
An official website of the United States government
The .gov means it’s official. Federal government websites often end in .gov or .mil. Before sharing sensitive information, make sure you’re on a federal government site.
The site is secure. The https:// ensures that you are connecting to the official website and that any information you provide is encrypted and transmitted securely.
- Publications
- Account settings
Preview improvements coming to the PMC website in October 2024. Learn More or Try it out now .
- Advanced Search
- Journal List
- Sensors (Basel)


Design and Modeling of a Test Bench for Dual-Motor Electric Drive Tracked Vehicles Based on a Dynamic Load Emulation Method
1 State Key Laboratory of Fluid Power and Mechatronic Systems, Zhejiang University, Hangzhou 310027, China; nc.ude.ujz@ehzw (Z.W.); nc.ude.ujz@108lhl (H.L.); nc.ude.ujz@mznrehc (Z.C.)
Haoliang Lv
Xiaojun zhou, zhaomeng chen.
2 Beijing Institute of Astronautical Systems Engineering, Beijing 100076, China; moc.liamg@repapgnoyy
Dual-motor Electric Drive Tracked Vehicles (DDTVs) have attracted increasing attention due to their high transmission efficiency and economical fuel consumption. A test bench for the development and validation of new DDTV technologies is necessary and urgent. How to load the vehicle on a DDTV test bench exactly the same as on a real road is a crucial issue when designing the bench. This paper proposes a novel dynamic load emulation method to address this problem. The method adopts dual dynamometers to simulate both the road load and the inertia load that are imposed on the dual independent drive systems. The vehicle’s total inertia equivalent to the drive wheels is calculated with separate consideration of vehicle body, tracks and road wheels to obtain a more accurate inertia load. A speed tracking control strategy with feedforward compensation is implemented to control the dual dynamometers, so as to make the real-time dynamic load emulation possible. Additionally, a MATLAB/Simulink model of the test bench is built based on a dynamics analysis of the platform. Experiments are finally carried out on this test bench under different test conditions. The outcomes show that the proposed load emulation method is effective, and has good robustness and adaptability to complex driving conditions. Besides, the accuracy of the established test bench model is also demonstrated by comparing the results obtained from the simulation model and experiments.
1. Introduction
Tracked vehicles, with their advantages of perfect dynamic performance under complicated driving conditions, are widely used in agriculture, construction, the military and many other fields. Compared with traditional tracked vehicles, dual-motor electric drive tracked vehicles (DDTVs) have been attracting increasing attention due to their high transmission efficiency, economical fuel consumption, silent driving performance and easy maintenance.
Currently, many advanced control technologies related to hybrid powertrain system have been successfully applied to passenger cars, while the applications for tracked vehicles are relatively narrow and immature. In this case, scholars have undertaken a large number of related studies, where they most concentrate on the drive control strategy (DCS) of the dual-motor under different driving conditions [ 1 , 2 , 3 , 4 ], and the energy management strategy (EMS) for power distribution such as the rule-based control strategy [ 5 ] and the optimization-based control strategy [ 6 , 7 , 8 , 9 ]. However, these strategies must be validated by other methods before they are accepted and equipped on real vehicles. Verification is an inevitable process to provide a reliable scientific basis for the development of vehicle technologies or products. Currently, the validation of DCS is mostly conducted by real road tests [ 2 , 10 ], and the verification of EMS is mainly based on software simulations [ 7 , 8 ].
There are mainly three ways for verification, namely system simulations based on software such as ADVISOR, CRUISE and RECURDYN [ 11 , 12 , 13 ], bench tests and real road tests [ 10 , 14 ]. Software simulation has the advantages of low cost, high efficiency and flexibility, but the complex structure of tracked vehicles makes it difficult to accurately mathematically model or describe them. Usually, an extra validation procedure is needed after the software simulation. As for real road tests, they incur in high costs to build the specified test ground and have a limited range of testing conditions though they have perfect fidelity. Bench tests, a combination of the above two ways, are regarded as a flexible and efficient approach that enables researchers to conduct a large bandwidth experiments just by simply reconfiguring the bench parameters corresponding to different test purposes. In this way, it is possible for researchers to study and evaluate new technologies in academic environments [ 15 ].
Bench tests can not only shorten the development cycle of new vehicle technologies but also reduce the test cost. However, the design of a test bench itself can be very complicated. At present, there are many references focusing on the construction of test benches for hybrid electric passenger cars [ 16 , 17 , 18 , 19 , 20 ]. As for tracked vehicles, the existing literature concerned with test benches is still scarce, and the few accessible investigations mainly concentrate on traditional tracked vehicles [ 21 , 22 ]. In this case, the development of new technologies for DDTVs may be affected. Hence, a test bench for DDTVs is both necessary and urgent.
In terms of DDTV test benches, emulation of the dynamic load may be the most critical part. A test bench should have the ability of emulating the loads the same as those when the vehicle runs on a real road to guarantee that real-time constraints can be matched. On the condition that the load emulated on a test bench is similar to a real-road one within a certain accuracy range, results obtained from the test bench could be reasonable and acceptable.
When a DDTV runs on a real road, the main load is composed of two parts. One is the road load, which is caused by the whole resistive forces opposing the vehicle’s motion, consisting of rolling friction resistance, aerodynamic drag and grading resistance. The other one is the inertia load caused by the vehicle’s mass, and emerges in the acceleration or deceleration driving conditions. A DDTV test bench should be capable of emulating both the road load and inertia load. Drum test benches used to be widely applied in the performance investigation of wheeled vehicles [ 23 ]. However, with the development of electric and control techniques, test benches increasingly use dynamometers to achieve better load emulation performance. Dynamometers perform well in static load tests of machines, but for testing variable speed drives, static load tests are not sufficient and dynamic load tests are required [ 24 , 25 ]. Usually, on a drive-line test bench, the dynamometer is utilized to emulate the road load, and the flywheel disks provide adjustable inertias and are used for emulating the inertia load [ 26 , 27 ]. Nevertheless, researchers have found that flywheel boxes with large inertia, high working speed and high dynamic balance requirement, are hard to manufacture and have safety risks [ 13 ]. In addition, different tested vehicles have different inertias, resulting in the reconfiguration of the flywheel disks to match the desired one. The fact that the inertias of flywheel disks are in discrete sizes will make the reconfiguration troublesome [ 28 , 29 ]. In this case, the flywheel box is usually eliminated, and instead, the dynamometer is controlled to emulate both the inertia load and the road load simultaneously.
There are several approaches to controlling dynamometers for dynamic load emulation. The inverse mechanical-dynamics (IMD) principle used to be widely applied due to its easy implementation [ 24 , 30 ]. However, in view of the sampling effects of digital microprocessors, the output of the inverse model will be noisy due to the existence of the derivative terms in the inverse transfer function. An approach with compensator based on system transient response is introduced in reference [ 31 ]. This compensator can be fully designed by applying parametric system identification to experimental data from transient system step tests. This method shows good performance for fast dynamics emulation at high speeds. References [ 32 , 33 , 34 ] have conducted adequate research on a nonlinear approach with the PI estimator, this method makes it more robust towards impacts of parameter variations and unmolded dynamics. It is designed to investigate unknown friction dynamics in the test bench and to compensate nonlinear friction. This paper presents a speed tracking algorithm with feedforward compensation. It applies a feedback controller together with a feedforward compensator for the calculation of demand load torque of the dynamometer [ 35 , 36 ]. The method can preserve the real road load model dynamics when used in a closed-loop system.
The aim of this work is to investigate the creative application of this dynamic load emulation method on the design of a DDTV test bench featuring high power and large inertia. It will be a reference for potential researchers in related field. Additionally, a MATLAB/Simulink model of the DDTV test bench is established based on detailed derivation of the system dynamics.
The organization of this paper is as follows. In Section 2 , the structure of a series DDTV is introduced. In Section 3 , road resistance model of a DDTV is built and the vehicle’s total equivalent rotational inertia calculated at the drive wheel is performed. Platform design, dynamic load emulation method, control strategy and test bench system modeling are illustrated in Section 4 . Section 5 introduces the experiment system, including general setup of the bench, important device parameters and different test contents. Section 6 shows the experimental results under different test conditions for the effectiveness validation of the proposed method and the accuracy verification of the established test bench model. Finally, conclusions are given in Section 7 .
2. Structure of a DDTV
The hybrid powertrain system is usually divided into three types according to their different structures. They are series systems, parallel systems and serial-parallel systems [ 37 ]. This paper focuses on a series DDTV and its schematic structure is shown in Figure 1 . Two tracks are attached to corresponding drive wheels. The dual drive wheels are separately driven by two permanent magnet synchronous motors (PMSM). Electric energy of these two motors is provided by the engine-generator set (EGS) and the energy storage unit (battery pack or supercapacitor). In this case, the vehicle’s dynamic performance features like acceleration, steering and braking could be achieved by independently controlling the dual side motors. The integrated power control unit is used for power allocation between the EGS and energy storage unit, thus ensuring the superior fuel economy.

Schematic diagram of a DDTV structure.
3. Analysis of DDTV Dynamics
3.1. longitudinal dynamics analysis.
There are three kinds of forces acting on a DDTV when running on a real road. They are the driving force provided by drive motors, braking force offered by a mechanical brake device or drive motor (in regenerative braking), and road resistance. The longitudinal dynamics equation can be denoted as:
where F d , F R refer to the driving force and road resistance, respectively, N. F f , F s , F w are the rolling friction resistance, grading resistance and aerodynamic drag, N. m is the vehicle mass, kg. f is the rolling friction resistance coefficient. g is the gravity, m/s 2 , θ is the slope angle, rad. ρ is the air density, Ns 2 /m 4 . C D is the coefficient of aerodynamic drag, v is the vehicle running speed, km/h. A is the frontal area of the vehicle, m 2 .
For convenient analysis, these forces are multiplied by the radius of drive wheel ( R ), thus converting to the corresponding torques acting on the drive wheels:
where T d ¯ , T R ¯ denotes the drive torque and road resistance torque, respectively, Nm. T i ¯ = J e r i t o t a l ¯ d ω r d t is inertia torque. J e r i t o t a l ¯ is the total equivalent rotational inertia (ERI) of the vehicle calculated at drive wheels, kg·m 2 . ω r is the rotational speed of drive wheel in rad/s.
Equation (3) indicates that when a DDTV runs on a real road, the main load is composed of two parts. One is the road load caused by the road resistance torque. The other one is the inertia load caused by the vehicle’s mass, and emerges in the acceleration or deceleration driving conditions.
From references [ 15 , 38 ], we know that under the same standard driving cycle, inertia torque shows more intense transient changes than road resistance torque, meanwhile, the inertia torque is usually larger than the road resistance torque when a sudden change in vehicle speed occurs. Given these facts, it is crucial to rigorously take inertia torque into consideration for getting accurate test results while emulating real-road driving conditions on a DDTV test bench.
3.2. Calculation of Equivalent Rotational Inertia
According to Equation (3), the inertia torque has a close relationship with the total ERI, so when calculating the inertia torque, a more accurate value of the total ERI is required. A DDTV mainly consists of three components including the body, tracks and wheels, as shown in Figure 2 . When a DDTV runs on a real road, the total kinetic energy is made up of the translational kinetic energy stored in the moving body and the rotational kinetic energy stored in the wheels and tracks. It is worth noting that the track of a DDTV accounts for a relatively large proportion of vehicle weight. Moreover, the speed of each part is not the same due to its irregular shapes, so its rotational kinetic energy should not be ignored [ 21 ]. In this case, the equivalent rotational inertia of the body, tracks and wheels calculated at the drive wheel are implemented separately in this work based on the kinetic energy conservation theory.

Schematic diagram of forces acting on track and wheels.
(1) The ERI of Vehicle Body
According to the energy conservation theory, the relationship between translational kinetic energy and rotational kinetic energy can be expressed as follows:
Subsequently, the ERI of the vehicle body calculated at the drive wheel can be obtained:
where, R is the radius of drive wheel, m. m is the mass of vehicle body, V v is the speed of body, m/s, the same as the vehicle running speed V . J e r i b represents the ERI of the vehicle body calculated at the drive wheel.
(2) The ERI of Track
A track is divided into four parts for individual analysis of the ERI calculated at the drive wheel because of different dynamic characteristics. They are the upper part, the lower part, the front part, and the rear part. Since the lower part is always attached to the ground, it has no translational kinetic energy as well as rotational kinetic energy, The ERI of this part can be neglected. As for the other three parts, taking the front part as an example to introduce the calculation method. The schematic diagram of forces acting on the front part is shown in Figure 2 . The dynamic equations can be described as follows:
Subsequently, the ERI of the front part of the track calculated at the drive wheel can be obtained:
where, v t _ f ⇀ , v t _ f c ⇀ , v t _ f r ⇀ refer to the absolute speed, pulling speed and relative speed, respectively, m/s. m t _ f is the mass of the front part of the track. J e r i t _ f represents the ERI of the front part track calculated at the drive wheel. φ A is the approach angle of the track.
ERI of the other two parts of the track calculated at the drive wheel is acquired using the same method above. The results are:
where, m t _ u , m t _ r are respectively the mass of the upper part track and the rear part track. J e r i t _ u , J e r i t _ r represent the ERI of the upper part track and the rear part track calculated at the drive wheel, respectively. φ D is the departure angle of the track.
Based on the Equations (7)–(9). The ERI of single-side track calculated at drive wheel can be denoted as:
(3) The ERI of Roadwheels
A roadwheel of a tracked vehicle is ring-shaped and its mass is concentrated on the edge of the wheel. The dynamic equations can be described as follows:
Then, the ERI of roadwheels calculated at the drive wheel can be obtained:
where, m r is the mass of the roadwheel. ω r w is the speed of the roadwheel. r 1 , r 2 are the radius of the outer circle and inner circle, respectively. J r is the rotational inertia of the roadwheel. n r is the number of roadwheels equipped on a single-side track. J e r i r represents the ERI of the whole single-side roadwheels calculated at the drive wheel.
According to Equations (5), (10) and (12), the total ERI of a DDTV calculated at the dual-side drive wheels is:
4. Modelling the Test Bench System
4.1. design of the test bench.
The schematic diagram of the designed DDTV test bench is shown in Figure 3 . Due to symmetrical arrangement of the system, only the left side is displayed in this figure. From the figure, it is clear that the test bench is composed of the vehicle drive system and the load emulation system. The vehicle drive system is the test object. The load emulation system consists of the dynamometer, gearbox, transmission shaft, torque sensors and speed sensors.

Schematic diagram of the DDTV test bench (The left side is only displayed due to symmetrical arrangement of the test bench).
Generally, a test bench should have the ability of emulating a large range of dynamic loads because of different type of the tested vehicles or different test conditions. For example, the dynamometer needs higher torque performance to emulate the dynamic load under the driving condition of acceleration or steering than that under the driving condition of uniform speed. If the dynamometer connects directly to the drive system, the rated torque of the dynamometer is always chosen according to the required peak load torque. In this case, it will apparently enhance the expenses of the dynamometer. Hence, a gearbox is added between the dynamometer and the drive system in this work. The gearbox adopts spray oil to lubricate the rolling bearings and meshing gears. It must be pointed out that ratio and inertia of the gearbox are the only two factors considered in this paper. Other gearbox dynamics, such as backlash which will bring about slight nonlinear effect to transmission system [ 39 ], is assumed to be negligible. The torque sensor is arranged at the end of the output shaft connected to the vehicle’s drive wheel so that the output drive torque of the vehicle can be measured directly. Additionally, the double-diaphragm coupling is used for linking the shafts because of its superior performance on eliminating the concentricity deviation which inevitably occurs in long shaft transmission.
4.2. Speed Tracking Method
When developing a test bench for a DDTV, the design of its control system is important. Accurately emulating the dynamic load of a vehicle when it runs on a real-road on a test bench is the most crucial issue. In this work, both the road load and the inertia load are emulated by dynamometer taking a single side drive wheel as the analysis object:

The transfer function model of the vehicle. ( a ) On a real road; ( b ) on a test bench.
- (2) On the other hand, when a DDTV is tested on a bench, the transfer function model of the vehicle is shown in Figure 4 b, and can be described as: ω t ( s ) T d ( s ) − [ T D ( s ) + T n ( s ) ] = G t ( s ) (15) where, ω t is the actual speed of drive wheel on the test bench in rad/s, here we call it actual speed. T D is the load torque imposed by the dynamometer, T n is the frictional resistance torque of the platform transmission system, mainly consists of bearing viscous friction, sliding friction caused by gear teeth meshing and wind friction.
The primary purpose of load emulation on a test bench is to ensuring that the Equation (14) and the Equation (15) are equivalent. To achieve this goal, inverse mechanical-dynamics (IMD) principle and speed tracking method are usually applied:
(1) IMD Principle
As for IMD principle, its control schematic diagram is shown in Figure 5 , the goal is to ensure the relationship between the actual speed ω t and the drive toque T d on a test bench results in the dynamics given by Equation (14). Thus, the load torque T D can be easily obtained by Equation (16). This method is simple and can give good results in continuous time. While, in view of the sampling effects of a digital microprocessor, the output of the inverse model will be noisy because of the existence of the derivative terms in the inverse transfer function. Besides, the system would be instable if the desired emulated vehicle inertia was twice larger than the inertia of the test bench itself [ 40 ]:

Control schematic diagram of IMD principle.
Due to the wide range of the desired emulated inertias of different tested DDTVs, the IMD principle method is inaccessible as it only performs well when the desired emulation inertia is two times less than that of the test bench. Therefore, in this work, we apply the speed tracking method for load emulation. Based on the original theory proposed by Hakan et al. [ 35 , 41 ], a speed tracking method with feedforward compensator is presented, the principle of this method is shown in Figure 6 .

Control schematic diagram of speed tracking method.
(2) Speed Tracking Method
In Figure 6 , C ( s ) and G c o m p ( s ) are, respectively, the feedback controller and feedforward compensator. They are used for the speed control of the dynamometer. In this method, the drive torque T d is applied to drive a desired dynamic G r ( s ) for obtaining the reference speed ω r , and this speed should be followed by the actual rotation speed ω t of the test bench. By comparing the reference speed ω r and the actual speed ω t , the feedback controller C ( s ) outputs the reasonable dynamometer torque T D .
According to Figure 6 , the dynamic model of the test bench can be denoted as:
when the feedforward compensator is designed as G c o m p ( s ) = [ C ( s ) G t ( s ) 1 + C ( s ) G t ( s ) ] − 1 , the actual speed ω t can track the reference speed ω r in real time. Thus, Equation (14) is equivalent to Equation (17). Remarkably, G c o m p ( s ) just contains the parameters of the test bench system itself and has nothing to do with the parameters of the tested vehicle, which makes the compensator constant in spite of different tested specimens. In addition, this method can preserve the pole–zero structure of the desired system dynamics and suitable for discrete-time applications [ 18 , 38 ].
4.3. System Modeling
According to Section 4.2 , the transfer function of the test bench itself should be known when implementing the speed tracking method. Since the components of the left-side test bench are the same as those of the right-side, the single side system is taken as an example for modeling and analysis, the system schematic diagram is shown in Figure 7 .

Dynamics of a single side test bench.
4.3.1. Vehicle Drive System
In any speed tracking control strategy, the reference speed plays an important role. The actual speed can perfectly track the reference speed provided that the reference speed is known ahead of time. Given the fact that the reference speed is related to the drive torque derived from the drive system, it is necessary to analyze this system.
The drive system of a DDTV consists of driver operation devices such as the acceleration pedal and braking pedal, and dual-drive motors. The driver’s intention can be explained as the required speed or torque of the drive motor. Usually, a wheel-side reducer exists between the drive motor and drive wheel. Thus, the output drive torque of the drive system can be denoted as:
where, T m ( l , r ) represents the torque of the left and right side drive motor, respectively. i w r is the ratio of the wheel-side reducer. The output torque T d ( l , r ) of the left and right side drive system are measured by two torque sensors, thus the reference speeds can be calculated by Equation (19):
where, T R ( l , r ) is the road resistance torque of the left and right side drive wheel. J e r i l ¯ , J e r i r ¯ are respectively the ERI of the vehicle calculated at the left and right side drive wheel. δ l , δ r are the ERI distribution coefficient. In this paper, we focus on the straight-line running, therefore, δ l = δ r = 0.5. That is to say, the ERI is equally distributed to the two side drive wheels.
4.3.2. Load Emulation System
As for the load emulation system, the dynamics can be represented as:
Implementing Laplace transformation on Equation (21), the transfer function of the system can be expressed as:
where, J t = J g b + J D + J c , J g b and J D are the rotational inertias of the gear box and dynamometer, respectively. J c is the total rotational inertia of the shaft attachments composed of the double-diaphragm couplings, shafts and torque sensors. B is the damping coefficient of the load emulation system. These parameters can be obtained from the product introduction or using system identification method [ 40 ].
The frictional resistance torque T n is a nonlinear factor in this system. But it has nearly no effect on the system dynamics given the fact that the friction torque is much smaller than the drive torque and load torque since the tested DDTV is of high inertia and high power. For simplicity, the nonlinear impact of this friction torque is neglected, and its value is assumed to be zero in this work.
Torque response of the dynamometer is assumed to be a first order plus time delay model:
where, T D ( l , r ) is the actual output torque of the left and right dynamometer, T D ( l , r ) * is the desired torque of the left and right dynamometer given by the controller. τ is a constant, denoting the torque response time of dynamometer.
4.4. Control Strategy and Simulink Model
The structure of control strategy for the bench system is displayed in Figure 8 . Its working principle can be described as follows: first, the two side drive torques T d ( l , r ) and the test bench actual speeds ω t ( l , r ) are measured by torque sensors and speed sensors, respectively. The drive torques are subsequently used for the calculation of the reference speeds w r ( l , r ) . Next, the speed tracking controllers generate the target torque commands T D ( l , r ) * to the dual side dynamometers based on the difference of the current actual shaft speeds and reference speeds, to ensure the actual shaft speeds capable of tracking the reference speeds in real time. The speed tracking controller is a PID controller here. Figure 9 is the corresponding MATLAB/Simulink model of the single side test bench.

The structure of control strategy of the test bench.

MATLAB/Simulink model of the single side test bench.
5. Experiment System Introduction.
5.1. general setup.
Figure 10 shows the designed test bench in this work. From a testing standpoint, the platform is mainly composed of two systems, the hardware system and the control system. The hardware system consists of two three-phase asynchronous squirrel-cage motors and their corresponding AC drives, two gearboxes and power resource. The asynchronous squirrel-cage motor with maximum power of 1200KW acts as the dynamometer to emulate the road load and the inertia road at the same time. The type of the AC drive is the ACS880 (ABB, Zurich, Switzerland). The control system mainly consists of a Siemens industrial personal computer (IPC, Berlin, Germany), a PXI chassis (National Instruments, Austin, TX, USA), two torque sensors (GIF, Alsdorf, Germany. 0~50,000 Nm, 0.1% FS) and other sensors.

Block diagram of the test bench.
Real-time communication of the devices are realized by a controller area network bus (CAN bus). The test bench uses CAN protocol to integrate the IPC, double-side AC drives and sensors, ensuring the synchrony of the torque commands and read back the real-time torque and speed. A PXI chassis is used for real-time data acquisition. An IPC is employed for building and executing the vehicle model as well as implementing the control strategies. The test software is developed on the NI LabVIEW platform (version 15.0, National Instruments Inc., Austin, TX, USA). This software has plentiful functions such as real-time monitoring and displaying, as well as convenient data acquisition, processing and preservation.
5.2. Device Parameters
In this work, major parameters of the tested DDTV and the established test bench are listed in Table 1 .
Major parameters of the tested DDTV and test bench.
5.3. Test Contents
In order to validate the effectiveness of the proposed load emulation method, several experiments with different contents were carried out. The detailed testing groups are shown in Table 2 , the test contents were designed for the following three aims. Firstly, in the first and the second group, the driving conditions were set the same while the vehicle mass were different, just for studying the robustness of the proposed method. Next, in the second to the third group, the vehicle mass was set the same while the driving conditions were different, just for studying the adaptability of the method to complex driving conditions. Finally, the test results from group 1 and group 2 are compared with the results obtained from simulation for verifying the accuracy of the established test bench Simulink model.
Test contents.
6. Results and Discussion
6.1. effectiveness validation of the dynamic load emulation method.
Under the same driving condition, if the total load torque of a vehicle on the test bench is similar to that of a vehicle on a real road within a minor error, the test bench could be considered a good performance in replicating the real road load conditions, thus the effectiveness of the load emulation method can be verified. According to Equation (3), the total load torque of a vehicle when running on a real road can be calculated as:
The load torques of the dual drive systems on a test bench are separately measured by two side torque sensors. So the total load torque of a vehicle on a test bench can be calculated as:
where, T l o a d t o t a l ¯ , T l o a d t o t a l are respectively called the reference load torque and the actual load torque.
A parameter μ is defined as the relative error of the reference load torque and actual load torque. It is served as an indicator to evaluate the load emulation performance, and can be calculated as:
6.1.1. Straight Line with Different Vehicle Masses
The experimental results obtained under the test contents of group 1 and group 2 are shown in Figure 11 and Figure 12 , respectively.

Experimental result under the driving condition of straight line with vehicle mass 20 t: ( a ) Speed tracking performance; ( b ) Comparison of total load torque of the vehicle; ( c ) Relative error of the load emulation (displayed by scatter plot).

Experimental result under the driving condition of straight line with vehicle mass 30 t: ( a ) Speed tracking performance; ( b ) Comparison of total load torque of the vehicle; ( c ) Relative error of the load emulation (displayed by scatter plot).
Figure 11 a and Figure 12 a show the reference speeds and actual speeds of both sides under the driving condition of straight line with different vehicle masses. The straight line is without slope, mild acceleration and deceleration intentions are executed alternatively on the vehicle. It is clear that the reference speeds are well followed by the actual speeds throughout the driving condition except for only few minor deviations. Additionally, from the partial enlargement of the figure, the actual speeds of both sides have a slight delay compared with the reference speeds. The speed-control loop delays, affected mainly by communication speed, control algorithm execution time and dynamometer response time, may account for this phenomenon. Figure 11 b and Figure 12 b show the reference load torque and actual load torque of the vehicle obtained by Equations (24) and (25). Generally, the actual load torque matches the reference load torque well. But it must be noted that the actual load torque is obviously lower than the reference load torque in region P1, P2 and P3 where sudden speed increases are observed in Figure 11 a and Figure 12 a. This is mainly a result of a poor response property of the dynamometer. The relative errors of the two torques throughout the driving condition are shown in Figure 11 c and Figure 12 c. Clearly, the relative errors are mostly concentrated within ±2%, almost all are within ±5%, indicating the good performance of the proposed load emulation method. Moreover, the experiments with different vehicle masses exhibit the similar good results demonstrates the robustness of the method.
6.1.2. Straight Line with Slopes
In order to verify the adaptability of the proposed load emulation method to complex working conditions, a driving condition containing slopes is designed. The slope angle gradually increases from 4° to 20°, and the experimental result is shown in Figure 13 .

Experimental result under the driving condition of straight line with slopes with vehicle mass 30 t: ( a1 ) Speed tracking performance; ( a2 ) Actual total load torque of the vehicle on the test bench; ( b1 , b2 ) are partial enlargements of the figure ( a1 , a2 ), respectively.
According to Figure 13 (a1), the actual speeds can generally track the reference speeds well throughout the whole driving condition. The straight line is with slope, and a slopping intention with the angle increasing from 4° to 20° is continuously implemented on the vehicle. Figure 13 (b1,b2) are respectively the partial enlargements of Figure 13 (a1,a2), which display the detailed test information when the slope angle varies from 8° to 12°. In these figures, it is obvious to see that the speed decreases while the load torque gradually increases at the instant transition stage of the two slope angles. This situation is similar to the one on a real road. However, the tracking performance is a little poor at this stage. The reason may be like this. The instantaneous change of the slope angle leads to the transient variation of the road resistance torque according to Equation (2), and the variation of this torque changes so fast that the dynamometer could not make an immediate response. This performance can be improved by applying a higher performance hardware system and using a more optimized control algorithm.
Table 3 is the load emulation performance under different slope angles. For a certain angle, due to slight changes of speed when a vehicle is running on the slope, the inertia load can be very small and dynamic load mainly consists of the road load. In this way, 1 second time range is considered for calculating the average relative error for each angle. As can be seen from the table, the load emulation errors under each slope angle are less than 2%, indicating that the dynamic load simulation method presented in this paper also shows a good application performance under the driving condition of straight line with slopes.
Load emulation performance under the driving condition of straight line with different slope angles.
Above all, the effectiveness of the proposed dynamic load emulation method is adequately validated under the driving condition of straight line in which the longitudinal dynamics of a DDTV is only taken into consideration. The lateral dynamics such as steering also plays an important role of DDTV drive performance [ 42 , 43 ]. A steering experiment should also be considered in future study to make the validation more adequate though this paper pay more attention to the method application in the load emulation system instead of the vehicle dynamics in the vehicle drive system.
6.2. Accuracy Validation of the Test. Bench Simulation Model.
Taking the actual torques ( T d ( l , r ) ) obtained from group 1 and group 2 experiments as the input of the test bench simulation model. The actual speeds ( ω t ( l , r ) ) obtained by the simulation model and the experiment are compared as shown in Figure 14 and Figure 15 .

Comparison of the actual speed obtained by the group 1 experiment and the simulation model with vehicle mass 20 t: ( a ) Left side actual speed; ( b ) Right side actual speed.

Comparison of the actual speed obtained by the group 2 experiment and the simulation model with vehicle mass 30 t: ( a ) Left side actual speed; ( b ) Right side actual speed.
Figure 14 and Figure 15 show that the speed obtained by the simulation model and the experiment matches very well in both sides with different vehicle masses, indicating that the simulation model is accurate. While, few minor deviations still exist. This is mainly because of the simplified operation in model establishment procedure, or inevitable external environment interference in a real bench test.
When designing a test bench for a DDTV, the simulation model can be used for beforehand research, such as the selection of dynamometer and gearbox, the optimization of control strategy, etc., thereby reducing the scheme changes and shortening the construction period.
7. Conclusions
This work innovatively focuses on the application of a dynamic load emulation method, denoted as speed tracking control strategy with feedforward compensation, on the design of a DDTV test bench featured with high power and large inertia. In this paper, the inertias of the vehicle body, tracks and roadwheels equivalent to the drive wheels are calculated separately to obtain an accurate vehicle total ERI. Dual dynamometers are applied to simulate the road load and the inertial load simultaneously. Experiments are conducted on the designed test bench under different test conditions. Results show that the proposed method has good robustness and adaptability to complex driving conditions, which demonstrates the effectiveness of the method application.
Findings of this paper will contribute to potential research in related fields. The detailed described dynamic load emulation method can be considered as a flexible and accurate approach to be extensively applied to other test benches of dual-motor drive vehicles. Additionally, the MATLAB/Simulink model of the DDTV test bench is established based on detailed derivation of the system dynamics, which can be used for initial design of a test bench, thereby shortening the platform construction period.
However, it must also be noted that at the instant of sudden transition in load torque, the speed tracking results exhibit slightly poor performance. This may be caused by the speed-control loop delays. Hence, a higher efficient hardware system and a more optimized control algorithm with consideration of nonlinear effect will be focused on in our future study. Moreover, lateral dynamics experiments such as steering, and real road test are needed to be conducted for further verifying the validity of the test bench response.
Author Contributions
Conceptualization, Z.W., H.L. and X.Z.; Data curation, Z.C.; Funding acquisition, X.Z.; Investigation, Z.W., H.L. and Y.Y.; Methodology, Z.C.; Project administration, X.Z.; Resources, H.L.; Software, Z.W. and Y.Y.; Supervision, Y.Y.; Validation, Z.W. and H.L.; Visualization, Z.C.; Writing-original draft, Z.W.; Writing-review & editing, Z.W. and X.Z.
This research was funded by the National Natural Science Foundation of China grant number [51275453] and the Fundamental Research Funds for the Chinese Central Universities grant number [2018QNA4001].
Conflicts of Interest
The authors declare no conflict of interest.

- < Previous
Home > Student Works > TDs > Doctoral Dissertations > 2575
Doctoral Dissertations
Electric-drive vehicle emulation using advanced test bench.
Poria Fajri
"Vehicle electrification is considered to be the most promising approach toward addressing the concerns on climate change, sustainability, and rapid depletion of fossil fuel resources. As a result electric-drive vehicle (EDV) technology is becoming the subject of many research studies, from academia and research laboratories to automotive industries and their suppliers. However, a crucial step toward the success of EDV implementation is developing test platforms that closely emulate the behavior of these vehicles.
In this dissertation, a new approach for emulating an EDV system on a motor/dynamometer test bench is investigated. Two different methods of emulation are discussed which are based on predefined drive cycle and unpredictable driving behavior. MATLAB/Simulink is used to model the test bench and simulations are carried out for each case. Experimental test bench results are also presented to validate hardware-in-the-loop (HIL) real-time performance for each method.
Furthermore, to provide a more realistic approach towards EDV emulation a braking system suitable for motor/dynamometer architecture is proposed. The proposed brake controller represents a very close model of an actual EDV braking system and takes into account both regenerative and friction braking limitations.
Finally, the challenges and restrictions of using a full scale test bench are outlined. To overcome these limitations, the development of an educational small scale hybrid electric vehicle (HEV) learning module is discussed which provides an ideal test platform to simulate and study both electric and HEV powertrains"--Abstract, page iv.
Ferdowsi, Mehdi
Committee Member(s)
Kimball, Jonathan W. Crow, Mariesa Zawodniok, Maciej Jan, 1975- Murray, Susan L.
Department(s)
Electrical and Computer Engineering
Degree Name
Ph. D. in Electrical Engineering
United States. Department of Energy
Support for this research was partially provided by the U.S. Department of Energy under grant DE-EE0002012.
Missouri University of Science and Technology
Publication Date
Journal article titles appearing in thesis/dissertation.
- Emulating on-road operating conditions for electric-drive propulsion systems
- EV braking emulation using a hardware-in-the-loop (HIL) motor/dynamometer test bench
- Development of an educational small-scale hybrid electric vehicle (HEV) setup
xii, 117 pages
Note about bibliography
Includes bibliographic references.
© 2014 Poria Fajri, All rights reserved.
Document Type
Dissertation - Open Access
Thesis Number
Electronic oclc #, recommended citation.
Fajri, Poria, "Electric-drive vehicle emulation using advanced test bench" (2014). Doctoral Dissertations . 2575. https://scholarsmine.mst.edu/doctoral_dissertations/2575
Since August 30, 2017
Included in
Electrical and Computer Engineering Commons
Advanced Search
- Notify me via email or RSS
- Collections
- Disciplines
- All Authors
- Faculty Authors
Author Corner
- Share Your Dissertation

Useful Links
- Library Resources
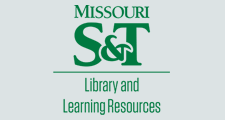
Dissertation Locations
- View dissertations on map
- View dissertations in Google Earth
Home | About | FAQ | My Account | Accessibility Statement
Privacy Copyright
On a new methodology for testing full load responses of wind turbine drivetrains on a test bench
Eine neue Methode zur Untersuchung des Volllastverhaltens von Antriebssträngen von Windenergieanlagen auf einem Systemprüfstand
- Originalarbeiten/Originals
- Open access
- Published: 20 March 2023
- Volume 87 , pages 173–184, ( 2023 )
Cite this article
You have full access to this open access article
- Muhammad Omer Siddiqui ORCID: orcid.org/0000-0002-5833-6768 1 , 2 ,
- Amir R. Nejad 2 &
- Jan Wenske 1
1574 Accesses
2 Citations
Explore all metrics
Today’s nacelle test benches are facing several challenges regarding meeting the increasing demands of modern wind turbines, which have been growing rapidly in operational range, size, and complexity. These challenges include reproducing the demanded extreme loads, dynamic load bandwidth, power capacity, and cost of testing. This contribution presents a new testing approach to tackle some of the aforementioned challenges faced by existing nacelle test benches. The method is demonstrated in a case study involving experimental measurements and simulations of a multi-megawatt wind turbine drivetrain recently tested at the DyNaLab of Fraunhofer IWES. By combining high-fidelity simulation models and partial load tests, the proposed approach has shown high potential for representing the full load response of a wind turbine nacelle. The proposed testing methodology has potential for resolving some of the challenges being faced by modern test benches in terms of obtaining full load responses on a nacelle test bench with a possibility of reducing the cost of testing.
Zusammenfassung
Moderne Gondelprüfstände stehen vor umfangreichen Herausforderungen, um den rapiden steigenden Anforderungen moderner Windenergieanlagen hinsichtlich Leistung, Größe und Komplexität gerecht zu werden. Zu diesen Herausforderungen gehören die Nachbildung der erforderlichen Extremlasten, die Dynamik der Lasteinleitung, die Last- und Leistungskapazität sowie die Prüfkosten. In diesem Beitrag wird eine neue Prüfmethode vorgestellt, mit welcher einige dieser Herausforderungen für bestehende Gondelprüfstände gelöst werden können. Die Methode wird anhand einer Fallstudie demonstriert, welche auf experimentellen Messungen und Simulationen eines auf dem Gondelprüfstand DyNaLab des Fraunhofer IWES getesteten Antriebsstrangs einer Multi-Megawatt-Windenergieanlage basiert. Durch die Kombination von detaillierten Simulationsmodellen mit physikalischen Tests unter Teillast zeigt die vorgeschlagene Methode ein großes Potenzial zur korrekten Vorhersage des Verhaltens eines Antriebsstrangs unter Volllast. Die vorgeschlagene Prüfmethode hat das Potenzial, einige der Herausforderungen zu lösen, mit denen moderne Prüfstände konfrontiert sind, indem das Volllastverhalten des Prüflings auf einem Gondelprüfstand präzise vorhergesagt wird, während sie gleichzeitig die Möglichkeit bietet, Prüfkosten zu senken.
Similar content being viewed by others
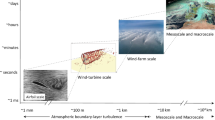
Wind-Turbine and Wind-Farm Flows: A Review
Fernando Porté-Agel, Majid Bastankhah & Sina Shamsoddin
Design of a vertical-axis wind turbine: how the aspect ratio affects the turbine’s performance
S. Brusca, R. Lanzafame & M. Messina
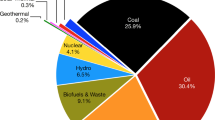
Principle Parameters and Environmental Impacts that Affect the Performance of Wind Turbine: An Overview
Mohamed Bashir Ali Bashir
Avoid common mistakes on your manuscript.
1 Introduction
The growth in wind power generation has maintained its rapid pace, as almost 94 GW of capacity were added in 2021 with a year-over-year growth of 12% [ 1 ]. In this growing industry, wind turbine manufacturers are competing to capture the greatest market share by developing reliable and cost-effective wind turbine systems [ 2 , 3 ]. They strive for successful and rapid prototype testing to ensure the desired product reliability and a faster time to market. These objectives have led to significant advances toward the development of several full-scale nacelle testing facilities around the world [ 4 ]. Table 1 lists some of the typical tests that can be conducted on a nacelle test bench. These facilities have become an attractive method for testing, as they offer system-level testing capabilities for the complete nacelle with the goal of applying realistic loads that the nacelle will experience in field operation in a controlled and repeatable environment.
However, the fast-growing trend of wind turbine size and operational capacity has increased the demands on the existing nacelle testing facilities. Many of them are already (or will soon be) too small to provide the required set of operational loads for the growing demands of larger wind turbines. As wind turbine technology is evolving, the existing testing methods also need to adapt correspondingly. There has been a trend for establishing larger test benches with increased load application capabilities to accommodate the demands of larger wind turbines [ 5 ]. However, this continuous trend of constructing bigger nacelle test benches for larger wind turbines might not be a sustainable solution. Furthermore, accessing the established nacelle test facilities is already financially difficult for smaller manufacturers of wind turbines and currently only possible for the bigger ones [ 6 ]. Constructing even larger test benches with possibly higher test costs may leave very few wind turbine manufacturers with the financial means to utilize these facilities in their development process.
Therefore, innovations are needed to enhance the functionality of the existing nacelle test benches and maximize their use. Scaled testing offers a potential solution, as it is a widely used approach across several industries for resolving difficulties related to test capacity and specimen size. Efforts are being made in the INNTERESTING research project [ 7 ] to explore the innovative use of scaled tests to resolve the abovementioned challenges in wind turbine system testing. This project proposes an innovative testing approach where advanced simulation techniques are combined with scaled tests of drivetrain components. The models are developed and validated using scaled test results and then used to simulate the full-scale component response without requiring full-scale tests. However, the successful demonstration and the application scope for this approach are yet to be seen.
Another possible solution lies in the use of virtual testing, which has already seen application in almost every major industrial sector including the automotive [ 8 , 9 , 10 , 11 ], railway [ 12 , 13 , 14 ], and aerospace [ 15 , 16 ] industries. Virtual testing forms a fundamental part of the development process in these industries, with the aim of either reducing the number of physical tests or pushing past the limits of physical testing. Although virtual testing of wind turbine drivetrains is rather new when compared with other industrial sectors, it has nevertheless demonstrated promising potential in several recent research studies [ 17 , 18 , 19 , 20 , 21 , 22 , 23 , 24 , 25 , 26 , 27 ]. The VirtGondel research project [ 28 ] at Fraunhofer IWES aims to advance the application of virtual testing further. The project proposes an innovative hybrid testing approach utilizing the virtual test bench model in combination with full-scale physical tests, which allows load ranges beyond the test bench capacity to be investigated. Unlike scaled testing, this approach removes the uncertainties that are inherent to a physical scaling of the test specimen.
This contribution presents this hybrid testing approach for emulating the full load response of a nacelle device under test (DUT). The detailed methodology will be explained in Sect. 2 . The high-fidelity model is described in Sect. 3 along with the required model fidelity. Case studies performed to demonstrate the proposed hybrid testing methodology are presented in Sect. 4 , followed by further discussion of the presented methodology in Sect. 5 . The conclusion can be found in Sect. 6 .
2 Hybrid nacelle test methodology
The proposed hybrid testing methodology for wind turbine nacelles is elaborated in Fig. 1 (represented inside the blue box). First, full-scale physical tests are conducted on a nacelle test bench at partial loads that are achievable within the load application capability of the test bench. Alongside these tests, virtual testing is performed for the same load regime. The measured DUT response at partial loads obtained from physical tests is compared against simulation results from virtual tests, and the virtual model is adapted as necessary to achieve the desired accuracy. Afterward, the validated virtual model is used to simulate the response of the DUT under full loads beyond the testing limits of the test bench.
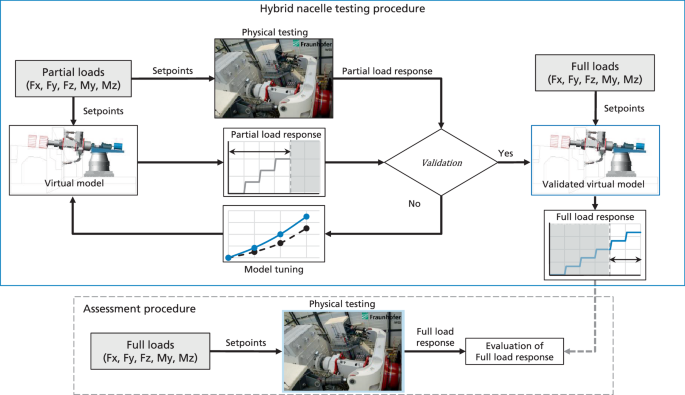
Workflow for the evaluation of the hybrid nacelle testing procedure
Nacelle tests on a 5 MW GE Cypress platform conducted at the DyNaLab facility of Fraunhofer IWES were used to demonstrate the proposed hybrid testing method. The nacelle features a multi-stage geared high-speed drivetrain with three point suspension topology. The main shaft is connected with the test bench load application system (LAS) via a hub adapter. The entire nacelle system rests on the tower adapter at the yaw bearing interface. During testing, the yaw system is locked to restrict the nacelle motion in the yaw direction. From the list of nacelle tests mentioned in Table 1 , the parasitic load tests have been chosen. The DyNaLab offers electrical and mechanical tests for a wind turbine nacelle of up to 10 MW power with the capability to apply up to 20 MNm bending moments and 2 MN forces at the hub interface. The virtual model of the nacelle is validated using only the partial load response obtained during the physical testing of the 5 MW nacelle. In this way, the capability of the validated virtual model to simulate the full load response can be evaluated using the available measurements from the physical tests conducted at full loads as shown in Fig. 1 (represented inside the gray dashed box).
3 Model description
A high-fidelity multibody simulation (MBS) model of the test setup was developed in Adams [ 29 ]. The model serves as a virtual twin of the physical test setup, as it includes all the relevant components of the test bench load application system and the nacelle drivetrain to reproduce the functionality and response of the actual physical system. Fig. 2 shows the entire virtual testing setup and the measurement locations for the DUT response of interest. The test bench flange adapters, coupling, and drive shaft are modeled as flexible bodies created by modal reduction of their respective finite element (FE) models using Craig-Bampton component mode synthesis [ 30 ]. Further details of the test bench LAS model have been elaborated in [ 31 ]. The MBS model of the nacelle drivetrain was developed such that it fulfills the NREL recommendations for drive train MBS model fidelity [ 32 ]. However, some enhancements have been made with regard to bearing stiffness. Instead of using bushing elements with a constant stiffness matrix, nonlinear force elements were used with spline functions to represent the bearing movements for wider ranges of applied load correctly. Table 2 summarizes the implemented modeling approach for the global system model.
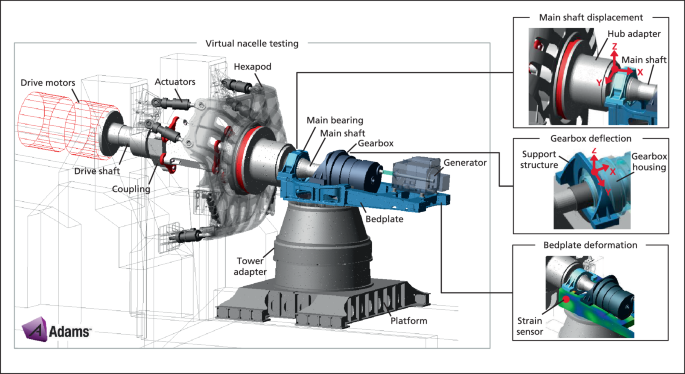
Virtual test bench model for the hybrid test concept and the measurement locations
Fig. 2 also shows the three measurement locations for the evaluation of the desired DUT response, which were implemented during the physical testing of the DUT. The first one is the relative displacement between the main shaft and the bedplate. This is measured in the physical system using three laser sensors for the measurement of the relative displacements in axial (X), yaw (Y), and pitch (Z) directions. The second one is the relative displacement between the gearbox housing and the gearbox support structure. Multiple laser sensors are installed between these two components to measure the gearbox housing deflections relative to the support structure in axial, yaw, and pitch directions. The simulation model delivers the relative displacements at the same locations to provide a one-to-one match with the physical measurements. Lastly, the bedplate deformations are measured using strain gauges installed at a location of interest. These are directly compared with the modal strains extracted from the bedplate flexible body at the same location where the strain gauge is installed.
4 Case studies
To demonstrate the proposed hybrid testing methodology, parasitic load tests have been carried out in which the LAS system of the test bench applies the following unidirectional loads on the drivetrain:
Pitch forces
Axial forces
Pitch moments
Yaw moments
In each of these tests, loads are applied individually at the hub interface with a stepped profile of increasing amplitude. As discussed in Sect. 2 , model validation and tuning using the results from partial load tests is a fundamental part of the proposed hybrid testing approach. However, performing the necessary tuning of model parameters to improve the error of a particular system response should not be detrimental to the remaining ones, since model parameters are very likely to have an influence on multiple system responses. It is vital to identify the influence of model parameters on the DUT responses first. Therefore, a sensitivity study is conducted by changing model parameters individually and comparing the changes in the response of interest. The findings are used as a reference during the model validation at partial loads for each of the unidirectional load cases.
4.1 Sensitivity study
The model parameters under study are the main bearing stiffness, the yaw bearing stiffness, the stiffness of the yaw lock system, the stiffness of the planet carrier bearing (stage 1), and the elastomer stiffness of the bolted connections between the gearbox housing flange and the gearbox support structure. These parameters are independently changed by a fixed percentage while keeping the remaining parameters unchanged. The results of the sensitivity study are plotted in Figs. 3 – 5 . The exact values of percentage change in response due to the parameter change are not shown for reasons of confidentiality. Instead, the percentage change is plotted in the vertical axis as a qualitative sensitivity measure with an upper limit (high) representing larger differences in response due to parameter change and a lower limit (low) representing no noticeable differences in response. Several interdependencies can be observed between some model parameters and the drivetrain response.
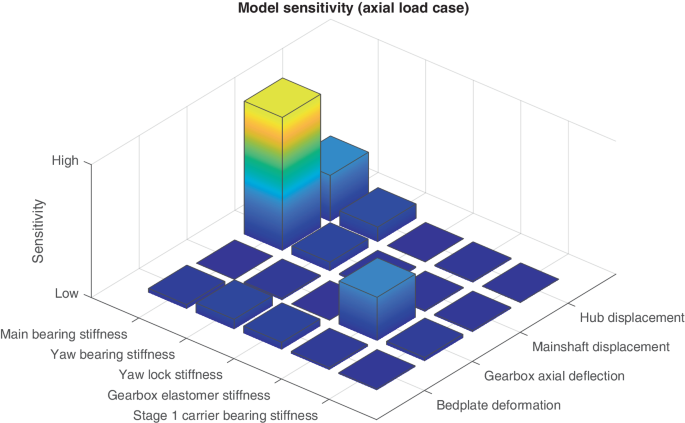
Model sensitivity for axial loads
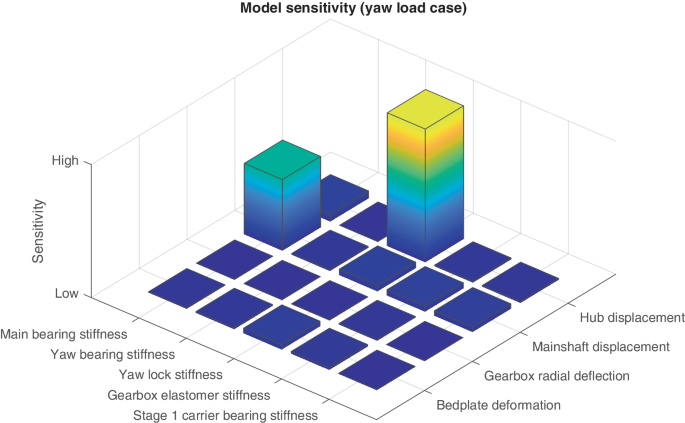
Model sensitivity for yaw loads
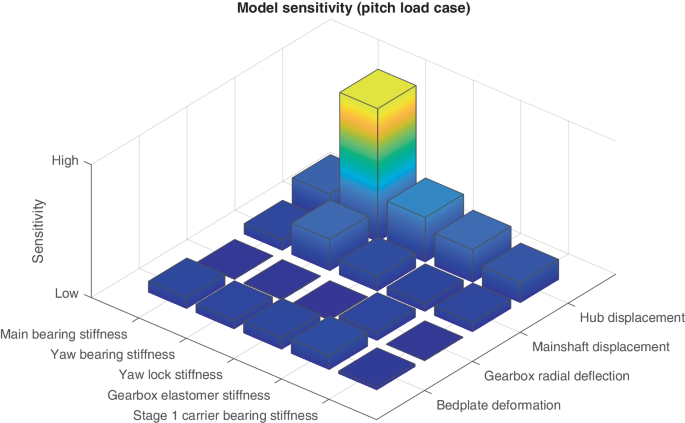
Model sensitivity for pitch loads
It is important to mention that, even though the main shaft is directly connected to the hub adapter, the displacement measurements of the two components have a key difference: the hub displacement measures the global movement of the hub relative to the stationary reference point on the ground, while the main shaft displacement is the relative motion between the main shaft and the bedplate. The stiffness of the main bearing has a direct influence on the displacement of the main shaft and the hub. It also has a noticeable effect on the strain readings at the strain gauge location on the bedplate for the pitch loads. The yaw bearing shows a higher influence on the hub displacement for the pitch loads as well as a noticeable effect on the bedplate strain readings and the main shaft displacement. The stiffness of the yaw locks strongly influences the hub displacements in the yaw direction and has some noticeable influence in the pitch direction. The gearbox elastomer stiffness has a stronger influence on the gearbox housing deflection for axial loads and shows some noticeable influence on several system responses for pitch loads. The bearing stiffness of the first stage planet carrier shows noticeable influence on the main shaft displacement and hub displacement for the pitch load case. These findings are used as a reference for the parameter tuning and model validation under partial loads.
4.2 Response under pitch forces
Fig. 6 shows the results for applied pitch loads. The DUT response corresponding to the partial loads and full load regions is separated by a vertical dashed line. The measured response at partial loads (i.e., below 60% load range) is used for model tuning with the objective of minimizing the error. This tuned model then simulates the response for extrapolated full loads (i.e., above 60% load range) shown on the right side of the vertical dashed line. The measured responses for all load ranges are also plotted for evaluation purposes. The relative error of the main shaft vertical displacement, although high in the 20–40% load regions, remains below 7% in the 60% load region and reduces significantly in the full load region. The reason for the higher relative error in the lower load regions could be linked to the higher nonlinearity in the stiffness of the main bearing at lower loads, due to which minor deviation of the modeled nonlinear stiffness curve from the real behavior can lead to higher uncertainties in response. The gearbox tangential deflection shows sufficient correlation with the measured results with the relative error remaining below 15% in the full load region. The simulated bedplate strain, although having a higher relative error in the partial load region, shows good correlation with the measured strain in the full load region with less than 3% relative error. The strain sensors installed on the bedplate also captured the oscillations corresponding to the main shaft rotation frequency. This is the reason for the noticeable oscillations in the bedplate strain measurements. These oscillations are not visible in the displacement measurements as those signals included filtering.
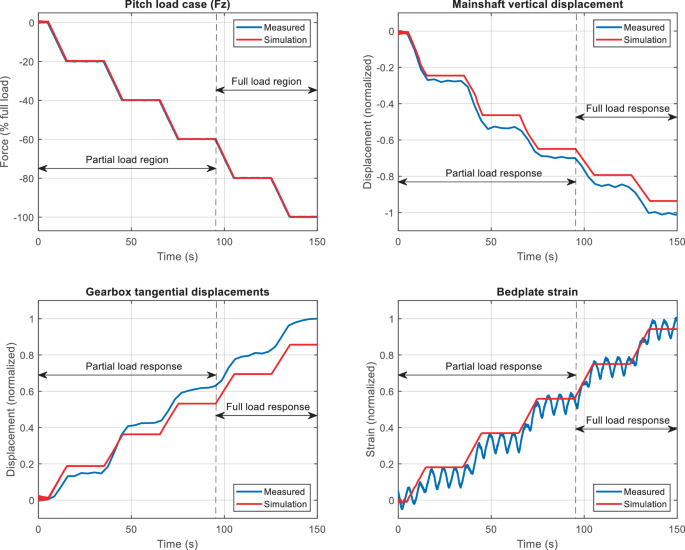
Load profile of the applied pitch forces at the hub interface and the corresponding drivetrain response
4.3 Response under yaw forces
Fig. 7 shows the case of yaw loads applied at the hub interface and the corresponding drivetrain response. The main shaft displacement in the yaw direction and gearbox radial deflection show a slight error in the partial load region but good agreement of the full load displacement response with the relative error remaining below 7%. However, the bedplate strain shows higher differences with a maximum relative error of 20% in the full load range.
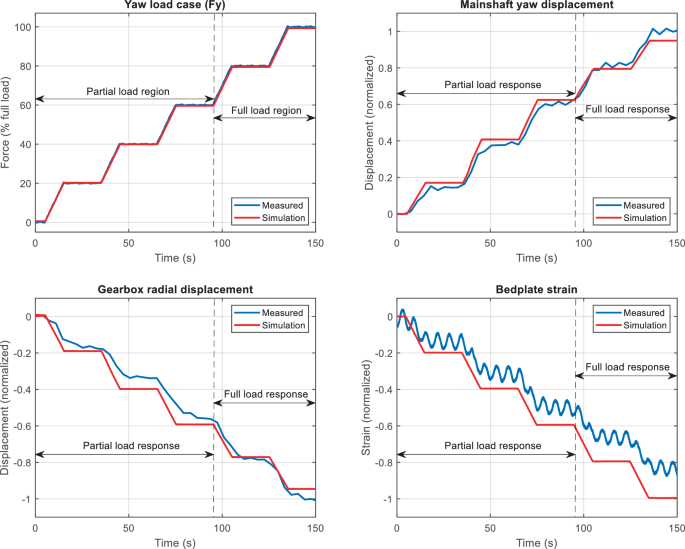
Load profile of the applied yaw forces at the hub interface for hybrid testing and the corresponding drivetrain response
4.4 Response under axial forces
For the axial load case, the main shaft axial displacement and the bedplate strain are compared and plotted in Fig. 8 . Due to the type of drivetrain topology, axial deflections of the gearbox housing did not occur in the discussed load regime and, therefore, are not included for this load case. The main shaft displacement results show good correlation with the measured values, with errors remaining below 4% in all load regions. The simulated bedplate strain follows the measured strain trajectory with a maximum relative error of 20% in the full load range.
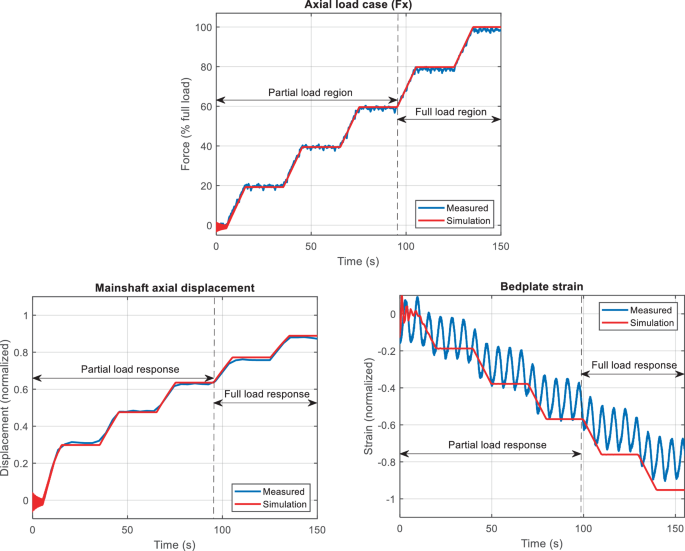
Load profile of the applied axial forces at the hub interface for hybrid testing and the corresponding drivetrain response
4.5 Response under pitch moments
Fig. 9 shows the case for applied pitch moments and the corresponding response. Very good agreement can be observed for the main shaft pitch displacement with the maximum relative error below 7% in full load response. The relative error in gearbox tangential deflection remains mostly very low until 75% load levels and below 12% in the full load range. The bedplate strain shows very good agreement in the partial load region with the error building up in the full load region but remaining just above 15%.
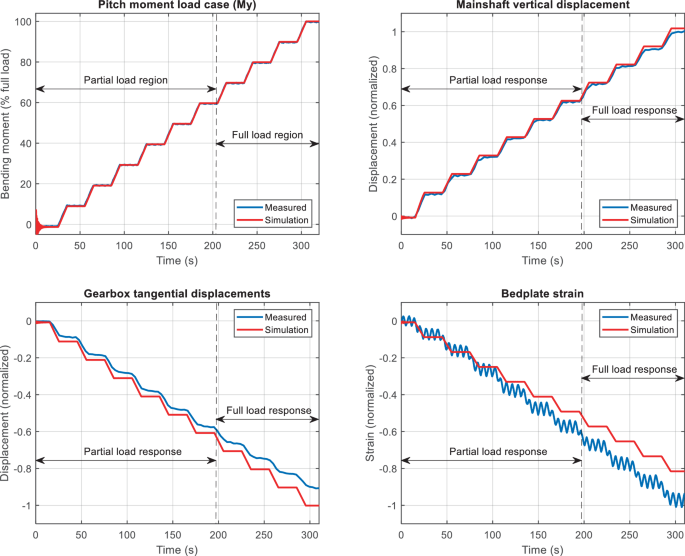
Load profile of the applied pitch moment at the hub interface for hybrid testing and the corresponding drivetrain response
4.6 Response under yaw moments
The drivetrain response under yaw moments is shown in Fig. 10 . The main shaft displacement remains in good agreement with the measured results, with the relative error less than 5% in partial loads. However, the error gradually increases at higher loads with a maximum relative error of 11% at full load. The bedplate strain response shows a good match with measured strains, with less than 5% relative error at partial loads and a maximum relative error of 8% in the full load region. The gearbox radial deflection, although having a higher relative error in the partial load range, shows satisfactory results at full loads with a maximum relative error of around 11%.
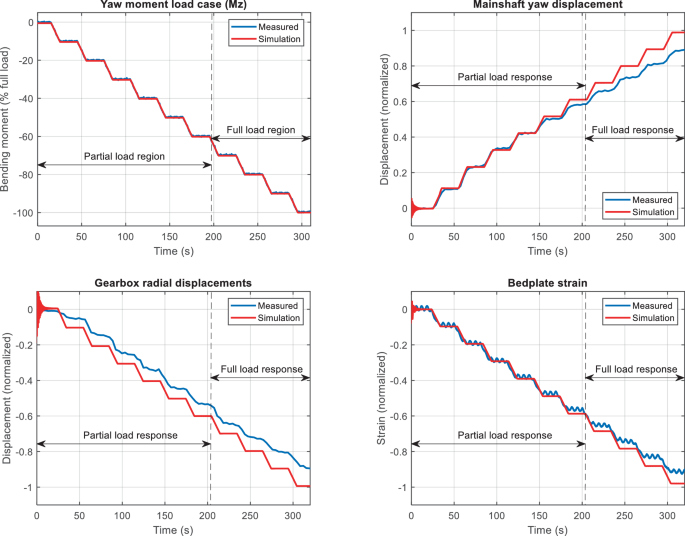
Load profile of the applied yaw moment at the hub interface for hybrid testing and the corresponding drivetrain response
5 Discussion
The proposed hybrid testing approach presented in this contribution aims to enhance the existing nacelle testing methods by combining the simulations with the experimental measurements. The results from the demonstrated load cases are promising, as the proposed hybrid test methodology was able to predict the full load drivetrain response under parasitic loads for most of the considered load cases. Table 3 summarizes the uncertainty in predicting the full load response of all the considered load cases. The bedplate strain showed a higher error in some load cases, which can be due to multiple reasons such as insufficient selected modes during flexible body generation, oversimplified interface definition (e.g., fixed joints instead of bolted connection with pretension) in the regions near the strain sensor, uncertainty in material definition (elastic modulus), or insufficient mesh density. Another possible solution for removing such errors is the integration of better validation criteria such as the incorporation of the rate of increase in error. These aspects will be investigated further in future work. It is also vital to identify the correlation between model parameters and the system response as well as possible nonlinearity in the system. The presented work considered nonlinear bearing stiffness, which showed good results for predicting the main shaft displacements at full loads. Only the parasitic load tests were considered in the presented work. Future work will incorporate this approach for more types of nacelle tests as listed in Table 1 .
The combined used of physical and simulative testing methods has been witnessed in almost every major industrial sector. Its implementation in the wind industry has significant potential, as it can help with the discovery of solutions to some of the challenges facing nacelle testing. The presented work is an attempt at advancing the use of hybrid testing methodology for wind turbine nacelles. This procedure achieves the actual test results covering most of the important aspects for design evaluation as well as obtaining the full load response backed up by validated models. The conducted physical tests, although in partial load regime, give important insights into the relevant system behavior and foster confidence in the validity of simulation models. These measurements are vital for developing reliable virtual models, as simulation models often require tuning and validation. The validated virtual model covers the full load response with potentially lower uncertainties compared with a virtual model which has not been validated. This method allows combination of the advantages of both realms (physical and virtual) of nacelle testing. Furthermore, the use of validated simulation models not only provides insights into the full load response, but can also reduce the number of physical tests required, which can reduce the test costs.
6 Conclusion
This contribution presented a hybrid testing method for nacelle testing which aims to predict the full load response of a wind turbine nacelle. The proposed approach utilized a high-fidelity virtual model of the nacelle and the test bench, which was validated by using measurements via physical nacelle testing conducted only at partial loads. Different parasitic load cases were considered as case studies for the demonstration of the proposed methodology. The results have shown that the virtual model after being validated using partial load measurements has performed well in predicting the full load response of the drivetrain. Possible solutions for the errors observed in some of the predicted responses have been discussed. This approach utilizes the existing tools and methods for predicting load response beyond the testing capacity of the nacelle test bench. Following further improvements, this method of hybrid nacelle testing not only has potential for resolving some of the challenges facing existing test benches for testing larger wind turbines, but might even help reduce the cost of conducting nacelle tests.
Lee J, Zhao F (2022) GWEC Global Wind Report 2022
Google Scholar
Mehroliya S, Anoop A, Mitra U, Paliwal P, Mundra P (2021) Comparative analysis of conventional technologies and emerging trends in wind turbine generator. In: IEEE 2nd International Conference On Electrical Power and Energy Systems (ICEPES). IEEE, pp 1–6
Prakash G, Anuta H (2019) Future of wind: deployment, investment, technology, grid integration and socio-economic aspects
International Energy Agency (2012) Advances in wind turbine and components testing. IEA R&D Wind Task 11 – Topical Expert Meeting
Siddiqui MO, Feja PR, Borowski P, Kyling H, Nejad AR, Wenske J (2023) Wind turbine nacelle testing: state-of-the-art and development trends. Renew Sust Energ Rev (under review)
MEGAVIND (2016) Test and demonstration facilities for wind energy test and demonstration facilities for wind energy needed to promote a competitive wind industry in Denmark
INNTERESTING: Innovative Future-Proof Testing Methods For Reliable Critical Components In Wind Turbines. https://www.innterestingproject.eu/ . Accessed 01-10-2022
Dressler K, Speckert M, Bitsch G (2009) Virtual durability test rigs for automotive engineering. Int J Veh Mech Mobil 47(4):387–401. https://doi.org/10.1080/00423110802056255
Article Google Scholar
Huizinga FTMJM, van Ostaijen RAA, van Oosten Slingeland A (2002) A practical approach to virtual testing in automotive engineering. J Eng Des 13(1):33–47. https://doi.org/10.1080/09544820110090304
Lee D-C, Han C-S (2009) CAE (computer aided engineering) driven durability model verification for the automotive structure development. Finite Elem Anal Des 45(5):324–332. https://doi.org/10.1016/j.finel.2008.10.004
Zhang B, Qingzhu C, Lu Y, Jianfeng W, Wang L, Wenqian C, Yao L, Yuqing G, Gu T, You SS (2017) Component tests based on vehicle modeling and virtual testing. SAE technical paper series. SAE International, Warrendale. https://doi.org/10.4271/2017-01-0384
Book Google Scholar
Matsumoto A, Sato Y, Ohno H, Suda Y, Michitsuji Y, Komiyama M, Miyajima N, Tanimoto M, Kishimoto Y, Sato Y, Nakai T (2008) Curving performance evaluation for active-bogie-steering bogie with multibody dynamics simulation and experiment on test stand. Int J Veh Mech Mobil 46:191–199. https://doi.org/10.1080/00423110801935806
Spiryagin M, Sun YQ, Cole C, McSweeney T, Simson S, Persson I (2013) Development of a real-time bogie test rig model based on railway specialised multibody software. Int J Veh Mech Mobil 51(2):236–250
Weidemann C (2010) State-of-the-art railway vehicle design with multi-body simulation. J Mech Syst Transp Logist 3(1):12–26
Ostergaard MG, Ibbotson AR, Le Roux O, Prior AM (2011) Virtual testing of aircraft structures. CEAS Aeronaut J 1(1–4):83–103. https://doi.org/10.1007/s13272-011-0004-x
You S, Gao SX, Nelson A (2019) Breaking the testing pyramid with virtual testing and hybrid simulation. Fatigue Aircr Struct 2019(11):1–10. https://doi.org/10.2478/fas-2019-0001
Giguère P, Wagner JR (2017) Wind turbine drivetrain test bench capability to replicate design loads: part I — evaluation methodology. In: ASME 2017 11th International Conference on Energy Sustainability
Giguère P, Wagner JR (2017) Wind turbine drivetrain test bench capability to replicate design loads: part II — case study of a multi-MW Drivetrain. In: ASME 2017 11th international conference on energy sustainability
Giguère P, Wagner JR (2022) Acceptance criteria for the tracking error of wind turbine drivetrain test bench when replicating dynamic loads. Wind Eng 46(1):160–176. https://doi.org/10.1177/0309524X211015271
Giguère P, Wagner JR (2022) Experimental verification of predicted capability of a wind turbine drivetrain test bench to replicate dynamic loads onto multi-megawatt nacelles, p 0309524X2110653
Matzke D, Schelenz R, Reisch S, Roscher B, Jacobs G, Theling J, Schroers M, Löpenhaus C, Brecher C (2018) Validation of the gearbox load calculation of a wind turbine MBS model. J Phys Conf Ser 1037:62025. https://doi.org/10.1088/1742-6596/1037/6/062025
Matzke D, Jacobs G, Schelenz R (2019) Validation of MBS modeling methods to calculate bearing and tooth loads in the planetary gear stage of a wind turbine. In: Conference for Wind Power Drives, CWD 2019 : conference proceedings. RWTH, Aachen, pp 333–348
Matzke D, Schelenz R, Jacobs G (2017) Full scale system simulation of a 2.7 MW wind turbine on a system test bench. In: Conference for Wind Power Drives, CWD 2017 : conference proceedings. RWTH, Aachen
Panyam M, Bibo A, Roach S (2018) On the multi-body modeling and validation of a full scale wind turbine nacelle test bench. In: ASME dynamic systems and control conference
Röder J, Jacobs G, Duda T, Bosse D (2020) Simulative investigation of the load propagation in a wind turbine drive train during a power converter fault. J Phys Conf Ser 1618(3):32028. https://doi.org/10.1088/1742-6596/1618/3/032028
Röder J, Jacobs G, Duda T, Bosse D, Herzog F (2021) Investigation of dynamic loads in wind turbine drive trains due to grid and power converter faults. Energies 14(24):8542. https://doi.org/10.3390/en14248542
Röder J, Jacobs G, Duda T, Bosse D, Herzog F (2021) Simulative investigation of wind turbine gearbox loads during power converter fault. Forsch Ingenieurwes 85(2):251–256. https://doi.org/10.1007/s10010-021-00461-2
VirtGondel: Development and validation of a virtual representation of the nacelle test bench for the elaboration of advanced test methods and more efficient test campaigns. Fraunhofer IWES
MSC Software Corporation Adams – the multibody dynamics simulation solution. http://www.mscsoftware.com/ . Accessed 06-09-2022
Craig RR (1987) A review of time-domain and frequency-domain component-mode synthesis techniques. 2:59–72. https://ntrs.nasa.gov/citations/19860042139
Siddiqui MO, Eich N, Eustorgi K, Feja P (2020) Implementation and experimental validation of a dynamic model of a 10 MW nacelle test bench load application system. J Phys Conf Ser 1618(3):32044. https://doi.org/10.1088/1742-6596/1618/3/032044
Guo Y, Keller J, Lacava W, Austin J, Nejad A, Halse C, Bastard L, Helsen J (2015) Recommendations on model fidelity for wind turbine gearbox simulations
Download references
Acknowledgments
The authors would like to thank the involved colleagues at Fraunhofer IWES and GE Renewable Energy for their contributions to the VirtGondel project. The funding of the VirtGondel project by the German Federal Ministry for Economic Affairs and Climate Action (BMWK) is kindly acknowledged.
Open Access funding enabled and organized by Projekt DEAL.
Author information
Authors and affiliations.
Fraunhofer Institute for Wind Energy Systems IWES, Bremerhaven, Germany
Muhammad Omer Siddiqui & Jan Wenske
Department of Marine Technology, Norwegian University of Science and Technology, NO-7491, Trondheim, Norway
Muhammad Omer Siddiqui & Amir R. Nejad
You can also search for this author in PubMed Google Scholar
Corresponding author
Correspondence to Muhammad Omer Siddiqui .
Rights and permissions
Open Access This article is licensed under a Creative Commons Attribution 4.0 International License, which permits use, sharing, adaptation, distribution and reproduction in any medium or format, as long as you give appropriate credit to the original author(s) and the source, provide a link to the Creative Commons licence, and indicate if changes were made. The images or other third party material in this article are included in the article’s Creative Commons licence, unless indicated otherwise in a credit line to the material. If material is not included in the article’s Creative Commons licence and your intended use is not permitted by statutory regulation or exceeds the permitted use, you will need to obtain permission directly from the copyright holder. To view a copy of this licence, visit http://creativecommons.org/licenses/by/4.0/ .
Reprints and permissions
About this article
Siddiqui, M.O., Nejad, A.R. & Wenske, J. On a new methodology for testing full load responses of wind turbine drivetrains on a test bench. Forsch Ingenieurwes 87 , 173–184 (2023). https://doi.org/10.1007/s10010-023-00629-y
Download citation
Received : 09 November 2022
Accepted : 19 January 2023
Published : 20 March 2023
Issue Date : March 2023
DOI : https://doi.org/10.1007/s10010-023-00629-y
Share this article
Anyone you share the following link with will be able to read this content:
Sorry, a shareable link is not currently available for this article.
Provided by the Springer Nature SharedIt content-sharing initiative
Advertisement
- Find a journal
- Publish with us
- Track your research
- Etusivu
- Opinnäytteet - ylempi korkeakoulututkinto
- Näytä viite
Implementation of interior permanent magnet synchronous machines and control in a wind power emulating test bench
Erling, ville (2017).

Avaa tiedosto
Hyväksymispäivämäärä, tiivistelmä.
- Opinnäytteet - ylempi korkeakoulututkinto [37813]
Selaa kokoelmaa
Omat tiedot.
Design and Test of Electro-Mechanical Brake Experiment System
Ieee account.
- Change Username/Password
- Update Address
Purchase Details
- Payment Options
- Order History
- View Purchased Documents
Profile Information
- Communications Preferences
- Profession and Education
- Technical Interests
- US & Canada: +1 800 678 4333
- Worldwide: +1 732 981 0060
- Contact & Support
- About IEEE Xplore
- Accessibility
- Terms of Use
- Nondiscrimination Policy
- Privacy & Opting Out of Cookies
A not-for-profit organization, IEEE is the world's largest technical professional organization dedicated to advancing technology for the benefit of humanity. © Copyright 2024 IEEE - All rights reserved. Use of this web site signifies your agreement to the terms and conditions.

IMAGES
VIDEO
COMMENTS
TEST BENCH DESIGN. The active parts of a lateral stator machine are the stator consisting of the lateral stator, windings and the shielding iron; and the rotor, consisting of the rotor steel and the permanent magnets. These components of the machine are responsible for the electromechanical performance of the machine such as torque and losses ...
Conclusion. A rotor test bench has been designed and constructed for performing the testing of a sensor device at rotation speeds of 19,000 rpm and at temperatures from −70 °C to 250 °C for up to 250 h. The rotor was balanced in several steps by increasing rotation speeds and shows vibrations and an emitted acoustic noise, which has the ...
The rotor dynamics study is critical in the design of rotating machinery. The dynamic modeling of rotors aims to estimate the operating condition of rotating machinery through the evaluation of parameters related to the critical velocity and responses to unbalance. The application of small-scale test bench and the development of dedicated experimental procedures are important for the grounding ...
In this paper, a new approach for emulating an electric-drive vehicle (EDV) system on a test bench setup consisting of a dynamometer, flywheel, and an electric propulsion unit is investigated. The equivalent rotational inertia of a vehicle is used to obtain a suitable control method based on vehicle and test bench dynamics. MATLAB/Simulink is used to model the test bench and simulate the ...
This work demonstrates the capability of a power electronic based power hardware-inthe- loop (PHIL) platform to emulate electric machines for the purpose of a motor drive testbench with a particular focus on induction machine emulation. PHIL presents advantages over full-hardware testing of motor drives as the PHIL platform can save space and cost that comes from the physical construction of ...
The test bench module (TBM) typically performs the following functions : 1. At the start of the simulation, the TBM reads the input image data from an external text file ... Details of the Sobel algorithm can be found in section 2.3 of this thesis. 19 3.2.2.1 Test Setup Figure 3.1 represents the diagram of the test bench module (TBM) used for ...
A test bench system with a DM coupled to a dynamometer is used to simulate on-road conditions for an EV system based on calculations of the vehicle's equivalent rotational inertia and all the forces exerted on the vehicle. (3) T W − T R = J e w × d ω m d t Here T W and T R is DM and total resistive torques at the wheel.
A test bench for the development and validation of new DDTV technologies is necessary and urgent. How to load the vehicle on a DDTV test bench exactly the same as on a real road is a crucial issue when designing the bench. This paper proposes a novel dynamic load emulation method to address this problem. The method adopts dual dynamometers to ...
Test bench is a cubic metal framed physical platform with its own wheels for moving. It is only being moved around by pushing it. The platform enables all the autonomous ... into the details of this thesis. 2.1 System description of the Sensible 4 main product As mentioned in the previous chapter, Sensible 4 mainly concentrates on ...
1. Introduction. In order to solve the background noise caused by the test bench's vibration, and to avoid the bench and. the laboratory floor resonance, and to improve the a ccuracy of the ...
The article proposes the design of a test bench simulator to test a parallel hybrid propulsion architecture for aeronautical applications. The virtual test bench simulates, in a scaled version, the real test bench, designed for a power of about 0.4 MW. After presenting the architecture of the real propulsion system, the virtual test bench is described. The real system is basically composed by ...
Fajri, Poria, "Electric-drive vehicle emulation using advanced test bench" (2014). Doctoral Dissertations. 2575. "Vehicle electrification is considered to be the most promising approach toward addressing the concerns on climate change, sustainability, and rapid depletion of fossil fuel resources. As a result electric-drive vehicle (EDV ...
A fully automated test bench was designed and commissioned which used a complete turbocharger unit to drive the compressor. The turbocharger turbine was driven by supplying compressed air at ambient temperature. The test bench was equipped with the necessary instrumentation which were required to obtain performance test measurements.
AUTOMATED TEST BENCH An Undergraduate Research Scholars Thesis by MILLIE KRIEL Submitted to the Undergraduate Research Scholars program at Texas A&M University in partial fulfillment of the requirements for the designation as an UNDERGRADUATE RESEARCH SCHOLAR Approved by Research Advisor: Dr. Stavros Kalafatis May 2019
By submitting this thesis electronically, I declare that the entirety of the work contained therein is my own, original work, that I am the sole author thereof (save ... the test bench covered in this report include integrating the dynamometer with a small test bench employing a single-cylinder, compression-ignition engine, ...
Diomède Senou Motor test bench designing for the Rotax 912 ULS motor . Engineering thesis 64 pages . Supervisor Head of Aeronautical Studies Heikki Aalto . 31.8.2009 _____ Abstract. In this work was rearched differend possibilities for a test bench assembly with a Rotax 912 ULS light aircraft engine.
II Objective of the thesis In order to solve the problem, we firstly designed and fabricated an original 3D gain characterization test bench on which experiments were performed. This is a semi-automatic setup with a compact dimension of 90×60×65 cm3 and it is designed for integrated antennas with frequencies above 26 GHz.
Today's nacelle test benches are facing several challenges regarding meeting the increasing demands of modern wind turbines, which have been growing rapidly in operational range, size, and complexity. These challenges include reproducing the demanded extreme loads, dynamic load bandwidth, power capacity, and cost of testing. This contribution presents a new testing approach to tackle some of ...
This thesis focuses on a wind power related test bench, in which permanent magnet synchronous machines are used. The test bench will be located in the laboratory of power electronics of Tampere University of Technology and it will have one motor and one generator, which are controlled by converters. ... The test bench uses interior permanent ...
in this final thesis submission. This project did not require approval from the Texas A&M University Research Compliance & Biosafety office. TABLE OF CONTENTS ... test bench are to rotate the shaft in the seal up to 6000 RPM, to supply gas with pressure up to 220 bars, to withstand a temperature of 0 upto 20°C and to be able to measure gas ...
this master thesis. It is remembered that the overall cost for the designed test bench is given in the section 1.1.1 and installation of the test bench. COST DIRECT 16108.10€ INDIRECT 25.44€ TOTAL 16133.54€ Table 9 Total cost of the master thesis (without considering the designed test bench) 1.3 ECONOMIC VIABILITY
By testing the characteristics of the bench, it is proved that the established simulation model can fully reflect the characteristics of the EMB system. Finally, two clamping force control methods are designed for the EMB system, and the bench test is carried out to compare the control effects. Both braking strengths and fast braking are achieved.
• Test a 10.6 cc/rev external gears pump to prove the correctness of the code and of the methodology followed. For both the design of the test bench and the drafting of the code is followed the standard ISO 10767:1-2015. To design the three kits are taken in account two external gear pumps and an axial piston