's work, avoid criticizing, finding faults, and apportioning blame on workers. Instead, carefully take note of everything happening without much interference.
You can not get this real-life example of a typical day in operation and the experiences and knowledge acquired through observation from reports.
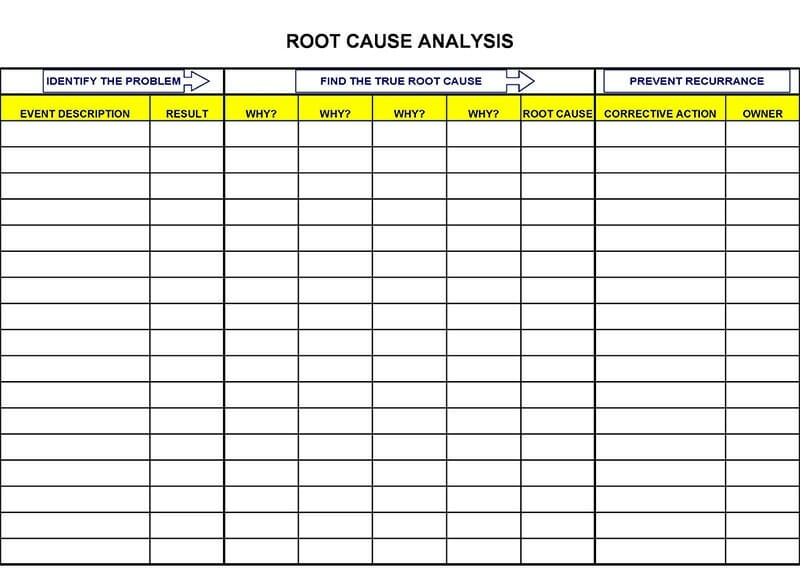
2. Address the Problem’s Root Cause
With the five why analysis, problem-solving comes easily if these principles are followed accurately.
This analysis helps to determine the root cause of a problem. It can serve as an effective technique in formulating solutions that prevent the recurrence of the identified problem.
This technique is equipped with creative suggestions for workers and supported by relevant information from where work happens. Managers can use it to implement low-cost but high-value improvements that sync with the quality objective of the organization.
3. Ensure Consistent Implementation of Changes
An organization's senior management consultant shows commitment to continuous improvement when it immediately takes action on the small incremental changes and follows through with significant long-term initiatives.
The notable changes should begin with you by personally making adjustments to how you work and carefully taking note of its significant effect on the quality of your output.
Kaizen is relevant to every organization member and not just exclusive to a particular set of people, such as team members alone. It should occur everywhere within the organization, not just on the shop floor.
You can save quality time and money from manual monitoring across various sites and levels of the organization by centralizing Kaizen management.
4. Impact of Continuous Improvement Efforts
While implementing Kaizen principles, most people are impatient . They may give up because they do not instantly see or feel notable differences their seemingly small actions make in the company.

The A3 or 8D reports are ideal documents that managers or leaders in an organization can share with employees because they measure the effectiveness, monitor the performance of implemented changes, and communicate the impact of Kaizen’s principles.
You should note the most impactful solution to know the specific actions the company needs to start, continue or stop taking.

5. How Else Can We Keep Improving?
The journey of continuous improvement is not marked by perfection but by a strong desire for personal and organizational growth.
If you can achieve 50% of your improvement goals, you are doing great; you need to celebrate your wins but never stop there; you must keep improving.
Do not leave issues that arise in the workplace to linger for a long time before you take significant action.
You should be proactive about solving problems in the workplace because Kaizen is an unending process. With these actions, you guarantee continuous improvement in the workplace.
How is 5S Used in the Kaizen System?
The 5S in the Kaizen system shows the concept of continuous improvements and notable actions taken to reduce waste.
1. Sort or Seiri
The first S, which stands for Sort, or Seiri, emphasizes the strong desire to eliminate any unnecessary object or entity clustering the work environment. It serves as a distraction or hindrance to workplace activities and constant improvement.
2. Set in Order or Seition
The second S is focused on effectively organizing useful objects in their rightful place. This action helps increase efficiency, improve productivity and minimize wastage of space and time.
Everything needed to accomplish given workplace tasks is properly arranged in the right place, at the right time, and in the right order.
3. Shine or Seiso
The third S emphasizes the cleanliness of the shop floor and how important it is to keep work items in their rightful place to ensure efficiency and organization.
4. Standardize or Seiketsu
The fourth S emphasizes the importance of recognizing and maintaining the processes that have been developed and proven effective.
Following this principle implies that every team member must respect and comply with the laid-down systems and processes in the workspace.
5. Sustain or Shitsuke
The final S focuses on ensuring that the organization experiences continuous improvement . Sustain, or Shitsuke, ensures that personal discipline is maintained around existing processes and vital knowledge is protected.
Examples of How Manufacturers Use the Kaizen Method
Different industries implement the Kaizen method to boost productivity and help the company do better.
Some examples of how certain manufacturing companies apply Kaizen in their activities include:
Toyota can be considered one of the most popular manufacturing companies that use the Kaizen method, which is part of the Toyota way and supports all the processes and systems.
This car manufacturing company has been implementing Kaizen for many decades. The Kaizen concept is firmly integrated into ‘The Toyota Way,’ the organization’s doctrine that supports all its systems and various processes.
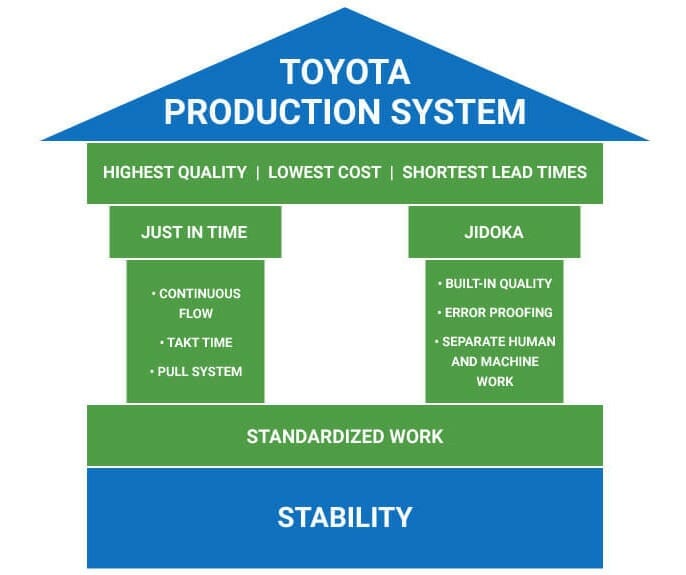
One notable way Toyota implements Kaizen is its use of Nemawashi, which is regarded as the beginning of the decision-making process.
The Japanese term Nemawashi translates to ‘laying the groundwork.’ Vital information is passed to every team member before making formal decisions. This process is designed to empower people and engage team members in the work process.
According to the information on Toyal’s website, the company uses the Kaizen principle to underpin the aim of forever thinking about the next, learning from the past, and improving the Toyota production system.
Nestle, a Swiss food and beverage company, is another notable organization for implementing Kaizen.
This manufacturing company uses techniques such as value stream mapping that display how the movement of materials and information should run to create the most efficient production line.
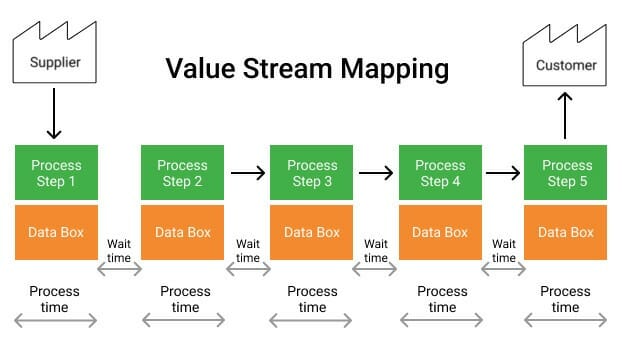
3. Lockheed Martin
Another notable manufacturer that takes advantage of the benefits of the Kaizen method is Lockheed Martin.
Lockheed Martin is a worldwide manufacturer of defense systems and military aircraft. With the Kaizen principle, Lockheed Martin has successfully cut its manufacturing cost by more than a third over just five years and cut its delivery time for products almost in half.

Benefits of Kaizen
1. increased customer satisfaction.
Waste reduction and increased productivity will naturally minimize any lags in customers’ deliveries or responses to their concerns.
2. Happier, More Engaged, and More Productive Workforce
Connecting all teams within the work environment in a joint effort to create continuous improvement means the employees are happier, more engaged, and more productive.
The emphasis on respecting every team member’s viewpoints and having a clear understanding of all elements of the factory floor generates goodwill.
3. The Razor-Sharp Focus on Cutting Waste
When you implement the Kaizen method, the natural result is a reduction in waste of all forms. Waste reduction can be in the form of the better use of leftover materials or improved use of labor systems and workflow.
Continuous Improvement in Your Workplace and Production Process
The Kaizen method is a great fit for big mass-production manufacturing businesses. SMEs can adopt its principles and mindset to improve their business culture and output quality.
Every employee in the business has to buy into the Kaizen method for it to be successful. Since SMEs tend to have a closer relationship with their workers than large production companies, they find it easier to implement Kaizen.
Accepting and implementing Kaizen as an effective way of improving work quality sets the organization for operational excellence. Small incremental changes or improvements yield notable results over time.
You can begin your Kaizen journey with these principles to get the desired result from implementing the Kaizen method.
Was This Article Helpful?
Martin luenendonk.
Martin loves entrepreneurship and has helped dozens of entrepreneurs by validating the business idea, finding scalable customer acquisition channels, and building a data-driven organization. During his time working in investment banking, tech startups, and industry-leading companies he gained extensive knowledge in using different software tools to optimize business processes.
This insights and his love for researching SaaS products enables him to provide in-depth, fact-based software reviews to enable software buyers make better decisions.

- What is Strategy?
- Business Models
- Developing a Strategy
- Strategic Planning
- Competitive Advantage
- Growth Strategy
- Market Strategy
- Customer Strategy
- Geographic Strategy
- Product Strategy
- Service Strategy
- Pricing Strategy
- Distribution Strategy
- Sales Strategy
- Marketing Strategy
- Digital Marketing Strategy
- Organizational Strategy
- HR Strategy – Organizational Design
- HR Strategy – Employee Journey & Culture
- Process Strategy
- Procurement Strategy
- Cost and Capital Strategy
- Business Value
- Market Analysis
- Problem Solving Skills
- Strategic Options
- Business Analytics
- Strategic Decision Making
- Process Improvement
- Project Planning
- Team Leadership
- Personal Development
- Leadership Maturity Model
- Leadership Team Strategy
- The Leadership Team
- Leadership Mindset
- Communication & Collaboration
- Problem Solving
- Decision Making
- People Leadership
- Strategic Execution
- Executive Coaching
- Strategy Coaching
- Business Transformation
- Strategy Workshops
- Leadership Strategy Survey
- Leadership Training
- Who’s Joe?
“Without continual growth and progress, such words as improvement, achievement, and success have no meaning.”
– Benjamin Franklin
During the 1980s, facing stiff and unrelenting competition from Japanese manufacturers, American manufacturers tried to leverage lean methodologies and tools to transform their productivity and quality. Unfortunately, many of their efforts failed miserably. They would bring in consultants or tiger teams to lean out processes only to see people revert back to wasteful methods. They were missing the heart and engine of lean, which is kaizen.
What is Kaizen?
Kaizen is the philosophy that every person in an organization , from the CEO to the janitor, has a DUTY to improve what they do, eliminate waste on a daily basis, continually learn, reflect, change and experiment . And, the overall efficiency and effectiveness of an organization are predicated on the emergence and compounded impact of thousands of small improvements and changes driven by every individual in an organization. While western thinking typically seeks out big step-function innovations, eastern thinking focuses on the sum of the parts of many little improvements. It is hard for western management teams to comprehend the fact that over the past 50 years there have been over 1,000,000 systemic improvements to the Toyota production system.
In Japanese, kai means “change” and zen means “good”, which translated into English means “continuous improvement.” While Toyota pioneered many of the core lean improvement tools, they also perfected kaizen, which embodies the cultural and philosophical underpinnings of lean.
Kaizen methodology – PDCA
Kaizen expands beyond the idea of the individual pursuing continuous improvement; there is also the methodology of kaizen, which at its most basic level is applying the scientific method to processes. The prerequisite of kaizen is that you have standardized processes, with the thought being if a process is in flux and changing, then you can’t truly understand cause and effect in a controlled way. So, first, standardize your processes and get them up to level 4 in the process maturity levels.
Once you have standardized processes, then the first step in kaizen is to observe and identify waste. Once you identify waste, then the next step is a reflection to truly understand the waste and diagnose the root cause of it. The third step is the beginning of the Deming Cycle, which is a simple process improvement framework of Plan, Do, Check, and Act (PDCA). Plan involves designing an improvement to a process. Do is implementing the plan. Check involves measuring the impact of the plan on the efficiency and effectiveness of the process. And, Act, is deciding what permanent changes will be adopted and standardized in the process.
In Toyota’s thinking, there are two types of kaizen (improvement). The first is what we refer to as Kaizen with a capital K. This is the big win. In the west, this is what companies typically seek. In Toyota, people prefer kaizen with a small k, which are the small day-to-day efforts that improve a process. In the east, Plan, Do, Study, Act is a daily ritual.
Kaizen can happen informally as part of someone’s daily job or through a simple suggestion box. Or, kaizen can happen more formally through a planned and intense kaizen workshop, where a team comes together for a few days to problem-solve a process. A kaizen workshop involves understanding the needs of the customer, mapping out the current state of a process, identifying waste in the process and root causes of the waste, mapping out a future state of the process, and building an implementation plan to pilot changes, evaluate their impact, and ultimately make permanent changes to standardize within the process.
Why is kaizen important?
It is hard to believe the amount of waste in most processes until you go through a Kaizen exercise on a process and see the waste firsthand. Whether or not you adopt the formal methodologies of kaizen, the underpinning philosophy of kaizen can be useful. The philosophy of continuous improvement and that everyone should be proactive in identifying waste, creating solutions, implementing positive change, learning, and experimenting is essential to continuously improve organizational performance . The era of command and control management is extinct, and survival is predicated on nurturing and encouraging the empowerment and duty of every individual to drive positive continuous change.
How do you embrace kaizen?
There is no easy answer to how to embrace kaizen within an organization. It took Toyota many decades to perfect the kaizen cultural norms of continuous reflection, idea generation, controlled experimentation , standardization, and sharing. Kaizen is not about the tools but instead is about the deep seeded culture of an organization. Whereas Toyota team members look at waste and issues as an opportunity for the team and organization to improve, westerners often look at waste and issues as somebody’s problem, mistake, and a reason to potentially fire them. Western thinking is often about breakthrough innovation and step function improvements, while Toyota has implemented over 1 million small and large improvements to its production processes through Kaizen. Western thinking often obsesses on getting the results; while kaizen thinking is that the right process will produce the right results. There aren’t any quick tips or tricks to embracing kaizen since it is a long road that requires considerable commitment, dedication, resources, and thoughtfulness.
NEXT SECTION: SIX SIGMA & DMAIC
DOWNLOAD STRATEGY PRESENTATION TEMPLATES
168-PAGE COMPENDIUM OF STRATEGY FRAMEWORKS & TEMPLATES 186-PAGE HR & ORG STRATEGY PRESENTATION 100-PAGE SALES PLAN PRESENTATION 121-PAGE STRATEGIC PLAN & COMPANY OVERVIEW PRESENTATION 114-PAGE MARKET & COMPETITIVE ANALYSIS PRESENTATION 18-PAGE BUSINESS MODEL TEMPLATE
JOE NEWSUM COACHING

EXECUTIVE COACHING STRATEGY COACHING ELEVATE360 BUSINESS TRANSFORMATION STRATEGY WORKSHOPS LEADERSHIP STRATEGY SURVEY & WORKSHOP STRATEGY & LEADERSHIP TRAINING
THE LEADERSHIP MATURITY MODEL
Explore other types of strategy.
BIG PICTURE WHAT IS STRATEGY? BUSINESS MODEL COMP. ADVANTAGE GROWTH
TARGETS MARKET CUSTOMER GEOGRAPHIC
VALUE PROPOSITION PRODUCT SERVICE PRICING
GO TO MARKET DISTRIBUTION SALES MARKETING
ORGANIZATIONAL ORG DESIGN HR & CULTURE PROCESS PARTNER
EXPLORE THE TOP 100 STRATEGIC LEADERSHIP COMPETENCIES
TYPES OF VALUE MARKET ANALYSIS PROBLEM SOLVING
OPTION CREATION ANALYTICS DECISION MAKING PROCESS TOOLS
PLANNING & PROJECTS PEOPLE LEADERSHIP PERSONAL DEVELOPMENT
- What is i-nexus
- Why i-nexus
- Strategy Execution
- Hoshin Kanri
- Operational excellence
- Case studies
- i-nexus reviews
- Strategy execution guide
- Hoshin Kanri guide
- Operational excellence guide
- Book a demo
- Demo on-demand
- Plan to practice
- Buy or build
- Customer success overview
- Customer success journey
- Customer services
- Customer support
- News & Press
The Kaizen method: our ultimate guide
Get to know how kaizen is used in businesses worldwide to drive strategic value from daily work and how you can implement it in your organization..
Meaning ‘continuous improvement’ in Japanese, Kaizen is a business philosophy that focuses on improving processes and operations and involving employees from all levels of an organization.
Kaizen focuses on the power of small, gradual, positive changes in the workplace. A business can improve employee and customer satisfaction through Kaizen, reduce waste, and boost productivity.
In this guide, we will explain how Kaizen is used in business to give you an idea of whether or not this philosophy might be helpful to you.
Jump to the section you want
Read on or click below to jump to the part of Kaizen you want to learn about:
- What is Kaizen?
The five elements of Kaizen
Employees and kaizen ideas.
- The benefits of Kaizen
- The challenges of Kaizen
Standard work and Kaizen
Value stream mapping and kaizen.
- How to implement Kaizen
Putting in place plans for continuous improvement
- Examples of implementing Kaizen
- Kaizen books to read
What is the Kaizen method?
Introduced in Masaaki Imai’s Kaizen: The Key to Japan’s Competitive Success, Kaizen is often applied by manufacturers; the most well-known example is Toyota.
It is also popular among the tech and healthcare industries and service improvement. It has even been adapted for life coaching and personal development.
Imai writes:
" the method of the Kaizen strategy is that not a day should go by without some kind of improvement being made somewhere in the company".
Kaizen involves its principles being a fully integrated part of a company’s culture.
More of a methodology than a business model, the Kaizen approach can work well alongside lots of other management tools and strategies.
Changes made through Kaizen may seem small to those seeking more obvious instant gratification, but they aim to contribute towards tremendous change in the long run.
With these principles in place in your organization’s culture, you can fully benefit from the Kaizen approach to making changes:
- A problem or area that could be improved is identified, and a goal is set
- Employees explore new ideas and possible solutions
- The goal is broken down into achievable or sub-objectives
- To make sure that no one’s tasks overlap and that no one is stretched too thinly, tasks are assigned to tackle each sub-objective
- Changes are implemented, and the results monitored
- If your changes provide the desired results, they are adopted permanently.
One of the methods used alongside Kaizen and by Lean practitioners in general to identify problems is the 5s framework.
This framework prioritizes standardization to see areas in need of improvement better. The 5Ses and their English translations are:
- Seiri (sort) - remove unnecessary things from the workplace
- Seiton (set in order) - organize what remains for ease of use
- Seiso (shine) - keep your workspace clean and tidy
- Seiketsu (standardize) - systemize how to keep things clean/running smoothly
- Shitsuke (sustain) - keep up this practice until it becomes an ingrained habit
This system is tailored towards Lean production but can easily be interpreted and adapted for many organizations and personal use.
5S floor markings in a manufacturing site
Manufacturing 5s floor markings are essential to efficiently organizing a manufacturing process and improving safety.
5s floor markings are used to standardize the layout of the workplace, visually communicate company values and goals, remind people about standard operating procedures, and provide guidance to employees in a consistent format.
Floor markings are one of the ways that 5s is implemented in a manufacturing setting.
Markings can be created through painting or tape, making it easy for employees to quickly identify what needs to be done, where tools should be stored, where hazardous materials are located, etc.
They also guide how processes should be performed safely and correctly.
Floor markings can also help indicate vehicle routes, workstations, assembly lines, safe walking paths etc. This cuts down on confusion related to processes which save time and help improve safety.
Manufacturing 5s floor marking helps streamline workflow by making different areas easier to identify from color-coding and visual cues such as arrows or shapes.
This improves efficiency since people working in the area know quickly where they need to go or what steps they must take without relying on human memory or guesswork.
Additionally, using symbols makes it easier for people with language barriers or disabilities to understand instructions without having to ask questions or search elsewhere for clarification.
This leads to improved safety and production times and higher overall customer satisfaction.
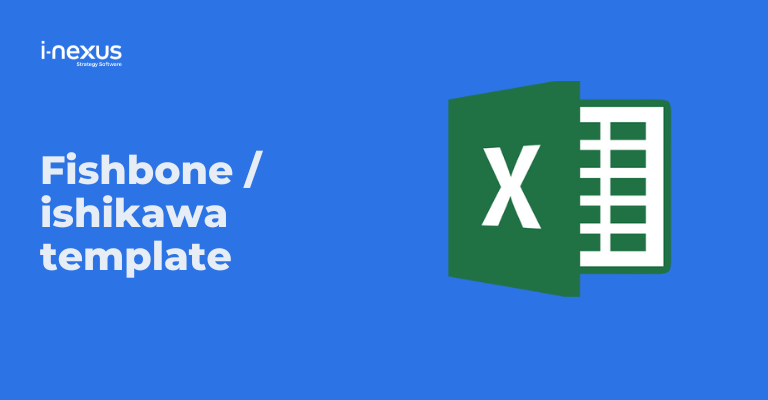
What are Kaizen ideas?
The idea that everyone should strive to make minor, incremental improvements in their work environment by suggesting ideas and initiating changes means you need a suggestion system where employees can submit ideas for improvement, which are then evaluated and implemented as needed.
Employee ideas are a key component of kaizen because it encourages people to think critically about their tasks and identify areas for improvement.
By having open communication channels where people can freely express their thoughts and concerns, organizations can better understand employees' needs and how best to address them.
With this feedback, you can make well-informed decisions about improving processes and creating an efficient working environment.
The benefits of employee ideas
The benefits of having employee ideas drive kaizen beyond improved efficiency; it also creates a culture of ownership among employees.
When workers feel like they are part of the decision-making process, they will feel a greater sense of accountability for their work and be more likely to go above and beyond to ensure its success.
Furthermore, when employees create solutions, they will become more engaged with their job and have increased job satisfaction.
Moreover, employee input is invaluable when executing kaizen since they often know firsthand which processes would benefit most from improvements or adjustments.
They may be able to recognize problems quicker than management due to their proximity to the work or identify creative solutions that wouldn’t be considered otherwise.
Additionally, they may be able to provide insights into potential obstacles that could arise from implementing specific changes before those changes occur - preventing avoidable disturbances in processes down the road.
Examples of how employee suggestions work with Kaizen
Here's an example of how employee ideas can drive kaizen:
Imagine that you work in a manufacturing plant and you've noticed a bottleneck in the production process causing delays. You come up with an idea for eliminating this bottleneck by reorganizing the layout of the production line.
You bring your idea to your supervisor, who is responsible for driving kaizen efforts in your department. Your supervisor likes your idea and suggests that you form a kaizen team to explore the idea further. The team meets regularly to brainstorm and identify possible solutions to the bottleneck issue.
As the team works on the problem, they gather data and analyze the results of their efforts. They also involve other employees in the process, seeking their input and feedback.
Eventually, the team came up with a solution that involved reorganizing the layout of the production line. They present their solution to upper management, who review and approve the proposal.
The solution is implemented, and the production process is streamlined, resulting in increased efficiency and reduced delays.
As you can see, employee input is one of the critical aspects of Kaizen.
This is based on the idea that employees are often in the best position to identify problems with the processes they go through every day.
This suggests that they should also be the best people to come up with the solution, with help and creative input from others.
What are the benefits of Kaizen?
One of the fundamentals of Kaizen is looking to eliminate waste - in this context, waste can mean wasted resources and wasted time, and energy.
An example would be improving a process to eliminate wasting valuable time.
This, combined with the fact that problems are solved in-house, is one of the reasons why Kaizen is seen as helpful for saving money and lowering costs.
Other benefits of Kaizen include:
More efficient problem-solving and less fear of blame
This is an obvious benefit as Kaizen restructures how problems and mistakes are approached - there is a go-to strategy for tackling problems as and when they arise.
Because there is a transparent system for dealing with issues, and the responsibility of thinking of solutions is shared, there is less fear of blame when raising them with your colleagues.
Kaizen encourages scrutiny because the desire for minor improvements outweighs the pride of being unable to admit fault.
This reduces stress and anxiety among employees in the long run.
Simplified processes
Due to the breaking down and even distribution of tasks, objectives are easier to approach, and the permanent changes resulting from improvements often focus on simplification and efficiency.
Small changes make a big impact
It can be hard to implement significant changes company-wide - there is often at least some resistance, and it can take a long time to roll out across all departments.
Because Kaizen focuses on small changes, which are easier to accept and set in motion, many small yet impactful improvements can happen with minimal disruption.
Greater customer satisfaction
As a direct result of all of the above, the customer experience is improved.
Mistakes are less frequent, the quality of work is higher and more streamlined, and communication is encouraged throughout all departments.
All of these things positively impact the customer experience and the end product.
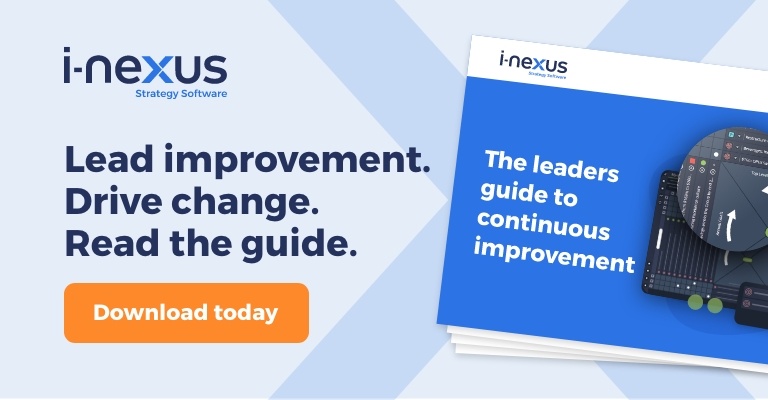
What are the challenges that come with Kaizen?
Some challenges of implementing a Kaizen approach include:
Resistance to change
Some employees may resist changing how they work, even if the changes are meant to improve efficiency and productivity. It's essential to communicate the benefits of the changes and involve employees in identifying areas for improvement.
Lack of resources
Implementing kaizen requires time and resources, such as training and equipment. A lack of resources can make implementing and sustaining kaizen efforts challenging.
Difficulty identifying areas for improvement
Identifying areas for improvement can be challenging, particularly if you're unsure where to start. It's essential to involve employees in identifying areas for improvement and using data and metrics to help identify areas of inefficiency.
Difficulty measuring progress
Measuring the impact of a minor, incremental improvements can be challenging. Establishing clear metrics and tracking progress over time is critical to ensure your kaizen efforts pay off.
Maintaining momentum
It's essential to keep up the momentum of kaizen efforts over time. This can be challenging if you don't have a clear plan in place or if you don't have the support of leadership and employees.
Kaizen and standard work are closely related concepts in continuous improvement.
What is standard work?
Standard work is a documented process that outlines the most efficient and effective way to perform a task. It serves as a baseline against which performance can be measured and improvements can be made.
Standard work typically focuses on the following elements of a task:
The steps involved in completing the task Standard work specifies the steps required to complete a task most efficiently and effectively as possible. This includes both the physical and mental steps involved in the process.
The sequence of steps Standard work also specifies the order in which the steps should be completed. This helps to ensure that the task is completed logically and efficiently.
The expected time to complete the task Standard work specifies the expected time it should take to complete a task, based on the most efficient and effective way of performing it. This helps identify areas where improvements can be made to reduce the time required to complete the task.
The resources required to complete the task Standard work specifies the resources (e.g. tools, materials, equipment) needed to complete a task. This helps to ensure that the necessary resources are available when needed.
The expected level of quality Standard work specifies the expected level of quality that should be achieved when performing a task. This helps to ensure that the task is completed to the required level of quality every time.
By focusing on these aspects of a task, standard work helps to ensure consistency and quality in the way work is performed and can serve as a baseline against which performance can be measured and improvements can be made.
How the two relate
Standard work and kaizen are often used as part of a continuous improvement strategy. An organization can identify areas where improvements can be made through kaizen by establishing a standard way of working.
For example, if an organization has established a standard way of performing a task, but there are still delays or inefficiencies in the process, a kaizen team could be formed to identify and eliminate the root causes of these issues.
Value stream mapping is a Lean manufacturing tool that helps identify and eliminate waste in a manufacturing process. It creates a visual representation of the flow of materials and information as a product or service moves through the production process, from raw materials to the finished product.
To use value stream mapping as part of a Kaizen manufacturing process, you would follow these steps:
Identify the product or service and the steps involved in its production.
Map out the current state of the production process, including all of the activities, information flows, and decision points.
Identify and classify the types of waste present in the production process, such as overproduction, waiting, defects, excess inventory, unnecessary motion, and unnecessary processing.
Identify opportunities for improvement and create a plan to eliminate or reduce the waste identified in step 3.
Implement the improvement plan and track the results.
Continuously review and improve the production process to ensure that it remains efficient and effective.
Value stream mapping is an effective tool for identifying and eliminating waste in a manufacturing process.
It helps you understand how the process currently works and where improvements can be made.
You can increase efficiency, reduce costs, and improve customer satisfaction by continuously reviewing and improving the production process.
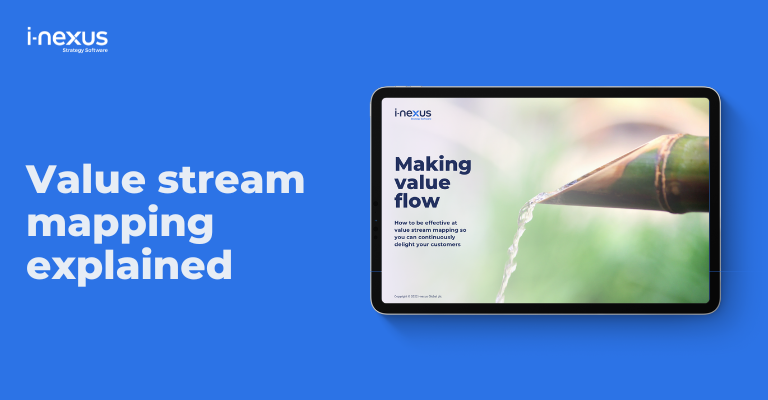
How do you go about implementing Kaizen in your business?
To introduce Kaizen to your organization, you might need to arrange what is known as a Kaizen event .
A Kaizen event involves identifying and focusing on a particular element of your organization that is in need of improvement.
This could be anything from a process that currently takes up too much time, where mistakes often occur; a task that could be made easier with the help of new tools; or something that regularly doesn’t meet client expectations.
Over a set period, usually a few days, employees work together to implement the Kaizen approach to this problem, and the 6-step process mentioned above is carried out.
When putting together a team of employees to tackle the issue, it is important to include employees who encounter the issue directly and employees from other departments who may provide fresh perspectives.
Running a successful Kaizen event takes a lot of preparation but can be incredibly rewarding.
Through Kaizen events, organizations and employees can better understand Kaizen and its principles and, as a result, can apply Kaizen to all areas of their performance.
When discussing Kaizen's advantages and disadvantages, it is worth mentioning that such events can help generate company-wide enthusiasm. Still, there is also the risk of this enthusiasm being short-lived.
The nature of Kaizen means that it doesn’t lend itself to sudden, dramatic innovation, meaning that some people can find the structure limiting. Others may struggle with not being able to see instantaneous results.
Keeping a log of ideas to address through Kaizen should ensure that you always have something to work towards, no matter how small.
This is also useful when changes cannot be done immediately - for example, immediately implementing any changes may create waste, as this would go against the fundamentals of Kaizen.
Some examples of implementing Kaizen
Below are some examples of the results of implementing Kaizen in different industries.
- The reduction of wait times for patients in healthcare industries
- The streamlining of onboarding processes
- Sustainably managing excess inventory in manufacturing
- Improved functionality in public sectors thanks to Kaizen training
More specifically, in manufacturing, life sciences, and automotives:
- Standardizing and automating work processes to reduce variability and improve quality
- Implementing Lean manufacturing techniques in the production of pharmaceuticals and medical devices, and streamline laboratory processes to increase efficiency
- Implementing just-in-time (JIT) production to reduce inventory
- Implementing visual management techniques, such as 5S, to improve organization and reduce waste
- Using tools such as value stream mapping and total productive maintenance (TPM) to identify and eliminate waste in the production process
- Implementing error-proofing techniques, such as poka-yoke, to reduce defects
Kaizen books you should read
If you’re looking to get started with kaizen, several books on the subject can help guide you. 1. Kaizen: The Key To Japan’s Competitive Success
One excellent book on the subject is Kaizen: The Key To Japan’s Competitive Success, written by Masaaki Imai.
This book explains the principles of kaizen and how companies use it as an approach to business management.
It looks at every aspect of kaizen, from its implementation in organizations to its application in daily life.
2. Lean Thinking: Banish Waste And Create Wealth In Your Corporation
Another excellent read for Kaizen is Lean Thinking: Banish Waste And Create Wealth In Your Corporation, co-authored by James Womack and Daniel Jones.
This book provides a comprehensive overview of lean manufacturing principles and how they apply to modern business practices, such as decreasing waste and increasing efficiency through streamlined processes and workflows.
3. Workplace Management
Thirdly, Taiichi Ohno's Workplace Management puts forth one of the most detailed approaches to workplace organization ever published.
Written by Toyota's original production system creator, this book delves into Ohno's profoundly influential model, which he called “the Toyota Production System," or TPS for short - now widely known as "lean manufacturing."
Through this system, Ohno was able to revolutionize not just production but also industries worldwide through his emphasis on process flow efficiency, technology utilization standardization, safety reductions in materials cost reductions in inventory turnover time, increased customer satisfaction, etc.
In addition to these, there are other important textbooks written about Kaizen, such as:
- Implementing Lean Six Sigma Throughout The Supply Chain by Vishal Garg et. al.
- Quality Improvement Using Six Sigma: An Overview for Executives by Dr. Jeffrey L Hendler et. al
How i-nexus can help you with continuous improvement
If you want to learn more about continuous improvement and want help driving strategic value from your operational and transformation work, i-nexus software could be the key.
If the Kaizen methodology speaks to you, why not look to combine it with Hoshin Kanri ? The Hoshin Kanri framework can help you align your resources with your goals for more efficient execution of tactics and success in your objectives.
To learn more about Hoshin Kanri and how i-nexus solutions can help you, contact us and book a demo today.
L earn more about operational excellence
Take the next steps in your journey by exploring our operational excellence resource hub or any of the below:
- K ey to strategy execution eBook : Read how companies like Danaher and HP have mastered strategy execution and what you can learn from them.
- What does it mean to be Business Agile?: Leap into the future of strategic planning and execution with this fascinating insight.
- How AI and Machine-Assisted Learning will help strategy execution : As Artificial Intelligence becomes a mainstay in our lives, read how AI and machine-assisted learning will evolve to support your strategy execution.
About the author
Sam Ancliff is the Demand and Lead Generation Manager at i-nexus.
In his role, his drive is to provide leaders with the tools and insights they need to make next-level decisions in their businesses and organizations.
If you’d like to talk more about strategy, contact Sam at [email protected] or connect with him on LinkedIn for the latest insights.

Core improvement tools & techniques: Operational basics & daily management

What is a Kaizen Event and how can you prepare for one?


4 tips to successfully facilitating your Kaizen event

- > The Fundamental Principles of Kaizen Project Management
The Fundamental Principles of Kaizen Project Management
Posted by Kade Jansson
Mar 7, 2024 6:15:13 PM
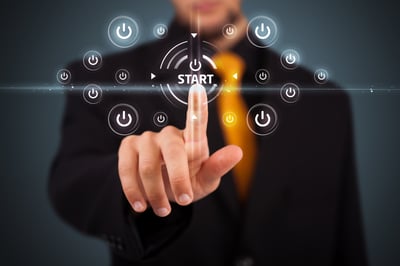
The continuous improvement methodology of Kaizen was once closely associated with industrial and automotive manufacturing. That’s because the Kaizen philosophy originated in the Japanese auto industry and was then later adopted by technology manufacturers like GE and Motorola.
But if you’ve been hearing about Kaizen project management in other sectors over the last few years, you are not alone.
The principles of Kaizen can lead to continuous improvement in almost every industry. The approach is now widespread in healthcare , construction, software development, education, logistics, and everything in between.
You won’t learn everything about Kaizen in any one blog post, but we can lay out the fundamentals of Kaizen project management.
What is Kaizen?
The Kaizen approach was first introduced to the world in a 1986 book by Masaaki Imai called, The Key to Japan’s Competitive Success. Imai had a simple way of explaining the concept. He said, “Kaizen is everyday improvement, everybody improvement, everywhere improvement.” The word Kaizen combines the Japanese words for “Good” (zen) and “Change” (kai). Kaizen doesn’t tell organizations how to improve; instead, it presents a mindset that when adopted, will influence decisions and impact the culture. Its principals are:
- Every process can be improved
- Continuous improvement essential to competitiveness
- Defects and errors are almost always the faults of flawed processes, not people
- Every person in the organization must be involved in improvement
- Incremental changes can have a significant impact
How to Become Effective at Kaizen Project Management
Almost no one is anti-Kaizen. What leader doesn’t want to build an organization that embraces positive change and involves everyone in improvement? Employees generally like the idea as well because it is based on mutual respect and accountability . But moving from a conceptual framework to daily action takes a plan. Here are the keys to Kaizen program management that works.
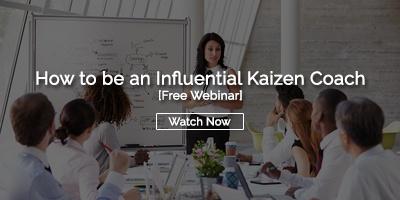
Implement Many Small Ideas
Kaizen management is not about swinging for the fences or coming up with the one idea that will change the industry landscape. Instead, getting to the point where every process is perfect is about gathering and acting upon many incremental improvements and executing recurring improvement cycles. Especially in the beginning, it is essential to reinforce the idea that no operational change is too minor to be considered. The team should be encouraged to document every opportunity they spot and given a software platform within which to do so.
Focus on Processes, Not People
The principle of Kaizen that states that “defects and errors are almost always the faults of flawed processes, not people,” is easy for project managers to overlook. People make mistakes, right? Yes, they do, especially when processes are rife with opportunities for error, when training is absent, when resources are not available, or when workspace conditions are not conducive to success. When defects happen, Kaizen project management means finding the root cause , which will almost always be a process imperfection of some sort. Improvements should be implemented to error-proof processes to avoid future quality flaws.
Eliminate Waste
In a perfect production system, every task, activity, and expense involved in a process adds value to the customer. Value is defined by the customer and excludes anything that they wouldn’t gladly pay for. Since we embrace the first principle of Kaizen, that every process can be improved, there is likely waste in your operations . Look for things like excess inventory, unnecessary movement of objects or people, features that customers never order or use, obsessive inspection, and disorderly workspaces. Talk to front-line employees about waste and train them to identify and report it.
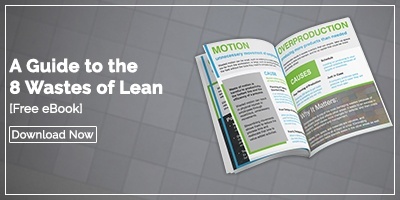
Introduce Standard Work
It is impossible to measure the results of a Kaizen improvement project if you don’t have a baseline from which to start. That’s why it is essential to document the current best practice for doing each task and ensure that everyone sticks to that standard until an improvement cycle such as PDSA or DMAIC is completed. It is important that everyone understand that setting standards don’t mean that there is no room for innovation; rather, it means that change will be intentional, orderly, and measured.
Support Your Kaizen Program with Software
It's possible to manage a Kaizen project without software to support it, but why make an already challenging proposition even more difficult? Kaizen software provides a platform for collecting all of those small ideas for positive change that you need to sustain your efforts. It supplies workflow functionality to make sure that every idea is evaluated and that those selected for implementation are successful. Importantly, it creates a repository of all of your Kaizen projects so that each new effort builds on the last, making your project managers smarter with every change.
Of course, this blog only touches the surface of Kaizen program management. If you’d like to learn more, we recommend going right to the source and picking up a copy of “ Kaizen: The Key to Japan’s Competitive Success ,” by Masaaki Imai. It contains more than 100 examples and 15 complete case studies.
Topics: Kaizen , Leadership , Improvement Methodology
Add a Comment
Subscribe via email, recent posts.
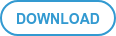
- Our Customers
Why KaiNexus
- Collaboration
- Standardization
- Customer Success Manager
- Lean Strategy
- Solutions Engineering
- Customer Marketing
- Configuration
- Continuous Enhancements
- Employee Driven
- Leader Driven
- Strategy Development
- Process Driven
- Daily Huddles
- Idea Generation
- Standard Work
- Visual Management
- Advanced ROI
- Notifications
- Universal Badges
- Case Studies
- Education Videos
Copyright © 2024 Privacy Policy
Kaizen is a Japanese word that means “continuous improvement”. Kaizen aims to make small, incremental improvements in processes and systems, leading to significant long-term benefits.
The Kaizen Philosophy
The kaizen philosophy has been successfully implemented in various industries, including lean manufacturing, to reduce waste and increase efficiency. This is achieved through a continuous improvement process that involves everyone in the organization. The kaizen process encourages employees to identify areas for improvement and come up with practical solutions that can be quickly implemented.
The Kaizen Process
The kaizen process is based on the PDCA (Plan-Do-Check-Act) cycles. This means that an organization first identifies areas for improvement, develops a plan to make changes, implements the changes, and then checks the results to see if further improvements can be made. This continuous cycle of improvement leads to a culture of innovation and progress.
The Kaizen philosophy was first introduced to the world by Masaaki Imai in 1986. Imai is a renowned expert on quality control and management and has been a driving force behind the popularization of the kaizen philosophy. He believes that the key to success is in continuous improvement and that this can only be achieved by involving everyone in the organization.
Reduce Waste with Kaizen
One of the primary goals of the kaizen philosophy is to reduce waste. This includes waste in terms of time, materials, and resources. By using the PDCA cycles, organizations can identify areas where resources are being wasted and take steps to reduce or eliminate this waste. The result is a more efficient organization that delivers high quality products/services a lower cost.
Improvement for the Long Term
The kaizen philosophy is not a one-time fix but a long-term approach. By making small, incremental changes, organizations can gradually improve their processes and systems, leading to significant long-term benefits. These benefits include increased efficiency, higher quality, and a more engaged and motivated workforce.
In conclusion, the kaizen philosophy is a powerful tool for organizations that want to improve and grow. By adopting a continuous improvement approach and involving everyone in the organization, companies can achieve significant long-term benefits and stay ahead of the competition.
Kaizen is for doing and learning. You get rapid gains and it will improve your culture. Art Byrne, former CEO of Wiremold
The Relationship between Kaizen and Standardized Work
The creator of the Toyota Production System Taiichi Ohno once said, “There can be no kaizen without a standard.”
Importantly, before engaging in continuous improvement, management must first establish a stable operating condition. In other words, machines are working, workers are present, jobs are repeatable with quality, and material is available. This is because without a stable operation teams perform kaizen on top of chaos. Consequently, gains rapidly vanish.
Assuming a stable operating condition, leaders should first develop standardized work to create a baseline for improvement. Then, leaders can set targets against this baseline. Once a team achieves a measurable gain, it should update the standard to reflect the new method of working. Critically, this ensures gains do not disappear.
Kaizen and standardized work are linked as John Shook explains in the article “Standardized Work or Kaizen? Yes” .
Eight Steps for Kaizen
- Background — lists the relevant information the audience and participants would need to know.
- Current-state definition — depicts the situation in a graphical, visual manner for the audience to see, e.g., value-stream maps.
- Current-state analysis — various factors, e.g., lead time, service, performance, cost, features, etc., are collectively examined for improvement potential.
- Goals — lists what is to be accomplished by when and specifies the levels of improvement to be obtained.
- Target-condition definition — often included as a visual representation for what the new improved state should look like. This can be a visual image, a flow chart, data, or a comparative look at the desired target condition.
- Implementation plan — there is often substantial work to be done. List the high-level details such as names, responsibilities, dates, and expected outcomes.
- Check results — a vital part of this routine, since improvement requires the demonstration of an improved state. Importantly, you are checking to see whether a new level of performance has been achieved.
- Follow up and standardize — list of actions must be taken to ensure results are sustained in the long run.
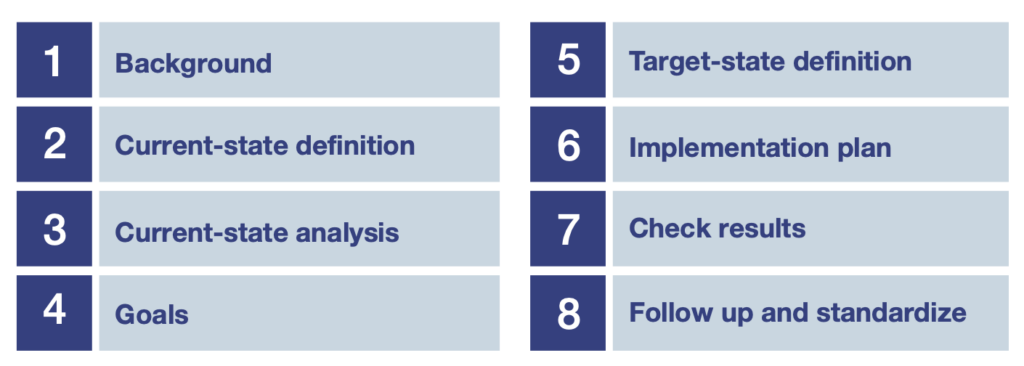
Smalley, Art. 2018. Four Types of Problems: from reactive troubleshooting to creative innovation. Cambridge: Lean Enterprise Institute, Inc.
Kaizen Events
A kaizen event (aka “kaizen blitz” or “kaizen workshop”) commonly last five days. During the event, a team identifies and implements a significant improvement in a process.
A common example is creating a continuous flow cell within a week. To do this a kaizen team analyzes, implements, tests, and standardizes a new cell. The basic steps of such an event are:
- Participants learn continuous flow principles.
- They go to gemba to assess actual conditions and plan the cell.
- They take action to move machines and test the new cell.
- The team standardizes the process and reports out to senior management.
Kaizen events can be excellent activities for developing capability and making substantial changes rapidly . However, leaders should not solely rely on them. This is because steady improvement through daily kaizen forces management to develop frontline problem-solving capability. As a result, business performance improves over time.
Some failure modes of kaizen events include:
- The critical KPI becomes the number of kaizen events held versus meaningful metrics ( e.g. safety, cost, quality, delivery).
- Gains made during the event are rapidly lost, as workers and managers return to the previous way or working.
- Management does not involve frontline workers in the event.
- Specialized engineers typically removed from day-to-day operations lead improvement versus frontline management and operators.
Watch an Example Kaizen Event
Take a Lean Eye Test: See and Improve Work
Watch a short video of an assembly job and try to identify opportunities for improvement. See if your ideas match the final outcome and examine how continuous improvement is not just about improving productivity but respecting people.
Examples across Industries
- Manufacturing — Thrustmaster Comes Around
- Healthcare — View from the Hospital Floor: How to Build a Culture of Improvement One Unit at a Time
- Hospitality — A Radical Redesign to Making Crudito
- Construction — Respect for People: Making the Job Easier for Workers
- Agriculture — Tending the Roots of Lean with Lean Farmer Ben Hartman
- Administration — Lean Thinking Helps City of Chula Vista with Budget Crunch
- Software — Doubling the Number of Performant Apps Using Kaizen
Articles and Books
- Cardboard, Duct Tape, and String: The Do-First Mindset – Mark Reich
- The Hard Work of Making Hard Work Easier – Mark Reich
- What Did I Transform Today? — Josh Howell
- Michikazu Tanaka of Daihatsu on “What I Learned from Taiichi Ohno” – John Shook
- Ask Art: Aren’t You a Little “Old School” in Your Kaizen Approach To Implementing Lean Thinking?
- Kaizen Express — John Shook and Toshiko Narusawa
See: Kaikaku ; Plan, Do, Check, Act (PDCA) ; Value Stream Mapping ; Standardized Work
Privacy Overview

Kaizen: A Complete Guide to Continuous Improvement
- April 3, 2022
- February 18, 2024
- Lean Basics
What is continuous improvement (Kaizen)?
An example of why kaizen is so important, one percent better everyday, 1. create an environment where everyone feels comfortable sharing ideas, 2. involve cross-functional teams in all improvements , 3. avoid any small losses due to waste, 4. let go of assumptions or the status quo, 5. use an iterative approach to avoid perfectionism, 6. think small to avoid paralysis, 7. avoid always going for the obvious solution.
- 8. Remove any obstacles
- 9. Measure your progress
10. Recognize that you will never be done
What are some tools you can use to implement continuous improvement, examples of continuous improvement (kaizen) in work and life.
Kaizen is a compound of two Japanese terms, kai meaning “change” and zen meaning “good”. This term defines the idea of continuous improvement which is the basis of Lean thinking.
Overall, Kaizen, or continuous improvement, is the idea that small, iterative changes to a process can compound to have massive benefits in the long-term.

The key word here is iterative. There is a reason why it is called CONTINUOUS improvement.
Whenever there is a goal you want to achieve, whether that be in your work or in your personal life, it is vital that you focus on small changes and continuously implement these improvements over a long period of time to drive massive results.
This idea of Kaizen was originally developed within the framework of Lean manufacturing, but you can also apply the idea of continuous improvement in every area of your life such as your work, personal goals, and relationships.
By the end of this article, you will have a clear understanding of Kaizen, such as:
- Why it is so important
- The key elements to succeeding at it
- Tools you can use to help implement it
- Examples of it in all areas of life
Why is Kaizen important?
So what’s all the fuss about continuous improvement? Why can’t we just make one big change all at once and call it done?
It’s definitely less exciting to make small, iterative improvements than it is to make one massive change all in one sitting, but continuous improvement is by far a more sustainable approach to any problem or goal.
For example, let’s say you have a goal of losing weight:
Unfortunately, many people who have this goal fall into the trap of taking drastic measures to lose weight quickly.
They may significantly cut their daily caloric intake and increase their workout regime. Not only is this an EXTREMELY unhealthy approach to fitness, but it also is very unsustainable.
After a short time of following this approach, someone may find that they are losing weight as they hoped, but they may also find themselves binge eating due to how much they are restricting themselves, injured due to the quick increase in workout intensity, or just generally burnt out.
Therefore, they will not be able to achieve sustainable results with this approach.
On the other hand, someone could take the continuous improvement approach to weight loss. This would consist of implementing small changes one at a time and building on them slowly.
For example, you could start by going for daily walks then, once you are comfortable with that change, you could try strength training a few times a week and then you can try decreasing your daily caloric intake slightly.
As you continue to build on these changes slowly, you will be able to get a better idea of what is working for you and what isn’t.
Taking this slower approach to a change will allow you to develop a sustainable, enjoyable lifestyle rather than an unsustainable, massive change that makes you miserable.

James Clear also emphasizes this principle of continuous improvement in his bestselling book, Atomic Habits . In this book, Clear promotes the idea of making small improvements everyday in order to achieve massive long-term gains.
“If you get one percent better each day for one year, you’ll end up thirty-seven times better by the time you’re done.” James Clear
A one percent change may not seem notable or even noticeable on a day-to-day basis, but that is the key to why it is so effective.
Making a one percent change to your daily habits will not feel like a large burden in the moment which will allow you to easily implement it in your routine. Then, as you continue to make these very small changes everyday, they will compound into a large change over time.
The same goes for getting one percent worse at something. If you slowly implement bad habits in your life, they may not have a drastic impact on your life immediately, but they will have massive detrimental results in the long-term.
Therefore, it is key that we focus on making small, sustainable, positive changes everyday to drive continuous improvement in any facet of our lives.
What are the keys to succeed with Kaizen?
Now that you understand why the idea of Kaizen, or continuous improvement, is so important, let’s take a look at the top 10 ideas you need to keep in mind in order to succeed at it.
One of the most important aspects of continuous improvement, especially within a company or organization, is making sure that everyone from all levels is involved in making improvements. To achieve this, organizations will need to create an environment where everyone feels as though they have a voice in making changes.
In practice, Kaizen is more than just an action plan to make improvements; it is a way of thinking that needs to spread to everyone in an organization in order to be most effective. It is not helpful if senior leadership or manager-level employees are engaging in discussions of continuous improvement if they are not engaging the frontline workers.
Organizations can create this environment by:
- Training all employees on the concept of Kaizen
- Hosting focused Kaizen events where all personnel involved in a particular process can voice their thoughts on potential improvements
Beyond the manufacturing or corporate environment, this idea of creating a space where everyone feels comfortable voicing an opinion is also vital when it comes to improving personal relationships. If all parties do not have a voice in a relationship, this will create conflict since someone may feel disrespected.
This first point is then closely related to the next key for success in continuous improvement…
Once an environment exists where everyone feels comfortable sharing their thoughts, it is important that a cross-functional team is involved in making all improvements.
This ensures that you are capturing ALL thoughts and perspectives before making a change. Therefore, you will avoid making changes that only benefit certain groups involved in a process.
This will result in increased efficiency and productivity in the long-term, as well as increased satisfaction from all involved groups.
When you are trying to decide on what to improve in a process at work or in your daily life, you should consider if you have any sources of waste in the current process.
The primary focus of Lean thinking is reducing waste in order to improve efficiency and productivity. Therefore, there are 8 identified forms of waste in Lean. These 8 wastes are:
- Overproduction
- Non-utilized talent
- Transportation
- Excess Processing
You can get a full overview of the 8 wastes of Lean and examples of each in both a manufacturing environment and daily life in my article here .
When you look into any process, I guarantee you will find at least one of these forms of waste. This can be an easy starting point for continuous improvement.
In order to continuously improve, you must be able to think outside of the status quo. If you continue to do things a certain way because “that’s how they have always been done”, you’re not allowing yourself the opportunity to see areas for improvement. This will leave you in a place of stagnation.
“If you always do what you’ve always done, you’ll always get what you’ve always got.” Henry Ford
In Kaizen, we are always striving for better results so we must be willing to try new ideas and methods.
In Lean thinking, continuous improvement is one of the five principles of Lean , but this is also sometimes referred to as “strive for perfection”.
This name can be a bit misleading though…
If you approach Kaizen with a mindset of perfectionism, you will likely never get started because you are looking for the perfect solution.
Therefore, you should treat continuous improvement as an iterative process where you slowly improve a process step-by-step. That is why it’s called CONTINUOUS improvement after all.
This also leads into the next point…
In order to avoid perfectionism in a process, it is key to think small. This means that you should create small, intermediate goals that you work towards on your way to achieving a larger goal.
Therefore, you will avoid feeling paralyzed by overwhelm from having such a large mountain to climb to reach your goal.
For example, if your goal is to write a book, you can break this down into very small steps. These could include:
- Determine a topic
- Complete your research
- Determine what sub-sections or chapters you want to include
- Write an outline
- Begin writing the content one chapter at a time
It is also key to avoid tackling the obvious solution every time you want to improve a process. The obvious solution is likely very surface level and won’t achieve the maximum potential.
Therefore, it is vital that you do research at the beginning of the improvement process. Root cause analysis can be a very useful tool for this.
In Lean, some root cause analysis tools include Ishikawa or fishbone diagrams, the 5 Why technique, Pareto charts, fault tree analyses, and failure mode and effects analyses (FMEA).
These tools will give you a better idea of all the root causes of the problem you are trying to solve or improve. Therefore, you will have a much clearer path to follow when approaching continuous improvement.
8. Remove any obstacles
When implementing continuous improvement in either a manufacturing environment or daily life, it is also key that you remove any obstacles that prevent the improvement cycle from happening.
In a manufacturing environment, this includes removing any obstacles that prevent employees from engaging with new improvement ideas. You can achieve this by implementing clear processes for giving suggestions such as:
- hosting Kaizen events,
- creating suggestion boxes,
- or completing daily Gemba walks.
For personal goals, this would likely mean removing any distractions from your life that prevent you from carrying through with the improvement. You can achieve this by:
- building solid habits,
- time blocking your schedule so that you have dedicated time to work towards your goals,
- or communicating your goals to those around you so that they can support you.
9. Measure your progress
Once you have started to improve your process or work towards a goal, you MUST be sure to measure your progress. This will allow you to see how you are doing in relation to your target state as well as areas for improvement.
If you are working towards a goal with others, such as in a manufacturing environment, you must also ensure that everyone involved in the process is aware of where the progress stands. That way, they can continue to offer valid feedback and suggestions to further improve.
The final point you must remember if you want to succeed at continuous improvement is that you will never be done. Again, it is called CONTINUOUS for a reason.
As you implement changes to improve a particular process, you will undoubtedly uncover new areas that you can work to improve.
You will also begin to recognize other areas of the company or other areas of your life that need improvement.
As you continue to practice Kaizen, it will get easier since you, and those around you, will adapt to the new mindset of thinking towards improvement.
You can use the concept of Kaizen or continuous improvement in any area of life. Some examples include:

Manufacturing

Relationships

Entrepreneurship
Kaizen, or continuous improvement, can allow you to achieve massive long-term goals or solutions by slowly implementing positive changes. When you develop the ability to think with a mindset of continuous improvement, there is no end to the goals you can achieve.
If you are able to practice the ideas of continuous improvement outlined in this article, I guarantee that you will see drastic benefits in both your work and your personal life.
Are there any areas in your life where you think you could benefit from the Kaizen approach? I’d love to hear from you in the comments below!
Lindsay Jordan
Hi there! My name is Lindsay Jordan, and I am a full-time Chemical Process Engineer. That means I work with the principles of Lean methodology everyday. My goal is to help you develop the skills to use Lean methodology to improve every aspect of your daily life both in your career and at home!
Leave a Reply Cancel Reply
Your email address will not be published. Required fields are marked *
Name *
Email *
Add Comment *
Save my name, email, and website in this browser for the next time I comment.
I accept the Privacy Policy
Post Comment
This site uses Akismet to reduce spam. Learn how your comment data is processed .
Trending now

Kaizen — what it is, how events work, and why it’s important for optimizing your business and your teams

As business teams have adopted more lean practices and processes, kaizen has also made the jump from manufacturing environments to offices. This Japanese business philosophy has helped world-leading companies like Toyota optimize their processes.
But kaizen offers tangible benefits to operations teams as well. To help you understand kaizen and how to use it to help your teams, this post will cover:
What is kaizen?
Kaizen events, advantages of kaizen, examples of kaizen for business.
Kaizen is a business philosophy that focuses on continuous improvement across the entire organization. The kaizen model helps companies focus on gradually and consistently increasing efficiency and reducing waste within processes. To do this, kaizen encourages input from any employee — from the factory floor to the C-suite — at any time.
https://main--bacom-blog--adobecom.hlx.page/blog/fragments/the-eight-wastes-of-lean
The kaizen method became popular in post-war Japan, at manufacturers like Toyota. Kaizen broadly means continuous improvement in Japanese. In the Toyota Production System, if a line worker sees an issue, they stop production and figure out a solution with their supervisor. The people who are involved in the daily work have the authority to make needed changes without formal approval from management. And they don’t need to go through long, drawn-out processes to enact change. This enables continuous improvement.
Traditionally, kaizen is a big part of lean project management in the manufacturing industry, but businesses in many other sectors are catching on to its effectiveness and implementing kaizen events.
A kaizen event is a three- to five-day team workshop in which employees, managers, and sometimes C-suite executives make an actionable plan to improve an existing process. Kaizen events often follow Gemba Walk s or the discovery of an inefficiency. Gemba Walks are visits to workplaces where management teams can witness processes in order of operation, talk to employees, gather insights, and identify any issues.
Value stream mapping is another useful tool for finding inefficiencies and problems. Create a process and material flow chart with the information you gained during the Gemba Walk. This detailed visualization of your processes provides an overview of the steps involved and can help identify waste.
After you’ve identified problems or bottlenecks in a process, start making small, continuous improvements. During the kaizen event, team members collaborate and think of solutions. The ideal outcome of these events is an actionable plan that is ready for immediate implementation.
Types of kaizen events
As kaizen has been applied to operations and other business environments, the types of kaizen events have grown and evolved. Kaizen events can take many forms to best serve their business application. Here are some of the most common types of kaizen events and when to use them.
- Focused-improvement kaizen. A focused-improvement event is a kaizen event centered on a single, known issue. Prioritize your most important losses and develop solutions to eliminate them. The scope of focused-improvement kaizen events is one, achievable goal.
- Waste kaizen. This type of event focuses on eliminating waste in your processes, as opposed to improving systems that are currently working. There are eight wastes of lean that a waste kaizen event might aim to address.
- Error-proofing kaizen. Use this type of event to reduce human error by improving processes. This could be as simple as standardizing checklists. Or it might mean automating parts of a system.
- Lead-time kaizen. This kind of event is suitable when you realize one of your processes is taking too long. The event aims to reduce the amount of time it takes to complete a process, like the time from processing an order to the customer receiving their goods.
How to run a kaizen event
There is no single, definitive way to conduct a kaizen event. Business teams all over the world have shaped kaizen events to meet their own needs. If you’re just getting started with kaizen, the plan-do-check-act (PDCA) framework is common and often recommended.

The Gemba Walk, mapping your value stream, and identifying the problems in your processes are part of the planning stage in a PDCA cycle. Follow these steps to get started.
- Speak to employees. They’re the people who know the daily process better than anyone, so find out what problems or issues they're aware of. This often happens on a Gemba Walk.
- Define and analyze the problem. When you’ve decided which issue to tackle, break it down and find the bottleneck in the process. Value stream mapping is helpful here.
- Establish the metrics you’ll use to measure success. Without this data it’s impossible to analyze the results after you’ve tested the solution.
- Decide on a goal. You should have one goal that is achievable within the event time frame.
- Finalize the steps and processes that will help you achieve your goal. Work as a team to find solutions to the problem. There should be no limits on the kind of solutions encouraged. Allow employees to use their creativity. Choose one with potential to start with.
2. Do Run a small scale test of your chosen solution. Make sure every team member involved is aware of the change and let it run long enough to gather meaningful data and feedback. 3. Check Collect data from your test and — using the metrics you already selected — assess its success. Talk to employees and other team members to get their insights as well. They will often have input that’s not captured in measurable data. 4. Act or adjust If the test was a success, implement your improved process company-wide or as a permanent update. However, if you found issues, or if the solution didn’t work, refine the process and run further tests or choose a different solution and try again. This should be a cyclical process. The kaizen event might be a one-time, three-to-five day event but the process of improving never stops. To keep the continuous loop going, repeat the cycle. Find more processes to improve or try out other solutions.
Kaizen has a lot to offer any kind of business. More organizations are adopting kaizen to optimize their workflows, reduce waste, and remain competitive. Here are some of the biggest benefits.
- Eases change. When organizations make sweeping changes, getting staff on board can be tough. With kaizen, small, ongoing changes are a gentler approach, so employees are more likely to adopt changes.
- Optimizes processes and resources. Kaizen reduces waste and errors in your processes. With fewer errors, you use fewer resources conducting inspections or correcting mistakes.
- Encourages employee engagement. One of the key principles of kaizen is that employees have a stake in the organization. This accountability increases employee motivation. Employees taking responsibility for improving processes gives them a purpose. And engaged, accountable employees are more likely to stick around.
- Strengthens teams. The collaboration and accountability of kaizen boosts teamwork, because employees are an active part of process improvement and are working together on a shared goal.
Many companies have successfully implemented kaizen. Let’s look at some examples.

Ed Catmull, co-found of Pixar, has spoken about his inspiration from Japanese lean manufacturing processes. The lessons he learned from an engaged workforce creatively solving problems at companies like Toyota is evident in Pixar’s processes.
One example of kaizen at Pixar is the Brain Trust . They’re a group of creative leaders who get together to collaborate, give honest opinions, and find problems within new movies. With a focus on candor and empathy, Pixar’s Brain Trust roots out problems in the creative process. Just like with kaizen in other industries, everyone is involved and has the power to make suggestions.
The Brain Trust is a big part of the Pixar process ever since it turned around Toy Story 2 . What was supposed to be a straight-to-video release, became a critical and commercial success. Now the Brain Trust gets together for all Pixar movies to identify issues in the process and suggest solutions.

Nestlé uses kaizen and lean processes to reduce waste in its factories. For example, Nestlé leadership did value stream mapping at a new bottling plant to find waste. This resulted in more efficient processes at the factory.
Nestlé has also used kaizen to change the company culture . Executives demonstrate the importance of kaizen and encourage employees to engage with the improvement process. Employees are empowered to make improvements and use the best tools and methods available.
Getting started with kaizen
Kaizen allows organizations to make small, iterative changes for continuous improvement. It does this by encouraging collaborative and creative problem solving. The result is streamlined processes, increased efficiency, and less waste. And on top of all that it gives your employees accountability, purpose, and a stake in the organization's success.
A good place to get started with kaizen is by analyzing current processes. Conduct Gemba Walks, analyze data, and talk with employees to identify any issues or loss in your systems. When you’ve compiled your list of issues, you can find the right kind of kaizen event for your needs.
Adobe Workfront is the solution more businesses use to optimize lean processes like kaizen in their workspaces. Workfront helps organize feedback and insights, define your solutions, share your plans across the organization, and provide visibility to get the work done.
Take a free product tour or watch the overview video to see how Adobe Workfront can help your business team continuously improve.
https://business.adobe.com/blog/basics/quality-management
https://business.adobe.com/blog/basics/priorities-management

Home PowerPoint Templates Kaizen
Kaizen PowerPoint Templates
Download pre-designed Kaizen PPT templates and slide designs for presentations. Kaizen is a system of continuous improvement in quality, technology, processes, company culture, productivity, safety and leadership. Download awesome Kaizen slide designs and PPT templates that you can use in presentations on total quality management and continuous improvement slide designs.
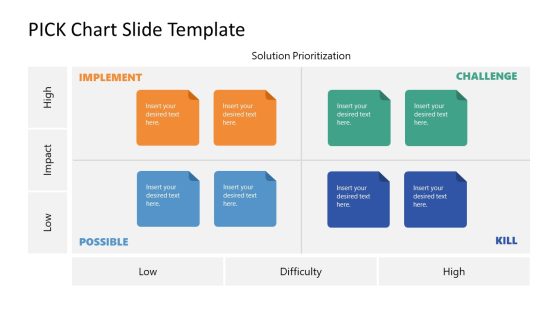
Kaizen PICK Chart Template for PowerPoint
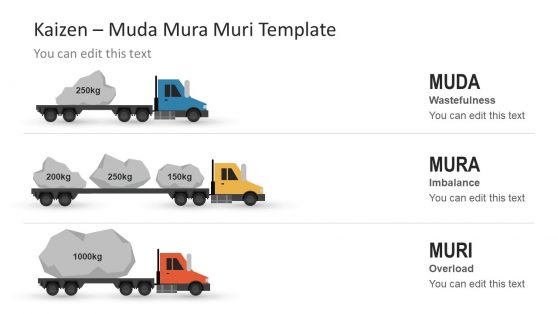
Kaizen Muda Mura Muri Template for PowerPoint
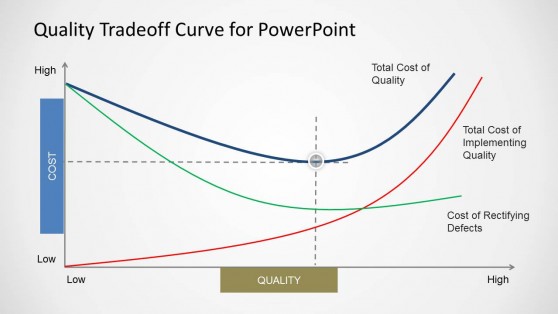
Quality Tradeoff Curve for PowerPoint
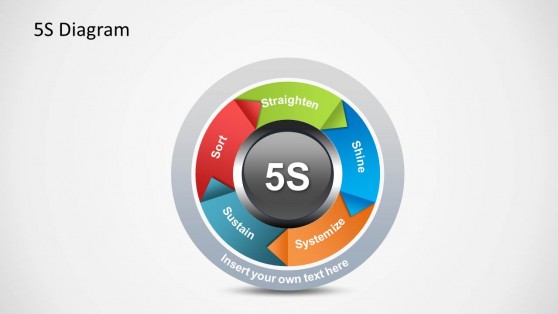
5S Diagram Template for PowerPoint
Download unlimited content, our annual unlimited plan let you download unlimited content from slidemodel. save hours of manual work and use awesome slide designs in your next presentation..
- Contact sales
Start free trial
5 Kaizen Principles That Underpin the Methodology

We all want to improve, or we should. Complacency might feel good in the moment, but that moment quickly passes. Don’t be left behind. The question is how can one improve? There are many answers, from educational and physical fitness to spirituality. But is there a unifying theory of improvement, and if so, can it be sustained?
Have you heard of kaizen? It’s a Japanese word that literally means improvement. That feels like a good place to start on our quest towards improvement.
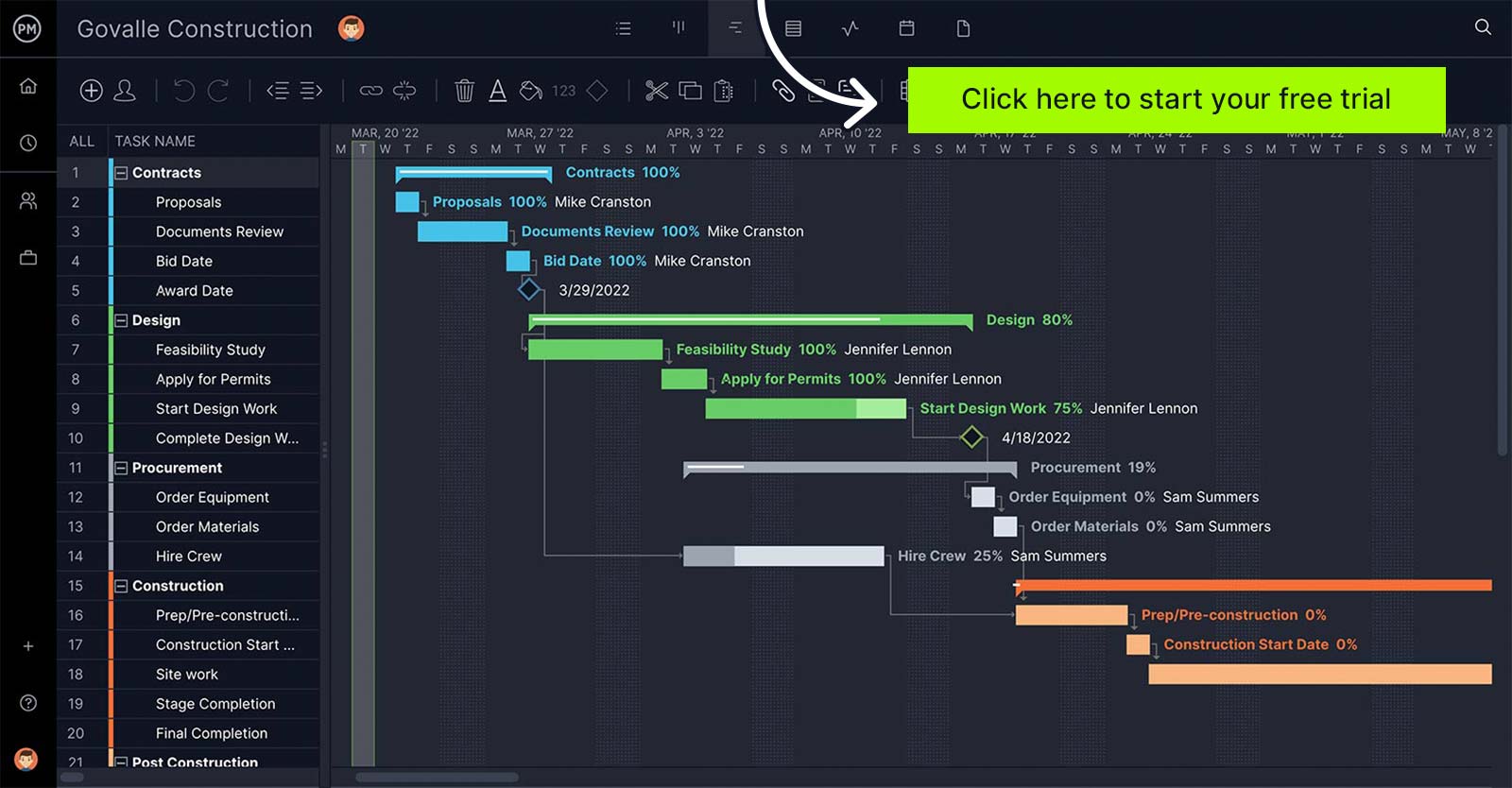
Kaizen Methodology
Kaizen means improvement, but more than just that, it means continual improvement. Improvement that is not reaching beyond what it can currently do is static.
Kaizen, more precisely, means change for the better (kai is change and zen is for the better). In terms of business, kaizen means that all activities must be continuously improving. That means everything in the organization, from employees to the CEO. But it’s not just applying to personnel, processes are also included.
The idea was codified by Masaaki Imai, an organizational theorist and management consultant, over 30 years ago with the publication of this book, Kaizen: the Key to Japan’s Competitive Success. Since then, the implications have reached beyond industry and the kaizen principles have been used to help in healthcare, psychotherapy, government, banking and even life coaching.
The kaizen methodology works at constant improvements through the elimination of waste. It’s been around in Japan since after World War II, though influenced by quality management ideas from the United States. It’s part of The Toyota Way , which is a set of principles that support the company’s management approach to production.
Kaizen Principles
The five principles of kaizen are fundamental to any application of kaizen.
- Know Your Customer: Knowledge of who your selling a product or service to is how one creates value. It is key that companies identify their customer’s interests to enhance their experience.
- Let It Flow: This applies to the target of achieving zero waste. It might be an impossible goal, but that’s kaizen for you: if you could achieve that objective improvement would stop. Therefore, everyone in the organization is working towards removing any waste from their corner of the business while also in the process creating value.
- Go to Gemba: The literal translation for gemba is “the real place.” In this context, it’s about leadership and knowing what is happening at every level of the organization. You can think of it as following the action, as value is created where something is actually happening. That’s where you want to be.
- Empower People: This one is directed towards teams and having them organized in such a way that it supports the kaizen principles. Therefore, leadership must set goals for their teams that are not contradictory. They should offer a system and tools to help the teams achieve these goals.
- Be Transparent: Data is the strongest determining factor. It’s the metric that measures success. Therefore, performance and improvements must be tracked with real data
Kaizen in Action
The principles are the guiding lights, the action plan is where kaizen hits the road running. It’s all about organizing, so that the focus is always on improvement and its target are every part of the organization. Everyone is part of the process. A consistent application of the kaizen action plan leads to continuous improvement.
First, take each corner of your organization and look at ways they can be improved. This will involve team collaboration and total involvement from everyone. Individuals need autonomy to take action on improvements themselves, which builds a culture of engagement. This is done with a continuing flow of suggestions and then implementing them to improve the organization.
Each event is outlined by the acronym PDCA, which stands for plan, do, check, act. Begin by setting goals, with documentations and background. Then review what the current state is with that part of the business and plan towards improving it. Identify what improvements will be implemented and try and fix what isn’t working. Report the results, follow-up and repeat.
The idea of always making small improvements is not dissimilar to lean manufacturing , especially with the emphasis of eliminating waste. Kaizen, like a lean or agile approach, works with iterations. It keeps companies flexible.
How Kaizen and ProjectManager Work Together
Ideas are great and methodologies are fundamental to implementing those ideas. But the best plans of mice and men often go astray if they don’t have a project management tool to track their progress. ProjectManager is a dynamic and nimble software that cashes the check that kaizen writes.
ProjectManager has Kanban Boards to Track Progress
What ProjectManager.com provides is a way to monitor that improvement. Kanban is another Japanese work, which translates as signboard or billboard. It also grew from the Toyota Way of manufacturing, offering a visual workflow that increase efficiencies by making sure that the supplies you need now are always on hand, but not more that must be stored.
It’s an elegant system of columns and cards. Each column can have a to do, doing and done heading. Under each of those column headings are cards, which capture the individual task. These cards are then moved from column to column as they’re identified, worked on and completed.
These boards are a great way to track the progress of the improvements. With ProjectManager.com, the kanban boards are even more useful, as they can be assigned to specific team members or a whole group. Then, because the software is online, as teams update their status that information is instantly reflected across the software.
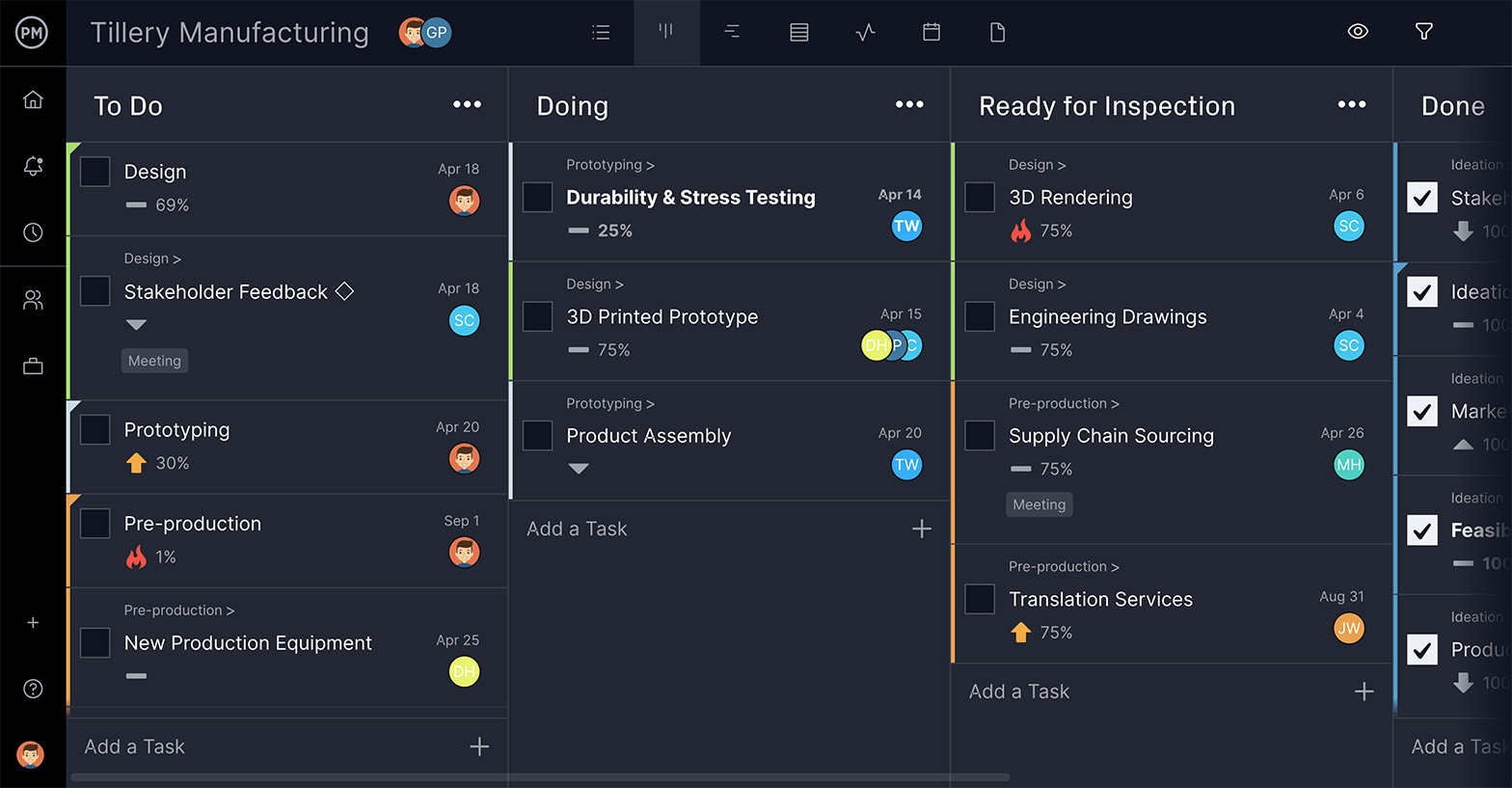
ProjectManager.com’s Real-time Dashboard Tracks Progress
Kaizen encourages collaboration and ProjectManager supports teamwork by giving teams a platform to communicate at the task level. Documents and images can be attached to the card in the board view of our software, so these important files are easy to access. There is a conversation box to dialogue with other team members. When a comment is added, all those assigned the task are notified. It’s especially helpful if your teams are distributed in different sites.
But teams aren’t the only ones who benefit from ProjectManager. Just as kaizen involves the whole organization in making continuous improvements , ProjectManager also gives managers the tools they need to assign easily and monitor the progress of the improvements as they’re implemented.
While project managers can view the progress of the kaizen implementation on the kanban board, they probably are going to want more detailed information. ProjectManager has a real-time dashboard that collects all the data team members input and then crunches those numbers into a series of project metrics that are displayed all in one place.
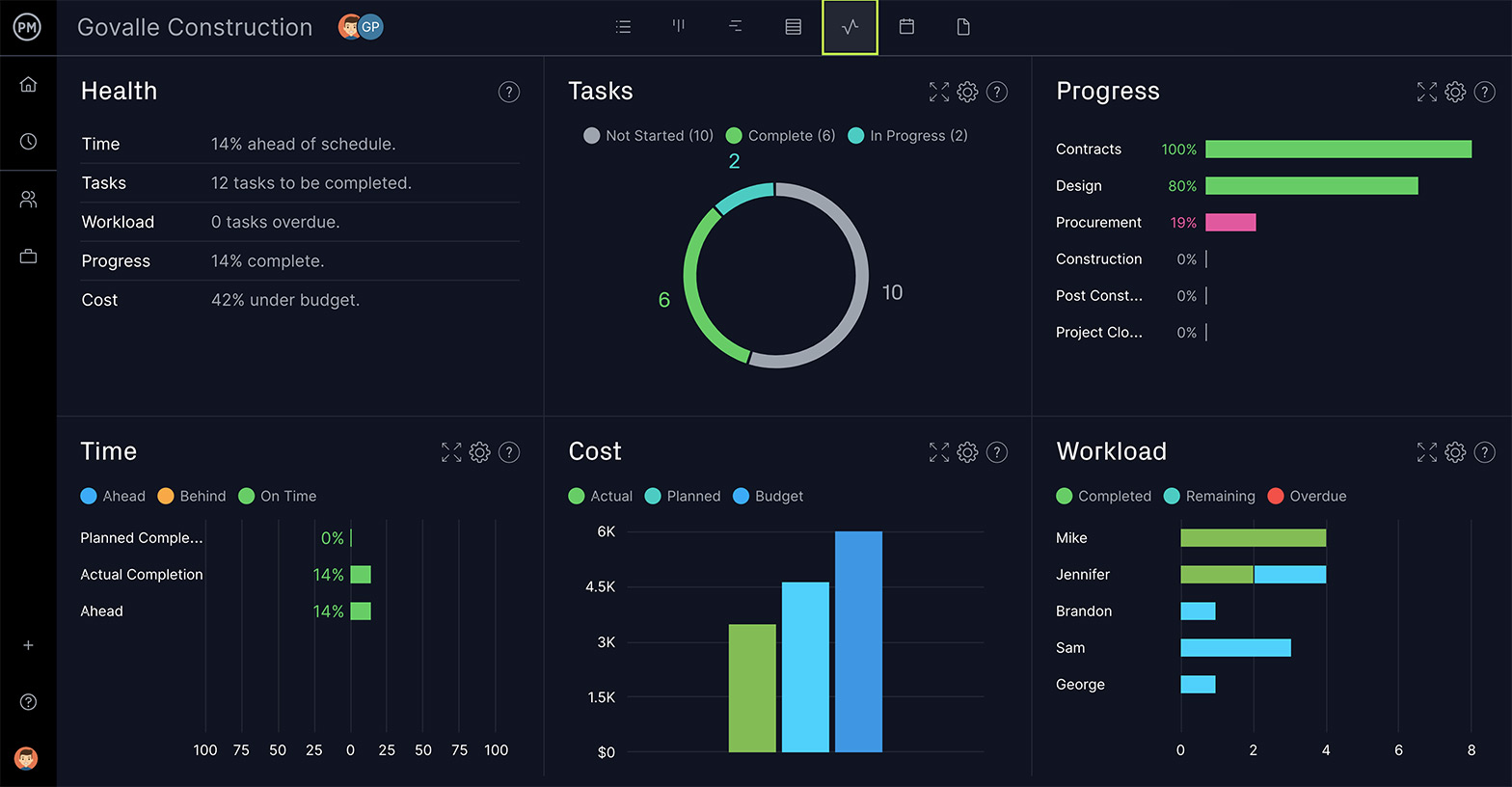
The real-time dashboard has colorful and easy to read graphs and charts that track progress, workload, timelines and more. These can be shared or printed out for presentation. But in ProjectManager.com, the graphs and charts can be filtered to show just the amount of data you need. This means when a project manager is discussing items with the team, they can go deep into the data, but if the stakeholders need a more general overview, that can be displayed in a click.
Kaizen and ProjectManager.com are a match made in project management heaven. But ProjectManager can do so much more than help you implement change. Our cloud-based project management software can plan, monitor and report on any kind of project. Online Gantt charts makes scheduling collaborative and teams love our easy-to-use task lists and timesheets. See how ProjectManager can improve your project management today by taking this free 30-day trial.

Deliver your projects on time and under budget
Start planning your projects.
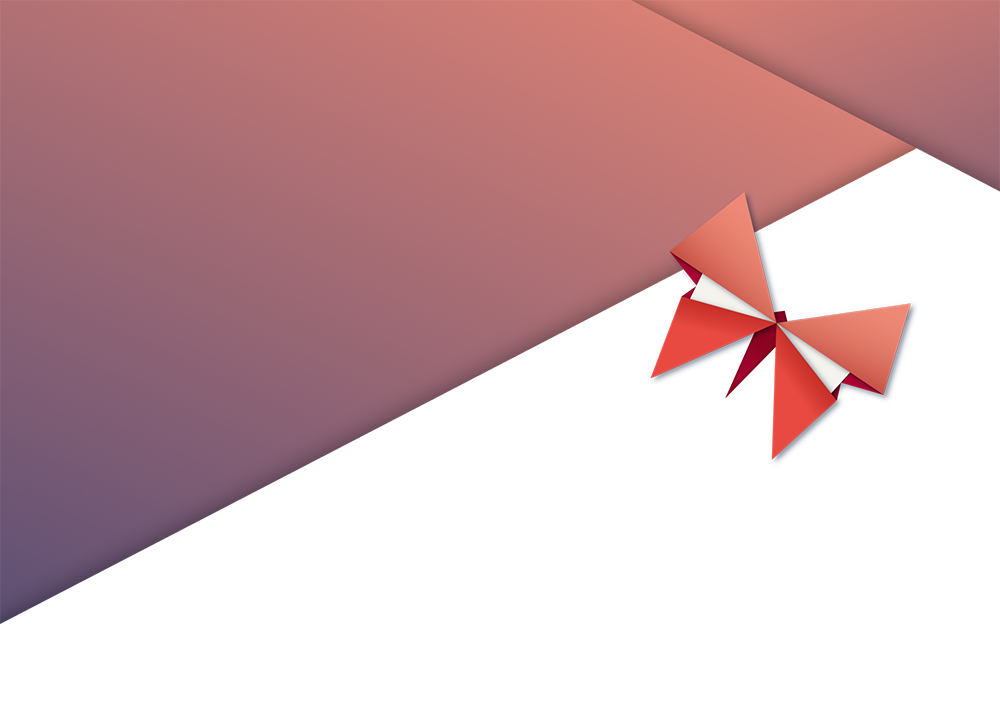
What is KAIZEN™
Dive into the kaizen™ methodology, improving the world with everyone, everywhere, every day – the kaizen™ way, definition of kaizen™.
Over 30 years ago, Masaaki Imai sat down to pen the groundbreaking book ‘Kaizen: The Key to Japan’s Competitive Success’ (McGraw Hill). Through this book, the term KAIZEN™ was introduced in the western world. Today KAIZEN™ is recognized worldwide as an essential pillar of an organization’s long-term competitive strategy. Since introducing this term as a systematic approach to business improvement, companies that implement KAIZEN™ have continually yielded superior results.
“KAIZEN™ means improvement. Moreover, it means continuing improvement in personal life, home life, social life, and working life. When applied to the workplace KAIZEN™ means continuing improvement involving everyone – managers and workers alike.” Masaaki Imai, Founder of Kaizen Institute
The Core of KAIZEN™
There are 5 Fundamental KAIZEN™ Principles that are embedded in every KAIZEN™ tool and every KAIZEN™ behavior. The 5 principles are: Know your Customer, Let it Flow, Go to Gemba, Empower People and Be Transparent. The implementation of those 5 principles in any organization is fundamentally important for a successful Continuous Improvement culture and to mark a turning point in the progression of quality, productivity, and labor-management relations.
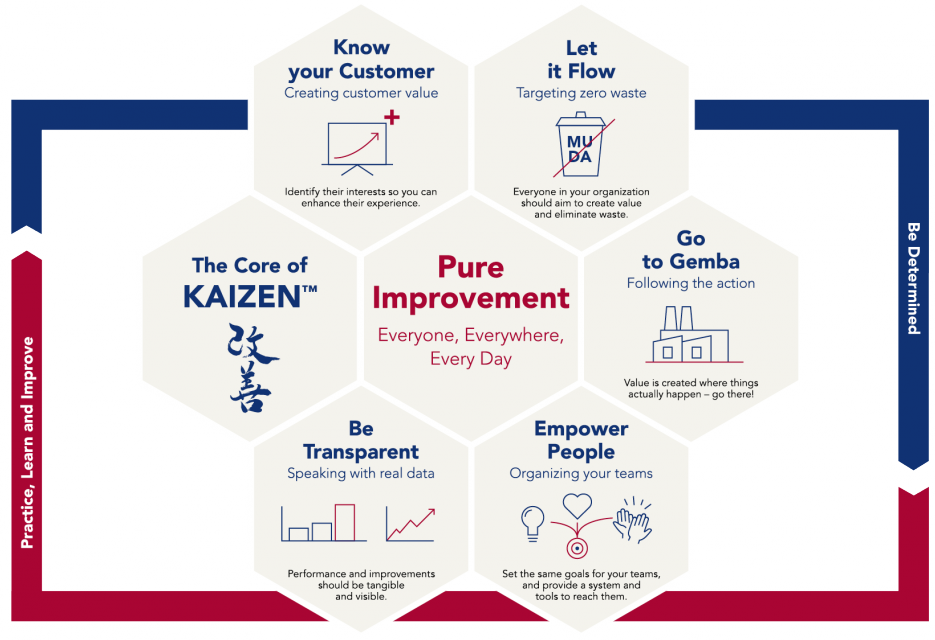
Level up you KAIZEN™ Skills
Discover our training offers and how we can support your organization implement Continuous Improvement
Want to know more?
Go back to basics and learn more about the KAIZEN™ terminology that reinforces the KAIZEN™ culture
KAIZEN™ Methodology Development History
The KAIZEN™ methodology has gradually developed over many decades. It was publicly and officially introduced to the world in the 1980s as a systematic methodology through the best-selling book “KAIZEN™” by Masaaki Imai, the founder of Kaizen Institute.
Masaaki Imai is born in Tokyo, Japan. The first domestic automotive production is planned in Japan, and the Just-In-Time concept is observed.
World War II to post-war economic reform period commences in Japan.
Imai works at the Japan Productivity Center in the USA and accompanies Japanese executives to visit and learn from US manufacturers. Japanese companies gain strength in their quality and worldwide competitiveness.
Imai works with Shoichiro Toyoda to observe the American way of business.
Imai works internationally with Taiichi Ohno to spread the message of the Toyota Production System (TPS).
KAIZEN™ is introduced to the world for the first time, as a systematic management methodology.
1990’s
KAIZEN™ appears for the first time as a word in the Oxford dictionary.
The term Lean was coined.
Lean concepts are promoted through various publications, to include Imai’s GEMBAKAIZEN™ book.
Tools, such as Six Sigma, gain popularity though clouding the importance of a systematic approach.
Kaizen Institute continues to offer practical, hands-on methods that fit the local culture and business practice, when implementing KAIZEN™ within organizations.
2000’s
KAIZEN™ Management System (KMS) is developed, to help companies to improve based on a systematic QCD Model.
KAIZEN™ Change Model (KCM) is added to enhance a KAIZEN™ culture, mindset and behaviors of the organization.
Many corporations start developing their own improvement strategies based on KAIZEN™, seeking to gain sustainable improvements and a competitive advantage within their markets.
KAIZEN™ Business System (KBS) supports organizations to achieve Continuous Improvement and sustainable growth.
Kaizen Institute continues to spearhead global development for the KAIZEN™ methodology, bringing awareness to Everyone, Everywhere, Everyday.
The KAIZEN™ Way
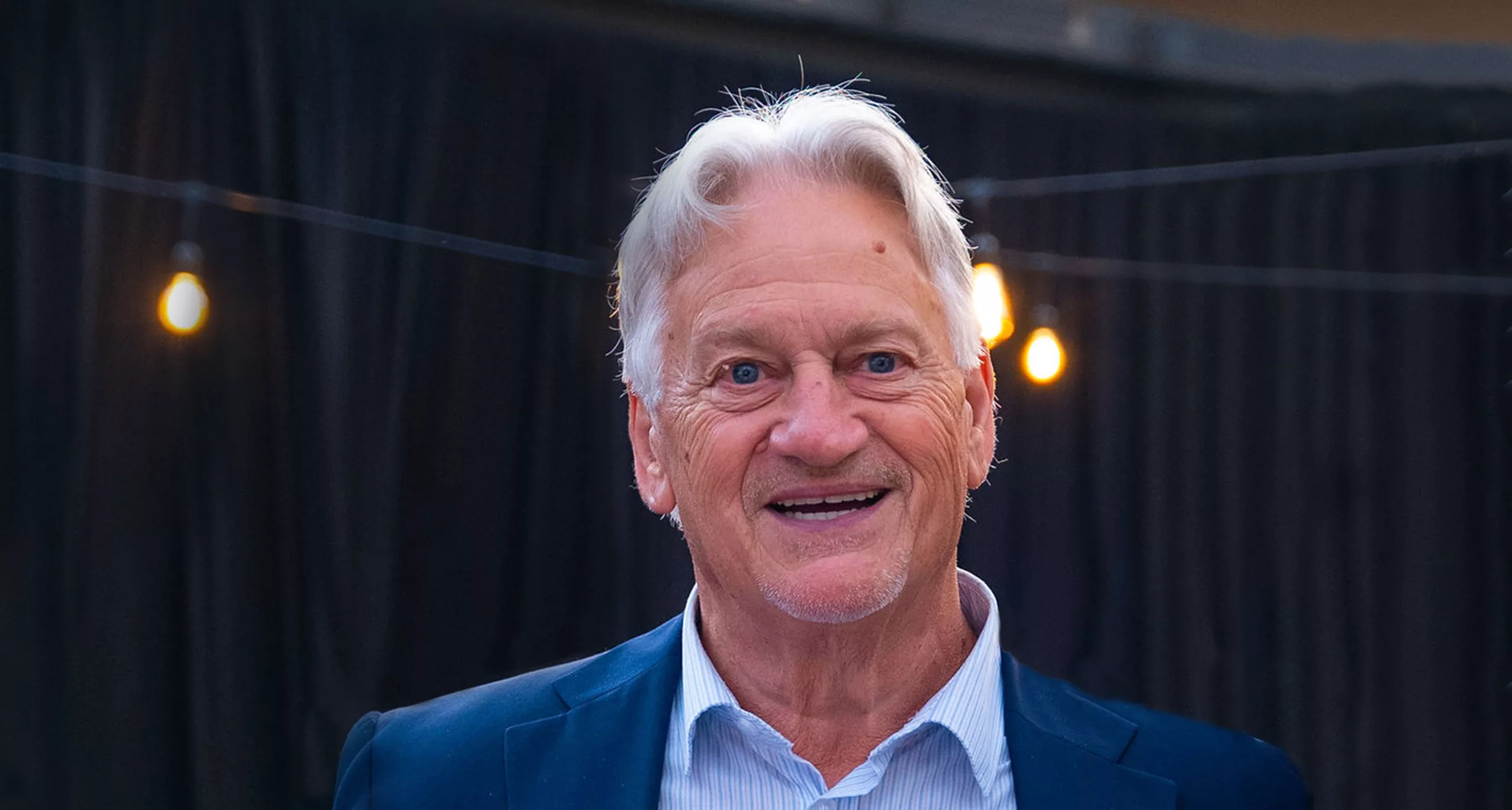
Kaizen Institute Announces the Passing of Charlie Sharman, Advisor of Kaizen Institute
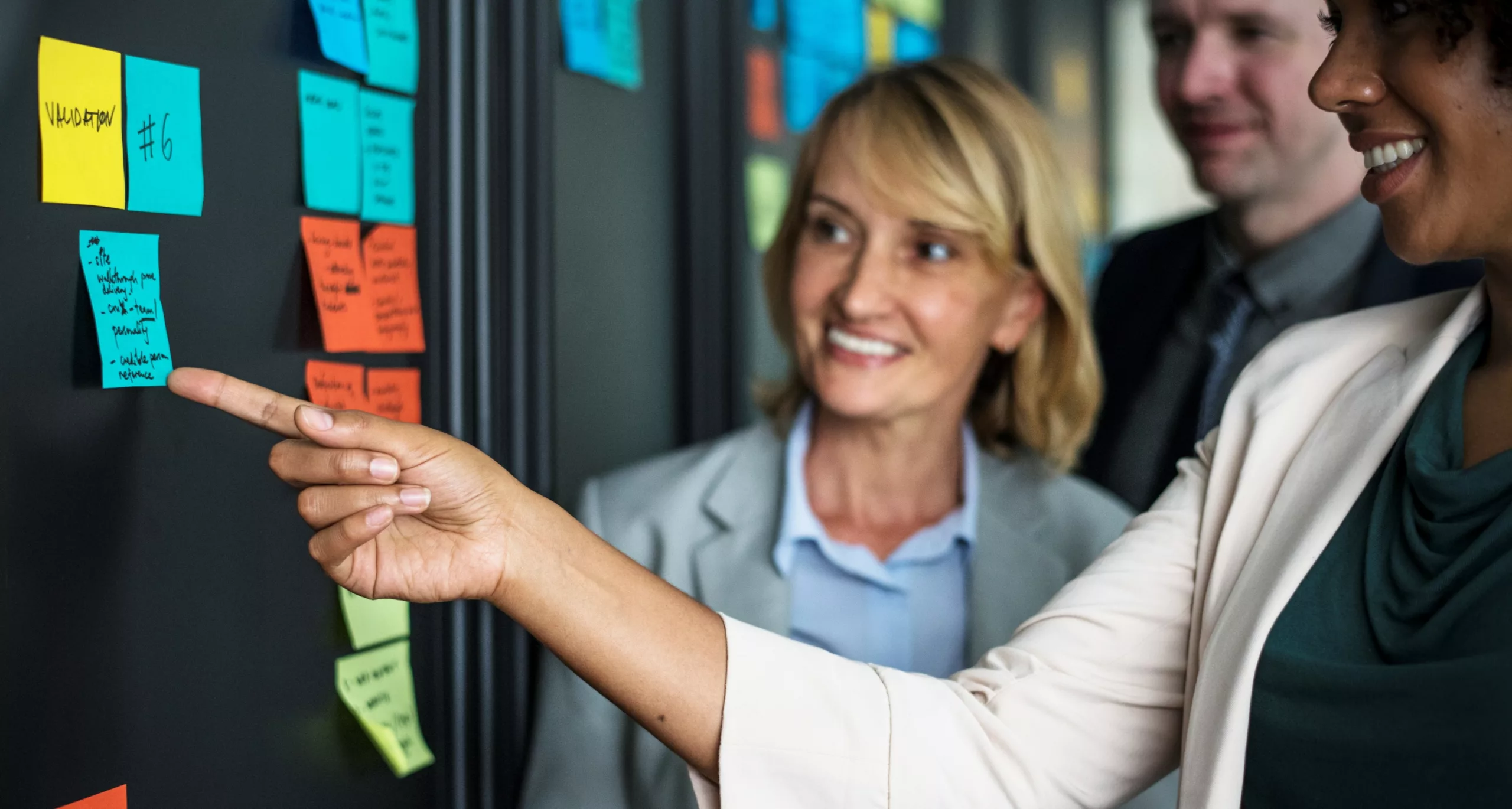
Mastering Kaizen and Lean Management for Operational Excellence
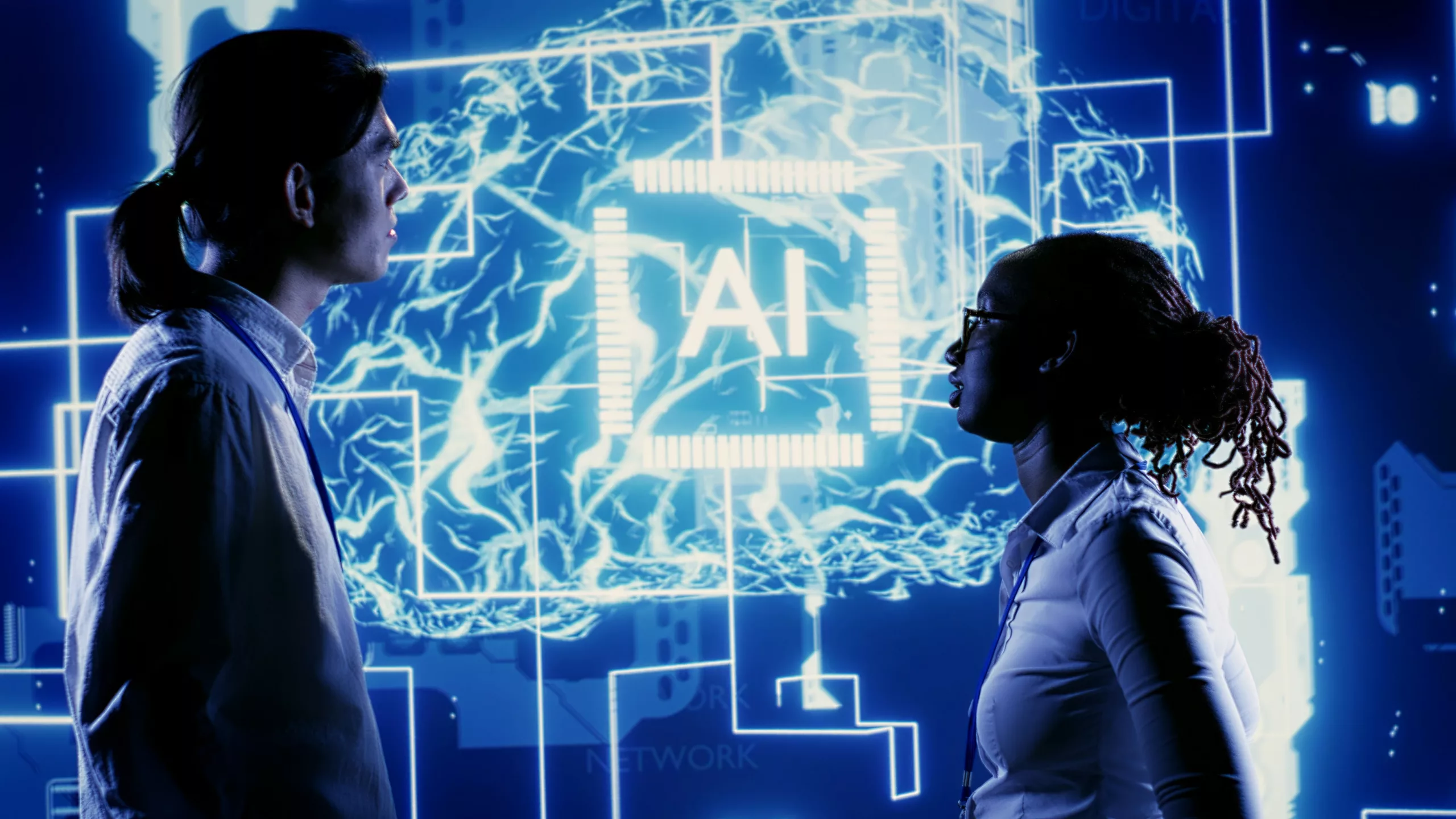
The Rise of Customized Generative AI Models in Enterprises
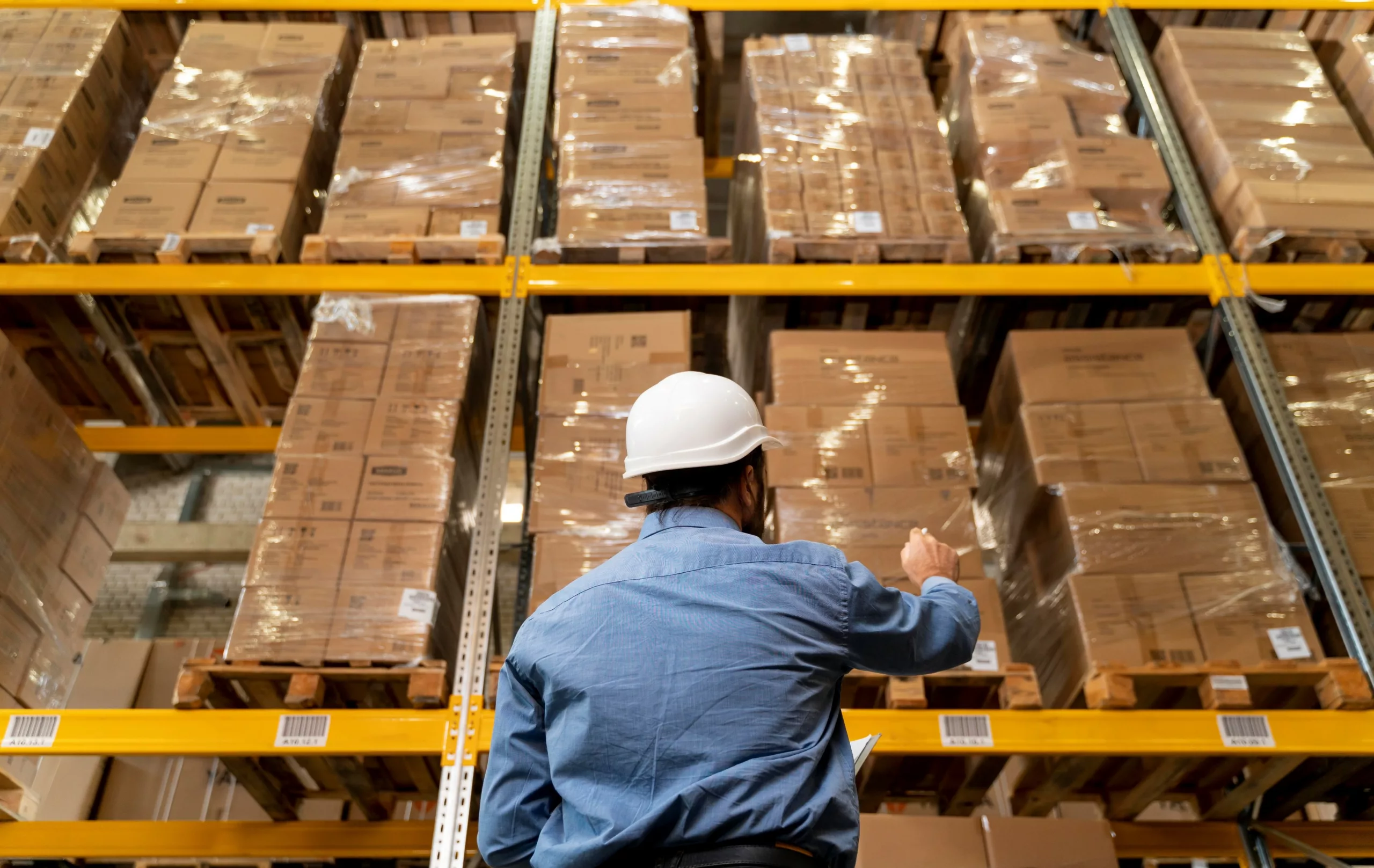
Implementing Kaizen for pull flow in the supply chain
Download pdf.
We noticed you're visiting from United States (US). We've updated our prices to United States (US) dollar for your shopping convenience. Use Euro instead. Dismiss

Where Thought Leaders go for Growth

The Kaizen approach: 6 steps to continuous improvement
Table of contents, a short history of the kaizen approach, personal and professional development, the 5 elements of the kaizen approach, the strategic objectives, the benefits of the kaizen approach, the drawbacks, the 6 steps of the kaizen approach, methods that can be combined with the kaizen approach, choose the right tool, step-by-step progress to meet your goals.
Are you familiar with the Kaizen approach ?
Known for being a quality management , collaboration, and continuous improvement tool, the Kaizen approach advocates progressive change management in a business, while limiting risks.
More efficient, more productive, more competent... We are constantly pushed to be better while going to the essential. This can be quite a challenge!
There are two schools of thought for this: radical change or continuous improvement . The fast track or the slow track. Pressure or experimentation. The Kaizen method, in the second category, is appreciated in process management for its reassuring side, supervised and not rushed, with the perspective of a soft but constant evolution.
From productivity to well-being at work , we will explain how this managerial technique works. And, perhaps you will want to try it?
What is the Kaizen approach?
A true Japanese development philosophy, kaizen is composed of two words, kai 改, and zen 善 which means "change" and "better".
Also known as the small-step work improvement approach , or the method of continuous improvement , the Kaizen approach was developed in the United States under the Training With Industry (TWI) program, set up by consultants (including W. Edwards Deming) under the supervision of General MacArthur, to help the Japanese industry recover after World War II.
Masaaki Imai made the term famous in 1986 with his book “Kaizen: The Key to Japan's competitive success”.
Initially implemented in the industrial sector, it was used for lean manufacturing , a management approach to reduce waste and increase profits.
Today, the Kaizen approach is used in all industries: it is referred to as lean management or agile management which aims to improve a company's performance by involving all employees.
The approach, therefore, requires a corporate culture adapted to this philosophy, and sometimes even guidance to change.
Be careful not to confuse the Kaizen approach with the Kaizen workshop, or kaizen blitz, or kaikaku (reform), which is used for major changes in a production system, a reengineering .
The Kaizen approach is increasingly used for personal development . Moreover, it is a vital tool for people who fear failure, abrupt changes, and frustration. They can use this approach to help learn a foreign language without putting pressure on themselves, quit smoking little by little and even overcome their shyness.

The Kaizen approach consists of 5 founding elements :
- personal discipline ,
- improved morale ,
- quality circles ,
- suggestions for improvement .
Chi va piano va sano ! (Slowly but surely!) One step at a time!
Toyota has been using the Kaizen approach since it was created, it is the best ambassador of the approach and the use it to improve processes , tools, and skills to :
- productivity ,
- safety (reduce risks),
- deadlines ,
- working conditions ,
- value collective intelligence and decompartmentalize skills ,
- reduce waste ( to improve inventory management).
Why implement the Kaizen approach?
Are you afraid to step out of your comfort zone? Then, the Kaizen approach is an ideal solution for you! It can be used to :
- set up new habits with minimal effort,
- simplify workflows and task management by breaking down an objective into sub-objectives that are easier to achieve,
- setbacks are accepted better because there are fewer consequences and they are less time-consuming,
- progress is clearer, with a path filled with as many successes as sub-objectives,
- improve estimates of costs and time frames,
- eliminate risk factors due to overly ambitious and outdated forecasts,
- value and motivate employees at their workstation.
- What is the Lean Startup Methodology? Basic principles
- Streamline Your Processes in 5 Steps with DMAIC
In short, the Kaizen approach improves the feasibility of a project and the morale of the teams!
We are more creative without stress. But adopting an improvement process that is too gradual can be a barrier to breakthrough innovation . Indeed, this requires making "leaps" forward from time to time and reactivity that is incompatible with the time constraints of continuous improvement.
As a result, Toyota has set aside the Kaizen approach for the manufacturing of its autonomous vehicles. Gill Pratt, CEO of the Toyota Research Institute, explained :
At Toyota, Kaizen or Continuous Improvement, is at the heart of everything we do. It remains the foundation and one of our biggest strengths. However, in these unprecedented times, we need additional approaches. In this particular domain, it’s simply not enough to only take small steps. You have to take leaps, which often results in failure. If you are lucky, after you have the courage to keep on failing again and again, you suddenly succeed.
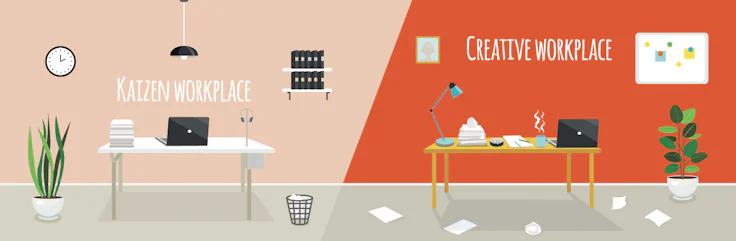
However, an innovative company can still use the Kaizen approach to review internal administrative procedures, routine projects. They can even integrate it into the management of an innovative project by combining several methods, depending on the tasks, flexibility and reactivity they require.
How to use the Kaizen approach
Here is a video that explains how the Kaizen approach works:
- identify an opportunity , an objective for improvement,
- explore new ideas by consulting with your employees,
- break the objective down into sub-objectives or deliverables,
- plan the tasks for each sub-objective, without overlapping human and material resources or timeframes,
- test , monitor progress and adapt the schedule ,
- move on to the next objective .
Many different approaches are used to break down projects, plan tasks, find the causes of problems, manage resources and monitor progress.
Among them (non-exhaustive list) :
- the Deming wheel (or PDCA cycle, Plan - Do - Check - Act/Adjust, to test new processes in 4 steps),
- TQM (total quality management) tools,
- the 5 W’s method (Who? What? Where? When? How? Why?),
- the 5 M’s (Ishikawa diagram) and the 5 P’s (for a search for the causes of problems),
- the 5 S's (to improve a workspace; in Japanese: Seiri, Seiton, Seiso, Seiketsu, Shitsuke or Clear the space of the superfluous, Tidy, Clean, Standardize, Progress),
- the Six Sigma (a management method aimed at improving the quality and efficiency of processes filed by Motorola),
- the WBS method (Work Breakdown Structure),
- the critical chain (CCPM or Critical Chain Project Management),
- the Adaptive Project Framework (APF),
- the Kanban board (visual method based on the just-in-time method, to provide key information in a just-in-time manner).
With a new generation of software in SaaS (Software as a Service) mode, there are many tools that you can use to improve your processes and continuous improvement.
Thanks to the real-time collection of production data, or taking into account feedback from project managers, these IT solutions are constantly improving and adapting to the needs of their users.
In addition, unlike on-premise software installed in workstations and requires purchasing updates, cloud solutions are constantly evolving with technological improvements.
Many solutions are adapted to task management ( Asana , Trello , and monday.com ) and offer functionalities that are in line with the Kaizen philosophy:
- priority management,
- incident management,
- dashboards,
- monitoring the profitability of projects…
There is also software dedicated to internal communication ( Slack and Yammer ) and idea management ( Brightidea ).
- 6 tips to improve your internal communication
What do you think, are you Kaizen-minded?
The well-being of a business depends on the well-being of its employees and on making their work easier.
There are many existing methods; choose the ones that fit your corporate culture and that have been proven to work in your teams. And why not combine them to meet special, continuous or short-term needs?
For several years now, appvizer has been improving the daily life of teams and managers by using the right tools.
Check out our articles and reviews and let us know what you think. This is the way to continuous improvement!
Articles on the same topic
- Enhance Productivity with the Continual Improvement Process
- Lean Management: the Philosophy that Helps you Optimize your Processes
Work Smarter : the Appvizer newsletter
New trends and tips to be more efficient at work, in your mailbox.
Best tools for you
Software vendors
Work smarter by appvizer.

How it works
For Business
Join Mind Tools
Article • 9 min read
Gaining the Benefits of Continuous Improvement
By the Mind Tools Content Team
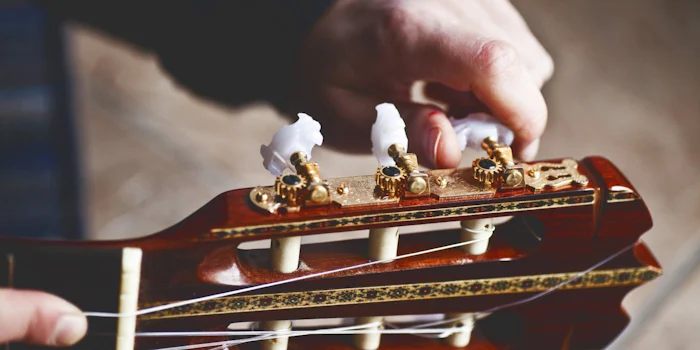
How does change happen in your organization? Is it through major initiatives, or is it part of the ongoing way you work?
Some types of change inevitably need a major project, meaning months of hard work, big budgets, and upheaval.
But an alternative or complementary approach to improving systems and processes involves more subtle, ongoing changes. This approach is often undervalued.
One way to do this kind of continuous, incremental improvement is kaizen . It originated in Japan, and the word translates as "change ( kai ) for the good ( zen )."
Kaizen is based on the philosophical belief that everything can be improved. With this approach, incremental changes add up to substantial changes over the longer term, without the need for radical innovation. It can be a much gentler and more employee-friendly way to institute the changes that must occur as a business grows and adapts to its changing environment.
Understanding the Approach
Because kaizen is more a philosophy than a specific tool, its approach is found in many different process-improvement methods, ranging from Total Quality Management (TQM) to the use of employee suggestion boxes. With kaizen, all employees are responsible for identifying gaps and inefficiencies. And everyone, at every level in the organization, suggests where improvements can take place.
Kaizen aims for improvements in productivity, effectiveness and safety. But people who follow this approach often unlock a number of other benefits, too, including:
- Less waste – inventory is used more efficiently, as are employee skills.
- People are more satisfied – they have a direct impact on the way that things are done.
- Improved commitment – team members have more of a stake in their job, and are more inclined to contribute fully in their role.
- Improved retention – satisfied and engaged people are more likely to stay.
- Improved competitiveness – increases in efficiency tend to contribute to lower costs and higher-quality products.
- Improved consumer satisfaction – a result of creating higher-quality products with fewer faults.
- Improved problem solving – looking at processes from a solutions perspective allows employees to solve problems continuously.
- Improved teams – working together to solve problems helps to build and strengthen teams.
Another Japanese term associated with kaizen is muda , which means waste. Kaizen is about decreasing waste by eliminating overproduction, improving quality, being more efficient, having less idle time, and reducing unnecessary activities. All these translate to cost savings, and can turn potential losses into profits.
The kaizen philosophy was developed to improve manufacturing processes, and it's one of the elements that led to the success of Japanese manufacturing through high quality and low costs. However, you can gain the benefits of the kaizen approach in many other working environments, both on a personal level and for your whole team or organization.
Much of the focus in kaizen is on reducing "waste," and this waste takes several forms:
- Movement – moving materials around before further value can be added to them.
- Time – spent waiting (no value is being added during this time).
- Defects – which require extra work to rectify, or mean that products have to be thrown away.
- Overprocessing – doing more to the product than is necessary to give the customer maximum value for money.
- Variations – producing bespoke solutions when a standard one will work just as well.
The table below shows some examples of these forms of waste in an office environment.
Using Kaizen
Here's our suggested approach for using "kaizen thinking," either on your own or with your team:
- Keep an "ideas log" of things that seem inefficient or that you'd like to improve. It's often easier to spot these in the heat of the moment than in cold reflection.
- Once a month, spend some time identifying areas where there's "waste" in the way that you or your team members operate. Use your ideas log as input, but also think about the wider picture and your overall ways of working. Go through each of the types of waste listed above as a checklist. How could each form of waste be eliminated?
- Plan out when you're going to make these changes. You need to strike a balance between getting on with making the improvements immediately (so that the area of waste doesn't become a bigger problem), and avoiding "change overload."
- It's important to take into account any difficulties or confusion that your change could cause for others – which could, in turn, make them resistant to that change. A great way to assess the impact of any potential changes is to use the Impact Analysis Tool .
- Whenever upcoming changes affect others, be sure to consult them about the new arrangements, and listen to their comments and concerns.
Kaizen is something that you can benefit from quickly as an individual. But embracing the approach with your team will take a concerted effort.
Here are some suggestions to help make kaizen work with your team:
- Learn – with your team – about the philosophy of kaizen.
- Allow everyone to submit their suggestions for improvements.
- Establish your overall kaizen approach and controls, creating a system to follow that everyone understands.
- Reward ideas, as the more ideas you generate, the more kaizen is at work in the day-to-day life of your team.
Mind Tools has resources about a range of other continuous-improvement tools, including Lean Manufacturing , The 5S System , and Value Stream Mapping .
Kaizen is a philosophy that supports continuous, incremental process changes that sustain a high level of efficiency.
It can help you to improve the way you work personally, by eliminating various types of "waste."
Kaizen can also be an organization-wide approach that harnesses suggestions and support from people at every level.
Wide participation can improve morale and satisfaction, as well as production, costs, and other hard measures.
Used well, a kaizen approach reveals what a big impact small changes can make!
You've accessed 1 of your 2 free resources.
Get unlimited access
Discover more content
The link and story methods.
Remembering a Simple List
How to Remember a Name
Use These Two Simple Memory Techniques
Add comment
Comments (0)
Be the first to comment!
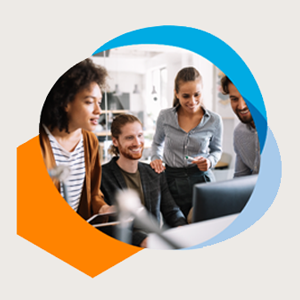
Team Management
Learn the key aspects of managing a team, from building and developing your team, to working with different types of teams, and troubleshooting common problems.
Sign-up to our newsletter
Subscribing to the Mind Tools newsletter will keep you up-to-date with our latest updates and newest resources.
Subscribe now
Business Skills
Personal Development
Leadership and Management
Member Extras
Most Popular
Newest Releases
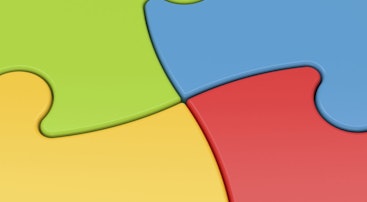
SWOT Analysis
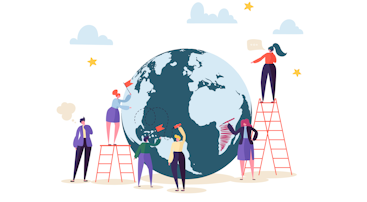
How to Build a Strong Culture in a Distributed Team
Mind Tools Store
About Mind Tools Content
Discover something new today
Top tips for delegating.
Delegate work to your team members effectively with these top tips
Ten Dos and Don'ts of Change Conversations
Tips for tackling discussions about change
How Emotionally Intelligent Are You?
Boosting Your People Skills
Self-Assessment
What's Your Leadership Style?
Learn About the Strengths and Weaknesses of the Way You Like to Lead
Recommended for you
8 ways to beat loneliness in the workplace.
Preventing People From Feeling Isolated
Business Operations and Process Management
Strategy Tools
Customer Service
Business Ethics and Values
Handling Information and Data
Project Management
Knowledge Management
Self-Development and Goal Setting
Time Management
Presentation Skills
Learning Skills
Career Skills
Communication Skills
Negotiation, Persuasion and Influence
Working With Others
Difficult Conversations
Creativity Tools
Self-Management
Work-Life Balance
Stress Management and Wellbeing
Coaching and Mentoring
Change Management
Managing Conflict
Delegation and Empowerment
Performance Management
Leadership Skills
Developing Your Team
Talent Management
Problem Solving
Decision Making
Member Podcast
Pursue the Next You in 2024 with a 20% Tuition Reduction on May Courses!
Critical Factors That Determine the Success of Kaizen Events
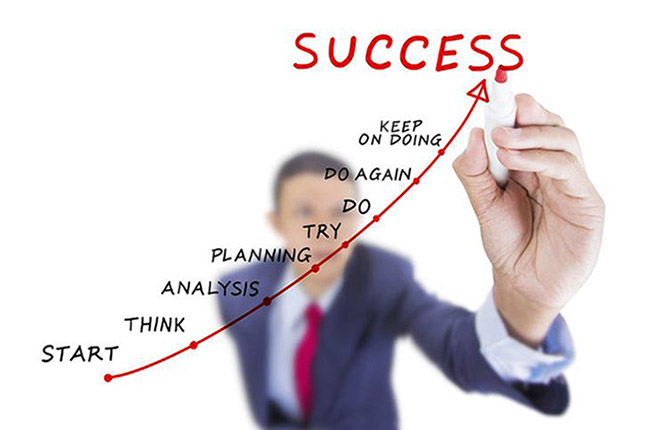
Last Updated March 8, 2024
A Kaizen Event is a way to focus on improvement to an existing process. It typically involves gathering together the frontline employees, managers and stakeholders involved with a specific operation, mapping the existing process, soliciting ideas for changes that will address problems and then implementing those that make improvements.
Kaizen is also notable for what it is not .
Villanova University’s Lean Six Sigma course teaches that Kaizen Events are not designed to lead to a cycle of big projects and events. Rather, the goal of Kaizen is to tap into the benefits of a culture of continuous improvement and make incremental improvements that can lead to significant benefits cumulatively.
These improvements must be within the scope of the people who participate in the process, not something that is asked of someone outside the process.
What Does Kaizen Mean?
Kaizen comes from two words. The first is “kai,” which means change. The second is “zen,” which means good or for the better. At its core, Kaizen Events are designed to lead to “good changes” that solve challenges and provide a better product or service to customers.
In the business world, Kaizen has come to represent the idea of continuous process improvement. It’s an approach that started at Toyota and has been emulated by businesses across multiple industries.
What is a Kaizen Event?
As taught in the Lean Six Sigma course , a Kaizen Event brings together all the people involved in making a process work correctly. This includes operators of a process, their direct managers, executives and other stakeholders.
At these events, the focus is completely on the process under discussion and nothing else. Although there is not a set time for a Kaizen Event, they are typically three to five-day events.
During Kaizen events, people spend the bulk of the time brainstorming ideas on how to solve specific challenges, cut waste, maximize value, streamline flow and reduce errors. In addition to these benefits, a Kaizen Event also leads to employees feeling a sense of empowerment. Their input is critical to making a Kaizen Event successful.
Breaking Down a Kaizen Event by Days
A Kaizen Event is part of the Lean methodology of process improvement that focuses on eliminating waste. It also has some similarities to the DMAIC methodology (define, measure, analyze, improve and control) used in Six Sigma. A successful Kaizen Event must have a clear and concise objective, along with immediately available resources and rapid results.
According to Villanova’s Lean Six Sigma Black Belt course , a five-day Kaizen Event should follow these steps.
Day 1: Begin training on fundamental Lean principles. The team should perform a waste walk (identifying areas of waste in a process) and gather data.
Day 2: Brainstorm ideas to improve the process. This can involve plan development, action item assignments, filling out time observation forms, constructing spaghetti charts and measuring travel distances.
Day 3: Time for action. The team might continue brainstorming activities, but by the end of the day, an improvement plan should be implemented.
Day 4: Bugs are worked out and the process is refined. At the end of this day or the beginning of the next, a discussion should take place on how to sustain the improved process.
Day 5: The last day involves a presentation to management, and a celebration of the work that has been completed.
Kaizen Event Best Practices
The above outlines how a Kaizen Event can break down over a five-day period. But what about the steps involved in an event, no matter how many days it lasts? The following outlines some of the major steps involved in planning for and implementing a successful Kaizen Event.
Planning the Kaizen Event
Preparation before the Kaizen Event is key. The first order of business is to establish the purpose of the event, the process that will be targeted, the list of who needs to attend and the desired outcome of the event.
Kaizen Events are sometimes led by a Lean Sensei. According to Six Sigma Master Black Belt and Villanova faculty member Tina Agustiady , “a Lean Sensei is a teacher who has mastered the skill and possesses leadership attributes. A Sensei is not only a good leader, but a good listener who facilitates Kaizen Events.”
The Lean Sensei or event leader should also craft a problem statement. This statement can be developed by answering these questions, according to the Association for Supply Chain Management :
- What is or isn’t occurring?
- Where in the process does it occur?
- Who does the problem impact?
- When did it occur, and has it occurred before?
- What is the magnitude of the issue in terms of frequency, cost, time and customer satisfaction?
Another key issue before the meeting is getting input (through a customer survey or other means) of the opinions of the end user. This is vital. Everything in Lean ultimately focuses on the impact on customers. What benefits customers is kept and improved. What doesn’t should be eliminated.
During the Kaizen Event
Here’s a list of the different steps that should be taken during the Kaizen Event itself.
- Train participants on the Lean and Six Sigma principles and tools that will be used
- Present input from customers, which should provide a clear picture of where the process is succeeding and failing
- Present data on the current operation
- Map out of the current operation using a flow chart
- Analyze the current process to find steps that don’t add value (waste)
- Brainstorm ideas to improve these areas
- Establish a process to implement changes
- Define ways to measure the success or failure of the changes
- Present a report on the findings to leadership
Many of these steps may involve the group reaching a consensus. The idea is to completely focus and move quickly on the issue. Many Lean tools may also be used, depending on the situation. Some choices include determining Takt Time (customer demand rate), using the Five Whys and creating a spaghetti map for the process.
15 Rules for Kaizen Events
The Lean Six Sigma Black Belt course also offers key points to keep in mind as you participate in and/or facilitate a Kaizen Event. They include:
- Keep an open mind to change
- Maintain a positive attitude
- Create a blameless environment
- Encourage nonjudgmental thinking
- Be aware of multiple alternatives
- Treat others as you want to be treated
- Respect and involve all team members
- One person, one vote
- Ignore position/rank
- Create a team environment
- There’s no such thing as a dumb question
- Create a bias for action – just do it
- Creativity before capital
- Never leave in silent disagreement
Remember to refer back to these rules as you’re facilitating a Kaizen Event.
“In my experience with having run dozens of short, focused Kaizen Events, I have found that most of these events returned improvements in excess of 50%. Additionally, they resulted in a rewarding experience for employees while increasing their sense of process commitment and ownership.” – Marv Meissner , MBA, Professor of Practice at Villanova .
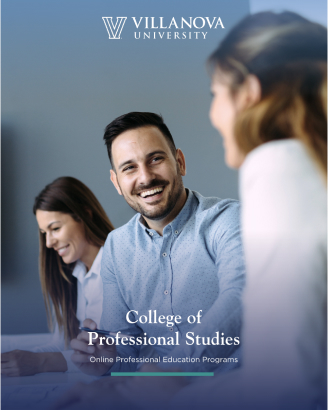
Related Articles
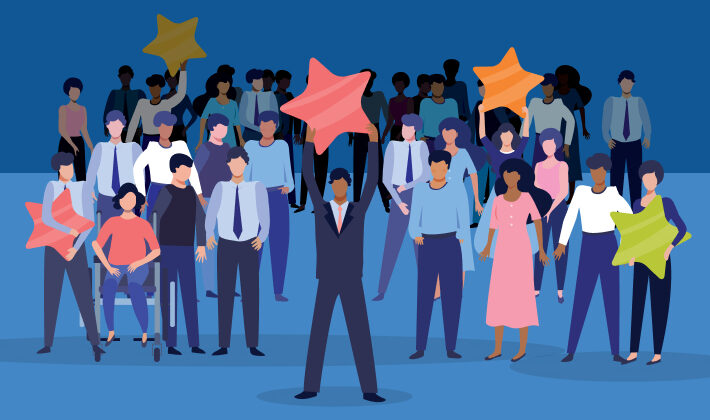
Take the next step in your career with a program guide!
By completing this form and clicking the button below, I consent to receiving calls, text messages and/or emails from BISK, its client institutions, and their representatives regarding educational services and programs. I understand calls and texts may be directed to the number I provide using automatic dialing technology. I understand that this consent is not required to purchase goods or services. If you would like more information relating to how we may use your data, please review our privacy policy .
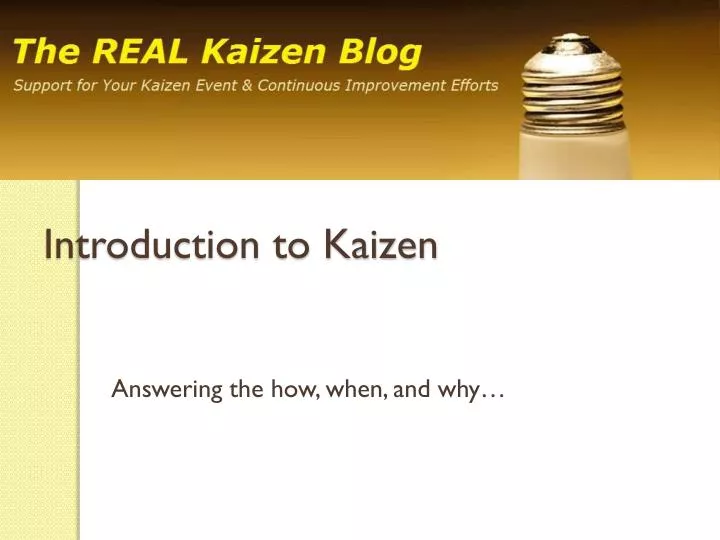
Introduction to Kaizen
Oct 21, 2014
2.91k likes | 5.33k Views
Introduction to Kaizen. Answering the how, when, and why…. What is Kaizen?. Kai = Change; Zen = Good Kaizen = Good Change, Change for the Better, Continuous Improvement Small, incremental changes; break apart and put back together better Focus on small, quick changes for long-term success
Share Presentation
- eliminate waste
- customer requirements
- reduce cycle time
- waste 8 underutilized people

Presentation Transcript
Introduction to Kaizen Answering the how, when, and why…
What is Kaizen? • Kai = Change; Zen = Good • Kaizen = Good Change, Change for the Better, Continuous Improvement • Small, incremental changes; break apart and put back together better • Focus on small, quick changes for long-term success • Elimination of the 8 Wastes The REAL Kaizen Blog @ http://REALKaizen.com
What is Kaizen? • Kaizen is: • Rapid improvement in a particular work cell, work station, small process, factory location, office area, etc. • Kaizen is not: • Improvements in complex cross-functional or systemic problems where Projects or 6-Sigma are required The REAL Kaizen Blog @ http://REALKaizen.com
Kaizen Targets • Eliminate waste (non value added activities) • Increase productivity / output • Reduce inventory (less material and labor) • Reduce cycle time (less time to produce specific part) • Reduce space (work cell, office area) • Improve On-Time Delivery (OTD) • Improve quality of product and process • Improve housekeeping, 5S and visual management • Reduce downtime (setup time, maintenance) • Reduce transport time and distance • Standardize the process (less variation) • Reduce operating costs The REAL Kaizen Blog @ http://REALKaizen.com
Ground Rules & Guidelines • Try to make all improvements within the event area. Avoid blame on suppliers (internal or external) • Don’t accept excuses. Just say no to “we’ve always done it that way” and the status quo. Keep an open mind to change • Think of how it can be done, not why it won’t work. Don’t make excuses-just make improvement happen • Ask “why” five times until you get to the root cause of the problem (The 5 Why’s) • The Team solution is usually the best solution • Don’t over-analyze. Understand the process, then “just do it,” and see if it works • Don’t seek perfection the first time. Do something now – a 30% improvement is better than nothing The REAL Kaizen Blog @ http://REALKaizen.com
Ground Rules & Guidelines • “Fast and crude” is better than “slow and elegant” or “maybe never”. • In the worst case, the original process can be restored • Never leave in silent disagreement; Silence is agreement = ‘I can live with it’ • Every person has a voice and there is no such thing as a dumb question • Keep a positive attitude and have fun. The possibilities for improvements are unlimited • Everyone respect everyone else The REAL Kaizen Blog @ http://REALKaizen.com
What is Lean? • Lean production focuses on eliminating waste in all processes • Lean production is not about eliminating people • Lean production is about expanding capacity by reducing costs and shortening cycle times between order and ship date • Lean is about understanding what is important to the customer The REAL Kaizen Blog @ http://REALKaizen.com
Value Add & Non-Value Add • Value Adding Activity • An activity that transforms or shapes product or information to meet customer requirements. • Value added is always determined from the customer’s perspective. • How would you define value for your customers? • Non-Value Adding Activity • Those activities that take time, resources or space, but do not add to the value of the product itself. The REAL Kaizen Blog @ http://REALKaizen.com
Value Add & Non-Value Add • Value Add – Activities that are performed that the customer is willing to pay for • Value Enabling – Activities that support Value Add • Waste – Activities that do not contribute to Value Add The REAL Kaizen Blog @ http://REALKaizen.com
Value Adding Activity • Steps that could be considered essential because they: • Physically change the product / service • Are done in the right sequence or location in the process • Provide a real and sustainable competitive advantage • Would be seen by the client as delivering the value they seek that they would be willing to pay for them The REAL Kaizen Blog @ http://REALKaizen.com
Value Enabling Activity • Steps that could be considered necessary because they: • Support company measurement or reporting requirements? • Reduce risk, defect, cost, etc. • Allow subsequent work for the customer to be performed more quickly or accurately • Satisfy legal or regulatory requirements • Satisfy good business practice requirements The REAL Kaizen Blog @ http://REALKaizen.com
Waste • Steps that could be considered non-essential because they: • Do not change/add to the product or service to be delivered • Are done out of sequence and/or are performed to correct prior actions • Would not be seen by the client as delivering value and so they would be unwilling to pay for them The REAL Kaizen Blog @ http://REALKaizen.com
8 Wastes The REAL Kaizen Blog @ http://REALKaizen.com
Waste 1 - Overproduction • Definition • To produce items sooner or in greater quantities than required for customer demand • Causes • Poor planning • Incorrect bottleneck assumptions • Problems • Overproduction discourages a smooth flow of production • Leads to excessive work in process inventory The REAL Kaizen Blog @ http://REALKaizen.com
Waste 2 - Inventory • Definition • Any raw material, Work in Progress (WIP) or finished goods which are being stored • Causes • Overproduction causes inventorybuild up between processes • Problems • Adds cost • Requires space • Hides process defects • Can become a defect The REAL Kaizen Blog @ http://REALKaizen.com
Waste 3 - Motion • Definition • Unnecessary movementwithin a Process • Causes • Poor workplace layout • Poor process planning • Poor Housekeeping • No Standard OperatingProcedures • Problems • Adds time & cost • Can be a safety issue The REAL Kaizen Blog @ http://REALKaizen.com
Waste 4 - Waiting • Definition • People or Parts that are waiting for a work cycle to be completed • Causes • Unreliable Supply Chain • Bottlenecks • Down Time • Problems • Excessive Lead Time • Causes Bottle Necks • Additional Time & Cost The REAL Kaizen Blog @ http://REALKaizen.com
Waste 5 - Transportation • Definition • Unnecessary movement ofitems between processes • Causes • Poor layout and/or process Design & Planning • Unstructured or not understood Value Stream • Complex Material flow • Problems • Increased Time & Cost to transport & search • Increased Defects due to accidents The REAL Kaizen Blog @ http://REALKaizen.com
Waste 6 – Over processing • Definition • Processing beyond the valuerequired by the Customer • Causes • Lack of Customer Focus • “Always done it this way” • Lack of understanding • Scheduled work time is longer than needed • Problems • Increases Time & Cost The REAL Kaizen Blog @ http://REALKaizen.com
Waste 7 - Rework • Definition • A defect is when the Customerbelieves they did not get whatthey paid for • Causes • Process Variation • Customer requirements not understood • Problems • Additional Time & Cost • Reduces Customer Confidence The REAL Kaizen Blog @ http://REALKaizen.com
Waste 8 – Underutilized People • Definition • Underutilization of people’s Knowledge, Skills, and Abilities (KSA) • Causes • Constant management turnover unaware of talent pool • Employee not happy in current position • Problems • Great ideas might be missed • Dominant personalities may force focus in wrong direction The REAL Kaizen Blog @ http://REALKaizen.com
Potential Non-Value Add Opportunities The REAL Kaizen Blog @ http://REALKaizen.com
Kill The “Re’s” • Action verbs that start with “re” usually bad news: • Rework • Retool • Reject • Restock • Retest • Recall • Retrain, etc. The REAL Kaizen Blog @ http://REALKaizen.com
Steps to Eliminate Waste • Brainstorm! • Clearly identify business, processes or area to focus improvements on where bottlenecks, high costs, or long throughputs exist • Perform detailed “current state” process analysis through value stream mapping, time and motion studies, video, measurements, interviews with employees, collect process data, stand and observe the process, etc. • Identify “value-added”, “non value-added but necessary” and “waste”. • Define “ideal / future state” map for the targeted process (What should it be without any or with minimum waste?). • Justify improvement benefits in safety, quality, customer and financial impact The REAL Kaizen Blog @ http://REALKaizen.com
Steps to Eliminate Waste • Involve employees and perform Kaizen events (apply problem solving & 4-Quadrant analysis, define and prioritize solutions). • Set action plans to get from current state to future state (assign ownership for improvements, set timelines and follow-up method). • Execute improvements and follow-up on agreed actions. • Train employees, document and standardize the process based on improvements made. • Reflect and learn from the process (what we did right and what we did wrong, how to improve in future). The REAL Kaizen Blog @ http://REALKaizen.com
The Visual Factory Describes how information and data flows. Uses visual methods to display and convey how material flows, where it is located, and how the work is accomplished. Visual Factory tools include Andon boards, signs, and charts. The REAL Kaizen Blog @ http://REALKaizen.com
5S • Workplace organization standard focused on efficiency, effectiveness, and safety • Sort (Seiri) • Straighten, Set in order (Seiton) • Shine, Sweep (Seiso) • Standardize (Seiketsu) • Sustain (Shitsuke) The REAL Kaizen Blog @ http://REALKaizen.com
5S - Before • Workplace Targets Office (Before) Factory (Before) The REAL Kaizen Blog @ http://REALKaizen.com
5S - After Office (After) Factory (After) The REAL Kaizen Blog @ http://REALKaizen.com
Importance of the Visual Image The REAL Kaizen Blog @ http://REALKaizen.com
Importance of the Visual Image • All factories should be as clean as “Clean Rooms” The REAL Kaizen Blog @ http://REALKaizen.com
Rules to Good Housekeeping • Remove / eliminate everything you don’t need from the floor, drawers, shelves, etc. • Gain space and eliminate waste (simplify) • Everything left will have a clearly defined place (lined-up & identified) • Everything left will be clean and neat (regularly cleaned, re-painted, etc.) • Ownership in the area • Keep the area neat and don’t let others mess it up The REAL Kaizen Blog @ http://REALKaizen.com
Waste ID – Gemba/MUDA Walk • Spend 1 to 2 hours in the area identifying waste • Write down every waste you see for 30 minutes (use form) • Prioritize and identify top 3 (15 minutes) • Propose solutions (15 minutes) • Discuss with Team all opportunities while in the area following the process (1 hour) The REAL Kaizen Blog @ http://REALKaizen.com
Going Lean Thru Kaizen Turn This… …Into This! The REAL Kaizen Blog @ http://REALKaizen.com
- More by User

Kaizen. Lean Manufacturing Series. Disclaimer and Approved Use. Disclaimer This presentation is intended for use in training individuals within an organization. The handouts, tools, and presentations may be customized for each application.
562 views • 6 slides
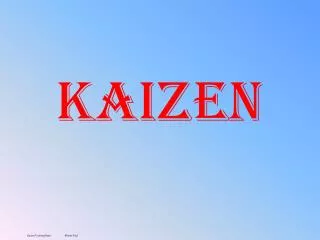
KAIZEN. WHAT IS KAIZEN. CONTINUOUS IMPROVEMENT NEW TECHNOLOGY ADAPTATION. KAIZEN. These improvement were made by involving all employees hence their Morale, Productivity and Quality went up, resulting in cost reduction Whenever any new technologies were introduce, the changeover was
2.84k views • 53 slides
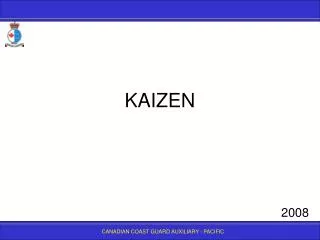
KAIZEN. 2008. CANADIAN COAST GUARD AUXILIARY - PACIFIC. The Principle of Kaizen. The Principle of Kaizen. Kaizen is a Japanese philosophy that extols an ideal of continuous improvement. The Principle of Kaizen.
674 views • 18 slides
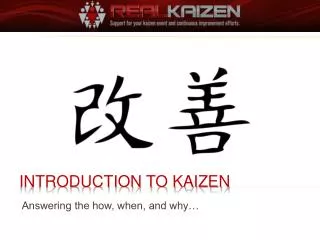
Answering the how, when, and why…. Introduction to Kaizen. What is Kaizen?. Kai = Change; Zen = Good Kaizen = Good Change, Change for the Better, Continuous Improvement Small, incremental changes; break apart and put back together better Focus on small, quick changes for long-term success
768 views • 34 slides
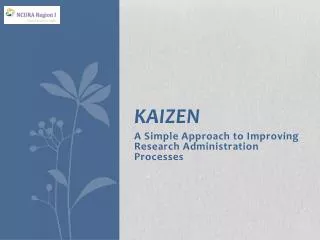
Kaizen. A Simple Approach to Improving Research Administration Processes Spring 2013. Good Change. Kai = change Zen = good A journey of a thousand miles begins with a single step. Kaizen.
1.59k views • 31 slides
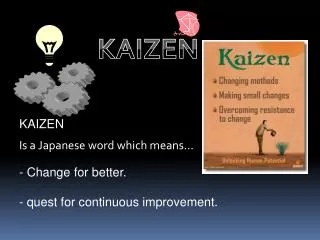
KAIZEN. KAIZEN . Is a Japanese word which means…. Change for better. quest for continuous improvement. TOOLS / METHOD TO MAKE KAIZEN WORK:. 1. Human Resources(HR) emphasis 2. Three(3) balloons to success 3. Three(3) M for doing a job. 4. Five(5) S strategy
4.06k views • 51 slides
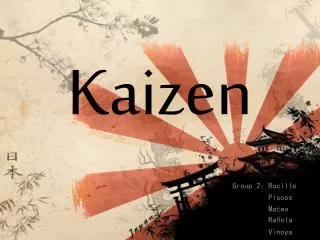
Kaizen. Group 2: Rocillo Piscos Mateo Ra ñola Vinoya. What is Kaizen?. Kaizen. JAPANESE. refers to philosophy or practices that focus upon continuous improvement of processes in manufacturing, engineering, game development, and business management .
2.76k views • 9 slides
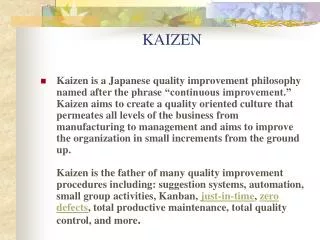
527 views • 12 slides
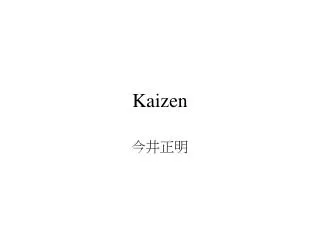
Kaizen. 今井正明. Kaizen Ongoing improvement involves everyone Top management Managers Workers A culture of supporting quality improvement more important than the use of any specific tools. Kaizen The unifying thread running through The philosophy The systems
760 views • 35 slides
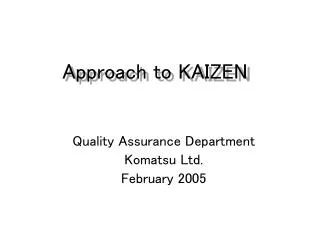
Approach to KAIZEN
Approach to KAIZEN. Quality Assurance Department Komatsu Ltd. February 2005. Kaizen( Improvement ). Stabilized era of economical field allowed just to follow the Job Description. Job shall be variable depending on environmental surroundings. Today. Future.
753 views • 23 slides
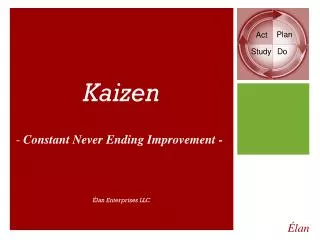
Kaizen. Plan. Act. Study. Do. Constant Never Ending Improvement -. Élan Enterprises LLC. What is Kaizen?. Kaizen (Ky’zen) “Kai” means “change” “zen” means “good (for the better)” Pronounced 'Gai San' in Chinese - Gai - The action to correct
904 views • 17 slides
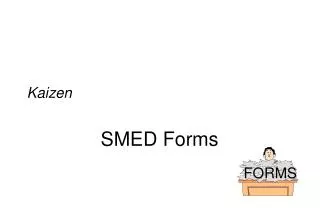
FORMS. Kaizen. SMED Forms. WASTE ANALYSIS. Team:. Event:. Date:. Location:. OPPORTUNITY SELECTOR. IMPLEMENTATION REF. No Opportunity Ref No Opportunity Ref. Team:. Event:. Date:.
348 views • 11 slides
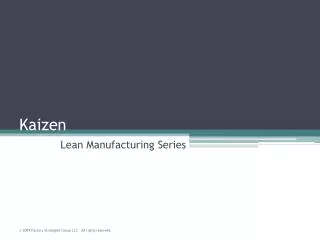
Kaizen. Lean Manufacturing Series. Outline. What is Kaizen? History How to Kaizen The Kaizen Blitz Roadblocks. What is Kaizen?. Kaizen (Ky’zen) “Kai” means “change” “zen” means “good (for the better)” Gradual, orderly, and continuous improvement Ongoing improvement involving everyone.
690 views • 5 slides
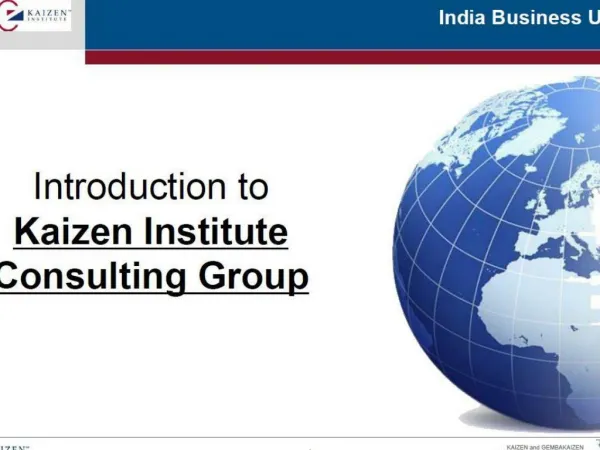
Introduction to Kaizen Institute Consulting Group
Kaizen Institute provides consulting services to companies around the world in the areas of Consulting, Training, Benchmarking as well as Qualification. To read more kindly browse through: http://in.kaizen.com/
443 views • 23 slides
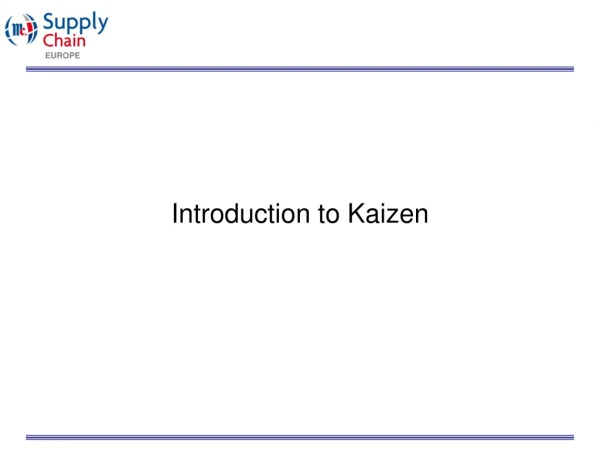
Introduction to Kaizen. Agenda. Kaizen! Learn the basics of Kaizen Understand Kaizen terminology Recognise when to Kaizen Understand how to Kaizen Kaizen tools & examples. What is Kaizen?.
320 views • 17 slides
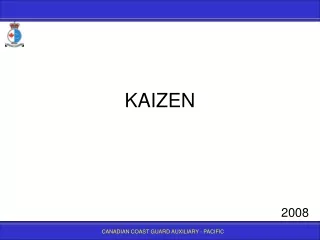
260 views • 18 slides
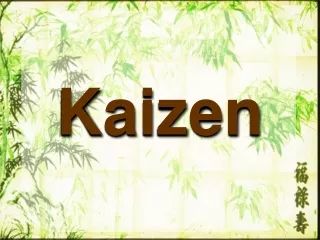
Kaizen. The Definition of Success:. Health Relationship Work: Excellence and Enthusiasm Sustained over Time. Exercise 1. What are your strategies for creating change? Please discuss a change, sale or improvement you made. What was your strategy?. The First Definition of Kaizen.
1.71k views • 85 slides

IMAGES
VIDEO
COMMENTS
Implementing Kaizen: Step by Step Guide. The system for implementing Kaizen is called the PDCA Cycle, an iterative model of change comprising four stages - Plan, Do, Check, and Act. It is a continuous activity that has to be repeated again and again. This model is also known as the Deming cycle, Shewhart cycle, and plan-do-study-act (PDSA ...
A kaizen blitz, or kaizen event, is a short-term improvement project designed to accomplish significant results in process management and quality issues. Kaizen events focus on improving a specific area of the company, meaning they are ideal to deploy in a business process or department of 50 or fewer employees.
Free Google Slides theme and PowerPoint template. The Kaizen method is a philosophy of continuous improvement that has gained popularity in the business world. The concept is simple yet powerful: small, incremental changes lead to significant progress over time. Slidesgo wasn't built in one day—it's been a journey of small steps until we got ...
This process is designed to empower people and engage team members in the work process. According to the information on Toyal's website, the company uses the Kaizen principle to underpin the aim of forever thinking about the next, learning from the past, and improving the Toyota production system. 2. Nestle.
About this Guided Project. During this project, we will be working together to create a Kaizen Event for a warehouse worker and walk through the steps together to improve their daily workflow. By the end of this project, you will learn how to Create a Google Slides presentation and define Kaizen, create a process map, create a 5W and 2H root ...
KAIZEN "Without continual growth and progress, such words as improvement, achievement, and success have no meaning." - Benjamin Franklin . During the 1980s, facing stiff and unrelenting competition from Japanese manufacturers, American manufacturers tried to leverage lean methodologies and tools to transform their productivity and quality. . Unfortunately, many of their efforts failed
This book explains the principles of kaizen and how companies use it as an approach to business management. It looks at every aspect of kaizen, from its implementation in organizations to its application in daily life. 2. Lean Thinking: Banish Waste And Create Wealth In Your Corporation.
Kaizen doesn't tell organizations how to improve; instead, it presents a mindset that when adopted, will influence decisions and impact the culture. Its principals are: Every process can be improved. Continuous improvement essential to competitiveness. Defects and errors are almost always the faults of flawed processes, not people.
Eight Steps for Kaizen. Background — lists the relevant information the audience and participants would need to know.; Current-state definition — depicts the situation in a graphical, visual manner for the audience to see, e.g., value-stream maps.; Current-state analysis — various factors, e.g., lead time, service, performance, cost, features, etc., are collectively examined for ...
Kaizen Event: Kaizen events are focused continuous improvement projects where cross-functional teams come together to develop improvements. Kaizen events introduce the concepts of continuous improvement to a group and help to drive a widespread cultural change towards this way of thinking. Gemba Walk: Gemba walks use the "go-and-see" approach.
Traditionally, kaizen is a big part of lean project management in the manufacturing industry, but businesses in many other sectors are catching on to its effectiveness and implementing kaizen events. Kaizen events. A kaizen event is a three- to five-day team workshop in which employees, managers, and sometimes C-suite executives make an ...
Download pre-designed Kaizen PPT templates and slide designs for presentations. Kaizen is a system of continuous improvement in quality, technology, processes, company culture, productivity, safety and leadership. Download awesome Kaizen slide designs and PPT templates that you can use in presentations on total quality management and continuous improvement slide designs.
Empower People: This one is directed towards teams and having them organized in such a way that it supports the kaizen principles. Therefore, leadership must set goals for their teams that are not contradictory. They should offer a system and tools to help the teams achieve these goals. Be Transparent: Data is the strongest determining factor.
Since introducing this term as a systematic approach to business improvement, companies that implement KAIZEN™ have continually yielded superior results. Definition of KAIZEN™. "KAIZEN™ means improvement. Moreover, it means continuing improvement in personal life, home life, social life, and working life.
A true Japanese development philosophy, kaizen is composed of two words, kai 改, and zen 善 which means "change" and "better". Also known as the small-step work improvement approach, or the method of continuous improvement, the Kaizen approach was developed in the United States under the Training With Industry (TWI) program, set up by consultants (including W. Edwards Deming) under the ...
This approach is often undervalued. One way to do this kind of continuous, incremental improvement is kaizen. It originated in Japan, and the word translates as "change ( kai) for the good ( zen )." Kaizen is based on the philosophical belief that everything can be improved. With this approach, incremental changes add up to substantial changes ...
An Image/Link below is provided (as is) to download presentation Download Policy: ... Kaizen Summary Sheet - Example 1 Project type: 5S Area: Sales & Marketing Office Team Leader: John Smith Before After Reasons project chosen: • Difficult to move around a cluttered office • Difficult to find information and supplies Tools used on project ...
1. VIDYALANKAR SCHOOL OF INFORMATION TECHNOLOGY TOPIC - KAIZEN PRESENTATION DONE BY GROUP-5 DATE OF PRESENTATION- 20TH JANUARY 2009. 2. MEMBERS OF GROUP-5 VINAY BIDARIMATH- 07B405 MEHUL JAGAWATH- 07B417 SNEHAL MOHITE- 07B429 MANALI RANE- 07B439 URVI SHETHIA- 07B445 RAVINDRA THAKUR- 07452 KIRAN DERE- 07B462. 3.
A successful Kaizen Event must have a clear and concise objective, along with immediately available resources and rapid results. According to Villanova's Lean Six Sigma Black Belt course, a five-day Kaizen Event should follow these steps. Day 1: Begin training on fundamental Lean principles. The team should perform a waste walk (identifying ...
Presentation Transcript. Introduction to Kaizen Answering the how, when, and why…. What is Kaizen? • Kai = Change; Zen = Good • Kaizen = Good Change, Change for the Better, Continuous Improvement • Small, incremental changes; break apart and put back together better • Focus on small, quick changes for long-term success • Elimination ...