Power and Energy Optimization in EV with Sensorless Externally Excited Synchronous Motor
- Research Paper
- Published: 19 March 2024

Cite this article
- T. Paulraj 1 &
- Yeddula Pedda Obulesu 1
37 Accesses
Explore all metrics
This paper presents a comprehensive analysis of an Externally Excited Synchronous Motor (EESM) integrated with sensorless Field-Oriented Control (FOC) using the stator and rotor mutual inductance method focusing on its impact on electric vehicle (EV) performance, energy efficiency, and optimization considerations. The investigation on the performance analysis of the EV shows that there is an improvement in the performance of the EV in terms of the efficiency of the three-phase Voltage Source Inverter (VSI) as 95.23, 95.07, and 94.51% across IHDC, WLTP, and NEDC drive cycles respectively. The efficiency of the traction motor, EESM, is 89.61, 89.92, and 88.46% for the same cycles, highlighting the efficacy of sensorless FOC in optimizing power and energy consumption. The research analysis reveals that the energy consumption rates of 280, 190, and 140 W/km for IHDC, WLTP, and NEDC cycles, with corresponding running costs of 1.19, 0.81, and 0.59 INR/km respectively. The analysis also uncovers driving ranges, with IHDC offering a maximum of 197 km, while WLTP and NEDC provide 290 and 400 km respectively. Additionally, the research study evaluates greenhouse gas emissions, with EESM-based EVs demonstrating substantial emission reductions. Specifically, IHDC records emissions of 198.8 g/km, WLTP at 134.9 g/km, and NEDC at 99.4 g/km, compared to 158.7 g/km for petrol cars and 145.25 g/km for diesel cars respectively. This research highlights the potential of EESM-based EVs with sensorless FOC control to enhance efficiency, reduced energy consumption and reduce emissions, making them a promising choice for sustainable transportation. The proposed research work carried out using Matlab/Simulink and results are presented to validate the proposed work.
This is a preview of subscription content, log in via an institution to check access.
Access this article
Price includes VAT (Russian Federation)
Instant access to the full article PDF.
Rent this article via DeepDyve
Institutional subscriptions
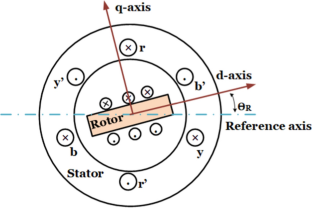
Similar content being viewed by others
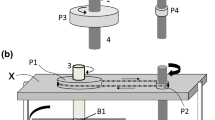
Advantages of Double-Rotor Electric Motors: A New Motor Equation
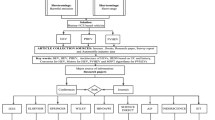
A comprehensive review on hybrid electric vehicles: architectures and components
Krishna Veer Singh, Hari Om Bansal & Dheerendra Singh
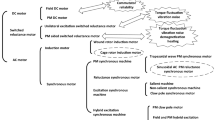
Review and Development of Electric Motor Systems and Electric Powertrains for New Energy Vehicles
William Cai, Xiaogang Wu, … Yujin Wang
Abbreviations
Electrically or externally excited synchronous motor
Greenhouse gas
Field-oriented control
Electric vehicle
Voltage source inverter
Indian highway drive cycle
Worldwide harmonized light vehicles test procedure
New european driving cycle
Permanent magnet synchronous motor
High-frequency signal injection
Electromagnetic interference
Extended kalman filter
Real-world driving cycle
Internal combustion engine vehicle
Machine learning
Space vector pulse width modulation
Indian rupees
Approved_report_emission__2021_22.pdf (2022) https://cea.nic.in/wp-content/uploads/baseline/2023/01/Approved_report_emission__2021_22.pdf .
Ayub M et al (2020) Wye-delta winding configuration for brushless operation of a wound field synchronous machine. Int J Appl Electromagn Mech 64(1–4):1165–1172. https://doi.org/10.3233/JAE-209433
Article Google Scholar
Choi G, Bramerdorfer G (2022) Comprehensive design and analysis of an interior permanent magnet synchronous machine for light-duty passenger EVs. IEEE Access 10:819–831
Chung HB, Kennel R (2020) ‘PWM-based sensorless control of electrically excited synchronous machine using mutual inductance’, In: 2020 International Symposium on Power Electronics, Electrical Drives, Automation and Motion, SPEEDAM 2020, pp 232–236. https://doi.org/10.1109/SPEEDAM48782.2020.9161944 .
Dursun M (2023) Enhancement fractional-order sliding mode controller design for induction motor vector control. Iran J Sci Technol Trans Electr Eng 47(3):1059–1080. https://doi.org/10.1007/s40998-023-00637-2
Ghule AN, Killeen P, Ludois DC (2021) Sensorless control of separately excited synchronous electrostatic machines. IEEE Trans Ind Appl 57(4):3744–3753. https://doi.org/10.1109/TIA.2021.3076419
Home charging calculator (2024)
Hussain A et al (2022) Wound rotor synchronous motor as promising solution for traction applications. Electronics (switzerland) 11(24):1–16. https://doi.org/10.3390/electronics11244116
Article CAS Google Scholar
Huynh TA, Chen PH, Hsieh MF (2022) Analysis and comparison of operational characteristics of electric vehicle traction units combining two different types of motors. IEEE Trans Veh Technol 71(6):5727–5742. https://doi.org/10.1109/TVT.2022.3179868
Huynh TA, Hsieh MF (2018) Performance analysis of permanent magnet motors for electric vehicles (EV) traction considering driving cycles. Energies. https://doi.org/10.3390/en11061385
IOCL fuel price (2024).
Kim D-M et al (2020) Design of traction motor for mitigating energy consumption of light electric vehicle considering material properties and drive cycles. Int J Automot Technol 21(6):1391–1399. https://doi.org/10.1007/s12239-020-0131-7
Koteich M, Messali A, Daurelle S (2017) ‘Self-sensing control of the externally-excited synchronous machine for electric vehicle traction application’, In: Conference Proceedings - 2017 8th International Symposium on Sensorless Control for Electrical Drives, SLED 2017, pp 91–96. https://doi.org/10.1109/SLED.2017.8078436
Krause PC, Wasynczuk O, Sudhoff SD (2002) Analysis of electric machinery and drive systems. IEEE Press, NewYork
Book Google Scholar
Liu C et al (2021) A critical review of advanced electric machines and control strategies for electric vehicles. Proc IEEE 109(6):1004–1028. https://doi.org/10.1109/JPROC.2020.3041417
Mahindra Xuv specifications no date. https://auto.mahindra.com/suv/xuv300 Accessed: 18 January 2024
Moujahed M et al (2018) Sensorless speed control and high-performance fault diagnosis in vsi-fed pmsm motor drive under open-phase fault: analysis and experiments. Iran J Sci Technol Trans Electr Eng 42(4):419–428. https://doi.org/10.1007/s40998-018-0088-y
Pravallika G, Sujatha P, Bharath Kumar P (2023) ‘Different traction motor topologies with lithium-air battery for electric vehicles: a review’, In: Materials Today: Proceedings, (xxxx), pp 3–6. https://doi.org/10.1016/j.matpr.2023.03.400
Renault (2017) ‘Renault Zoe’, Ideal.Es/Granada, February, pp 5–7
Ruuskanen V et al (2015) Drive cycle analysis of a permanent-magnet traction motor based on magnetostatic finite-element analysis. IEEE Trans Veh Technol 64(3):1249–1254. https://doi.org/10.1109/TVT.2014.2329014
Singirikonda S, Yeddula Pedda O (2023) Investigation on performance evaluation of electric vehicle batteries under different drive cycles. J Energy Storage 63:106966. https://doi.org/10.1016/j.est.2023.106966
Yang Y et al (2017) Design and comparison of interior permanent magnet motor topologies for traction applications. IEEE Trans Transp Electr 3(1):86–97. https://doi.org/10.1109/TTE.2016.2614972
Yang Z et al (2015) Comparative study of interior permanent magnet, induction, and switched reluctance motor drives for EV and HEV applications. IEEE Trans Transp Electr 1(3):245–254. https://doi.org/10.1109/TTE.2015.2470092
Zhang J et al (2020) Design and analysis of a low-speed and high-torque dual-stator permanent magnet motor with inner enhanced torque. IEEE Access 8:182984–182995. https://doi.org/10.1109/ACCESS.2020.3028425
Zhang X (2013) Sensorless Induction motor drive using indirect vector controller and sliding-mode observer for electric vehicles. IEEE Trans Veh Technol 62(7):3010–3018. https://doi.org/10.1109/TVT.2013.2251921
Zhu X, Cheng M (2010) Design, analysis and control of hybrid excited doubly salient stator-permanent-magnet motor. Sci China Technol Sci 53(1):188–199. https://doi.org/10.1007/s11431-009-0357-0
Article ADS Google Scholar
Download references
The research presented in this paper was conducted without any external funding.
Author information
Authors and affiliations.
School of Electrical Engineering, Vellore Institute of Technology, Vellore, 632014, India
T. Paulraj & Yeddula Pedda Obulesu
You can also search for this author in PubMed Google Scholar
Corresponding author
Correspondence to Yeddula Pedda Obulesu .
Ethics declarations
Conflict of interest.
We have no conflicts of interest to disclose. All authors declare that they have no conflicts of interest.
From the above Eqs. ( 15 – 25 ), a program was developed using python to calculate the energy consumption, cost/km and range of the EV as given below.
Python Program to Analyse Energy Consumption.
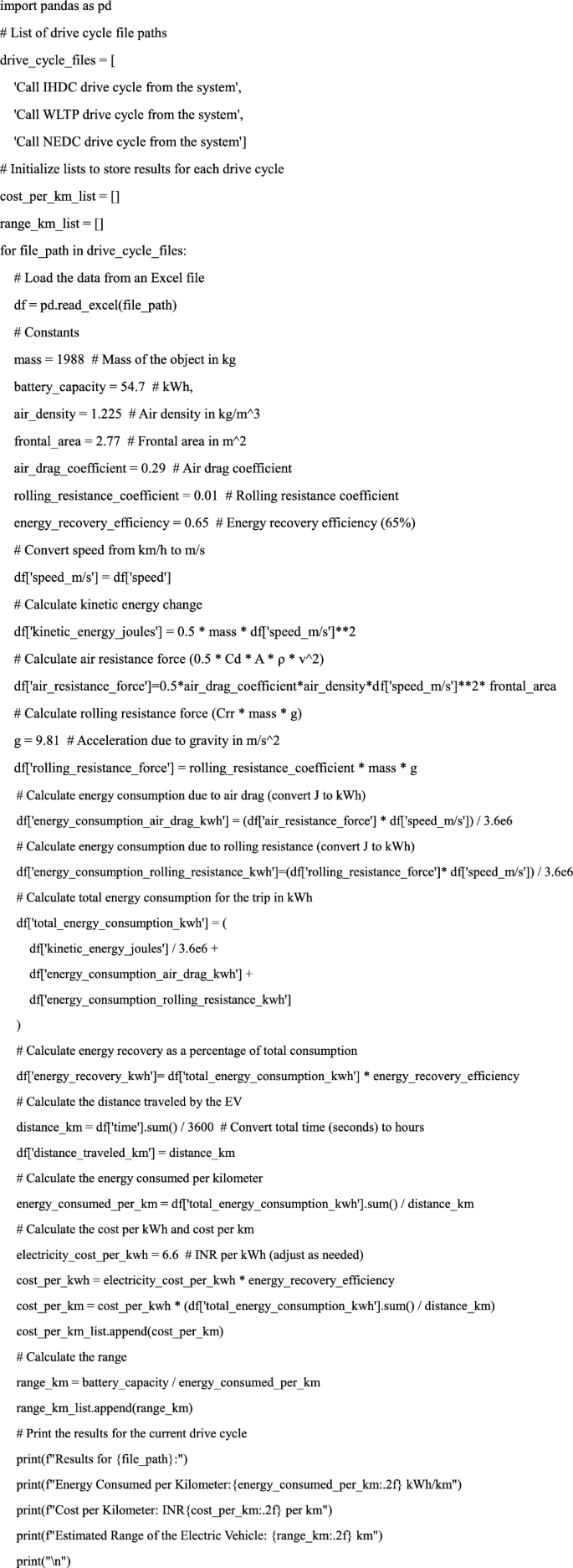
Rights and permissions
Springer Nature or its licensor (e.g. a society or other partner) holds exclusive rights to this article under a publishing agreement with the author(s) or other rightsholder(s); author self-archiving of the accepted manuscript version of this article is solely governed by the terms of such publishing agreement and applicable law.
Reprints and permissions
About this article
Paulraj, T., Obulesu, Y.P. Power and Energy Optimization in EV with Sensorless Externally Excited Synchronous Motor. Iran J Sci Technol Trans Electr Eng (2024). https://doi.org/10.1007/s40998-024-00714-0
Download citation
Received : 08 November 2023
Accepted : 25 February 2024
Published : 19 March 2024
DOI : https://doi.org/10.1007/s40998-024-00714-0

Share this article
Anyone you share the following link with will be able to read this content:
Sorry, a shareable link is not currently available for this article.
Provided by the Springer Nature SharedIt content-sharing initiative
- Performance analysis
- Energy consumption
- GHG emissions
- Externally excited synchronous motor
- Sensorless control
- Stator and rotor mutual inductance method
- Find a journal
- Publish with us
- Track your research
electric motors Recently Published Documents
Total documents.
- Latest Documents
- Most Cited Documents
- Contributed Authors
- Related Sources
- Related Keywords
Techno Economic Assessment of IE3 Electric Motors in the Medium Size Brazilian Industry
Characteristics of hydraulic and electric servo motors.
Until the 1970s, hydraulic actuators were widely used in many mechanical systems; however, recently, electric motors have become mainstream by virtue of their improved performance, and hydraulic motors have largely been replaced by electric motors in many applications. Although this trend is expected to continue into the future, it is important to comprehensively evaluate which motor is most suitable when designing mechanical systems. This paper presents the results of a survey of the performance of electric and hydraulic servo motors and aims to provide quantitative data that can be used as a reference for selecting appropriate motors. We surveyed AC, AC direct, brushless DC, and brushed DC electric motors and swash plate-type axial piston, bent axis-type axial piston, crank-type radial piston, and multistroke-type radial piston hydraulic motors. Performance data were collected from catalogs and nonpublic data. We compared and evaluated the characteristics of these diverse servo motors using indexes such as torque, rotating speed, output power, power density, and power rate.
Assessment criteria of the feasibility of replacement standard efficiency electric motors with high-efficiency motors
Multiphysics simulation of electric motors with an application to stators, simulation modeling of a ship propulsion system in wavesfor control purposes.
The article deals with a simulation approach to the representation of the ship motions in waves, interacting with the propulsion system behavior (diesel engine and propeller). The final goal is the development of a simulator, as complete as possible, that allows the analysis of the main engine thermodynamics in different sea conditions, also in the unfavorable event of dynamic instability of the hull, and the correct management of the other propulsion components. This latter aspect is particularly interesting in some of the last new energy solutions for decarbonization of ships, concerning, for example, auxiliary electric motors, powered by batteries, to support the traditional diesel-mechanical propulsion (especially in heavy weather conditions). From this point of view, a proper analysis of the engine dynamic performance, affected by particular sea states, is fundamental for a smart management and control of shaft generators/auxiliary electric motors, batteries, etc. To this end, the work presents and highlights the main features of a ship simulator, suitable for the study of the new propulsion solutions that are emerging in maritime transport. Some representative results will point out the complex non-linear behavior of the propulsion plant in waves. Moreover, a parametric roll scenario will be investigated, in order to highlight the capability of the conceived simulator in modeling the effects of the dynamic instability of the hull on the propulsion plant.
Comparison of Loss Characteristics of 2-Level 3-Phase Inverter based on SiC Power Semiconductor to Increase Driving Efficiency of Electric Motors in Railway Vehicles
Analysis of depolymerization of insulating compositions of electric motor windings based on ultrasonic radiation.
This work is a continuation of the fundamental study on implementing an innovative method of repairing electric motors using ultrasound. A study of the method of dismantling windings based on ultrasound has been carried out for the purpose of energy efficiency, environmental friendliness and less time spent on the repair cycle of electric motors in terms of removing the stator winding. The investigated dismantling method is optimal for a number of technical issues in comparison with the existing methods for dismantling electric motor windings. In the work, the main focus is on the material of the winding insulation. Lacquer and compound types of insulation of industrial electric motors, which are the main ones everywhere, have been analyzed. The analysis of the impregnating electrical insulating compositions of the stator windings of electric motors and the influence of ultrasound on them during dismantling of the windings of electric motors at different levels of influence of forcing factors: duration and power of ultrasonic action, concentration and temperature of the working solution. The applied mathematical software systems for calculation and modeling guarantee the reliability and rationality of the results of the experiments obtained during the work. A system of equations has been modeled and models of the effect of useful factors relative to each other have been constructed, the results obtained have been optimized and the optimal parameters of both varnish and compound insulation systems have been identified. The optimal parameters of the investigated types of insulation show encouraging results on many important points: duration, energy consumption, environmental friendliness.
Low-Cost Drive System for Electric Motors based on the IRAM Module
With the increasing use of equipment that demand electric drive systems, the need for new systems that meet requirements of compactness, versatility, safety and low cost has increased. The IRAM module is an electronic circuit that provides a driver for DC and AC motors, being extremely compact and presents high performance. In this context, this work contributes to the power electronics area, presenting a design and construction of a low cost drive system, based on IRAM module, developed for individual or simultaneous drive, up to two DC motors. To carry out the experiments, DC motors responsible for moving a welding robot, were used. Experimental results are presented to shown the feasibility of using this system.
Aircraft Electric Machines
Current trend in aviation is to increase efficiency of all the aircraft’s systems. This leads to a reduction of fuel consumption which has also positive effect on emissions. One possibility how to reach this aim is to replace hydraulic and pneumatic system with an electrical power system. Because many on-board electrical loads are in the form of electrical drives, the special attention is given to electric motors and their electronic speed controllers / power converters. Furthermore, electric motors suitable for traction/propulsion are presented. Moreover, the various types of starter/generators suitable for on-board utilisation are compared in the paper.
Export Citation Format
Share document.
Performance Analysis of Electric Motors Using Vibration Measurement
Ieee account.
- Change Username/Password
- Update Address
Purchase Details
- Payment Options
- Order History
- View Purchased Documents
Profile Information
- Communications Preferences
- Profession and Education
- Technical Interests
- US & Canada: +1 800 678 4333
- Worldwide: +1 732 981 0060
- Contact & Support
- About IEEE Xplore
- Accessibility
- Terms of Use
- Nondiscrimination Policy
- Privacy & Opting Out of Cookies
A not-for-profit organization, IEEE is the world's largest technical professional organization dedicated to advancing technology for the benefit of humanity. © Copyright 2024 IEEE - All rights reserved. Use of this web site signifies your agreement to the terms and conditions.

- Vehicle Technologies Office
- About the Vehicle Technologies Office
- Technology Areas
- Technology Integration
- Reports and Publications
The Vehicle Technologies Office (VTO) is supporting research and development (R&D) to improve motors in hybrid and plug-in electric vehicles, with a particular focus on reducing the use of rare earth materials currently used for permanent magnet-based motors.
In an electric drive system, an electric motor converts the stored electrical energy in a battery to mechanical energy. Electric motors consist of a rotor (the moving part of the motor) and a stator (the stationary part of the motor). A permanent magnet motor includes a rotor containing a series of magnets and a current-carrying stator (typically taking the form of an iron ring), separated by an air gap. There are three types of electric motors that can be used in hybrid or plug-in electric vehicle traction drive systems.
- Internal permanent magnet (IPM) motors have high power density and maintain high efficiency over a high percentage of their operating range. Almost all hybrid and plug-in electric vehicles use rare earth permanent magnets in their traction motors. Because of the high costs of magnets and rotor fabrication, these motors are relatively expensive. Other challenges to using IPM motors include the limited availability and high cost of rare earth magnetic materials. Despite the challenges, the automotive industry anticipates continuing to use IPM motors in the majority of electric drive vehicles over the next decade.
- Induction motors have high starting torque and offer high reliability. However, their power density and overall efficiency are lower than that of IPM motors. They are widely available and common in various industries today, including some production vehicles. Because this motor technology is mature, it is unlikely research could achieve additional improvements in efficiency, cost, weight, and volume for competitive future electric vehicles.
- Switched reluctance motors offer a lower cost option that can be easy to manufacture. They also have a rugged structure that can tolerate high temperatures and speeds. However, they produce more noise and vibration than comparable motor designs, which is a major challenge for use in vehicles. Also, switched reluctance motors are less efficient than other motor types, and require additional sensors and complex motor controllers that increase the overall cost of the electric drive system.
VTO Electric Motor R&D
VTO's primary goal is to decrease electric motors' cost, volume, and weight while maintaining or increasing performance, efficiency, and reliability. To meet 2022 cost targets, research must reduce the cost of the motor by 50%.
To achieve these goals, VTO and its partners are examining many research avenues:
- The Beyond Rare Earth Magnets (BREM) R&D project led by Ames Laboratory is investigating lower-cost permanent magnets and magnetic materials. This effort is closely coordinated with the Critical Materials Institute also led by Ames Laboratory .
- Oak Ridge National Laboratory and industry projects are pursuing reduced rare-earth magnet motors, non-permanent magnet motor designs, and innovative motor materials and designs.
- The National Renewable Energy Laboratory is focusing research on improving electric motor thermal management, performance and reliability.

COMMENTS
This paper presents a review on the recent research and technical progress of electric motor systems and electric powertrains for new energy vehicles. Through the analysis and comparison of direct current motor, induction motor, and synchronous motor, it is found that permanent magnet synchronous motor has better overall performance; by comparison with converters with Si-based IGBTs, it is ...
4.5.3 Spoke motor. Recent trends in electric motor design have shown a drift towards the spoke brushless DC motor. These motors are known for their high power density. The design of a spoke motor is of an interior permanent magnet motor. The superiority of this motor is due to the higher saliency ratio, which concentrates the magnetic flux ...
Through the proper motor type selection and design, the performance of EVs can be enhanced, such as efficiency and stability. This paper presents a state-of-the-art overview of alternative electric motors for EV applications. Firstly, the classification and performance of alternative electric motors is described. Then, research gaps and ...
This paper presents a review on the recent research and technical progress of electric motor systems and electric powertrains for new energy vehicles.
An Electric Vehicle is a vehicle controlled by an electric motor and is run utilizing the power put away in the batteries. ... 2018. Hence, various types of electric motors are currently utilized depending upon the power requirement. In this paper, authors provide a comparison of the most popular classes of electric motors being used over the ...
In this paper, a review of. different electric motors with respect to their design simplicity, cost, ruggedness and efficiency is presented. Finally, the brushless. DC motor is proven to be an ...
Abstract: This paper presents a comprehensive state-of-the-art review of the modeling and analysis methods for the multidisciplinary design of electric motors for various applications including vehicular power and propulsion systems and electrified powertrains. It covers the important aspects of different engineering domains, such as dynamic modeling, loss calculations, demagnetization ...
Electric motors play a crucial role in modern industrial and domestic applications. With the trend of more and more electric drives, such as electric vehicles (EVs), the requirements for electric motors become higher and higher, e.g., high power density with good thermal dissipation and high reliability in harsh environments. Many efforts have been made to develop high performance electric ...
Feature papers represent the most advanced research with significant potential for high impact in the field. A Feature Paper should be a substantial original Article that involves several techniques or approaches, provides an outlook for future research directions and describes possible research applications.
This paper presents a comprehensive analysis of an Externally Excited Synchronous Motor (EESM) integrated with sensorless Field-Oriented Control (FOC) using the stator and rotor mutual inductance method focusing on its impact on electric vehicle (EV) performance, energy efficiency, and optimization considerations. The investigation on the performance analysis of the EV shows that there is an ...
Figure 1. Typical AC induction motor.Figure 1. In this paper, different possibilities are explored that could be applied to reduce the weight of the electric motor (the study is specifically performed for a fluid-cooled motor) by analysis of various research papers and an in-depth study of all concepts. Through this
In this paper, different electric motors are studied and compared to see the benefits of each motor and the one that is more suitable to be used in the electric vehicle (EV) applications. There ...
Hence, few EVs currently use SRMs, for example, Land Rover unveiled a range of seven electric research vehicles powered by an SRM and drive system developed at the 2013 Geneva Motor Show. The EVs are based on Land Rover's 110 Defender model in which the standard diesel engine and gearbox have been replaced by a 70 kW switched reluctance motor.
Electric motor is certainly the core and most important components of an electric car, and the thermal management for electric motors has drawn increasing attention from both industry and academic society. ... To enlighten the future research, in this paper, both the theoretical modeling and experimental investigations of the latest thermal ...
Cluster #3 (electric motors and powertrains) and #6 (in-wheel motors and control strategies) both concern motor solutions. ... In this paper, we have studied the scholarly research trends by analysing patterns of document co-referencing of the period 1990-2021. Our results show several interesting trends, gaps, and need for future development ...
Explore the latest full-text research PDFs, articles, conference papers, preprints and more on ELECTRIC MOTORS. Find methods information, sources, references or conduct a literature review on ...
The switched reluctance motor (SRM) is an electric motor that can function effectively in challenging operating conditions thanks to its sturdy construction and resilience to external factors. Despite somewhat weaker parameters in terms of energy and power density compared to other types of electric motors, the SRM is recommended for applications such as the military, mining, industry, and ...
Permanent magnet synchronous motor (PMSM) is widely used in various areas. Its small volume, light weight, high efficiency, high power factor, fast response, wide speed range, and good accuracy make it replace DC motor to be broadly used in electric vehicles (EV) including pure electric vehicles (PEV) as well as hybrid electric vehicles (HEV).
4.3 | Permanent magnet synchronous (PMS) motors (or brushless AC) The brushless AC motor is another type of AC motor used in electric vehicle propulsion. There have been many car manu-facturers using this technology to power their vehicles. These motors are fed sinusoidal AC current which pro-duces a sinusoidal field.
Research of the Modes of Starting and Braking during Work of the Systems of Group Electric Drive of Mine Electric Locomotive with the Different Types of Electric Engines. Microsystems Electronics and Acoustics . 10.20535/2523-4455.mea.237329 . 2021 .
induction motors are the most acceptable motors for use in. electric propulsion. They have advantages such as reliability, low maintenance, low cost and robustness [ 14]. The typical ...
This research paper presents a performance analysis of electric motors using vibration measurement with an emphasis on the vibration measurement caused by bearing faults, loose ball bearing races, and rotor imbalance. Fault analysis occurring in the electric motor was made following the ISO 10816-3 Standard. The results obtained from the analysis will be used as references and guidelines for ...
VTO Electric Motor R&D. VTO's primary goal is to decrease electric motors' cost, volume, and weight while maintaining or increasing performance, efficiency, and reliability. To meet 2022 cost targets, research must reduce the cost of the motor by 50%. To achieve these goals, VTO and its partners are examining many research avenues:
This paper provides a review of electrical motor drive technologies used in EV applications, with a performance comparison of candidate machines and their drive topologies. EV applications demand ...