Center for Integrated Agricultural Systems
University of wisconsin-madison, collaborative research on sustainability.
- Values-Based Food Supply Chain Case Studies
These publications are part of a series of case studies and Research Briefs examining values-based food supply chains—strategic business alliances formed between primarily midsize farms/ranches and their supply chain partners. Values-based food supply chains distribute significant volumes of high-quality, differentiated food products and share the rewards equitably. Farmers and ranchers function as strategic partners rather than easily replaced input suppliers. All participants in these business alliances recognize that creating maximum value for the product depends on significant interdependence, collaboration and mutual support.
- Values-based food supply chains: An introduction to nine case studies
- Values-based food supply chains: Strategies for agri-food enterprises of the middle
- Values-based food suppy chains: Program participation and policy changes
- Using values-based food supply chain case studies in university classes
- Values-based food supply chains: Cross-case observations

Case studies: Multi-farm direct-to-wholesale food business chains
Country Natural Beef
- Research Brief
Organic Valley
Shepherd’s Grain
Case studies: Multi-farm direct-to-consumer business chains
Co-op Partners Warehouse
Full Circle
Home Grown Wisconsin
Good Earth Farms
Idaho’s Bounty
These publications were produced as part of the national Agriculture of the Middle initiative. “Agriculture of the Middle” refers to a disappearing sector of mid-scale farms/ranches and related agrifood enterprises that are unable to successfully market bulk commodities or sell food directly to consumers. For more information, visit www.agofthemiddle.org .
The case study research team includes:
- Kate Clancy, University of Minnesota Institute for Sustainable Agriculture
- Robert P. King, University of Minnesota Department of Applied Economics
- Larry Lev, Oregon State University Department of Applied Economics
- Marcia Ostrom, Washington State University Center for Sustaining Agriculture and Natural Resources
- G.W. Stevenson, UW-Madison Center for Integrated Agricultural Systems
- Farming Systems
- Farm to institution
- Food Transportation
- Dairy Growth Management
- Partnerships
- Learning About Sustainable Agriculture & Food Systems
New Refreshed Project Logos are Here! Read on
How Walmart brought unprecedented transparency to the food supply chain with Hyperledger Fabric
Download Printable Case Study
When an outbreak of a food-borne disease happens, it can take days, if not weeks, to find its source. Better traceability could help save lives by allowing companies to act faster and protect the livelihoods of farmers by only discarding produce from the affected farms.
Walmart thought that blockchain technology might be a good fit for the decentralized food supply ecosystem. To test this hypothesis, the company created a food traceability system based on Hyperledger Fabric. Walmart, together with its technology partner IBM, ran two proof of concept projects to test the system. One project was about tracing mangos sold in Walmart’s US stores and the other aimed to trace pork sold in its China stores.
The Hyperledger Fabric blockchain-based food traceability system built for the two products worked. For pork in China, it allowed uploading certificates of authenticity to the blockchain, bringing more trust to a system where that used to be a serious issue. And for mangoes in the US, the time needed to trace their provenance went from 7 days to… 2.2 seconds!
Walmart can now trace the origin of over 25 products from 5 different suppliers using a system powered by Hyperledger Fabric. The company plans to roll out the system to more products and categories in the near future. In fact, it has recently announced that it will start requiring all of its suppliers of fresh leafy greens (like salad and spinach) to trace their products using the system.
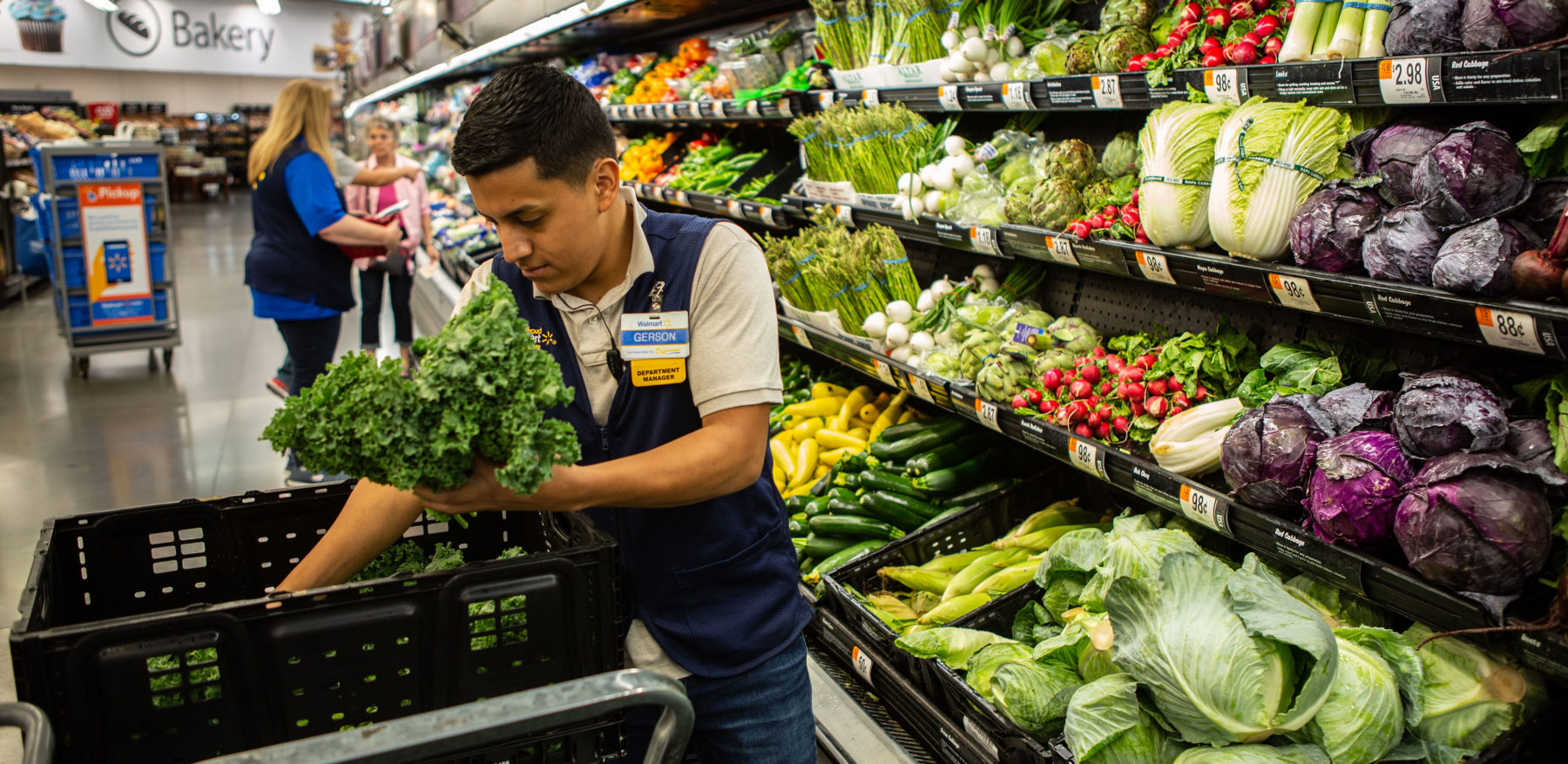
Tracking food for better safety
We rarely think about it, but the modern food system is a marvel. We have access to fresh produce all year round, buy exotic food from all around the world, and have more variety than our ancestors could ever dream of.
Our food is generally safe to eat. Still, occasionally it can make us sick. Last year in 2018 there were at least 18 reported outbreaks of foodborne illnesses in the USA, including the E. coli found in romaine lettuce.
“People talk about the food supply chain,” says Frank Yiannas, former Vice President of Food Safety at Walmart. “But it is not actually a chain, it’s a complex network.” When an outbreak of a food-borne disease does happen, it can take days, if not weeks, to find its source. If investigators cannot point to a specific farm or farms, the government usually advises consumers to avoid products grown in a certain area (as happened with romaine lettuce from Yuma, Arizona), or even to avoid the type of product altogether. According to Walmart , millions of bags or heads of lettuce had to be removed, and consumers lost confidence in romaine lettuce altogether. Better traceability could help save lives by allowing companies to act faster and protect the livelihoods of farmers by only discarding produce from the affected farms.
For this reason, Walmart has always been interested in enhancing transparency and traceability in the food system. Mr. Yiannas explains that the company has tried many systems and approaches to solving this problem over the years; none had brought them the kind of results they were after. When Yiannas first heard about blockchain and the idea of using it to trace food in the supply chain, he was skeptical.

From blockchain skeptic to believer
Karl Bedwell, Senior Director at Walmart Technology, explains, “Creating a (traceability) system for the entire food supply ecosystem has been a challenge for years, and no one had figured it out. We thought that blockchain technology might be a good fit for this problem, because of its focus on trust, immutability, and transparency.”
Bedwell and his team introduced Yiannas to the possibilities of blockchain technologies for enterprise solutions. Says Yiannas, “I really had an “aha” moment once I deeply understood the technology. I had been hesitant about creating yet another traceability system – the ones we had tried in the past never scaled. Now I understand that was because they were centralized databases. Blockchain, with its decentralized, shared ledger felt like it was made for the food system!”
With the business interest in blockchain technology confirmed, Walmart started working on two proof of concept (POC) projects with their technology partner IBM.
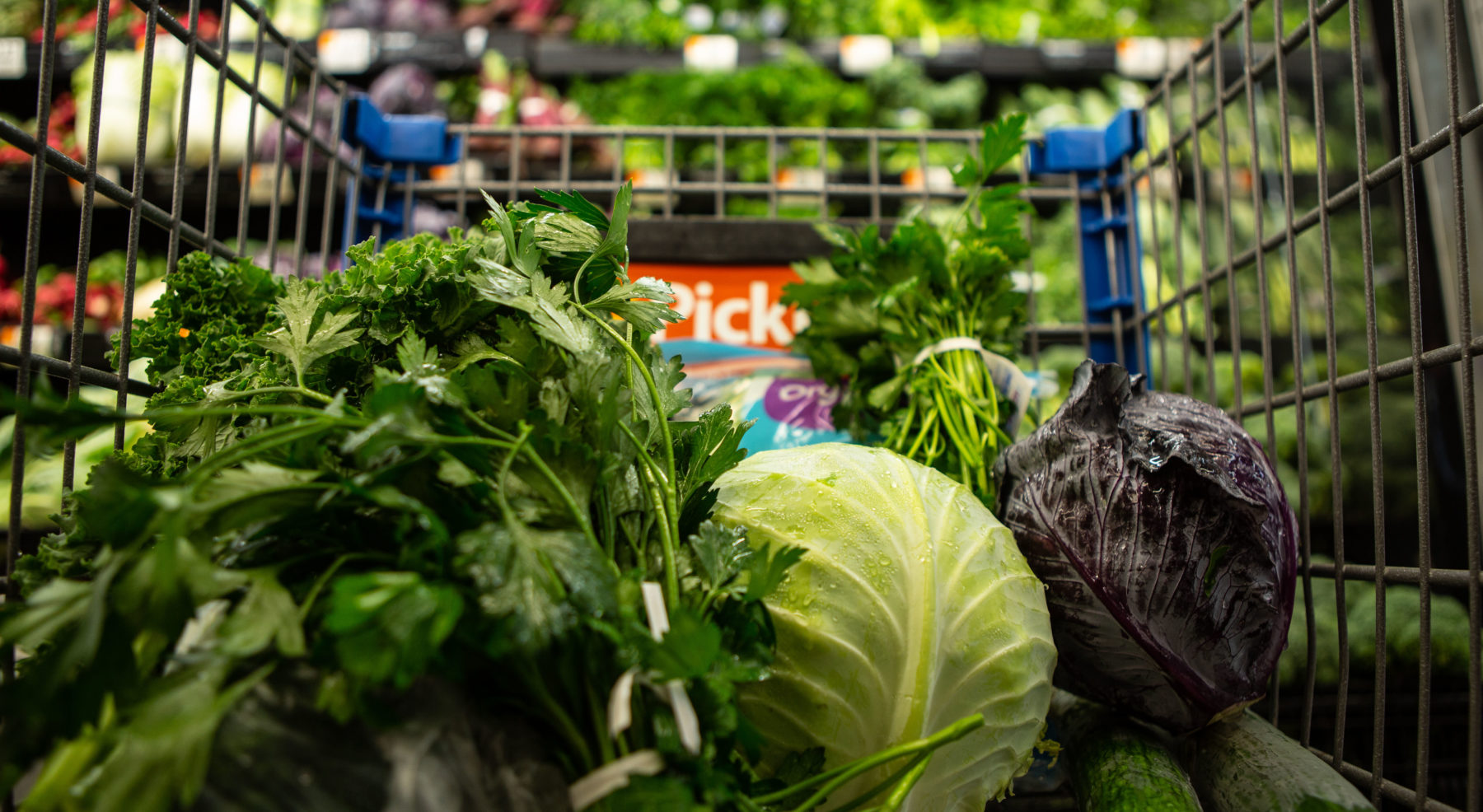
Choosing the blockchain
Walmart Technology considered several blockchain technologies but ultimately decided to go for Hyperledger Fabric.
“IBM brought Hyperledger Fabric to us. We looked into Ethereum, Burrow project and others. Ultimately, we decided to go with Hyperledger Fabric because it met most of our needs for a blockchain technology,” Bedwell said. “We felt that it best met our needs. It is an enterprise-grade blockchain technology, and it is permissioned.”
The team also found it important to work with an open-source, vendor-neutral blockchain. Since the food traceability system was meant to be used by many parties, including Walmart’s suppliers and even direct competitors, the technology ecosystem underlying it needed to be open.
Hyperledger Fabric is a blockchain framework implementation and one of the Hyperledger projects hosted by The Linux Foundation. Intended as a foundation for developing applications or solutions with a modular architecture, Hyperledger Fabric allows components, such as consensus and membership services, to be plug-and-play. Hyperledger Fabric leverages container technology to host smart contracts called “chaincode” that comprise the application logic of the system.
For mangoes in the US, the time needed to trace their provenance went from 7 days to… 2.2 seconds!
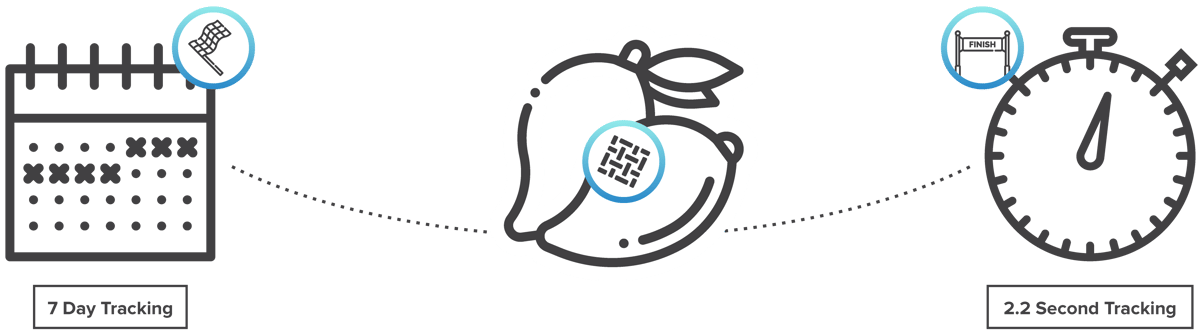
In October 2016, Walmart, together with its technology partner IBM, announced the two projects: one was about tracing the origin of mangos sold in Walmart’s US stores and the other aimed to trace pork sold in its China stores.
For the mango POC, Yiannas started by creating a benchmark. He bought a packet of sliced mangoes at a nearby Walmart store and asked his team to identify which farm they had come from – as fast as possible. The team started calling and emailing distributors and suppliers, and eventually had an answer almost seven days later. This was not bad by industry standards, but Walmart wanted to do much better. So together with IBM, they got to work building a blockchain-based food traceability system.
The Walmart Technology team looked at their own processes as well as those of their suppliers to design the application. Archana Sristy, Director of Engineering at Walmart, explains, “[Our team at Walmart Technology] co-led the core design and setup of the application (with IBM), as well as built the integration with the enterprise systems. We worked with GS1 (the standards authority in barcodes and labeling) to define the data attributes for upload to the blockchain. IBM wrote the chaincode.
Suppliers used new labels and uploaded their data through a web-based interface.
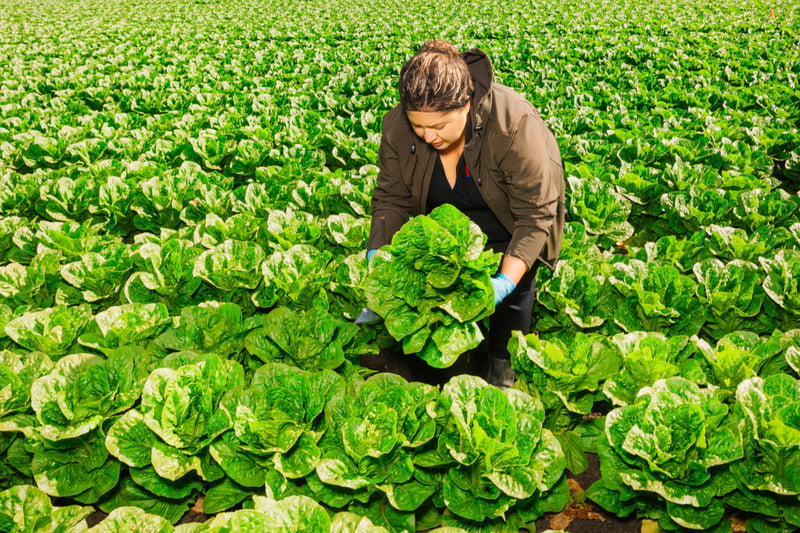
From POC to production, from Walmart to IBM Food Trust
Once Walmart saw that the system worked, they wanted to expand it – and not just within Walmart. Given the interconnected nature of the food system and the company’s negative experience with closed systems, Walmart wanted to make sure that this time, many players were involved. Says Yiannas, “(Walmart’s) CEO was reaching out to other food companies the next day, including other retailers!” Wal-Mart collaborated with IBM and others to set up IBM Food Trust , involving prominent players in the food industry, like Nestle and Unilever.
The Walmart team had a positive experience working with Hyperledger. “Every question that we had, it looked like the Hyperledger community had already been working on addressing that,” says Bedwell. For example, in building a truly open system, the Walmart team worried about interoperability with other blockchain-based traceability systems. And as if in answer to their concern, Hyperledger recently announced its collaboration with Ethereum. He adds, “It seems that the Hyperledger community is addressing everything that enterprises would be concerned about.”
Says Yiannas, “I really had an ‘aha’ moment once I deeply understood the technology. I had been hesitant about creating yet another traceability system – the ones we had tried in the past never scaled. Now I understand that was because they were centralized databases. Blockchain, with its decentralized, shared ledger felt like it was made for the food system!”
Tips from Frank Yiannas on implementing your blockchain project
1. Let the business lead the project , not the IT department.
2. Understand the business case deeply. Make sure that you know and can explain why blockchain is the right solution.
3. In a large organization, you need to bring a lot of people along. Think about all the different departments that will be affected by the projects. Meet with these stakeholders early on and explain what you are trying to do.
4. Have your soundbite! People don’t get inspired by technology, but by a vision. For us, it was the story of mangoes – 7 days vs. 2.2 seconds with blockchain.
5. Participate in forums that allow you to speak to other companies who have launched similar projects successfully. It helps if you help an expert in the field who’s willing to come in and educate fellow members.
6. Start small, with a POC. And when you’ve run your pilots and are convinced about the business value, go ahead and scale. After all, Yiannas says, “Walmart is a pretty big lab! If it can scale at Walmart, it can scale anywhere!”

Looking forward
Walmart now traces over 25 products from 5 different suppliers using IBM Blockchain which is built atop Hyperledger Fabric. The products include produce such as mangoes, strawberries and leafy greens; meat and poultry such as chicken and pork; dairy such as yogurt and almond milk; and even multi-ingredient products such as packaged salads and baby foods.
Yiannas says of the impact, “This solution allows us to see the whole chain in seconds! We can take a jar of baby food and see where it was manufactured and trace back all the ingredients to the farms!”
Walmart plans to roll out the system to more products and categories in the near future in cooperation with IBM Food Trust.. In fact, the company recently announced that it will start requiring all of its suppliers of fresh leafy greens (like salad and spinach) to trace their products using the system.
“Using the IBM Food Trust network that relies on blockchain technology, we have shown that we can reduce the amount of time it takes to track a food item from a Walmart Store back to source in seconds, as compared to days or sometimes weeks,” Walmart wrote in a letter to suppliers.
Beyond tracing the products’ journey, the company might start tracing other data, like sustainability.
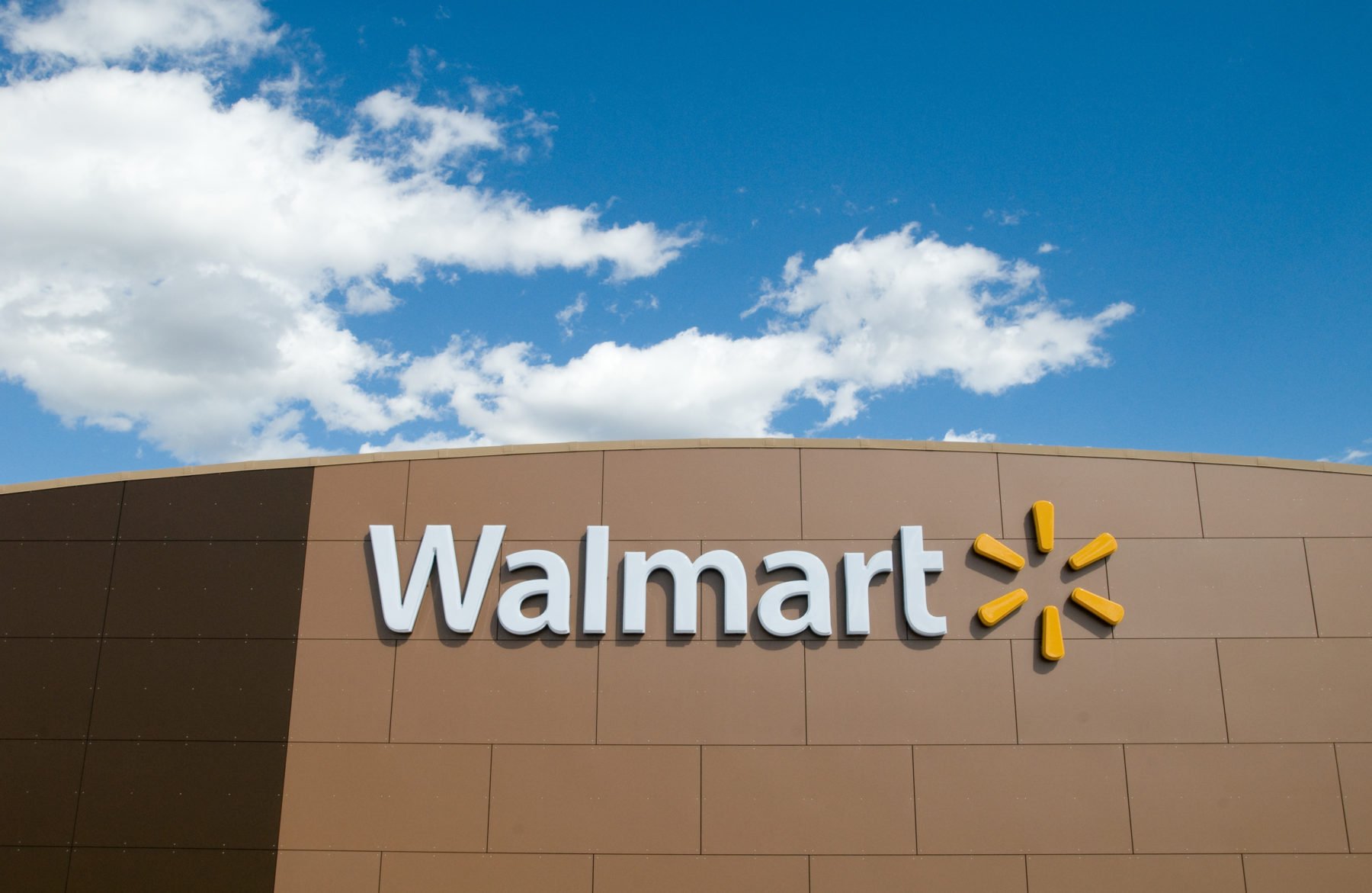
About Walmart
Walmart Inc. (NYSE: WMT) helps people around the world save money and live better – anytime and anywhere – in retail stores, online, and through their mobile devices. Each week, nearly 265 million customers and members visit our more than 11,200 stores under 55 banners in 27 countries and eCommerce websites. With fiscal year 2018 revenue of $500.3 billion, Walmart employs over 2.2 million associates worldwide. Walmart continues to be a leader in sustainability, corporate philanthropy and employment opportunity. Additional information about Walmart can be found by visiting http://corporate.walmart.com .
About Hyperledger
Hyperledger is an open source collaborative effort created to advance cross-industry blockchain technologies. It is a global collaboration including leaders in banking, finance, Internet of Things, manufacturing, supply chain, and technology. The Linux Foundation hosts Hyperledger under the foundation. To learn more, visit hyperledger.org
Sign up for Hyperledger Horizon & /dev/weekly newsletters
By signing up, you acknowledge that your information is subject to The Linux Foundation's Privacy Policy
- Architecture and Design
- Asian and Pacific Studies
- Business and Economics
- Classical and Ancient Near Eastern Studies
- Computer Sciences
- Cultural Studies
- Engineering
- General Interest
- Geosciences
- Industrial Chemistry
- Islamic and Middle Eastern Studies
- Jewish Studies
- Library and Information Science, Book Studies
- Life Sciences
- Linguistics and Semiotics
- Literary Studies
- Materials Sciences
- Mathematics
- Social Sciences
- Sports and Recreation
- Theology and Religion
- Publish your article
- The role of authors
- Promoting your article
- Abstracting & indexing
- Publishing Ethics
- Why publish with De Gruyter
- How to publish with De Gruyter
- Our book series
- Our subject areas
- Your digital product at De Gruyter
- Contribute to our reference works
- Product information
- Tools & resources
- Product Information
- Promotional Materials
- Orders and Inquiries
- FAQ for Library Suppliers and Book Sellers
- Repository Policy
- Free access policy
- Open Access agreements
- Database portals
- For Authors
- Customer service
- People + Culture
- Journal Management
- How to join us
- Working at De Gruyter
- Mission & Vision
- De Gruyter Foundation
- De Gruyter Ebound
- Our Responsibility
- Partner publishers

Your purchase has been completed. Your documents are now available to view.
Short food supply chains – a growing movement. The case study of the Viseu Dão Lafões Region
In spite of the increasing attention being paid to short food supply chains (SFSCs), research in the area is still scarce, particularly in Portugal. Thus, based on a case study in Viseu Dão Lafões Region (VDLR), we intend to identify and discuss (emphasizing potentialities and constraints) the movement of SFSCs in the region. This case study is based on document analysis and interviews with agrifood baskets’ promotors. On the one hand, the results show the wide variety of SFSCs that exist in the region and the emergence of new forms of SFSCs like the agrifood baskets. On the other hand, the empirical research also emphasizes the environmental, economic, and sociocultural benefits of SFSCs that will have a positive impact on the well-being of producers, consumers, and/or on the whole region. However, the interviews have also exposed a (certain) limitation in terms of communication and marketing that may constraint these initiatives. From a practical point of view, it became clear that producers must do their best to develop their communication and marketing strategies; from a political point of view, local authorities should provide the necessary assistance to help implement training programmes and develop suitable communication and marketing skills.
1 Introduction
Globalization has opened the way for several food products to be made available all over the world. This opportunity represents a huge increase in the financial return of the food industry, of food producers, and of consumers (Cappelli and Cini 2020 ). In 2016, for instance, the European Union (EU) imported almost 93 million tonnes of food from outside the EU and exported 91 million tonnes of food to countries that don’t belong to the UE. Compared to 2012, food imports have increased by 6% in terms of volume and exports have increased 42% (EC 2017 ).
This evolution has clearly changed consumers’ eating and buying habits, and more than often, they choose to replace local and retail markets with supermarkets and discount stores where they can purchase all the food products they need. Furthermore, the significant change in people´ lifestyle, the ever-increasing working hours that keep people away from their houses, and the fact that people do not have time to do their own cooking any more (Duarte 2013 ) forced them to seek these larger infrastructures. It is true that we are constantly drawn to easy, junk, exotic, and hyper-transformed food influenced by the seductive messages of large supermarket chains (Pinto 2013 ) that fail to include small farmers.
In this context, the short food supply chains (SFSCs) can be an interesting alternative. A review of literature shows the economic, social, and environmental benefits associated with SFSCs, for producers and consumers.
For local producers, who were not able to work with the large supermarket chains for a number of reasons (e.g. low production capacity, non-competitive prices, being away from large population centres, etc.), the attention attached to SFSCs gives them the opportunity to contribute to territorial development (Mundler and Laughrea 2016 ) by bringing back and revaluing different indigenous varieties of vegetables or fruit (Cappelli et al. 2018 ) and by generating a significant economic contribution (Mundler and Laughrea 2016 ; Raftowicz et al. 2020 ). For consumers, it is an opportunity to purchase safer products of higher quality. Duarte ( 2013 ), for example, states that these products are increasingly in demand due to their taste and organoleptic attributes and consumers are more and more concerned with nutrition, health, and safety issues.
Moreover, previous crises and food insecurities were key to emphasize the importance of local markets and alternative food networks (Wilkinson 2011 ), since they may represent a response to allay the population’s concerns by providing them with food products that do not have to travel long distances to be available.
As claimed by Fiore ( 2016 ), concerning direct selling in the wine sector, understanding consumer needs and expectations is achieved from this close relationship with them, which in turn can be achievable through innovative marketing tools and actions.
Despite the prevailing views showing the advantage of SFSCs over long ones, this form of sales still has its opponents and is treated rather as a supportive solution, due, for example, to its costs of transportation disproportionate to the scale of production (Raftowicz et al. 2020 ). Moreover, a lot of barriers emerge concerning the operationalization of SFSCs. For instance, Hyland et al. ( 2019 ), through the Short Supply Chain Knowledge and Innovation Network (SKIN) EU horizon 2020 project, revealed that a lot of difficulties are evident in terms of the regulation of farmers’ activities: restrictions on what they can sell in their on-farm shops, the burden of compliance with food hygiene laws, and marketing side of their business.
Despite their potential, a review of available studies indicates a certain limitation of research studies on SFSCs (Raftowicz et al. 2020 ). There are particularly few empirical studies that focus on the opinions held by the different SFSCs promotors, particularly in Portugal.
Hence, taking into account this gap, based on a case study, this research aims to identify and discuss the SFSC movement in the Centre of Portugal, particularly in the Viseu Dão Lafões Region (VDLR). This case study is based on the collection and organization of information of SFSCs that allowed us to identify and build a database of SFSCs in the region. Additionally, in order to understand feelings and behaviours of promotors of SFSHs, particularly promotors of agrifood baskets, this information was complemented with 5 interviews with them.
We have selected the VDLR as the study region since it is a predominantly rural and remote region (Naldi et al. 2015 ). Here, agriculture is still an important activity, both economically and socially (Pato 2012 ).
The paper consists of five parts. After the introduction (Section 1 ), Section 2 covers the review of the Local Production concept, SFSCs, and other related issues. The study design is explained in Section 3 , while Section 4 presents the qualitative study. In the Discussion section (Section 5 ), results are discussed and interpreted in accordance with previous studies. In the Conclusion (Section 6 ), the study´s main results are presented, the limitations are pointed out, and possible areas for future research are suggested as well.
2 Local production and short food supply chain: A diverse movement
2.1 meanings and benefits of sfscs.
In many countries around the world, short food chains are appearing and resurging with the aim of proposing a different possibility to the mainstream food market by promoting an exchange between producers and consumers, that is as direct and local as possible (Matacena and Corvo 2019 ). The aforementioned SKIN EU 2020 project [1] aims at stimulating the creation of a collaborative innovation network in different EU agriculture sectors through the improvement of knowledge and good practices exchange among farmers, research centres, practitioners, and citizens involved in SFSCs (Hyland et al. 2019 ).
This new perspective has gradually increased over the present century following broader debates on ‘alternative food chains’ (Ilbery and Maye 2005 ), ‘alternative food networks’ (Barberaa and Joselle 2016 ; Goszczynski 2016 ; Mastronardi et al. 2019 ; Goszczyński and Wróblewski 2020 ), ‘sustainable food chains’ (Smith 2008 ; Knorr et al. 2020 ), or ‘localized agrifood systems’ (O’Neill 2014 ; Mantino and Vanni 2018 ), among other related concepts.
Even though it is difficult to exhaustively identify the phenomena that fall within the designations of all these alternative/sustainable/or localized agrifood systems, geographical proximity and/or the location are crucial features of food provision. Thus, it is understandable that a supply food chain is considered short when the geographic distance between the farm and the consumer is perceived as short and/or when the number of intermediaries between the producer and the consumer is limited (one being the ideal number) (Kebir and Torre 2013 ). In other words, SFSCs are defined as all processes that seek to change the location of the product in time and space, along with information shaping and optimizing these processes (Raftowicz et al. 2020 ), including physical and social distance (Galli and Brunori 2012 ; Aubry and Kebir 2013 ) (see Figure 1 ).

The meaning of “Short”. Source: Adapted from Galli and Brunori ( 2012 ).
In this social relationship between the producer and the consumer, information exchanged includes details about the origin, production method, and sustainability of the product, and also about the identity, values, and ethics of both actors taking part in the process (Galli and Brunori 2012 ). Generating closer relations between producers and consumers is indeed a fundamental aspect of the potential endogenous (rural) development dynamics of SFSCs (Aubry and Kebir 2013 ). In other words, SFSCs can increase sustainability in all its dimensions: environmental, social, economic, and well-being, as referred in several studies (see Figure 2 ).

Sustainability of SFSCs. Source: Adapted from Galli and Brunori ( 2012 ).
As for environmental sustainability, SFSCs are important to minimize the use of fossil fuel or packaging and to increase the adoption of pesticide-free or less intensive methods of production (Galli and Brunori 2012 ; Aubry and Kebir 2013 ; Tibério 2013 ). As for social sustainability, the relationship between producers and consumers (often direct) has reinforced the fairness and trust-based relations among the actors who are involved in these food chains (Ilbery and Maye 2005 ; Aubry and Kebir 2013 ). Moreover, as referred by Drejerska et al. ( 2019 ), using social media farmers and other promotors of SFSCs can also communicate their social responsibility.
Their contribution to the creation of jobs and income in rural areas, as many small farmers do not have easy access to large commercial channels due to the inconsistency in their supply in terms of volume and/or continuity, also emphasizes the role played by SFSCs in the economic sustainability of the region (Galli and Brunori 2012 ; Tibério 2013 ; Zirham and Palomba 2016 ). Testa et al. ( 2020 ), for instance, state that alternative food networks could represent a strategy to increase the profitability of many small and medium-sized farms (organic and non-organic), particularly in an increasingly global and diversified market.
Last but not the least, SFSCs have increased knowledge and concern about food among consumers and led to the adoption of healthier diets and health and well-being sustainability (Cohen et al. 2012 ; Galli and Brunori 2012 ).
2.2 Boundaries and forms of SFSCs
The types and boundaries of such SFSCs vary. Regulation 1305/13 of 17 December focuses on the support for rural development between 2014–2020 and reports measures for the implementation of food chain organization and, in particular, of short supply chain. It defines a supply chain as being the one that involves ‘a limited number of economic operators, committed to cooperation, local economic development, and close geographical and social relations between producers, processors and consumers’ (article 2, m).
In Portugal, for instance, the Portuguese Ministério da Agricultura, Florestas e Desenvolvimento Rural , through the Ordinance no. 152/2016 of 25 May, refers that there shouldn’t be more than one intermediary in this whole process. In fact, in Portugal, a short supply chain is the ‘supply circuit that do not involve more than one intermediary between the producer and the consumer’ (article 4, b).
However, shortness is in this context usually related to the ‘local’ scale (Kebir and Torre, 2013 ); other authors have given ideal limits. For instance, Aubry and Chiffoleau ( 2009 ) mentioned that SFSCs can be identified as ‘proximity’ or ‘local’ when they are limited to a reduced geographical radius (80 km).
For that reason, it is not surprising that SFSCs may vary in nature and practise and exist all over the world in a wide variety of forms, even in both non-commercial and commercial settings (Aubry and Kebir 2013 ). Commercial forms often include: direct selling in farmers’ shops or at farmers’ markets, box schemes, internet selling, consumer cooperatives, etc. (Galli and Brunori 2012 ; Tibério 2013 ). Today, authors distinguish ‘old’ forms of short supply chains (farmers market, on-farms selling, etc.) from others which are more innovative (box schemes, community-supported agriculture forms, pick-your-own, etc.) (Delfosse and Bernard 2007 ).
producers’ markets – the market is reserved for agricultural and agrifood producers; the products sold are exclusively produced in-house and have an identified origin;
bio-producers’ market – the market is reserved for agricultural and agrifood producers certified with organic production; it’s a public access place where producers only sell organic products; the products sold are exclusively produced in-house and have also an identified origin;
local products fairs – spaces where producers can sell a local product or different products that are somehow related and that are in many cases the main channel through which those products are sold;
collective points of sale – a commercial space where agriculture or agrifood producers organize themselves to sell their products directly to consumers;
agrifood product baskets or box schemes – direct, local, and seasonal sale of diversified agrifood products (selected by the consumer), with regular delivery (weekly, biweekly, monthly, etc.) in a place previously agreed between the producer and the consumer (consumer’s home, company headquarters, cooperatives, stores, etc.). In this form, the consumer has the possibility to choose the products to be included in the basket.
The development of these forms of SFSCs is challenging and improves the production and consumption system in many aspects: technically (diversification of farm production and new forms of product delivery, etc.), socio-institutionally (emergence of new actors and network structures), and territorially (scales articulation, proximity/distance relationships, relocation processes, etc.) (Aubry et al. 2012 ). They enhance knowledge development both from the supply side and consumer side – communication ability, organizational skills, consumers’ knowledge of food and of their region, etc. (Kebir and Torre 2013 ). For instance, it is now widely accepted that communication ability, particularly new information and communication technologies (ICTs), and improvements in supply logistics management have an important role in increasing the competitive potential of each form of SFSCs and in the development of entire food economic sector (Schimmenti et al. 2012 ).
3 Materials, methods, and the study region
3.1 material and methods.
To carry out the empirical survey, an instrumental case study approach was adopted. As a research strategy, the case study is used in many situations to contribute to the knowledge of individual, group, organizational, social, and related phenomena (Yin 2003 ). Case study is the preferred research method when ‘how’ or ‘why’ questions are being asked (Yin 1984 , 2014 ) and when the topic under study is something dynamic and not static (Chetty 1996 ).
The case study implies the use of diverse information sources (Chetty 1996 ; Yin 2014 ). These include direct observation, documentation, interviews, and so on (Chetty 1996 ). Therefore, in order to identify SFSCs in the selected region in the first stage, a document analysis was conducted. Considering that the information on SFSCs was dispersed, we started with the information concerning SFSCs included in the Portuguese Rede Rural Nacional ( 2020a ) and complemented it with information found on the internet. Particularly, we consulted the web page of the municipalities of the VDLR and social networking websites of some local organizations/players (local associations, business associations, etc.). At the end of this step, we obtained a database with approximately 25 initiatives in the region (including producers markets, fairs of agrifood products, and promotors of agrifood baskets).
In a second stage, with the purpose to understand feelings and behaviours of promotors of SFSHs, particularly promotors of agrifood baskets, we developed a guideline for the semi-structured interview. It was based on the literature review conducted on SFSCs and includes questions related to: (i) motives; (ii) distribution of agrifood baskets; (iii) activity history and production profile; (iv) places of distribution, distribution periodicity, and communication; and (v) COVID-19 and demand (see Appendix 1).
The third stage involved the application of the interview. Between 15 July and 5 August 2020, based on the information gathered on agrifood promotors’ products baskets in the VDLR, five interviews were conducted. These represent all the promotors that we identified in the previous stage.
Because of the COVID-19 pandemic situation, the interviews were conducted via telephone (2) or online (3). In order to identify the main discourse of the different agrifood products basket producers (AFBPs), the interviews were identified by numbers (1–5), recorded, and transcribed.
Finally, in the fourth stage, a content analysis of the data gathered from the interviews was performed. The purpose of this content analysis is to systematically transform a large amount of text into a very organized and concise summary of key results (Erlingsson and Brysiewicz 2017 ).
3.2 The study-case
This study focuses on the VDLR, a Portuguese Region located in the Centre of Portugal (see Figure 3 ). This 3,483 km 2 area comprises fourteen municipalities: Aguiar da Beira, Carregal do Sal, Castro Daire, Mangualde, Nelas, Oliveira de Frades, Penalva do Castelo, Santa Comba Dão, São Pedro do Sul, Sátão, Tondela, Vila Nova de Paiva, Viseu, and Vouzela (Pato 2019 ).

Localization of Viseu Dão lafões Region in Portugal, Source: INE ( 2015 ).
Viseu Dão lafões was selected as study region because it is a predominantly rural and remote region (Naldi et al. 2015 ). This remote and inland region is a disadvantaged region: in 2018, it was below the national average in terms of regional development indexes structured in three dimensions: competitiveness, cohesion, and environmental quality (INE 2020 ).
However, the territory shows great potential in terms of: (i) edaphoclimatic conditions that allow the production of a wide variety of agricultural products that may turn into an important source of income; and (ii) endogenous and traditional food products (DRAPC 2015 ). Agriculture is an important activity in the region, from both economic and social perspectives (Pato 2012 ). Here, many traditional agrifood products (e.g. ‘vinho do Dão,’ ‘maçã Bravo de Esmolfe,’ etc.) represent important factors of regional identity (Pato 2012 ) that can be used to foster the expected rural development.
4.1 Initiatives of SFSCs in VDLR
As it is seen in Table 1 , virtually all the municipalities included in the VDLR have developed some kind of initiatives related to SFSCs. Municipality markets are the initiatives with greater exposure in the region.
Producers markets and fairs of agrifood products in the Viseu Dão Lafões Region
Source: our source.
In fact, most of the 14 municipalities of the region have local markets (Aguiar da Beira, Carregal do Sal, Oliveira de Frades, and Vila Nova de Paiva are the exceptions). The periodicity of these markets varies: some take place on a daily basis (see in Table 1, the cases of Castro Daire and Tondela) and others happen at least once a week (see in Table 1, the cases of Nelas, Penalva do Castelo, and Sátão).
In addition to municipality markets, there are other producers’ markets initiatives such as ‘the traditional and familiar agriculture market’ in S. Pedro do Sul and the ‘Ao sabor,’ producers market in Tondela. Those are initiatives that bring producers and consumers together. As it happened in the aforementioned cases, the key actors who are responsible for implementing those markets are a group composed of local stakeholders, farmers, and municipalities brought together by the idea that local producers and local food have to be given greater importance, as emphasized in other works (e.g. Šūmane 2013a ; Šūmane 2013b ). [2] [3]
The VDLR has also some notable examples of local and agrifood product fairs. The ‘Maçã Bravo de Esmolfe’ fair with its 24 editions and the ‘Vinho do Dão’ fair with 28 editions in 2019 are two of the oldest fairs of the region where people can find traditional products.
In addition to producers markets and agrifood product fairs, baskets of agrifood products are increasingly becoming a reality in the VDLR. Five initiatives involving agrifood product baskets (see Table 2 ) are currently taking place in those municipalities.
Baskets of agrifood products
In four of them, the basket is mainly composed of vegetables and fruit and in one of them it includes vegetables, fruit, wine, meat, and honey.
4.2 Distribution of agrifood baskets – A growing tendency
All the respondents in this analysis own a farm production. So, the distribution of agrifood baskets is a natural extension of their activity, whether for the sake of survival and profitability or simply for the sake of making the best of their production surplus.
“ For the company to be viable and to survive we had to think about the distribution part as well ” (AFBP, 3).
“(…) it was because of the production surplus that we had. Instead of throwing it away or using it to feed the farm animals, we decided to take advantage of that production surplus (…)” (AFBP, 5).
It is also interesting to note that behind these reasons, there is also a strong desire to know the consumer and establish a closer relationship with him:
“ (…) there is nothing better than meeting our customers. It is not like using carriers and never getting to know our customers. And they never get to know us either. At least that way we show up and it’s a vote of confidence ” (AFBP, 4).
The agricultural products baskets offered by the five respondents came from an organic production (in four cases) or from a more ‘natural’ and more environmentally friendly production (in one case). The demand for those products has been increasing over the years because for more and more people they represent a healtier and more environmentally friendly production. The following expressions clearly illustrate this position:
People are more aware of the problems affecting industrial meat. There are many films on the problems involving industrial meat (…) this initiative is making a difference (…) (AFBP, 2).
Demand has increased (…). We started with one basket and presently we deliver 25 baskets every week and there are other customers who want our products (…) (AFBP, 5).
It is also worth noting that one of the respondents started selling his baskets of agrifood products during the period of the COVID-19 pandemic and that another respondent started to add vegetables and fruits to the basket (initially composed solely of meat) also during this pandemic period. According to these two respondents, they began this ‘new distribution’ due precisely to the growing demand felt at that time:
Because of the quarantine, people could not leave their house. And then we talked at home, and we thought it would be a good idea to start delivering baskets (…). Then we started receiving messages from people who wanted baskets of agrifood products (AFBP, 4).
I’ve always had organic meat and I’ve been delivering meat for 10 years now. But in March there were many customers who asked if I had anything other than meat because they wouldn’t go to the stores (AFBP, 2).
All the respondents agree that the present COVID-19 pandemic has increased the importance and demand for local productions, particularly for agrifood baskets.
Demand skyrocketed (…) the baskets delivery doubled. And it doesn’t increase more because I don’t have enough products right now. I am unable at this time to satisfy more customers (…) (AFBP, 1).
During the pandemic there was greater demand because people wanted to get the products at home and did not want to leave their house… (AFBP, 3).
We started delivering in the city. In the meantime, we started to receive messages from other locations (…) and now we are already covering quite a few kilometers. And so we had to start using two vans to deliver the products. One was going to one area and the other was covering another area (AFBP, 4).
Considering the apparent growth of consumer baskets sales, which went on even after the confinement period, there is an increased recognition that the actual crisis of COVID-19 in addition with food insecurities has changed some consumers’ buying habits with regard to agrifood products: (…) now people can go to stores again (…) but still they keep ordering from me (AFBP, 2). Of course, this is happening because consumers are super-satisfied (AFBP, 4) with organic and/or more natural agrifood products.
In fact, the consumer gets more freshness and flavour and establishes a trust-based relationship with the producer: the consumer feels more confident. He knows he will get more freshness. It gets higher quality products . So, that’s it (AFBP, 3).
Additionally, and despite its reduced scale, this movement of demand for these types of products has an impact on local and traditional production:
(…) once we saw how demand was increasing, we looked for other farmers in my village to join us in our food basket initiative. And now there are 5 of us (AFBP, 5).
(…) it’s our duty to help local producers (AFBP, 2).
Despite this growth in SFSCs, it should be noted that little effort has been made to improve marketing and communication. In fact, information related to local fairs, producers markets, and particularly to agrifood baskets is (quite) scarce. None of these initiatives are well-advertised. There are very few websites that used to promote the products and, where they do exist, those are often outdated. One of the respondents chose not to advertise his products and he justifies this position by saying that right now he is unable to supply the needs of more consumers, so advertising his food baskets on the internet is clearly unjustified (SFSC, 1).
Besides, word of mouth seems to be the strategy that best serves the initiative and the products they want to sell: “ (…) nothing better than word of mouth (AFBP, 5).
5 Discussion
The VDLR has developed multiple SFCSs initiatives. Municipality markets are the initiatives with greater visibility in the region. These are managed by the municipality and mainly formed by small farmers and local inhabitants who seek to sell their production surplus. This sort of markets is a source of financial income for the producers and provides a face to face contact in which a consumer buys directly from the producer, which is extremely important to increase costumer loyalty and confidence in local production (Galli and Brunori 2012 ; Reina-Usuga et al. 2020 ).
Local fairs have also brought along important gains, not only for producers and consumers, but also for the whole region itself. Not only do they allow producers to sell a large part of their products and increase sales volume and incomes, but they also attract visitors and tourists. This increase in visitors has boosted the development of local activities related to handicraft, gastronomy and tourism and helped promote the culture and identity of the region (Meneses et al. 2007 ; RRN 2020b ). In fact, in SFSCs, sharing the place of production suggests sharing reputation and quality, which is twofold: the product gains reputation if the region is renowned (Sellitto et al. 2018 ); or the region gains prestige and notoriety when their products create reputation (Carbone 2017 ).
Environmental: resulting from the adoption of an organic or more natural agriculture. Four of the producers of agrifood baskets grow their products organically, whereas in one case the products are not organically certified, but the respondent tries to delivery more ‘natural’ (with the use of less chemical products). At the same time, with local distribution, the needs for transport, packaging, and refrigeration tend to be lower and there is a decrease in the use of fossil fuels and in the emissions of air pollutants.
Economic: by valuing local production and providing extra income for small local farmers. In this study, at least three of the respondents use the production of small local farmers (from the same parish or adjacent parishes).
Social-cultural: by increasing the relationship and confidence between producers and consumers. This applies to all the agrifood baskets producers who were interviewed. On the one hand, agrifood baskets make it possible to preserve plant and animal production systems, and on the other hand, they promote the cohesion of rural communities, since the initiative unifies several local farmers who work together to produce the food baskets.
Health and well-being: by contributing to the adoption of a healthier diet, since the agrifood baskets come from an organic or more ‘natural’ production (that is, the use of chemicals is reduced to a minimum).
However, in order to increase these benefits for producers, consumers, and for the territory as a whole, on the one hand, special attention should be given to communication and promotion used. As a matter of fact, websites, newsletters, designed packaging, and direct communication or information on the producer or the farm (pictures, news, etc.) are essential to emphasize the proximity relation (Kebir and Torre 2013 ). The dissemination of ICTs has remarkably changed the way producers and consumers communicate and interact. Using ICTs, consumers can visualize the products they want to buy and their characteristics and choose and order them carefully and safely. From the supply side, virtualization and internet can be a powerful approach to manage this relationship because it enables supply chains to monitor, control, plan, and optimize the business processes (Verdouw et al. 2016 ).
On the other hand, the empowerment and support of all stakeholders, from production to consumption, including the role of civil society organizations, public institutions, and academia, are essential (Raftowicz et al. 2020 ; Reina-Usuga et al. 2020 ). Thus, learning spaces and the adaption of social solutions to collectively minimize difficulties and solve problems must be promoted (Sonnino et al. 2016 ).
6 Conclusion and paths for future research
Despite the increasing interest attached to local productions and SFSCs, research in the area is still scarce (Raftowicz et al. 2020 ), particularly in Portugal. Therefore, taking as the study region the VDLR in Portugal, an empirical research was conducted. This research makes some important contributions to the existing knowledge. First, it underlines the importance of local production and SFSCs for producers, consumers, and for the whole territory of VDLR. For consumers, this tendency has brought along some health and social benefits and has contributed to their well-being. Moreover, the current crisis caused by the COVID-19 pandemic has emphasized the importance of SFSCs since these initiatives have partially helped overcome people’s fears and uncertainties in relation to products that come from outside their comfort zone (Cappelli and Cini 2020 ; Pato 2020 ). For producers, the reinforcement of this local micro-economy is also useful in a period of crisis and turbulence, since it betters their chances of employment and, therefore, improves their quality of life.
For the VDLR, the adoption of an organic or more natural agriculture has led to the preservation of the environment and of its resources, and the products obtained are instrumental in promoting a sense of rural identity.
Second, it shows that in the VDLR, some forms of SFSCs (particularly agrifood baskets initiatives) are still at an early stage of development as opposed to some other regions (Teixeira 2017 ). These are essentially developed, thanks to the will and energy of some local producers. However, the interviews conducted with them have also exposed a (certain) limitation in terms of communication and marketing that may constraint these initiatives.
From a practical point of view, it became clear that producers must do their best to develop their communication and marketing strategies in order to promote these initiatives; from a political point of view, local authorities should provide the necessary assistance they need to keep on developing their action (Pato 2020 ). This support is fundamental to promote knowledge exchange and better training for the producers and consumers involved in SFSCs, especially in areas that require marketing, promotion, and communication skills (Kneafsey et al. 2013 ). Without the necessary policy support, some rural businesses will be forced to close down, thus endangering a critical component of rural life (Pato and Teixeira 2018 ).
Naturally, this study has its limitations. It had to deal with time constraints that made it difficult for researchers to analyse the role played by other SFSC actors, like all those who are involved in the producers markets and even other possible promotors of agrifood baskets. So, a possible path to be explored in future research studies would be to extend research to other actors who are part of different SFSC initiatives developed in the region. Another interesting line of research would be to try to understand the kind of perception consumers have of SFSCs.
Acknowledgement
This work is funded by National Funds through the FCT - Foundation for Science and Technology, I.P., within the scope of the project Refª UIDB/00681/2020. Furthermore, we would like to thank the CERNAS Research Centre and the Polytechnic Institute of Viseu for their support.
Conflict of interest : Authors declare no conflict of interest.
[1] Aubry C, Chiffoleau Y. Le développement des circuits courts et l’agriculture périurbaine: Histoire, évolution en cours et questions actuelles. Innov Agronomiques. 2009;5:53–67. Search in Google Scholar
[2] Aubry C, Kebir L. Shortening food supply chains: A means for maintaining agriculture close to urban areas? The case of the French metropolitan area of Paris. Food Policy. 2013;41:85–93. 10.1016/j.foodpol.2013.04.006 Search in Google Scholar
[3] Aubry C, Kebir L, Pasquier C. Le raccourcissement des circuits alimentaires: Une nouvelle ruralité en périphérie des villes? (étude de cas en Île-de-France). In: Papy F, editor. Nouveaux rapports à la nature dans les campagnes. Versailles: Editions Quæ; 2012. p. 55–69. 10.3917/quae.papy.2012.01.0055 Search in Google Scholar
[4] Barberaa F, Joselle D. Building alternatives from the bottom-up: The case of alternative food networks. Agric Agric Sci Procedia. 2016;8:324–31. 10.1016/j.aaspro.2016.02.027 . Search in Google Scholar
[5] Cappelli A, Cini E. Will the COVID-19 pandemic make us reconsider the relevance of short food supply chains and local productions? Trends Food Sci Technol. 2020;99:566–7. 10.1016/j.tifs.2020.03.041 . Search in Google Scholar PubMed PubMed Central
[6] Cappelli A, Cini E, Guerrini L, Masella P, Angeloni G, Parenti A. Predictive models of the rheological properties and optimal water content in doughs: An application to ancient grain flours with different degrees of refining. J Cereal Sci. 2018;83:229–35. 10.1016/j.jcs.2018.09.006 Search in Google Scholar
[7] Carbone A. Food supply chains: Coordination governance and other shaping forces. Agric Food Econ. 2017;5(3):1–23. 10.1186/s40100-017-0071-3 Search in Google Scholar
[8] Chetty S. The case study method for research in small-and medium-sized firms. Int Small Bus J. 1996;15(1):73–85. 10.4135/9781473915480.n71 Search in Google Scholar
[9] Cohen JN, Gearhart S, Garland E. Community supported agriculture: A commitment to a healthier diet. J Hunger Environ Nutr. 2012;7(1):20–37. 10.1080/19320248.2012.651393 Search in Google Scholar
[10] Delfosse C, Bernard C. Vente directe et terroir. Méditerranée. 2007;109:23–9. 10.4000/mediterranee.108 Search in Google Scholar
[11] DRAPC. Delegação de Viseu O território Agrícola. Retrieved from https://www.drapc.gov.pt/base/documentos/debates_deleg_viseu_2015_vf.pdf; 2015. Search in Google Scholar
[12] Drejerska N, Gołębiewski J, Fiore M. Social media for interactions with customers within the short food supply chain: The case of the SKIN project. Stud Agric Econ. 2019;121:94–101. 10.7896/j.1908 . Search in Google Scholar
[13] Duarte F. Consumo alimentar: Regresso ao passado?. In: Santos JL, Carmo Id, Graça P, Ribeiro I, editors. O Futuro da Alimentação: Ambiente, Saúde e Economia. Lisboa: Fundacação Calouste Gulbenkian; 2013. p. 123–39. Search in Google Scholar
[14] EC. EU trade in food. Retrieved from https://ec.europa.eu/eurostat/web/products-eurostat-news/-/EDN-20171016-1?inheritRedirect=true; 2017. Search in Google Scholar
[15] Erlingsson C, Brysiewicz P. A hands-on guide to doing content analysis. Afr J Emerg Med. 2017;7(3):93–9. 10.1016/j.afjem.2017.08.001 . Search in Google Scholar PubMed PubMed Central
[16] Fiore M. Direct selling in the wine sector: Lessons from cellars in Italy’s Apulia region. Br Food J. 2016;118(8):1946–54. 10.1108/BFJ-05-2016-0201 . Search in Google Scholar
[17] Galli F, Brunori G. Short food supply chains as drivers of sustainable development. Evidence document. Document developed in the framework of the FP7 project FOODLINKS (GA No. 265287). Pisa PI: Laboratorio di studi rurali Sismondi; 2012. Search in Google Scholar
[18] Goszczynski W. Bridging food studies. East Eur Countrys. 2016;22(1):261–70. 10.1515/eec-2016-0013 . Search in Google Scholar
[19] Goszczyński W, Wróblewski M. Beyond rural idyll? Social imaginaries, motivations and relations in Polish alternative food networks. J Rural Stud. 2020;76:254–63. 10.1016/j.jrurstud.2020.04.031 . Search in Google Scholar
[20] Hyland J, Crehan P, Colantuono F, Macken-Walsh Á. The significance of short food supply chains: Trends and Bottlenecks from the SKIN thematic network. Stud Agric Econ. 2019;121:59–66. 10.7896/j.1904 . Search in Google Scholar
[21] Ilbery B, Maye D. Alternative (Shorter) food supply chains and specialist livestock products in the Scottish–English borders. Environ Plan A: Economy Space. 2005;37(5):823–44. 10.1068/a3717 . Search in Google Scholar
[22] INE. NUTS 2013 As novas unidades territoriais para fins estatísticos. Lisboa: INE; 2015. Search in Google Scholar
[23] INE. Indice Sintético de Desenvolvimento Regional. Retrieved from https://www.portugal2020.pt/content/indice-sintetico-de-desenvolvimento-regional; 2020. Search in Google Scholar
[24] Kebir L, Torre A. Geographical proximity and new short supply food chains. In: Lazzeretti L, editor. Creative industries and innovation in europe: Concepts, measures. New York: Routledge; 2013. p. 194–211. Search in Google Scholar
[25] Kneafsey M, Venn L, Schmutz U, Balázs B, Trenchard L, Eyden-Wood T, et al. Short food supply chains and local food systems in the EU. A state of play of their socio-economic characteristics. Seville: European Commission, Joint Research Centre, Institute for Prospective Technological Studies; 2013. Search in Google Scholar
[26] Knorr D, Augustin MA, Tiwari B. Advancing the role of food processing for improved integration in sustainable food chains. Front Nutr. 2020;7:34. 10.3389/fnut.2020.00034 . Search in Google Scholar PubMed PubMed Central
[27] Mantino F, Vanni F. The role of localized agri-food systems in the provision of environmental and social benefits in peripheral areas: Evidence from two case studies in Italy. Agriculture. 2018;8(8):120. 10.3390/agriculture8080120 . Search in Google Scholar
[28] Mastronardi L, Marino D, Giaccio V, Giannelli A, Palmieri M, Mazzocchi G. Analyzing alternative food networks sustainability in Italy: A proposal for an assessment framework. Agric Food Econ. 2019;7(1):1–19. 10.1186/s40100-019-0142-8 . Search in Google Scholar
[29] Matacena R, Corvo P. Practices of food sovereignty in italy and england: Short food supply chains and the promise of de-commodification. Sociologia Ruralis. 2019;60:414–37. 10.1111/soru.12283 . Search in Google Scholar
[30] Meneses BUL, Rico González M, González-Andrés F. The contribution of agrifood fairs to rural development: The Castilla and Leon region in Spain case study. Econ Rural Dev. 2007;3(2):22–7. Search in Google Scholar
[31] Mundler P, Laughrea S. The contributions of short food supply chains to territorial development: A study of three Quebec territories. J Rural Stud. 2016;45:218–29. 10.1016/j.jrurstud.2016.04.001 . Search in Google Scholar
[32] Naldi L, Nilsson P, Westlund H, Wixe S. What is smart rural development? J Rural Stud. 2015;40:90–101. 10.1016/j.jrurstud.2015.06.006 . Search in Google Scholar
[33] O’Neill K. Localized food systems – What role does place play. Regional Stud Regional Sci. 2014;1(1):82–7. 10.1080/21681376.2014.904596v Search in Google Scholar
[34] Pato L. Dinamics of rural tourism – impacts concerning rural development. PhD thesis. Aveiro: University of Aveiro; 2012. Search in Google Scholar
[35] Pato L. Comunicacão em turismo rural e línguas estrangeiras entre o desejado e a realidade. Millenium J Education, Technologies, Health. 2019;2(4):11–20. 10.3390/su12072934 . Search in Google Scholar
[36] Pato L. A (crescente) ênfase nos produtos agrícolas e agroalimentares produzidos localmente Os efeitos da Pandemia COVID-19 nos circutos curtos de proximidade. Paper presented at the 27th APDR Congress Sustainable management of the Sea for Sustainable Regional Development, 10–11 September, Angra do Heroísmo, Terceira, Azores; 2020. Search in Google Scholar
[37] Pato L, Teixeira AAC. Rural entrepreneurship: The tale of a rare event. J Place Manag Dev. 2018;11(1):46–59. 10.1108/JPMD-08-2017-0085 . Search in Google Scholar
[38] Pinto AS. A agricultura portuguesa está viva e recomenda-se. In: Santos JL, Carmo Id, Graça P, Ribeiro I, editors. O Futuro da Alimentação: Ambiente, Saúde e Economia. Lisboa: Fundacação Calouste Gulbenkian; 2013. p. 106–11. Search in Google Scholar
[39] Raftowicz M, Kalisiak-Medelska M, Stru´s M. Redefining the supply chain model on the milicz carp market. Sustainability. 2020;20(12):1–16. 10.3390/su12072934 . Search in Google Scholar
[40] Reina-Usuga L, Haro-Giménez T, Parra-López C. Food governance in territorial short food supply chains: Different narratives and strategies from Colombia and Spain. J Rural Stud. 2020;75:237–47. 10.1016/j.jrurstud.2020.02.005 . Search in Google Scholar
[41] RRN. CCA modalities. Retrieved from http://www.rederural.gov.pt/circuitos-curtos-agroalimentares/2016-06-01-13-32-37/conceito-de-circuito-curto-agroalimentar; 2020a. Search in Google Scholar
[42] RRN. Local products Trade Shows. Retrieved from http://www.rederural.gov.pt/circuitos-curtos-agroalimentares/2016-06-01-13-36-46/feira-de-produtos-locais; 2020b. Search in Google Scholar
[43] Schimmenti E, Vassiliadis E, Galati A. The role of information and communication technology and supply chain logistics management in competitiveness in the sicilian fruit and vegetable sector. Economia Agro-Alimentare. 2012;2:11–40. 10.3280/ECAG2012-002002 . Search in Google Scholar
[44] Sellitto MA, Vial LAM, Viegas CV. Critical success factors in short food supply chains: Case studies with milk and dairy producers from Italy and Brazil. J Clean Prod. 2018;170:1361–68. 10.1016/j.jclepro.2017.09.235 . Search in Google Scholar
[45] Smith BG. Developing sustainable food supply chains. Philos Trans R Soc. 2008;363:849–61. 10.1098/rstb.2007.2187 . Search in Google Scholar PubMed PubMed Central
[46] Sonnino R, Marsden T, Moragues-Faus A. Relationalities and convergences in food security narratives: Towards a place based approach. Trans Inst Br Geographers. 2016;41(4):477–89. 10.1111/tran.12137 . Search in Google Scholar
[47] Šūmane S. Case study – Ka dzi’: CSA Riga-Gulbene (Latvia). In: Galli F, Brunori G, editors. Short food supply chains AS drivers of sustainable development. Evidence Document. Document developed in the framework of the FP7 project FOODLINKS (GA No. 265287). Pisa PI: Laboratorio di studi rurali Sismondi; 2013a. p. 70–2. Search in Google Scholar
[48] Šūmane S. Case study – Straupe market of rural goods (Latvia). In: Galli F, Brunori G, editors. Short food supply chains as drivers of sustainable development. Evidence Document. Document developed in the framework of the FP7 project FOODLINKS (GA No. 265287). Pisa PI: Laboratorio di studi rurali Sismondi; 2013b. p. 66–9. Search in Google Scholar
[49] Teixeira FSL Circuitos Curtos Agroalimentares em Portugal: estudo de casos. Master thesis, Lisboa: ISCTE – Instituto Universitário de Lisboa; 2017. Search in Google Scholar
[50] Testa R, Galati A, Giorgio S, Crescimanno M, Trapani AMD, Migliore G. Are alternative food networks winning strategies to increase organic SMEs profitability Evidence from a case study. Int J Globalisation Small Bus. 2020;11(1):65–82. 10.1504/IJGSB.2020.10027241 . Search in Google Scholar
[51] Tibério L. Sistemas Agroalimentares Locais e Comercialoização em Circuitos Curtos de Proximidade. Rev da Rede Rural Nacional. 2013;3:6–9. Search in Google Scholar
[52] Verdouw CN, Wolfert J, Beulens AJM, Rialland A. Virtualization of food supply chains with the internet of things. J Food Eng. 2016;176:128–36. 10.1016/j.jfoodeng.2015.11.009 . Search in Google Scholar
[53] Wilkinson J. From fair trade to responsible soy: Social movements and the qualification of agrofood markets. Environ Plan A: Economy Space. 2011;43(9):2012–26. 10.1068/a43254 . Search in Google Scholar
[54] Yin RK. Case Study Research: Design and Methods. Thousand Oaks, CA, USA: Sage Publications; 1984. Search in Google Scholar
[55] Yin RK. Case Study Design and Methods. 3rd edn. Thousand Oaks, CA, USA: Sage Publications; 2003. Search in Google Scholar
[56] Yin RK. Case Study Research Design and Methods. 5th edn. Thousand Oaks, CA: Sage Publications; 2014. Search in Google Scholar
[57] Zirham M, Palomba R. Female agriculture in the short food supply chain: A new path towards the sustainability empowerment. Agric Agric Sci Procedia. 2016;8:372–7. 10.1016/j.aaspro.2016.02.032 . Search in Google Scholar
© 2020 Maria Lúcia Pato, published by De Gruyter
This work is licensed under the Creative Commons Attribution 4.0 International License.
- X / Twitter
Supplementary Materials
Please login or register with De Gruyter to order this product.
Journal and Issue
Articles in the same issue.

An official website of the United States government
The .gov means it’s official. Federal government websites often end in .gov or .mil. Before sharing sensitive information, make sure you’re on a federal government site.
The site is secure. The https:// ensures that you are connecting to the official website and that any information you provide is encrypted and transmitted securely.
- Publications
- Account settings
Preview improvements coming to the PMC website in October 2024. Learn More or Try it out now .
- Advanced Search
- Journal List
- Elsevier - PMC COVID-19 Collection

Food retail supply chain resilience and the COVID-19 pandemic: A digital twin-based impact analysis and improvement directions
In this study, we examine the impact of the COVID-19 pandemic on food retail supply chains (SCs) and their resilience. Based on real-life pandemic scenarios encountered in Germany, we develop and use a discrete-event simulation model to examine SC operations and performance dynamics with the help of anyLogistix digital SC twin. The computational results show that food retail SC resilience at the upheaval times is triangulated by the pandemic intensity and associated lockdown/shutdown governmental measures, inventory-ordering dynamics in the SC, and customer behaviours. We observe that surges in demand and supplier shutdowns have had the highest impact on SC operations and performance, whereas the impact of transportation disruptions was rather low. Transportation costs have spiked because of chaotic inventory-ordering dynamics leading to more frequent and irregular shipments. On bright side, we observe the demand growth and utilization of online sales channels yielding higher revenues. We propose several directions and practical implementation guidelines to improve the food retail SC resilience. We stress the importance of SC digital twins and end-to-end visibility along with resilient demand, inventory, and capacity management. The outcomes of our study can be instructive for enhancing the resilience of food retail SCs in preparation for future pandemics and pandemic-like crises.
1. Introduction
Epidemic outbreaks and associated pandemics are specific cases of supply chain (SC) disruptions as they can spread rapidly and disperse worldwide. Recent examples include SARS, MERS, Ebola, swine flu, and most recently, the novel coronavirus (COVID-19/SARS-CoV-2) ( Choi, 2020 , Govindan et al., 2020 , Ivanov, 2020a , Paul and Venkateswaran, 2020 , Queiroz et al., 2020 , Chowdhury et al., 2021 , El Baz and Ruel, 2021 , Sodhi et al., 2021 ). In this study, we analyse the pandemic impacts on food retail SCs in Germany.
The novel coronavirus, first reported in Wuhan, China, in December 2019, expanded rapidly worldwide and was first detected in Germany at the end of January 2020. A pandemic was then declared in March 2020. The COVID-19 outbreak has profoundly impacted human lives and economic activities worldwide, affecting global SCs across many industries by reducing access to markets and materials, leading to significant operational and financial impacts ( Dolgui et al., 2020b , Veselovská, 2020 , Choi, 2021 , Ivanov, 2021c , Nagurney, 2021 ).
Among others, SCs in the food industry have experienced unprecedented shocks during the COVID-19 pandemic ( Chowdhury et al., 2020 , Loske, 2020 , Singh et al., 2021 ). The crisis has also affected many different sectors in Germany, leading to drastic falls or spikes in demand. Hence, Germany’s Gross Domestic Product (GDP) decreased by 6% during 2020 compared to the previous year ( IMF, 2020 ). Retail workers have been significantly affected – many shops have been closed because of pandemic mitigation measures, and as other industries have slowed down, consumption of certain goods has declined. On the other hand, food retailers and grocery store workers have seen a surge in demand as people in confinement buy food and other necessities, often stocking up for long periods of isolation ( Chinn et al., 2020 , ILO, 2020 ). In this way, as the COVID-19 pandemic has advanced, particular attention has been given to food retailers. They have had to adapt quickly and respond to the crisis given their critical role in providing daily-life essentials ( Ivanov, 2020b , Ivanov and Dolgui, 2021a ).
Some of the most visible implications of the pandemic in the food retail industry have included panic buying, changes in food purchasing patterns, food deliveries and digital services, frontline hygiene and preventive measures, logistics and organization of distribution in stores, and supply-side issues due to labour shortages and disruptions to transportation and supply networks ( ILO, 2020 , PwC, 2020 , Rathore et al., 2020 , Ivanov, 2021b , Paul and Chowdhury, 2021 ). Limits on people’s mobility have reduced seasonal workers’ availability for planting and harvesting in many countries. For example, in the wake of the COVID-19 pandemic, many producers/suppliers could not harvest fruits in the UK primarily because of labour shortages, which led to large-scale food loss and waste (The Guardian, 2020 ).
Moreover, COVID-19 has led to disruptions in food processing industries, which have been affected by social distancing rules and other measures aiming to contain the spread of the virus, thus reducing operations’ efficiency. Similarly, bottlenecks in transport and logistics have disrupted the movement of products – which are transported using three main modes of transportation: bulk (ships and barges), containers (by boat, rail, or truck) and other road transport, and air freight – along SCs ( OECD, 2020 ). At the same time, according to Chinn et al. (2020) , food retail in Germany was able to seize new post-crisis opportunities. Thus, the food retail industry has not only faced structural challenges during the COVID-19 crisis, it has also grown during the crisis.
Despite the ongoing research on disruptions management associated with the COVID-19 pandemic, little is known about the impacts of the pandemic on food SCs, the reasons for these impacts, and the most promising directions for SC recovery. Moreover, the partial or even full shutdown of whole industry sectors and regions represents a novel and underexplored setting in SC resilience literature ( Ivanov and Das, 2020 ). While some research has examined the initial impact of the pandemic on food SCs ( Chowdhury et al., 2020 , Loske, 2020 , Singh et al., 2021 ), the existing literature lacks overarching insights based on real-life pandemic scenario analysis over a longer time scale that includes several pandemic waves and the associated disruptions and recovery phases ( Hosseini et al., 2019 , Aldrighetti et al., 2021 , Hosseini et al., 2020 , Ivanov, 2021a ). We have developed this study to close these research gaps.
We examine the impact of the COVID-19 pandemic on the food retail SCs. Based on real-life scenarios encountered in German food SCs during the COVID-19 pandemic, we have developed and used a discrete-event simulation model to examine the impact of the pandemic on SC operations and performance. Previous research has provided strong and substantial insights about how to evaluate, measure, and improve resilience in SCs using simulations ( Wilson, 2007 , Carvalho et al., 2012 , Ghadge et al., 2013 , Schmitt et al., 2017 , Macdonald et al., 2018 , Currie et al., 2020 , Ivanov and Dolgui, 2021a , Llaguno et al., 2021 ). For example, Olivares-Aguila and ElMaraghy (2020) have suggested an evaluation framework for SC resilience using system dynamics simulation. In the first phase, their SC simulation model is constructed and used to determine the SC performance in different scenarios. Then, potential disruptions and possible mitigation strategies and configurations are identified. Finally, the disruptions that have the most significant impact on the SC are proposed to build scenarios for analysis. However, neither this nor other works have captured the real-life pandemic scenarios in the food SC over a long period of time or considered two pandemic waves – distinct and substantial contributions made by our study.
Our study makes substantial contributions by uncovering the impact of the COVID-19 disruptions in a food retailer’s SC and providing guidelines for recovery actions. Our research outcomes can be instructive for developing SC actions to respond to COVID-19 disruptions and improve SC resilience in the food retail industry. Moreover, we provide generalized recommendations for SC stabilization and recovery that address our two research questions (RQ):
RQ1: How and why has the COVID-19 pandemic outbreak impacted food retail SC performance?
The purpose of this question is to analyse the impact of different COVID-19 disruption scenarios and identify concrete impacts on the operations and performance in food retailers’ SCs.
RQ2: How can food retail SC resilience be improved?
This question aims to identify SC actions in response to a pandemic that would increase food retailers’ SC resilience.
The rest of this paper is organized as follows: In Section 2 , the underlying case study, data sources, and simulation model are presented. Section 3 structures the pandemic scenarios for analysis. Our computational results are described in Section 4 . Section 5 is devoted to sensitivity analysis. In Section 6 , we discuss implications of the simulations and offer guidelines for resilience enhancement in future. Finally, in Section 7 , we conclude by summarizing the study’s major outcomes and delineating some future research directions.
2. Case study, data, digital twin, and simulation model
2.1. case study and data.
We used anyLogistix SC simulation and optimization software to study a multi-stage SC for a retail company in Germany. This software has been frequently and successfully used for SC resilience analysis ( Ivanov, 2017 , Ivanov, 2018 , Aldrighetti et al., 2020 , Dolgui et al., 2020a , Ivanov, 2021c ). Without loss of generality, we restricted ourselves to the consideration of ten product categories and 28 supermarket locations in five different countries (Germany, Austria, the Czech Republic, Italy, and Hungary). We selected product categories that experienced significant changes due to new consumer trends during the COVID-19 pandemic – Fresh Fruits, Fresh Vegetables, Fresh Meat, Fish & Sea Food, Rice, Pasta, Convenience Food, Frozen Meals (ready-to-eat), Wheat Flour, and Confectionary Food. Product demand was calculated by multiplying the annual per capita consumption for each product category by the retail company’s market share. The selling prices for each product were taken from Statista data regarding the average price for each product category in 2020.
Next, we created a sample of three suppliers per product category (30 suppliers in total) by analysing supermarket data and manually identifying supplier locations. Three distribution centre (DC) locations were selected, one in east, one in west, and one in south Germany. Fig. 1 shows the SC design.

Supply chain design (interface from anyLogistix Studio Edition).
The suppliers produce and ship their products via trucks to the DCs. We assumed that the costs of shipping the products are already included in the final price agreed with the retailer. Inventory spending corresponds to the expenses for replenishing the inventory. This is the sum of the initial inventory purchase costs and the replenishment costs. This cost is calculated by anyLogistix automatically for suppliers by multiplying initial stock units by the costs for the corresponding product.
2.2. Digital twin and simulation model
Digital SC twins are defined as ‘computerized models that represent the network state for any given moment in time’ ( Ivanov and Dolgui, 2021c ). The main difference between digital twins and simulation models is comprised of three aspects, i.e., system complexity , real-time connectivity , and decision-making integration . First, the system complexity in digital twins is higher as in simulation models. The digital SC twins are comprised of multiple layers such as network structure, flows, process control algorithms, and operational parameters. Second, data in the digital twins is updated through connectivity with external systems and databases. Third, integration of digital twins into decision-making is much higher as compared to models. Simulation and optimization models are important parts of digital twins whereby digital twins can offer more functions for decision-making support as classical offline modelling, e.g., performance analysis of suppliers, updating SC data in ERP systems, and comparison of the existing processes with the optimal ones. Digital twins allow for both computations of some numerical outcomes and an extended analysis of bottlenecks, comparison of different options, and analysis of resilience investments. A digital SC twin is a part of SC management toolbox, control towers, and decision-making support at strategic, tactical, and operational levels. Besides, data-driven modelling in digital twins allows using artificial intelligence in order to support decision-making by so called dispatch advisors or digital companions. For example, a decision-maker can ask the digital twin to find all current shortages in the SC and suggest possible ways to resolve these problems. In the next step, the shortage data can be used for optimization and simulation to develop most appropriate action plans.
Digital twins can be used for building end-to-end SC visibility, enhancing resilience, and assessing contingency plans. Cavalcante et al. (2019) point out that digital SC twins display the ‘physical SC based on actual transportation, inventory, demand, and capacity data’. Therefore, they can be utilized by decision-makers for planning, monitoring, and supervising. Hence, digital SC twins can improve SC visibility and, as a result, SC resilience. Ivanov and Dolgui (2020) and Hosseini et al. (2020) state that there is an urgent need to visualize SC networks because of the increasing number of SC disruptions.
Digital SC twins enable real-time transparency about important logistics data such as financial key performance indicators (KPIs), inventory level, stock level, service level, capacity, and transportation data. They are powerful data-driven tools and firms’ control towers. Performance-based simulation models help create efficient contingency plans to prevent or recover from disruptions by simulating and creating what-if scenarios that predict the future impact. Digital twins not only visualize SCs and associated risks but also offer supplier performance and risk analysis along with forecasts of SC interruptions and risks. In addition, they can allow to establish and examine detailed backup routes, including estimated time of arrival (ETA) calculations. During disruptions, digital twins utilize real-time data to calculate the impact of the disruption, build alternative SC networks and perform KPI analysis to get real-time data about inventory levels, service level, financial parameters and demand ( Ivanov, 2020a ). With the help of anyLogistix SC simulation and optimization software, a digital SC can be designed ( Fig. 2 ).

Digital supply chain design for disruption analysis using anyLogistix (based on Ivanov and Dolgui, 2021b ).
Fig. 2 shows the structure of a digital SC twin created in this study for disruption analysis. The digital SC twin encompasses three major perspectives– the network, the flows, and the parameters. The SC network can be designed using different location objects, such as customers, DCs, factories, and suppliers. The flows in the network can be flexibly arranged to represent the specifics of different SCs. The flows are associated with some design (i.e., maximum) capacities in production, warehouses, and transportation and controlled by the associated production, inventory, sourcing, and shipment policies. These policies can be flexibly adapted to the specifics of the SC and its management rules. Finally, different operational parameters such as demand, lead time, and control policies’ thresholds (e.g., re-order point, target inventory, and minimum vehicle load) can be defined. With that functionality, a digital model of a physical SC (i.e., a digital SC) can be created and used for optimization and simulations to analyse SC operations and performance dynamics under disruptions.
The simulation model structure developed in the anyLogistix digital twin is shown in Fig. 3 .

Simulation model design.
The simulation model is based on production-inventory control with five main components in the control loop ( Fig. 3 ): demand, lead time, continuous inventory control with a re-order point and a target stock setting, production control, and transportation control. It is assumed in this simulation that the DCs follow (s,S) inventory control policy. For this simulation, the re-order point(s) per product per DC equals the daily demand per product at each DC since the lead-time is less than 1 day. Similarly, the target inventory (S) corresponds to twice the value of the re-order point. The computation of target inventory (also known as the baseline stock) is a complex task subject to specific requirements (e.g., a dependence on some service level thresholds) and analysis objectives ( Chen and Disney, 2007 , Minner and Transchel, 2010 , Svoboda et al., 2021 )). In this study, we do not pretend to analytically determine optimal re-order points and target inventory for our system. The role of inventory control in our model is to enable dynamic simulation of the SCs. With that in mind, we rely on studies ( Ivanov, 2017 , Aldrighetti et al., 2020 ) that used as a target inventory the twice value of the re-order point. Inventory carrying costs for DCs is $0.22. It is assumed that suppliers have limited inventory. Therefore, an (s,S) inventory policy with the same replenishment logic for the DCs was applied.
The Expected Lead Time (ELT) for each order is 1 day. In other words, if the order is delivered within one day, it is considered on-time delivery. Otherwise, the order is counted as a delayed delivery. The delayed deliveries have a negative impact on the ELT service level (i.e., on-time delivery), which is defined as a ratio of on-time delivered orders to the total number of orders. The facilities have some processing costs, which can be classified as inbound and outbound costs. These costs correspond to the expenses incurred in receiving shipments from a supplying site and from sending shipments to a receiving site, respectively.
The pandemic is modelled by setting some disruption and recovery events for supply and capacities along with surges in demand. The results of the simulations are evaluated through the following KPIs (following studies by Ivanov, 2017 , Ivanov, 2018 , Singh et al., 2021 , Dolgui et al., 2020a ):
- ▪ Financial indicators : Statistics related to this group provide detailed information on generated revenue and incurred expenses during the simulation experiment for the specified scenario. They include profit, revenue, and costs (inventory carrying costs, transportation costs, inventory spending, inbound processing costs, outbound processing costs, and other costs).
- ▪ Expected lead time : It displays statistics on the delivery time of every ordered product item. It is updated each time a shipment containing the order is delivered (all delivered orders are considered whether they are on time or delayed).
- ▪ Average daily available inventory : It shows statistics on the daily integral mean of the available volume of products in stock.
- ▪ Demand (product backlog) : It illustrates the quantity of processed products for incomplete orders (orders that currently lack the required number of products).
- ▪ Fulfillment (late orders) : It shows statistics on the number of orders that failed to arrive within the specified ELT (e.g., the orders that are still being delivered after the ELT has expired).
- ▪ ELT service level by orders : It shows the service level based on the ratio of on-time orders to the overall number of outgoing orders.
We validated the model in several ways. First, we tested the model on the ideal (i.e., business-as-usual) scenario (see Fig. 5 ). Second, we compared the results of our simulations with statistical data for German retail in 2020, which confirmed the trends identified in our experiments (e.g., growing demand and increasing transportation costs). Third, we visually checked the dynamics of material flows through the simulations jointly with two retail SC managers, who confirmed the correlation between our simulation and performance dynamics and real-life settings. Fourth, we performed a set of variation experiments with different parameters (e.g., re-order point and demand). They confirmed the model’s sensitivity. The sensitivity analysis with individual parameters did not reveal any interesting or novel managerial implications, so we have omitted the presentation of these test computations and focussed on the managerial implications of our experimental results. However, another set of sensitivity analyses with consideration of time-to-recovery provided interesting insights which are discussed in Section 5 . Finally, we used the output data analysis in the log files and replication tests for the validity proof. We selected the timing of disruptions to avoid the ‘noise’ at the start of the simulation experiment.

Experiment description: Bottlenecks in transport.
3. COVID-19 pandemic scenarios
Our analysis aimed to investigate the impact of COVID-19 on German food retail SC performance. Therefore, different disruptions resulting from policies adopted to contain the spread of COVID-19 were examined. For analysis purposes, the timeline of the COVID-19 outbreak in Germany was used.
The first coronavirus case was reported in Germany in January 2020. By mid-February 2020, Germany’s COVID-19 cases had been contained. However, on 25 and 26 February, multiple cases were detected in the country, and the virus began spreading ( WHO, 2020 ). To contain the spread of the coronavirus, numerous restrictions to public life – including rules for reduced contact in daily life, the closing of non-essential businesses, and temporary border controls – were imposed.
In May 2020, an initial lifting of border controls, a gradual relaxation of the containment measures, and a return to public life started to occur. However, a second wave of increased coronavirus cases began around 20 October. A partial lockdown was imposed on 1 November and continued until the end of the year.
We created the following timeline as a guideline for the simulation experiments ( Deutschland.de., 2020 ) ( Fig. 4 ).

Timeline of simulation experiments following the real-life COVID-19 control dynamics Based on the timeline shown in Fig. 4 , we developed several simulation scenarios.
3.1. Scenario 0. Disruption-free (baseline) scenario
This simulation analyses the performance of the food retail SC in a scenario free of COVID-19 disruptions. We consider it as a baseline scenario. The results serve as a basis for comparing and analysing the food retail SC performance during COVID-19 pandemic-induced disruption events.
3.2. Scenario 1. Increase in demand
Four fixed periods that are distinct in demand are simulated ( Table 1 ).
Experiment description: Demand levels.
The demand disruptions belong to the most important vulnerabilities in SCs ( Shen and Li, 2017 ). The logic of this experiment is as follows. Base demand (i.e., 100%) corresponds to a business-as-usual scenario. This period corresponds to the beginning of 2020, when COVID-19 was not yet widespread in Germany. The base demand increase by 75% corresponds to the first lockdown period. It starts when the first restrictions on public life were imposed and ends when social distancing restrictions were relaxed and a slow return to public life began (following the timeline described above). During this period, panic buying increased the demand enormously in different product categories, which is reflected in our scenarios ( Paul and Chowdhury, 2021 ). Next, a period of 10% increase in the base demand is introduced. This period corresponds to the time when coronavirus control measures were relaxed. Finally, the third period of base demand increase (of 35%) corresponds to Germany’s second lockdown period, which impacted the demand to a lesser extent than the first lockdown. The objective of this scenario is to simulate the impact of increasing demand over the whole year. The results are analysed using the KPIs explained in Section 4.1 .
3.3. Scenario 2. Shutdown at suppliers’ factories
The pandemic has caused temporary shutdowns of factories, which in turn has resulted in a sharp decline in production. Limits on people’s mobility have reduced seasonal workers’ availability for planting and harvesting in many countries. In addition, food processing industries have been affected by social distancing rules and other measures aiming to contain the virus’s spread, which have reduced operations’ efficiency ( OECD, 2020 ). Thus, we simulate a shutdown at three factories (i.e., suppliers) to analyse the impact of their closure on food retailers. Table 2 shows the experimental setup for the event simulation and the period when the shutdown occurs.
Experiment description: Supplier’s factories shut down.
The shutdown period for each site is consistent with the German government’s period of restrictions to contain the coronavirus spread (explained in the timeline above). The objective of this scenario is to simulate the impact of closing the factories of two major suppliers during a fixed period of 10 days in March and one supplier’s factory during a 15-day fixed period in April.
3.4. Scenario 3. Bottlenecks in transport
Bottlenecks due to increased border controls are simulated in this experiment according to real-life scenarios encountered in spring 2020 ( BMI, 2020 ). Although no border closures for the transportation of goods were imposed, traffic jams at the border and long queues occurred because of the temporary border controls during the first lockdown in Germany. This limited the normal flow of transports into the country. Bottlenecks in transport due to border control delays are simulated for six different periods. This scenario simulates an interruption of material flows over a period of 2 days in each experiment. Fig. 5 shows the interrupted paths with their respective durations.
The disruption period for each route is consistent with the period during which the German government’s restrictions to stop the coronavirus spread were in effect, as explained in the timeline above. The purpose of this scenario is to simulate the impact of closing paths from suppliers to DCs and from DCs to customers during short periods of 2 days in March and April.
3.5. Scenario 4. COVID-19: Increase in demand, shutdown of suppliers’ factories, and transport bottlenecks
This scenario simulates the impact of COVID-19 on the food retail industry SC by combining scenarios 1, 2, and 3. This simulation aims to reflect the overall food SC performance during two pandemic waves in 2020.
4. Results and analysis
4.1. impact of covid-19 in germany’s food retail sc performance.
This section aims to respond to RQ1: How and why has the COVID-19 pandemic outbreak impacted food retail SC performance? This section presents the simulation results and analysis of the simulation experiments. First, the performance of a disruption-free scenario will be described. Subsequently, the disruption scenarios will be evaluated using four simulation experiments. Additionally, a cross-comparison analysis of the scenarios and generalizations of the COVID-19 impact in the food SC will be provided.
4.1.1. Scenario 0. Disruption-free (baseline) scenario
This section describes the SC performance of the food retail industry in Germany in a pandemic-free (i.e., baseline) scenario. Fig. 6 shows the simulation results.

Experiment results: Disruption-free (baseline) scenario.
Regarding Lead Time , Fig. 6 shows a histogram of the daily lead time, representing the delivery time for each product item ordered. The x-axis shows the lead-time in days, and the y-axis indicates the number of occurrences of orders with a particular lead-time. Products are delivered within a time interval of 0 and 12 h, but most of the products are delivered within a 2-hour timeframe. Thus, the customer’s ELT of 1 day is met for all product categories. This case suggests that lead times in the food retail industry are usually short because of recurring orders and high inventory rotation in DCs.
With respect to the Average Daily Available Inventory , the simulation outcome shows the inventory levels in DCs for all product categories. The order-up-to-level policy (s,S) allows ordering quantities up to level S when reaching the re-order point s . This policy prevents excessive inventory levels and shortages and considers some situational demand fluctuations. From the results, it is evident that there is enough stock availability from day 1 in all scenarios, which allows for high flexibility to match demand. Small fluctuations with low amplitude can also be seen for all products. Moreover, inventory levels do not fall to the 0 level during the year, which means that the inventory policy allows the retailer to satisfy demand across the SC.
Demand satisfaction can be measured in terms of Product Backlog , which indicates the number of processed products for orders that lack the required number of products. In Fig. 6 , a backlog of 0 can be observed, meaning that all orders are completely delivered.
Fulfilment (Late Orders) shows the number of orders that fail to arrive within the specified ELT. As the ELT is one day, every order delivered within a frame greater than 1 is considered a late delivery. In Fig. 6 , it can be seen that all products are delivered on time because the number of late orders is 0. Therefore, the number of on-time orders equals the total number of orders.
Finally, the ELT Service Level analyses the ratio of on-time orders to the overall number of outgoing orders. Hence, late deliveries have a negative impact on ELT service. Results show a service level of 1, which means that customers receive 100% of their orders without delays and within the expected lead time.
4.1.2. Scenario 1. Increase in demand
Scenario 1 shows the impact on the food SC performance after an increase in demand resulting from the COVID-19 pandemic outbreak. Fig. 7 illustrates the results for each KPI.

Experiment results: Increase in demand.
This scenario reveals that an increase in demand positively influences the revenues because a higher volume of products is sold, which increases the profits. Additionally, inventory levels decrease because of demand growth. Consequently, lead time increases, as well as the number of late orders, reducing the ELT service level. An increase in the product backlog can also be seen because of a rise in the number of incomplete orders.
Lead Time for most orders in scenario 1 is between 0 and 10 days. Under normal conditions, lead time is a maximum of half a day. Also, with a lower frequency, some orders can take up to 50 days to be delivered to the customer. It can be inferred from these results that as the demand increases, procuring the quantities required to meet it takes longer because the available inventory is insufficient to satisfy the growing demand. Delays in delivery occur until the stock is replenished. The results also show that the Average Daily Available Inventory dramatically decreases because of the increased demand. Fluctuations throughout the year can be seen in the ‘Average Daily Available Inventory’ graph in Fig. 7 . When demand increases by 75% (corresponding to Germany’s first lockdown), there is a sharp drop in inventory. Inventory levels do not recover to a level similar to that in the initial scenario throughout the year. On the other hand, during the second lockdown, a slight decrease in inventory can be seen for some product categories, but this decrease is not as abrupt as the decrease during the first lockdown. An increase in the demand for all products simultaneously over a relatively long period causes delays and unattended orders.
In addition, concerning the Product Backlog , the results show that orders are not completely delivered, and thus demand is not 100% satisfied. The ‘Demand (Product Backlog)’ graph in Fig. 6 shows a sharp increase in the product backlog during the first lockdown period, when demand for all products increases by 75% compared to their initial level (in the disruption-free scenario). Then, beginning on day 150 of the year, there is a decrease in the backlog as demand decreases compared to the first lockdown period but remains 10% higher than in a disruption-free scenario. An increase in the backlog appears again on day 300 – which corresponds to Germany’s second lockdown period – representing an increase in demand of 35% compared to its initial level. According to the simulation results, the accumulated backlog throughout the year is 32.1 million kg, while the total demand for all products is 1.157 trillion kg. Therefore, 2.7% of the total demand is not satisfied after an increase in demand due to the COVID-19 pandemic.
The results also indicate that when there is an increase in lead time, the Fulfillment (Late Orders) indicator is affected. In the ‘Fulfillment (Late Orders)’ graph in Fig. 7 , a growing line over time indicates the number of orders that are not delivered on time for all products in all customer locations. According to the results, 3,949 orders are delivered late throughout the year, representing 3.7% of the total number of orders placed by the customers.
Similarly, Fig. 7 shows that the ELT Service Level for all products is 100% from the start of the year until the beginning of the first lockdown period in mid-March. Then, the average service level falls to 87.2% and remains at this level throughout the rest of the year. The increasing number of late orders is the reason for these ELT service level dynamics.
4.1.3. Scenario 2. Shutdown in suppliers’ factories
Scenario 2 shows the impact on the food SC performance after a shutdown in suppliers’ factories due to the COVID-19 pandemic outbreak. We simulated a shutdown for three different product categories over periods of 10 and 15 days. This yielded the results depicted in Fig. 8 . According to these results, a temporary production shutdown at three suppliers’ factories slightly reduces profit as total costs increase. Moreover, a reduction in inventory levels at DCs occurs as suppliers stop delivering the products during the disruption period. Additionally, there is a high increase in inventory when the factories are reopened. This effect can be explained by disruption tails – that is, a destabilization of production-ordering dynamics in the post-disruption period due to a lack of adaptability in the production-inventory control policies when transitioning from the disruption to the recovery period ( Ivanov, 2019 , Ivanov and Rozhkov, 2020 ). Consequently, lead time (as well as the number of late orders) increases, which decreases the ELT service level over an extended period. Furthermore, the number of incomplete orders also grows, generating product backlog in some product categories.

Experiment results: Suppliers’ factories shutdown.
After an outage of products, incoming quantities accumulate in DCs. Thus, stock levels grow, causing an increase in inventory carrying costs. Also, during a supply outage, incomplete orders are transported from DCs to customers, decreasing the vehicle capacity utilization. Then, when products become available after the suppliers’ factories re-open, the number of trips escalates to deliver the missing quantities. Therefore, transportation costs increase. Inbound and outbound costs remain the same. Other administrative costs do not vary, as they are fixed costs. The ELT service level falls to an average of 88.2% as the minimum value and improves throughout the year, reaching a level close to 100% at the end of the year.
4.1.4. Scenario 3. Bottlenecks in transport
Scenario 3 shows the impact on the food SC performance of multiple transport bottlenecks due to the COVID-19 pandemic outbreak. Six bottleneck events are simulated for 2-day periods in different paths from suppliers to DCs and from DCs to customers. The results are depicted in Fig. 9 .

Experiment results: Bottlenecks in transport.
According to the results of scenario 3, transport bottlenecks have a small impact on profit performance. There is a minor reduction in inventory levels at DCs during the disruption as suppliers stop delivering the products within short time periods. Therefore, the number of late orders increases, although in minimal quantities compared to the total number of orders. Moreover, the number of incomplete orders rises but only slightly, resulting in a very low backlog. As a result, the service level remains close to 100% within the entire period, indicating demand satisfaction.
In terms of Fulfillment (Late Orders) , a growing line that stabilizes over time can be observed. 30 orders are delivered late throughout the year, representing approximately 0.03% of the total number of orders placed (102,280). Finally, the ELT service level is approximately 100% during the whole period. This number can be explained by the small number of late deliveries as most orders were delivered on time. Thus, the demand during the year is satisfied overall despite the transport disruptions.
With regard to scenario 3, we can conclude that the magnitude of the disruption impact is significantly lower as compared to scenarios 1 and 2. The short-term bottleneck in transport lasts for two periods, with a lead time of one period and can be considered rather an operational risk event and not as a disruption. Fig. 8 confirms that there is no significant SC performance impact.
4.1.5. Scenario 4. Full impact of COVID-19 pandemic through two waves in 2020 – A combination of all scenarios
Scenario 4 shows the impact on the food SC performance after experiencing a combination of the three disruptive scenarios explained above: an increase in demand, a shutdown in suppliers’ factories, and transport bottlenecks. Fig. 10 shows the results of the experiment through the selected KPIs.

Experiment results: COVID-19 scenario.
This simulation illustrates the SC performance in the food retail industry during the COVID-19 pandemic outbreak in Germany. In this scenario, synergetic effects of adding different negative events can be observed. Interestingly, the aggregation of events results in a positive impact on SC financial performance. Increased revenues and decreased total costs have a positive impact on profit. Nevertheless, delays occur, and a considerable percentage of products are not delivered on time or are incompletely delivered (reflected in the fulfilment (late orders) and demand (products backlog) graphs, respectively). These outcomes lead to out-of-stock products, especially during the first lockdown period. Moreover, a decrease in inventory followed by a considerable increase after the government relaxes the lockdown measures is apparent in the average daily available inventory graph.
The second wave of COVID-19 impacts the industry to a lower extent than the first wave as inventory levels do not drop significantly and a smaller backlog is accumulated. Furthermore, the late orders curve is flattened, which implies a smaller number of delayed orders. The accumulated disruptions result in a drop in the service level to 80%, demonstrating that a significant percentage of the demand is still satisfied despite the pandemic outbreak. Therefore, in general terms, the simulation suggests that the food retail industry can benefit from the pandemic in terms of financial performance and growth opportunities.
Transportation costs increase in the COVID-19 scenario because a higher quantity is shipped in response to higher demand during the pandemic. However, there are inefficiencies in transport as incomplete orders are shipped from the warehouse to customers when suppliers’ factories are shut down, leading to lower vehicle capacity utilization. In addition, transportation costs increase because there is an increase in the average number of vehicles used to transport the requested amounts. Inbound and outbound costs also increase because increasing demand leads to more goods needing to be processed at warehouses. Other costs do not vary as they are fixed administrative costs.
The Lead Time graph shows that a considerable number of orders are delivered to the customer within a range of 0 to 10 days, but under normal conditions, this takes a maximum of half a day. Less frequently, orders may take up to 70 days to be delivered. Thus, the disruptions resulting from the coronavirus outbreak affect the lead time, so providing customers with the required quantities of goods within the expected time becomes a challenge for food retailers.
Moreover, Average Daily Available Inventory levels are affected by the COVID-19 disruption. Initially, a sharp drop in inventory occurs because of the increased demand along with factory shutdowns and bottlenecks in transport during Germany’s first lockdown. During the second lockdown, a slight decrease in inventory can be observed; however, it is not as abrupt as that in the first lockdown. Also, alterations in stock at the end of the period can be observed inducing the ripple effect ( Ivanov et al., 2014 , Dolgui et al., 2018 , Li et al., 2021 ) of the first lockdown. For some product categories, inventory levels recover to a level similar to that in a disruption-free scenario throughout the remaining part of the year.
Regarding Product Backlog , the results show that some orders are not entirely delivered because of a lack of the required number of products, and thus demand is not 100% satisfied. The graph starts with a sharp increase in the product backlog, which results from the 75% increase in demand, disruptions in transport, and shutdowns in the suppliers’ factories during the first lockdown. Then, beginning on day 150, a decrease in the backlog can be observed. This result occurs as coronavirus regulations are softened, and the country begins a gradual return to normality. As a result, demand decreases compared to the first lockdown period, suppliers’ factories reopen, and transport operates under normal conditions. At the end of the year, a slight increase in product backlog can be explained by the increased demand during Germany’s second lockdown period.
The pandemic outbreak negatively impacted the Fulfillment (Late Orders) indicator, which shows a growing line over the whole period beginning on day 80, which coincides with the first lockdown. This line indicates the number of orders that fail to be delivered on time in all customer locations. According to the results, 9,067 orders are delivered late throughout the year, representing approximately 8% of the total number of orders (102,290). Finally, this scenario shows that the ELT service level is 100% from the start of the year until the first lockdown period in mid-March, when the service level falls to 80% and remains at this level throughout the rest of the year.
4.2. Cross-comparison analysis
After evaluating each simulation scenario separately, we used a cross-comparison analysis of all scenarios to evaluate the results and create generalizations. A summary of the computational results is presented in Table 3 .
Summary of computational results.
The overview in Table 3 allows for analysing the effects of the COVID-19 outbreak in the food SC for the selected KPIs. It serves as a guide for addressing the main SC issues in Germany’s food retail industry resulting from the pandemic.
Regarding financial performance in the scenarios, Table 3 displays detailed information on generated revenue and incurred expenses during the initial scenario simulation experiment. Revenue includes the income generated from selling products to customers. Total costs include inventory carrying costs, transportation costs, processing costs (inbound and outbound), inventory spending, and other costs. Profits are calculated by subtracting total costs from revenues. The baseline scenario shows profitability, leading to outstanding performance. Total costs add up to USD 2.750bn and represent 90% of the revenue (USD 3.057bn). Given that companies in the retail industry do not usually produce, but rather purchase, inventory, inventory spending (i.e., 84.6%) typically represents the highest costs in their SC. Inventory carrying costs represent 12.8% of the total costs. As many of the products are perishable, they rotate quickly – typically on a daily basis. Thus, DCs do not accumulate excessive stock, leading to relatively low inventory costs.
For scenario 1, the results suggest that an increase in demand in different periods throughout the year shows a positive impact on sales as profit increases because of increased revenues. The total costs add up to USD 2.723bn and represent around 71% of the revenue (USD 3.825bn). Transportation costs increase and represent 6.2% of the total costs (see Table 3 ). This increase results from a growth in the number of shipping vehicles as larger quantities are transported from the DCs to customers. Inbound and outbound costs also increase because more goods must be processed to meet demand.
In scenario 2, financial performance is not strongly affected throughout the year after experiencing a stoppage in supply for a certain period. Profit decreases by approximately 1% compared to a disruption-free scenario. Although revenues are not impacted, total costs are affected by increased inventory and transportation costs. Thus, total costs add up to USD 2.753bn and represent 90% of the revenue (USD 3.057bn). Inventory levels are readjusted to satisfy the demand because the min-max policy allows variable order quantities, thus preventing inventory shortages.
In scenario 3, the financial performance shows only a minimum change as compared to the baseline scenario. The COVID-19 scenario (no. 4) has a positive impact on revenues and profits. The increasing demand throughout the year is the principal reason for revenue generation. Total costs add up to USD 2.707bn and represent approximately 71% of the revenue (USD 3.816bn). Regarding inventory costs, the min-max policy allows adjusting the inventory levels to satisfy demand, preventing inventory shortages. Thus, inventory levels change to cope with the multiple disruptions faced. Nevertheless, available inventory is rapidly consumed, leading to lower stock levels at DCs. As a result, inventory carrying costs decrease by 17% in the COVID-19 scenario compared to the disruption-free scenario.
Analysis of the results from the different scenarios yields several important observations. As the overall demand increases (scenario 1) at different levels during the selected period, inventory levels decrease. Also, the number of total shipping vehicles rises as more orders need to be dispatched. At the same time, longer lead times can be observed, leading to an increase in the late-orders ratio, which in turn reduces the service level. Backlogs due to incomplete orders also occur, but they are low when compared to the total demand. From a financial point of view, an increase in demand positively impacts revenues, leading to growing profits.
A shutdown in three suppliers’ factories (scenario 2) for 10 or 15 days generates increased inventory levels and a higher number of shipping vehicles used when inventory accumulates at DCs after the factories are reopened. This growth in the number of shipping vehicles used leads to decreased transport efficiency because some vehicles are not fully utilized during the shutdown. Longer lead times can be observed, leading to an increased late-orders ratio and a reduced service level. Backlogs due to incomplete orders are evident.
Multiple short-time bottlenecks in transport (scenario 3) have a small impact on the KPIs selected. The inventory levels and the number of shipping vehicles used slightly increase. The mean lead time remains low, within the expected lead time of 1 day, and the number of late orders rises, although in a small quantity compared to the total demand. This leads to a high service level, close to 100%. Backlogs due to incomplete orders occur in small quantities such that the approximate value of backlogs is 0. Profits slightly decrease because of increased total costs and declined revenues. A combination of the disruptions mentioned above is simulated in the COVID-19 scenario, providing insights regarding the synergetic effects. Since disruptions coincide along the simulation period, a more substantial impact on SC performance and operations can be observed. Inventory levels decrease because of a rapid demand increase at the beginning of the first coronavirus wave, which is intensified when products stop being received because of production stoppages and transport barriers. In turn, the inventory decrease leads to higher lead times and unattended orders, generating an increase in the mean lead time and late orders rate, and entailing an overall reduced ELT service level.
5. Sensitivity analysis
In this section, we discuss the design and results of sensitivity analysis using the Time-to-Recover (TTR) approach proposed by Simchi-Levi et al. (2015) and extended by Kinra et al. (2020) for the purpose of validation and derivation of additional managerial insights.
The Simchi-Levi et al.’ (2015) model introduced the TTR notion as the time it would take for a particular node in the SC network to be restored to some required functionality after a disruption. Kinra et al. (2020) extended the optimization-based TTR approach through the lens of simulation. They used service level (SL) (i.e., the ratio of on-time orders to the overall number of outgoing orders) as an indicator of disruption and recovery in the SC and computed the TTR based on Eq. (1) :
where t failureSL is the point of time at which the SL drops to a level which is considered as a failure, and t recoveredSL is the point of time at which the service level returns to a level which is considered as a recovery.
We run a series of the sensitivity experiments for different values of SL failureSL and SL recovered in the range between 50% and 100% (or 0.5 and 1). Two results are presented in Fig. 11 , Fig. 12 considering scenario no. 4 (i.e., full impact of COVID-19 pandemic). The TTR has been analysed for all 10 product groups involved with our case-study.

Time-to-recover for service level SL failure = 0.9 and SL recovered = 0.98 .

Time-to-recover for service level SL failure = 0.7 and SL recovered = 0.9 .
It can be observed in Fig. 11 , Fig. 12 that the model is sensitive to the selection of SL failure and recovery thresholds. In Fig. 11 , the TTR for the thresholds SL failure = 0.9 and SL recovered = 0.98 are presented. The average TTR is between 0 and 1.5 weeks for 3 product groups, between 3.2 and 4.8 weeks for 6 other product groups, and between 14.7 and 16.3 weeks for another product group. In Fig. 12 , the TTR for the thresholds SL failure = 0.7 and SL recovered = 0.9 are presented. The average TTR is between 0 and 0.72 weeks for 3 product groups, between 3.2 and 4 weeks for 6 other product groups, and between 5.65 and 6.47 weeks for another product group.
The results displayed in Fig. 11 , Fig. 12 show the sensitivity of TTR to the selected SL thresholds. This sensitivity analysis has several managerial implications. First, through the analysis of the results, one can identify the products with longer TTR which would require more attention, and develop measures to strengthen their resilience. Second, the TTR analysis allows for understanding of SL thresholds to be associated with SC operations and performance dynamics according to different disruption scenarios.
6. Discussion and implications
This section aims to respond to RQ2: How can food retail SC resilience be improved? In particular, we discuss what companies should do to increase resilience during a pandemic and how these measures can be implemented.
The COVID-19 pandemic has brought both challenges and opportunities to the food retail industry in Germany. Customers have modified their shopping behaviour and increased their home consumption. Thus, the demand for food has seen a rapid and unprecedented growth that has impacted Germany’s food SC. Nevertheless, the increased demand has introduced significant pressure on the SC, creating many immediate challenges. It has caused alterations in inventory levels, which have led to simultaneous surpluses for producers and shortages for consumers. Hence, food retailers experienced a sharp reduction in inventory, increased product backlog, and late orders during the first lockdown period. Some product categories presented delays and did not arrive within the expected lead times. In short, empty shelves in supermarkets were seen at the beginning of the COVID-19 outbreak in Germany.
Furthermore, food processing plants experienced shutdowns or were forced to operate at reduced capacity because of Germany’s measures to contain the coronavirus’s spread during the first lockdown. Transport bottlenecks have disrupted the movement of goods along the food SC. Although the simulation carried out was limited to land transport by truck, the effects of an interruption in the road that connects suppliers with DCs and DCs with customers was evidenced. Additionally, on-time deliveries and service levels also decreased. In sum, this section’s results, combined with the examined literature review, identify the following SC issues in Germany’s food retail SC due to the COVID-19 pandemic: (1) change in the quantity demanded, (2) change in the demand patterns and market composition, (3) suppliers’ output reduction due to partial or total capacity shutdown, (4) inventory shortages and surpluses at DCs, (5) transport and logistics backlogs, (6) adoption of new distribution channels (e.g., a shift to online sales), (7) capacity constraints at DCs, (8) increased lead times, (9) increased number of non-fulfilled orders, and (10) increased hygienic regulations and traceability requirements. When these changes and challenges occur, the food retail industry should adjust its SC to increase its resilience. In this section, we discuss some directions and actions that food retail companies can take to increase their SC resilience, and how these measures can be implemented in practice ( Fig. 13 ).

Post-disruption framework to increase SC resilience in the food retail industry.
In the context of the COVID-19 outbreak, the first step we recommend is that companies in the food retail industry evaluate the impact of COVID-19 disruptions on their business. Companies must assess and address the effect of disruptions in their SCs by carrying out a rapid evaluation of their current situation and those of their most important partners. During this phase, we also recommend that companies identify potential worst-case scenarios that may emerge from the outbreak and analyse real-time reports to develop measures to stabilize these situations.
The second step we recommend aims to respond to SC challenges resulting from COVID-19 disruptions. Food retailers should increase communication and collaboration across their SCs to design alternative plans and supply allocations, aiming to minimize the disruption’s impact on SC operations and performance. Thus, contact with key suppliers to make decisions that could prevent stockouts or other potential problems for the end customer is essential. Food retailers should also enhance end-to-end visibility to enable them to better understand disruptions and conduct specific actions based on existing priorities. Visibility should extend beyond tier 1 suppliers along the entire SC. Through visibility, access to the real status of inventory at suppliers’ locations, production schedules, and shipment status can be gained, which may help food retailers respond accordingly. End-to-end visibility can be achieved by utilizing a variety of available digital technologies, such as big data analytics, blockchain, and collaborative SC platforms ( Cavalcante et al., 2019 , Dubey et al., 2019 , Ivanov et al., 2019 , Lohmer et al., 2020 , Wamba and Queiroz, 2020 , Dubey et al., 2021 ). Furthermore, end-to-end visibility can enable mapping of the SC beyond the first or second tiers (e.g., using digital twins) ( Ivanov and Dolgui, 2021c , Frazzon et al., 2021 ).
Securing additional stock and redefining inventory strategies is another recommendation for companies in the food retail industry. Along with alternative supply sources and logistic transport options, food retail companies can maintain the required inventory levels and respond quickly to COVID-19 disruptions such as demand changes, transport disruptions, or factory shutdowns. Additionally, expanding DCs’ capacity or outsourcing DCs can help respond to pandemic challenges related to increasing demand and an accelerated shift to online sales. Finally, food retailers should restructure operations to be in line with essential SC priorities in the presence of disruptions.
As the third step, we recommend that food retailers leverage opportunities from the COVID-19 outbreak. Food retail is one of the few sectors in Germany that faces new opportunities as a result of the pandemic. Although the food retail SC may suffer short-term challenges, the food retail industry has the potential to grow during the crisis. Companies in this industry should benefit from demand increase and assess the market by collecting data on new customer segments, capturing customers’ evolving preferences. This would help food retailers adjust their SCs to respond to changes in demand patterns, improve operations, and increase their market share and revenues. We also suggest that food retailers transform their operations model and SC to adapt to permanent changes in the industry such as the shift to home deliveries, online sales, and increasing digital payments. As a result, companies must decide on product investment, channel selection, store composition, and payment systems to respond to these changes.
In addition, food retailers can seize new opportunities through digitalization. Building a Food Retail Industry 4.0, which completely digitalizes (e.g., through cloud-based services) the entire food SC, will become necessary in a post-pandemic environment. Artificial intelligence, blockchain and T&T technologies, robotics and automation, and smart data for predictive analytics can be implemented to increase resilience and grow opportunities in the industry by increasing productivity and reducing costs ( Brintrup et al., 2020 , Winkelhaus and Grosse, 2020 , Fürstenhans et al., 2021 ). Digital technologies can also help address the safety and hygienic concerns enabling the ‘contactless concept’.
In sum, to grow and take advantage of new opportunities, food retailers must seek meaningful partnerships that can become a critical component of their SCs to build redundancies, thus enhancing customer experience and ensuring long-term business stability.
7. Conclusion
The research on disruptions management and resilience in light of the COVID-19 outbreak has become an essential field in SC management. Post-disruption recovery analysis amid the COVID-19 pandemic outbreak is relevant for organizations seeking to respond to disruptions and create new growth opportunities.
We contribute to the existing literature on this topic by examining the COVID-19 pandemic’s impact on food retail SCs with the help of a discrete-event simulation methodology and secondary data support. We examined the impact of multiple scenarios of the COVID-19 disruptions (i.e., temporary bottlenecks in transport, shutdown in suppliers’ factories, and increasing demand) to determine ( i ) the overall impact on food retailers’ SC performance and ( ii ) SC actions that increase resilience in response to the identified problems. Our simulation results showed how the COVID-19 pandemic impacted the food retail SC operations and performance but also created growth opportunities. Although food retailers’ SCs have experienced adverse effects from the pandemic – specifically in terms of demand backlogs and delayed orders, long lead times, decreased service levels, and increased total costs – opportunities have also arisen because of the increased demand.
A cross-comparison analysis of the examined scenarios suggested a positive relationship between the duration of the disruption and its SC impact. Moreover, this analysis provided insights regarding the events’ synergetic effects and the impact of the sequence of disruptions during the pandemic on the SC performance.
We have suggested potential improvements and SC actions in response to the identified challenges. Furthermore, we have created a framework containing structured recommendations for stabilization and recovery in a post-disruption environment, which can be used as a guideline for the main SC actors in the food retail business. This framework identified the following five main directions for food SC resilience improvement: digitalization, inventory management, SC flexibility, SC collaboration, and end-to-end SC visibility.
As for the limitations of this study, it should be noted that the simulations were performed using data from certain secondary sources, which may lead to misleading generalizations and generate inaccuracy. Another limitation is related to the restricted timeline available for observing the effects of implementing potential improvements in the disruption scenarios. Our improvement suggestions have been developed from a qualitative point of view and require quantitative validation in the post-pandemic future. In addition, the study has limitations due to reduced complexity because our analyses of the scenarios were confined to a limited number of variables and SC locations. Finally, as COVID-19 is an outgoing event, restrictions on data access should be noted.
Nevertheless, our study suggests a number of directions for further research. One exciting research path would investigate SC policies to address and improve control of the ripple effect in case of pandemic outbreaks. Responding to COVID-19 disruptions and creating a long-term recovery strategy is becoming a priority for companies facing enormous challenges in their SC due to the pandemic outbreak ( Ivanov and Dolgui, 2021c , Ruel et al., 2021 ). Hence, another interesting future research avenue would create generic actions to recover from the pandemic through digital technologies that enhance end-to-end visibility along the SC. For the specific case of food retailers, it would be interesting to analyse how the use of robotics and automation at distribution centres can help the transition to online sales, which is one of the biggest challenges the industry faces because of the pandemic ( Azzi et al., 2011 , Winkelhaus and Grosse, 2020 , Fragapane et al., 2021 ). With regards to the specific scenarios, it would be interesting to include some other features of real-life scenarios encountered through the COVID-19 pandemic such as shortages of packaging materials and boxes in food SCs ( Battini et al., 2016 ). Another promising research path would analyse how predictive analytics can help food retailers be prepared for new customer patterns and market composition, adjusting their SC accordingly. Finally, research should be conducted on the next steps to enhance SC resilience in a post-pandemic environment in the food retail industry.
CRediT authorship contribution statement
Diana Burgos: Conceptualization, Methodology, Software, Validation, Formal analysis, Investigation, Writing - original draft, Visualization. Dmitry Ivanov: Conceptualization, Methodology, Validation, Resources, Writing - review & editing, Supervision.
Acknowledgement
We thank the Co-Editor-in-Chief, Prof. Tsan-Ming Choi, the Associate Editor, and four anonymous reviewers for their thoughtful comments which have greatly aided in the improvement of the manuscript.
- Aldrighetti R., Zennaro I., Finco S., Battini D. Healthcare Supply Chain Simulation with Disruption Considerations: A Case Study from Northern Italy. Glob. J. Flexible Syst. Manage. 2020; 20 (1):81–102. [ Google Scholar ]
- Aldrighetti R., Battini D., Ivanov D., Zennaro I. Costs of resilience and disruptions in supply chain network design models: a review and future research directions. International Journal of Production Economics. 2021; 235 [ Google Scholar ]
- Azzi A., Battini D., Faccio M., Persona A., Sgarbossa F. Innovative travel time model for dual-shuttle automated storage/retrieval systems. Comput. Ind. Eng. 2011; 61 (3):600–607. [ Google Scholar ]
- Battini D., Calzavara M., Persona A., Sgarbossa F. Sustainable packaging development for fresh food supply chains. Packag. Technol. Sci. 2016; 29 (1):25–43. [ Google Scholar ]
- BMI, 2020. Vorübergehende Grenzkontrollen an den Binnengrenzen zu Österreich, der Schweiz, Frankreich, Luxemburg und Dänemark. Bundesministerium des Innern, für Bau und Heimat. Retrieved 4 February 2021, from https://www.bmi.bund.de/SharedDocs/pressemitteilungen/DE/2020/03/grenzschliessung-corona.html .
- Brintrup A., Pak J., Ratiney D., Pearce T., Wichmann P., Woodall P., McFarlane D. Supply chain data analytics for predicting supplier disruptions: a case study in complex asset manufacturing. Int. J. Prod. Res. 2020; 58 (11):3330–3341. [ Google Scholar ]
- Carvalho H., Barroso A.P., Machado V.H., Azevedo A., Cruz-Mahado V. Supply chain redesign for resilience using simulation. Comput. Ind. Eng. 2012; 62 :329–341. [ Google Scholar ]
- Cavalcante I.M., Frazzon E.M., Forcellinia F.A., Ivanov D. A supervised machine learning approach to data-driven simulation of resilient supplier selection in digital manufacturing. Int. J. Inf. Manage. 2019; 49 :86–97. [ Google Scholar ]
- Chen Y.F., Disney S.M. The myopic order-up-to policy with a proportional feedback controller. Int. J. Prod. Res. 2007; 45 (2):351–368. [ Google Scholar ]
- Chinn, D., Sjatil, P., Stern, S., Tesfu, S., Windhagen, E., 2020. Navigating the post-COVID-19 era: A strategic framework for European recovery. McKinsey. Retrieved 4 February 2021, from https://www.mckinsey.com/industries/public-and-social-sector/our-insights/navigating-the-post-covid-19-era-a-strategic-framework-for-european-recovery .
- Choi T.-M. Risk analysis in logistics systems: A research agenda during and after the COVID-19 pandemic. Transp. Res. Part E: Logist. Transp. 2020; 140 [ PMC free article ] [ PubMed ] [ Google Scholar ]
- Choi T.-M. Fighting Against COVID-19: What Operations Research Can Help and the Sense-and-Respond Framework. Ann. Oper. Res. 2021 doi: 10.1007/s10479-021-03973-w. [ PMC free article ] [ PubMed ] [ CrossRef ] [ Google Scholar ]
- Chowdhury M.T., Sarkar A., Paul S.K., Moktadir M.A. A case study on strategies to deal with the impacts of COVID-19 pandemic in the food and beverage industry. Oper. Manage. Res. 2020 doi: 10.1007/s12063-020-00166-9. [ CrossRef ] [ Google Scholar ]
- Chowdhury P., Paul S.K., Kaisar S., Moktadir M.D. COVID-19 pandemic related supply chain studies: A systematic review. Transp. Res. Part E: Logist. Transp. Rev. 2021; 148 [ PMC free article ] [ PubMed ] [ Google Scholar ]
- Currie C.S.M., Fowler J.W., Kotiadis K., Monks T., Onggo B.S., Robertson D.A., Tako A.A. How simulation modelling can help reduce the impact of COVID-19. J. Simul. 2020; 1–15.14 (2):83–97. [ Google Scholar ]
- Deutschland.de, 2020. The timeline regarding coronavirus in Germany. Retrieved 1 February 2021, from https://www.deutschland.de/es/the-timeline-corona-virus-germany .
- Dolgui A., Ivanov D., Rozhkov M. Does the ripple effect influence the bullwhip effect? An integrated analysis of structural and operational dynamics in the supply chain“ Int. J. Prod. Res. 2020; 58 (5):1285–1301. [ Google Scholar ]
- Dolgui A., Ivanov D., Sokolov B. Ripple effect in the supply chain: an analysis and recent literature. Int. J. Prod. Res. 2018; 56 (1–2):414–430. [ Google Scholar ]
- Dolgui A., Ivanov D., Sokolov B. Reconfigurable supply chain: The X-Network. Int. J. Prod. Res. 2020; 58 (13):4138–4163. [ Google Scholar ]
- Dubey R., Gunasekaran A., Childe S.J., Wamba S.F., Roubaud D., Foropon C. Empirical Investigation of Data Analytics Capability and Organizational Flexibility as Complements to Supply Chain Resilience. Int. J. Prod. Res. 2021; 59 (1):110–128. [ Google Scholar ]
- Dubey R., Gunasekaran A., Childe S.J., Papadopoulos T., Blome C., Luo Z.W. Antecedents of resilient supply chains: an empirical study. IEEE Trans. Eng. Manage. 2019; 66 (1):8–19. [ Google Scholar ]
- El Baz J., Ruel S. Can supply chain risk management practices mitigate the disruption impacts on supply chains’ resilience and robustness? Evidence from an empirical survey in a COVID-19 outbreak era. Int. J. Prod. Econ. 2021; 233 [ Google Scholar ]
- Fragapane G., Hvolby H.H., Sgarbossa F., Strandhagen J.O. Autonomous mobile robots in sterile instrument logistics: an evaluation of the material handling system for a strategic fit framework. Eur. J. Oper. Res. 2021; 294 (2):405–426. [ Google Scholar ]
- Fürstenhans M., Grosse E., Glock C. Smart lighting systems: state-of-the-art and potential applications in warehouse order picking. Int. J. Prod. Res. 2021 doi: 10.1080/00207543.2021.1897177. [ CrossRef ] [ Google Scholar ]
- Ghadge A., Dani S., Chester M., Kalawsky R. A systems thinking approach for modelling supply chain risk propagation. Supply Chain Manage. Int. J. 2013; 18 (5):523–538. [ Google Scholar ]
- Govindan K., Mina H., Alavi B. A decision support system for demand management in healthcare supply chainsconsidering the epidemic outbreaks: A case study of coronavirus disease 2019 (COVID-19) Transp. Res. Part E: Logist. Transp. Rev. 2020; 138 [ PMC free article ] [ PubMed ] [ Google Scholar ]
- Frazzon E.M., Freitag M., Ivanov D. Intelligent Methods and Systems for Decision-Making Support: Toward Digital Supply Chain Twins. Int. J. Inf. Manage. 2021; 57 [ Google Scholar ]
- Hosseini S., Ivanov D., Dolgui A. Review of quantitative methods for supply chain resilience analysis. Transp. Res. Part E: Logist. Transp. Rev. 2019; 125 :285–307. [ Google Scholar ]
- Hosseini S., Ivanov D., Dolgui A. Ripple effect modeling of supplier disruption: Integrated Markov Chain and Dynamic Bayesian Network Approach. International Journal of Production Research. 2020; 58 (11):3284–3303. [ Google Scholar ]
- ILO, 2020. COVID-19 and food retail. International Labour Organization. Retrieved from https://www.ilo.org/wcmsp5/groups/public/ed_dialogue/sector/documents/briefingnote/wcms_741342.pdf .
- IMF, 2020. Germany: Growth rate of the real gross domestic product (GDP) from 2009 to 2021. In Statista – The Statistics Portal. Retrieved 4 February 2021, from https://www.statista.com/statistics/375203/gross-domestic-product-gdp-growth-rate-in-germany/ .
- Ivanov D. Disruption tails and revival policies: A simulation analysis of supply chain design and production-ordering systems in the recovery and post-disruption periods. Computers and Industrial Engineering. 2019; 127 :558–570. [ Google Scholar ]
- Ivanov D., Das A. Coronavirus (COVID-19 / SARS-CoV-2) and supply chain resilience: A research note. International Journal of Integrated Supply Management. 2020; 13 (1):90–102. [ Google Scholar ]
- Ivanov D., Rozhkov M. Coordination of production and ordering policies under capacity disruption and product write-off risk: An analytical study with real-data based simulations of a fast moving consumer goods company. Ann. Oper. Res. 2020; 291 (1–2):387–407. [ Google Scholar ]
- Ivanov D. Viable Supply Chain Model: Integrating agility, resilience and sustainability perspectives – lessons from and thinking beyond the COVID-19 pandemic. Ann. Oper. Res. 2020 doi: 10.1007/s10479-020-03640-6. [ PMC free article ] [ PubMed ] [ CrossRef ] [ Google Scholar ]
- Ivanov D. Supply Chain Viability and the COVID-19 Pandemic: A Conceptual and Formal Generalisation of Four Major Adaptation Strategies. Int. J. Prod. Res. 2021 doi: 10.1080/00207543.2021.1890852. [ CrossRef ] [ Google Scholar ]
- Ivanov D. Springer Nature; Cham: 2021. Introduction to Supply Chain Resilience. [ Google Scholar ]
- Ivanov D. Exiting the COVID-19 Pandemic: After-Shock Risks and Avoidance of Disruption Tails in Supply Chains. Ann. Oper. Res. 2021 doi: 10.1007/s10479-021-04047-7. [ PMC free article ] [ PubMed ] [ CrossRef ] [ Google Scholar ]
- Ivanov D. Simulation-based Ripple Effect Modelling in the Supply Chain. Int. J. Prod. Res. 2017; 55 (7):2083–2101. [ Google Scholar ]
- Ivanov D. Predicting the impacts of epidemic outbreaks on global supply chains: A simulation-based analysis on the coronavirus outbreak (COVID-19/SARS-CoV-2) case“ Transp. Res. Part E: Logist. Transp. Rev. 2020; 136 [ PMC free article ] [ PubMed ] [ Google Scholar ]
- Ivanov D., Dolgui A. Viability of Intertwined Supply Networks: Extending the Supply Chain Resilience Angles towards Survivability. A Position Paper Motivated by COVID-19 Outbreak. International Journal of Production Research. 2020; 58 (10):2904–2915. [ Google Scholar ]
- Ivanov D., Dolgui A. A digital supply chain twin for managing the disruption risks and resilience in the era of Industry 4.0. Prod. Plan. Control. 2021; 32 (9):775–788. [ Google Scholar ]
- Ivanov D., Dolgui A. OR-methods for coping with the ripple effect in supply chains during COVID-19 pandemic: Managerial insights and research implications. Int. J. Prod. Econ. 2021; 232 [ PMC free article ] [ PubMed ] [ Google Scholar ]
- Ivanov D., Dolgui A., Sokolov B. The impact of digital technology and Industry 4.0 on the ripple effect and supply chain risk analytics. Int. J. Prod. Res. 2019; 57 (3):829–846. [ Google Scholar ]
- Ivanov D., Dolgui A. Stress testing supply chains and creating viable ecosystems. Oper. Manage. Res. 2021 doi: 10.1007/s12063-021-00194-z. [ CrossRef ] [ Google Scholar ]
- Ivanov D., Sokolov B., Dolgui A. The Ripple Effect in Supply Chains: Trade-off ‘Efficiency-Flexibility-Resilience’ in Disruption Management. Int. J. Prod. Res. 2014; 52 (7):2154–2172. [ Google Scholar ]
- Ivanov D. Springer International Publishing; Berlin, Germany: 2018. Structural dynamics and resilience in supply chain risk management. [ Google Scholar ]
- Li Y., Chen K., Collignon S., Ivanov D. Ripple effect in the supply chain network: Forward and backward disruption propagation, network health and firm vulnerability. Eur. J. Oper. Res. 2021; 291 (3):1117–1131. [ PMC free article ] [ PubMed ] [ Google Scholar ]
- Kinra A., Ivanov D., Das A., Dolgui A. Ripple effect quantification by supply risk exposure assessment. Int. J. Prod. Res. 2020; 58 (19):5559–5578. [ Google Scholar ]
- Llaguno A., Mula J., Campuzano-Bolarin F. State of the art, conceptual framework and simulation analysis of the ripple effect on supply chains. Int. J. Prod. Res. 2021:1–23. doi: 10.1080/00207543.2021.1877842. [ CrossRef ] [ Google Scholar ]
- Lohmer J., Bugert N., Lasch R. Analysis of Resilience Strategies and Ripple Effect in Blockchain-Coordinated Supply Chains: An Agent-based Simulation Study. Int. J. Prod. Econ. 2020; 228 [ PMC free article ] [ PubMed ] [ Google Scholar ]
- Loske D. The impact of COVID-19 on transport volume and freight capacity dynamics: An empirical analysis in German food retail logistics. Transp. Res. Interdiscipl. Perspect. 2020; 6 [ PMC free article ] [ PubMed ] [ Google Scholar ]
- Macdonald J.R., Zobel C.W., Melnyk S.A., Griffis S.E. Supply chain risk and resilience: theory building through structured experiments and simulation. Int. J. Prod. Res. 2018; 56 (12):4337–4355. [ Google Scholar ]
- Minner S., Transchel S. Periodic review inventory-control for perishable products under service-level constraints. OR Spectrum. 2010; 32 (4):979–996. [ Google Scholar ]
- Nagurney A. Supply Chain Game Theory Network Modeling Under Labor Constraints: Applications to the Covid-19 Pandemic. Eur. J. Oper. Res. 2021 doi: 10.1016/j.ejor.2020.12.054. [ PMC free article ] [ PubMed ] [ CrossRef ] [ Google Scholar ]
- OECD Food Supply Chains and COVID-19: Impacts and Policy Lessons. 2020. http://www.oecd.org/coronavirus/policy-responses/food-supply-chains-and-covid19-impacts-and-policy-lessons-71b57aea/ Retrieved 16 August 2020, from.
- Olivares-Aguila J., ElMaraghy W. System dynamics modelling for supply chain disruptions. Int. J. Prod. Res. 2020; 1–19 doi: 10.1080/00207543.2020.1725171. [ CrossRef ] [ Google Scholar ]
- Paul S.K., Chowdhury P. A production recovery plan in manufacturing supply chains for a high-demand item during COVID-19. Int. J. Phys. Distrib. Logist. Manage. 2021; 51 (2):104–125. [ Google Scholar ]
- Paul S., Venkateswaran J. Designing robust policies under deep uncertainty for mitigating epidemics. Comput. Ind. Eng. 2020; 140 [ Google Scholar ]
- PwC, 2020. How COVID-19 is changing food retail. https://www.pwc.de/en/retail-and-consumer/how-covid-19-is-changing-food-retail.html . Retrieved 4 February 2021, from https://www.pwc.de/en/retail-and-consumer/how-covid-19-is-changing-food-retail.html .
- Queiroz M.M., Ivanov D., Dolgui A., Fosso Wamba S. Impacts of Epidemic Outbreaks on Supply Chains: Mapping a Research Agenda Amid the COVID-19 Pandemic through a Structured Literature Review. Ann. Oper. Res. 2020 doi: 10.1007/s10479-020-03685-7. [ PMC free article ] [ PubMed ] [ CrossRef ] [ Google Scholar ]
- Rathore R., Thakkar J.J., Jha J.K. Impact of risks in food grains transportation system: a system dynamics approach. Int. J. Prod. Res. 2020:1–20. [ Google Scholar ]
- Ruel S., El Baz J., Ivanov D., Das A. Supply Chain Viability: Conceptualization, Measurement, and Nomological Validation. Ann. Oper. Res. 2021 doi: 10.1007/s10479-021-03974-9. [ PMC free article ] [ PubMed ] [ CrossRef ] [ Google Scholar ]
- Schmitt T.G., Kumar S., Stecke K.E., Glover F.W., Ehlen M.A. Mitigating disruptions in a multi-echelon supply chain using adaptive ordering. Omega. 2017; 68 :185–198. [ Google Scholar ]
- Shen B., Li Q. Market disruptions in supply chains: A review of operational models. Int. Trans. Oper. Res. 2017; 24 :697–711. [ Google Scholar ]
- Simchi-Levi D., Schmidt W., Wei Y., Zhang P.Y., Combs K., Ge Y., Gusikhin O., Sander M., Zhang D. Identifying risks and mitigating disruptions in the automotive supply chain. Interfaces. 2015; 45 (5):375–390. [ Google Scholar ]
- Singh S., Kumar R., Panchal R., Tiwari M.K. Impact of COVID-19 on logistics systems and disruptions in food supply chain. Int. J. Prod. Res. 2021; 59 (7):1993–2008. [ Google Scholar ]
- Sodhi M., Tang C., Willenson E. Research opportunities in preparing supply chains of essential goods for future pandemics. Int. J. Prod. Res. 2021 doi: 10.1080/00207543.2021.1884310. [ CrossRef ] [ Google Scholar ]
- Svoboda J., Minner S., Yao M. Typology and literature review on multiple supplier inventory control models. Eur. J. Oper. Res. 2021; 293 :1–23. [ Google Scholar ]
- Guardian The. A disastrous situation': mountains of food wasted as coronavirus scrambles supply chain. 2020. https://www.theguardian.com/world/2020/apr/09/us-coronavirus-outbreak-agriculture-food-supply-waste accessed on 5th March 2021.
- Veselovská L. Supply chain disruptions in the context of early stages of the global COVID-19 outbreak. Problems Perspect. Manage. 2020; 18 (2):490. [ Google Scholar ]
- Wamba S.F., Queiroz M.M. Industry 4.0 and the supply chain digitalisation: a blockchain diffusion perspective. Prod. Plan. Control. 2020:1–18. [ Google Scholar ]
- Wilson M.C. The impact of transportation disruptions on supply chain performance. Transp. Res. Part E: Logist. Transp. Rev. 2007; 43 (4):295–320. [ Google Scholar ]
- WHO, 2020. Rolling updates on coronavirus disease (COVID-19). Who.int. Retrieved 4 February 2021, from https://www.who.int/emergencies/diseases/novel-coronavirus-2019/events-as-they-happen .
- Winkelhaus S., Grosse E.H. Logistics 4.0: a systematic review towards a new logistics system. Int. J. Prod. Res. 2020; 58 (1):18–43. [ Google Scholar ]
Analyzing the Effects of Covid-19 on Food Supply Chains: A Case Study on Ranking the Obstacles with ANP Methodology
Affiliations.
- 1 Centre of Excellence Supply Chain and Transportation (CESIT), KEDGE Business School, 680 Cr de la Libération, 33405 Bordeaux, France.
- 2 Department of Industrial Engineering, Sharif University of Technology, Tehran, 14588-89694, Iran.
- PMID: 38620796
- PMCID: PMC9605725
- DOI: 10.1016/j.ifacol.2022.09.672
Coronavirus pandemic has severely affected the supply chain network of many industries. Various activities have been disrupted throughout supply chains due to the increasing number of patients, death rate growth, quarantine regulations, social distancing, closed borders, and the phenomenal decrease in travel rate. Furthermore, the pandemic had dramatic effects on consumers' behavior all over the world, making them more eager/reluctant to purchase certain industrial products. In this paper, considering the actual supply chain of an Iranian company, the disruptive obstacles that the pandemic can create against properly undertaking activities in a food supply chain, are investigated. The examined obstacles are ranked and prioritized using the Analytical Network Process (ANP) technique. For this purpose, pairwise comparison questionnaires have been designed and completed by 28 managers and supervisors active in the food supply network. The answers are collected and the geometric mean of the matrices and their incompatibility rates are calculated. Based on the obtained results "labor shortage" and "low flexibility" have respectively the highest and lowest priorities among all analyzed obstacles.
Keywords: ANP method; Covid-19; Food Supply Chain; Pandemic Effects; Supply Chain Obstacles.
© 2019, IFAC (International Federation of Automatic Control) Hosting by Elsevier Ltd.

- Undergraduate Students
- Graduate Students
- All Information for Students
- Penn State Ag Council
- Ag Action Network
- Recruitment and Employer Relations
- Continuing Education
- Labs and Services
- All Information for Industry
- Get Involved
- Awards and Recognition
- Armsby Honor Society
- All Information for Alumni
- Faculty & Staff Resources
- All Information for Faculty & Staff
- Places to Visit
- Service Laboratories
- Programs and Events
- Youth Opportunities
- All Information for Visitors & Public
Case Studies of Supermarkets and Food Supply Chains
11 Case Studies of Supermarkets and Food Supply Chains in Low-Income Areas of the Northeast, and cross-case comparisons. Conducted by members of the EFSNE Distribution Team. All case studies were written by Kristen Park, Miguel Gómez, and Kate Clancy. Published by Cornell University in conjunction with the EFSNE project and the Northeast Regional Center for Rural Development.
PDF document, 417.4 KB
This report summarizes the findings that cut across the cases. These are presented as key lessons that offer researchers and policymakers a better understanding of how regional food systems operate and how policies may be made to maintain a sustainable food system in the Northeast. Written by Kristen S. Park, Miguel I. Gómez, Kate Clancy. Published jointly by Cornell University and the Northeast Regional Center for Rural Development. 427KB PDF
PDF document, 1.5 MB
This case study describes a supermarket and with it the supply chains of two of the eight foods in the EFSNE project’s market basket (apples and ground beef). Written by Kristen S. Park, Miguel Gómez, and Kate Clancy. Published jointly by Cornell University and the Northeast Regional Center for Rural Development. 1.6MB PDF.
PDF document, 1.7 MB
This case study describes a supermarket and with it the supply chains of two of the eight foods in the EFSNE project’s market basket (fluid milk and frozen broccoli). Written by Kristen S. Park, Miguel Gómez, and Kate Clancy. Published jointly by Cornell University and the Northeast Regional Center for Rural Development. 1.6MB PDF.
This case study describes a supermarket and with it the supply chains of two of the eight foods in the EFSNE project’s market basket (bread and potatoes). Written by Kristen S. Park, Miguel Gómez, and Kate Clancy. Published jointly by Cornell University and the Northeast Regional Center for Rural Development. 1.6MB PDF.
PDF document, 1.4 MB
This case study describes a supermarket and with it the supply chains of two of the eight foods in the EFSNE project’s market basket (canned peaches and frozen broccoli). Written by Kristen S. Park, Miguel Gómez, and Kate Clancy. Published jointly by Cornell University and the Northeast Regional Center for Rural Development. 1.5MB PDF.
This case study describes a supermarket and with it the supply chains of two of the eight foods in the EFSNE project’s market basket (fluid milk and ground beef). Written by Kristen S. Park, Miguel Gómez, and Kate Clancy. Published jointly by Cornell University and the Northeast Regional Center for Rural Development. 1.8MB PDF.
This case study describes a supermarket and with it the supply chains of two of the eight foods in the EFSNE project’s market basket (frozen broccoli and potatoes). Written by Kristen S. Park, Miguel Gómez, and Kate Clancy. Published jointly by Cornell University and the Northeast Regional Center for Rural Development. 1.5MB PDF.
This case study describes a supermarket and with it the supply chains of two of the eight foods in the EFSNE project’s market basket (potatoes and cabbage). Written by Kristen S. Park, Miguel Gómez, and Kate Clancy. Published jointly by Cornell University and the Northeast Regional Center for Rural Development. 1.5MB PDF.
This case study describes a supermarket and with it the supply chains of two of the eight foods in the EFSNE project’s market basket (frozen broccoli and canned peaches). Written by Kristen S. Park, Miguel Gómez, and Kate Clancy. Published jointly by Cornell University and the Northeast Regional Center for Rural Development. 1.5MB PDF.
This case study describes a supermarket and with it the supply chains of two of the eight foods in the EFSNE project’s market basket (apples and cabbage). Written by Kristen S. Park, Miguel Gómez, and Kate Clancy. Published jointly by Cornell University and the Northeast Regional Center for Rural Development. 1.5MB PDF.
This case study describes a supermarket and with it the supply chains of two of the eight foods in the EFSNE project’s market basket (cabbage and frozen broccoli). Written by Kristen S. Park, Miguel Gómez, and Kate Clancy. Published jointly by Cornell University and the Northeast Regional Center for Rural Development. 1.5MB PDF.
This case study describes a supermarket and with it the supply chains of two of the eight foods in the EFSNE project’s market basket (bread and potatoes). Written by Kristen S. Park, Miguel Gómez, and Kate Clancy. Published jointly by Cornell University and the Northeast Regional Center for Rural Development. 1.8MB PDF.
Zip archive, 15.4 MB
A zipped file containing all 11 of the EFSNE case studies of supermarkets and food supply chains in low-income areas of the Northeast US, and also the write-up of findings across cases. 16.1MB download.
To read this content please select one of the options below:
Please note you do not have access to teaching notes, blockchain: case studies in food supply chain visibility.
Supply Chain Management
ISSN : 1359-8546
Article publication date: 7 May 2020
Issue publication date: 16 June 2020
This paper aims to investigate how blockchain has moved beyond cryptocurrencies and is being deployed to enhance visibility and trust in supply chains, their limitations and potential impact.
Design/methodology/approach
Qualitative analysis are undertaken via case studies drawn from food companies using semi-structured interviews.
Blockchain is demonstrated as an enabler of visibility in supply chains. Applications at scale are most likely for products where the end consumer is prepared to pay the premium currently required to fund the technology, e.g. baby food. Challenges remain in four areas: trust of the technology, human error and fraud at the boundaries, governance, consumer data access and willingness to pay.
Research limitations/implications
The paper shows that blockchain can be utilised as part of a system generating visibility and trust in supply chains. Research directs academic attention to issues that remain to be addressed. The challenges pertaining to the technology itself we believe to be generalisable; those specific to the food industry may not hold elsewhere.
Practical implications
From live case studies, we provide empirical evidence that blockchain provides visibility of exchanges and reliable data in fully digitised supply chains. This provides provenance and guards against counterfeit goods. However, firms will need to work to gain consumer buy-in for the technology following repeated past claims of trustworthiness.
Originality/value
This paper provides primary evidence from blockchain use cases “in the wild”. The exploratory case studies examine application of blockchain for supply chain visibility.
- Blockchain for good
- Research4 good
- Supply chains
- Supply chain visibility
- Supply-chain management
- Supply chain vulnerability
- Supply risk
- Food security
- Information transparency
Acknowledgements
The authors gratefully acknowledge the funding contributions of the Economic and Social Research Council (UK), grant reference ES/P000630/1, and the Engineering and Physical Sciences Research Council (UK) to the Dynamic, Real time, On-demand Personalisation for Scaling (DROPS) [EP/R033374/1] and Control and Trust as Moderating Mechanisms in addressing Vulnerability for the Design of Business and Economic Models (ConTriVE) project [EP/N028422/1], which have contributed substantially to the research conducted and the writing of this paper. We further recognise the support from the British Academy Leverhulme “Blockchain for Good [B4G]” project grant SG160335 and from institutions Centre for Business, Organisations and Society at University of Bath School of Management, Cambridge Institute for Sustainability Leadership (CISL) at the University of Cambridge, Centre of Digital Economy (CODE) at Surrey Business School, University of Surrey, and Bristol Business School, UWE.
The authors would like to thank Genia Mineeva, Leanne Melnyk, Maria Carrascosa, Alaa Ezz-al-Arab, Benn Lawson and Leonardo Ceron for their help and advice during the course of this research.
The authors would also like to acknowledge the contribution made by the two anonymous reviewers, who encouraged significant improvements in the paper, and our interviewees, whose openness to research we appreciate.
Rogerson, M. and Parry, G.C. (2020), "Blockchain: case studies in food supply chain visibility", Supply Chain Management , Vol. 25 No. 5, pp. 601-614. https://doi.org/10.1108/SCM-08-2019-0300
Emerald Publishing Limited
Copyright © 2020, Emerald Publishing Limited
Related articles
We’re listening — tell us what you think, something didn’t work….
Report bugs here
All feedback is valuable
Please share your general feedback
Join us on our journey
Platform update page.
Visit emeraldpublishing.com/platformupdate to discover the latest news and updates
Questions & More Information
Answers to the most commonly asked questions here
Advertisement

Green food supply chain design considering risk and post-harvest losses: a case study
- Original Research
- Published: 08 June 2020
- Volume 295 , pages 257–284, ( 2020 )
Cite this article
- D. G. Mogale 1 ,
- Sri Krishna Kumar 2 &
- Manoj Kumar Tiwari ORCID: orcid.org/0000-0001-8564-1402 2 , 3
1904 Accesses
49 Citations
1 Altmetric
Explore all metrics
The global food insecurity, malnourishment and rising world hunger are the major hindrances in accomplishing the zero hunger sustainable development goal by 2030. Due to the continuous increment of wheat production in the past few decades, India received the second rank in the global wheat production after China. However, storage capacity has not been expanded with similar extent. The administrative bodies in India are constructing several capacitated silos in major geographically widespread producing and consuming states to curtail this gap. This paper presents a multi-period single objective mathematical model to support their decision-making process. The model minimizes the silo establishment, transportation, food grain loss, inventory holding, carbon emission, and risk penalty costs. The proposed model is solved using the variant of the particle swarm optimization combined with global, local and near neighbor social structures along with traditional PSO. The solutions obtained through two metaheuristic algorithms are compared with the optimal solutions. The impact of supply, demand and capacity of silos on the model solution is investigated through sensitivity analysis. Finally, some actionable theoretical and managerial implications are discussed after analysing the obtained results.
This is a preview of subscription content, log in via an institution to check access.
Access this article
Price includes VAT (Russian Federation)
Instant access to the full article PDF.
Rent this article via DeepDyve
Institutional subscriptions
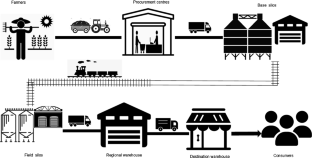
Similar content being viewed by others
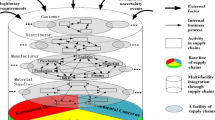
Mathematical modeling for sustainable agri-food supply chain
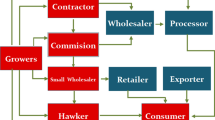
A mathematical model for the optimization of agricultural supply chain under uncertain environmental and financial conditions: the case study of fresh date fruit
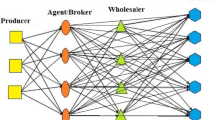
Compromising allocation for optimising agri-food supply chain distribution network: a fuzzy stochastic programming approach
Akkerman, R., Farahani, P., & Grunow, M. (2010). Quality, safety and sustainability in food distribution: A review of quantitative operations management approaches and challenges. OR Spectrum, 32 (4), 863–904.
Google Scholar
Alagusundaram, K. (2016). Should India consider shifting to bulk food grain storage system?—A conceptual frame work. In Proceedings of the 10th International Conference on Controlled Atmosphere and Fumigation in Stored Products (CAF2016), CAF Permanent Committee Secretariat, Winnipeg, Canada (pp. 431–437).
Aliano Filho, A., de Oliveira Florentino, H., Pato, M. V., Poltroniere, S. C., & da Silva Costa, J. F. (2019). Exact and heuristic methods to solve a bi-objective problem of sustainable cultivation. Annals of Operations Research . https://doi.org/10.1007/s10479-019-03468-9 .
Article Google Scholar
Allaoui, H., Guo, Y., Choudhary, A., & Bloemhof, J. (2018). Sustainable agro-food supply chain design using two-stage hybrid multi-objective decision-making approach. Computers & Operations Research, 89, 369–384.
An, K., & Ouyang, Y. (2016). Robust grain supply chain design considering post-harvest loss and harvest timing equilibrium. Transportation Research Part E: Logistics and Transportation Review, 88, 110–128.
Arabani, A. B., & Farahani, R. Z. (2012). Facility location dynamics: An overview of classifications and applications. Computers & Industrial Engineering, 62 (1), 408–420.
Ardjmand, E., Young, W. A., Weckman, G. R., Bajgiran, O. S., Aminipour, B., & Park, N. (2016). Applying genetic algorithm to a new bi-objective stochastic model for transportation, location, and allocation of hazardous materials. Expert Systems with Applications, 51, 49–58.
Asgari, N., Farahani, R. Z., Rashidi-Bajgan, H., & Sajadieh, M. S. (2013). Developing model-based software to optimise wheat storage and transportation: A real-world application. Applied Soft Computing Journal, 13 (2), 1074–1084.
Banasik, A., Kanellopoulos, A., Claassen, G. D. H., Bloemhof-Ruwaard, J. M., & van der Vorst, J. G. (2017). Assessing alternative production options for eco-efficient food supply chains using multi-objective optimization. Annals of Operations Research, 250 (2), 341–362.
Bilgen, B., & Ozkarahan, I. (2007). A mixed-integer linear programming model for bulk grain blending and shipping. International Journal of Production Economics, 107 (2), 555–571.
Boonmee, A., & Sethanan, K. (2016). A GLNPSO for multi-level capacitated lot-sizing and scheduling problem in the poultry industry. European Journal of Operational Research, 250 (2), 652–665.
Chan, F. T., Wang, Z. X., Goswami, A., Singhania, A., & Tiwari, M. K. (2020). Multi-objective particle swarm optimisation based integrated production inventory routing planning for efficient perishable food logistics operations. International Journal of Production Research . https://doi.org/10.1080/00207543.2019.1701209 .
Chauhan, A., Kaur, H., Yadav, S., & Jakhar, S. K. (2019). A hybrid model for investigating and selecting a sustainable supply chain for agri-produce in India. Annals of Operations Research . https://doi.org/10.1007/s10479-019-03190-6 .
De, A., Mogale, D. G., Zhang, M., Pratap, S., Kumar, S. K., & Huang, G. Q. (2019). Multi-period multi-echelon inventory transportation problem considering stakeholders behavioural tendencies. International Journal of Production Economics . https://doi.org/10.1016/j.ijpe.2019.107566 .
Department of Food & Public Distribution, Ministry of Consumer affairs, Food & Public Distribution. PDS Portal of India. Retrieved February 17, 2017, from http://www.pdsportal.nic.in/main.aspx/ .
Department of Food & Public Distribution, Ministry of Consumer Affairs, Food & Public Distribution. Public Distribution, NFSA & Computerisation. Retrieved February 5, 2017, from http://dfpd.nic.in/nfsa-act.htm .
Diabat, A., Govindan, K., & Panicker, V. V. (2012). Supply chain risk management and its mitigation in a food industry. International Journal of Production Research, 50 (11), 3039–3050.
Dora, M., Wesana, J., Gellynck, X., Seth, N., Dey, B., & De Steur, H. (2019). Importance of sustainable operations in food loss: Evidence from the Belgian food processing industry. Annals of Operations Research . https://doi.org/10.1007/s10479-019-03134-0 .
Eberhart, R., & Kennedy, J. (1995.). A new optimizer using particle swarm theory.In MHS’95. Proceedings of the sixth international symposium on micro machine and human science (pp. 39–43).
Eskandarpour, M., Dejax, P., Miemczyk, J., & Péton, O. (2015). Sustainable supply chain network design: An optimization-oriented review. Omega, 54, 11–32.
Eskandarpour, M., Dejax, P., & Péton, O. (2017). A large neighborhood search heuristic for supply chain network design. Computers & Operations Research, 80, 23–37.
Esteso, A., Alemany, M. M., & Ortiz, A. (2018). Conceptual framework for designing agri-food supply chains under uncertainty by mathematical programming models. International Journal of Production Research, 56 (13), 4418–4446.
Etemadnia, H., Goetz, S. J., Canning, P., & Tavallali, M. S. (2015). Optimal wholesale facilities location within the fruit and vegetables supply chain with bimodal transportation options: An LP-MIP heuristic approach. European Journal of Operational Research, 244 (2), 648–661.
FAO. (2011). Global food losses and food waste—Extent, causes and prevention. Rome.
FAO, Ifad, UNICEF, WFP, & WHO. (2019). The state of food security and nutrition in the world 2019. Safeguarding against economic slowdowns and downturns . Rome: FAO.
Farahani, R. Z., SteadieSeifi, M., & Asgari, N. (2010). Multiple criteria facility location problems: A survey. Applied Mathematical Modelling, 34 (7), 1689–1709.
Florentino, H. D. O., Cantane, D. R., Jones, D. F., Ouelhadj, D., Khosravi, B., & Irawan, C. A. (2020). An optimization model for combined selecting, planting and harvesting sugarcane varieties. Annals of Operations Research . https://doi.org/10.1007/s10479-020-03610-y .
Food Corporation of India. Retrieved January 5, 2018, from http://fci.gov.in/movements.php?view=32 .
Ge, H., Goetz, S., Canning, P., & Perez, A. (2018). Optimal locations of fresh produce aggregation facilities in the United States with scale economies. International Journal of Production Economics, 197 (January), 143–157.
Ge, H., Gray, R., & Nolan, J. (2015). Agricultural supply chain optimization and complexity: A comparison of analytic vs simulated solutions and policies. International Journal of Production Economics, 159, 208–220.
Gholamian, M. R., & Taghanzadeh, A. H. (2017). Integrated network design of wheat supply chain: A real case of Iran. Computers and Electronics in Agriculture, 140, 139–147.
Göbel, C., Langen, N., Blumenthal, A., Teitscheid, P., & Ritter, G. (2015). Cutting food waste through cooperation along the food supply chain. Sustainability, 7 (2), 1429–1445.
Govindan, K., Jafarian, A., Khodaverdi, R., & Devika, K. (2014). Two-echelon multiple-vehicle location-routing problem with time windows for optimization of sustainable supply chain network of perishable food. International Journal of Production Economics, 152, 9–28.
Gustavsson, J., Cederberg, C., Sonesson, U., Van Otterdijk, R., & Meybeck, A. (2011). Global food losses and food waste: Extent, causes and prevention, FAO, Rome, Italy. Retrieved August 12, 2018 from http://www.fao.org/docrep/014/mb060e/mb060e00.pdf .
Hamadani, A. Z., Abouei Ardakan, M., Rezvan, T., & Honarmandian, M. M. (2013). Location-allocation problem for intra-transportation system in a big company by using meta-heuristic algorithm. Socio-Economic Planning Sciences, 47 (4), 309–317.
Hosseini-Motlagh, S. M., Samani, M. R. G., & Saadi, F. A. (2019). A novel hybrid approach for synchronized development of sustainability and resiliency in the wheat network. Computers and Electronics in Agriculture, 168, 105095.
Kaur, H. (2019). Modelling internet of things driven sustainable food security system . Benchmarking: An International Journal. https://doi.org/10.1108/BIJ-12-2018-0431 .
Book Google Scholar
Ketzenberg, M., Bloemhof, J., & Gaukler, G. (2015). Managing perishables with time and temperature history. Production and Operations Management, 24 (1), 54–70.
Khalifehzadeh, S., Seifbarghy, M., & Naderi, B. (2015). A four-echelon supply chain network design with shortage: Mathematical modeling and solution methods. Journal of Manufacturing Systems, 35, 164–175.
Khamjan, W., Khamjan, S., & Pathumnakul, S. (2013). Determination of the locations and capacities of sugar cane loading stations in Thailand. Computers & Industrial Engineering, 66 (4), 663–674.
Kiil, K., Dreyer, H. C., Hvolby, H. H., & Chabada, L. (2018). Sustainable food supply chains: The impact of automatic replenishment in grocery stores. Production Planning & Control, 29 (2), 106–116.
Krishnan, R., Agarwal, R., Bajada, C., & Arshinder, K. (2020). Redesigning a food supply chain for environmental sustainability—An analysis of resource use and recovery. Journal of Cleaner Production, 242, 118374.
Leat, P., & Revoredo-Giha, C. (2013). Risk and resilience in agri-food supply chains: The case of the ASDA PorkLink supply chain in Scotland. Supply Chain Management: An International Journal, 18 (2), 219–231.
Liotta, G., Stecca, G., & Kaihara, T. (2015). Optimisation of freight flows and sourcing in sustainable production and transportation networks. International Journal of Production Economics, 164, 351–365.
Maiyar, L. M., & Thakkar, J. J. (2017). A combined tactical and operational deterministic food grain transportation model: Particle swarm based optimization approach. Computers & Industrial Engineering, 110, 30–42.
Maiyar, L. M., & Thakkar, J. J. (2019). Modelling and analysis of intermodal food grain transportation under hub disruption towards sustainability. International Journal of Production Economics . https://doi.org/10.1016/J.IJPE.2018.07.021 .
Melo, M. T., Nickel, S., & Saldanha-da-Gama, F. (2009). Facility location and supply chain management—A review. European Journal of Operational Research, 196, 401–412.
Milman, O. (2015). Earth has lost a third of arable land in past 40 years, scientists say. Retrieved August 14, 2019, from https://www.theguardian.com/environment/2015/dec/02/arable-land-soil-food-security-shortage .
Mishra, N., & Singh, A. (2018). Use of twitter data for waste minimisation in beef supply chain. Annals of Operations Research, 270 (1–2), 337–359.
Mogale, D. G., Cheikhrouhou, N., & Tiwari, M. K. (2019a). Modelling of sustainable food grain supply chain distribution system: A bi-objective approach. International Journal of Production Research . https://doi.org/10.1080/00207543.2019.1669840 .
Mogale, D. G., Ghadge, A., Kumar, S. K., & Tiwari, M. K. (2019b). Modelling supply chain network for procurement of food grains in India. International Journal of Production Research . https://doi.org/10.1080/00207543.2019.1682707 .
Mogale, D. G., Kumar, M., Kumar, S. K., & Tiwari, M. K. (2018a). Grain silo location-allocation problem with dwell time for optimization of food grain supply chain network. Transportation Research Part E: Logistics and Transportation Review, 111, 40–69.
Mogale, D. G., Kumar, S. K., Márquez, F. P. G., & Tiwari, M. K. (2017). Bulk wheat transportation and storage problem of public distribution system. Computers & Industrial Engineering, 104, 80–97.
Mogale, D. G., Kumar, S. K., & Tiwari, M. K. (2018b). An MINLP model to support the movement and storage decisions of the Indian food grain supply chain. Control Engineering Practice, 70, 98–113.
Mohammed, Ahmed, & Wang, Qian. (2017). The Fuzzy Multi-Objective Distribution Planner for a Green Meat Supply Chain. International Journal of Production Economics, 184, 47–58.
Naderi, B., Govindan, K., & Soleimani, H. (2019). A Benders decomposition approach for a real case supply chain network design with capacity acquisition and transporter planning: Wheat distribution network. Annals of Operations Research . https://doi.org/10.1007/s10479-019-03137-x .
Nicholson, C. F., Gómez, M. I., & Gao, O. H. (2011). The costs of increased localization for a multiple-product food supply chain: Dairy in the United States. Food Policy, 36 (2), 300–310.
Nourbakhsh, S. M., Bai, Y., Maia, G. D. N., Ouyang, Y., & Rodriguez, L. (2016). Grain supply chain network design and logistics planning for reducing post-harvest loss. Biosystems Engineering, 151, 105–115.
Orgut, I. S., Ivy, J., & Uzsoy, R. (2017). Modeling for the equitable and effective distribution of food donations under stochastic receiving capacities. IISE Transactions, 49 (6), 567–578.
Orjuela-Castro, J. A., Sanabria-Coronado, L. A., & Peralta-Lozano, A. M. (2017). Coupling facility location models in the supply chain of perishable fruits. Research in Transportation Business and Management, 24, 73–80.
Paksoy, T., Pehlivan, N. Y., & Özceylan, E. (2012). Application of fuzzy optimization to a supply chain network design: A case study of an edible vegetable oils manufacturer. Applied Mathematical Modelling, 36 (6), 2762–2776.
Parwez, S. (2014). Food supply chain management in Indian Agriculture: Issues, opportunities and further research. African Journal of Business Management, 8 (14), 572–581.
Pongchairerks, P., & Kachitvichyanukul, V. (2009). Particle swarm optimization algorithm with multiple social learning structures. International Journal of Operational Research, 6 (2), 176–194.
Ramanathan, V., S. Sundar, R. Harnish, S. Sharma, J. Seddon, B. Croes, A. Lloyd, et al. (2014). India California air pollution mitigation program: Options to reduce road transport pollution in India . Published by The Energy and Resources Institute in collaboration with the University of California at San Diego and the California Air Resources Board.
Rancourt, M. È., Cordeau, J. F., Laporte, G., & Watkins, B. (2015). Tactical network planning for food aid distribution in Kenya. Computers & Operations Research, 56, 68–83.
Raut, R. D., Gardas, B. B., Kharat, M., & Narkhede, B. (2018). Modeling the drivers of post-harvest losses–MCDM approach. Computers and Electronics in Agriculture, 154, 426–433.
Report of the Comptroller and Auditor General of India. (2013). Storage management and movement of food grains in food corporation of India . New Delhi: Union Government Ministry of Consumer Affairs, Food and Public Distribution.
ReVelle, C. S., & Eiselt, H. A. (2005). Location analysis: A synthesis and survey. European Journal of Operational Research, 165 (1), 1–19.
Rohmer, S. U. K., Gerdessen, J. C., & Claassen, G. D. H. (2019). Sustainable supply chain design in the food system with dietary considerations: A multi-objective analysis. European Journal of Operational Research, 273 (3), 1149–1164.
Sachan, A., Sahay, B. S., & Sharma, D. (2005). Developing Indian grain supply chain cost model: A system dynamics approach. International Journal of Productivity and Performance Management, 54 (3), 187–205.
Sharon, M., Abirami, C. V., & Alagusundaram, K. (2014). Grain storage management in India. Journal of Postharvest Technology, 2 (1), 12–24.
Sheane, R., McCosker, C., & Royston, S. (2018). Report of Food system framework: A focus on food sustainability.
Shukla, M., & Jharkharia, S. (2013). Agri-fresh produce supply chain management: A state-of-the-art literature review. International Journal of Operations & Production Management, 33 (2), 114–158.
Soleimani, H., & Kannan, G. (2015). A hybrid particle swarm optimization and genetic algorithm for closed-loop supply chain network design in large-scale networks. Applied Mathematical Modelling, 39 (14), 3990–4012.
Song, M., Wang, S., & Fisher, R. (2014). Transportation, iceberg costs and the adjustment of industrial structure in China. Transportation Research Part D: Transport and Environment, 32, 278–286.
Soto-Silva, W. E., Nadal-Roig, E., González-Araya, M. C., & Pla-Aragones, L. M. (2016). Operational research models applied to the fresh fruit supply chain. European Journal of Operational Research, 251 (2), 345–355.
Soysal, M., Bloemhof-Ruwaard, J. M., & Van Der Vorst, J. G. A. J. (2014). Modelling food logistics networks with emission considerations: The case of an international beef supply chain. International Journal of Production Economics, 152, 57–70.
Timperley, J. (2019). The carbon brief profile: India. Retrieved August 14, 2019, from https://www.carbonbrief.org/the-carbon-brief-profile-india .
Validi, S., Bhattacharya, A., & Byrne, P. J. (2014). A case analysis of a sustainable food supply chain distribution system—A multi-objective approach. International Journal of Production Economics, 152, 71–87.
Validi, S., Bhattacharya, A., & Byrne, P. J. (2018). Sustainable distribution system design: A two-phase DoE-guided meta-heuristic solution approach for a three-echelon bi-objective AHP-integrated location-routing model. Annals of Operations Research . https://doi.org/10.1007/s10479-018-2887-y .
Veeramachaneni, K., Peram, T., Mohan, C., & Osadciw, L. A. (2003). Optimization using particle swarms with near neighbor interactions. In Genetic and evolutionary computation conference (pp. 110–121). Springer, Berlin.
Vlajic, J. V., Van der Vorst, J. G., & Haijema, R. (2012). A framework for designing robust food supply chains. International Journal of Production Economics, 137 (1), 176–189.
Wang, F., Lai, X., & Shi, N. (2011). A multi-objective optimization for green supply chain network design. Decision Support Systems, 51 (2), 262–269.
Wang, X., Li, D., & Shi, X. (2012). A fuzzy model for aggregative food safety risk assessment in food supply chains. Production Planning & Control, 23 (5), 377–395.
Wisittipanich, W., & Hengmeechai, P. (2017). Truck scheduling in multi-door cross docking terminal by modified particle swarm optimization. Computers & Industrial Engineering, 113, 793–802.
Xu, J., Yan, F., & Li, S. (2011). Vehicle routing optimization with soft time windows in a fuzzy random environment. Transportation Research Part E: Logistics and Transportation Review, 47 (6), 1075–1091.
Yakavenka, V., Mallidis, I., Vlachos, D., Iakovou, E., & Eleni, Z. (2019). Development of a multi-objective model for the design of sustainable supply chains: The case of perishable food products. Annals of Operations Research . https://doi.org/10.1007/s10479-019-03434-5 .
Yamada, T., & Febri, Z. (2015). Freight transport network design using particle swarm optimisation in supply chain-transport supernetwork equilibrium. Transportation Research Part E: Logistics and Transportation Review, 75, 164–187.
Zhao, X., & Dou, J. (2011). A hybrid particle swarm optimization approach for design of agri-food supply chain network. In 2011 IEEE international conference on service operations, logistics, and informatics (SOLI) (pp. 162–167).
Zhu, Z., Chu, F., Dolgui, A., Chu, C., Zhou, W., & Piramuthu, S. (2018). Recent advances and opportunities in sustainable food supply chain: A model-oriented review. International Journal of Production Research, 56 (17), 5700–5722.
Zhu, Y., Ge, H., & Zhen, T. (2009). Hybrid particle swarm algorithm for grain logistics vehicle routing problem. In 3rd International symposium on intelligent information technology application, IITA 2009 , (Vol. 2, pp. 364–367).
Download references
Author information
Authors and affiliations.
Logistics and Operations Management, Cardiff Business School, Cardiff University, Cardiff, UK
D. G. Mogale
Department of Industrial and Systems Engineering, Indian Institute of Technology Kharagpur, Kharagpur, West Bengal, 721 302, India
Sri Krishna Kumar & Manoj Kumar Tiwari
National Institute of Industrial Engineering (NITIE), Mumbai, India
Manoj Kumar Tiwari
You can also search for this author in PubMed Google Scholar
Corresponding author
Correspondence to Manoj Kumar Tiwari .
Additional information
Publisher's note.
Springer Nature remains neutral with regard to jurisdictional claims in published maps and institutional affiliations.
1.1 Indices
Index for procurement centres, p = 1,2,…, P
Index for a potential location of base silos, b = 1,2,…, B
Index for a potential location of field silos, f = 1,2,…, F
Index for regional warehouse, r = 1,2,…, R
Index for destination warehouse, d = 1,2,…, D
Index for time period t = 1,2,…, T
Index for capacity of base silo, h = 1,2,…, H
Index for capacity of field silo, j = 1,2,…, J
Index for truck type present at procurement centre, \( n_{1} \) = 1,2,…, \( N_{1} \)
Index for rake type present at base silo, \( n_{2} \) = 1,2,…, \( N_{2} \)
Index for truck type present at field silo, \( n_{3} \) = 1,2,…, \( N_{3} \)
Index for truck type present at regional warehouse, \( n_{4} \) = 1,2,…, \( N_{4} \)
1.2 Model parameters
1.2.1 cost parameters.
Fixed cost of establishing the base silo with capacity h at location b
Fixed cost of establishing the field silo with capacity j at location f
Transportation cost from procurement centre p to base silo b (per MT per km)
Transportation cost from base silo b to field silo f (per MT per km)
Transportation cost from field silo f to regional warehouse r (per MT per km)
Transportation cost from regional warehouse r to destination warehouse d (per MT km)
Inventory holding cost at base silo b (per MT per period)
Inventory holding cost at field silo f (per MT per period)
Inventory holding cost at regional warehouse r (per MT per period)
Food grain lost cost (per MT)
Cost of ton of carbon dioxide emission
Risk penalty cost
1.2.2 Distance parameters
Distance between procurement centre p to base silo b
Distance between base silo b to field silo f
Distance between field silo f to regional warehouse r
Distance between regional warehouse r to destination warehouse d
1.2.3 Vehicle related parameters
Capacity of truck type \( n_{1} \)
Capacity of rake type \( n_{2} \)
Capacity of truck type \( n_{3} \)
Capacity of truck type \( n_{4} \)
Total number of \( n_{1} \) type trucks available at procurement centre p in period t
Total number of \( n_{2} \) type rakes available at base silo b in period t
Total number of \( n_{3} \) type trucks available at field silo f in period t
Total number of \( n_{4} \) type trucks available at regional warehouse r in period t
1.2.4 Procurement, demand, capacity and percentage of loss parameters
Amount of food grain quantity available at procurement centre p in period t
Demand of food grain of destination warehouse d in period t
Capacity of base silo type h
Capacity of field silo type j
Capacity of regional warehouse r
Transit loss of food grain if transported in bulk form
Transit loss of food grain if transported using conventional way of jute bags
Storage loss of food grain if stored in silos
Storage loss of food grain if stored in conventional warehouses
1.2.5 Emission parameters
Amount of CO 2 released per unit distance for each \( n_{1} \) type of truck travelling from procurement centre p to base silo b
Amount of CO 2 released per unit distance for each \( n_{2} \) type of rake travelling from base silo b to field silo f
Amount of CO 2 released per unit distance for each \( n_{3} \) type of truck travelling from field silo f to regional warehouse r
Amount of CO 2 released per unit distance for each \( n_{4} \) type of truck travelling from regional warehouse r to destination warehouse d
1.2.6 Risk related parameters
Establishment risk of locating base silo with size h at potential location b
Establishment risk of locating field silo with size j at potential location f
Risk of transportation between procurement centre p to base silo b
Risk of transportation between base silo b to field silo f
Risk of transportation between field silo f to regional warehouse r
Risk of transportation between regional warehouse r to destination warehouse d
1.3 Decision variables
1.3.1 binary variables.
1, if base silo type h is selected to be established at location b
0 Otherwise
1, if field silo type j is selected to be established at location f
1, if procurement centre p is assigned to base silo b in time period t
0, Otherwise
1, if base silo b is assigned to field silo f in time period t
1, if field silo f is assigned to regional warehouse r in time period t
1, if regional warehouse r is assigned to destination warehouse d in time period t
1.3.2 Continuous variables
Shipment quantity from procurement p to base silo b in period t
Shipment quantity from base silo b to field silo f in period t
Shipment quantity from field silo f to regional warehouse r in period t
Shipment quantity from regional warehouse r to destination warehouse d in period t
Fraction of shipment quantity that loss from procurement p to base silo b in period t
Fraction of shipment quantity that loss from base silo b to field silo f in period t
Fraction of shipment quantity that loss from field silo f to regional warehouse r in period t
Fraction of shipment quantity that loss from regional warehouse r to destination warehouse d in period t
Inventory in base silo b at the end of period t
Inventory in field silo f at the end of period t
Inventory in regional warehouse r at the end of period t
Fraction of inventory stock that loss in period t at base silo b
Fraction of inventory stock that loss in period t at field silo f
Fraction of inventory stock that loss in period t at regional warehouse r
1.3.3 Integer variables
Number of \( n_{1} \) type of vehicles used from procurement centre p to base silo b in time period t
Number of \( n_{2} \) type of rakes used from base silo b to field silo f in time period t
Number of \( n_{3} \) type of vehicles used from field silo f to regional warehouse r in time period t
Number of \( n_{4} \) type of vehicles used from regional warehouse r to destination warehouse d in time period t
Rights and permissions
Reprints and permissions
About this article
Mogale, D.G., Kumar, S.K. & Tiwari, M.K. Green food supply chain design considering risk and post-harvest losses: a case study. Ann Oper Res 295 , 257–284 (2020). https://doi.org/10.1007/s10479-020-03664-y
Download citation
Published : 08 June 2020
Issue Date : December 2020
DOI : https://doi.org/10.1007/s10479-020-03664-y
Share this article
Anyone you share the following link with will be able to read this content:
Sorry, a shareable link is not currently available for this article.
Provided by the Springer Nature SharedIt content-sharing initiative
- Food grain supply chain
- Food security
- Transportation
- Particle swarm optimization
- Find a journal
- Publish with us
- Track your research
Food Chains Cultivate Common Ground In Safety And Sustainability

- Share to Facebook
- Share to Twitter
- Share to Linkedin
Regulatory changes in both food safety and sustainability are increasingly impacting organizations across the supply chain from fruit and vegetable farmers to distributors and retailers.
On the food safety front, the US FDA traceability records rule takes effect in January 2026. Meanwhile, new sustainability regulations are emerging in regions including Europe and North America . Agribusiness experts shared the stage at the International Fresh Produce Association (IFPA) conference last fall to talk about their leading-edge preparations for compliance.
Technology helps every member of the farm-to-consume food chain modernize systems with connected data automation that reduces costs and improves results for sustainable business resilience.
Agribusiness has metric-based strengths for sustainability
Enacted to improve the FDA’s ability to rapidly track and trace food, the new US regulations raise the bar on traceability up and down the food supply chain. Leaders during the event drew parallels between the upcoming food safety rules and rising policymaker and consumer interest in sustainable business. The good news is that agribusiness has significant experience with the kind of metrics that sustainability-related reporting will increasingly require.
“As food safety professionals, we have a good eye on and understanding of what’s happening in the supply chain,” said Jennifer Pulcipher, director of food safety and compliance at North Bay Produce . “We’re plugged into different growing practices and have assessed their risks. Sustainability looks at different standards and reporting, and we’re already familiar with food safety audits.”
Food safety benchmarks align with sustainable value chains
Other panelists agreed that there’s significant overlap between food safety and sustainability tracking as regulations change for the latter from periodic certification to transaction-specific data and regular reporting.
Roberta Anderson, president of GLOBALG.A.P. North America , said that benchmarking was central to her organization’s mission. Best known for designing and operationalizing food safety standards, the company has widened its reach into areas including environmental sustainability, worker well-being, animal welfare, and supply chain transparency.
“We have customers in various markets that may want different comparisons and benchmarks. We participate in alignment activities to help them harmonize with other standards, which streamlines auditing and reduces duplication,” Anderson said.
Farmers provide sustainability expertise
Janis McIntosh, director of marketing innovation and sustainability at Naturipe Farms , said that farmers have been largely uncredited as the boots on the ground implementing sustainable farming practices for years. A farmer-owned producer and marketer of berries and avocados, Naturipe Farms created a task force with team leads by region that provide monthly sustainability updates and action items.
“We’re trying to capture, measure, and quantify everything that farmers are doing and articulate it, so retailers understand,” she said. “We’re spread out globally and get different questions from various types of retailers and consumers. We have an accounting firm, and we’re trying to figure out the best way to capture and report the data.”
Food safety lessons learned can conquer audit fatigue
Just as IFPA has played an active role in industry food safety groups like the Global Food Safety Initiative (GFSI), the association is collaborating in the same way through its Sustainable Supply Chain Initiative (SSCI). The group is developing a proposal for harmonized sustainability certifications across the fruit and vegetable farming supply chain.
“Audit fatigue is running high and it’s a huge challenge,” said Dr. Emily Moyer, vice president of regulatory compliance and global food safety standards at IFPA. “If you’re going to develop a sustainability standard, we need to agree on what those standard components should include.”
One major learning from food safety efforts is the importance of giving everyone along the sustainability supply chain a seat at the table.
“Food producers were often left out of the conversation when it came to food safety,” McIntosh said. “We need to bring everyone together, from retailer down to producers so we are on the same page, achieving something together to ensure the industry successfully moves forward.”
Technology is critical for sustainable business
After the event, I talked with Gary Decker, SAP’s North American industry advisor for agribusiness, who said there’s growing demand for technology that provides data transparency across the food chain.
“We see a broad need to operationalize the capture and generation data that supports auditability and reporting mandates,” Decker said. “Technology helps every member of the ‘grower-to-consumer’ food chain modernize systems with connected data automation that reduces costs and improves results for sustainable business resilience.”
How to protect consumers and the environment
Fresh fruits and vegetables are healthy for us until they’re not. Growers, packers, processors, and retailers have always been focused on regulatory compliance along with protecting consumers and the environment. As food safety regulations evolve, the entire value chain will work even closer together connecting data from fields to retailers to deliver food with the healthiest nutritional and sustainable business value.
Find out more about the data-driven future for fresh produce, from farmer to grocer.
- Editorial Standards
- Reprints & Permissions
Building Insights Into Supply Chains: A Case Study

Image: iStock.com/metamorworks
For time-sensitive or temperature-controlled cargo, most shippers will agree that high-quality, real-time tracking information is crucial. Though that technology can be expensive, the investment is easy to justify when it could mean the difference between an on-time delivery and spoiled cargo. But for general cargo — which does not have strict timeline requirements — it can be harder for shippers to justify that cost. Individualized tracking information simply isn’t as critical for those standard loads. And if shippers do decide to invest in tracking devices for general cargo, rarely is the technology advanced enough to make a sizable difference to their bottom line.
Some leaders in the shipping space argue that this view is shortsighted — and could cost companies far more than they realize. Without the data that tracking technology could provide, they believe, many shippers lose out on important insights into their general cargo — data that could significantly improve travel timelines and ultimately justify that initial cost.
Two of these leaders are Maersk, a provider of transportation and logistics services, and Tive, a global leader in supply chain and logistics visibility technology. Both organizations felt that the potential value of tracking insights into general cargo was too important to overlook. So when Erez Agmoni, global head of innovation at Maersk, and Krenar Komoni, founder and CEO of Tive, crossed paths at a supply chain event at MIT a few years back, it was no surprise that they found a common purpose.
Both Agmoni and Komoni knew that tracking technology was too costly to be used across every type of cargo. “Unless it’s valuable, perishable cargo,” says Agmoni, “nobody will want to just go and track every single container, every single shipment — especially considering a few years ago, when it was really expensive.” Agmoni and Komoni knew they needed to develop a more affordable solution that could provide data that was actually relevant to all types of general cargo shipments.
The Proof of Concept
In the years following the MIT event, Agmoni and Komoni explored alternatives that could offer the value they sought at a price point shippers would accept. The first step in their experiment was to design a proof of concept. The team at Maersk took on the task, beginning with outreach. “We went to customers, we brought them in, we started some discussions,” says Agmoni. “We looked into what could help them improve their supply chains.” Over the course of their research, customers commonly expressed frustration with transit times: They were unreliable, inaccurate, and did little to help them plan around the situation at hand. That’s when Agmoni had an idea. Instead of tracking each individual shipment — which, as customers were saying, wasn’t providing the information they actually needed — they could also track aggregated data.
The Maersk Innovation Center designed a proof of concept for a means of keeping tabs on thousands of shipments without having to view each one individually. In other words, they would track aggregated data from thousands of shipments, starting with a route from Los Angeles to Memphis. Tive, meanwhile, started building the hardware and the backend technology. Once the product was ready, Tive ensured that all of the trackers were properly installed at the warehouse in Los Angeles, and that each of them was linked to the appropriate shipment and order.
From there, Tive’s data science and data analytics teams, with input from Maersk, went to work analyzing the data from the trackers — looking at which algorithms they wanted to run on the dataset to figure out what insights they could gain. “Working together, we were able to find some really interesting things,” says Komoni. In the end, the higher-level view yielded surprising insights.
The Results
On the drive from Los Angeles to Memphis, there are two main routes from which truckers can choose: a southern route, which runs near the U.S.–Mexico border, and a northern route, which is a slightly more direct line from point A to point B. On all navigation systems, the northern route is estimated to be two hours faster than its counterpart. But when Maersk and Tive started looking at the aggregated data, they learned something that they couldn’t have known from individualized tracking information.
“When we started to look at the aggregated data,” says Agmoni, “we found out that the northern route is taking six days, plus or minus two — so four to eight days.” Though Google Maps will estimate the drive to be 32 hours, it’s expected that drivers will need to stop and rest along the way, stretching the trip out into several days. But when they looked at the presumably slower, southern route, the average driver was completing the trip in four to six days. Not only was this faster, but the driving estimate was more precise.
To understand why this was, they had to go back to the data. Using a collection of tools and graphs that they’d custom built for this purpose, Tive began to calculate the idle times along each route. “What we said is, ‘why don’t we figure out where the trucks are stopping for the longest time?’” says Komoni. “And then we mapped that out, and we saw these big red spots on areas where they’re stopping on the southern route and also where they’re stopping on the northern route.
”It quickly became clear from the data that drivers on the northern route were stopping much more frequently than on the southern route. “We couldn’t know why they’d do that,” says Agmoni, “so we had to call some of them. And we learned a very interesting thing.”
After speaking with some of the drivers, they learned that rest stops on the northern route are small and, more often than not, completely full. “It’s a very busy route,” says Agmoni. “They don’t trust that there will be space at the rest stop when they’ve reached the maximum hours of driving. So they start looking two or three stops beforehand. If there is one, they stop; if not, they’ll go to the next on the route.” On the southern route, however, the stops are more reliable. Drivers can trust that when they need to make a stop, there will be space for them to do so — allowing them to maximize the number of hours that they can drive, and shortening the total transit time altogether.“
That really helped us to change the way we route things. You can’t find this information if you follow one shipment at a time; you really need the aggregated data,” says Agmoni.
“It's great insight,” Komoni adds, “because now you finally have value that you can sell. You can justify the cost on all types of general cargo — and not just on time-sensitive, temperature-sensitive, high-value shipments.”
Maersk and Tive’s proof of concept was a clear success, allowing them to move forward in the development of their product.
The Solution
Using what they learned, Maersk has since developed a new product called Ocean + Transload, a solution for cargo transportation that improves transit time variability, reduces carbon emissions, and helps minimize detention and demurrage charges.
“It’s a replacement for the inland port solutions that carriers sell,” says Agmoni. Typically with intermodal travel, carriers see a lot of fluctuation in transit times. “The intermodal connection of international containers is not to the level of our customer expectation,” he says.
With Ocean + Transload, they can take containers and translate them into trailers by putting them back on the rail or on the road. “And of course we are adding visibility trackers to all those shipments at no extra cost — to provide our customers with a solution that first, gives them a much more precise time, and second, sends alerts way in advance when the shipment is about to arrive.” Armed with this increased visibility into their shipments, customers no longer need to follow up to receive updates on the status of their shipment. Updates come to them directly.
According to Komoni, the uniformity of the data made possible by the collaboration was a central component to the solution’s success. “I think that uniformity is the real value that allows Maersk to do aggregated analytics and understand insights for their customers. There is tremendous value in uniformity,” he says.
What started as a shared frustration at the lack of tracking information on general cargo shipments resulted in not only a successful collaboration between two companies — it also provided a much-needed advancement in tracking technology and shipping analytics that will help companies make smarter and more cost-efficient decisions across the supply chain.
RELATED CONTENT
RELATED VIDEOS
Five Critical Challenges Facing Pharma Supply Chains
Subscribe to our daily newsletter.
Timely, incisive articles delivered directly to your inbox.
Popular Stories
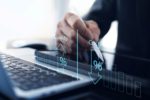
How Businesses Can Cut Supply Chain Costs Without Jeopardizing Long-Term Growth
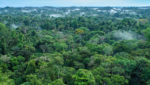
Fashion Brands Make Earth Day Commitment to Preserve Endangered Forests
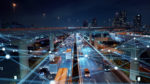
Why Planning Isn’t Enough to Achieve True Operational Excellence
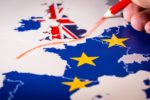
U.K. Brexit Import Checks Delayed, Causing Confusion
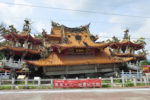
Taiwan Quake Was a Lesson in Resiliency for the Global Supply Chain
Digital edition.
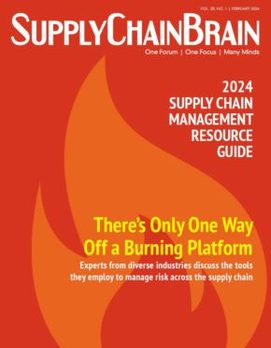
2024 Supply Chain Management Resource Guide: There's Only One Way Off a Burning Platform
Case studies, recycled tagging fasteners: small changes make a big impact.

Enhancing High-Value Electronics Shipment Security with Tive's Real-Time Tracking

Moving Robots Site-to-Site
Jll finds perfect warehouse location, leading to $15m grant for startup, robots speed fulfillment to help apparel company scale for growth.

An official website of the United States government
Here’s how you know
The .gov means it’s official. Federal government websites often end in .gov or .mil. Before sharing sensitive information, make sure you’re on a federal government site.
The site is secure. The https:// ensures that you are connecting to the official website and that any information you provide is encrypted and transmitted securely.
Take action
- Report an antitrust violation
- File adjudicative documents
- Find banned debt collectors
- View competition guidance
- Competition Matters Blog
New HSR thresholds and filing fees for 2024
View all Competition Matters Blog posts
We work to advance government policies that protect consumers and promote competition.
View Policy
Search or browse the Legal Library
Find legal resources and guidance to understand your business responsibilities and comply with the law.
Browse legal resources
- Find policy statements
- Submit a public comment
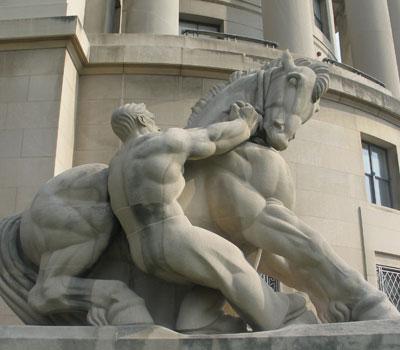
Vision and Priorities
Memo from Chair Lina M. Khan to commission staff and commissioners regarding the vision and priorities for the FTC.
Technology Blog
Consumer facing applications: a quote book from the tech summit on ai.
View all Technology Blog posts
Advice and Guidance
Learn more about your rights as a consumer and how to spot and avoid scams. Find the resources you need to understand how consumer protection law impacts your business.
- Report fraud
- Report identity theft
- Register for Do Not Call
- Sign up for consumer alerts
- Get Business Blog updates
- Get your free credit report
- Find refund cases
- Order bulk publications
- Consumer Advice
- Shopping and Donating
- Credit, Loans, and Debt
- Jobs and Making Money
- Unwanted Calls, Emails, and Texts
- Identity Theft and Online Security
- Business Guidance
- Advertising and Marketing
- Credit and Finance
- Privacy and Security
- By Industry
- For Small Businesses
- Browse Business Guidance Resources
- Business Blog
Servicemembers: Your tool for financial readiness
Visit militaryconsumer.gov
Get consumer protection basics, plain and simple
Visit consumer.gov
Learn how the FTC protects free enterprise and consumers
Visit Competition Counts
Looking for competition guidance?
- Competition Guidance
News and Events
Latest news, ftc finalizes changes to the health breach notification rule.
View News and Events
Upcoming Event
Commissioner bedoya speaks at loyola university school of law’s 24th annual loyola antitrust colloquium.
View more Events
Sign up for the latest news
Follow us on social media
--> --> --> --> -->
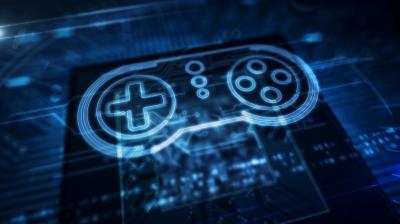
Playing it Safe: Explore the FTC's Top Video Game Cases
Learn about the FTC's notable video game cases and what our agency is doing to keep the public safe.
Latest Data Visualization
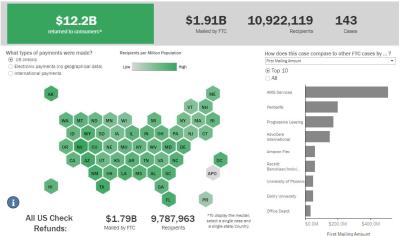
FTC Refunds to Consumers
Explore refund statistics including where refunds were sent and the dollar amounts refunded with this visualization.
About the FTC
Our mission is protecting the public from deceptive or unfair business practices and from unfair methods of competition through law enforcement, advocacy, research, and education.
Learn more about the FTC
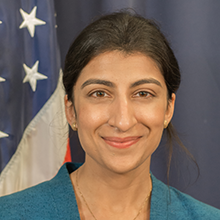
Meet the Chair
Lina M. Khan was sworn in as Chair of the Federal Trade Commission on June 15, 2021.
Chair Lina M. Khan
Looking for legal documents or records? Search the Legal Library instead.
- Cases and Proceedings
- Premerger Notification Program
- Merger Review
- Anticompetitive Practices
- Competition and Consumer Protection Guidance Documents
- Warning Letters
- Consumer Sentinel Network
- Criminal Liaison Unit
- FTC Refund Programs
- Notices of Penalty Offenses
- Advocacy and Research
- Advisory Opinions
- Cooperation Agreements
- Federal Register Notices
- Public Comments
- Policy Statements
- International
- Office of Technology Blog
- Military Consumer
- Consumer.gov
- Bulk Publications
- Data and Visualizations
- Stay Connected
- Commissioners and Staff
- Bureaus and Offices
- Budget and Strategy
- Office of Inspector General
- Careers at the FTC
FTC Releases Report on Grocery Supply Chain Disruptions
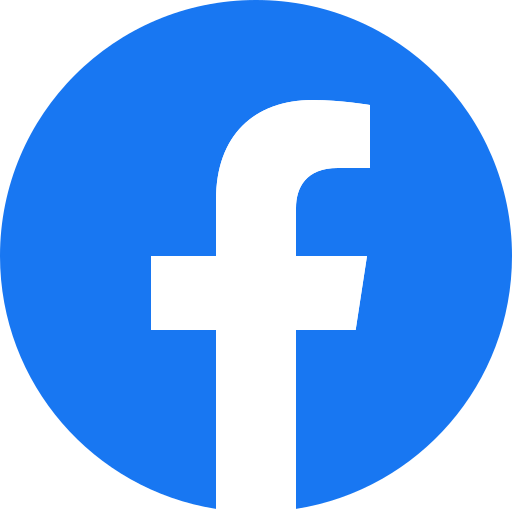
- Competition
- Office of Policy Planning
- Bureau of Competition
- Grocery/Supermarkets
The Federal Trade Commission today issued a report on the causes behind grocery supply chain disruptions resulting from the COVID-19 pandemic. The report revealed that large market participants accelerated and distorted the negative effects associated with supply chain disruptions.
The FTC’s report also examined how supply chain disruptions affected competition among retailers, wholesalers, and producers, as well as the impacts on consumers and businesses. The report found that consumers felt the negative effects of supply chain disruptions in the form of sky rocketing prices for groceries and product shortages for essentials, like toilet paper.
Notably, consumers are still facing the negative impact of the pandemic’s price hikes, as the Commission’s report finds that some in the grocery retail industry seem to have used rising costs as an opportunity to further raise prices to increase their profits, which remain elevated today.
“As the pandemic illustrated, a major shock to the supply chain can have cascading effects on consumers, including the prices they pay for groceries,” said FTC Chair Lina M. Khan. “The FTC’s report examining U.S. grocery supply chains finds that dominant firms used this moment to come out ahead at the expense of their competitors and the communities they serve.”
As the report explains, supply chain disruptions did not equally impact every retailer, wholesaler, or producer. Instead, smaller firms, especially smaller grocery retailers, disproportionately faced difficulties obtaining products compared to larger firms. Some larger firms were better able to protect their product supply compared to smaller competitors.
The pandemic also prompted some larger firms to consider buying manufacturing suppliers, which potentially threatens to make certain supply chains even more concentrated in the future. Taken together, the report’s findings reveal how supply chain bottlenecks can leave markets exposed to major supply chain shocks—and that those shocks, in turn, can allow major firms to entrench their dominance.
The report’s findings stem from orders the FTC issued in 2021 under Section 6(b) of the FTC Act to Walmart Inc., Amazon.com, Inc., Kroger Co., C&S Wholesale Grocers, Inc., Associated Wholesale Grocers, Inc., McLane Co, Inc. Procter & Gamble Co., Tyson Foods, Inc., and Kraft Heinz Co. The findings also draw from publicly available data on industry costs and revenues.
Competitive Impacts of Supply Chain Disruptions
The report highlights several key insights regarding market structure and business conduct among grocery retailers, wholesalers, and producers, as well as their effects on consumers. These insights include:
- Grocery retailer profits rose & remain elevated : Food and beverage retailer revenues increased to more than 6% over total costs in 2021, higher than their most recent peak in 2015 of 5.6%. In the first three-quarters of 2023, retailer profits rose even more, with revenue reaching 7% over total costs, casting doubt on the assertions of some companies that rising prices at the grocery store are the result of retailers’ own rising costs.
- Large purchasers sought favorable supplier allocations : Some companies, most often larger ones, re-imposed strict delivery requirements on their upstream suppliers during the height of the pandemic and threatened fines for noncompliance, pressuring suppliers to favor them over rivals. In some cases, suppliers preferentially allocated product to the purchasers threatening to fine, giving larger companies a competitive advantage over smaller retailers at a time when having products in-stock was a critical advantage for attracting customers.
- Excessive consolidation recognized as a liability : During the pandemic, some retailers sought to diversify their supplier base, particularly of private label goods, as firms recognized the risks associated with having few suppliers available. Some firms buying goods in markets with few suppliers even began exploring whether to build or acquire manufacturing capacity to reduce their exposure to concentrated markets. The report warns, however, that moves by larger customers to buy one of the few remaining market participants rather than building that capability from scratch could leave the remaining buyers, notably smaller competing firms, even worse off.
- Decrease in promotional spending : During the pandemic, manufacturer promotional spending on items in short supply declined. Companies employing the more traditional grocery retailing model that relies on manufacturer promotional spending to lower prices for products sometimes faced higher prices compared to other companies. Companies that used an “Every Day Low Price” (EDLP) strategy, in which producers consistently provide low wholesale prices rather than short-term promotional price reductions, were less affected when manufacturer promotional spending was curtailed.
The Commission voted 3-0 to issue the staff report.
Commissioner Rebecca Kelly Slaughter issued a statement .
The Federal Trade Commission develops policy initiatives on issues that affect competition, consumers, and the U.S. economy. The FTC will never demand money, make threats, tell you to transfer money, or promise you a prize. Follow the FTC on social media , read consumer alerts and the business blog , and sign up to get the latest FTC news and alerts .
Press Release Reference
Contact information, media contact.
Victoria Graham Office of Public Affairs 415-848-5121

IMAGES
VIDEO
COMMENTS
These publications are part of a series of case studies and Research Briefs examining values-based food supply chains—strategic business alliances formed between primarily midsize farms/ranches and their supply chain partners. Values-based food supply chains distribute significant volumes of high-quality, differentiated food products and ...
1.3 Objectives of the study. The objective of the research is to explore the extent of adoption of supply chain management (SCM) practices employed in a food supply chain within an SME. The specific objectives of the study are: 1. To provide insight for the development of a supply chain design suited for SMEs.
Discover how Walmart is revolutionizing food traceability using blockchain technology. By implementing a Hyperledger Fabric-based system, Walmart has reduced the time it takes to trace the provenance of products from days to seconds, enhancing transparency and safety in the food supply chain. Read the Walmart case study now.
The case study analysed in this paper derives from the food sector, in which the waste produced is reused as a resource, avoiding the disposal of different materials through resource-recovery activities that allow waste to be returned to the main supply chain as valuable inputs to configure a new supply chain.
The interest in short food supply chains (SFSCs) has grown significantly in the last decade, notably in respect of their potential role to achieve more sustainable food chains. However, a major barrier to achieving sustainable supply chains is the uncertainty associated with supply chain activities. Therefore, this paper aims to explore the different resilience capabilities that SFSCs possess ...
Design/methodology/approach. The paper presents a comprehensive review of the literature on food sustainable supply chain management (FSSCM). Using systematic review methods, relevant studies published from 1997 to early 2021 are explored to reveal the research landscape and the gaps and trends.
Taking into account that the analysis of a supply chain as a whole is a complex and difficult task and in order to explore the SSCM critical factors, practices and performance in the food industry, a case study was selected as the most appropriate research method [27,28]. This study investigates a sustainable supply chain in order to capture ...
The downstream distribution of food products to retailers or drop-off points plays a significant role in the environmental performance of food supply chains. Efficient logistics and technologies are critical success factors for distribution systems in most supply chain networks, including food (Tarantilis et al., 2005).
Taking into account that the analysis of a supply chain as a whole is a complex and difficult task and in order to explore the SSCM critical factors, practices and performance in the food industry, a case study was selected as the most appropriate research method [27,28].
In spite of the increasing attention being paid to short food supply chains (SFSCs), research in the area is still scarce, particularly in Portugal. Thus, based on a case study in Viseu Dão Lafões Region (VDLR), we intend to identify and discuss (emphasizing potentialities and constraints) the movement of SFSCs in the region. This case study is based on document analysis and interviews with ...
The emergence of big data (BD) offers new opportunities for food businesses to address emerging risks and operational challenges. BD denotes the integration and analysis of multiple data sets, which are inherently complex, voluminous and are often of inadequate quality and structure. While BD is a well-established method in supply chain management, academic research on its application in the ...
The case study suggests that a collaboration between different types of chains and supply chain-rural community nexus will promote the transformation of agri-food systems to be more sustainable. In summary, knowing the whole system by observation and inquiry offers opportunities for intervention at the system level.
1. ]. The United States is one of. the world's top producers of fresh tomatoes. With 0.97 million metric tons of production. valued at $1 billion USD in 2021, fresh tomato is the highest-valued ...
Contains detailed case studies of blockchain implementation processes within three pioneering food companies; Applies the multiple case study method to deeply investigate blockchain implementations in real-world context; Provides insights into the latest academic research on blockchain and food supply chain management
This paper provides a critical analysis of the UK food supply chain and its implications for the economy, society and the environment, using a sustainability assessment model. A set of sustainability indicators is proposed to measure the effects of the food supply chain, comprising stages of agriculture, food processing, food wholesaling, food ...
In this study, we examine the impact of the COVID-19 pandemic on food retail supply chains (SCs) and their resilience. Based on real-life pandemic scenarios encountered in Germany, we develop and use a discrete-event simulation model to examine SC operations and performance dynamics with the help of anyLogistix digital SC twin.
In this paper, considering the actual supply chain of an Iranian company, the disruptive obstacles that the pandemic can create against properly undertaking activities in a food supply chain, are investigated. The examined obstacles are ranked and prioritized using the Analytical Network Process (ANP) technique.
The purpose of this study is twofold: firstly, to provide a literature review of sustainable supply chain management (SSCM) critical factors, practices and performance; and secondly, to develop a comprehensive and testable model of SSCM in the food industry. The research conducted comprises a literature review and a case study. The literature review findings propose a theoretical framework ...
11 Case Studies of Supermarkets and Food Supply Chains in Low-Income Areas of the Northeast, and cross-case comparisons. Conducted by members of the EFSNE Distribution Team. All case studies were written by Kristen Park, Miguel Gómez, and Kate Clancy. Published by Cornell University in conjunction with the EFSNE project and the Northeast Regional Center for Rural Development.
The proposed conceptual framework is found to be useful for measuring performance of the tomato supply chain. From the case study it is concluded that four main categories of performance measures (i.e. efficiency, flexibility, responsiveness, and food quality) are identified as key performance components of the tomato supply chain performance ...
Purpose This paper aims to investigate how blockchain has moved beyond cryptocurrencies and is being deployed to enhance visibility and trust in supply chains, their limitations and potential ...
From live case studies, we provide empirical evidence that blockchain provides visibility of exchanges and reliable data in fully digitised supply chains. This provides provenance and guards against counterfeit goods. However, firms will need to work to gain consumer buy-in for the technology following repeated past claims of trustworthiness.
Application of fuzzy optimization to a supply chain network design: A case study of an edible vegetable oils manufacturer. Applied Mathematical Modelling, 36(6), 2762-2776. Google Scholar Parwez, S. (2014). Food supply chain management in Indian Agriculture: Issues, opportunities and further research.
Regulatory changes in both food safety and sustainability are increasingly impacting organizations across the supply chain from fruit and vegetable farmers to distributors and retailers.
Exploratory Study on Hyperledger Fabric Framework: Food Supply Chain as a Case Study. August 2023. International Journal of Engineering and Manufacturing 13 (4):11-19. DOI: 10.5815/ijem.2023.04.02 ...
Both organizations felt that the potential value of tracking insights into general cargo was too important to overlook. So when Erez Agmoni, global head of innovation at Maersk, and Krenar Komoni, founder and CEO of Tive, crossed paths at a supply chain event at MIT a few years back, it was no surprise that they found a common purpose.
The Federal Trade Commission today issued a report on the causes behind grocery supply chain disruptions resulting from the COVID-19 pandemic. ... Studies; Testimony; Policy Statements; International; ... Food and beverage retailer revenues increased to more than 6% over total costs in 2021, higher than their most recent peak in 2015 of 5.6% ...