

7 QC Tools for Process Improvement | PDF | Case Study

From Where Did the 7 QC Tools Come?

Why we use The 7 QC Tools for Process Improvement?
What is the use of 7 qc tools.

The 7 QC Tools:
- Flow Charts
- Cause and Effect Diagram (Fishbone or Ishikawa)
- Pareto Chart
- Scatter Diagram
- Control Chart
👉 Download 7 QC Tools PDF file
[1] flow charts :.
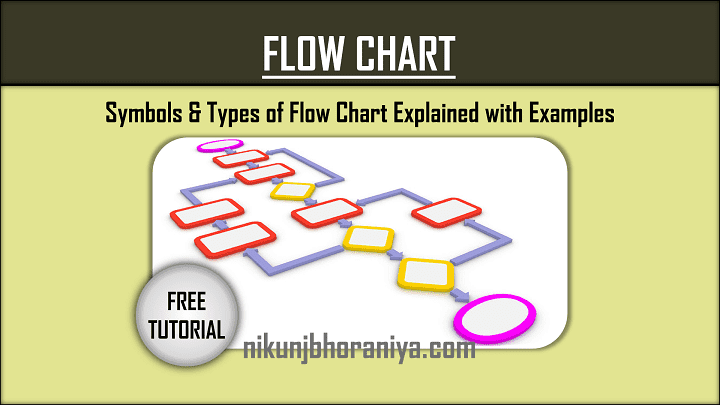
[2] Cause and Effect Diagram :
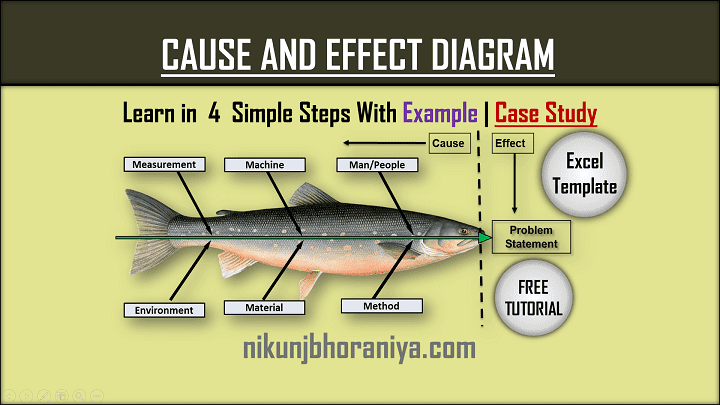
[3] Check Sheet :

[4] Histogram :
➨ types of histogram:.

[5] Pareto Chart :

[6] Scatter Diagram :
➨ different names of the scatter diagram:, ➨ different correlation between two variables in the scatter plot:.

[7] Control Chart :

Related Posts
22 comments.

very good presentation skill and to the point explaination

Thanks for your feedback and kind comment!!!
How to download???
You can check the individual articles!!!
Best in short... Great work Nikunj
Thank you very much for your kind comment!!!
Simply wonderful. Thanks very much!
this is a great initiative , well done
Thank you for your kind words!!!
Thanks and happy learning!!!
Nice teaching
Thank you and Happy Learning!!!
Great good initiative 👍 a How to Download
Thank you for your kind word!!
This is so helpful
Thanks for your feedback
HOW MAKE PARETO
Sir can you please share process audit checklist
You can reach us at: [email protected]
Post a Comment
Contact form.
To read this content please select one of the options below:
Please note you do not have access to teaching notes, the use and application of the 7 new quality control tools in the manufacturing sector: a global study.
The TQM Journal
ISSN : 1754-2731
Article publication date: 15 March 2023
Issue publication date: 5 December 2023
The main objective of this study is to investigate the 7 new quality control or the 7 new management tools and their use in manufacturing organisations. This research investigates the understanding, knowledge of the tools and the level of application of the tools within the manufacturing sector. In addition, this paper aims to identify the benefits, challenges and critical success factors (CSFs) for the application of the 7 new quality control (QC) tools.
Design/methodology/approach
An online survey instrument was developed, and data collection was performed utilising a stratified random sampling strategy. The primary strata/clusters were formed by quality professionals working in all aspects of manufacturing organisations and functions. A total of 86 participants from different countries responded to the survey.
The main finding of this study is that 10% of participants within the manufacturing sector perceived that the 7 new QC tools could solve above 80% of organisational problems. Another relevant finding presented in this paper is that tree diagrams were the most utilised of the 7 new QC tools within the manufacturing sector. The least utilised tools are arrow diagrams. The common benefits of using 7 new QC tools in the manufacturing sector are helping people define, measure and analyse the problem areas or even prioritises them and providing some form of structure to the problem-solving efforts. This paper also revealed that the 7 new QC tools were most used in the manufacturing area but least utilised in the new products and research and development (R&D) functions. This work also presents a list of CSFs and challenges required to properly apply the 7 new QC tools in the manufacturing sector.
Research limitations/implications
This study was just carried out in manufacturing organisations. It would be interesting to try and expand to services sectors and compare use within the services sector.
Originality/value
Authors understand that this is the very first empirical study analysing the use and understanding of the 7 new QC or management tools within the manufacturing sector. The results of this study represent an important first step towards a complete understanding of the applicability of these tools in continuous improvement programs on a global scale and the context in which they can be utilized.
- 7 new management tools
- Quality tools
- Problem-solving
- Global survey
- Manufacturing sector
- Critical success factors
- Critical failure factors
McDermott, O. , Antony, J. , Sony, M. , Fernandes, M.M. , Koul, R. and Doulatabadi, M. (2023), "The use and application of the 7 new quality control tools in the manufacturing sector: a global study", The TQM Journal , Vol. 35 No. 8, pp. 2621-2639. https://doi.org/10.1108/TQM-06-2022-0186
Emerald Publishing Limited
Copyright © 2023, Emerald Publishing Limited
Related articles
We’re listening — tell us what you think, something didn’t work….
Report bugs here
All feedback is valuable
Please share your general feedback
Join us on our journey
Platform update page.
Visit emeraldpublishing.com/platformupdate to discover the latest news and updates
Questions & More Information
Answers to the most commonly asked questions here

Streamlining Six Sigma Projects with The 7 QC Tools
Updated: September 26, 2023 by Ken Feldman

As in any tool chest, you can have dozens, if not hundreds, of different tools for all types of specialized tasks. Such is the case with Six Sigma. There are many tools available for your use depending on what you want to accomplish. However, like your home tool chest, there are a small set of basic tools that are your go-to tools you will use most often and on most projects.
Let’s review the 7 QC tools that are most commonly used in Six Sigma , the benefits of those tools, and some best practices for using them.
Overview: What are the 7 QC tools?
It is believed that the 7 QC tools were introduced by Kaoru Ishikawa in postwar Japan, inspired by the seven famous weapons of Benkei. Benkei was a Japanese warrior monk who armed himself with seven weapons and was on a personal quest to take 1,000 swords from samurai warriors who he believed were arrogant and unworthy.
Ishikawa was influenced by a series of lectures on statistical quality control given by Dr. W. Edwards Deming in 1950 to a group of Japanese scientists and engineers. Unfortunately, the complexity of the subject intimidated most workers, so Ishikawa focused primarily on a reduced set of tools that would suffice for most quality-related issues.
The 7 QC tools are:
- Check sheet
- Fishbone diagram (cause and effect diagram, or Ishikawa diagram)
- Pareto chart
- Control chart
- Scatter diagram
- Stratification
Let’s explore each in a little more detail.
Check sheet: A form to collect and tally data for further analysis.

Image source: techqualitypedia.com .
Fishbone diagram: Fishbone diagrams are used to drill down to find the root cause of a problem. As the name implies, the diagram looks like the bones of a fish, where each main bone represents a specific category of possible root cause, and the subsequent drilling down is shown as smaller and smaller bones.

Image source: asq.org .
Histogram: This is a bar graph showing the frequency of a set of data, usually continuous data. The histogram allows you to see the center of the data, the range of the data, and the distribution of the data. It is a very useful snapshot. The downside is that you can’t see the sequence or order of the data.

Image source: statisticsbyjim.com .
Pareto chart: This chart is based on the 80/20 principle that says 80% of your effect is caused by 20% of your causes. For example, 80% of your sales comes from 20% of your customers. Dr. Joseph Juran, who developed this chart, often referred to this principle as the vital few and trivial many . He later revised that to the vital few and useful many . The Pareto chart lists the causes in descending order of frequency or magnitude. It is used to prioritize what you should look at first to improve your process.

Image source: www.automateexcel.com .
Control chart: A control chart is a statistical tool that looks at your process data over time for the purpose of distinguishing between special cause and common cause variation.

Image source: www.spcforexcel.com .
Scatter diagram: These are also known as scatter plots. They’re used to show a graphical correlation between a set of paired data on an X and Y axis. It is the graphical representation of what you would use for regression analysis.

Image source: www.spcforexcel.com .
Stratification: This is a graph that shows data that has been stratified when the data comes from different sources. It is useful to view the data by certain strata such as shift, gender, geographic location, machines, or suppliers.
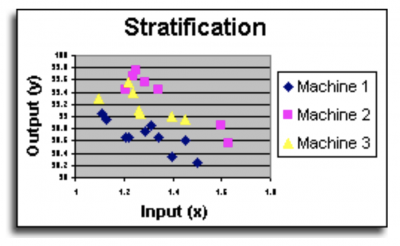
Image source: www.systems2win.com .
3 benefits of the 7 QC tools
These seven tools are easy to understand and apply and will help you understand what is going on in your process.
1. Easy
These 7 QC tools are easy to understand and implement yet powerful in identifying root causes, in discriminating between types of variation, and as a visual description of your data. A picture is truly worth 10,000 words (or statistical calculations).
2. Software-driven
Gone are the days when you had to draw all of your graphs by hand. There are many simple and cost-effective software packages that will take your data and quickly produce graphs.
3. 80/20
The Pareto principle applies to the 7 QC tools as well. 80% of your quality issues can be addressed by using 20% of the most common tools.
Why are the 7 QC tools important to understand?
The key thing to understand is when to use each tool — which one is appropriate for your specific situation?
Tools address different issues
The more familiar you are with these common tools, the quicker you’ll be able to select the right one to help you solve your problem or answer your question. The Fishbone diagram is used to search for root causes of your problem. A control chart is used to distinguish between common and special cause variation. A scatter diagram is used to look for correlation or relationship between an X and Y variable.
Graphs don’t tell the whole story
Graphs and diagrams are useful for providing an overview and directional indicator of your process, but statistical analysis will provide greater confidence than a graph alone.
Flexibility
These seven tools can be used for different types of data and across any type of function. Their flexibility makes them useful in myriad situations and industries, so becoming familiar with them can be a wise investment.
3 best practices when thinking about the 7 QC tools
Use these tools for as many applications as is feasible. Keep it simple, and only use the more sophisticated and complex tools if you need the additional information and analysis.
1. Have a clear idea of what question you’re trying to answer
Since each of the tools can be used to answer different data and process questions, be sure you’ve clearly defined the question you’re trying to answer.

2. Use them as your primary presentation
Use the 7 QC tools and their accompanying graphs and diagrams as your primary presentation format. Reserve the statistical analysis for questions that go beyond what’s answered in the graphs.
3. Make sure they’re self-explanatory
Be sure your graphs are succinct and self-explanatory so people can understand what you’re trying to tell them without the need for a long-winded explanation.
Frequently Asked Questions (FAQ) about the 7 QC tools
What is meant by stratification .
If you collected production data throughout the day across all three shifts and five machines, you might want to stratify or separate your data and look at it by shift and by machine. This would allow you to understand whether there were any differences between the strata. This might indicate the source of a root cause or an opportunity to improve the other shifts if one is found to be doing better than the others.
What are the 7 basic QC tools?
Scatter diagrams, Pareto charts, control charts, histograms, stratification, fishbone diagrams and check sheets.
Do I have to draw the graphs and diagrams for the 7 QC tools by hand?
With the use of current software and computer technology, you will rarely be required to create the graphs by hand. Still, it might be interesting to do it by hand once to fully appreciate the tools and software available to us.
Let’s review what’s in your tool belt
The 7 QC tools are basic graphical representations of your data. They can be used to answer a wide variety of questions about your data and your process. Use them as your primary presentation format when talking about what your data is telling you. While they are not a complete list of tools, they should be robust enough to address many of your improvement issues.
The 7 QC tools, while basic, are foundational to the Six Sigma methodology and have stood the test of time. Their simplicity and versatility make them indispensable for professionals across industries. As businesses evolve and data becomes more integral to decision-making, the importance of these tools only grows. They bridge the gap between raw data and actionable insights, allowing teams to make informed decisions. Moreover, in today’s digital age, with the integration of AI and machine learning, these tools can be further enhanced to provide even deeper insights. However, the essence remains the same: understanding and improving processes through data visualization.
Key Points About The 7 QC Tools:
Origin and Influence: Introduced by Kaoru Ishikawa, inspired by Benkei’s seven weapons and influenced by Dr. W. Edwards Deming’s lectures on statistical quality control.
List of 7 QC Tools: Check sheet, Fishbone diagram, Histogram, Pareto chart, Control chart, Scatter diagram, and Stratification.
Benefits: These tools are easy to understand, software-driven, and adhere to the 80/20 principle, addressing 80% of quality issues with 20% of the most common tools.
Importance: They address different issues, provide an overview of processes, and offer flexibility across data types and functions.
Best Practices: Clearly define the question, use the tools as the primary presentation format, and ensure graphs are self-explanatory.
About the Author
Ken Feldman
The 7 Quality Control (QC) Tools Explained with an Example!
Please provide the following information to access the course, or click here to learn more about the Industry 4.0 Academy

Controlling the Defects of Paint Shop using Seven Quality Control Tools in an Automotive Factory
- I. A. Memon Department of Mechanical Engineering, Quaid-e-Awam University of Engineering, Science and Technology, Pakistan
- A. Ali Department of Electrical Engineering, Sukkur IBA University, Pakistan
- M. A. Memon Department of Electrical Engineering, Quaid-e-Awam University of Engineering, Science and Technology, Pakistan
- U. A. Rajput Department of Mechanical Engineering, Quaid-e-Awam University of Engineering, Science and Technology, Pakistan
- S. A. K. Abro Department of Electrical Engineering, Sukkur IBA University, Pakistan
- A. A. Memon Department of Electrical Engineering, Quaid-e-Awam University of Engineering, Science and Technology, Pakistan
Seven quality control (7QC) tools are used for reducing defects during manufacturing. These tools are highly effective in productivity and quality improvement. In this case, the study of the 7QC tools was applied in an automotive factory in order to reduce paint shop defects. Within four months the production line was inspected, defects were categorized and the 7QC tools were successfully applied, reducing the overall defect rate by 70%. Although every tool was important, the cause and effect diagram was responsible for finding the root causes of the defects.
J. C. Benneyan, “The design, selection, and performance of statistical control charts for healthcare process improvement”. International Journal of Six Sigma and Competitive Advantage, Vol. 4, No. 3, p. 209-239, 2008 DOI: https://doi.org/10.1504/IJSSCA.2008.021837
P. Kuendee, “Application of 7 quality control (7 QC) tools for quality management: A case study of a liquid chemical warehousing”, 4th International Conference on Industrial Engineering and Applications, Nagoya, Japan, April 21-23, 2017 DOI: https://doi.org/10.1109/IEA.2017.7939188
H. Hailu, H. Tabuchi, H. Ezawa, K. Jilcha, “Reduction of excessive trimming and reject leather by integration of 7 QC tools and QC story formula: The case report of Sheba Leather PLC”, Industrial Engineering & Management, Vol. 6, No. 3, 2017
B. Neyestani, “Seven basic tools of quality control: The appropriate techniques for solving quality problems in the organizations”, 2017 DOI: https://doi.org/10.2139/ssrn.2955721
N. Visveshwar, V. Vishal, V. Venkatesh, R. V. Samsingh, P. Karthik, “Application of quality tools in a plastic based production industry to achieve the continuous improvement cycle”, Calitatea, Vol. 18, No. 157, pp. 61-64, 2017
P. S. Parmar, T. N. Desai, “Reduction of rework cost in manufacturing industry using statistical process control techniques: a case study”, Industrial Engineering Journal, Vol. 10, No. 6, pp. 40-46, 2017 DOI: https://doi.org/10.26488/IEJ.10.6.46
A. Jaware, K. Bhandare, G. Sonawane, S. Bhagat, R. Ralebhat, “Reduction of machining rejection of shift fork by using seven quality tools”, International Journal of Engineering and Technology, Vol. 5, No. 4, pp. 4323-4334, 2018
S. M. Ahmed, R. T. Aoieong, S. L. Tang, D. X. Zheng, “A comparison of quality management systems in the construction industries of Hong Kong and the USA”, International Journal of Quality & Reliability Management, Vol. 22, No. 2, pp. 149–161, 2005 DOI: https://doi.org/10.1108/02656710510577215
D. R. Prajapati, “Implementation of SPC techniques in automotive industry : a case study”, International Journal of Emerging Technology and Advanced Engineering, Vol. 2, No. 3, pp. 227-241, 2012
T. V. U. K. Kumar, “SPC tools in automobile component to analyze inspection process”, Vol. 2, No. 1, pp. 624–630, 2013
C. Fotopoulos, E. Psomas, “The use of quality management tools and techniques in ISO 9001:2000 certified companies: The Greek case”, International Journal of Productivity and Performance Management, Vol. 58, No. 6, pp. 564–580, 2009 DOI: https://doi.org/10.1108/17410400910977091
R. H. Fouad, A. Mukattash, “Statistical process control tools : a practical guide for Jordanian Industrial Organizations”, Vol. 4, No. 6, pp. 693–700, 2010
R. Srinivasu, G. S. Reddy, S. R. Rikkula, “Utility of quality control tools and statistical process control to improve the productivity and quality in an industry”, International Journal of Reviews in Computing, Vol. 5, pp. 15-20, 2011
T. M. Young, B. H. Bond, J. Wiedenbeck, “Implementation of a real-time statistical process control system in hardwood sawmills”, Forest Products Journal, Vol. 57, No. 9, pp. 54–62, 2007
N. Afzaal, A. Aftab, S. Khan, M. Najamuddin, “To analyze the use of statistical tools for cost effectiveness and quality of products”, IOSR Journal of Humanities and Social Science, Vol. 20, No. 1, pp. 47–57, 2015
G. Paliska, D. Pavletic, M. Sokovic, “Quality tools: systematic use in process industry”, Journal of Achievements in Materials and Manufacturing Engineering, Vol. 25, No. 1, pp. 79–82, 2007
M. Sokovic, J. Jovanovic, J. Krivokapic, A. Vujovic, “Basic quality tools in continuous improvement process”, Journal of Mechanical Engineering, Vol. 55, No. 5 pp. 333-341, 2009
G. Patidar, D. D. S. Verma, “Implimantation of statistical process control in small scale industries- a review”, International Journal of Technologies and Engineering, Vol. 2, No. 7, pp. 121-124, 2015
V. Parkash, D. Kumar, R. Rajoria, “Statistical process control”, International Journal of Research in Engineering and Technology, Vol. 2, No. 8, pp. 70–72, 2013 DOI: https://doi.org/10.15623/ijret.2013.0208010
P. S. Parmar, V. A. Deshpande, “Implementation of statistical process control techniques in industry : a review”, Journal of Emerging Technologies and Innovative Research, Vol. 1, No. 6, pp. 583–587, 2014
J. V. Koleske, “Mechanical properties of solid coatings”, in: Encyclopedia of Analytical Chemistry: Applications, Theory and Instrumentation, John Wiley and Sons, 2006 DOI: https://doi.org/10.1002/9780470027318.a0608
A. E. Bryson, The control of quality in the manufacture of paint, PhD Thesis, Masachusetts Institute of Technology, 1950
P. Bhangale, R. Dhake, G. Gambhire, “Reduction in defects of car body panel using 7QC tools approach”, National Conference on Modelling, Optimization and Control, Pune, India, March 4-6, 2015
I. A. Memon, Q. B. Jamali, A. S. Jamali, M. K. Abbasi, N. A. Jamali, Z. H. Jamali, “Defect reduction with the use of seven quality control tools for productivity improvement at an automobile company”, Engineering, Technology and Applied Science Research, Vol. 9, No. 2, pp. 4044–4047, 2019 DOI: https://doi.org/10.48084/etasr.2634
M. L. Chew Hernandez, L. Viveros Rosas, R. F. Retes Mantilla, G. Espinosa Martínez, V. Velazquez Romero, “Supply chain cooperation by agreed reduction of behavior variability: a simulation-based study”, Engineering, Technology and Applied Science Research, Vol. 7, No. 2, pp. 1546–1551, 2016 DOI: https://doi.org/10.48084/etasr.1039
How to Cite
- Endnote/Zotero/Mendeley (RIS)
Authors who publish with this journal agree to the following terms:
- Authors retain the copyright and grant the journal the right of first publication with the work simultaneously licensed under a Creative Commons Attribution License that allows others to share the work with an acknowledgement of the work's authorship and initial publication in this journal.
- Authors are able to enter into separate, additional contractual arrangements for the non-exclusive distribution of the journal's published version of the work (e.g., post it to an institutional repository or publish it in a book), with an acknowledgement of its initial publication in this journal.
- Authors are permitted and encouraged to post their work online (e.g., in institutional repositories or on their website) after its publication in ETASR with an acknowledgement of its initial publication in this journal.
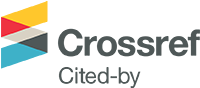
Most read articles by the same author(s)
Proposed remedies to prevent road traffic accidents (rtas) on highways in pakistan, a review on self compacting concrete with cementitious materials and fibers, defect reduction with the use of seven quality control tools for productivity improvement at an automobile company, comparison of mechanical properties of lightweight and normal weight concretes reinforced with steel fibers, design and analysis of news category predictor, effect of water-cement ratio on flexural strength of rc beams made with partial replacement of coarse aggregates with coarse aggregates from old concrete, effect of maximum aggregate size on the bond strength of reinforcements in concrete, effect of prepackaged polymer on compressive, tensile and flexural strength of mortar, sediment transport dynamics in the upper nara canal off-taking from sukkur barrage of indus river, effects of uncrushed aggregate on the mechanical properties of no-fines concrete.

Frequently Asked Questions
Download the Template
Make a submission
Data & Statistics
Indexing & Links
Latest Issue
Journal Issues
Journal Abbreviation Eng. Technol. Appl. Sci. Res.
eISSN 1792-8036
pISSN 2241-4487
Web of Science JCI 0.49
Web of Science Impact Factor 1.5
Clarivate JCI Quartile Ranking Q2
Scopus CiteScore Tracker (April 2024) 2.9
SCImago SJR 0.37
SCImago Quartile Ranking Q2
Crossref Membership DOI prefix: 10.48084 Direct DOI link: https://doi.org/10.48084/etasr
Citation Styling Available in the official Zotero Style Repository (add it from inside Zotero or download the csl file )
RIS/BIB Files Download links available in each article's abstract page.
Additional Information For Readers For Authors For Librarians
Announcements See all our announcements here .
[ETASR cover artwork created by our late friend, the great N. Tsagkarakis. Download HR here ]
Some updated stats about ETASR (April 02, 2024): - Editorial Board: 46 board members / 46 institutions / 31 different countries - 14th year of operation, 80 issues (bimonthly, first issue in Feb. 2011) - 2267 published papers, 7037 authors (3.10 authors per paper) from 80 different countries and 1178 different institutions/organizations (not counting departments) - 15253 registered readers from 116 different countries - mean number of Crossref citations per paper: 4.44 - days to acceptance: 45 - Clarivate (Web of Science) Impact Factor: 1.5 - Clarivate (Web of Science) JCI: 0.49 - Clarivate JCI Quartile Ranking: Q2 - Scopus CiteScore Tracker (March 2024) : 2.9
Indexed in : Web of Science / Master Journal List / Emerging Sources Citation Index, Scopus, SCImago National Library of Greece, Directory of Open Access Journals (DOAJ) (incl. DOAJ Seal), Crossref, HEAL-Link, Scilit, EBSCOhost, Exaly, HEC Journal Recognition System (HJRC), Zenodo, Google Scholar, SHERPA/ROMEO, MedOAnet, Directory of Open Access Scholarly Resources (ROAD), Publication Integrity & Ethics (PIE) and many more.
7 QC Tools Training
The 7 QC Tools are essential tools that help businesses identify, analyze, and effectively address quality-related issues. From increasing process effectiveness to decreasing defects, these tools give organizations the power to consistently enhance and deliver top-notch products and services. At Swades QMS, we strive to help organizations reach greatness in their quality management endeavors. As an industry leader, we provide intensive training sessions, including our extremely popular 7 QC Tools Training. Our program furnishes learners with the knowledge, capabilities, and practical insights needed to make these tools work effectively in their sector.
Our Training Methodology
We follow a dynamic training methodology that focuses on active participation, experiential learning, and knowledge application. Our experienced trainers employ a variety of techniques to create a stimulating and immersive training environment.
Interactive and Practical Sessions:
Our training sessions are far from passive lectures. We foster an atmosphere of collaboration and engagement, encouraging participants to actively contribute and learn from one another. Through group discussions, workshops, and hands-on exercises, participants gain practical experience in using the 7 QC Tools.
Hands-On Exercises, Case Studies, and Real-World Examples:
We firmly believe in learning by doing. Our training program incorporates hands-on exercises that simulate real-life quality scenarios, allowing participants to practice applying the 7 QC Tools in a controlled environment. We also utilize relevant case studies and real-world examples to illustrate the application of these tools across different industries.
Industry Best Practices and Relevant Standards:
Our training is grounded in industry best practices and the latest quality management standards. We provide insights into how the 7 QC Tools align with internationally recognized quality frameworks, such as ISO 9001. By integrating these practices and standards into the training, participants gain a comprehensive understanding of how the tools can be effectively utilized within their organization.
Training Content
1. introduction to quality control and the 7 qc tools.
- Overview of quality control principles and importance in organizations
- Introduction to the concept of the 7 QC Tools and their significance
- Explanation of how the 7 QC Tools contribute to quality improvement initiatives
2. Pareto Chart
- Understanding the Pareto principle and its application in quality control
- Steps to create a Pareto chart for identifying and prioritizing quality issues
- Analyzing and interpreting Pareto charts to focus improvement efforts
3. Cause-and-Effect Diagram (Fishbone Diagram)
- Introduction to cause-and-effect diagrams and their purpose in problem-solving
- Steps to construct a cause-and-effect diagram to identify root causes
- Using the fishbone diagram to facilitate team brainstorming and analysis
4. Check Sheet
- Understanding the purpose and benefits of check sheets in data collection
- Designing and utilizing check sheets for collecting quality-related data
- Analyzing check sheet data to identify trends, patterns, and areas for improvement
5. Scatter Diagram
- Introduction to scatter diagrams and their role in analyzing relationships between variables
- Creating scatter diagrams to visualize correlations and potential cause-and-effect relationships
- Interpreting scatter diagrams and making data-driven decisions based on the analysis
6. Histogram
- Explanation of histograms and their application in data analysis
- Constructing histograms to understand distribution patterns and variations
- Interpreting histograms to identify process performance and areas for improvement
7. Control Chart
- Overview of control charts and their significance in monitoring process stability
- Steps to create and interpret control charts for tracking process performance
- Utilizing control charts to identify and respond to process variations and out-of-control situations
8. Scatter Diagram
9. data collection and analysis techniques.
- Best practices for effective data collection and management
- Techniques for analyzing and interpreting data using the 7 QC Tools
- Integrating the 7 QC Tools into a comprehensive quality control system
10. Application and Case Studies
- Applying the 7 QC Tools to real-world quality issues and challenges
- Analyzing case studies to understand practical implementation of the tools
- Discussion and sharing of success stories and lessons learned
11. Q&A and Wrap-Up
- Addressing participant questions and concerns
- Summarizing key takeaways from the training program
- Closing remarks and next steps for participants to apply the acquired knowledge
Who Should Attend
- Managers, Executives, Engineers and Other Staff
- Students or any Professionals requiring an overview of 7 QC Tools
About Swades QMS
- ISO 9001:2015 Quality Management System Consultancy
- ISO 14001:2015 Environmental Management System Deployment
- ISO 45001:2018 Occupational Health & Safety Management System Deployment
- ISO 13485:2016 Medical Devices Quality Management System Deployment
- Quality and Productivity Improvements Projects
- Six Sigma Green Belt Training
- MSA – Measurement System Analysis
- Process Capability
- Hypothesis Testing
- Design of Experiments
- Statistical Process Control Training
- Lean Manufacturing Awareness
- Minitab Training
WhatsApp us
Academia.edu no longer supports Internet Explorer.
To browse Academia.edu and the wider internet faster and more securely, please take a few seconds to upgrade your browser .
Enter the email address you signed up with and we'll email you a reset link.
- We're Hiring!
- Help Center
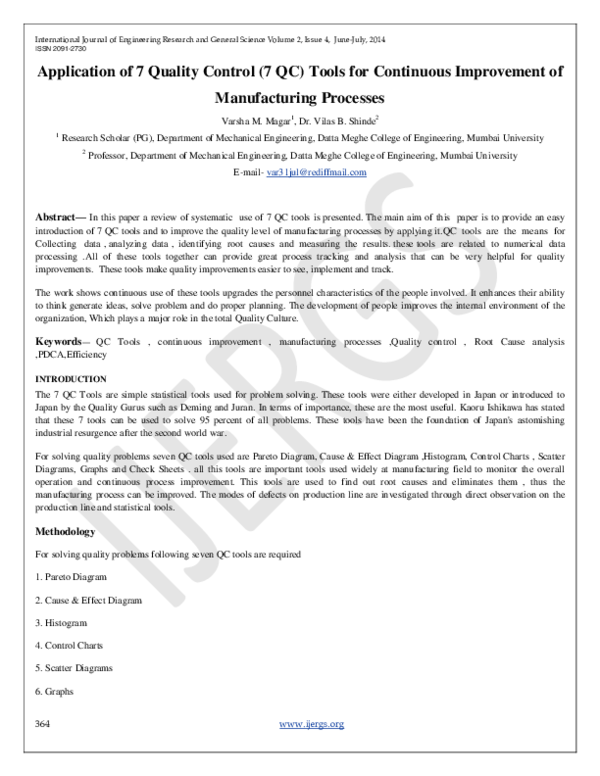
Application of 7 Quality Control (7 QC) Tools for Continuous Improvement of Manufacturing Processes

In this paper a review of systematic use of 7 QC tools is presented. The main aim of this paper is to provide an easy introduction of 7 QC tools and to improve the quality level of manufacturing processes by applying it.QC tools are the means for Collecting data , analyzing data , identifying root causes and measuring the results. these tools are related to numerical data processing .All of these tools together can provide great process tracking and analysis that can be very helpful for quality improvements. These tools make quality improvements easier to see, implement and track.
Related Papers
Pranay S . Parmar
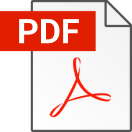
Mohamed Elsherif
If organizations wish to achieve continuous quality improvement they need to use appropriate selection of quality tools and techniques. In this paper a review of possibilities of the systematic use of seven basic quality tools (7QC tools) is presented. It is shown that 7QC tools can be used in all process phases, from the beginning of a product development up to management of a production process and delivery. It is further shown how to involve 7QC tools in some phases of continuous improvement process (PDCA-cycle), Six Sigma (DMAIC) and Design for Six Sigma (DMADV) methodologies, and Lean Six Sigma.
Kassu Sileyew , Haftu Berhe (PhD)
The purpose of the project is to minimize existing long delivery time of shoe Venice model by integration of 7QC tools manufacturing industries are facing big challenges to exceed their customers' expectations. For the reason that these industries could not achieve the delivery time that fixed by the custom leather Industry PLC is one of Ethiopian leather and shoe manufacturing industry facing this problem. As well, generating skilled manpower capable of continuously solve problems analytically. At the time of the project, there was customer complai time of Venice model shoe. It takes more than three months to dispatch 240 pairs of Venice model shoe. In addition, there was concentration of wastes like transportation, waiting, defect and inventory. The methodology followed for this project is problem solving approach. Tensteps of quality control story formula integrated with quality control seven tools were used. The findings of the project after the completion of nine month implementation period, the holding again process analysis. 38 activities were non reason, the delivery time is shortening by 18,236.55 min with 51.08 % improvement. In addition, process analysis a manufacturing industries can similarly use and follow the problem solving approach and 7 QC tools to eliminate wastes. Due to time constraint, the project is only focused on Venice mode however there were more than 30 model shoe types. At the end, the cross functional team members should solve another chronic problem by practicing problem solving approach. The top management should monitor and evaluate the activities in order to s implementation.
Journal ijmr.net.in(UGC Approved)
Continuous quality improvement process assumes and requires that a team of experts together with the company leadership actively use six sigma and quality tools in their improvement activities and decision making process. Currently there are a significant number of quality assurance and quality management tools available, so the selection of the most appropriate is not always an easy task. Tools are essential ingredients of a process and basic instruments for the success of a quality program. Many companies have used tools without giving sufficient thought to their selection and have then experienced barriers to progress. Six sigma & Quality Tools cannot remedy every quality problem but they certainly are a means for solving problems. Consequently, it needs to be emphasized that while tools can be very effective in the right hands, they can be very dangerous in the wrong hands. It is, therefore, important to know how, when and which tools should be used in problem solving or improvement processes.
Mirko Soković
The paper is dealing with one segment of broader research of universality an systematicness in application of seven basic quality tools (7QC tools), which is possible to use in different areas: power plant, process industry, government, health and tourism services. The aim of the paper was to show on practical examples that there is real possibility of application of 7QC tools. Furthermore, the research has to show to what extent are selected tools in usage and what reasons of avoiding their broader application are. The simple example of successful application of the quality tools are shown on selected company in process industry. .
Purpose: The paper is dealing with one segment of broader research of universality systematicness in application of seven basic quality tools (7QC tools). The research was carried out in different areas that include power plant, process industry, government, health and tourism services. The aim of the research was to show on practical examples that there is real possibility of application of 7QC tools. Furthermore, the research has to show to what extent are selected tools in usage and what reasons of avoiding their broader application are. The simple example of successful application of one of quality tools are shown on selected company in process industry.Design/methodology/approach: In the research each of 7QC tools have been tested and its applicability in the frame of selected business has been shown. Systematic approach is explained on the example of selected company in process industry which is ISO 9000:2000 certified.Findings: Conducted research has shown that there is possi...
MALAYSIA ITALY DESIGN INSTITUTE
wan mohamad akram
Trackwork maintenance consist of a few process and activities due to the various sections and areas that need to cover. To do the maintenance, Trackwork department requires many teams to complete the task. Based on observation, the management tend collect the data and unable to identify the possible critical defects. The scenario referred to the build – up maintenance team since there are so many types of defects occurring everyday with different defects. To detect the critical and the most defective areas and types of defects are important for continuous improvement programme and to avoid the repetitive problem. To complete this research, researcher need to join the team for maintenance program to see the flow and to prove that the earlier statement is correct. A few internal interviews has been conducted to gain as much as possible information and data from the field personnel. Sometimes, there are bit challenges to collect the data since the personnel are not always free and not ready to share their ideas. Some important data are so confidential makes researcher hard to get the real information. Result from this research gain through a few method and study techniques. To get the defects trend, a line chart are requires using the data and information and the using the pareto chart to recognise the vital few and trivial many of the defect at the early stage. Then, using ishikawa diagram to find out the root cause and using failure modes and effects analysis to study the root causes based on the defects and classified into three categorized, neglect, monitoring and solve. With the study, hopefully it can help the build – up team at particular areas to implement the countermeasure plan to minimize the risk and the problem by their own technique and way. The overall results are specific for build – up team at Rapid Rail Ampang Line and the results may vary to other areas.
Pharveen Parameswaran
This paper aims at providing an overview of the evolution, current research and the history of continuous improvement over time through reviewing the literature extensively. The paper covers the inception of continuous improvement and its evolution into today's world's sophisticated methodologies. The research covers the well-known programs of continuous improvement if not covering the entire plethora of the past and the present. It also covers the various tools used by the organizations for addressing the need of continuous improvement and thus may serve the purpose of reference for people who wish to pursue the field of continuous improvement and wants to know its development form its historical form to its modern day avatar.
ΒΑΣΙΛΕΙΟΣ ΙΣΜΥΡΛΗΣ
Purpose – The purpose of this paper is to examine the benefits of ISO 9001 certification and the association between them, the level of implementation of the critical success factors (CSFs) required for the appropriate functioning of the quality management system in ISO 9001:2008 certified companies and between other demographic variables. Design/methodology/approach – A research project was carried out in Greek companies from all business sectors using the questionnaire technique. The selected companies implement a quality management system in accordance with the ISO 9001:2008 standard. Correspondence analysis, a methodology from the field of multidimensional statistics, was used to identify significant differences between the effects on performance and other variables such as the implementation level of CSFs relating to the quality management system and years of certification. Findings – External benefits seem to be more important than internal benefits. The least important benefits were mostly business results, such as profits, costs and market share. Differences were detected between the level of performance and certain demographic variables such as the use of International Organization for Standardisation (ISO) alone, size and years of certification. The certified companies have generally benefited from ISO implementation. Research limitations/implications – The study was based on the perceptions (subjective data) of only one quality manager/representative from each company. The motives for ISO certification, which can seriously affect the benefits derived, were not examined. Practical implications – The measures presented here can be used by certified companies to evaluate performance (financial or not) related to ISO 9001 certification and to discover those factors that contribute to the better exploitation of the ISO 9001:2008 standard. Originality/value – This paper aims to evaluate performance since the implementation of the ISO 9001:2008 standard in Greek companies, which are confronting a tough economic environment and to analyse this data with a methodology from the multidimensional field, with the complementary use of some special tables of coincidence.
RELATED PAPERS
YASH ACHARYA
IJAERS Journal
Rami Hikmat Fouad Al-Hadeethi
Mohamed Aichouni
IAEME Publication
Aditya Abdul
Anas SHOSHAN
8th ACIS International Conference on Software Engineering Research, Management and Applications, SERA 2010
Olga Ormandjieva , Alain Abran
Arnoldo Sandoval
Gagic Snjezana
Rushik Trivedi
Monica Aguirre
IJEETE Journals
WARSE The World Academy of Research in Science and Engineering
YADALA RAVI KUMAR
daniel torija
Christian Pachas
TJPRC Publication
Carlos Medrano
Israel Vicenteño
IJESRT Journal
- We're Hiring!
- Help Center
- Find new research papers in:
- Health Sciences
- Earth Sciences
- Cognitive Science
- Mathematics
- Computer Science
- Academia ©2024

IMAGES
VIDEO
COMMENTS
The 7 QC Tools: Flow Charts. Cause and Effect Diagram (Fishbone or Ishikawa) Checksheet. Histogram. Pareto Chart. Scatter Diagram. Control Chart. Note: We are considering here the Flow chart in this article as a part of 7 Basic QC Tools.
To elucidate the effectiveness of quality control methods, we embarked on a case study using the 7 QC tools and PDCA cycle on a data base of a sample bottle manufacturing unit. The results were ...
In this paper a review of systematic use of 7 QC tools is presented. The main aim of this paper is to provide an easy introduction of 7 QC tools and to improve the quality level of manufacturing ...
It involves analysis of the usage of the 7 QC tools and identifying the barriers, benefits, challenges and critical success factors (CSFs) for the application of the 7 QC tools in a HEI setting.,An online survey instrument was developed, and as this is a global study, survey participants were contacted via social networks such as LinkedIn.
Abstract: -. In this paper a review of systematic use of 7 QC tools for improving the quality of deep groove ball bearing is presented. QC tools are the means for Collecting data, analyzing data, identifying root causes and measuring the results. Quality Control tools are related to numerical data processing techniques.
The main finding of this study is that 10% of participants within the manufacturing sector perceived that the 7 new QC tools could solve above 80% of organisational problems. Another relevant finding presented in this paper is that tree diagrams were the most utilised of the 7 new QC tools within the manufacturing sector.
Unfortunately, the complexity of the subject intimidated most workers, so Ishikawa focused primarily on a reduced set of tools that would suffice for most quality-related issues. The 7 QC tools are: Check sheet. Fishbone diagram (cause and effect diagram, or Ishikawa diagram) Histogram. Pareto chart. Control chart.
The aim of this project was to study the quality improvement after accomplishment of 7QC tools in a manufacturing practice of visors used in speedometer. The main motive of this project was used to detect the defects that occurred in the manufacturing procedure and analyzed using 7 QC tools. Moreover that, the new design has been planned for ...
Using the Seven Basic Quality Tools in 2022: In this course, you will learn the theory behind these seven quality tools and will also learn, to take the power of these tools to the next level using the current computing power. During the post-war industrial revolution, Kaoru Ishikawa proposed seven basic quality tools to improve quality.
— In this paper a review of systematic use of 7 QC tools is presented. The main aim of this paper is to provide an easy introduction of 7 QC tools and to improve the quality level of manufacturing processes by applying it.QC tools are the means for Collecting data , analyzing data , identifying root causes and measuring the results. these tools are related to numerical data processing .All ...
Available [email protected] 355. Review on Quality Management using 7 QC Tools. 1 Nikunjkumar A. Parmar and 2Shubham Awasthi, 1,2 Department of Mechanical Engineering, Parul Institute of ...
It was found from the results that after the successful implementation of the QC tools, the defect level reduced by 90% (from 132 to 13 defects) at the chassis line. Similarly, the defect level was reduced by 80% (from 157 to 28 defects) at the trim line. The automobile company implemented only a few of the seven QC tools in their assembly line.
The Power of 7 QC Tools and PDCA: A Case Study on Quality Problem Solving Muhammad Umar Ibrahim CSCP®, CSSMBB® 5mo 14 QC Tools Stephen (Steve) Ansuini 6y ...
Case Studies Contact Blog The 7 Quality Control (QC) Tools Explained with an Example! Topic. Advanced Analytics. Subtopic. Foundations (Statistics & Excel) ... Youíll learn ALL about the 7 QC Tools while we work an example to demonstrate how you might use these tools in the real world. What You'll Learn. High level use of Flow Chart, Check ...
PurposeThe main purpose of this study is to revisit Ishikawa's statement: "95% of problems in processes can be accomplished using the original 7 Quality Control (QC) tools". The paper critically investigates the validity of this statement in higher education institutions (HEIs). It involves analysis of the usage of the 7 QC tools and identifying the barriers, benefits, challenges and ...
Business-related examples and case studies. Downloadable resources for learning 7 basic quality tools and quality management. Your queries will be responded by the Instructor himself. Start using 7 basic quality tools to their full potential to become proficient at tools of quality today! Either you're new to excel and quality tools, or you've ...
Seven quality control (7QC) tools are used for reducing defects during manufacturing. These tools are highly effective in productivity and quality improvement. In this case, the study of the 7QC tools was applied in an automotive factory in order to reduce paint shop defects. Within four months the production line was inspected, defects were categorized and the 7QC tools were successfully ...
7 QC Tools are also known as Seven Basic Quality Tools and Quality Management Tools. These graphical and statistical tools are used to analyze and solve work-related problems effectively. The 7 Quality Tools are widely applied by many industries for product and process improvements, and to solve critical quality problems.. 7QC tools are extensively used in various Problem Solving Techniques ...
The purpose of the study was to apply some of the seven quality control tools (7 QC tools) for reducing delay the delivery problem. The Cause and Effect Diagram was found out the root causes of this problem and the Pareto Chart was used to help ordering the important of delay the delivery problem, it was found that coordination problem was the major cause. Finally, the Matrix Diagram was used ...
Through group discussions, workshops, and hands-on exercises, participants gain practical experience in using the 7 QC Tools. Hands-On Exercises, Case Studies, and Real-World Examples: We firmly believe in learning by doing. Our training program incorporates hands-on exercises that simulate real-life quality scenarios, allowing participants to ...
In this paper a review of systematic use of 7 QC tools is presented. The main aim of this paper is to provide an easy introduction of 7 QC tools and to improve the quality level of manufacturing processes by applying it.QC tools are the means for Collecting data , analyzing data , identifying root causes and measuring the results. these tools are related to numerical data processing .All of ...
The 7 QC tools also known as " The Basic Seven" are: Cause-and-effect diagram template. Check sheet template. Control chart template. Histogram template. Pareto chart template. Scatter diagram template. Stratification template. Let's dive into what each of these 7 basic QC tools is and what they are used for!
planned a study to reduce the rejection of castings using Quality control tools (QC) in North India. The study results in annual saving of Rs. 10 lakhs. [14] conducted a study aimed to find out the causes of quality related problems. Quality tools like cause and effect diagram, histogram, Pareto diagram and check sheet were used in the study. The
️ 7 QC Tools Explained with Case Study: https://lnkd.in/fknYdE6 ️ Join us on WhatsApp: https://lnkd.in/diKb6-uV ️ Join us on LinkedIn:…